Вращающаяся печь для обжига портландцемента по мокрому способу. Курсовая работа (т). Физика.
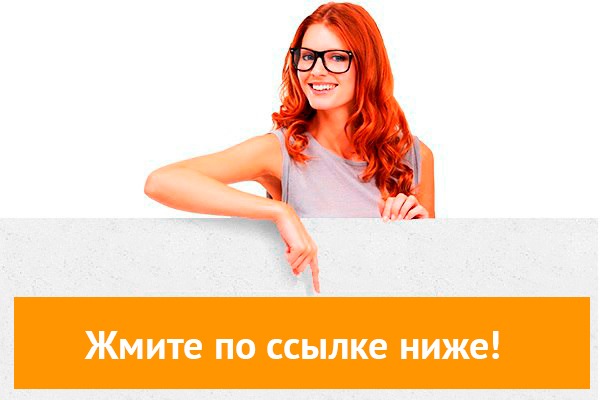
👉🏻👉🏻👉🏻 ВСЯ ИНФОРМАЦИЯ ДОСТУПНА ЗДЕСЬ ЖМИТЕ 👈🏻👈🏻👈🏻
Вы можете узнать стоимость помощи в написании студенческой работы.
Помощь в написании работы, которую точно примут!
Похожие работы на - Вращающаяся печь для обжига портландцемента по мокрому способу
Скачать Скачать документ
Информация о работе Информация о работе
Скачать Скачать документ
Информация о работе Информация о работе
Скачать Скачать документ
Информация о работе Информация о работе
Скачать Скачать документ
Информация о работе Информация о работе
Скачать Скачать документ
Информация о работе Информация о работе
Скачать Скачать документ
Информация о работе Информация о работе
Скачать Скачать документ
Информация о работе Информация о работе
Нужна качественная работа без плагиата?
Не нашел материал для своей работы?
Поможем написать качественную работу Без плагиата!
Пояснительная записка к курсовому проекту
Вращающаяся печь для обжига портландцемента по мокрому способу.
В силикатной промышленности,
охватывающей цементное, керамическое, стекольное и другие виды производств,
основными технологическими процессами являются обжиг, сушка или плавление
шихтовых материалов. Промышленные печи относятся к очень важному
производственному оборудованию, отличающемуся сложностью тепловых,
аэродинамических и химических процессов, происходящих в них.
В современных условиях значительно
возросла мощность заводов силикатной промышленности, а вместе с этим мощность,
размеры и производительность печей, оснащенных средствами автоматизации.
Значительно усовершенствовались конструкции печей и сушил за счет применения
новых теплообменных, топливосжигающих и других устройств и печных элементов.
Более сложной стала и эксплуатация таких печей, требующих точного регулирования
тепловых процессов, высококвалифицированного обслуживания.
В печах и сушилах силикатной
промышленности осуществляются весьма сложные технологические процессы,
связанные с сушкой и обжигом материалов и изделий, а также с расплавлением
шихтовых материалов, например для получения цементного клинкера.
Промышленная печь как тепловой
аппарат отличается тем, что в ней получают тепловую энергию за счет сжигания
топлива (или за счет электрической энергии электропечей) и передают ее
материалам или изделиям, подвергаемым тепловой обработке. Основными
теплотехническими процессами являются процессы сжигания топлива и
теплопередачи, происходящие часто одновременно в рабочем пространстве печи. При
этом большую роль играет создание необходимых условий для движения газов
(аэродинамика).
Основным принципом проектирования
современных печей служит непрерывность производственных процессов тепловой
обработки материалов или изделий и высокая производительность.
При проектировании печей необходимо
учитывать, что к ним предъявляются определенные теплотехнические и
технологические требования:
достаточно высокая тепловая
мощность, обеспечивающая данную производительность;
в рабочем пространстве печи должны
быть достигнуты необходимые температуры, соответствующие технологическому
режиму производства;
наиболее эффективное сжигание
подаваемого в печь топлива, высокий коэффициент использования топлива,
минимальный удельный расход тепла на обжиг или другой тепловой процесс;
высокая удельная производительность,
высокое качество выпускаемой продукции при заданной производительности;
наибольшая экономичность в
эксплуатации, легкость и простота в обслуживании;
наибольшая продолжительность работы
без ремонтов, т.е. высокая стойкость огнеупорной кладки при воздействии высоких
температур;
печь должна быть автоматизированным
тепловым агрегатом.
