Галерея 3096499
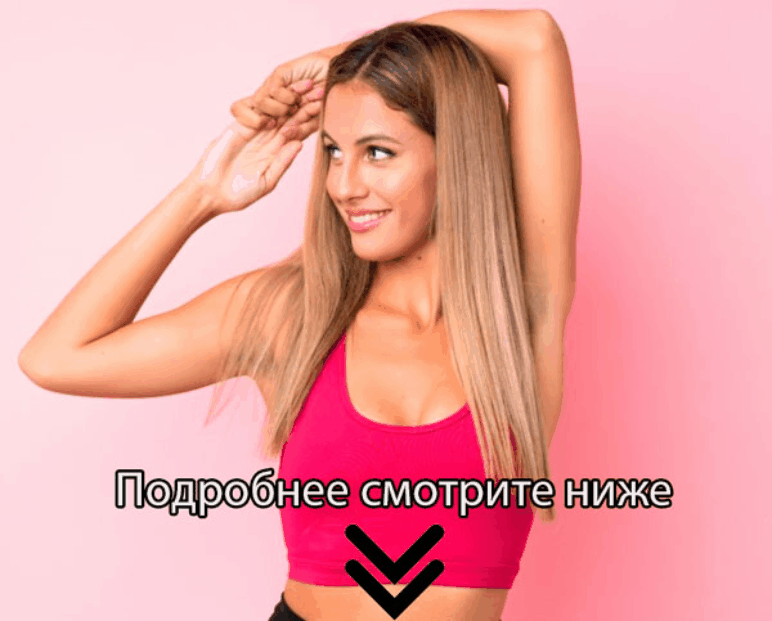
🛑 ПОДРОБНЕЕ ЖМИТЕ ЗДЕСЬ 👈🏻👈🏻👈🏻
Галерея 3096499
M. W. HUDS VAR July 2, 1963 INVENTOR. MILTON W. HUDSON BY FRED d. MOORE SR. MJM
ATTORNEY United States Patent fig 3,096,499 VARIABLE RESITOR Milton W. Hudson, St. Petersburg, and Fred J. Moore, Sr.,
Largo, Fla., assignors to International Resistance Company, Philadelphia, Pa.
Filed May 22, 1961, Ser. No. 111,659 Claims. (Cl. 338-163) The present invention relates to a variable resistor, and more particularly to a subminiature variable resistor which is accurate, reliable, and yet simple in construction so as to be inexpensive to manufacture.
In the electrical industry, the trend has been to making electronic equipment smaller and more compact so that the electrical components used to make up such electrical equipment must also be smaller and more compact. Furthermore, there has been an increasing use of printed circiut panels for mounting and connecting the electrical components. For use on the printed circuit panels, the electrical components must not only be small and compact to take up a minimum amount of space on the printed circuit panel, but the electrical components must be capable of being easily and quickly mounted on the panel.
In the electrical resistor field, the major problem in meeting the demands for miniaturized components has been with regard to variable resistors, such as rheostats and potentiometers. Heretofore, the more accurate and reliable variable resistors have been made up of many different parts including a rotatable shaft on which the movement contact is mounted. In attempting to miniaturize such variable resistors, it has been found that merely reducing the size of the various parts has its limitations since the smaller the parts the more difiicult it is to assemble the variable resistor, and still maintain the accuracy and reliability of the variable resistor. Thus, it has been found that to make miniature variable resistors, and particularly subminiature variable resistors of about one-half inch in diameter, it has been necessary to redesign the variable resistor to minimize the number of parts making up the variable resistor.
It is an object of the present invention to provide a novel variable resistor.
It is another object of the present invention to provide a novel subminiature variable resistor.
It is still another object of the present invention to provide a novel variable resistor which is small, compact and light in weight, but which is still accurate and reliable.
It is a further object of the present invention to provide a subminiature variable resistor having a minimum number of parts so as to be relatively easy and iuexpensive to manufacture.
It is a still further object of the present invention to provide a subminiature variable resistor which can be easily and quickly mounted on a printed circuit panel.
Other objects will appear hereinafter.
For the purpose of illustrating the invention there is shown in the drawings a form which is presently preferred; it being understood, however, that this invention is not limited to the precise arrangements and instrumentalities shown.
FIGURE 1 is a transverse sectional view of the variable resistor of the present invention.
FIGURE 2 is an elevational view of the front side of the variable resistor of the present invention.
FIGURE 3 is a sectional view taken along line 3-3 of FIGURE 1.
ing 12 has a circular base 14, and a cylindrical wall 16 integral with and projecting from the edge of the base 14. In the subminiature variable resistor 10 of the present invention, the base 114 of the housing 12 can be as small as one-half inch in diameter, and the cylindrical wall 16 approximately one-quarter inch in length.
