The 9-Minute Rule for Tide Rock Holdings Acquires PDM, Bringing - WFMZ
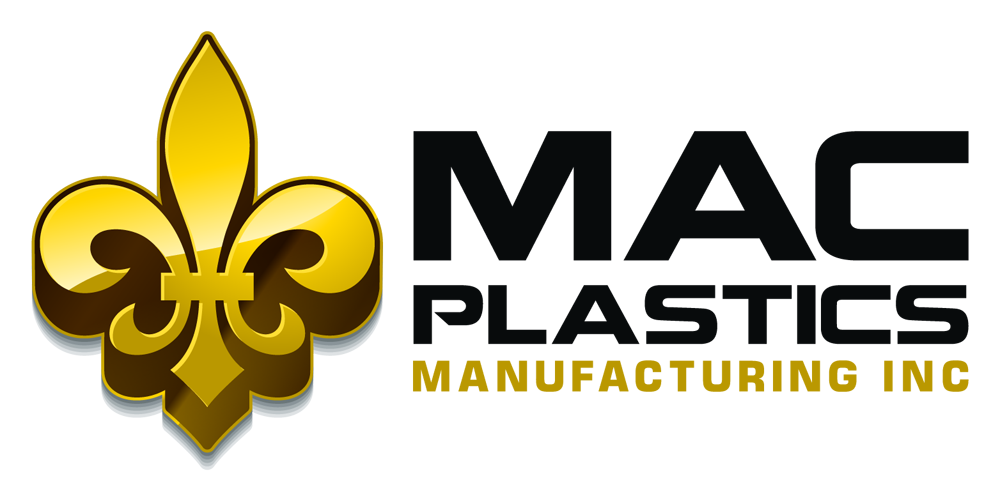
Design and Manufacturing of Plastics Products - ScienceDirect for Dummies
The resin is not perfect for parts that will undergo continual intense heat as it will warp or melt above/ around 200 degrees Fahrenheit. are a state-of-the-art class of thermoplastics that are quickly molded and typically increases shatter resistance. Naturally transparent, polycarbonate is ideal for high-strength glass-like applications (security goggles, medical lab applications and more).
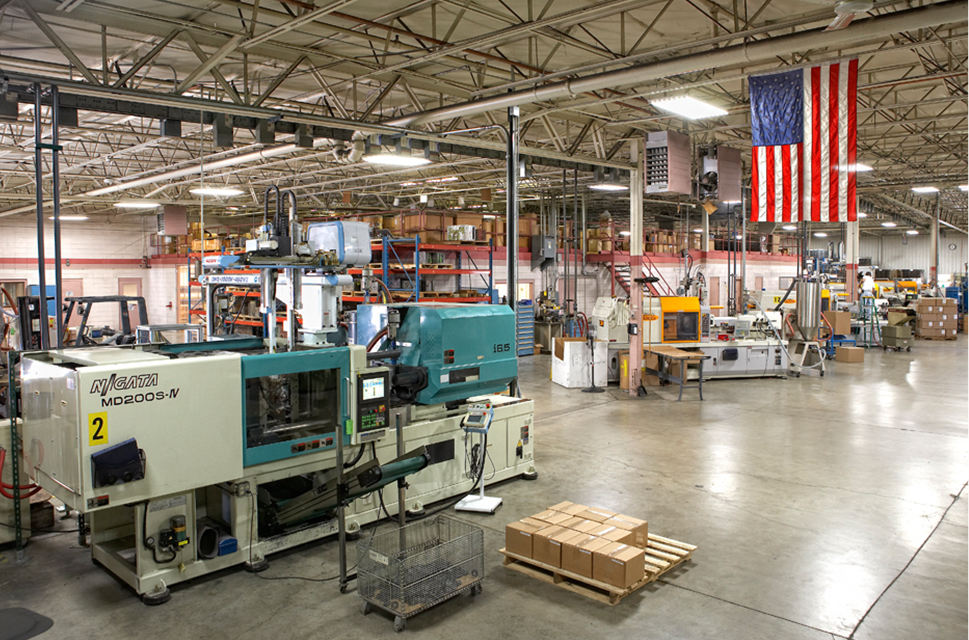
is a strengthened thermoplastic, where the base nylon resin has glass fibers included to it for extra strength and heat resistance. This resin is also more nonconductive to electricity than lots of others, but despite of its high melting point, it is more prone to burning than other materials. is a versatile thermoplastic that appropriates for commercial and consumer applications.
Polypropylene also provides resistance to solvents, chemicals and UV rays. is understood to offer terrific friction resistance and is an extremely stiff material. It can be easily colored and colored in the molding procedure; however, does not use remarkable heat resistance. Among the most essential steps when getting ready for injection molding resin choice is to create a comprehensive material choice list of requirements for the product.
The Best Guide To Plastic Design & Manufacturing, Inc(PDM)It's also important to consider that some characteristics of high heat and unique resins are special and might perform differently from one application to another. To recognize This Is Cool and product's fullest benefits, knowledgeable style engineers and injection molders have a number of aspects to consider. Comprehending Surface Finishing and its Role in DFM Design for Production a plastic part or item, prior to constructing a mold or tooling, should include discussions and choices about surface area completing.
In the design stage, the plastic injection molding partner, OEM and customer need to be going over wanted outcomes for the part or item, such as needs for: Permitting trapped gasses to leave rapidly Getting rid of plastic flow creases Getting much better sticker label adhesion Improving grip Improving paint adhesion Making a high polish surface Producing a smooth surface Making the highest polish finish Getting rid of tooling marks Utilizing texture to make undercuts Like other parts of the DFM approach, surface completing belongs to the cost/quality/customer satisfaction formula that must take place at the beginning of an agreement.