При проектировании всегда стремятся
к тому, чтобы печь наиболее полно удовлетворяла этим требованиям. Однако
существующие типы печей почти всегда имеют какие-либо конструктивные и
эксплуатационные недостатки. Поэтому непрерывно происходит совершенствование
существующих типов печей и разработка принципиально новых конструкций на базе
научных исследований и практики работы действующих печных установок.
В производствах спекаемых материалов
- цементного клинкера, шамота, металлургических магнезита и доломита - ведущую
роль играют вращающиеся печи. В цементной промышленности наиболее
распространены вращающиеся печи с внутренними теплообменными устройствами для
мокрого способа производства. Современные вращающиеся печи имеют колосниковые
холодильники для охлаждения обожженного продукта.
1. Вращающаяся печь:
особенности строения, принцип работы
Вращающиеся печи, используемые для
получения цементного клинкера, работают по принципу противотока. При мокром
способе производства шлам подаётся в печь со стороны её верхнего (холодного) конца,
а топливно-воздушная смесь, сгорающая на протяжении 20 - 30 м длины печи,
вдувается со стороны нижнего (горячего) конца. Горячие газы движутся навстречу
материалу, нагревая его до требуемой температуры.
Вращающаяся печь (трубчатая печь,
барабанная печь), промышленная печь цилиндрической формы с вращательным
движением вокруг продольной оси, предназначенная для нагрева сыпучих материалов
с целью их физико-химической обработки. Вращающиеся печи различают: по принципу
теплообмена - с противотоком и с параллельным током газов и материала; по
способу передачи энергии - с прямым, косвенным (через стенку муфеля) и
комбинированным нагревом обрабатываемого материала. По назначению различают
вращающиеся печи для спекания шихт в производстве глинозёма, получения цементного
клинкера, окислительного, восстановительного, хлорирующего обжига, прокалки
гидроокиси алюминия, кокса, карбонатов, сульфатов и др., обезвоживания
материалов, извлечения цинка и свинца (вельц-печи), получения железа или
сплавов цветных металлов их прямым восстановлением из руд в твёрдой фазе
(кричные печи), обжига огнеупорного сырья и др.
Основными являются вращающиеся печи,
в которых сжигается пылевидное, твёрдое, жидкое или газообразное топливо
непосредственно в рабочем пространстве печи и греющие газы движутся навстречу
обрабатываемому материалу. Металлический барабан, футерованный огнеупорным
кирпичом, устанавливают под небольшим углом к горизонту на опорные ролики .
В ряде случаев диаметр барабана делают переменным по длине. Барабан приводят во
вращение (1-2 об/мин) электродвигателем через редуктор и открытую зубчатую
передачу. Шихту загружают со стороны головки. Сухую шихту подают механическими
питателями, а шихту в виде пульпы - наливом или через форсунки. Топливо (10-30%
от массы шихты) вводят через горелки (форсунки), помещённые в горячей головке.
Здесь же выгружают готовый продукт, направляемый в холодильник. Газы из
вращающиеся печи очищают от пыли (возгонов) в системе. Для улучшения условий
теплопередачи во вращающиеся печи встраивают различные теплообменные устройства
- перегребающие лопасти, полки, цепные завесы, насадки и т.д. С этой же
целью в ряде случаев футеровку печей выполняют сложной формы, например
ячейковой. Основные размеры вращающиеся печи варьируются в значительных
пределах: длина от 50 до 230 м , а диаметр от 3 до 7,5 м .
Производительность вращающейся печи достигает 150 т/ч (готового
продукта). Наблюдается тенденция к соединению вращающиеся печи с различными
теплообменными аппаратами, что позволяет при повышении технико-экономических
показателей работы печей уменьшать их размеры.
Вращающаяся печь (рис.
1), состоит из цилиндрического корпуса 1 , опирающегося через
бандажи 2 на опорные ролики 3. Корпус имеет уклон 3,5-4% и
вращается со скоростью 0,5-1,2 об/мин. Привод печи двойной и состоит из двух
электродвигателей 4 , двух редукторов 5, двух подвенцовых шестерен
и одного венцового колеса 6 .
В середине печи, на
одной из ее опор, устанавливается пара роликов (горизонтально) для контроля за
смещением печи вдоль оси (вниз или вверх).