The base 14 of the housing 12 has a circular groove 18 in its inner surface next to the inner surface of the cylindrical wall 16. The base 14 is provided with a second circular groove 20 in its inner surface within and next to the groove 18. The groove 18 in the base 14 is deeper than the groove 20. A slot 22 is provided in the inner surface of the base 14, which slot 22 extends from the center of the base 14 radially to the groove 20. A stop lug 24 is integral with the base 14 and projects upwardly from the inner surface of the base along the inner surface of the cylindrical wall 16. The stop lug 24 extends from the inner surface of the cylindrical wall 16 across the groove 1-8. As shown in FIGURE 3, the opposed side walls of the stop lug 24 are tapered toward each other from the inner surface of the cylindrical wall 16 at an angle of approximately 15 with respect to each other.
The cylindrical wall 16 of the housing 12 is provided with a cylindrical groove 26 in its inner surface which extends from the free end of the cylindrical wall to a point adjacent the stop lug 24. The cylindrical surface of the groove 26 is provided with an annular groove 28 therein at the radial surface of the groove 26. The cylindrical surface of the groove 26 is also provided with a V-shaped groove 30 therearound intermediate its ends.
As shown in FIGURE 2, the free end surface 32 of the cylindrical wall 16 has a pair of cylindrical projections 34 integral with and projecting therefrom. The projections 34 are circumferentially spaced apart 40, and are positioned at equal distances on opposite sides of the stop lug 24. Seven additional cylindrical projections 36 are provided on the free end surface 32 of the cylindrical wall 16, and are uniformly spaced around the surface 32. The projections 36 are smaller in diameter than the projections 34. Thus, the projections 34 and 36 are circumferentially spaced apart at 40 intervals around the free end surface 32 of the cylindrical wall 16.
Three terminal pins 38, 40 and 42 are secured to the base 14 of the housing 12, and project from the outer surface of the base. As shown in FIGURE 1, the terr'ninal pin 38 has an enlarged head 38a at one end. The head 38a of the terminal pin 38 extends through and is secured in the base 14 with the top surface of the head 3 8a extending into the groove 20* in the inner surface of the base. The terminal pin 38 is positioned so that the top surface of the head 38a is juxtaposed to the open end of the slot 22 in the inner surface of the base. Each of the terminal pins 40 and 42 has a head, not shown, on one end similar to the head 38a of the terminal pin 38. The heads of the terminal pins 40 and 42 extend through and are secured to the base 14 of the housing 12 with the top surfaces of the heads being within the groove 20 in the base 14. The terminal pins 40 and 42 are positioned around the groove 20 on opposite sides of and substantially from the terminal pin 38. H
An arcuate resistance element 44 is mounted in the groove 18 in the base 14 of the housing 12. Resistance element 44 comprises a core 46 which is circular in transverse cross-section, and is made of an electrically insulating material. A resistance wire 48 is helically wound around and along the core 46. As shown in FIGURE 3, the resistance element 44 is of a length to extend completely around the groove 18 with the ends of the resistance element being adjacent opposite sides of the stop accuses lug 24. The resistance element 44 may be secured in the groove 18 by a suitable cement or the like. As shown in FIGURE 3, one end 48a of the resistance wire 48 extends along the groove 2t) in the base 14 of the housing 12 to the head of the terminal pin 40, and the other end 431) of the resistance wire 48 extends along the groove 20 to the head of the terminal pin 42. The ends 43a and 48b of the resistance wire 48 are electrically and mechanically secured to the heads of the terminal pins 40 and 42 by soldering, welding or the like.
A contact plate 50 of an electrically conductive metal is secured in the slot 22 in the base 14 of the housing 12. Contact plate 50 is of a length to extend the entire length of the slot 22, and projects across the groove 20 to engage the head 38a of the terminal pin 38. The contact plate 50 may be secured to the head 38a of the terminal pin 38 by soldering, welding or the like.
A circular cover 52 of an electrically insulating material is mounted in the open end of the housing 12. Cover 52 is of a diameter substantially equal to the diameter of the cylindrical wall of the groove 26 in the wall '16 of the housing 12. Thus, the cover 52 extends completely across the open end of the housing 12 with the edge of the cover rotatably fitting in the groove 26 in the wall 16 of the housing. A cylindrical hub 54 is provided on the center of the inner surface of the cover 52. The hub 54 has a slot 56 extending diametrically thereacross. A stop lug 58 projects from the inner surface of the cover 52 adjacent one end of the slot 56 in the hub 54. The peripheral surface of the cover 52' has an annular groove 6t) therein which is directly opposed to the V-shaped groove 36 in the wall 16 of the housing 12. The outer surface of the cover 52 has a narrow slot 62 extending diametrically across the center portion thereof. As shown in FIGURE 2, a triangular shaped projection 64 is provided on the outer surface of the cover 52 adjacent one end of the slot 62. The projection 64 is positioned with its base being adjacent the end of the slot 62, and its apex being adjacent the edge of the cover 52 and in alignment with the longitudinal axis of the slot 62. Thus, the slot 62 and the projection 64 provide the appearance of an arrow.
