Through Penetration
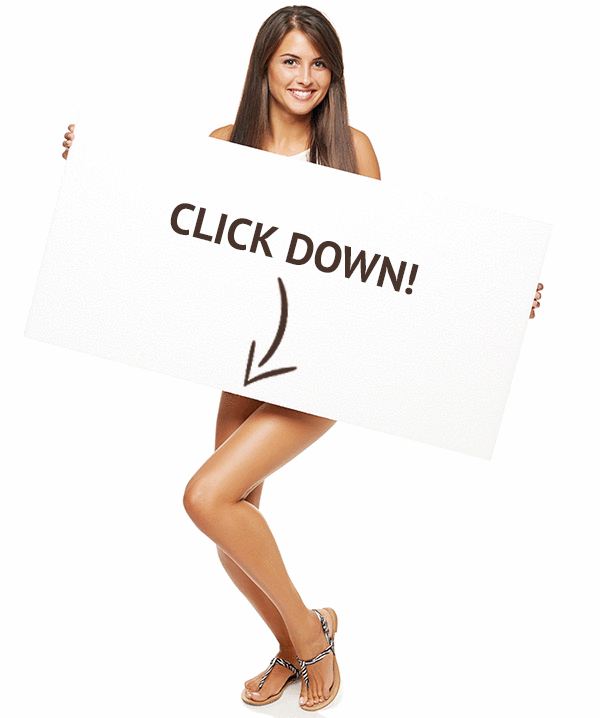
🔞 ALL INFORMATION CLICK HERE 👈🏻👈🏻👈🏻
Through Penetration
Search
search
close search
This website requires certain cookies to work and uses other cookies to help you have the best experience. By visiting this website, certain cookies have already been set, which you may delete and block. By closing this message or continuing to use our site, you agree to the use of cookies. Visit our updated privacy and cookie policy to learn more.
This Website Uses Cookies By closing this message or continuing to use our site, you agree to our cookie policy. Learn More
This website requires certain cookies to work and uses other cookies to help you have the best experience. By visiting this website, certain cookies have already been set, which you may delete and block. By closing this message or continuing to use our site, you agree to the use of cookies. Visit our updated privacy and cookie policy to learn more.
Search
search
close search
How do you feel about the push toward decarbonization and electrification in the plumbing and HVAC industries?
I’m for it – we need to get there as quickly as possible because it’s in the best interest of the planet and the PHVAC industry.
We need to get there, but the government is moving too fast. We need to slow down and ensure the grid can handle it.
It’s bad for the industry because it limits choices while raising costs for our clients.
Get our new eMagazine delivered to your inbox every month. Stay in the know on the latest plumbing, piping, hydronic and fire protection trends. SUBSCRIBE TODAY
Search
search
close search
Forty years ago, when I started practicing engineering, through penetration firestops were very simple. Once the opening through the fire barrier was made, and the pipe or other item was installed, the annular space was "stuffed" with a non-combustible material such as mineral wool, fiberglass, or heaven forbid, asbestos (this was before asbestos was known to be a carcinogen).
In 1975, a fire at the Browns Ferry Nuclear Plant demonstrated that it was not only important to seal penetrations to limit the spread of fire, but also to limit the spread of smoke. Previously used materials were found to be inadequate for this purpose. As a result of the fire, Dow Corning Corp. developed a silicone foam material which provided both a fire and smoke seal for penetrations. Subsequent to this initial development, a series of tests were developed for testing these materials in combination with various fire barrier constructions, resulting in the Underwriters Laboratories (UL) Fire Resistance Directory, containing 1,478 pages of through penetration firestop systems. Each system deals with a specific firestop material, penetrating element and construction system.
In existing construction, there may be little or no guidance from drawings. It is necessary to study the building and the local building code to determine the locations of the fire barriers. In multi-story buildings, each floor is generally separated by 1- or 2-hr. rated construction, although it could be greater in some cases. Shafts and stairs are generally separated by 2-hr. rated construction. Boiler rooms, incinerator rooms, storage rooms over 100 sq. ft., paint shops and maintenance shops will often be separated by 2-hr. rated construction. Enclosed corridors used for access to exits, separations between tenants and separations between dwelling units generally carry a 1-hr. rating, although in some cases these may be non-rated partitions in buildings which are provided with automatic sprinklers. Also, storage rooms under 100 sq. ft., trash chute access rooms, linen chute access rooms and laboratories are examples of rooms which may be separated by 1-hr. rated construction.
