Wellhead Penetration
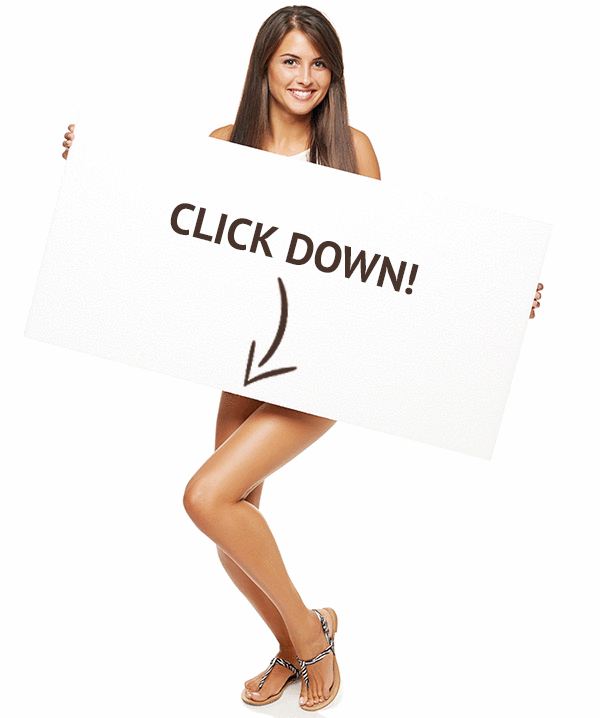
🔞 ALL INFORMATION CLICK HERE 👈🏻👈🏻👈🏻
Wellhead Penetration
Home Surface Equipment ESP Wellhead Equipment Electrical Connector Systems (Wellhead Penetrators)
RELIABLE
The lower penetrator is the key to the reliability of COSCO Connector Systems. It’s unique design eliminates the need for a connection in the annulus, thereby eliminating a weak spot. Corrosion resistant stainless steel is used for the housing and flange of the connector. The electrical conductors are insulated by an inner Viton seal and an external Torlon face block. These components work in conjunction to provide superior protection from corrosive well-bore fluids and pressure damage.
EASY TO INSTALL
The lower penetrator bolts to the bottom of the tubing hanger by means of a flange. The upper connector bolts into the top of the electrical port located on the tubing hanger. The lower connector bolts into the bottom port in a similar manner. Each connector is secured in place by means of a flange and four bolts. The lower connector pigtail is spliced to the down hole power cable. No special tools are required for installation.
LOW PROFILE DESIGN
COSCO wellhead penetrator systems allow a lower profile x-mas tree assembly. The side entry system is specifically designed for applications where low tree profiles are critical, such as offshore applications.
VERSATILE
COSCO connectors can be installed into most existing wellhead equipment for conversion to Electrical Submersible Pumps systems, or to replace other types of electric feed-through systems.
R Series Gasket
Pack-off Bushing
ESP Wellhead
Tubing Head Adapter
Tubing Hanger
API 6A
Lock Down Screws
Secondary Seal
North American made
ESP Flat Cable Extension
Made in Canada
Seal Nipple
Transition Sleeve
Gasket
Oval Ring Joint Gasket
API 6A Gaskets
ESP Motor Lead Cable
Flat Cable Extension
FCE
MLC
Motor Lead Cable
MLE
Cable Splicing Materials
540 series
copper splicing sleeves
EFT
ESP Motor Controller
Electrical Connector System
ESP Flat Cable
ESP Power Cable
API 6A Wellhead
456 series
Electric Feed-through
esp splicing tape
electrical splicing tape
Canadian Oilwell Systems Company Ltd.
9760-60 Avenue NW Edmonton Alberta Canada T6E 0C5
Ph: 780-430-0840 email: sales@coscoltd.com
COSCO manufactures a complete line of rugged Electric Feed-thru Systems (Penetrators) for wellheads used in Electrical Submersible Pump Applications. COSCO connector systems represent the utmost in reliability, simplicity, versatility, and convenience. COSCO wellhead penetrators are adaptable to any application, onshore or offshore under the harshest conditions.