The cover 52 is secured in the housing 12 by an annular snap. ring 66. The snap ring fits partially into the V-shaped groove in the Wall 16 of the housing 12, and partially into the annular groove 61 in the peripheral surface of the cover 52. Thus, the snap ring 66 secures the cover 52 in the housing 12, but permits rotation of the cover 52 with respect to the housing 12. An annular washer 63 is provided between the edge portion of the inner surface of the cover 52 and the radial surface of the groove 26 in the wall 16 of the housing 12. The outer peripheral portion of the washer 68 extends into the groove 28 in the wall 16 of the housing 12 to secure the washer to the housing. Thus, the washer 68 seals the space between the peripheral surface of the cover 52 and the cylindrical surface of the groove 26 in the wall 16 of the housing 12.
A contact 70 of a strip of an electrically conductive metal is carried by the cover 52. The contact 70 is pro vided at one end with a resistor contact arm 72 which extends into slidable engagement with the resistance wire 48 of the resistance element 44. The other end of the contact 70 has an arm 74 which extends back across the contact 70 and slidably engages the contact plate 50 at substantially the center of the base 14 of the housing 1.2. Each of the arms 72 and 74 of the contact 70 are spring arms which are bent back slightly toward the cover 52 so that the resiliency of the arms holds them tightly against the resistance element 44 and contact plate 50 respectively. Thus, the resistance element 44 is electrically connected to the terminal pin 38 through the contact 70 and the contact plate 50.
In the use of the variable resistor 10 of the present invention, the cover 52 can be rotated by means of a screw driver or similar tool which is inserted into the slot 62 in the outer surface of the cover. As the cover 52 is rotated, the end of the resistance element contact arm 72 of the contact 70 is moved along the resistance element 44. Since the resistance element 44 is electrically connected between the terminal pins 40 and 42, a desired resistance value can be obtained between the terminal pin 38 and either of the terminal pins 46 and 4-2 by rotating the cover 52. Since as shown in FIGURE 1 the end of the resistance element contact arm 72 is directly beneath the stop lug 58 on the cover 52, when the end of the resistance element contact arm is at either end of the resistance element 44, the cover stop lug 58 will engage the stop lug 24 on the housing 12. Thus, the rotation of the cover 52 with respect to the housing 12 is limited so that the end of the resistance element contact arm 72 does not leave the ends of the resistance element 44.
As shown in FIGURE 1, the triangular projection 64 on the outer surface of the cover 52 is positioned directly over the stop lug 58 of the cover. Thus, when the cover 52 is rotated to a position where the cover stop lug 58 engages the housing stop lug 24, the apex of the triangular projection 64 will point to one of the indicator projections 34 on the end surface 32 of the wall 16 of the housing 12. As the cover 52 is rotated, the arrow formed by the slot 62 and the triangular projection 64 will point to the smaller projections 36 on the end surface 32 of the wall 216 of the housing 12. Thus, the arrow formed by the slot 62 and the triangular projection 64 on the cover 52 along with the projections 34 and 36 on the end surface of the housing 12 provide an indication of the position of the resistance element contact arm 72 along the resistance element 44, with the larger projections 34 indicating the ends of the resistance element. By knowing the maximum resistance value provided by the resistance element 44, the approximate resistance value provided by any setting of the cover 52 can be easily and quickly determined.
Thus, the variable resistor 10 of the present invention provides a small, compact unit which is composed of a minimum number of parts so that it can be easily and inexpensively manufactured. Also, the variable resistor 10 of the present invention can be easily and quickly mounted on a printed circuit board by merely inserting the terminal pins 38, 40 and 42 into holes in the printed circuit board with the outer surface of the base 14 of the housing 12 being seated on the printed circuit board. Since the variable resistor 10 of the present invention is only onehalf inch in diameter and approximately one-quarter inch in thickness, and does not have a shaft projecting therefrom, the variable resistor 10 would cover only a minimum area of the printed circuit board, and would project only a small distance from the board so as not to interfere with any other electrical components mounted on the board. However, when the variable resistor 10 of the present invention is mounted on a printed circuit board, the cover 52 would be completely exposed for ease of rotating the cover to obtain a desired setting of the variable resistor. In addition, the arrow formed by the slot 62 and the triangular projection 64 on the cover 52 along with the indicator projection 34 and 36 on the end surface of the housing 12 permit ease of adjusting the variable resistor 10 to achieve any desired resistance value.