Institutional buildings such as hospitals and nursing homes have an additional requirement for smoke barriers to separate floors, so that patients can be moved to an area protected from smoke in the event of fire. These smoke barriers must also carry a 1-hr. fire resistance rating, so the penetrations through them must be protected with through penetration firestop systems.
One method that may be used, while not always accurate, is to look for labels on doors and frames that contain hourly ratings. Generally, the ratings of fire doors are as follows:
Both the 2000 Edition of the ICC International Building Code (IBC) and the 2003 Edition of the NFPA Building Construction and Safety Code require that penetrations through all fire barriers be protected with a through penetration firestop system having an F rating equal to the hourly rating of the assembly. NFPA includes the additional requirement that the F rating cannot be less than 1 hr. There is an exception in both codes that says where the penetrating items are 6" diameter maximum steel, copper or cast iron pipes, the annular spaces can be filled with grout to the full depth of the assembly. A T rating is not required for these assemblies because they are generally located above any combustible materials that could come in contact with the penetrating item.
For horizontal fire barriers (floors and floor/ceiling assemblies), both codes require additionally that the T rating of the through penetration firestop system has to be equal to the hourly rating of the assembly, except where the penetration is contained within a fire-rated wall or partition assembly. The additional T rating requirement is in recognition of the fact that many vertical pipes may come in contact with combustible materials that are on the floor of the areas where they are located. If it can be assured that there will be no combustibles near the piping, NFPA allows that the T rating requirement may be dropped.
Neither of the building codes call for an L Rating on smoke barriers at the present time. The only reference to a pressure differential is in the IBC, which requires the firestop system to be tested under a differential pressure of 0.01". The ASTM E 814 and UL 1479 standards require a 0.01" positive pressure as a minimum for all through penetration firestop system tests. This is done to assure that the system will withstand a fire pressure attempting to push the heat through it. It is typically more of an issue with non-metallic penetrating items where the fire could push through the burned off sections of piping.
With 1,478 pages of these systems in the UL Fire Resistance Directory, this appears to be a formidable task. UL has developed an elaborate system of identification for these through penetration firestop systems that will serve to make the search for a particular system to be used on a project a little less difficult. This system consists of a three-component designation that identifies the area in the directory where a particular application may be found. This designation consists of the following components:
A--Concrete floors with a minimum thickness < or = 5"
B--Concrete floors with a minimum thickness >5"
E--Floor-Ceiling assemblies consisting of concrete with membrane protection
J--Concrete or masonry walls with a minimum thickness < or = 8"
K--Concrete or masonry walls with a minimum thickness >8"
Therefore, a through penetration firestop system with the designation C-AJ has been tested for concrete floors and concrete or masonry walls with a thickness < or = 5" for floors and < or = 8" for walls.
1000-1999--Metallic pipe, conduit or tubing
2000-2999--Non-metallic pipe, conduit or tubing
4000-4999--Cable trays with electric cables
6000-6999--Miscellaneous electrical items, such as bus ducts
7000-7999--Miscellaneous mechanical penetrating items, including air ducts
8000-8999--Combinations of penetrating items, including any combination of items listed above
Figure 1 is a typical UL-listed through penetration firestop system. This system is listed under two UL designations:
--C-AJ 5021-F Rating-2 and 3 hr., T Rating-1/2 and 1 hr., L Rating-<1 CFM/sq. ft.
--C-AJ-5087-F Rating-2 hr., T Rating-1 hr.
While the above detail represents the firestop system, it is necessary to review the full UL listing to verify that all of the details of the system are in compliance. A review of the UL listing for these systems indicates that the main difference between the two systems is that the C-AJ-5087 system can be used with a sleeved opening up to 30" in diameter, while the C-AJ-5021 system is limited to a maximum 8" diameter opening. These systems illustrate a major problem facing designers in finding systems for floor penetrations using metallic pipes. It is difficult to get T Ratings that will equal the F Rating. This is because the metal transmits heat through the fire barrier at a greater rate than either the fire barrier construction or the firestop sealant, resulting in less time to reach the 325 degrees F maximum temperature. Generally, it will be necessary to use insulation on the piping, and you will still probably end up with an F rating greater than needed for the particular fire barrier. This is generally not as great a problem when using non-metallic piping because of the lower heat transmission rate.
