Wellhead System Without Penetrations
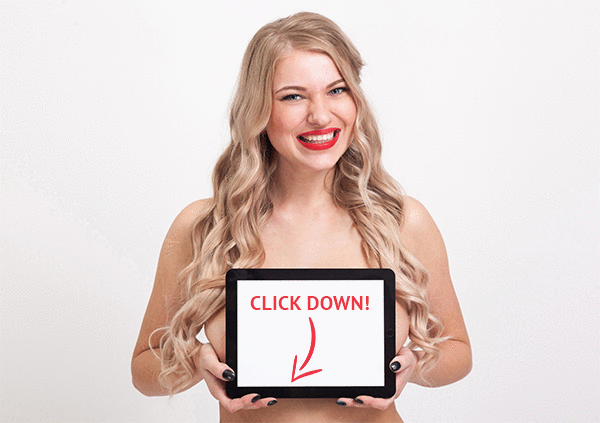
🔞 ALL INFORMATION CLICK HERE 👈🏻👈🏻👈🏻
Wellhead System Without Penetrations
Выбрать язык русский арабский вьетнамский индонезийский испанский итальянский китайский (упрощенный) корейский немецкий нидерландский норвежский персидский польский португальский турецкий финский японский
You must log in to edit PetroWiki. Help with editing
Content of PetroWiki is intended for personal use only and to supplement, not replace, engineering judgment. SPE disclaims any and all liability for your use of such content. More information
Copyright 2006,
Society of Petroleum Engineers
Chapter 8 - Introduction to Wellhead Systems
ISBN 978-1-55563-114-7
Get permission for reuse
The objective of this chapter is to provide a brief overview of the types of wellhead systems and equipment commonly found on wells drilled in today
’
s oil and gas industry. First, we discuss two broad categories of surface wellhead systems: onshore and offshore. Then, we discuss wellhead systems used in subsea and ultradeepwater applications.
When a well is drilled on land, an interface is required between the individual casing strings and the blowout preventer (BOP) stack. This interface is required for four main reasons:
Fig. 8.1—Illustration of a typical land wellhead system and casing program (all figures in this chapter are courtesy of Dril-Quip).
Fig. 8.2—Photo of a starting casing head and installation components. This casing head is typical of a thread-on or weld-on configuration used in land drilling operations.
Fig. 8.3—Photo of a starting casing head and slip-and-seal assembly with installation components. This casing head has a gusseted base plate typically seen in jackup drilling operations.
Fig. 8.4—Photo of a typical intermediate casing head and additional components required to assemble it during the drilling operation.
Fig. 8.5—Photo of a typical tubing head with installation components.
Casing weight is transferred to the starting casing head and intermediate spools with two different types of hanger systems:
Fig. 8.6—Photo of a typical weight-set slip-and-seal assembly with casing-head installation components.
Fig. 8.7—Illustration (cutaway) of a mandrel-type tubing hanger.
Fig. 8.8—Illustration of a weight-set slip-and-seal casing-hanger assembly.
Fig. 8.9—Photos of the wear bushings for a typical land drilling wellhead system.
Fig. 8.10—Photo of the wear bushing running tools. These tools are also used to test the BOP stack.
For onshore wells, during the drilling operation, access to each annulus is required for the following reasons:
When ordering wellhead equipment, the following should be considered:
Fig. 8.11—Tables showing typical gate-valve sizes (above) and trims (below). These trims are also applicable to surface wellheads.
Fig. 8.12—Illustration of a typical mudline suspension system showing running tools on the left side and tieback tools on the right side.
Fig. 8.13—All mudline hangers should stack down to provide washout efficiency. Washout efficiency is supplied by a series of wash ports located in the running tool that (when opened for washing out) are positioned below the running tool attached to the previously run mudline hanger.
Fig. 8.14—Illustration of a mudline suspension system with temporary abandonment caps installed after the well is drilled.
Fig. 8.15—Illustration of a mechanical-set slip-and-seal assembly.
