Робот, инфузия, композиты: три предприятия и большие перспективы
Объединенная Авиастроительная КорпорацияК 15-летию АО «АэроКомпозит» мы побывали на трех площадках в Москве, Казани и Ульяновске. Если сказать простыми словами, то Москва – это центр компетенций, в непосредственной близости от основного своего заказчика – ПАО «Яковлев». Это, скажем так, альма матер авиационного композита. Тут начался путь освоения и внедрения в гражданскую авиаотрасль композитных материалов. Ульяновск – это инфузионная технология выкладки композитов. Казань – автоклавная. Все три площадки со своим характером и со своими амбициозными задачами.
Предлагаем вам репортаж из Казани от первого лица и свежим взглядом – о композитах, перспективах и инновациях.
КАПО-Композит
Приезжаем в Казань, снежно. Погода настраивает на новогодне-волшебное настроение. И не зря. Нас ждет настоящее волшебство. Переступив порог КАПО-Композит мы попадаем в стерильный мир композитного производства. На сравнительно небольшой площади творятся чудеса. О них нам рассказал Дмитрий Королев, директор по производству.
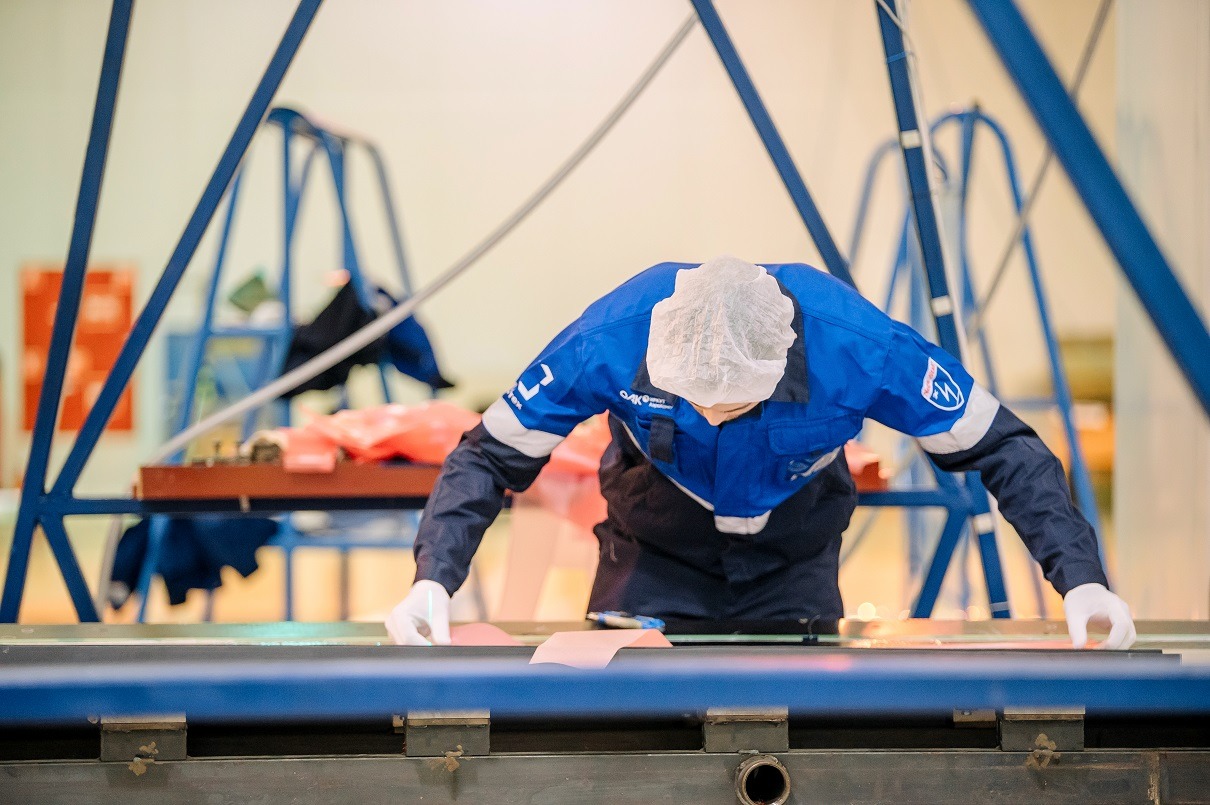
А еще мы отметили необычайную молодость коллектива. Энергия, позитив и динамика. Движение. Планы. Мы не заметили, как прошел целый день. Средний возраст сотрудников - 36 лет. Численность менее 500 человек, может быть поэтому ощущается как семья. Сами растят себе кадры - привлекают молодежь, обучают, подбирают наставников.
