Blessed Memory of Dr. Andreas Noak
According to the recently murdered German chemist, Dr. Andreas Noak, it is the BLADE of a microscopic razor that CUTS the smooth endothelial lining of blood vessels!
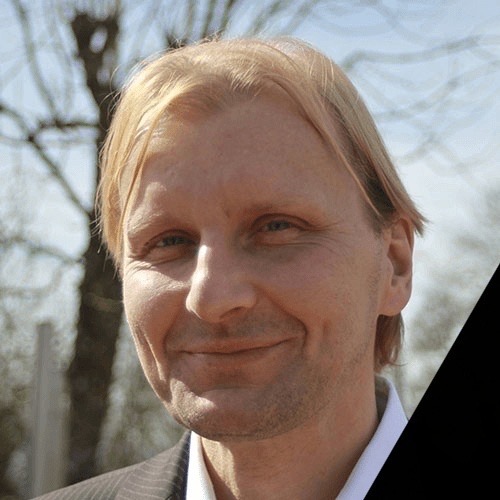
🕯🕯
German chemist Dr. Andreas Noak discovered graphene razors in fashionable. He himself claims (now, alas, it should be said "claimed") that he is one of the experts on carbon materials in the world.
In the video, he states:
"I detected graphene hydroxide in 'injections' using spectrograph analysis. Graphene hydroxide and graphene oxide have a similar toxic effect on the body, the material has a thickness of 0.1 nm and a length of 50 nm. It is almost transparent and 200 times stronger than steel, is not destroyed by the body, is inert when injected intramuscularly, but acts like a microscopic razor blade if it enters the blood vessels, cutting through the smooth endothelial lining of blood vessels and making them "sticky". This type of injury cannot be detected in a modern autopsy."
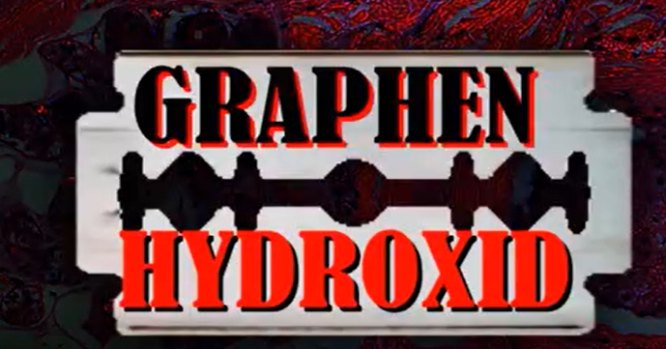
This could explain why young people and especially athletes have the highest risk of cardiovascular injuries from the vaccine, as they have faster blood flow and therefore more blood vessel incisions. This also explains why some people have had immediate adverse reactions to the vaccine that would not have occurred from mRNA alone. Since graphene will remain in the muscle of most people who get a "prick," I think they could end up flicking a 5g "switch" that would transmit a frequency that moves graphene hydroxide particles into the blood vessels.
From the category of "Suddenly, unexpectedly, mysteriously":
👉 33-year-old profitable dancer Santo Giuliano dies 5 days after a heart attack
😢 32-year-old Olympic tennis player Joachim Gerard rolls over during a game with heart problems
👉 19-year-old footballer Jalen Livy dies on campus after a game
😢 23-year-old baseball player Daniel Brito suffered a stroke while playing
👉 19-year-old footballer Tyrrell Williams dies on the field
😢 21-year-old footballer Okafor Kelechi dies in training
👉 29-year-old footballer Lee Moses dies in training
😢 15-year-old footballer Stephen Sylvester dies during cardio training
👉 18-year-old Emmanual Antwi football player dies on the playing field
😢 13-year-old football player Cajetan Chinoyelum Nsofor dies during training
👉 Moira Claire Arnie footballer, 15, died during training
😢 High school baseball pitcher Andrew Roseman died suddenly and unexpectedly, more details unknown
👉 17-year-old footballer Nicholas Lavrinas died suddenly and unexpectedly, the cause, according to media reports, is unclear.
😢 17-year-old footballer Mikel Lugo died during training
👉 16-year-old Devon DuHart, the footballer died under mysterious circumstances in July 2021.
😢 16-year-old football player Ivan Hicks dies of circulatory disease
👉 19-year-old soccer player Joe Bradshaw dies under mysterious circumstances off campus, the cause of death is unclear
😢 16-year-old Drake Geiger dies while playing
👉 15-year-old footballer Joshua Ivory dies during the game
😢 19-year-old Quandarius Wilburn falls during a workout and then dies.
👉 17-year-old footballer Dmitry Mackey dies after training
😢 28-year-old rugby player Tevita Bryce rolls over during a game due to a heart attack.
👉 29-year-old rugby player Dave Hyde rolls over and dies after a game.
😢 27-year-old baseball player Yusuke Kinoshita dies during training
😢 24-year-old Olympic cyclist Olivia Podmor suddenly and mysteriously dies in her room,
👉 😞At this week, another sprinter, Cameron Burell, dies under mysterious circumstances.
😢 23-year-old Chinese Olympic champion Gilbert Kvemoy felt weak and died on the way to the hospital.
👉 37-year-old former French footballer Franck Berje is dead
😢 German goalkeeper coach SV Niederpöring had a heart attack
👉 24-year-old Bordeaux professional Samuel Coul suffered a cardiac arrest
😢 25-year-old Belgian footballer Jente Van Genechten suffered a cardiac arrest.
👉 31-year-old Fabrice N'Sakala Besiktas Istanbul rolls over on the playing field
😢 Inflammation of the heart of 29-year-old Pedro Obiang of the First League of Italy
👉 30-year-old Venezuelan marathon master Alexaida is dead Guedez
😢 29-year-old Jose dos Reis (Luxembourg) goes on the field and needs resuscitation
👉 Germany C-Ligist Dillenburg players from Hirzenhain tilts, match cancelled
😢 16-year-old Diego Fersho from ASPT-Kan suffered a cardiac arrest
😢 16-year-old unnamed football player Bergamo suffered a cardiac arrest
👉 27-year-old Belgian amateur footballer Jens De Smet has died
😢 13-year-old footballer Janus Nova falls on the field with cardiac arrest
👉 17-year-old football player Dylan Rich dies of a heart attack during a game
😢 Birati Club Münster player suffered cardiac arrest
👉 24-year-old Lucas Surek from BFC Chemie Leipzig suffers from inflammation of the Heart
😢 49 Ain/ France: Frédéric Lartillo dies in the dressing room of a heart attack
👉 Sports director Calcio Orsago, 45-year-old Andrea Astolfi, died without prior illness
😢 22-year-old Abu Ali capsizes due to cardiac arrest during a match in Denmark
👉 19-year-old hockey player Sebastian Bos is dead. He died suddenly and unexpectedly.