Вспомогательный привод
включается в работу при ремонтах печи, в период
розжига и остановки,
когда печь должна вращаться медленно. Сырьевая мука
подается в питательную
трубу 7 при помощи ковшовых или объемных дозаторов, находящихся у
холодного конца печи. Со стороны головки 8 в печь подается топливо и
воздух; в результате сгорания топлива получаются горячие газы, поток которых
направлен от горячего конца печи к холодному - навстречу движущемуся материалу.
Для улучшения теплопередачи и обеспыливания газов внутри печи в холодном ее
конце размещается цепной фильтр-подогреватель 9 . Пыль, уловленная за
печью в результате газоочистки, возвращается обратно в печь. Она
транспортируется пневмонасосом в бункер, а из него при помощи периферийного
загружателя 10 направляется в полую часть печи, со стороны горячего
конца. Клинкер охлаждается в колосниково-переталкивающем холодильнике 11.
На печах корпус оборудован центральной системой смазки 12 .
Таблица 1 - Техническая
характеристика вращающейся печи
Предлагаемая вращающаяся печь с
рекуператорным холодильником предназначена для получения цементного клинкера по
«мокрому» способу производства.
В печи применены опоры на
подшипниках качения, что снижает расход электроэнергии, предусмотрены
эффективные цепная завеса и ячейковый теплообменник, позволяющие снизить расход
тепла на обжиг материала.
Плавное регулирование частоты
вращения печи обеспечивает оптимальный для технологического процесса режим
обжига, в результате увеличивается срок службы футеровок и снижается расход
топлива.
1.1 Технология мокрого
способа производства
На цементных заводах, работающих по
мокрому способу, в качестве сырьевых материалов для производства
портландцементного клинкера обычно используют мягкий глинистый и твердый
известняковый компоненты. В этом случае технологическая схема производства
цемента выглядит следующим образом:
Рисунок 2 - Технологическая схема
мокрого способа производства
Начальной технологической операцией
получения клинкера является измельчение сырьевых материалов. Необходимость
тонкого измельчения сырьевых материалов определяется тем, что однородный по
составу клинкер можно получить лишь из хорошо перемешанной сырьевой смеси,
состоящей из мельчайших частичек ее компонентов.
Куски исходных сырьевых материалов
нередко имеют размеры до 1200 мм. Получить из таких кусков материал в виде
мельчайших зерен можно только за несколько приемов. Вначале куски подвергаются
грубому измельчению, дроблению, а затем тонкому помолу. Для грубого измельчения
материалов применяют различные дробилки, а тонкое измельчение в зависимости от
свойств исходных материалов производят в мельницах или в болтушках в
присутствии большого количества воды.
При использовании в качестве
известкового компонента мела, его измельчают в болтушках. Если применяют
твердый глинистый компонент, то после дробления его направляют в мельницу.
Из болтушки глиняный шлам
перекачивают в мельницу, где измельчается известняк. Совместное измельчение
двух компонентов позволяет получать более однородный по составу сырьевой шлам.
В сырьевую мельницу известняк и
глиняный шлам подают в определенном соотношении, соответствующем требуемому
химическому составу клинкера. Однако даже при самой тщательной дозировке
исходных материалов не удается получить из мельницы шлам необходимого химического
состава из-за колебаний химического состава сырья одного и того же
месторождения. Чтобы получить шлам заданного химического состава, его
корректируют в бассейнах.
Для этого в одной или нескольких
мельницах приготовляют шлам с заведомо низким или высоким содержанием CаCO3
(называемым титром) и этот шлам в определенной пропорции добавляют в
корректирующий шламовый бассейн.
Приготовленный таким образом шлам,
представляющий собой сметанообразную массу с содержанием воды до 35-45%,
насосами подают в расходный бачок, откуда равномерно сливают в печь.
Для обжига клинкера при мокром
способе производства используют вращающиеся печи. Они представляют собой
стальной барабан длиной до 150-230 м и диаметром до 7 м, футерованный внутри
огнеупорным кирпичом; производительность таких печей достигает 1000-3000 т
клинкера в сутки.
Барабан печи устанавливают с уклоном
3-40 гр. шлам подают с поднятой стороны печи холодного конца, а топливо в виде
газа, угольный пыли или мазута вдувают в печь с противоположной стороны (горячего
конца). В результате вращения наклонного барабана находящиеся в нем материалы
продвигаются по печи в сторону ее горячего конца. В области горения топлива
развивается наиболее высокая температура: материала - до 15000 С, газов - до
17000 С, и завершаются химические реакции, приводящие к образованию клинкера.