Several different options are available to meet any need:
Skip to main content Enable accessibility for visually impaired Open the accessibility menu
Houston, TX, USA: + 1-281-476-9100 | Dubai, UAE: +971 56 774 3242
Cayman ™ Fail-Safe Wellhead Penetrator
Field-attachable and rebuildable system
Black anti-corrosive/anti-galling finish
Floating seal
Dual opposing cable seals for mirrored protection
Redundant pressure barriers
Compatible with BOP test running tools
Compatible with various ESP cable sizes
5,000 psi (proof tested to 7,500 psi)
5kV (proof tested to 20kV)
180A (depending on cable size)
Up to 350° F (175° C) depending on operating requirements and conditions
Haz-Loc surface LB configurations available
1-3/4″ slim profile (can be configured for other profiles as well)
POWER FEED-THRU SYSTEMS & CONNECTORS LLC
Houston, TX, USA 1-866-819-9100 • 1-281-476-9100
Dubai, UAE +971 56 774 3242
PFT’s field-attachable Cayman TM Fail-Safe* Penetrator represents an advance in safety with benefits to both field operators and the environment. The penetrator is equipped with a mechanical means of retention within the tubing hanger, as well as a mechanism to allow the ESP cable to pull away under a prescribed load. In the event of a downhole failure of the production tubing, seal barriers remain in place and well control is maintained. Comparable systems currently in use offer no means of retention. In the event of a tubing failure the entire penetrator will be pulled from the tubing hanger, leaving an open pathway for wellbore fluids to escape to the atmosphere. Such circumstances may jeopardize public safety, as well as damage the surrounding environment.
PEEK ™ Insulator PEEK ™ is well suited for all downhole applications. Depending on the material grade, PEEK ™ can work continuously at 260° C (500° F). PEEK ™ , in comparison to molded rubber, does not take a “set” when put into compression nor is it subject to gas penetration.
Cable Seal Assembly Our innovative “floating” cable seal design incorporates the latest technology in elastomers with the ability to adjust to thermal expansion and decompression.
Connector Body Parts Components are carbon steel and meet NACE MR0175 specifications. The black finish provides maximum corrosion protection as well as lubrication for the threaded components.
While the matching thread profiles on some PFT components may allow them to be connected to products supplied by other manufacturers, PFT does not advocate or recommend this practice. Mating PFT products with those from other manufacturers violates PFT product warranties, and invalidates any and all safety certifications for that product.
Serving global exploration and production.
©2022 Power Feed-Thru Systems & Connectors LLC – All rights reserved.
All text graphics, audio and video are copyright of Power Feed-Thru Systems & Connectors LLC. Any redistribution or reproduction of any materials contained herein is strictly prohibited.
* = Covered by U.S. and foreign patents
PFT, BLACK GATOR, GATOR GRRIP, GATOR LOC, GATOR FEED, GATOR SPLICE, GATOR-PAK, TRI-GATOR and I-SEAL are trademarks or registered trademarks of Power Feed-Thru Systems & Connectors LLC. GATOR GRRIP, GATOR FEED, GATOR SPLICE and TRI-GATOR are covered by U.S. and foreign patents. PEEK is a trademark of Victrex PLC. AFLAS is a registered trademark of the Aashi Glass Co. Ltd. Viton is a registered trademark of DuPont Performance Elastomers L.L.C. All other trademarks are the property of their respective owners.
NOTICE: Power Feed-Thru Systems & Connectors, LLC (aka PFT Systems) It has come to our attention that certain unknown parties have been perpetuating a SCAM pretending to be PFT and soliciting various individuals and offering positions and/or training classes or to purchase equipment. Please be advised Power Feed-Thru Systems & Connectors LLC (PFT Systems) DOES NOT and never will solicit employees via the internet or our website nor, would we encourage individuals to take training classes or purchase equipment under any circumstances.