300 Athletes Worldwide Collapsed On Field After The C-19 Vaccination In 2021!
The point is that these vaccinations contain GRAPHENE HYDROXIDE are, simply, razor blades in nano-sized blood vessels that cut through blood vessels, the heart and other human organs, causing bleeding and eventual death, and which are not biologically excreted by anything. The faster the blood circulates, i.e. the greater the physical exertion (or acute the disease of a person), the greater the likelihood of death. Dr. Noak calls it mass murder, genocide and the extermination of the nation.
According to the latest information, immediately after the publication by this scientist of his video about the presence of graphene dioxide in the vaccines, on November 26, the police arrived, and he ... died suddenly. His widow confirmed death.
In Germany, armed bandits in the state uniform of the German police broke into a doctor's residential or office premises for far-fetched violations of quarantine measures.
The real reason is the German authorities, who are Putin's accomplices seeking to cover up their war crimes against the German people and humanity.
A shocking video on my channel shows How Dr. Andreas Noak is detained by armed bandits in the person of police officers.
In the video, Noak is on the stream conducting a dialogue with someone, after which he is distracted by the incoming sounds outside the room. Then you can hear bangs on the door and a cry of "Polizei!", immediately after which the armed police break into the room and order Noak to lie on the floor, treating him as some kind of dangerous terrorist.
Noak is handcuffed, and a masked police officer tries to turn off the stream, but he only manages to turn the camera around.
Politics , 04 Dec 2020, 20:30 471 131
Putin appointed Chubais to a new position. What is important to know
Anatoly Chubais will become the president's special representative for relations with international organizations. What exactly he will supervise is still unclear: formally, in the sphere of his competence - the "sustainable development" of the country
Read more on RBC:
https://www.rbc.ru/politics/04/12/2020/5fca72019a79470a666599d5
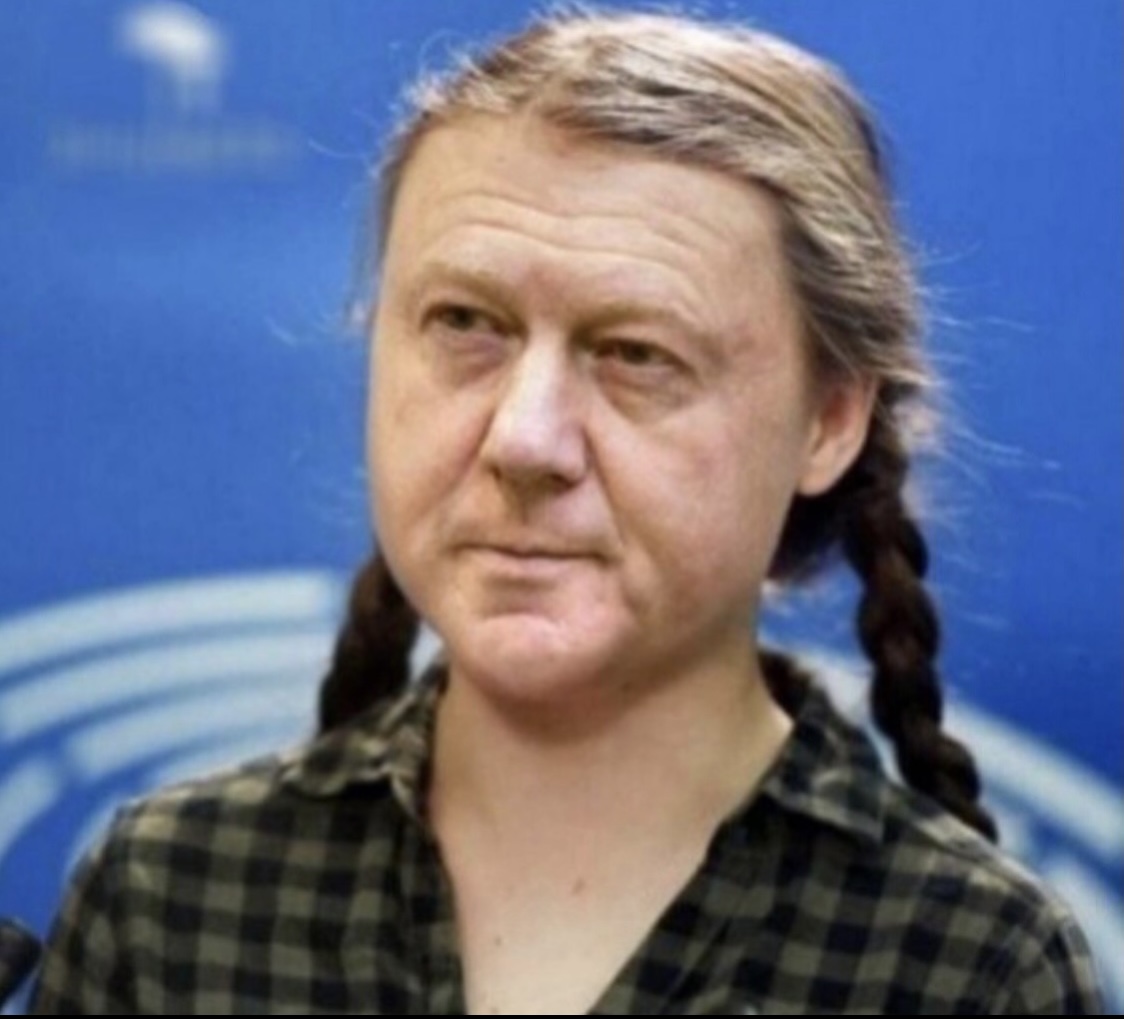
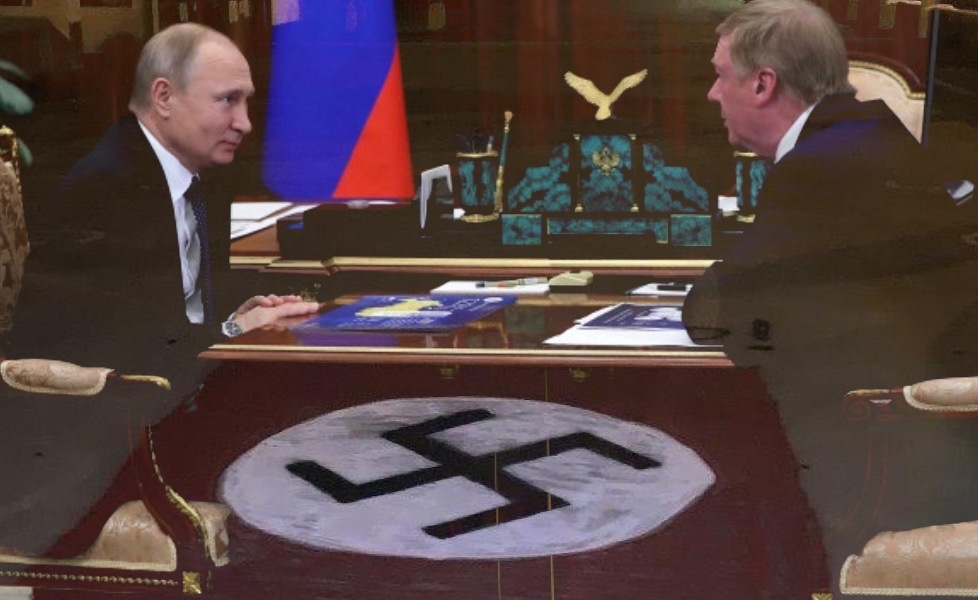
Well, what the huesos, jumped?!