Remember the steps in finding the firestop sealant needed for a particular project:
2. Determine whether you will be penetrating floors, walls or both.
3. Determine the F, T and L Ratings you need or want to achieve.
4. Determine the construction details of the fire barrier.
5. Check the UL Fire Resistance Directory for a system that will meet your needs.
Join us for the only event focused on plumbing system design pros and engineers. Learn new skills, earn CEUs, and get solutions while you discover new products, technologies and services from 100’s of global exhibitors.
Copyright ©2022. All Rights Reserved BNP Media.
Design, CMS, Hosting & Web Development :: ePublishing
Through Penetration Firestop at left; Membrane Penetration Firestop at right
Fire Resistive Joint at left; Perimeter Barrier at right
Related Articles
Thermal & Moisture Protection Industry Resources
Intumescent Paint, Fireproofing, and Firestopping
Spray Applied Fireproofing (SFRM)
Newest Articles
Steep Sloped Roofing Systems
Fabrics and Textiles for Interiors and Furniture
Best LEED Green Associate Exam Prep Materials
Circadian Lighting
WELL AP Study Guide Reviews
Follow Archtoolbox
Twitter
LinkedIn
Architecture News Feed
Archlinks Architecture News
Copyright © 2022 Archtoolbox. All rights reserved. Archtoolbox is a Trademark of Aggregate Digital LLC.
Penetration firestopping systems and fire resistive joint systems are a passive means of fire protection. There is no movement or activation required. These passive systems are mainly used to compartmentalize a fire and keep it from spreading for a period of time long enough that occupants can evacuate the building and so firefighters can perform initial lifesaving tasks.
Modern buildings are full of various services that travel from room to room throughout a building. Electrical cables, data cables, and plumbing pipes are few of the items that pass through walls as they travel through a building. Engineers try to avoid having these services pass through fire and smoke barriers, but it is usually impossible. When a service must pass through a rated wall, penetration firestop systems are used to ensure the wall rating is maintined.
There are two types of penetration firestopping:
Through Penetration Firestop systems are those that protect penetrations that pass all the way through the barrier, whether it is a wall or a floor. In general, both sides of the penetration are sealed with the proper system.
Membrane Penetration Firestop systems protect penetrations that pass through part of the barrier, but not the entire barrier. Some examples are outlet boxes, sink drains, or conduit that leads from a back-box to the space above the ceiling. Membrane penetrations use the same products and similar details to protect the opening, but there are exceptions that allow them to be unprotected if the opening is small. Another way of saying this is that there are limits to the size and density of unprotected membrane penetrations within a rated separation.
Fire resistive joint systems protect the joints or spaces installed within or between fire rated assemblies. The most common example of a fire resistive joint system is where the wall of a rated space meets the deck of the rated floor above. You will notice that these joints are protected with fire stopping, which tends to be a red colored sealant that spans between the two barriers.
The space between a rated floor slab and the inside face of a curtain wall system is a special case that is called a perimeter barrier. This is an important joint because the wall system requires a wider space than other wall systems and there could be significant movement in the joint, which could allow fire and smoke to pass through easily. The current standard used to test these systems is ASTM E2307: Standard Test Method for Determining Fire Resistance of Perimeter Fire Barrier Systems Using Intermediate-Scale, Multi-story Test Apparatus.
This article is about firestop systems, which are specifically designed products that are combined into an assembly that is tested and confirmed to stop the spread of fire or smoke.
On the other hand, fireblocking is made from generic building materials (wood, mineral wool insulation, gypsum wall board, etc.) and is intended to prevent the spread of fire and smoke within the cavities of a building. In residential construction, where fireblocking is used most often, fire can spread in floor or wall cavities very easily so fireblocking is installed.