Дымовые газы движутся вдоль барабана
печи навстречу обжигаемому материалу. Встречая на пути холодные материалы,
дымовые газы подогревают их, асами охлаждаются. В результате, начиная от зоны
обжига, температура газа вдоль печи снижается с 1700 до 150-2000 С. Из печи
клинкер поступает в холодильник, где охлаждается движущимся навстречу ему
холодным воздухом. Охлажденный клинкер отправляют на склад. В ряде случаев
клинкер из холодильника направляют непосредственно на помол в цементные
мельницы.
Перед помолом клинкер дробят до
зерен размером 8-10 мм, чтобы облегчить работу мельниц. Измельчение клинкера
производится совместно с гипсом, гидравлическими и другими добавками.
Совместный помол обеспечивает тщательное перемешивание всех материалов, а
высокая однородность цемента является одной из важных гарантий его качества.
Гидравлические добавки, будучи
материалами сильно пористыми, имеют, как правило, высокую влажность (до 20-30%
и более). Поэтому перед помолом их высушивают до влажности примерно 1%,
предварительно раздробив до зерен крупностью 8-10 мм. Гипс только дробят, так
как его вводят в незначительном количестве и содержащаяся в нем влага легко
испаряется за счет тепла, выделяющегося в мельнице в результате соударений и
истирания мелющих тел друг с другом и с размалываемым материалом.
Из мельницы цемент транспортируют на
склад силосного типа, оборудованный механическим (элеваторы, винтовые
конвейеры), пневматическим (пневматические насосы, аэрожелоба) или
пневмомеханическим транспортом.
Отгружают цемент потребителю либо в
таре - в многослойных бумажных мешках по 50 кг, либо навалом в контейнерах,
автомобильных или железнодорожных цементовозах, в специально оборудованных
судах. Каждая партия цемента снабжается паспортом.
1.2 Физико-химические
процессы, протекающие при тепловой обработке портландцемента
Образованию портландцементного
клинкера предшествует ряд физико-химических процессов, протекающих в
определенных температурных границах - технологических зонах печного агрегата -
вращающейся печи. При мокром способе производства цемента по ходу движения
обжигаемого материала условно выделяют следующие зоны: I - испарения, II -
подогрева и дегидратации, III - декарбонизации, IV - экзотермических реакций, V
- спекания, VI - охлаждения. Рассмотрим эти процессы начиная с поступления
сырьевой смеси в печь, т.е. по направлению с верхнего ее конца (холодного) к
нижнему (горячему).
В зоне испарения при постепенном
повышении температуры с 70 до 200°С испаряется влага; сырьевая смесь
подсушивается., Подсушенный материал комкуется. Перемещаясь, комья распадаются
на более мелкие гранулы. В печах сухого способа зона испарения отсутствует.
В зоне подогрева при постепенном
нагревании сырья с 200 до 700°С выгорают органические примеси, из глиняных
минералов удаляется кристаллохимическая вода (при 450…500°С) и образуется
безводный каолинит Al 2 0 3 -2Si0 2 . Зоны испарения
и подогрева при мокром способе занимают 50…60% длины печи. В зоне
декарбонизации температура обжигаемого материала повышается с 700 до 1100°С;
происходит диссоциация карбонатов кальция и магния с образованием свободных СаО
и MgO. Одновременно продолжается распад глинистых минералов на оксиды SiO2, Аl2O3, Fe2O3, которые вступают в химическое
взаимодействие с СаО. В результате этих реакций, происходящих в твердом
состоянии, образуются минералы ЗСаО-Fe2О3, СаО-А12O3 и частично 2CaO-SiO2.
В зоне экзотермических реакций при
температуре 1200… 1300°С завершается процесс твердофазового спекания материала,
образуются ЗСаО-Fe2О3, 4СаО-А12O3-Fе2O3 и белит, резко уменьшается количество свободной извести, но
достаточное для насыщения двухкальциевого силиката до трехкальциевого.