Andreas Noack, a German chemist, was killed on November 26, 2021, for the materials published in this video.
https://t.me/archenoack
The "covid vaccines" contain graphene hydroxide (not to be confused with graphene oxide), which are the sharpest nano-sized blades that cut blood vessels, heart and other organs, causing the corresponding consequences.
Dr. Noak calls it mass murder, genocide and the extermination of the nation.
GRAPHENE OXIDE PRODUCTION METHOD
(19)
RU
(11)
2 709 594
(13)
C1
(51)
IPC
C01B 32/198(2017.01)
B82B 3/00(2006.01)
B82Y 40/00(2011.01)
(21) (22)
Request:
2018134006, 2018.09.26
(24)
Patent Term Report Start Date: 2018.09.26
(22)
Application date: 2018.09.26
(45)
Published: 2019.12.18
(72)
Authors:
Tkachev Aleksey Grigoryevich (RU)
Melezhik Aleksandr Vasilevich (RU)
Osipov Aleksey Aleksandrovich (RU)
Tkachev Maksim Alekseevich (RU)
(73)
Patent holders:
Limited Liability Company "NanoTechCenter" (RU)
(56)
Documents cited in the search report:
US 9815701 B1, 14.11.2017.
RU 2648892 C2, 28.03.2018.
US 2012/0129736 A1, 24.05.2012.
CN 106915741 A, 04.07.2017.
NINA I.
KOVTYUKHOVA et al.
Layer-by-Layer Assembly of Ultrathin Composite Films from Micron-Sized Graphite Oxide Sheets and Polycations, Chem.
Mater., 1999, v.
11, p.p.
771-778.
Illustrations1

Abstract
The invention relates to the chemical industry and nanotechnology. First, graphite is treated with a solution of hydrogen peroxide in sulfuric acid, and the amount of hydrogen peroxide is taken from 0.15 to 0.30 wt.h. per 1 wt.h. graphite in terms of 100% hydrogen peroxide with a total concentration of free water in the reaction mixture not exceeding 0.5%, taking into account the water formed in the reaction H2O2 + H2SO4 = H2SO5 + H2O. After that, water is added to the reaction mixture in such an amount that the concentration of free water becomes close to 2%. Potassium permanganate is then added while maintaining the concentration of free water. In the resulting reaction mixture, water is added in an amount that provides a concentration of free water close to 5%, and hydrogen peroxide is reintroduced. The resulting carbon-containing oxidation product is washed with an acid solution, then with water. The method of obtaining graphene oxide is environmentally friendly and suitable for industrial production. 1 z.p. f-ly, 1 il., 1 tablet., 1 pr.
Claims
1. A method for producing graphene oxide, comprising treating the carbon material with a first oxidizing agent (potassium permanganate) in a concentrated sulfuric acid medium, diluting the reaction mixture with water, then treating the second oxidizing agent (hydrogen peroxide) and washing the resulting carbon-containing oxidation product with an acid solution, then with water, characterized by the fact that graphite is used as a carbon material, and before treatment with potassium permanganate, graphite is further treated with graphite a solution of hydrogen peroxide in sulfuric acid, and the amount of hydrogen peroxide is taken from 0.15 to 0.30 wt.h. per 1 wt.h. graphite in terms of 100% hydrogen peroxide.
2. The method according to claim 1, characterized in that the process of oxidation of graphite is carried out in four stages with a controlled water content in the reaction mixture in stages in accordance with the following scheme:
- at the first stage of treatment of graphite with hydrogen peroxide, the amounts of reactants are calculated so that the total concentration of free water in the reaction mixture does not exceed 0.5%, taking into account the water formed in the reaction H2O2 + H2SO4 = H2SO5 + H2O;
- in the second step, water is added to the reaction mixture in such an amount that the concentration of free water becomes close to 2%;
- in the third stage, potassium permanganate is added to the system while maintaining the concentration of free water of the second stage;
- in the fourth step, water is added to the reaction mixture in an amount providing a concentration of free water close to 5%.
Description
The invention relates to the technology of graphene materials, specifically, to the technology of obtaining graphene oxide by oxidation of graphite.
Graphene oxide (OG) is a derivative of graphene, which is widely used in science and technology. However, to date, this substance remains very expensive, from 100 to 400 dollars. USA for 1 gram of dry matter. The high cost is associated with the complexity of the technology for the synthesis of OG and the complexity of its scaling.
It should be noted that before the graphene material research boom began, graphene oxide was called (and is sometimes called) graphite oxide. The name "graphene oxide" is a tribute to fashion. Graphene oxide and graphite oxide are the same substance.
Currently, the method described in 1958 by Hammers and Offeman [W.S. Hummers Jr., R.E. Offeman. Preparation of Graphitic Oxide // Journal of American Chemical Society, 1958, Volume 80, Issue 6, p. 1339]. One of the modern variants of this method is described in the book [Manual on Inorganic Synthesis. Vol. 3. Ed. by G. Brouwer. - M., Mir, 1985, 392 p. - P. 675-677]. This method involves the oxidation of natural graphite with potassium permanganate with the addition of sodium nitrate in concentrated (95-98%) sulfuric acid. Currently, there are many modifications of this method, relating to the preparation of initial components and their mass ratio, technological modes, methods of product purification. A review of known methods for the synthesis of graphene oxide is given in the work [S. Shamaila, A.K.L. Sajjad, I. Anum. Modifications in development of grapheme oxide synthetic routes. Chemical Engineering Journal (2016), doi: http://dx.doi.org/10.1016/j.cej.2016.02.109].
Despite numerous attempts to improve the hammers-Offemann method of synthesis of OH [W.S. Hummers Jr., R.E. Offeman. Preparation of Graphitic Oxide // Journal of American Chemical Society, 1958, Volume 80, Issue 6, p. 1339], it remains complex in terms of controlling technological regimes and takes a long time (especially for cleaning the final product). This method includes the following technological operations:
- mixing of crystalline graphite, sodium nitrate and concentrated (66 ° Ev≈95%) sulfuric acid when cooling the reactor in an ice bath;
- addition to the reaction mixture with intensive stirring of solid potassium permanganate (3 wt. h. per 1 wt. graphite) at such a rate that the temperature of the reaction mixture does not exceed 20 ° C;
- after adding all potassium permanganate, heating the reaction mixture to 35 ° C and holding at this temperature for half an hour;
- dilution of the reaction mixture with water, washing with water, then with ion exchange resins to remove electrolyte residues (salts).
