Галерея 3230162
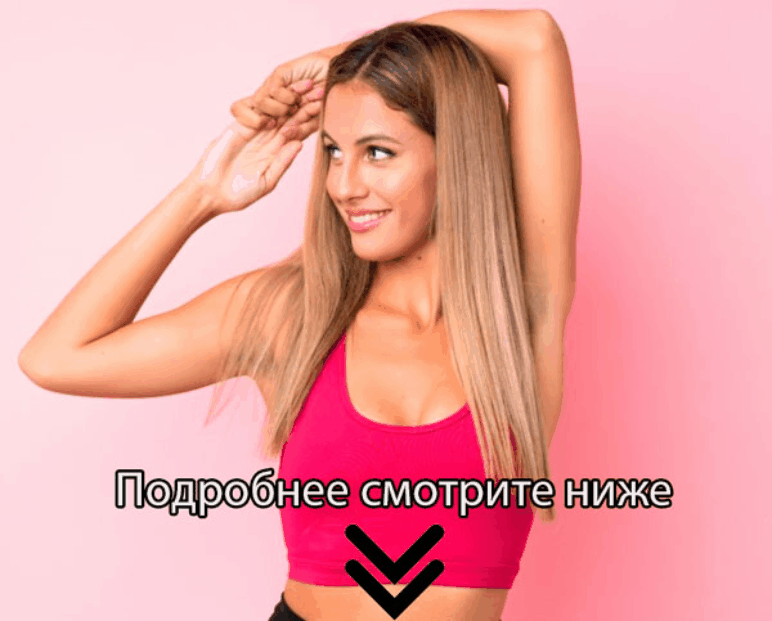
Галерея 3230162
Jan. 18, 1966 A, E GlLCHRlS-f 3,23,162
ELECIRGPAINTING PROCESS AND PAINT BINDER CONCENTRATE COMPOSITION THEREFOR Filed Aug. 14, 1965 United States Patent O 3,230,162 ELECTROPAINTING PROCESS AND PAlNT BINDER CNCENTRATE COMPOSITION THEREFR Allan E. Gilchrist, Fairview Park, Ohio, assignor, by
mesne assignments, to Ford Motor Company, Dearborn, Mich., a corporation of Delaware Filed Aug. 14, 1963, Ser. No. 304,297 53 Claims. (Cl. 204-181) This application is a continuation-in-part of my copending U.S. Patent Application Serial Number 249,812, filed January 7, 1963, now abandoned which in turn is a continuation-in-part of my copending US. Patent applications Serial Numbers: 132,303, filed August 18, 1961, now abandoned; 183,024, filed March 28, 1962, now abandoned; 186,320, filed April l0, i962; 186,- 496, filed April l0, 1962, now abandoned; 202,691, filed lune l5, 1962, now abandoned; and 218,575, filed August 22, 1962, now abandoned. The disclosures of these copending applications are incorporated herein by reference.
Advantages of my invention over prior practices include operating stability of the painting bath and paint binder compositions therein, even deposition of the paint film, simplicity of operating control, good paint coating into crevices and around corners, deposition in a selflimiting thickness, and resistance of the deposited film to condensed vapor washing prior to and during ultimate cure, as, for example, by baking.
Broadly, my process is an improvement for electrocoat-ing an anode in an electrical circuit comprising a bath of aqueous medium in electric contact with an anode and a cathode. In one aspect the improvement comprises dispersing in said bath a film-forming paint binder containing a polycarboxylic acid resin at least partially neutralized with water soluble amino compound, said polycarboxylic acid resin having electrical equivalent weight between about 1,000 and about 20,000, acid number between about 30 and about 300, and, in said bath, exhibiting anionic polyelectrolyte behavior as indicated by its deposition on said anode substantially directly proportional with the electric current being passed through said bath; passing direct current through said circuit to a maximum potential of about 50 to about 500 volts, thereby causing a iilm containing said resin to electrodeposit on said anode; withdrawing the resulting coated anode from said bath; and thereafter curing said film.
A further aspect of this invention deals with maintaining such coating operations over an extended period wherein said polycarboxylic acid resin is depleted from the bath and an amino compound reserve accumulates in the bath. A supplemental quantity of said polycarboxylic acid resin is added to the bath gradually, this supplemental quantity being sufiicient to maintain bath pH below about 8.4. The supplemental quantity added at any time is, of course, suificiently small to preserve the anionic polyelectrolyte behavior of the polycarboxylic acid resin in the bath.