В зоне охлаждения температура
клинкера понижается с 1300 до 1000°С, здесь полностью формируются его структура
и состав, включающий алит C3S, белит C2S, C3A, C4AF, MgO (периклаз),
стекловидную фазу и второстепенные составляющие. Границы зон во вращающейся
печи достаточно условны и не являются стабильными. Меняя режим работы печи,
можно смещать зоны и регулировать тем самым процесс обжига.
Образовавшийся таким образом
раскаленный клинкер поступает в холодильник, где резко охлаждается движущимся
навстречу ему холодным воздухом. Клинкер, выходящий из холодильника вращающихся
печей с температурой около 100°С и более, поступает на склад для окончательного
охлаждения и вылеживания (магазинирования), где он находится до 15 дней. Если
известь содержится в клинкере в свободном виде, то в течение вылеживания она
гасится влагой воздуха. На высокомеханизированных заводах с четко
организованным технологическим процессом качество клинкера оказывается
настолько высоким, что отпадает необходимость его вылеживания.
Помол клинкера совместно с добавками
производят в трубных многокамерных мельницах.
Тонкое измельчение клинкера с гипсом
и активными минеральными добавками в тонкий порошок производится
преимущественно в сепараторных установках, работающих по открытому или
замкнутому циклу.
Эффективная работа трубной мельницы
обеспечивается охлаждением мельничного пространства путем его аспирации
(вентилирования). Благодаря аспирации производительность мельниц растет на
20…25%, уменьшается пылевыделение, улучшаются условия труда. Для интенсификации
помола вводят добавку - сульфитно-дрожжевую бражку (СДБ), при этом
производительность мельниц увеличивается на 20…30%.
На современных цементных заводах
помол портландцемента в открытом цикле проходит по следующей технологической
схеме. Клинкер, гипс и активные минеральные добавки со склада подаются в
бункера и дозируются тарельчатыми питателями. После измельчения цемент
поступает через цапфу мельницы в аспирационную шахту, а из нее в бункер цемента
и далее на склад. Мельничное пространство аспирируется, запыленный воздух
частично очищается в аспирационной шахте, а затем в циклонах и электрофильтре,
далее собирается шнеком и направляется в расходный бункер цемента. Недостатком
помола в открытом цикле является трудность получения цемента с высокой удельной
поверхностью (до 400…500 м 2 /кг).
Мельницы, работающие в замкнутом
цикле, дают более однородный по размеру зерен продукт большей удельной
поверхности (4000…5000 см 2 /г); замкнутый цикл помола включает
помольный агрегат и центробежный сепаратор, определяющий крупные зерна,
возвращаемые на домол в первую камеру, а тонкая фракция домалывается в третьей
камере, из которой выгружается готовый цемент. В полностью замкнутом цикле
материал проходит через сепаратор дважды.
В последнее время получает
распространение короткая трубная мельница, обычно двухкамерная, работающая в
замкнутом цикле с сепаратором.
Готовый портландцемент (с
температурой 100°С и более) пневматическим транспортом направляется в силосы
для охлаждения. После этого его расфасовывают по 50 кг в многослойные бумажные
мешки или загружают в специально оборудованный автомобильный, железнодорожный
или водный транспорт.
2. Теплотехнические
расчеты вращающейся печи
Основным топливом служит природный
газ из групп северных месторождений Западной Сибири. Транспортируется он по
газопроводу. Резервным топливо служит мазут. Для его использования имеется
циркуляционный магистральный мазутопровод от мазутного хозяйства комбината до
цеха, а также разводка его до каждой печи. В таблице 9 показан состав сухого
газа.
Топливо считается с коэффициентом
расхода воздуха α = 1,14. Воздух, идущий на горение, нагревается до температуры
700°С.
Принимаем содержание влаги в воздухе
1,0%. Пересчитаем состав сухого газа на влажный рабочий газ:
= СН 4 ∙(100-Н2О/100)
= 98,16∙(100-1/100) = 97,18
Определим теплоту сгорания газа по
следующей формуле:
Находим теоретически
необходимое количество сухого воздуха:
Находим теоретически
необходимое количество воздуха с учетом его
Действительное
количество воздуха при коэффициенте расхода α = 1,14:
сухого: Lα= 1,14∙9,4 = 10,716 м³/м³;
атмосферного: L´α = 1,14∙9,55
= 10,887 м³/м³
Определим количество и
состав продуктов горения при α = 1,14 по
формулам:
VС02
= 0,01 ∙(СО2+СН4+2С2Н6+3С3Н8+4С4Н10). (4)
VС02=0,01∙(0,05+97,18+2∙0,69+3+0,22+4∙0,05)
= 0,995 м³/м³
VН2О=0,01∙(Н20+2∙СН4+3∙С2Н6+4∙С3Н8+5∙С4Н10+0,16∙d∙Lα), (5)
где d - влагосодержание атмосферного
воздуха, d=10г/кгс. в.