The role of sodium nitrate in this method is not well understood. It can be assumed that in the medium of concentrated sulfuric acid, nitrate gives a nitronium cation, which, being a strong oxidizing agent, initiates an oxidative intercalation reaction of graphite and thereby contributes to its exfoliation, which in turn accelerates oxidation by permanganate. It has been experimentally established that without the addition of nitrate, the impurity of under-oxidized graphite in the final product is much greater.
The general essential features of the claimed invention and the classical method of obtaining Hammers-Offemann exhaust gas are the following:
- Treatment of graphite suspended in concentrated sulfuric acid, potassium permanganate.
- Dilution of the reaction mixture with water.
- Addition of hydrogen peroxide to the reaction mixture for the reduction of manganese compounds of higher oxidation degrees to ferrous manganese sulfate.
- Application of ion exchange resins to remove electrolytes from the aqueous dispersion of graphene oxide.
This method has the following disadvantages:
- The use of sodium nitrate in the process of oxidation of graphite, which entails the need to purify washing waters from nitrate ion. In addition, the use of nitrate in concentrated sulfuric acid gives evaporation of nitric acid, and as a result of the reaction with graphite, toxic nitrogen oxides are obtained.
- As a rule, this method gives a not fully oxidized product, that is, graphene oxide flakes, in the center of which are dark inclusions of under-oxidized graphite. The completeness of oxidation is highly dependent on the quality of the initial graphite and the temperature-time regime of the process; with graphite of very high quality (with a perfect crystal structure), the impurity of under-oxidized graphite is minimal. But with commonly used grades of graphite available on the market, the graphene oxide produced by the method in question contains a significant admixture of under-oxidized graphite.
To eliminate these shortcomings in various works, attempts were made to improve the Hammers-Offemann method, which were mainly reduced to the pre-preparation of the initial graphite by its preliminary intercalation and exfoliation, which accelerated the subsequent oxidation reaction of potassium permanganate.
So, in the work [Ling Sun, Bunshi Fugetsu. Mass production of graphene oxide from expanded graphite // Materials Letters, 2013, vol. 109, p. 207-210] used thermoexpanded graphite as the starting graphite and modified the order of mixing the components. First, thermally expanded graphite was mixed with a powder of finely ground potassium permanganate, then 98% sulfuric acid was added to this mixture when cooled in an ice bath during stirring. A thick paste was formed. Then the cooling bath was removed and stirring continued, as a result, oxidation with foaming of the reaction mass occurred. Further processing of the product is usual.
The disadvantage of this method, firstly, is the need to obtain thermally expanded graphite. Secondly, the addition of concentrated sulfuric acid immediately to the mixture of thermally expanded graphite and solid finely ground potassium permanganate is very dangerous, because under these conditions, if the mixing regime or temperature regime is violated, explosive oxide of hepavalent manganese can be obtained. Obviously, this method is not only dangerous, but also of little use for scaling, despite the declaration of mass production of graphene oxide in the title of the article.
In the patent [United States Patent 9,428,394. Highly oxidized graphene oxide and methods for production thereof. Tour J.M., Kosynkin, D.V. August 30, 2016] in order to eliminate the use of nitrate and at the same time ensure the completeness of graphite oxidation, increased the mass ratio of potassium permanganate to graphite and carried out the process in a mixture of sulfuric and phosphoric acids.
The method of obtaining OH described in the work [Nina I. Kovtyukhova, Patricia J. Ollivier, Benjamin R. Martin, Thomas E. Mallouk, Sergey A. Chizhik, Eugenia V. Buzaneva, and Alexandr D. Gorchinskiy is known. Layer-by-Layer Assembly of Ultrathin Composite Films from Micron-Sized Graphite Oxide Sheets and Polycations // Chemistry of Materials, 1999, vol. 11, No. 3, pp. 771-778] (prototype). In this paper, attention is drawn to the fact that usually the Hammers-Offemann method gives an under-oxidized product, that is, scales with dark inclusions of the original graphite in the center. To eliminate this deficiency, graphite was subjected to preliminary oxidative intercalation in a solution containing concentrated sulfuric acid, phosphorus pentoxide and potassium persulfate. In this case, a dark blue pintercalated graphite compound was obtained, which, obviously, is nothing more than graphite bisulfate of the first stage of intercalation.
Note: It is evident that phosphorus pentoxide in this work was used to bind free water to concentrated sulfuric acid. As our experience with this and similar systems shows, the oxidative intercalation of graphite by potassium or ammonium persulfates to a blue intercalated compound of stage graphite occurs only in the medium of anhydrous sulfuric acid. In ordinary concentrated sulfuric acid, containing about 5% water, when persulfates on graphite, the blue compound of graphite is not formed, intercalation does not occur completely.
After oxidative intercalation under these conditions, the reaction mixture was diluted with water, the graphite was filtered, washed with water to a neutral pH and dried. Then the usual synthesis of OH according to Hammers was carried out, as a result of which an OG without dark inclusions was obtained. The resulting product after the reduction of manganese dioxide with hydrogen peroxide was filtered, washed first with diluted (1: 10) hydrochloric acid to remove metal salts, then the product was washed with dialysis until the hydrochloric acid was removed. An aqueous dispersion of graphene oxide containing no inclusions of under-oxidized graphite was obtained.
As is known in the art, oxidative intercalation of graphite to blue graphite bisulfate of stage I, followed by hydrolysis, leads to partial exfoliation of graphite crystals into thin scales, wherein exfoliation occurs at the hydrolysis stage. Thus, the access of permanganate to the inner zones of graphite scales is accelerated, which ultimately leads to a more complete oxidation of graphite into graphene oxide. Probably, the effect of graphite exfoliation provides completeness of oxidation of graphite by potassium permanganate under these conditions.
The experimental part of the work in question does not say whether the authors added sodium nitrate to the reaction mixture or not. It is written only that the oxidation of pre-treated graphite, as described above, by the Hammers method was carried out and the technique is briefly described. Perhaps sodium nitrate forgot to mention.
Common essential features of the claimed invention and the prototype method are as follows:
- Treatment of graphite with peroxide reagent in sulfuric acid.
- Treatment of graphite under conditions causing graphite exfoliation.
- Treatment of pre-exfoliated graphite suspended in concentrated sulfuric acid, potassium permanganate.
- Dilution of the reaction mixture with water.
