Галерея 3056492
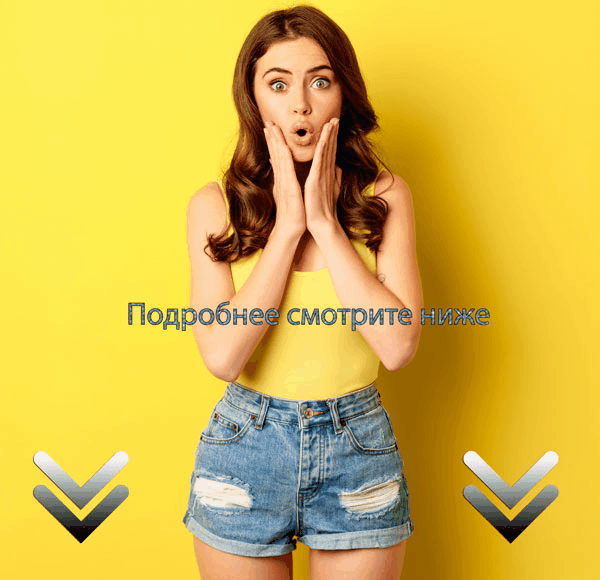
⚡ ПОДРОБНЕЕ ЖМИТЕ ЗДЕСЬ 👈🏻👈🏻👈🏻
Галерея 3056492
Oct. .2, 1962 .L E. CAMPBELL 3,056,492
FLUID CONTAINERS Filed Oct. 5, 1960 INVENTOR.
, sul-re" 3,056,492 Patented ct. 2, 1962 ffice 3,056,492 FLUID CONTAINERS John E. Campbell, Needham, Mass., assigner to Polaroid Corporation, Cambridge, Mass., a corporation of Dela- Ware Filed Uct. 3, 1960, Ser. No. 60,006 8 Claims. (Cl. 20o-56) This invention relates to uid containers and more particularly to fluid containers adapted to retain photographic processing compositions.
This application is a continuation-in-part of my copending application Serial No. 758,056, liled August 29, 1958.
United States Patents Nos. 2,543,181; 2,634,886; 2,653,- 732; 2,674,532; 2,702,146; 2,723,051; and 2,750,075 disclose liuid containers adapted to retain photographic processing compositions and which are formed of a plurality of layers comprising, respectively, an outer layer of kraft paper, a layer of metal foil, and an inner liner or layer of a thermoplastic resin, preferably a polyvinyl acetal, especially polyvinyl butyral. In addition, it is disclosed that the aforesaid thermoplastic resins may be modified, as for example by the addition of appropriate plasticizers. A preferred polyvinyl butyral liner is disclosed as having admixed therewith dibutyl sebacate and nitrocellulose.
The containers of the prior art are subject to deterioration thereof effected by prolonged contact with caustic alkali and/or organic nitrogen-containing compounds, as for example, the cyclic imide `and nitrogenous base silver halide complexing `agents `disclosed in United States Patent No. 2,857,274.
Objects of the present invention are to provide improved fluid containers, that is, improved containers of the aforesaid construction wherein the polyvinyl acetal inner coat or layer is replaced by an inner coat, liner or layer of polyvinyl chloride; substantially impervious to vapor; substantially impervious to alkali, especially to highly caustic liquid solutions; substantially impervious to nitrogen-containing compounds of the last-mentioned type; having pliable walls whereby said container is readily deformable; `and having a sealed passage adjacent to at least one edge thereof which may be substantially uniformly sealed throughout a predetermined length of said sealed passage upon application of stress to said container.
Further objects of the present invention comprise providing a continuous material from which individual blanks, adapted to form the aforementioned iluid containers, may be manufactured.
Other objects of the present invention will in part be obvious and will in part appear hereinafter.
The invention accordingly comprises the products possessing the features, properties, Aand relation of components which are exemplified in the following detailed disclosure, and the scope of the application of which will be indicated in the claims.
For a fuller understanding of the nature and objects of the invention, reference should be had to the following detailed description taken in connection with the accompanying drawing wherein like reference characters refer to like parts throughout the several views and whereinz' 'FIGURE 1 is a perspective View of one form of fluid container prior to introduction of a liquid thereinto and subsequent closure of the container walls;
yFIG. 2 is `a cross-sectional View comprising the huid container of FIG. l after introduction of a liquid and closure of said containers walls;
FIG. 3 is a fragmentary, plan view of the continuous material which is used in the formation of the container blanks of FIG. l; and
FIG. 4 is la cross-sectional view of the continuous material of FIG. 3.