VН2О=0,01∙(1+2∙97,18+3∙0,69+4∙0,22+5∙0,05+0,16∙10∙10,72)=2,166
м³/м³
VN2 = 0,79 ∙ 10,72 + 0,01 ∙ 0,81 =8,48 м³/м³
Общее количество
продуктов горения составляет:
Vα = 0,995 + 2,166 + 8,48 +0,276 = 11,917 м³/м³
Находим процентный
состав продуктов горения по формулам:
Составляем материальный баланс
процесса горения (таблица 4). Он необходим для определения количества воздуха,
пошедшего на горение, и продуктов сгорания в результате горения.
Таблица 4 - Материальный баланс
процесса горения
природный газ: СН4 = 97,18 ∙ 0,717 С2Н6 = 0,69 ∙1,356
С3Н8 = 0,22 ∙ 2,020 С4Н10 = 0,05 ∙ 2,840 СО2 = 0,05 ∙ 1,977
Н2О = 1,0 ∙ 0,804 Воздух: О2 =9,43 ∙ 21 ∙1,14 ∙1,429
69,678 0,936 0,444 0,142 0,099 0,804 322,603
продукт горения: СО2 = 0,995 ∙ 100∙ ∙1,977 Н2О
= 2,166 ∙ 100∙ ∙0,804 N2
= 8,48 ∙100 ∙1.251 O2
= 0,276 ∙100 ∙1,429 Невязка:
196,711 174,146 1060,848 39,440 -0,191
N2 = 198.03 ∙
1,14 ∙3,762∙ ∙1,251 Н2О = 0,16 ∙ 10∙10,72 ∙0,804
Невязка баланса составляет: (100∙0,191):1470,954
= 0,013%
Определим теоретическую температуру
горения. Для этого находим теплосодержание продуктов горения с учетом подогрева
воздуха до температуры 700°С при α =
1,14.
По i-t-диаграмме находим теплоту нагрева
атмосферного воздуха, iвозд = 960 кДж/м³.
Тогда iобщ = Qн/ Vα+Lα∙iвозд/Vα = 35509,84/11,917 +
10,887*960/11,917 = 3856,79 кДж/м³
По i-t-диаграмме при а = 1,14
теоретическая температура горения 1 теор = 2120°С, а калориметрическая
температура горения tк = 2308°С.
Определим калометрическую
температуру горения с помощью таблиц энтальпий, для этого задаемся температурами
t1 =
2200°С и t2 = 2300°С. Теплота продуктов горения для температур t1 и t2 определяется с помощью приложения.
СО 2 =
0,080∙5387,0 = 430,96; СО 2 = 0,080∙5658,7 = 452,70;
Н 2 О =
0,172∙4402,2 = 757,18; Н 2 О = 0,172∙4643,8 - 798,73;
N 2 = 0,716∙3289,3 =
2355,14; N 2 = 0,716∙3452,6 =
2472,06;
О 2 =
0,032∙3482,7 = 111,45; О 2 = 0,032∙3656,5
= 117,01;
il = 3654,73 кДж/м 3 . i2 = 3840,5 кДж/м 3 .
Следовательно,
3840,5> i общ <3654,73
∆t = 200,54∙100/186 = 108,
следовательно, tК = 2200+108 = 2308°С
Определим действительную температуру
горения при коэффициенте η=0,8:
iдейст = iобщ∙η = 3856,79∙0,8 = 3084,2 кДж/м³
Действительная температура горения
по i-t-диаграмме при α = 1,14 с учетом
диссоциации равна 1810°С.
. Выход продукции из вращающейся
печи с учетом безвозвратных потерь при транспортировке:
где q1 - процент безвозвратных потерь при
транспортировке;
Qгод - годовой объем выпуска продукции, т/год.
Масса безвозвратных
потерь при транспортировке:
где Δmпрк - потери при прокаливании, %.
. Подача сырья в печь с
учетом потерь при прокаливании:
. Подача сырья в печь с
учетом пылеуноса:
где q3 - процент всей уносимой пыли.