- Addition of hydrogen peroxide to the diluted reaction mixture to reduce manganese compounds of higher oxidation degrees to ferrous manganese sulfate.
- Washing the product with an acid solution.
- Alternatively, flushing the product with dialysis.
The disadvantages of the prototype method are as follows:
- The process of graphite pretreatment, including oxidative intercalation of graphite with potassium persulfate in a solution of sulfuric acid with phosphorus oxide, dilution, washing with water and drying, is multi-stage and requires additional equipment for its implementation. Also, new production waste appears, which entails additional costs for their neutralization or disposal. This complicates and increases the cost of technology.
- Since the authors of the prototype method write about the application of the classical Hammers method, sodium nitrate was probably used, which leads to the appearance of hard-to-catch nitrate waste in production waste, as well as the above problems associated with the appearance of toxic vapors of nitric acid and nitrogen dioxide.
The closest to the claimed invention (prototype) is a method for producing reduced graphene oxide described in the United States Patent 9815701. Synthesis of reduced graphene oxide nanoparticles. Nov. 14, 2017]. According to the prototype, the synthesis of nanoparticles of reduced graphene oxide includes the following steps:
- mixing carbon black with acid;
- the gradual addition to the solution of a first oxidizing agent for the oxidation of the carbon starting material to obtain a suspension;
- stirring of the suspension at a temperature of 35 ° C, followed by an increase in temperature to about 60 ° C;
- addition to the resulting solution (suspension) of water;
- addition to the suspension of a second oxidant by stirring, resulting in the formation of nanoparticles of reduced graphene oxide.
Sulfuric acid with the addition of phosphoric acid is used as an acid. As the first and second oxidizing agent, potassium permanganate and hydrogen peroxide are used, respectively.
It follows from the description of Example 1 of the prototype method that the actual process according to the prototype method is no different from one of the known variants of the Hammers method, except that carbon carbon black is used as a carbon base material instead of graphite. It should be noted that hydrogen peroxide, which is introduced into the reaction mixture after oxidation of the parent carbon material by potassium permanganate in the acid medium, after dilution of the reaction mixture with water, is not an oxidizing agent, as erroneously stated by the inventors of the prototype invention. In this case, hydrogen peroxide is added to reduce manganese dioxide to ferrous manganese sulfate. In this case, hydrogen peroxide is oxidized by manganese dioxide with the release of molecular oxygen.
The disadvantages of the known method are the following:
The use of carbon soot instead of graphite does not allow to obtain high-quality graphene oxide, since soot is not able to intercalate and separate into layers of oxidized graphene. In fact, it follows from the X-ray diffractogram of the product given in the description of the prototype method that the resulting product is an oxidized form of low-order carbon, and not at all graphene oxide. Indeed, if we look at the X-ray diffractogram given in this patent, then the maximum at 2 Θ = 25 degrees and at the radiation wavelength indicated in the figure λ = 0.154060 nm corresponds, according to the well-known Wolf-Bragg formula (2dsinΘ = nλ), to the interlayer distance d = 0.3948 nm. This is slightly larger than the interlayer distance in graphite (d = 0.3354 nm), and indicates a very imperfect structure of the carbon skeleton with graphene-like fragments. In high-quality graphene oxide, this interlayer distance is much larger, usually in the range of d = 0.9-1.4 nm, because the oxidized graphene layers in graphene oxide are easily separated in water and polar solvents. There is nothing like the product obtained under the prototype patent.
It is also obvious that, with the exception of the carbon base material used, the prototype method is identical to the well-known Hammers method, with all its drawbacks. In particular, even when using crystalline graphite as a carbon starting material, the known method yields a product containing a significant impurity of under-oxidized graphite.
The basis of the claimed invention is the task, by changing the reagents used and the choice of technological modes, to create an environmentally friendly technology for obtaining high-quality graphene oxide, suitable for industrial production with minimal costs.
The problem is solved by the fact that in the method of obtaining graphene oxide, including the treatment of the carbon material with the first oxidizing agent (potassium permanganate) in the medium of concentrated sulfuric acid, dilution of the reaction mixture with water, then treatment with a second oxidizing agent (hydrogen peroxide) and washing of the resulting carbon-containing oxidation product with an acid solution, then water, graphite is used as a carbon material in the declared method, and graphite is used before treatment with potassium permanganate. graphite is further treated with a solution of hydrogen peroxide in sulfuric acid, and the amount of hydrogen peroxide is taken from 0.15 to 0.30 wt.h. per 1 wt.h. graphite in terms of 100% hydrogen peroxide.
In this case, it is optimal to carry out the process with a controlled water content in the reaction mixture in stages in accordance with the following scheme:
- at the first stage of treatment of graphite with hydrogen peroxide, the amounts of reactants are calculated so that the total concentration of free water in the reaction mixture does not exceed 0.5%, taking into account the water formed in the reaction H2O2 + H2SO4 = H2SO5 + H2O;
- in the second step, water is added to the reaction mixture in such an amount that the concentration of free water becomes close to 2%;
- in the third stage, potassium permanganate is added to the system while maintaining the concentration of free water of the second stage;
- in the fourth step, water is added to the reaction mixture in an amount providing a concentration of free water close to 5%.
An explanation is needed here regarding the alleged mechanisms of the reactions taking place. It is known in the art that the reaction of graphite with peroxomoseric acid, H2SO5, taken as a solution in sulfuric acid, leads to rapid exfoliation of graphite with a significant increase in apparent volume. Peroxodiseric acid also reacts with graphite with its exfoliation, however, the process of exfoliation with peroxodiseric acid is much slower. For the first time these effects were described in the work [Melezhik A.V., Chuiko A.A. Cold expansion of graphite - the way to new technologies // Chemical Technology (Kyiv), 1992, No2, pp. 3-11]. Hydrogen peroxide itself does not react with graphite.Therefore, for rapid and effective exfoliation of graphite in the first stage, it is necessary to create conditions under which hydrogen peroxide added to sulfuric acid turns into peroxo-monosulfur acid according to the reaction equation:
It has been experimentally established that the equilibrium of the reaction (1) is shifted to the right if sulfuric acid is present in excess and the content of free water in it is less than 0.5%. To do this, it is necessary to take sufficiently concentrated hydrogen peroxide (at least 50%, preferably 60%, hydrogen peroxide with a higher concentration is not available on the free market) and a sufficiently large excess of anhydrous sulfuric acid.
Thus, when using 60% hydrogen peroxide in the claimed mass ratio range H2O2k graphite, the use of anhydrous (100%) sulfuric acid in the amount further specified in the exemplary embodiments of the invention ensures an almost complete conversion of hydrogen peroxide into peroxomoseric acid and effective exfoliation of graphite. To implement the claimed invention, it is possible to use more dilute hydrogen peroxide, for example, 30-50%, but at the same time a certain amount of oleum will need to be added to 100% sulfuric acid to bind excess water. The required amount of oleum can be calculated according to the reaction equation:
The calculation of the required number of components according to the reaction equations (1) and (2) can be performed by any chemist with secondary education. However, in practice, given the availability of 60% hydrogen peroxide on the market, it is advisable to use it, while there is no need to add oleum or calculate its amount. Hydrogen peroxide of a higher concentration can also be used, however, it is dangerous in circulation and does not go on free sale.