A further aspect of this invention is an improved filmforming organic resin paint binder concentrate composition adapted for dispersing in an aqueous electrocoating bath containing suiiicient additional water soluble amino compound to impart anionic polyelectrolyte behavior in said bath to resin in said binder concentrate composition. The binder concentrate composition comprises about 50-95% by weight of polycarboxylic acid resin having electrical equivalent weight between about 1,000 and 20,000 and an acid number between about 30 and about 300; about 1-l0% vof water soluble amino compound based on the weight of said polycarboxylic acid resin in said composition; and the balance water. These perice centages are given on a pigment and mineral filler-free basis.
A further aspect of this invention is the electrical deposition of an enduring (as opposed to fugitive after cure) paint film on an anode by dispersing with water soluble amino compound film-forming polycarboxylic acid anionic polyelectrolyte in an aqueous bath as the essential and fundamental part of the paint binder, which polyelectrolyte undergoes conversion of sufficient of its ionic sites into hydrogen form to render the polyelectrolyte substantially water insoluble from its amino-dispersed form in the bath upon reaching the electricallycharged anode and coalesces there to apply a paint deposit substantially uniform in thickness. Such polyelectrolyte can make up the entire resinous binder fraction of the paint, or it can be extended with minor proportions, on a total resin basis, lof extender resins such as phenolic resins, hydrocarbon resins, and/or a latex not exhibiting such polyelectrolyte properties, provided, however, such proportion is restricted suiiic-iently so as not to mask the electrical migration characteristics of the polyelectrolyte resin binder, the fundamental and essential binder constituent for this operation. The electrical specific resistance of the polyelectro-lyte resin when it is dispersed in the bath is low, and upon this conversion on the anode the resin forms a film of very high specific resistance.
The drawing is a cross-sectional elevation of apparatus useful for conducting my coating process and simultaneously electrodialyzing Water soluble amino cornpound accumulations from an anode zone.. This apparatus and its operation is more fully described in an example following.
In this application painting by electrodeposition is meant to include the deposition of finely ground pigment and/ or filler in the binder, the deposition of binder without pigment and/or filler or having very little of same, but which can be tinted if desired, and the deposition of other water reducible surface coating compositions containing the binder which might be considered to be broadly analogous to enamel, varnish, or lacquer bases, and the coating material for such deposition is termed a paint Thus, the binder, which is converted to a water-resistant film by the electrodeposition and ultimately converted to a durable film resistant to conventional service conditions by final curing, can be all or virtually all that is to be deposited to form the film, or it can be a vehicle for pigmentary and/ or mineral filler material or even other resins on which it exerts the desired action for depositing the lm. It can, in some instances, be reduced with compatible organic solvents such as nonionic liquids which are fugitive on curing of the resulting film. When pigments and/or fillers are used, it is advantageous that water soluble salts in them, such as potassium or sodium salts, are very low and preferably absent so that electrical resistance of the bath and fil-m deposit is not subject to uncontrolled variation, and that the primary control of electrical conductance in the operation is by means of the binder resin and neutralizing amino compound dispersed in the bath.
In some cases as indicated expressly hereafter, my at least partially neutralized resin appears to go into clear solution in the aqueous bath; in other cases some of the resin appears to be dispersed in the bath in a haze of particles of extreme fineness, a maximum resin particle size present being estimated at not more than about 500 millimicrons. In these latter instances I have often been able to apparently dissolve these dispersed particles into a clear aqueous bath solution by adding additional water soluble amino compound to the bath.
At any rate, the at least partially neutralized dispersed polycarboxylic acid resins in my baths exhibit typical anionic `solute behavior with respect to migration to the anode in the electrical eld used because this migration for a particular resin binder in my operation varies substantially directly with the amperage through the bath. In other words, when allowance is made for the electric current used to -drive to the cathode varying concentrations of amino material present in excess of the minimum needed to impart the polyelectrolyte behavior, the coulombs of electricity used per gram of a particular resin binder deposited is substantially independent of voltage.
For practical purposes the nal electrodeposited lm does not appear to exhibit porosity and the thicknes builds up rapidly to between about l and about 100 microns (in the absence of loading the bath with a very high proportion of electrically-conductive pigments such as metal powders, graphite, or the like) to virtually if not completely shut off current at a particular selected maximum voltage. This is in contrast to aqueous latex and similar water-reducible dispersions heretofore electrically deposited. When such prior art dispersions are subjected to the same sort of electrical environment as mine, they deposit films which are of fairly high electrical conductance and continue to build up in thickness instead of being self-terminating for a particular voltage, particle migration to the anode will vary substantially with voltage, and the resulting films tend to coat the anode thickest at points where the voltage is highest, e.g., at edges and corners, and are not especially uniform in thickness like the films which can be laid down by my process.