Frequently it is required that a small quantity of liquid material be applied in a relatively thin layer over a fairly large surface area. For example, a photosensitive film may be processed or a picture may be toned by applying on the surface thereof, a layer of liquid containing the processing reagents, for example, a silver halide developing composition of the type disclosed in Unit-ed States Patent No. 2,543,181, issued February 27, 1951, to Edwin H. Land, or toning agents in solution. Another example of the need for applying a thin liquid layer over a large surface area resides in the application of a dye or ink to a hand press or printing block for producing prints or impressions. Adhesion of two elements also often necessitates a continuous layer of an adhesive between surfaces of said elements. The present invention comprehends lan inexpensive, preferably disposable, container adapted to provide for such uses a liquid which is in `a quantity sufficient to carry out a single application to the respective surfaces of a sheet to be treated and which is in condition for direct application to said surfaces whereby to afford greater eiiiciency and economy of operation. Where desired, the aforementioned container may be directly axed to or in apposition to a surface to be treated.
In one embodiment, the container is an elongated structure, having a length of at least twice its width, and is relatively flat, having a depth which is only a fraction of its width. The container is deformable in its filled and sealed condition so that it can `be curved in the direction of its Width, for example, about a radius equal to its width, without danger of rupturng its seal. A sealed passage extends the length of the container along one edge thereof and is the Weakest of the edge seals which define the liquid-containing cavity 'and which confine the contents of said cavity.
The container should be duid-tight, vapor-impervious and inert to its retained contents whereby the contents may be kept substantially unaffected by external agents, including the container itself, for an extended time interval.
The present invention is concerned with improved fluid containers of the `aforementioned type which `substantially avoid container degradation and fluid contamination resultant from the utilization of said containers to retain organic nitrogen-containing compounds and/or caustic alkali liquids such as highly caustic and/or organic nitrogen compounds containing photographic processing compositions.
In addition, the present invention is concerned with providing frangible containers of the aforementioned type which exhibit increased differential strength ofthe respective edge seals, thus facilitatiing uniform rupture and distribution of the containers fluid contents by means o-f a predetermined passage orice upon application of stress to said containers deformable surfaces.
The container is preferably formed from a single, essential-ly rectangular blank folded niedially, as illustrated in FIG. l.
prising walls 7 and l0, said individual Walls being formed by medial fold 11.` A surface portionof one of said Walls as, for example, portion 6 of wall 7, is suitable for receiving and in part confining said liquid, and a substantially equal surface portion of the other of said walls as, for example, surface portion l of wall 10 is suitable for further confining said uid upon closure of said walls. The container may also be formed from -two essentially rectangular blanks secured together at the marginal edges. It is so simply constructed that the container blank of FIG. 3, from which the container is The container is constructed of ai multilayer, preferably medially folded, material com- 3 formed, may be cut without waste from a continuous strip of sheet material, permitting the material of the container walls to be processed and the container to be filled, sealed and served as part of one continuous operation.
The aforesaid fluid container is preferably constructed, as illustrated in FIG. 2, of an outer layer 15 as a backing or support layer, said outer layer 15 being preferably preformed of a thin, deformable, relatively inexpensive, tough material which may be a plastic but which is preferably a paper, such as a kraft paper. A thin film or sheet 14 of a relatively thin, imprevious sheet material, such as a metal foil, 4for example, a sheet of lead, aluminum, etc., foil, approximating 0.001 inch in thickness and having dimensions predetermined according to the intended use is suitably adhered to a surface of a layer 15. A layer 13 comprising a polymeric material Icontaining a major portion of polymerized vinyl chloride, eg., 90% vinyl chloride and 10% vinyl acetate, is suitably adhered to the exposed surface of layer 14.
The polyvinyl chloride liner may be adhered to the metal foil layer by coating and/ or laminating procedures well known to the art. Where a precast polyvinyl chloride liner is laminated to the metal foil, it is generally preferred to utilize an adhesive coating or layer interposed between the polyvinyl chloride and the metal foil layer, which adhesive layer is itself stable or stabilized against interaction with the containers fluid contents. There is, according to this method of lamination, thus `afforded an additional layer enhancing the stability of the container and its retained liquids. Maximum-thickness laminating adhesive coats serve as an added barrier coating for retaining the containers liquid contents. It is also contemplated, within the scope of the present invention, 4to employ as the polyvinyl chloride liner a `coated layer of polyvinyl chloride, as for example, a polyvinylidene chloride coated layer of polyvinyl chloride.