Further, in the embodiments, the amounts of reagents used are given based on the use of 60% hydrogen peroxide. If hydrogen peroxide of a different concentration is used, the amount of water added at various stages should be recalculated, which can be easily done by any chemist.
The following are data proving the feasibility of implementing the claimed method and its effectiveness.
The following starting materials were used to implement the invention.
Graphite
The quality of the graphene oxide obtained depends to a large extent on the quality of the original graphite. It is preferable to use high-purity graphite with a good crystal structure, preferably not fine dust, but, if possible, large scales, of the order of 0.1-0.5 mm. Special low-ash graphite of soviet production of the GSM-1 brand (99.9% carbon) showed itself very well. However, it is not being released now. Preferably, the graphite contains as little as possible of a fine (dusty) fraction, which may have a defective crystal structure and poorly intercalate. Our experiments have shown that for the implementation of the claimed invention, a special low-ash GSM-2 graphite according to GOST 17022-81, containing up to 0.5% ash, is quite suitable. Hydrogen peroxide
The 60% hydrogen peroxide available on the market is used. Its density is 1.2505 g/cm3.
Sulphuric acid
In the free market 100% sulfuric acid (monohydrate) is absent, because it freezes at + 10 ° C and its transportation in cold weather is impossible. Therefore, you have to prepare it on the spot. For this purpose, a calculated amount of oleum with a known SO3 content (usually 24% in technical oleum or 60% in hCG grade) is added to ordinary concentrated HCG sulfuric acid containing about 5% free water. The stoichiometry point can be controlled with great accuracy by the presence or absence of acid smoke in contact with air moisture [A. Gordon, R. Ford, Chemist's Companion. M., "Mir", 1976. - P. 442]. According to the cited work, this simple method allows you to adjust the composition of sulfuric acid with an accuracy of + _0.02% in water. If sulfuric acid is a monohydrate or contains water, it does not smoke. If it contains even a very small amount of free SO3, a clearly visible smoke appears when in contact with moist air. Potassium permanganate
ChDA stamps were used, in the form of small crystals. If there are fragile lumps, they must be kneaded through a plastic film. The presence of a large number of strong lumps suggests that potassium permanganate does not meet the standard or was stored in unsuitable conditions. Such permanganate should not be used.
Equipment
A factory stainless steel reactor with a working area volume of about 30 liters, equipped with a stirrer, a thermostatic checker and dosing devices for loading / unloading solid and liquid components, was used.
Filtration of the product and washing with a solution of sulfuric acid was carried out on a filter made of non-woven polypropylene material.
Removal of sulfuric acid from the graphene oxide suspension was carried out by treatment in a drum dializer.
The rest of the equipment and auxiliary devices were standard.
Example 1
In a dry and clean reactor at room temperature, 6.00 liters of 100% sulfuric acid are poured and 200 g of graphite GSM-2 are loaded. Close the reactor with a lid with an attached agitator. Turn on the agitator.
In the first step, with a continuously operating agitator, 60 ml of 60% hydrogen peroxide (density 1.2505 g / cm3, 60 ml = 75.03 g) is poured into the reactor in a thin stream through a capillary tube and the reaction mixture is stirred for 1 hour.
In the second step, 166 ml of water is added to the reaction mixture using a dispenser in a thin stream through a capillary tube, and stirred for another 30 minutes.
At the third stage, 600 g of potassium permanganate is loaded into the reactor for 3 hours, the temperature during the administration of the entire potassium permanganate is maintained at 20 ° C. After loading the entire potassium permanganate, stirring at 20 ° C continues for another 1 hour.
In the fourth step, 331 ml of distilled water is added to the reaction mixture with continuous stirring for 40 minutes. In this form, the reactor with the reaction mixture is left overnight, since the implementation of all the above technological operations takes a full working shift.
The next day, the agitator is turned on and 24 liters of water are slowly poured into the reactor at a speed that excludes the excess of the temperature of the reaction mixture above 60 ° C.
After that, 1 liter of 60% hydrogen peroxide is added to the reactor with continuous mixing, while the color of the reaction mixture turns from brown to golden yellow, which is associated with the reduction of manganese dioxide by hydrogen peroxide.
The resulting reaction mixture is a suspension of approximately 32 liters containing shiny golden-colored scales. This suspension is poured onto a polypropylene filter, filtered and washed with a solution of sulfuric acid with a concentration of 1 mol / l (= 9.2%). Washing is carried out until the manganese sulfate is completely removed from the suspension. To test the completeness of washing, aqueous ammonia or an alkali solution is added to the leachate sample until an alkaline reaction. The formation of a black or brown precipitate, or turbidity indicates the presence of manganese sulfate. When the flushing is completed, the leachate sample after alkalinization remains completely transparent and colorless.
The amount of 1M sulfuric acid required for complete washing depends on the filtration regimen, but is approximately 30-35 l. It should be noted that the product after unloading can not be washed immediately with water, because graphene oxide in acid-free water is easily exfoliated to form a gel that clogs the filter and water filtration is extremely slow.
The resulting product containing a certain amount of sulfuric acid is washed from the acid using a drum-type dialyzer, after which the concentration of graphene oxide is brought to a standard concentration by adding water. The most convenient concentration for various applications is 0.5% per parent graphite. That is, if the loading of graphite into the reactor was 200 g, the final product is brought with water to a total mass of 40 kg and thoroughly mixed. It should be noted that the concentration is more convenient to calculate the original graphite, because graphene oxide does not have a constant composition, in addition, its dry mass depends on the humidity of the air.
When dried, the aqueous dispersion of graphene oxide forms a flexible transparent film, red-brown in color on the lumen. With rapid heating to 200-250 ° C, this substance flares up and turns into highly dispersed carbon.
In the production of graphene oxide according to the claimed invention, wastewater containing sulfuric acid, potassium sulfate and manganese sulfate is formed. For their utilization, ammonia is added to a slightly alkaline reaction and then a small amount of hydrogen peroxide to oxidize the precipitated bivalent manganese hydroxide to tetravalent manganese hydroxide. Tetravalent manganese hydroxide is separated by filtration, and it can be used as a chemical reagent for various purposes (for example, as a depolarizer in chemical current sources). The solution contains ammonium sulfate with a small amount of potassium sulfate. This solution can be used as a fertilizer in agriculture.