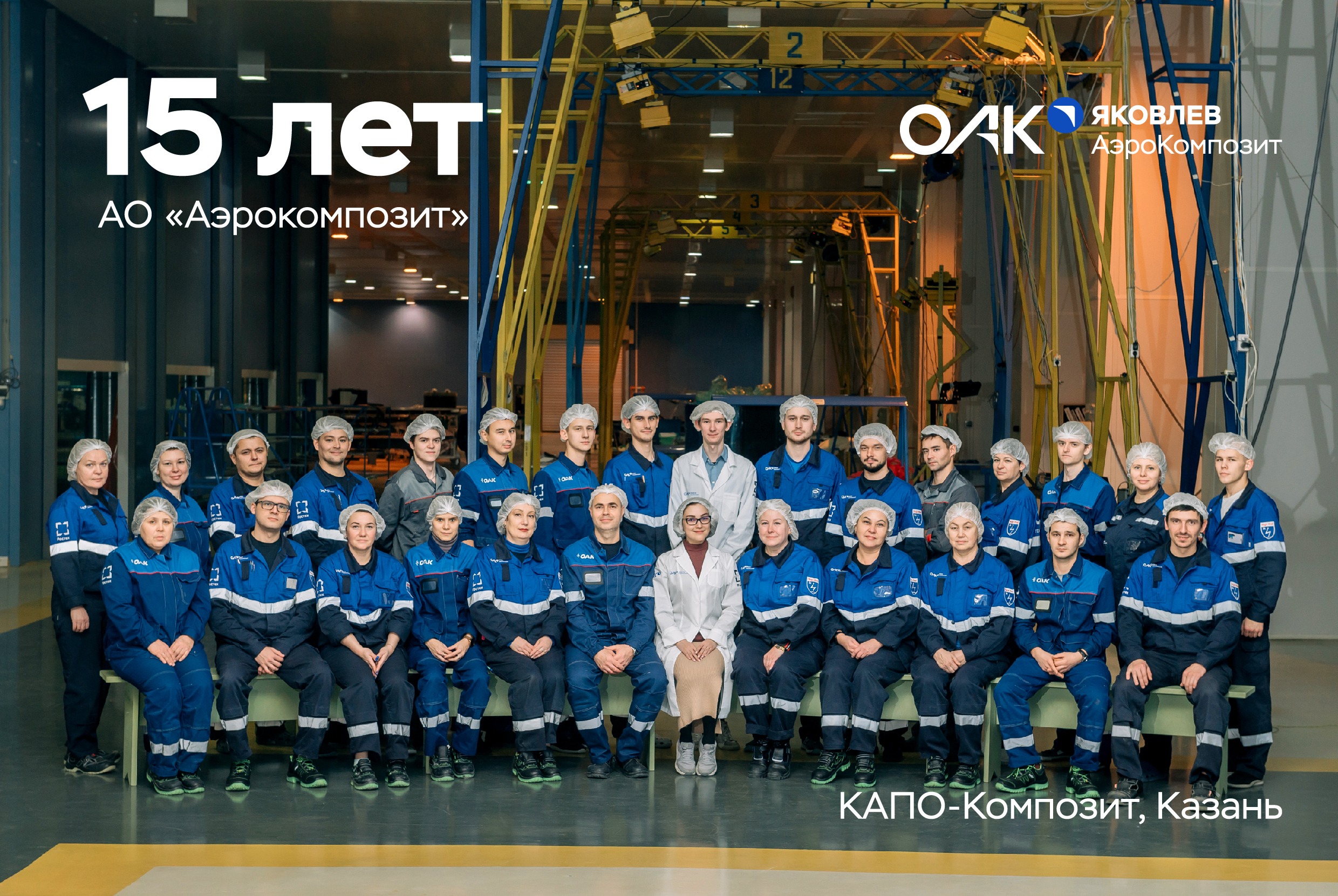
Мы надеваем специальные халаты, бахилы и шапочки, чтобы пройти внутрь. К нам присоединяется Дмитрий Владимирович Королев, и вместе с ним мы исследуем завод. Он рассказывает о сложных технологиях так просто, что начинает казаться будто мы сами можем с легкостью присоединиться к коллективу. Но магия композитного производства сложнее, намного сложнее.