The term polyvinyl chloride as used herein, is intended to signify, in addition to polyvinyl chloride, a ycopolymeric derivative thereof, as for example, vinyl chloride-vinyl `acetate copolymers, preferably comprising `approximately 90% vinyl chloride and approximately vinyl acetate, by Weight. It will be recognized that the respective aforementioned concentrations of the copolymeric components` may be modified to suit the requirements of the operator provided that the predominant or major portion of the respective copolymer comprises polymerized vinyl chloride. A second illustrative copolymeric derivative comprises vinyl chloridevinylidene chloride copolymers, the concentrations of which components may be varied over a wide range.
In the completed, closed, liquid-carrying container, the aforementioned polyvinyl chloride coating 13 serves both to substantially prevent direct contact of the carried fluid with the vapor-impervious layer 14 and as a means of bonding together the facing marginal portions of said polyvinyl chloride layer bordering the enclosed liquid when, for example, the marginal portions are subjected to an application of heat and/or pressure, said portions thus bonded providing means for sealing the liquid within the container. A Second coating 9 of an adhesive composition as, for example, of the following illustrative composition:
(l) 100 ec. of a composition comprising:
10.0 grams of Acryloid B-72 (solid) (trade name of Rohm & Haas Company, Philadelphia, Pennsylvania, for an acrylic ester resin),
3.4 grams of one half second cellulose nitrate,
overlaid on a marginal portion 8 of polyvinyl chloride layer 13, when bonded to a facing marginal polyvinyl chloride portion 2, serves as a means for bonding said facing marginal portions differentially with respect to 4 other facing marginal portions 4, 5, 3 and 12 comprising solely polyvinyl chloride.
Upon closure of walls 7 and 10, marginal surface portions 2, 4 and 12 come in contact with marginal surface portions 8, 5 and 3, respectively, and may be suitably bonded together and, when thus bonded, provide, in conjunction with fold 11, means for effecting a completely sealed enclosure or space.
In the aforementioned adhesive composition, the inherent sealing capacity of the acrylic ester resin to a polyvinyl chloride base is modied by the release characteristics of the cellulose nitrate with the ratio indicated of cellulose nitrate to acrylic ester resin, i.e., on the lorder of l to 3 critical to the functionality of the container structure. A significant alteration of said ratio produces a seal either too Strong or too weak such that in the former case, the container will not open satisfactorily, and in the latter case will rupture too easily. As indicated, the ratio of the cited materials is specific for a given polyvinyl chloride base, that is, a copolymer comprising about vinyl chloride and about 10% vinyl acetate, but may be altered to function with other bases with different sealing characteristics, e.g., a vinyl chloride-vinyl acetate copolymer with less vinyl acetate. Other `solvents may be used in the above system as also other cellulose nitrate resins or other acrylics, but those cited are preferred to produce in conjunction a container structure with operable functionality in ambient temperatures (32-l20 F.) and humidities (0-98% RH).
Referring lto FIG. 3, there is shown a blank 40 from which one embodiment of the novel container of the present invention may be formed, said blank 40, as Ishown, being substantially rectangular in shape and having a length equal to the container length, and a width approximately twice the width of the finished, filled container. As previously stated, the blank 40 is preferably formed of a composite, deformable sheet material comprising a plurality of strata, as illustrated in FIG. 4.
Outer layer 15 serves as the aforementioned backing or support layer which has applied thereto layer 14 which, as previously mentioned, is a thin film or sheet of a relatively vapor-impervious material, such as a metal foil. On the surface of said foil layer 14, a layer 13 of polyvinyl chloride comprising one or more strata is adhered to said foil layer 14 by the application of heat and/or pressure and/or an appropriate adhesive. Layers 13 and 14 are relatively thin, being only sufficiently thick to be continuous.
Along one edge of the blank 40, there is provided a strip 9 of the thermoplastic composition previously set forth which exhibits, preferably, a lesser adhesive affinity for polyvinyl chloride layer 13 than the latter polyvinyl chloride layer has for itself upon sealing.