Масса уносимой пыли:
'3 = Q3 - Q2. (17)
. Подача сырья в печь с
учетом возврата пыли:
. Подача сырья в печь с
учетом влажности:
Масса воды, испаряемой в печах:
'5 = Q5 - Q4. (22)
Обобщенные данные сведем в таблицу
5.
Таблица 5 - Материальный баланс
сырья
Невязка баланса составляет: (100∙0):86665
= 0%
2.3 Расчет теплового
баланса вращающейся печи
где - тепло сгорания
топлива, кДж/м³;
. Тепло, вносимое подогретым
воздухом:
где Lα - действительное
количество воздуха, подаваемое для горения топлива, м³ /м³;
iвозд - теплосодержание воздуха, кДж/м³.
Считаем, что весь воздух,
необходимый для горения поступает в печь из холодильника с температурой 700°С.
По расчету горения топлива Lα = 10,887 м³/м³, iвозд = 960 кДж/м3, тогда
Qвозд = 10,887·960·В = 10451,52·В кВт
Физическое тепло холодного
природного газа не учитывается.
Qприх = Qг + Qвоз (25)
Qприх = 35509,84· B + 10451,52·В = 45961,36 · В кВт
. Тепло, затраченное на нагрев
обжигаемого материала:
Qм = P · Сk · tk - Pc· Сн ·tн , (26)
где Р - производительность печи по
сухому (обожженному) материалу, кг/с;
Рс - расход сухих шихтовых
материалов, кг/с;
Ck, tk - энтальпия (теплосодержание) материала в конце нагрева до конечной
температуры обжига, кДж/кг;
Cн, tн - теплосодержание материала в начале нагрева при начальной
температуре tн кДж/кг.
где ∆mпрк - потер массы при прокаливании.
Qм
= 2,6 · 1730 · 1,31 - 2,7· 10 ·0,912 = 5867,8 кВт
. Расход тепла на
испарение физической влаги, содержащейся в материале:
Qисп
= (2500 - 4,2· tн + )·Wвл, (28)
где Wвл - количество влаги, испаряемой из материала, кг/с;
,804 - удельная масса
водных паров, кг/м³;
tн
- температура влажных материалов, поступающих в печь,°С;
iуг
- теплосодержание водяных паров при iуг
= 600°С, кДж/м³.
Qисп
= (2500 - 4,2· 10 + )·1,8
= 4627,2 кВт
. Расход тепла на
химические реакции:
где qхим - теплота, расходуемая на физико-химические процессы 1 кг
исходного химического вещества в необожженном продукте, кДж/кг;
G - количество исходного химического вещества в материале,
загружаемом в печь.
G = 0,01 · n · Рс, (31)
где n - процентное содержание исходного
химического вещества в сухой массе материала, %;
Рс - количество сухого материала,
поступающего в печь, кг/с.
Теплота диссоциации: МgСО3 - 1310 кДж/кг, СаСО3 - 1780
кДж/кг
Qхим = 1310·50,64·0,027 + 1780·15,17·0,027 = 2520 кВт
. Потери с уходящими продуктами
разложения:
Qдис = 0,01·Рс· (0,4 · СаО+0,553·МgО) · iСО2, (32)
где МgО и СаО - содержание оксидов в
обожженном продукте, %
iСО2 - теплосодержание СO2 при tух = 600°С, iСО2 = 814,4 кДж/м
Qдис = 0,01·2,7·(0,4·14,7+0,553·75)·814,4= 1041,4 кВт
Принимаем общий унос сухого
материала 25%, степень теплоты декарбонизации безвозвратного уноса β = 0,3…0,6; принимаем β=0,5.
Общий унос тепла определяется по
формуле:
где G'ун - количество уносимой из печи сырьевой пыли, (процент от
расхода сухого сырья);
β
- степень полноты декарбонизации безвозвратного уноса для вращающихся печей.
Определим потери тепла с
пылью, уносимой с продуктами горения в атмосферу:
Qун = Gун · Сун · tух, (34)
где Cун - теплоемкость уносимой пыли, Cун = 1,6 кДж/кг∙град;
tух - температура уходящих газов,°С.