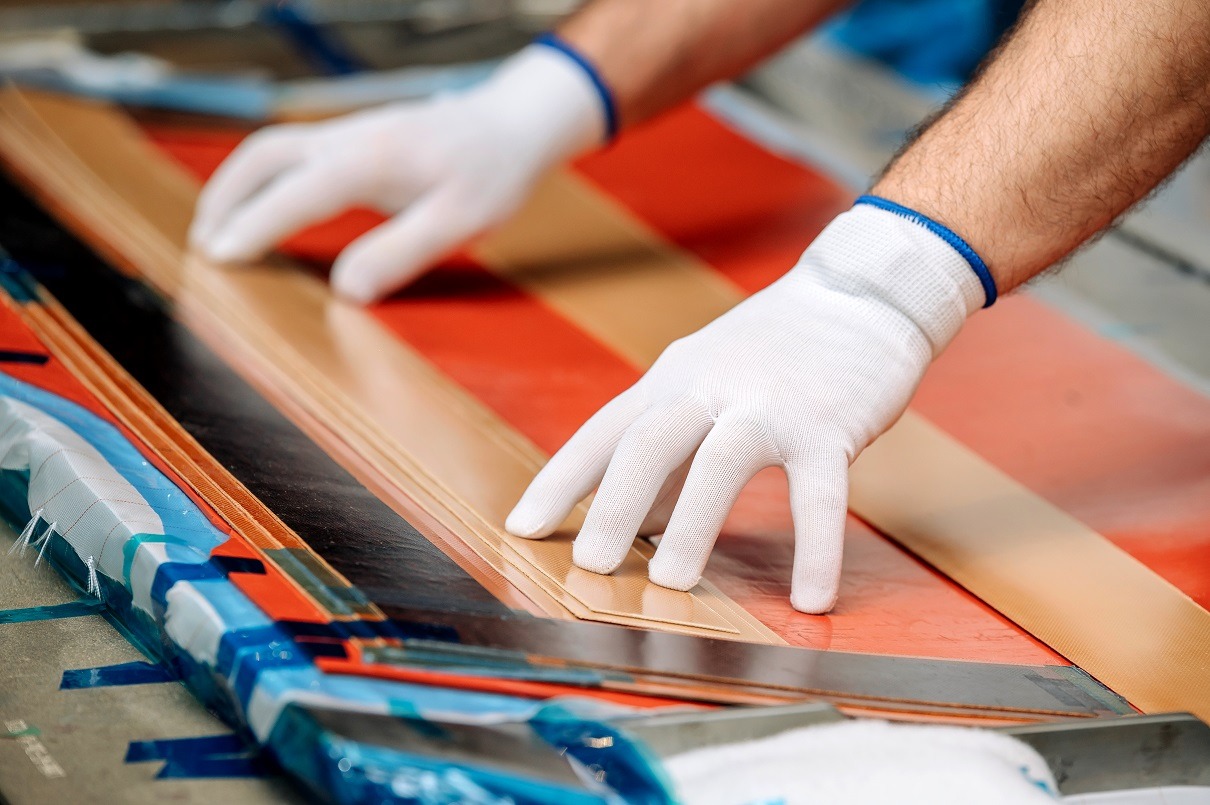
Дмитрий Владимирович рассказывает:
Композитное производство- постоянное поддержание температуры и влажности, и 8 класс чистоты с соответствии ГОСТ. Предприятие изначально строилось по принципу производство 21 века, мы ушли от механического ручного труда по раскрою материалов и его детальной подгонки во время ручной выкладки. На это уходило довольно много времени, и не экономично в части материалоемкости. Раскрой производим на автоматизированных центрах, по программе. Далее раскроенный материал поступает под лазерные проекционные системы, которые подсвечивают по заданной программе каждый слой материала. Теперь не нужно делать подрезки, подгонки. Направления слоев, укладка и номер слоев промаркированы. Остается только снять подложку и выложить слой. Это положительно сказалось на качестве и скорости выполняемой работы.
Самый главный враг композита – это поры воздуха внутри материала и посторонние включения они могут вызвать зону непроклея материала и именно поэтому на производстве стерильная чистота, контроль за спецодеждой строжайший.
В процессе выкладки есть детали относительно простые, например, панели и лючки крыла, они могут быть как монолитные, так и с сотовым заполнителем.
