True Hole
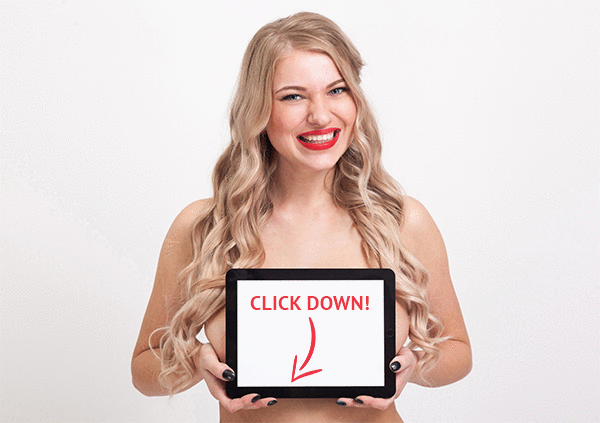
🛑 ALL INFORMATION CLICK HERE 👈🏻👈🏻👈🏻
True Hole
Subscribe
Advertise
Contact
Register/Log in
Home
Product News
True Hole Technology
ShortCUTS Search
Articles & Columns
Blogs & Briefs
Product News
Video Reports
Subscribe
Advertise
Privacy Policy
Glossary
Contact
1 Northfield Plaza
Suite 240
Northfield, IL 60093
Phone: (847) 498-9100 Fax: (847) 559-4444 Email: ctenews@ctemedia.com
Hypertherm's True Hole Technology was introduced to the market in 2009 and has created a lot of interest from end users, particularly with regard to its capabilities. While many acknowledge the difficulties in using plasma for hole cutting, advancements in technology have enabled a way to significantly improve hole quality from a functional perspective, which addresses the main concerns expressed by customers. Today, end users have multiple options to produce holes, such as drilling or laser cutting; however, the advantages of being able to use plasma include both productivity enhancements and a lower operating cost. Traditionally, the main complaint customers have had regarding plasma cut holes have centered on the quality of the holes, in particular how to produce a hole that is functional.
Two specific concerns with plasma holes are the taper and the ding or divot that is present on the interior of the hole. Both of these cut quality issues prevent a bolt from being able to pass through the hole; therefore, operators typically would have to perform secondary operations in order to improve the roundness of the hole to the point where a bolt would cleanly fit. After years of research, Hypertherm developed True Hole Technology in order to address these concerns. Now that this technology has been in the market for over a year, many people are asking for more information about True Hole Technology, which is the intent of this article. Having a better understanding of the depth behind this technology can help educate anyone who is currently using or considering using True Hole Technology.
Being informed about any potential limitations of the technology can also help mitigate frustrations that may arise from any misunderstanding during the sales process. As with any purchase, knowledge is an important and integral step that should be discussed early to ensure satisfaction with the overall end result. True Hole Technology is a patent-pending technology that was developed by Hypertherm to enable customers to easily and consistently produce significantly better hole quality than what had previously been possible with plasma.
Hypertherm is a major manufacturer of plasma cutting systems and is located in the United States. As part of their ongoing commitment to product development, Hypertherm often conducts "voice of the customer" surveys in order to better understand how the future work of their engineers can be best prioritized to meet the needs of end user customers. In a survey conducted several years ago, the number one complaint from end users about plasma cutting was the poor quality of the cut holes.
One key advantage of True Hole includes the virtual elimination of hole taper, which was a common complaint about the quality of holes from end users. The purpose of a hole is typically to pass a bolt through, yet the presence of taper necessitated either oversizing the hole which led to a loose fitting hole, or performing secondary operations such as reaming or drilling in order to improve the overall hole quality. Both of these options resulted in less than satisfactory results in terms of quality, productivity, and operating costs. Through the elimination of hole taper, the secondary steps are no longer necessary, saving time and money when producing bolt-quality holes.
A second key advantage is that the ding or divot has been minimized and biased to the outside of the hole. This ding or divot is often formed by the intersection of the cutting lead-in with the outer edge of the hole, and was another common complaint with end users. Similar to taper, anything that protruded into the hole prevented a bolt from easily passing through. Some end users would have to oversize the hole, while others would have to use secondary operations to try and improve the quality of the hole.
A third very important advantage with True Hole is that improved hole quality is delivered automatically, without any operator intervention. This means consistently good hole quality for a variety of thicknesses from gauge to 1 inch, with all parameters preset in the software. With the use of an auto gas console that enables automatic gas switching, the operator does not have to manually manipulate any settings, with consistent, high-quality output every time.
There are three patents that have been filed with the US patent office, which emphasizes the level of engineering and technology that has been incorporated into the development of True Hole technology. The first patent defines the use of one shield gas for contour cutting, switching to a second shield gas with a lower nitrogen content for the hole cutting. It is this process of gas switching and using a gas with a lower nitrogen content that virtually eliminates the hole taper so commonly associated with plasma-cut holes.