It is important to note that fireblocking is not a tested assembly and there are no referenced standards; however, some jurisdictions require fireblocks to meet ASTM E-136: Test Method for Behavior of Materials in a Vertical Tube Furnace at 750˚C .
The F-Rating for a firestop system indicates the number of hours that the assembly will prevent flames from passing through to the other side of the barrier.
A firestop system’s T-Rating indicates the number of hours until the ambient temperature on the non-fire side of the barrier rises by 325-degrees Fahrenheit when the protective is subjected to fire.
Many firestopping systems are tested for both thermal and flame resistance. In this case, the design will have an FT-Rating. The FT-Rating is the number of hours that a system will prevent the passage of flame as well as preventing a 325-degree-Fahrenheit temperature rise – it will always be the lesser of the F and T Ratings. For instance, if a system receives a 1 hour T-Rating and a 2 hour F-Rating, the system will receive an FT-Rating of 1 hour.
The L-Rating for a firestop system indicates the amount of air that can pass through a protective. The number represents the leakage rate in cubic-feet-per-minute. The L-Rating is an optional test under ANSI/UL 1479 ( Fire Tests of Through-Penetration Firestops ) so assemblies may not receive an L-Rating. Since many systems are not tested for leakage, it is important to know if you need a system to have an L-Rating.
In general, the architect’s specifications provide requirements and it is the responsibility of the installing contractor to ensure that the correct system is selected and properly installed. However, there are some things for architects to think about when they are observing construction.
The annular space is the area between the penetrating object and the barrier construction. Each firestop system has limitations for the annular space so if an architect or inspector observes a condition where the annular space is excessive, then further investigation is required.
Load bearing fire stopping or joint systems are a special case scenario that needs to be reviewed with a certified installer or engineer. Most fire stop manufacturers have load bearing assemblies, but there are strict guidelines for proper usage and installation.
Understanding the amount of movement, especially in fire resistive joint systems, is critical for proper protection. If you anticipate moderate or excessive movement of a joint it is important to have the system reviewed by a fire stopping engineer.
The International Building Code (IBC) requires that fire walls, fire barriers, fire partitions, smoke barriers, and smoke partitions be permanently identified with stenciled lettering or other labels. However, penetrations are not required to be identified or labeled.
While labels are not required, many installers provide them and some building managers require them. The labels are specific to each manufacturer, but they typically include the installation date, the installer’s name, the detail used, and any engineering judgments that apply. The label will identify the penetration as fire resistance rated fire stopping and indicate that tampering with it can affect the system performance.
***Always check your local codes to confirm the testing procedures required. The following information is general in nature and must be confirmed with the local building codes and the Authority Having Jurisdiction.
Through Penetration Firestop systems are usually tested according ASTM E814: Fire Tests of Through Penetration Fire Stops . The firestop system shall have an F-rating equal to or more than the rating of the wall penetrated. Floor penetrations shall have an F-rating and T-Rating of at least an hour, but not less than the fire resistance rating of the floor.
Fire resistive joint systems are generally tested to meet UL 2079: Tests for Fire Resistance of Building Joint Systems . The joint systems shall have a tested rating of not less than that of the required rating for the assembly they are a part of.
As we stated above, perimeter barriers are tested using ASTM E2307: Standard Test Method for Determining Fire Resistance of Perimeter Fire Barrier Systems Using Intermediate-Scale, Multi-story Test Apparatus .
In many cases, the various tested firestop systems are not applicable to particular field conditions. If a tested system does not exist, an engineering judgment can be obtained. The engineering judgment, often referred to as an EJ, is prepared by a manufacturer or engineer and provides a new detail that hasn’t been tested, but that is judged to be effective based on the engineer’s knowledge and proper interpolation of other tested systems.
It is critical that these EJs be prepared by an experienced engineer. The EJ will include a sketch of the detail to allow proper installation and will provide some language about where it is appropriate for use.
Most manufacturers of firestop systems have developed databases that allow building managers to keep detailed records for the many penetrations and joints that are within their facilities. These systems allow a facility manager to maintain code compliance information and manage maintenance and installations. The systems are usually web-based so that information can be pulled up on
Overwatch 12
Girls Peeing Groups
Outdoor Activities