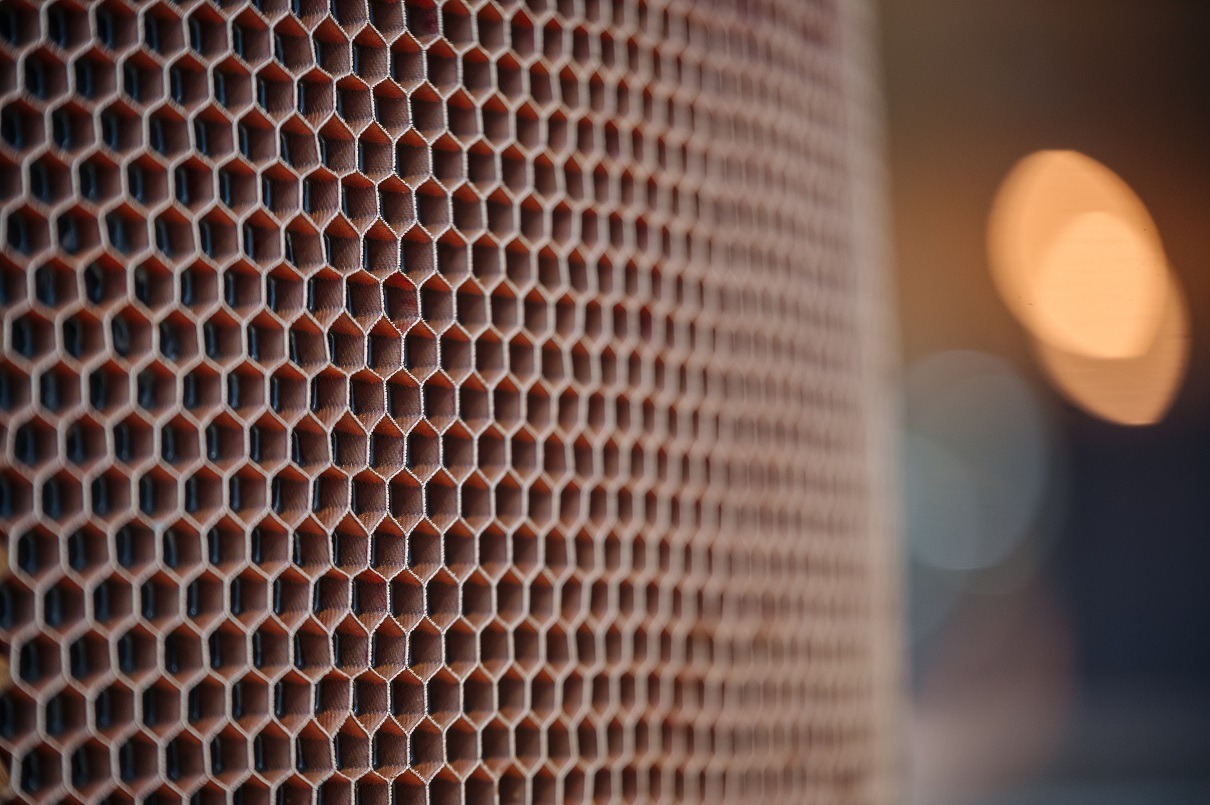
Есть агрегаты более сложной конструкции, например, малые агрегаты механизации крыла – интерцепторы, воздушные тормоза. Это детали сложной интегральной конструкции, и изготавливаются из нескольких отвержденных углепластиковых деталей, и слоев-полуфабрикатов из неотвержденного углепластика играющих роль соединительных элементов, которые отверждаются в едином цикле формования - одностадийное формование.
Одностадийное формование – это одна из наших особенностей. Традиционно существует двустадийное формование. Сначала формуют нижнюю обшивку, после чего подгоняют сотовый заполнитель, укладывают предварительно отвержденные детали диафрагму, лонжерон и формуют второй раз. Мы же это делаем быстрее – за один раз. Но дело не только в скорости, но и экономичности процесса.
На данный момент осваиваем изготовление стрингерных панелей для изготовления хвостового оперения из углеродной ленты. Полностью перешли на отечественные аналоги по используемым материалам.
Что касается оснастки для формования, то проектирование и изготовлением занимаемся самостоятельно. Вся крупногабаритная оснастка – композитная и изготовленная собственными силами.
У нас несколько автоклавов, если кратко, то температуры формования до 200 градусов, при среднем давлении 6 атмосфер.