Расход тепла на декарбонизацию и
дегазацию уноса, выбрасываемого в атмосферу, определяется по формуле:
= ·
(29,64 · СаО + 17,0 · МgО),
(35)
где СаО и МgО - содержание оксидов в составе шихты, %;
- количество сухих и
сырьевых материалов в безвозвратном уносе, кг/с.
= 0,66·(29,64· 14,7+17,0·75,0)
= 1129,1 кВт
Продукты дегазации
уноса, уходящие с дымовыми газами определим по формуле:
Общие потери тепла с уносом
составляют:
Qун =
633,6 + 1129,1 + 52,07 =1814,77 кВт
6. Потери тепла с уходящими
продуктами горения:
дым = Vдым · iдым ·В, (38)
где Vдым - объем продуктов горения,
уходящих из рабочего пространства печи с учетом подсосов окружающего воздуха, м³/с.
где iдым - энтальпия продуктов горения
при температуре уходящих газов, кДж/м³.
Qдым = 11,917 · В · 866,3 = 10323,7·В кВт
. Потери тепла корпусом печи в
окружающую среду:
Qкор
= 0,15 · 35509,84 · B = 5326,48· B кВт
. Неучтенные потери
тепла вследствие неполноты горения топлива,
выбивания газов и
излучения через отверстия в головке печи:
Qнеуч
= 0,5·35509,84·В = 17754,92·В кВт
Составим уравнение
теплового баланса и определим расход топлива:
Qприх
= Qг + Qвозд = 35509,84· В +
10451,52· B = 45961,36 · B
кВт
Qрасх
= Qм + Qисп + Qхим +Qун +Qдис + Qдым + Qкор + Qнеучт (41)
Qрасх = 5867,8+4627,2+2520+1814,77+1041,4+10323,7·B+5326,48·B +
Удельный расход тепла, внесенное
топливом:
где 29300 - теплота
сгорания топлива, кДж/м³;
Р - секундная
производительность печи, кг/с.
Таблица 6 - Тепловой
баланс вращающейся печи
4. Потери с уходящими продуктами разложения
6. Потери тепла с уходящими продуктами горения 7. Потери в
окружающую среду 8. Неучтенные потери
Невязка баланса составляет: (100∙69,29):57892,3
= 0,12%
3. Контроль соблюдения и
регулирования режима работы вращающейся печи
Движение печи вниз осуществляется за
счет небольшой смазки бандажей. Для контроля положения печи существуют
контрольные ролики, для кратковременного удержания - кратковременные ролики.
Для предотвращения падения печи или схода печи с опорных роликов конечные
отсекатели, отключение электроэнергии. Кроме основного привода предусмотрен
вспомогательный привод для кратковременного поворота печи во время ремонта и
непрерывного вращения печи во время охлаждения и разогрева. Горячая печь должна
обязательно вращаться, иначе возникает прогиб корпуса между опорами.
Загрузка в печи и горны выгрузка из
них деталей должны быть максимально механизированы. Ручная загрузка ил выгрузка
деталей должны производиться с помощью специальных клещей и захватов, размеры и
форма
Похожие работы на - Вращающаяся печь для обжига портландцемента по мокрому способу Курсовая работа (т). Физика.
Реферат по теме Бухгалтерский учет и аудит расчетов по оплате труда в с/х
Словосочетание Контрольная Работа 8 Класс С Ответами
Курсовая работа по теме Психосексуальное развитие подроста
Текст Защиты Дипломной Работы Пример
Реферат по теме Мифы о гормонах ( предохранение от беременности)
Реферат по теме Средневековье и Возрождение: противоречивые образы культуры
Слова Для Вывода В Эссе
Сочинение На Тему Хорошие Привычки
Реферат по теме Основные виды национальной экономики
Москва Столица Нашей Родины Эссе
Заполнение Отчета Практики
Реферат по теме Классификация PR технологий
Кризис Образования Реферат
Реферат: Социально-политические взгляды Платона
Реферат: Художественная культура как особая область культуры
Реферат по теме География нефтяной промышленности
Сочинение: Федот Кадушкин - трагическая фигура своего времени (по роману И. Акулова «Касьян Остудный»)
Титульный Лист Реферата Сибупк
Реферат по теме Авиация Второй мировой войны
Отчет по практике по теме Пассивные операции ОАО 'Айыл Банк'
Похожие работы на - О значении первых впечатлений детства
Похожие работы на - Исследование использования производственных мощностей
Похожие работы на - Концепция шоппер-маркетинга