Accordingly, whether these polycarboxylic acid resin binders when at least partially neutralized with water soluble amino compound are in true aqueous solution, or apparent solution, or in ultrane aqueous dispersion in the bath, they can be typified as polyelectrolytes in aqueous dispersion. They show migration in the bath with respect to the electric current characteristic of current-carrying anions in an aqueous solution and other solution properties, and therefore I consider them as solutes with respect to their critical operative action, which solutes coprecipitate on the anode with suspended resin, pigment, and other bath-insoluble materials. The resin migrates to an anode With respect to current put through the bath much as do metal cations to a cathode in an electroplating bath and is deposited by Faradic current, which is the dominating electrical phenomenon in the operation.
The especially useful polycarboxylic acid resins for my binders have an electrical equivalent weight between about 1,000 and about 20,000 and preferably between about 1,000 and about 2,000 for ease of dispersion and eiciency of operation. These resins disperse eiectively in the painting bath for my operation when partially to fully neutralized (with respect to acid number) with Water soluble amino compound and convert from a uent material to a highly adherent, comparatively immobile film when deposited on a vertical surface by my process. At electrical equivalent weights above about 20,-000 the polycarboxylic acid resins are difficult to disperse in my process, and their throwing power (ability to coat surfaces in interstices, etc.) can be impaired as compared to those in the ranges called for.
The electrical equivalent weight of a given resin or resin mixture is herein dened as that amount of resin or resin mixture that will deposit per Faraday of electrical energy input under the conditions of operation set forth in detail in the succeeding paragraph. For this purpose the value of one Faraday in coulombs is herein taken to be 107.88 (atomic weight of silver)+0.00l1l8 (grams of silver deposited by one Coulomb from silver nitrate solution) or 96,493. Thus, if 0.015 gram of coating, the binder polycarboxylic acid resin moiety of which is 90% by weight and the balance of which is amino compound used to disperse it in the bath is transferred and coated on the anode per Coulomb input to the process, the
electrical equivalent weight of the resin is about 1303 or 0.0l5 0.9 107.88+0.001118.
By way of further illustration I iind electrical equivalent weight (in the nature of a gram equivalent weight in accordance with Faradays laws) of a particular polycarboxylic acid resin or resin mixture simply and conveniently for typical process conditions standardized on as follows: a polycarboxylic acid resin concentrate is made up at 65.56 C. (150 F.) by thoroughly mixing 50 grams of polycarboxylic acid resin, 8 grams of distilled water and diisopropanol amine in an amount suficient to yield resin dispersion pH of 7.8 or lslightly lower after the concentrate has been reduced to 5% by weight resin concentration with additional distilled water. The concentrate is then diluted to one liter with additional distilled water to give 5% resin concentration in the resulting dispersion. (If a slight insufliciency of the amine has been used, and the dispersion pH is below 7.8, pH is brought up to 7.8 with additional diisopropanol amine.) The dispersion is poured into a metal tank, the broadest side walls of which are substantially parallel with and 2.54 cm. out from the surfaces of a thin metal panel anode. The tank is Wired as a direct current cathode, and the direct current anode is a 20 gauge, 10.17 cm. (4 inches) wide, tared steel panel immersed in the bath 7.62 cm. (3.5 inches) deep. At 26.67 C. (80 F.) bath temperature direct current is impressed from anode to cathode at volts for one minute from an external power source, the current measured by use of a coulometer, and the current turned oii. The anode panel is removed immediately, rinsed with distilled water, baked for 20 minutes at 176.67 C. (350 F.) and weighed. All volatile material such as water and amine is presumed to be removed from the iilm for practical purposes by the baking operation. The dierence between tared weight of the fresh panel and nal weight of the baked panel divided by the coulombs of current used, times 107.88, divided by 0.001118 gives the electrical equivalent weight of the resin for purposes of this invention.
The polycarboxylic acid resin can be modified and extended in various ways without impairing its useful characteristics. Modification often can actually improve the paint such as by hardening the resulting baked film. Thus, I have used polycarboxylic :acid resins wherein there was blended thermoplastic, non-heat reactive phenolic resins into the polycarboxylic acid resin batches, which extended resins then were dispersed in water with the polyfunctional amino compound. The heating together, preferably With agitation, of the polycarboxylic acid resin with such phenolic resin for at least about 1/2 hour, and preferably about one to two hours or more, at a temperature between about 200 and about 260 C. appears to give a chemical bonding between those two components and no free phenolic resin appears to remain in the resin mixture. Thus, when the resulting resin is used in lmy electrocoating process, the coating is essentially homogeneous, and in an electrocoating bath containing the resulting resin product there is no appreciable accumulation of free phenolic bodies dissociated from the resin in an appreciable operating time.