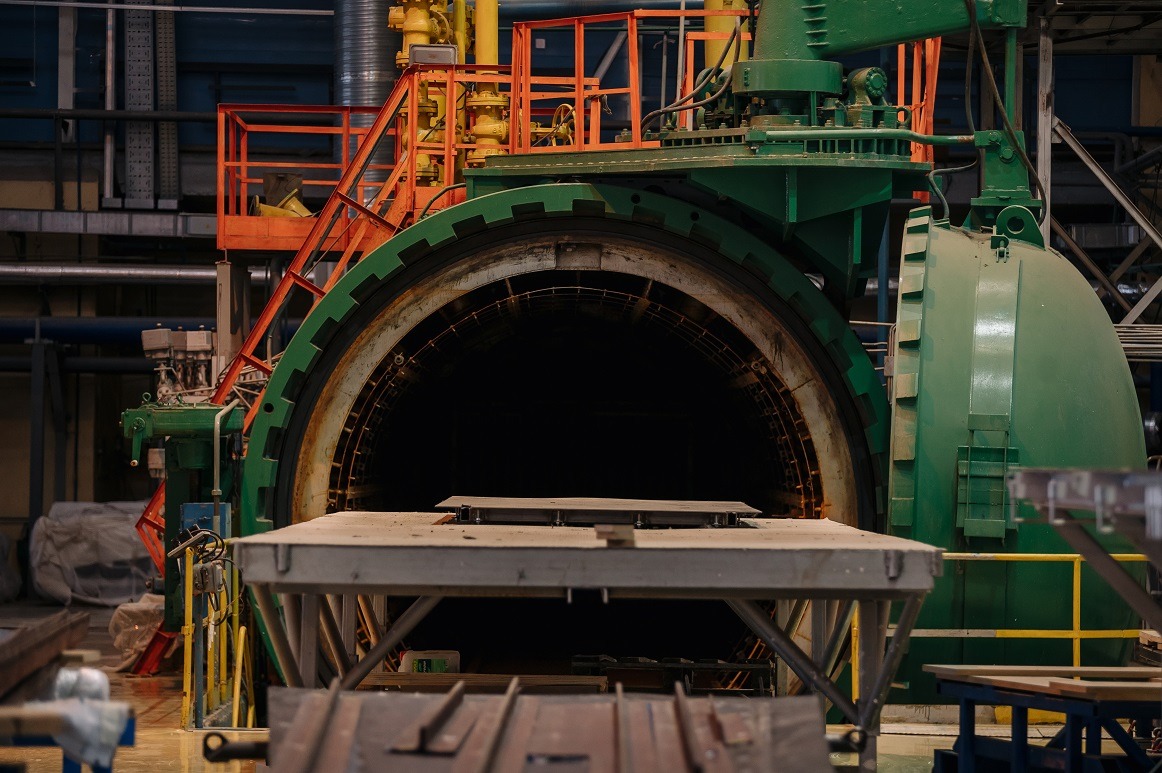
Далее отвержденная деталь попадает на механообрабатывающее производство. Где производим обработку по контуру в номинал и проявляем направляющие отверстия для сборки.
Для «Аэрокомпозит-Ульяновск» мы делаем большую номенклатуру – порядка 250 наименований. (Остальная номенклатура уже под наше собственное изготовление – под изготовление малых агрегатов и всей механизации крыла и хвостового оперения).
Еще одна интересная инновация уже на механической обработке – «мягкий» стол. Сейчас он в тестовой эксплуатации. Его использование позволит уйти от использования оснастки. Деталь выставляется на присоски, и обработка будет производиться без каких-либо приспособлений по заданной программе.
Как контролируется изделие из композита?
В чистой комнате параллельно с изготовлением детали изготавливаются плоские образцы, панели- спутники, которые поступают на испытания. Образец из той же партии, произведенный тем же сотрудником, прошедший на той же линии автоклава, даже располагается на той же оснастке. Эти образцы проходят физические и химические испытания, неразрушающий и ультразвуковой контроль. Данные образцы хранятся до списания воздушного судна. Они подтверждают качество материала и изготовления детали.
Проверка самих деталей проходит в центральной заводской лаборатории, как с помощью роботизированной системы, так и вручную. Если очень обобщенно и не вникая в подробности то, процесс чем-то похож на знакомое нам УЗИ.
Качество изделия зависит от чистоты производства, от технологии производства и ответственности сотрудников, выполняющих работу. Например, соты могут не склеиться, не проклей слоев в сложных углах, натяжение препрега. Даже руками без перчаток нельзя прикасаться до изделия – может отразиться на приклейке слоев. Приходится быть очень внимательными.