The mudline suspension system also allows the well to be temporarily abandoned (disconnected) when "TD" is achieved (when drilling is finished at total depth). When this occurs, the conductor is normally cut approximately 5 to 6 ft above the mudline and retrieved to the surface. After each casing string is disconnected from the mudline suspension hanger and retrieved to the rig floor in the reverse order of the drilling process, threaded temporary abandonment caps or stab-in temporary abandonment caps (both of which makeup into the threaded running profile of the mudline hanger; see Fig. 8.14 ) are installed in selected mudline hangers before the drilling vessel finishes and leaves the location. The temporary abandonment caps can be retrieved with the same tool that installed them.
Fig. 8.16—Illustration of a mudline suspension system with threaded tieback tools installed (left) and “stab-in” tieback tools installed (right) in each hanger body.
Fig. 8.17—Illustration of a typical unitized wellhead system for land applications. Offshore unitized wellhead systems are typically similar but include the use of a metal-to-metal seal assembly.
Fig. 8.18—Photo of a 13⅝-in. 5,000-psi unitized wellhead system and its major components.
Fig. 8.19—Photo of a unitized wellhead mandrel hanger.
Fig. 8.20—Photo of a seal assembly for the mandrel hanger. This seal assembly features elastomeric seals, but it also can feature true metal-to-metal seals.
The unitized wellhead is more often used with platform-development projects than with exploration applications.
Fig. 8.21—Illustration of a typical subsea wellhead system with temporary abandonment cap installed. This illustration also shows the wellhead configuration with a 30 × 20 × 13⅜ × 9⅝ × 7-in. casing program.
Fig. 8.22—Illustration of typical guide bases, both guidelined and guidelineless. Each guide base can incorporate customer-specified features, such as remote-retrievable capabilities and special flow-by features.
Fig. 8.23—Illustration of typical low-pressure wellhead housings. Each low-pressure housing can also incorporate various features based on the particular application and drilling environment.
Fig. 8.24—18¾-in. wellheads are manufactured with several different locking profiles to mate with the wellhead connector located on the bottom of the BOP stack or subsea production tree. The wellhead systems are usually rated for 10,000 or 15,000 psi and can be installed with a standard lock ring or a rigid lockdown mechanism, which is the preferred choice for deepwater operations.
Fig. 8.25—Illustrations of the subsea casing hangers. Notice features to accommodate casing, a seal assembly, and a running tool.
Fig. 8.26—Photo of the 18¾-in. seal assembly (left), and illustration of the metal-to-metal seal that seals off the annulus between the casing hanger and the wellhead.
Fig. 8.27—Photos of the nominal bore protector, 133/8-in. wear bushing, and 95/8-in. wear bushing. These wellhead components are run on a multipurpose tool.
Fig. 8.28—Illustration of the SS-15 Subsea Wellhead System running tool family.
Fig. 8.29—Illustration of the Big Bore Subsea Wellhead System with the 18-in. and 16-in. supplementalcasing-hanger systems.
Fig. 8.30—Deepwater subsea wellhead, designed specifically to meet the requirements of higher-strength and pressurized shallow-zone water flows associated with ultradeepwater drilling in the Gulf of Mexico.
As has been discussed in this chapter, wellhead systems (whether the application is surface wellheads on land, jackups or offshore production platforms, or subsea wellheads) serve as the termination point of casing and tubing strings. As such, these systems control pressure and provide access to the main bore of the casing or tubing or to the annulus. This pressure-controlled access allows drilling and completion activities to take place safely and with minimal environmental risk. Multiple barriers are used, such as primary and secondary seals, to reduce risk in case of equipment failure. Land wellhead systems, offshore surface wellhead systems, and subsea wellhead systems have been discussed. Offshore wellhead systems are normally more sophisticated in design to handle ocean currents, bending loads, and other loads induced by the environment during the life of the well. Some of these loads are cyclic in nature, so fatigue-resistant designs are desirable, particularly for deepwater developments. Material specifications play an important role in equipment performance; organizations such as API, the American Soc. of Mechanical Engineers (ASME), and NACE Intl. offer helpful standards to provide cost-effective solutions to technical challenges. In certain applications such as deepwater platforms, spars, and tension-leg platforms (TLPs), surface wellheads and subsea wellheads are used together to safely produce hydrocarbons. In water depths of 500 to 1,400 ft, subsea wellheads are used to explore and develop offshore fields. Deepwater production platforms can be placed over these wells and tied back to the subsea wellheads; the top termination of the tieback at the platform will typically use surface unitized wellheads with solid block Christmas trees (which have fewer leak paths) as pressure-controlled access points to each well. Spars and TLPs are floating vessels used in deep water up to 4,500 ft. The wells are drilled using subsea wellheads, which are then tied back to the production deck of the spar or TLP, again using unitized wellheads and solid block trees to safely control and produce the well. For these special applications, it is recommended to contact your equipment supplier for more detailed information.