Выбрать язык русский азербайджанский аймара албанский амхарский английский арабский армянский ассамский африкаанс бамбара баскский белорусский бенгальский бирманский болгарский боснийский бходжпури валлийский венгерский вьетнамский гавайский галисийский греческий грузинский гуарани гуджарати датский догри зулу иврит игбо идиш илоканский индонезийский ирландский исландский испанский итальянский йоруба казахский каннада каталанский кечуа киргизский китайский (традиционный) китайский (упрощенный) конкани корейский корсиканский коса креольский (гаити) крио курдский (курманджи) курдский (сорани) кхмерский лаосский латинский латышский лингала литовский луганда люксембургский майтхили македонский малагасийский малайский малаялам мальдивский мальтийский маори маратхи мейтейлон (манипури) мизо монгольский немецкий непальский нидерландский норвежский ория оромо панджаби персидский польский португальский пушту руанда румынский самоанский санскрит себуанский сепеди сербский сесото сингальский синдхи словацкий словенский сомалийский суахили сунданский таджикский тайский тамильский татарский телугу тигринья тсонга турецкий туркменский узбекский уйгурский украинский урду филиппинский финский французский фризский хауса хинди хмонг хорватский чви чева чешский шведский шона шотландский (гэльский) эве эсперанто эстонский яванский японский Google Site Translate Form
Selection guidelines for wellhead equipment
This article describe the design and selection criteria necessary in the construction of safe and cost effective Wellheads and Christmas trees.
The objective of standardizing wellhead design is to obtain a cost effective completion of the well and ease of well maintenance.
Wellheads have traditionally been of the individual spool type. The spool type wellhead offered flexibility because it was relatively easy to add or omit casing strings. However to further enhance safety and rig time saving, wellhead design evolved from the spool type wellhead to the compact wellhead.
The compact wellhead is a technically superior design which offers enhanced safety and rig time savings without incurring a direct cost penalty. The design of compact wellheads is constantly evolving and there are now several variations available on the market.
Note that BOP protection is an essential factor of wellhead design which should never be underestimated particularly in the workover situation .
As a result of potential safety hazards the wellhead configurations should be such that it is not necessary to remove the BOP after cementing. The wellhead most traditionally used in the drilling industry has been of the individual spool type. With these types of wellhead the BOP has to be removed each time a casing is cemented thereby relying on the cement to seal the annulus and on the float equipment to seal the inside of the casing.
Experience has shown that the cement does not always reach the hydrocarbon-bearing formations resulting in either "roping" of the cement or micro annuli; as indicated by annular pressures. Similarly, the float equipment, which is seldom designed to act as a hydrocarbon barrier, can be eroded or pumped through.
To improve the safety and cost effectiveness of wellhead operations the BOP should be designed so that it has to be run only once and all casings, hangers, seal assemblies and tubings can be run through it (unitised wellheads). This design results in rig time saving and enhanced safety not only of the well but also of personnel as it requires less heavy-lifts and work under the BOP.
A wellhead is the crossover between a BOP or Christmas tree and the various casings of the well. For design purposes the wellhead, tree and casings should be considered as pressure vessels, which have to be hydrocarbon tight. This is complicated by the many penetrations, outlets, inspection ports and large through bore connections.
There are several variations of the compact type of wellhead and the final choice will depend on the category of well and its unique characteristics such as pressure, flow, etc. Also if it is an onshore or offshore well.
Wells can be divided into the following six categories:
The following types of well are defined as "specialist":
One of the main advantages of the compact wellhead, also know as the unitised wellhead, is its reduced height; which is one of the requirements of the selection criteria.
To make wellheads fire resistant by "add ons" is not recommended. The preferred approach is to design fit for purpose fire resistant wellheads.
Prior to selection the following aspects should be considered:
·It is possible that weakness of the wellhead systems can be concealed. This situation can occur when the formation evaluation is carried out using Drill Stem Tests which bypass the casing and head. This practice is unlikely to reveal any weaknesses as most exploration wells do not become 'production' wells.
·The casing scheme finally selected will impose a number of restrictions on the wellhead design, such as pressure rating, tie-in points, etc.
·The selected BOP system will have an impact on the upper connection style.
·It is important that both drilling and production requirements are reconciled in the design phase to maximise operating performance.
Selection of wellhead equipment usually involves the following departments/personnel:
·Exploration and Production who provide data for the objectives.
·Production department (Technology and Well Services) who define the production, testing, and completion requirements.
·Driller or Production Operator who finally selects the wellhead.
Normally the wellhead is selected by Drilling Personnel, based on the interpretation of the forecast by the Exploration team.
In the past the standard practice was to develop a field with the back-up exploration wellhead. This practice was based upon the availability of equipment and a propensity towards standardisation.
The completion, normally designed by a Production Technologist, was then added to the Exploration Wellhead. Unfortunately the exploration wellhead was selected on the basis of information yet to be validated, and, very often, with short term seal design. As a result the exploration wellhead was only guaranteed hydrocarbon tight for a short period of time and therefore became the weakest part of the construction. The tubing, tubing hanger and Christmas tree were then relied upon for the integrity of hydrocarbon containment.