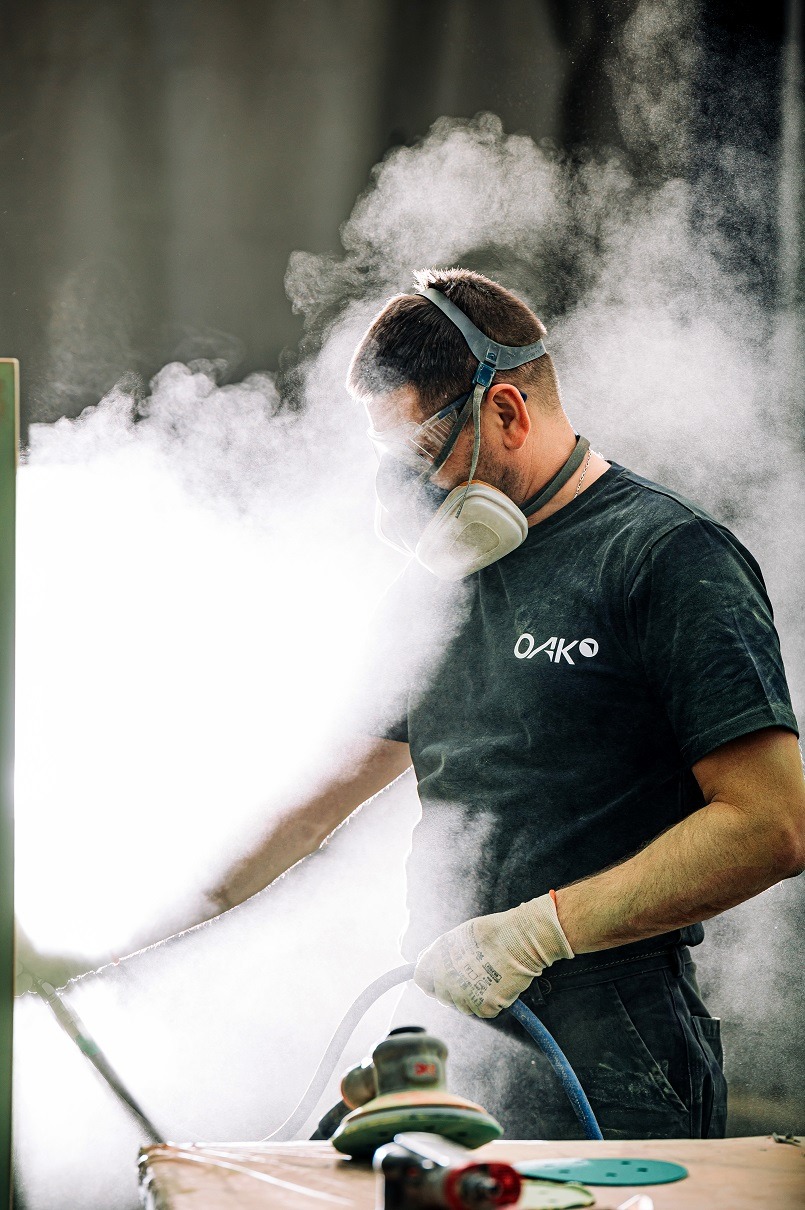
В самом конце на детали наносят лакокрасочное покрытие. Кстати, композит сложнее красить, чем металл. Структура у него пористая, ворсистость.
И финальный штрих – агрегатно-сборочное производство.
У нас стоят современные стапеля, разработанные нашими конструкторами. Предприятие за последний год проделало огромную работу по подготовке производства к серийному выпуску продукции, а также с учетом новых объемов таких как изготовление хвостового оперения МС-21. Проработали потоки производства, осуществили перестановку оборудования, теперь в одной зоне изготавливается вся механизация крыла МС-21 (закрылки, элероны, внутренние\внешние, малые агрегаты). Плюс тут же стоят стапеля под механизацию Суперджет-100 (закрылки, элероны, рули).
Напротив зона где, располагаются мощности под сборку киля стабилизатора МС-21, здесь же разместили рули высоты, руль направления – полностью весь хвост самолета в одном месте.