The second patent covers the hole cutting motion techniques that include specific cut speed and timing parameters that are important and contribute to reducing and biasing the ding to the outside of the hole. While the use of oxygen actually increased the size of the ding or divot, it is the combined motion techniques that minimize and move this protrusion to the outside of the hole. It is the combination of both of these patents working together that produces bolt-ready holes.
The third patent is a combination of the previous two patents, applying the True Hole technology techniques for multiple hole sizes and thicknesses within the nest, from gauge to 1 inch plate. One of the comments from end users was the inconsistency in hole quality from operator-to-operator, shift-to-shift, and site-to-site. Now with True Hole technology, this variability has been eliminated producing consistent hole quality for all specified holes.
The True Hole Technology begins by using an oxygen plasma/air shield gas to pierce directly in the center of the hole, automatically adjusting for kerf compensation without shifting the pierce point. The placement of this pierce point has a dramatic effect on the resultant shape of the hole. Once the pierce is complete, the automatic gas console automatically changes the process to an oxygen plasma/oxygen shield gas which is used to cut the hole.
As shown in the Figure, a semi-circle lead-in is applied, which minimizes the amount of excess material that contributes to the size of the ding or divot. The lead-in speed is also automatically set, based on plate thickness, hole size and amperage, and varies from the actual cutting speed. After the lead-in is complete, the speed is automatically increased to full cut speed in order to cut the outer circle of the hole. Towards the end of the cut, True Hole technology automatically begins to ramp down the current. Once the outer cut crosses the original semi-circle lead-in, the current is shut off completely while maintaining full torch motion. The optimum lead-out length is also automatically applied, which varies by hole size and plate thickness. The timing of the arc-shutdown, table motion, and table deceleration are all critical to the resultant quality of the hole. These automatic parameter settings combine to minimize the ding or divot and bias it towards the outside of the hole. As a last step, once the hole has completed cutting, the automatic gas console automatically switches back to an oxygen plasma/air shield gas for further contour cutting.
True Hole Technology has made great advancements with the quality of holes cut with plasma. However, cut quality is still dependent on the table, with table motion directly related to the roundness of the holes. It is important to discuss table motion with the original table manufacturers, to determine if True Hole Technology will bring the desired results on their specific table. Once a table manufacturer has been selected, the proper components must be specified in order to get True Hole Technology. A HyPerformance Auto Gas system is a pre-requisite, as True Hole Technology was developed for use only with this plasma system. A True Hole configured controller, torch height control, and nesting and process optimization software all need to be added, which the table manufacturer can help specify.
Hypertherm controllers, torch height controls, and ProNest 2010 are all configured for True Hole Technology and as well, some table manufacturers also have a license to embed the True Hole Technology motion techniques into their hardware and software. The best solution is to work directly with your table manufacturer to discuss the options. The best test to determine if True Hole will meet your cutting needs is to have a sample cut from the potential table in question. Once the sample is made, take note of the functionality of the hole. There should be a snug fit at both the top and bottom of the hole when a bolt or a gauge pin is inserted into the hole. This demonstrates the removal of taper and the minimization and bias of the ding or divot to the outside of the hole.
There are a few things to remember about True Hole Technology that are important considerations before you buy. The first is this technology is only applicable for mild steel plate, which covers the majority of cutting today. While hole quality on stainless steel is an opportunity for improvement, the use of an oxygen gas would not be acceptable. It is the switching of the shield gas to a lower nitrogen content gas such as oxygen that contributes to the elimination of taper that is so prevalent when cutting holes with plasma. The second thing to note is True Hole Technology was developed for gauge material up through and including 1 inch, with a hole diameter-to-plate thickness ratio of 2:1. At this time, there are no further plans to expand True Hole Technology above 1 inch; however, some nesting and optimization software packages have been able to provide some incremental improvements to hole quality on thicker plate. Make sure to work with your table manufacturer for best results.
As people have started using True Hole, they have expressed their delight with the overall improvements to hole quality. Several have been able to reduce and even eliminate all secondary operations, saving both time and money. Those who were using laser have been able to shift jobs over to plasma for improvements in productivity gains. Others have been able to bring more jobs in-house, adding more profit to their bottom line. Overall satisfaction with plasma hole cutting has been on the rise, due to the technology and engineering expertise built-in to True Hole Technology.
Tangential velocity on the surface of the tool or workpiece at the cutting interface. The formula for cutting speed (sfm) is tool diameter 5 0.26 5 spindle speed (rpm). The formula for feed per tooth (fpt) is table feed (ipm)/number of flutes/spindle speed (rpm). The formula for spindle speed (rpm) is cutting speed (sfm) 5 3.82/tool diameter. The formula for table feed (ipm) is feed per tooth (ftp) 5 number of tool flutes 5 spindle speed (rpm).
Width of cut left after a blade or tool makes a pass.
© Copyright 1995 - 2022. Cutting Tool Engineering. All rights reserved.
CTE Publications uses cookies to improve your experience and to analyze the use of our website. By accepting, you agree to the terms stated in our Privacy Policy
www.hypertherm.com needs to review the security of your connection before proceeding.