It is recommended to select the production casing of a well on the same engineering criteria as the testing/production tubing and in accordance with casing design standards. The completed well is then subjected to either a Production Test or a Drill Stem Test.
The same practice that has been adopted for testing/production tubing has been applied to the design of wellheads. The benefits of this practice are that in the event of a discovery the wellhead used for exploration is also suitable for permanent completion with less functional limitations and reduced chances of future interventions.
The design should be in accordance with the following standards:
The selection of a wellhead depends on the objectives of the well and its completion requirements, such as pressure rating, tie-in points, wellhead bore, etc.
The selection criteria must include the following:
·Technical specifications; Reliability and Completability.
·Maintenance requirements; Repeatability, Retrievability, Side-track ability, and Tie-back ability.
Ranking of the different available alternatives in order of priority varies with each application. Standardisation is further hampered by the different casing schemes, bore size and pressure rating as well as modern tighter casing schemes and slimhole drilling.
In the past the importance of completability and maintainability have often been overlooked by designers. It is therefore recommended to adopt a standardised approach to design. This does not mean all future wellheads should be identical. It does mean that such an approach to design will determine the objectives and allow the incorporation of any new engineering developments that will achieve those objectives by the most cost effective methods.
The wellhead used during offshore appraisal drilling with a floating rig cannot be used during the platform development phase. Therefore the wellhead must be selected to suit the field under development.
The main designs are compact type wellheads which are available under the following trade names:
Compact wellheads reduce the height of the assembly significantly and allow the use of smaller valves and lighter assemblies which reduce the costs. However, smaller valves are a disadvantage when a well has to be killed by pumping.
When considering wellhead selection for onshore, the exploration and development situations are different to those offshore. For onshore, there is a tendency to extend the use of the wellhead used in exploration and appraisal, into development as it is usual for the exploration and development of onshore drilling to be performed in a back to back sequence with the same rig. Hence the popularity of the flexible spool type heads in spite of their shortcomings.
However, the experience indicates that in using uniheads, it is not necessary to make any distinction in design - provided that the unihead is maintainable - they offer enough flexibility with enhanced safety and rig time savings. Therefore it is recommended to design the wellhead for both exploration/appraisal and development. Although the operational flexibility is reduced this is considered a minor disadvantage when measured against the overall benefits.
ISO-9000 is the international standard for quality assurance.
During the design and fabrication stages it is advisable that Quality Control Surveyors, End Users, and Vendors Service Engineers are systematically and regularly consulted.
Selecting seals is an important aspect of wellhead design as a wellhead relies heavily on seals for its pressure integrity. The leakage rate acceptable should always be clearly stated to vendors to ensure they comply with the required standards. Failure to do this may result in vendors using their own acceptable leakage rates which may vary to suit their needs. For example 700 kPa (100 psi)/3 minutes is a common standard.
In the nuclear industry zero leakage is any leak rate below 0.00000001 cm3/second of helium at atmospheric pressure. NASA and the aerospace industry define their upper limits as 0.0014 cm3/seconds of Nitrogen at 2000 kPa (300 psi) and ambient temperature.
For tubular premium connections to be acceptable, a limit of 0.001 cm3/second is normally set. This aims at avoiding significant annular pressures in a ten year completion. (The accuracy of the Helium detector normally used is 0.0001 cm3/second).
When considering the seals to be selected for the wellhead(s) there are three main types of seals on the market. These are the:
·Polymeric or resilient seals. Which are either elastomeric (natural or synthetic rubbers) or plastomeric e.g. Teflon.
·Metal encapsulated polymeric seals. Which are a combination of the first two types.
Static Metal to Metal seals require greater precision and attention to detail during installation but once satisfactorily tested they have a longer lifespan.
Polymeric seals are less predictable than metal seals as they often seal on installation but can fail soon afterwards.
The metal encapsulated polymeric seals are in certain cases an acceptable compromise. They are almost as forgiving as the elastomer seals and last longer, as the endless anti-extrusion devices minimise the contact with well bore fluids.
The recommendation is to use metal to metal seals; metal encapsulated polymer seals should only be used for pressures below 28,000 kPa (4
Mature Lingerie Vintage
Mature Video Hd
Hentai Cosplay Masturbate