Не так давно был замечательный первый опыт стыковки киля стабилизатора МС-21. Все прошло отлично.
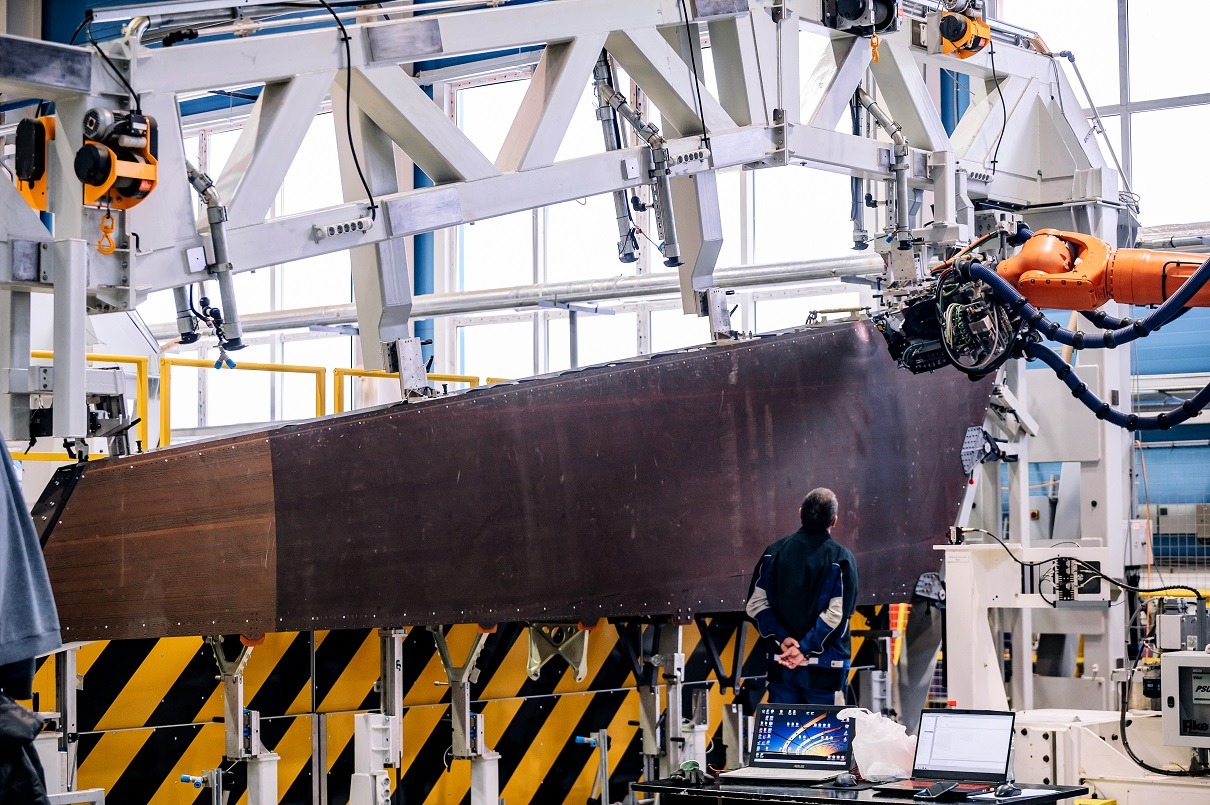
Вместе с Дмитрием мы поочередно прошлись по всему технологическому циклу композитного изделия на заводе. На всех участках кипит работа.
- КАПО-Композит – это замкнутое производство, полный цикл изготовления агрегатов из композитов.
Наши два основных производства – композитное и агрегатно-сборочное. Тут больше всего задействовано сотрудников. Остальное в большей степени автоматизировано с помощью оборудования ЧПУ.
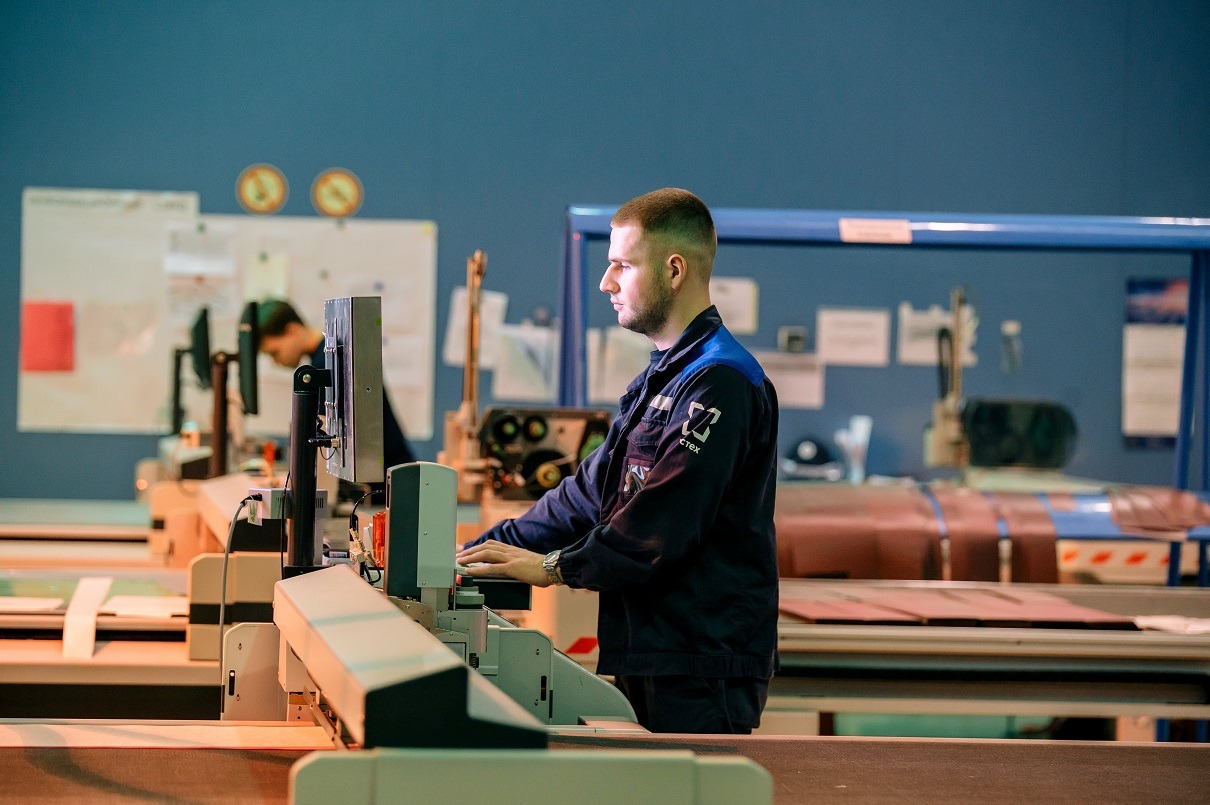
Мы гордимся своей чистой комнатой. Поддерживаем высокий класс чистоты и организации производства в ней, используем оборудование по максимуму – лазерно-проекционные системы, раскройные центры и автоклав.
