What Are The Problems With Air Compressors?
Vaishali AegisAir compressors are strong and indispensable appliances that make several difficult activities easier to do. These heavy-duty gadgets have proven their worth in commercial and industrial environments, making them a must-have for facilities looking to better their day-to-day operations. Repairing of air compressors are very versatile and adaptable, with many models designed for specific applications. They make the workplace a safe, clean, and comfortable place to work.
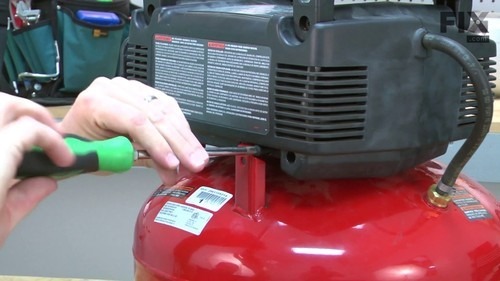
Like many other heavily used machines, air compressors require routine maintenance to keep their efficiency and effectiveness. They are, nevertheless, prone to wear and tear due to heavy use. You’ll run into problems sooner or later. It doesn’t have to be expensive, thankfully. The first step is to figure out what problem you’re dealing with and how to solve it.
Typical Air Compressor Issues
Keep a watch out for the following air compressor issues and be prepared to deal with them if they arise:
Failure of the compressor
One of the most common issues you may have when using an air compressor is not starting. It can happen as a result of a simple oversight. One of the following difficulties may be causing your compressor not to start, shut down, or supply air pressure while it’s running:
The compressor will not start
This is frequently the result of neglecting power connections, such as a disconnected power cord or a power switch turned off. Check the power button and switch before starting. If necessary, breakers should also be checked.
Repairing of air compressors can fail due to a lack of sufficient air pressure concerning the cut-in pressure, in addition to a lack of electrical power. If this occurs, examine the cut-in pressure settings and make any necessary adjustments.
It could also be due to a lack of oil. To keep the tank from running dry, check or replace the compressor fluids.
The compressor is unable to come to a halt.
When the tank pressure reaches the cut-off point, the compressor should turn off. It could be due to a malfunctioning pressure release valve or a faulty power switch if it doesn’t happen.
If the valve fails to release pressure, the compressor will become excessively pressured to operate, causing catastrophic damage to your equipment. Cut the power and replace the valve in this situation. On the other hand, a faulty power switch may fail to send a switch-off signal to internal controls. The problem should be resolved with the installation of a new switch.
Failure to provide sufficient pressure
There could be a problem with your air-intake pump if the repairing of air compressors is running but not producing any air pressure. It could also be a problem with the compressor’s gasket between the low- and high-pressure compartments. Changing them out will improve the performance of your machine.
Issues that are getting in the way
It could be a motor problem if your compressor only works efficiently for short periods and runs out of steam quickly, often prematurely.
Compressors can also become clogged when the power source is shared with other devices. Air compressors require their power supply, which is connected to a 15-to-20-amp breaker. Your unloader valve could also be to blame. Open the tank to drain the water and let the air out to assess the problem. It’s time to replace the valve if the air compressor still bogs down.
Leaks of air
You have an air leak if you deactivate the air compressor once the tank is full and notice that the gauge indicates reduced pressure. Leaks, fortunately, are simple to fix. Listen for a hissing sound or run your fingertips over the component to feeling air escaping to determine the leak’s location.
If you can’t discover the leak using these methods, use liquid soap to lather the connections, including the couplers and power switch. The bubbling will reveal the location of the leak. To seal the coupler, tighten it where it bubbles.
The tank check valve can also be inspected. When a valve fails to close entirely, air leaks are common. If the pressure gauge continues to drop after the tank has been switched off, check the condition of the valve and clean or replace it as needed.
Noise and vibrations that are out of the ordinary
Loud noises or strange vibrations from the repairing of air compressors may indicate that something is wrong. These are signs of a malfunctioning internal system. While this does not always imply that major repairs are required, little modifications can help to avoid more serious problems.
Problems with Flow and Pressure
Problems with pressure and flow are more subtle. The machine may continue to function normally. Repairing of air compressors can either produce too much or too little air. Similarly, the pressure can only go up to a certain PSI and not much more.
Components such as the intake valve, pressure valve, gasket, piston seal, or tank check valve may be jeopardized if you detect these problems. Check these components for wear and damage, and replace them if necessary.
Problems with pressure and flow can also be caused by the following:
• Filters that are clogged, putting a load on the compressor and making it take longer to produce air.
• Airflow is obstructed by an ill-fitting coupler.
• Low-pressure setting on the pressure gauge.
On/Off Switch Is Broken
If your air compressor’s motor does not turn on when you turn on the switch, there could be a problem with the switch, but you should conduct some testing before making any conclusions. Check the power cord to make sure it’s plugged into a working outlet. Whether the power switch still doesn’t work, try plugging a light or electronic device into the outlet to check if it works.
If the outlet works for other devices but not your compressor, pull back the housing that encases the switch, remove it from the socket, and look up the switch’s specifications in the compressor owner’s manual.
Conclusion
On a professional and personal level, repairing of air compressors are used for a variety of tasks. Pressurized air is used to build anything from autos and aircraft to appliances and home furnishings, from pressing plants and factories to repair shops and studios. Today’s compressors are built to offer maximum power while maintaining a stylish appearance over a long period.