Aldridge, D. and Dodd, P. 1996. Meeting the Challenges of Deepwater Subsea Completion Design. Presented at the SPE Asia Pacific Oil and Gas Conference, Adelaide, Australia, 28-31 October 1996. SPE-36991-MS. http://dx.doi.org/10.2118/36991-MS .
Anchaboh, L., de Lange, F.P.A., van Beelen, C.J. et al. 2001. Conductor Sharing Wellheads—More For Less. Presented at the SPE Asia Pacific Oil and Gas Conference and Exhibition, Jakarta, 17–19 April. SPE-68699-MS. http://dx.doi.org/10.2118/68699-MS .
Andersen, J.N., Rosine, R.S., and Marshall, M. 2000. Full-Scale High-Pressure Stripper/Packer Testing with Wellhead Pressure to 15,000 psi. Presented at the SPE/ICoTA Coiled Tubing Roundtable, Houston, Texas, 5-6 April 2000. SPE-60699-MS. http://dx.doi.org/10.2118/60699-MS .
Bazile II, D.J. and Kluck, L.M. 1987. New Wellhead Equipment for Old Oilfields. Presented at the SPE/IADC Drilling Conference, New Orleans, Louisiana, 15-18 March 1987. SPE-16122-MS. http://dx.doi.org/10.2118/16122-MS .
Burman, S.S. and Norton, S.J. 1998. Mensa Project: Well Drilling and Completion. Presented at the Offshore Technology Conference, Houston, Texas, 4 May-7 May 1998. OTC-8578-MS. http://dx.doi.org/10.4043/8578-MS .
Cort, A.J.C. and Ford, J.T. 1995. The Design and Testing of Subsea Production Equipment: Current Practice and Potential for the Future. Presented at the SPE Annual Technical Conference and Exhibition, Dallas, Texas, 22-25 October 1995. SPE-30675-MS. http://dx.doi.org/10.2118/30675-MS .
Dupal, K. and Flodberg, K.D. 1991. Auger TLP: Drilling Engineering Overview. Presented at the SPE Annual Technical Conference and Exhibition, Dallas, Texas, 6–9 October. SPE-22543-MS. http://dx.doi.org/10.2118/22543-MS .
Eaton, L.F. 1999. Drilling Through Deepwater Shallow Water Flow Zones at Ursa. Presented at the SPE/IADC Drilling Conference, Amsterdam, The Netherlands, 9–11 March. SPE-52780-MS. http://dx.doi.org/10.2118/52780-MS .
Gordy, C.A., Combes, J.F., and Childers, M.A. 1987. Case History of a 22,000-ft Deepwater Wildcat. Presented at the SPE/IADC Drilling Conference, New Orleans, Louisiana, 15-18 March 1987. SPE-16084-MS. http://dx.doi.org/10.2118/16084-MS .
Hadj-Moussa, N. 1999. Rig Equipment Planning for a Deep, Deviated High-Pressure/High Temperature Khuff Well. Presented at the SPE/IADC Middle East Drilling Technology Conference, Abu Dhabi, United Arab Emirates, 8-10 November. SPE-57553-MS. http://dx.doi.org/10.2118/57553-MS .
Harms, D.A. 1994. Coiled-Tubing Completion Procedure Reduces Cost and Time for Hydraulically Fractured Wells. Presented at the SPE Western Regional Meeting, Long Beach, California, 23-25 March. SPE-27892-MS. http://dx.doi.org/10.2118/27892-MS .
Heijnen, W.H.P.M. 1989. A New Wellhead Design Concept. Presented at the Offshore Europe, Aberdeen, United Kingdom, 5-8 September. SPE-19252-MS. http://dx.doi.org/10.2118/19252-MS .
Holand, P. 2001. Reliability of Deepwater Subsea Blowout Preventers. SPE Drill & Compl 16 (1): 12-18. SPE-70129-PA. http://dx.doi.org/10.2118/70129-PA .