Theoretically, sulfuric acid can be regenerated, without being neutralized by ammonia, by evaporation. The feasibility of a particular method of disposal is determined by economic considerations.
In FIG. 1 is an X-ray diffractogram of an air-dry film of graphene oxide obtained according to Example 1. As can be seen, the band corresponding to graphite (interlayer distance 0.3354 nm, which corresponds to 2teta = 39.94 ° with an X-ray wavelength of 2.29091 A) is absent, which indicates the completeness of graphite oxidation. The observed intense band with a maximum at 2teta = 9.28 ° corresponds to an interlayer distance of 1.416 nm. In different literature sources, the interlayer distance for graphene oxide varies widely, 0.6-1.2 nm, depending on the degree of oxidation of graphite and the humidity of the sample. Judging by the interlayer distance observed by us, the resulting graphene oxide has a fairly high degree of oxidation.
Thus, it is obvious that in the claimed invention, the completeness of oxidation of graphite by potassium permanganate in sulfuric acid without the addition of nitrate is achieved due to the preliminary exfoliation of graphite during its interaction with peroxomoseric acid, which, in turn, is formed in the reaction of hydrogen peroxide with sulfuric acid with a minimum content of free water in the system. This claimed invention differs from the prototype method, in which when graphite is treated with a peroxide compound in sulfuric acid, only oxidative intercalation of graphite occurs, and partial exfoliation occurs already during hydrolysis and washing with water. At the same time, the degree of exfoliation is small.
In order to find out the limits of the mass ratio of hydrogen peroxide to graphite, at which effective exfoliation of graphite occurs, a series of experiments were conducted in which a suspension of graphite in 100% sulfuric acid was treated with different amounts of 60% hydrogen peroxide, which under these conditions was converted into peroxomoseric acid. In these experiments, the ratio of sulfuric acid to graphite was constant, namely, 75 ml of 100% sulfuric acid per 2.5 g of graphite, which corresponds to the ratio in Example 1. The reaction mixture was kept for 1 h at 60° C. until the expansion of the intercalated graphite was completed. The degree of expansion (exfoliation) was estimated by the apparent volume of the surfaced layer of the expanded graphite compound (without stirring, it floated due to the presence of pores containing oxygen gas). It was found that the apparent volume of the layer of the expanded graphite compound increases with an increase in the amount of hydrogen peroxide (respectively, peroxomoseric acid), the data are given in the table.
Table.
The dependence of the apparent volume of the expanded graphite compound layer in the graphite -H2SO5-H2SO4 system on the mass ratio of the peroxide compound to graphite, moreover, the peroxide compound is recalculated by the mass of 100% H2O2.
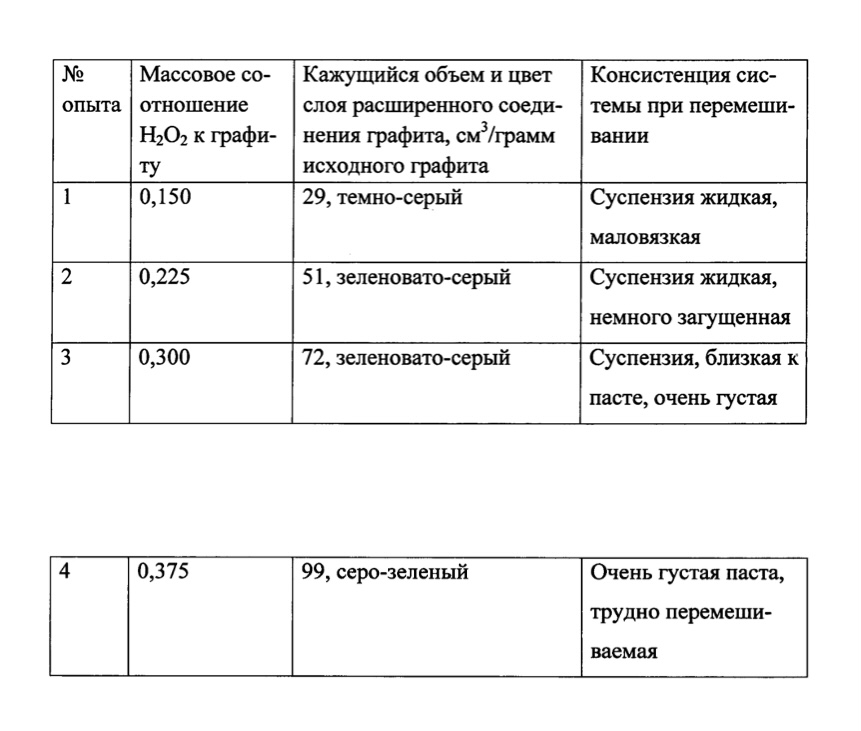
In this case, the mass ratio H2O2k graphite in experiment No. 2 corresponds to the synthesis of OG according to example 1.
From the table it can be seen that the apparent volume of the layer of the expanded graphite compound formed in the reaction of graphite with peroxomoseric acid increases approximately in proportion to the mass ratio H2O2k graphite. The larger this volume, the more efficient the exfoliation of graphite occurs, which means that the more complete the subsequent oxidation of the expanded graphite substance by potassium permanganate will be. However, technological limitations should be taken into account. The reaction mass shall be easily mixed. With a ratio H2O2k graphite of 0.225 (experiment #2 = example 1), the suspension is liquid and easily mixed, so this ratio can be considered optimal. With a mass ratio H2O2k to graphite of 0.300 (experiment 3), the system can still be mixed. However, already with a mass ratio of H2O2k to graphite equal to 0.375 (experiment 4), the system is such a thick paste that it is almost impossible to work with it, introduce any reagents into it and evenly mix it. Of course, it is possible to increase the amount of sulfuric acid in the system to dilute this paste and make it fluid. However, an increase in the amount of sulfuric acid leads to an unjustified increase in the cost of both the synthesis itself and the subsequent disposal of waste. Therefore, we consider the mass ratio of H2O2k to graphite equal to 0.300 as the upper practically acceptable limit.
As for the lower limit of the mass ratio H2O2k to graphite, it can be assumed to be equal to 0.150 (experiment 1), at which there is still a significant expansion (exfoliation) of graphite. It is not advisable to reduce this ratio further, because we will lose the quality of the product, and it makes no sense to save on cheap hydrogen peroxide.
The technological process of obtaining graphene oxide according to the claimed invention is easily scalable, the resulting product can be widely used in engineering and technology.
Documents cited in the search report1
Document Number Title
RU2648892C2 A METHOD FOR OBTAINING GRAPHENE-CONTAINING MATERIALS AND...
Related documents20
Document Number Title
RU2455365C1 METHOD OF HYDROLYSIS OF VEGETABLE FIBROUS...
RU2657504C2 GRAPHENE PRODUCTION METHOD
RU2453607C1 METHOD OF HYDROLYSIS OF VEGETABLE FIBROUS...