The present invention may be embodied in other specific forms without departing from the spirit or essential attributes thereof and, accordingly, reference should be made to the appended claims, rather than to the foregoing specification as indicating the scope of the invention.
1. A variable resistor comprising a housing of an electrical insulating material having a base and a cylindrical Wall extending from the edge of the base, an arcuate resistance element mounted on the inner surface of the base of the housing and extending along the inner surface of the cylindrical wall, said resistance element including a core and a resistance material on the surface of the core, a pair of terminal pins of an electrically conductive metal extending through and secured to the base of the housing, a contact plate of an electrically conductive metal mounted on the inner surface of the base of the housing, said contact plate extending from the center of the base of the housing to one of said terminal pins and contacting said one terminal pin, the other terminal pin being electrically connected to the resistance material of said resistance element, a circular cover fitting in and rotatably supported on the cylindrical wall of said housing and extending across the open end thereof, means securing said cover in said housing but permitting rotation of said cover with respect to said housing, and a contact of an electrically conductive metal carried on the inner surface of said cover, said contact having a pair of contact arms extending therefrom, one of said contact arms slidably engaging the resistance element and the other contact arm slidably engaging said contact plate.
2. A variable resistor in accordance with claim 1 including indicating means on the outer surface of the cover in the form of an arrow extending diametrically across the cover with the head of the arrow being adjacent the edge of the cover, and a plurality of individual projections on the free end surface of the cylindrical wall of the housing, said projections being uniformly spaced apart with two of the projections being adjacent separate ends of the resistance element.
3. A variable resistor in accordance with claim 2 in which the two indicating projections which are adjacent the ends of the resistance element are larger than the other projections.
4. A variable resistor in accordance with claim 1 in which the means securing the cover in the housing comprises an annular groove in the edge surface of the cover, an annular groove in the inner surface of the cylindrical wall of the housing directly opposed to the annular groove in the cover, and a snap ring partially fitting into each of said annular grooves.
5. A variable resistor in accordance with claim 4 including an annular gasket compressed between the cover and the inner surface of the cylindrical wall of the housing to seal the space between the edge surface of the cover and the housing.
References Cited in the file of this patent UNITED STATES PATENTS 988,456 Gernsback Apr. 4, 1911 2,691,087 Holleran Oct. 5, 1954 2,829,224 De Bell Apr. 1, 1958' 2,880,293 Blanco Mar. 31, 1959
1. A VARIABLE RESISTOR COMPRISING A HOUSING OF AN ELECTRIAL INSULATING MATERIAL HAVING A BASE AND A CYLINDRICAL WALL EXTENDING FROM THE EDGE OF THE BASE, AN ARCUATE RESISTANCE ELEMENT MOUNTED ON THE INNER SURFACE OF THE BASE OF THE HOUSING AND EXTENDING ALONG THE INNER SURFACE OF THE CYLINDRICAL WALL, SAID RESISTANCE ELEMENT INCLUDING A CORE AND A RESISTANCE MATERIAL ON THE SURFACE OF THE CORE, A PAIR OF TERMINAL PINS OF AN ELECTRICALLY CONDUCTIVE METAL EXTENDING THROUGH AND SECURED TO THE BASE OF THE HOUSING, A CONTACT PLATE OF AN ELECTRICALLY CONDUCTIVE METAL MOUNTED ON THE INNER SURFACE OF THE BASE OF THE HOUSING, SAID CONTACT PLATE EXTENDING FROM THE CENTER OF THE BASE OF THE HOUSING TO ONE OF SAID TERMINAL PINS AND CONTACTING SAID ONE TERMINAL PIN, THE OTHER TERMINAL PIN BEING ELECTRICALLY CONNECTED TO THE RESISTANCE MATERIAL OF SAID RESISTANCE ELEMENT, A CIRCULAR COVER FITTING IN AND ROTATABLY SUPPORTED ON THE CYLINDRICAL WALL OF SAID HOUSING AND EXTENDING ACROSS THE OPEN END THEREOF, MEANS SECURING SAID COVER IN SAID HOUSING BUT PERMITTING ROTATION OF SAID COVER WITH RESPECT TO SAID HOUSING, AND A CONTACT OF AN ELECTRICALLY CONDUCTIVE METAL CARRIED ON THE INNER SURFACE OF SAID COVER, SAID CONTACT HAVING A PAIR OF CONTACT ARMS EXTENDING THE RESISTANCE ELEMENT AND THE OTHER CONTACT ARM SLIDABLY ENGAGING SAID CONTACT PLATE.
Improvements in or relating to variable resistors
US3096499A
true
US3096499A
( en )
US111659A
Expired - Lifetime
US3096499A
( en )
US3193786A
( en )
*
US3237143A
( en )
Симпатичная милфа Эмили
Поебались и обоссались
Вечером на лавочке парочка сидит