Huntoon II, G.G. 1994. A Systems Approach to Completing Hostile Environment Reservoirs. Presented at the International Petroleum Conference and Exhibition of Mexico, Veracruz, Mexico, 10-13 October. SPE-28738-MS. http://dx.doi.org/10.2118/28738-MS .
Kenda, W.P., Allen, T.J., and Herbel, R.R. 2003. Offline Subsea Wellhead MODU Operations Provide Significant Time Savings. Presented at the SPE/IADC Drilling Conference, Amsterdam, Netherlands, 19-21 February. SPE-79834-MS. http://dx.doi.org/10.2118/79834-MS .
Landeck, C.R. 1996. Application of Stacked Template Structures Offshore Indonesia. Presented at the SPE Asia Pacific Oil and Gas Conference, Adelaide, Australia, 28-31 October. SPE-37033-MS. http://dx.doi.org/10.2118/37033-MS .
McLeod, S. and Harlety, F.J. 2001. Drilling Technology Part 1: Poseidon 29,000-ft well in 4,800-ft depths harbinger of future for US Gulf. Offshore Magazine. 61 (4): 56.
McLeod, S. and Hartley, F.J. 2001. Drilling Technology: Part II: Positive and negative events in drilling of Poseidon 29,750-ft well. Offshore Magazine. 61 (5): 68.
Nikravesh, M., Soroush, M., Johnston, M.R. et al. 1997. Design of Smart Wellhead Controllers for Optimal Fluid Injection Policy and Producibility in Petroleum Reservoirs: A Neuro-Geometric Approach. Presented at the International Thermal Operations and Heavy Oil Symposium, Bakersfield, California, 10-12 February. SPE-37557-MS. http://dx.doi.org/10.2118/37557-MS .
Schulz, R.R., Stehle, D.E., and Murall, J. 1999. Completion of a Deep, Hot, Corrosive East Texas Gas Well. SPE Prod & Oper 14 (2): 150-157. SPE-14983-PA. http://dx.doi.org/10.2118/14983-PA .
Tuah, J.B., Rujhan, M., Mat, B. et al. 2000. Triple Wellhead Technology in Sarawak Operations. Presented at the Asia Pacific Oil and Gas Conference and Exhibition, Brisbane, Australia, 16–18 October. SPE-64277-MS. http://dx.doi.org/10.2118/64277-MS .
Watson, P., Kolstad, E., Borstmayer, R. et al. 2003. An Innovative Approach to Development Drilling in Deepwater Gulf of Mexico. Presented at the SPE/IADC Drilling Conference, Amsterdam, The Netherlands, 19–21 February. SPE-79809-MS. http://dx.doi.org/10.2118/79809-MS .
Wei, J. 2000. Technique for Close Cluster Well Head Concentrated High Quality and High Speed Drilling Cementing Surface Interval in Sz36-1d. Presented at the IADC/SPE Asia Pacific Drilling Technology, Kuala Lumpur, Malaysia, 11-13 September 2000. SPE-62776-MS. http://dx.doi.org/10.2118/62776-MS .
We are grateful to our generous sponsors for their assistance in building and supporting PetroWiki.
Who We Are
Newsroom
Careers
Investors
Sustainability
New Energy
Search
Sign In
Contact
Characterization
Well Construction
Completions
Production
Intervention
Insights
Resource Library
Locations
Software
Seismic
Borehole Seismic
Geosolutions Software
Multiclient Data Library
Survey Design and Modeling
Seismic Data Processing
Seismic Imaging
Multiphysics
Seismic Reservoir Characterization
Seismic Drilling Solutions
Surface and Downhole Logging
Mud Logging
Cuttings Analysis
Logging While Drilling (LWD)
Optiq Schlumberger Fiber-Optic Solutions
Wireline Openhole Logging
Wireline Cased Hole Logging
Digital Slickline
Reservoir Testing
Surface Testing
Zero-Flaring Well Test and Cleanup
Downhole Reservoir Testing
Flowback Testing
Well Test Design and Interpretation
Reservoir Sampling
Muzic Wireless Telemetry
Rock and Fluid Analysis
Reservoir Laboratories
Outdoor Cum Facial
Wanking Outdoor
Rus Nudist