Container 20, illustrated in IFIG. 2, is formed by folding blank `40 along a substantially medial line 34 extending the length of the container and then securing together the faces of the marginal portions 32 along the short edges of the container and the facing marginal surface portions 31 along the long edge of the container. As previously mentioned, the several marginal portions are secured together by the application of heat and/ or pressure and, in addition, it is preferable to adhesively secure together a narrow strip 33 of the container walls adjacent to the fold line 34. This provides a thin leading edge for the container over which a suitable pressure-applying device, such as a pressure roll or a doctor blade, may be readily advanced to compress the container Walls and effect the release of the container contents by differential hydraulic rupture of the sealed marginal surfaces, preferably along the long edge of the container. The seal along the long edge of the container is effected between the inner polyvinyl chloride layer 13 and the material strip 9 which, as hereinbefore indicated, is a material which has a different adhesive afiinity, preferably a lesser adhesive affinity, for polyvinyl chloride layer 13 from polyvinyl chloride for itself. Since the short-edged portions 32 are secured together by a bond formed by direct contact between the inner polyvinyl chloride layers 13, the latter bond exhibits a differing adherence capacity, preferably an adhesive capacity substantially stronger, than the seal along the long edge.
This structure assures a unidirectional release of the contents of the container upon application of the compressive squeezing force to the walls thereof. In the preferred embodiment, to make certain a uniform peeling or separation of the marginal portions along the long edge of the container is obtained when the container is subjected to a liquid-releasing force, strip 9 not only extends to the very edge of the container but is also substantially wider than the width of the seal 31 and extends within the liquid-carrying cavity of the container, as shown in FIG. 2. A further precaution against the hazard of an uneven seal consists in displacing the blank containing strip 9 just beyond the long edge of the blank to which it is adhered. As a result, strip 9 projects be yond both long edges of the bond.
In the formation of the container, the contents may be introduced as the container walls are being sealed together. For example, the long edges of the container may be sealed together before the blank is severed from the stock of material from which it is formed. During the sealing together of the long edges, the desired quantity of liquid content for the container is introduced between the folded walls of the blank and thereafter the short edges are sealed together and the finished container severed from the remainder of the sheet stock. The sealing is preferably effected by the application of heat and/or pressure, and the uniform heat and/ or pressure may be applied to all of the marginal portions being sealed together in View of the difference between adhesive properties of the strip 9 and those of the polyvinyl chloride of the inner layer 13.
In one preferred form of the container for spreading a liquid reagent to a thickness of approximately 0.003 inch over an area approximately three inches by four inches, a container 31/2 inches long and having a maximum thickness of IAG of an inch can be used. The overall width of such container will be approximately 3%; of an inch and the width of the seals at the marginal areas will be approximately EAG of an inch, while the seal at the release edge of the container will :be approximately 1/16 of an inch. The overall thickness of the sheet materials from which the container walls are formed may be approximately 0.0048 of an inch, with layer approximately 0.0025 of an inch thick, layer 14 approximately 0.0014 of an inch thick, and layer 13 approximately 0.0009 of an inch thick.
The aforesaid materials and constructions provide a container capable of substantially confining a liquid as, for example, a liquid adapted for processing a photographically exposed photosensitive film and, in conjunction therewith, said container effectively preventing loss of liquid content due to exudation, absorption, or evaporation thereof and acting to preserve said liquid substantially free from oxidation, it being understood that the liquid may be introduced into the container in an inert atmosphere.
The instant materials and constructions, to wit, frangible fluid containers comprising, respectively, an outer layer of kraft paper, a sheet of lead foil and an inner layer of polyvinyl chloride, having interposed between the long marginal edge thereof a strip comprising an adhesive composition of the type heretofore described, and standards comprising representative prior art disclosed frangible fluid containers comprising, respectively, an outer layer of kraft paper, a sheet of lead -foil and an inner layer of double coated polyvinyl butyral, having interposed between the long marginal edge thereof a strip comprising ethyl cellulose, were subjected to an accelerated aging test. The aging test comprised maintaining photographic processing composition retaining containers at a temperature of V F'. for two Weeks. This procedure disclosed severe deterioration of the standards polyvinyl butyral layers in contradistinction to the instant'containers which exhibited substantially no deterioration of their polyvinyl chloride layers.
The aforementioned experimental results are illustrative of the decreased iuid contamination and container deterioration afforded by the instant containers, especially decreased contamination and container deterioration caused by caustic liquids containing organic nitrogen compounds.
Wher
Худая кубинка раздвигает ножки
Галерея 3493351
Молодая пышная деваха показывает свою натуральную обнаженную красоту