Агрегатной сборкой никого не удивишь сейчас, она есть на каждом авиационном предприятии, мы отличаемся от других предприятий тем, что доля ПКМ в наших агрегатах до 80%, и это тянет за собой новые методы сборки и технологии, а так же использование специального инструмента.
В планах построить цех подготовки производства, в том числе и для хранения оснастки. Представьте: каждая деталь самолета - это своя оснастка. Например, номенклатура на один самолетокомплект МС-21 и Суперджет-100 - это 800-900 наименований. Одна оснастка механической обработки под панели закрылков состоит их трех отдельных двухметровых элементов.
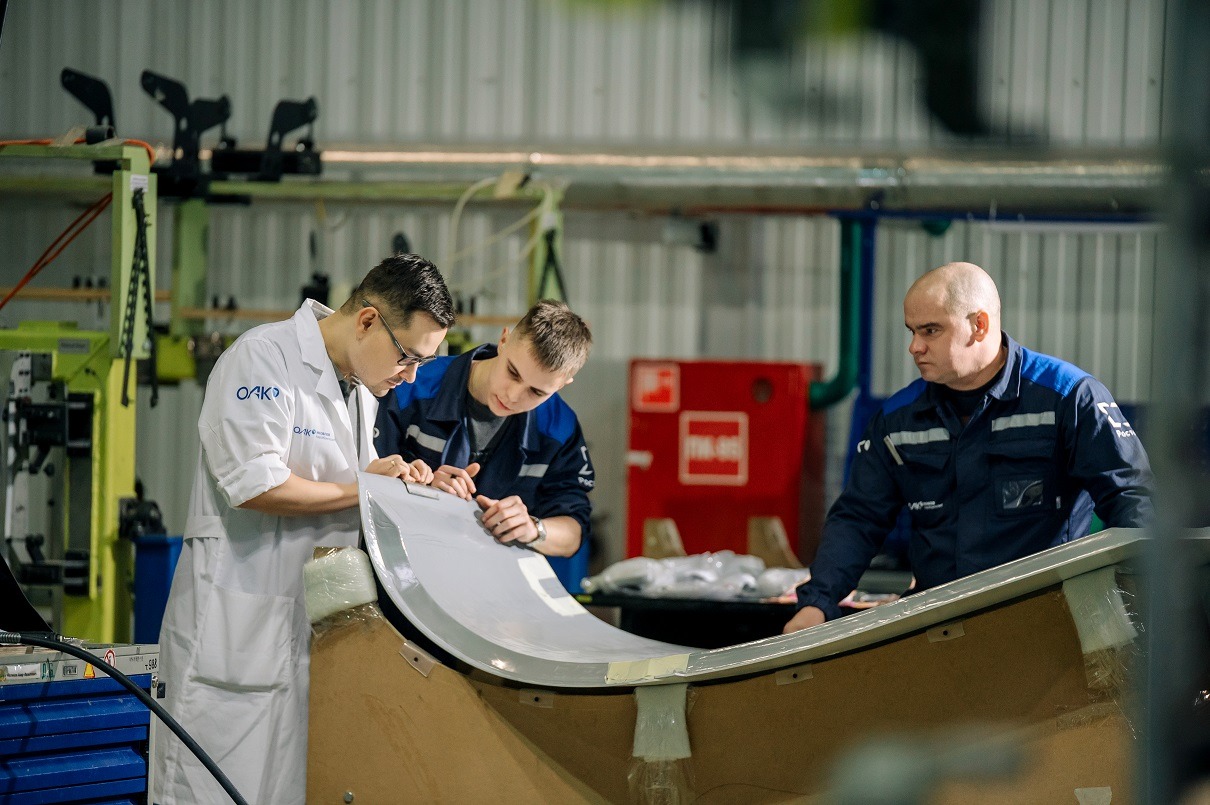
Пожалуй, основной сдерживающий нас фактор сейчас – это площадь. Задача предприятия – выпускать 36 самолетокомплектов в год. Мы уже прошли программу подготовки на 18 самолетокомплектов, сейчас выходим на 36. Так что планы – грандиозные!