Other suitable extenders for the polycarboxylic acid resins include hydrocarbon resins such as cumarone-indene resins, which are generally inert and thermoplastic, and diolefinic petroleum resins such as those of essentially naphthenic structure which are heat-rea-ctive, e.g., cyclopentadiene resins. Addition of resins such as this also can give increased chemical resistance to the resulting cured til-m. Many other resinous extenders and lm plasticizers of conventional nature, e.g., amino aldehyde resins, butadiene-styrene latices, vinyl chloride and vinylidene chloride homopolymer and copolymer latices, polyethylene resins, iluorocarbon resins, bis phenol-glycidyl ether resins, dicyclo diepoxy carboxylate resins, etc., vare permissible also, provided however, that their concentration is not so high as to mask the unique electrical migration characteristics ofthe polycarboxylic acid resin anionic polyelectrolyte behavior in the electrocoating bath and thus cause deposition of a film that is manifestly uneven and coated heavier at edges and corners of a simple rectangular sheet anode than on its immersed faces.
Broadly, the polycarboxylic acid resins useful in the practice of my invention are film-forming at the electrodeposition bath temperature and are curable to a tackfree iilm. They include: coupled siccative oils, eg., cou- -pled glyceride drying or semidrying oils such as sunllower, saiower, perilla, hempseed, walnut seed, dehydrated castor oil, rapeseed, tomato seed, menhaden, corn, tung, soya, oiticica, or the like, the olelinic double bonds in the oil being conjugated or nonconjugated or a mixture, the coupling agent being an acyclic olenc acid or anhydride, preferably maleic anhydride, but also crotonic acid, citraconic acid, or anhydride, fumarie acid, or an acyclic olenic aldehyde or ester of an acyclic olelinic ester such as acrolein, vinyl acetate, methyl maleate, etc., or even a polybasic acid such as phthalic or succinic, particularly coupled glyceride oils that are further reacted with about 2-25 of a polymerizable vinyl monomer; maleinized unsaturated fatty acids; maleinized rosin acids, alkyd resins, e.g., the esterication products of a polyol with a polybasic acid, particularly glyceride drying oil-extended alkyd resins; acidic hydrocarbon drying oil polymers such as those made from maleinized copolymers of butadiene and diisobutylene; diphenolic acid and like polymer resins; and acrylic and vinyl polymers and copolymers having carboxylic acid groups such as butyl acrylate-methyl methacrylate-methacrylic acid copolymers, vinyl acetate-acrylic acid copolymers, acrylic acid and lower alkyl (C14) substituted acrylic acid-containing polymers, i.e., those having carboxyl groups contributed by alpha, beta unsaturated carboxylic acids or residues of these acids, etc,
The acid number of the polycarboxylic acid resin for the paint binder should be at least about 30 for effective dispersion as the polyelectrolyte, and it can be as high as about 300 for practice of my invention. Using alkyd resins I have found that the best electrodeposition is from those having acid number between about 60 and about 200. The acid number of resins without appreciable content of anhydride groups can be determined with KOH by the ASTM standard method 555-54. Ii appreciable anhydride groups are present, the acid number can be determined by reuxing a 1.5-2 gram sample of the portion of the resin for one hour with 50 ml. of 0.5 N aqueous KOH and ml. of pyridine, then back titrating with 0.5 N HC1 to a 4phenolphthalein end point.
My preferred polycarboxylic acid resin for incorporating into the paint binder concentrate composition is a coupled siccative glyceride oil reacted with about 2-25%, basis the weight of the coupled oil, of a polymerizable vinyl monomer such as vinyl toluene, styrene, alpha methyl styrene, acrylonitrile or the like. The reaction with the vinyl monomer appears to enhance the deposited film by making it convert especially rapidly from a liuent dispersed material into an immobile, adherent, nonwettable (with water) and water resistant film on the substrate anode when at least about 2% of the vinyl monomer is reacted into the coupled oil; the electrical resistance of the bath is desirably raised when this resin is used also. However, if more than about 25% of the vinyl monomer is so reacted into the coupled oil, the iilm tends to entrap oxygen bubbles and can occasionally give a bubbly appearance which is often undesirable. The preferred vinyl monomer for economy and efiiciency in the practice of my invention is vinyl toluene, preferably limited to 15% maximum on the weight of the coupled oil. When this resin is extended with non-heat reactive phenolic resin by the high temperature process previously described, it is the most highly preferred one for metal priming because of its linal hardness.
In general I have found that the more highly acidic 6 polycarboxylic acid resins for my binder compositions, e.g., those having acid number substantially above about 10
Галерея 3361265
Девушка делает минет пожилому мужчине в фотоателье
Фигуристая негритоска ебется с белым хуем в туалете