Did you know botnets can be used to shutdown popular websites?
Requests from malicious bots can pose as legitimate traffic. Occasionally, you may see this page while the site ensures that the connection is secure.
Performance & security by Cloudflare
www.hypertherm.com needs to review the security of your connection before proceeding.
Did you know some signs of bot malware on your computer are computer crashes, slow internet, and a slow computer?
Requests from malicious bots can pose as legitimate traffic. Occasionally, you may see this page while the site ensures that the connection is secure.
Performance & security by Cloudflare
Southern Fabricating Machinery Sales
Southern Fabricating Machinery Sales (SFMS) has been an expert in buying, selling, and brokering used machinery and used industrial equipment since the 1980's. We work in and with machine shops, tool dies, mold and fab shops just like yours, running the very machinery we now offer as solutions for your manufacturing needs!
© 2022 Southern Fabricating Machinery Sales, Inc. All Rights Reserved. | Privacy Policy
This website stores cookies on your computer. These cookies are used to collect information about how you interact with our website and allow us to remember you, in order to personalize your experience. To find out more about the cookies we use, see our Privacy Policy .
Posted By: Southern Fabricating Machinery Sales | Posted On: July 1, 2019
True-Hole Technology ® is one of the latest buzzwords circling around the plasma cutting community, but What is it? What does it do? How does it work, and most importantly, how do you know if you need it? In this article we will explain true hole technology and discuss the features and benefits of using it in your shop and on your parts.
What Is It? : True-Hole Technology ® is a trademarked reference to a technology by plasma manufacturer Hypertherm . Similar manufacturers such as Esab have a similar feature (Esab’s Precision Hole Technology ®). The technology developed provides for more detailed and defined holes with less taper and minimal lead-in/lead out marks. In today’s ever changing manufacturing climate, this technology moves Hi-Definition Plasma Cutting ever closer to the definition and preciseness of cutting on a laser cutting machine.
What Does it Do : This new technology produces significantly better hole cutting than previous models of plasma cutting systems were able to produce. Specifically when cutting small holes. In previous generations of plasma cutting power sources, fine or small holes where very problematic. The plasma stream performing the cutting was not defined enough to accurately cut small details leaving a rough finish and highly tapered edge on small details, like holes. Typically the limitation was 1/1 or in other words, a hole diameter that was at or less than the thickness of the plate from which it was being cut was impossible to cut cleanly enough to drop a gage pin through. These small details were then generally left out and machines in a separate drilling operation adding more time and more material handling to complete.
Step 1) A mixture of software programming and a capable controller control the critical lead in allowing for slower speeds and a radial lead-in, ramping up to faster cutting along with optimal power and gas flow/mix increases.
Step 2) An ‘auto-gas’ console controlling the mixture and flow of the cutting gasses switches between entry gas mixture to cuitting gas mixture automatically. Amperage is also increased to optimum cutting amperage.
Step 3) Gasses are again switched and power ramped down on an exit arc.
These three elements combined allow for better control of the plasma jet stream which in turn controls the washout and taper in a hole. These technologies, Tru-Hole and Precision Hole Technology is another feature available to Hi-Definition plasma machines and one that can take the efficiency of plasma cutting even closer to that of laser or even waterjet.
Do I Need It? Your application may or may not require “Tru-Hole Technology” as your parts may be sufficient if produced on a standard plasma cutting system. As with many other processes the more definition, accuracy and quality of cut we demand the more critical our setup, consumables, gasses, programming, material etc. These all lead to an increase in operational costs and a reduction in cutting speeds. You may find in your given application that standard plasma cutting works great for your specific situation and chasing Laser quality accuracy with Tru Hole or Fine Hole Technologies is simply not worth the added costs. However if your work is 50% or greater in the range of this technology you would be best suited to have it available.
You can read more about the Hypertherm technology, Tru-Hole® directly from their website HERE
You can read about Esab’s technology, Precision Hole from their website HERE .
At Southern Fabricating Machinery Sales, Inc. our team are experts not only in Plasma Cutting Technologies, but also the comparable shape cutting technologies Laser , Oxy-Fuel and Waterjet . We know how to help you select the right machine for your process, part, time and budget. Call us today at 813-444-4555 or visit us on the web at www.southernfabsales.com
You can learn more about Plasma Cutting, Lasers, Waterjets and other types of fabrication processes by visiting our Technical Resource Library HERE . If your in the market for a new Plasma Cutting System, we offer the latest in technologies available HERE
Electrical discharge machining (EDM) is a critical tool for many modern manufacturing applications that has evolved over decades of use. One commonly used type ...
Many of the durable items that surround us feature intricate designs and configurations that are made through metalworking and as we all know, metalworking ...
Welding has come a long way since the beginning of metal fabrication. Even with modern technology, it's changing all the time. Using robots to weld has been ...
Southern Fabricating Machinery Sales, Inc.
10417 South County Road 39 Lithia, FL 33547
Teen Handjob Webcam
Head Over Heels In Love
Glory Hole Videos