RU2626635C1 Method of purification of fullerene C 60 from oxide impurities
RU2486256C2 PRE-TREATMENT METHOD FOR SACCHARIFICATION...
RU2530126C2 PRODUCTION OF IRON ORTHOPHOSPHATE
RU2242277C2 METHOD AND SORBENTS FOR SULFUR REMOVAL
RU2635567C1 PHOSPHORUS-CONTAINING CATALYST FOR CONVERSION...
RU2693755C1 METHOD OF OBTAINING GRAPHENE MATERIAL
RU2510431C2 LIQUID FOR CHEMICAL CONVERSION TREATMENT...
RU2447936C1 CARBON-BASED CATALYST FOR...
RU2347763C2 Soluble CHROMATE REDUCER,...
RU2681538C2 METHOD OF LIMITING THE EMISSION OF DUST FROM GRAINS...
RU2230608C2 SORBENT COMPOSITION, METHOD OF ITS PREPARATION AND...
RU2356885C2 METHOD OF REMOVAL AND REGENERATION OF MIXTURES OF NITR...
RU2394017C2 METHOD FOR OBTAINING HIGH-PURITY TEREPHTHALIC ACID
RU2602859C2 HIGH PURITY GRANULAR SILICON DIOXIDE FOR...
RU2728137C2 Composition containing modified red...
RU2565594C2 REACTION SYSTEM AND ITS PRODUCTS
RU2436627C2 CATALYST FOR THE PRODUCTION OF HYDROCARBONS FROM...
Source
https://yandex.ru/patents/doc/RU2709594C1_20191218
The full Russian case is here ⬇️
https://telegra.ph/Russian---American---Chinese-case-of-the-crown--19-12-28
https://telegra.ph/New-Years-Cases-Crown--19-12-28
https://telegra.ph/The-story-of-how-graphene-works-in-the-human-body-01-02
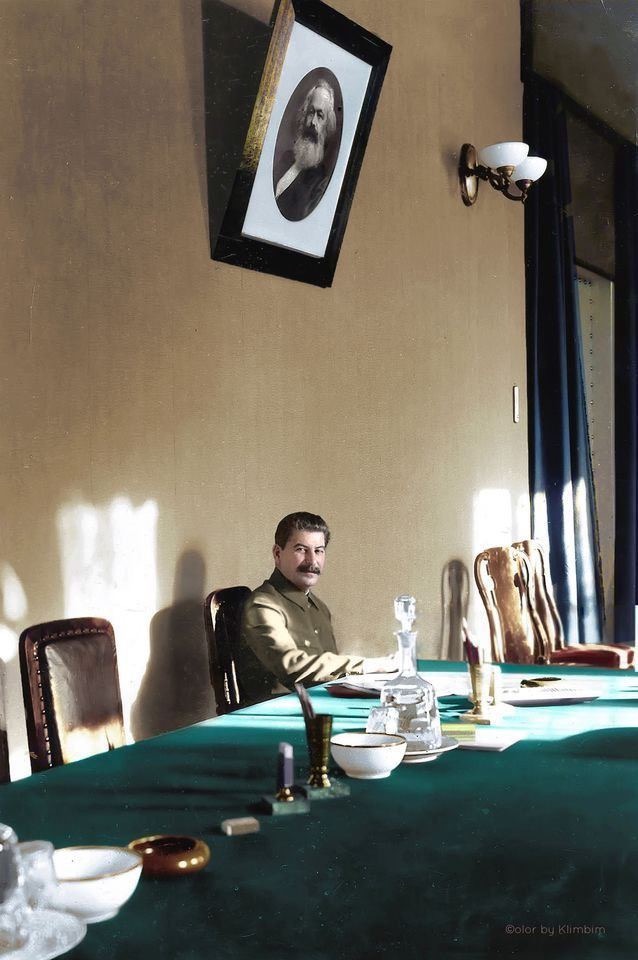
Stalin in the Kremlin, 1932.
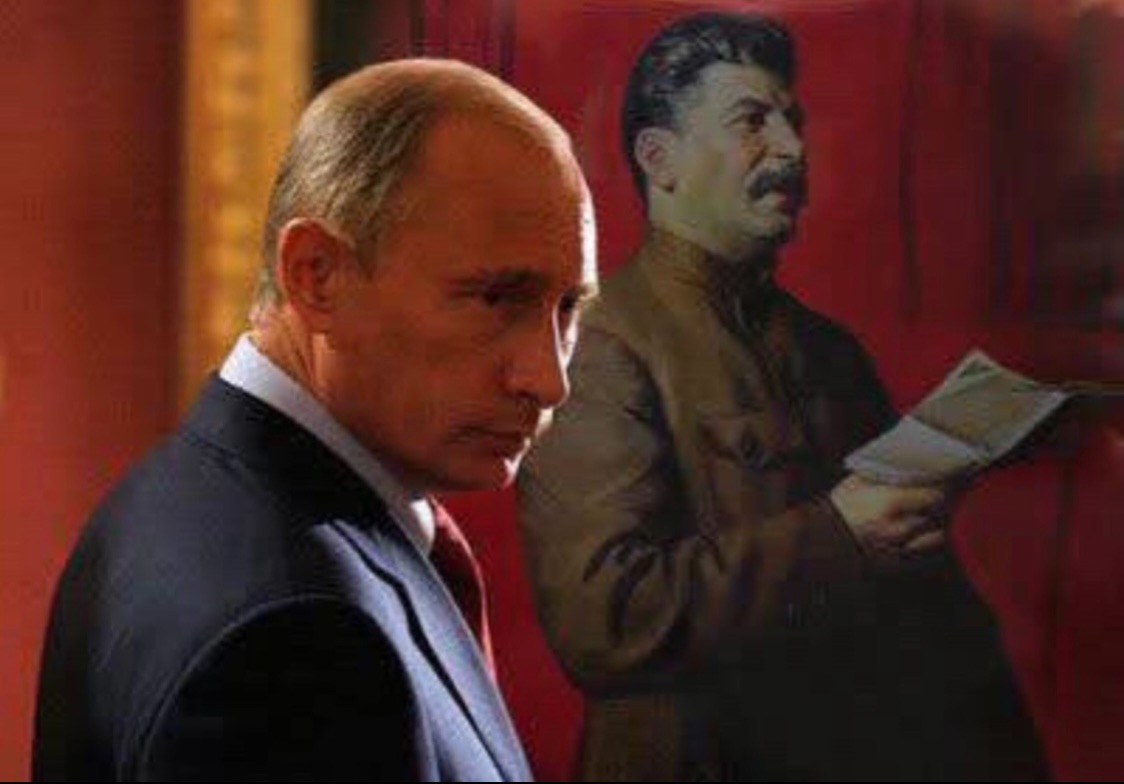