Via Hole
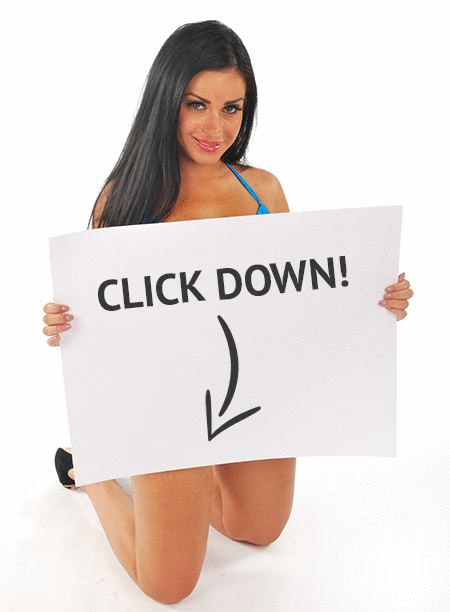
⚡ ALL INFORMATION CLICK HERE 👈🏻👈🏻👈🏻
Via Hole
Prototype PCB assembly
Turnkey PCBA
SMT Assembly
BGA Assembly
Low Volume PCB Assembly
High Volume PCB Assembly
Through Hole PCB Assembly
PCB usb Hub
Carbon Ink PCB
Ceramic PCB
Halogen Free PCB
Thick copper PCB
Rogers PCB
Multilayer PCB up to 50 layer
Single/double PCB
More +
Sign in
Join Free
Shopping Cart( 0 )
Company News
Industry Trends
Knowledge Base
Customer Feedback
Service Hotline:
0755-27492756
Open Hours:9:00-21:00
Email: JS@pcbasic.com
In most cases, we also call pcb via hole as the conductive hole. It is composed of two corresponding pads on different layers. Usually, we will electroplate it. That's pcb through-hole plating.
Vias can connect lines to each other and have higher requirements for surface mount technology. Therefore, the PCB industry has derived the Via Plugging process. To meet customer requirements, we must plug the PCB via hole. The traditional approach uses an aluminum sheet to fill the hole and white mesh for the solder mask. Time has proved that this method is stable and reliable.
But PCB Plug Via must meet the following conditions.
1. If there is copper in the via hole, the solder mask can be plugged or not.
2. The tin-lead thickness in the via hole should reach 4 microns. Be careful not to let the solder mask ink enter the hole, otherwise tin beads will appear.
3. Use solder mask ink to plug the hole and not transmit light.
Closer to home, PCB Plug Via has five functions.
1. Prevent tin from flowing into the component surface from the via hole during wave soldering and causing a short circuit. Especially for BGA pads, plugholes must be made first to facilitate soldering.
2. Avoid the solder resist residue in the pcb via hole.
3. The pcb, which helps to complete the assembly of the components, passes through the testing machine to form a negative pressure.
4. Prevent the virtual soldering caused by the inflow of solder paste from affecting the placement.
5. Avoid the PCB short circuit caused by the ejection of tin beads during wave soldering.
The surface mount technology of BGA and IC has stringent requirements for vias. For example, it must be flat, the difference between bumps and protrusions must not exceed one mil, and the edges must not be red. To achieve these requirements, various Via Plugging processes have appeared on the market. Now we have organized and summarized these Via Plugging processes. You can clearly see their advantages and disadvantages.
Its process is board surface solder mask→HAL→plug hole→curing. They use hot air to screed the flat surface and then use an aluminum sheet or ink screen. As for plugging ink, it is usually photosensitive ink or thermosetting ink. In addition, the plugging ink is preferably the same as the ink on the board surface. The advantage of this process is to ensure that the via hole does not drop oil. But the disadvantage is that the plug hole ink easily contaminates the board surface and makes it uneven. In addition, customers may experience false soldering during surface mounting. Therefore, many customers disapprove of this method.
Use a CNC drill to make a screen and plug holes in the aluminum sheet. The advantage is that the hole plugging of the via hole is complete. We can
choose thermosetting inks because it has the advantages of high hardness, a slight change in resin shrinkage, and good adhesion to the hole wall.
The process is: pre-processing → plug hole → grinding plate → pattern transfer → etching → board surface solder mask.
In this way, the hole plugging will be very smooth, and there will be no quality problems such as oil explosions and oil drops. But this method also has disadvantages: It only supports one-time thickening so that the copper thickness of the hole wall can reach the standard. Therefore, there are very high requirements for the performance of the whole plate copper plating and the plate grinding machine. We must ensure that the resin on the copper surface is completely removed during the operation without contamination. However, many PCB factories do not have a one-time thickening copper process, or the performance of the equipment does not meet the requirements. Therefore, it is not used much in PCB factories.
As above, first, use a drill to drill holes in the aluminum sheet. Then plug it on the screen printing machine. The point is that the residence time after completing the plug hole should not exceed 30 minutes. At this time, 36T silkscreen is used directly for the screen-printed board surface solder mask. The process is: pre-treatment-plug hole-silk screen-pre-baking-exposure-development-curing.
Then its advantage is that the oil cover of the via hole is good, and the plug hole is flat. More importantly, the color after the wet film is consistent. Because the via hole is not easy to be tinned after the hot air is leveled, and no tin beads appear in the hole. However, ink may appear in the hole on the pad after curing, resulting in poor solderability. In addition, the hot air leveling will cause bubbling and oil loss on the edge of the through-hole. Using this method to control products will be more difficult. Therefore, we recommend that engineers adopt specific processes and parameters to ensure the quality of plug holes.
Similarly, use a CNC drilling machine to drill out the plug holes of the aluminum sheet and then make a screen. Next, plug the hole. Usually, the plughole must be full, preferably with protrusions on both sides. After curing, grind the board again and perform the surface treatment. The process is pre-treatment-plug hole-pre-baking-development-pre-curing-board surface solder mask. The advantage is that the solidification plug hole can ensure that no oil will drop or explode. But HAL can also cause tin beads to be hidden in the plug hole. Moreover, it isn't easy to solve the situation that tin appears on the via hole. So many customers still do not accept this method.
In this process, we need to use a pad or a bed of nails to install the 36T screen on the screen printing machine. In other words, when the solder mask is completed, all the vias are plugged. Process: pre-treatment-screen printing-pre-baking-exposure-development-curing. Its process is concise, which can save us a lot of time. In addition, the through-holes after the hot air leveling can not lose oil or tin. We all know that a large amount of air will be left in the via hole if we use the silkscreen plug. In the subsequent process, curing will cause the air to expand and break through the solder mask. The pcb board surface will be uneven, there will be voids, and there will be a small amount of tin hidden in the via holes.
Nevertheless, PCBASIC company has basically solved these problems after a lot of adjustment work. The method is to choose inks of different viscosities and types and adjust the pressure of the silkscreen. Now our company uses this process for mass production. If you are looking for a PCB manufacturer, please contact us. We will surely satisfy you.
Copyright ©2012 - 2021 PCBasic Co., Limited All Rights Reserved.
Dear customers, Please kindly have an alert that according to our project experience, we foresee that many ICs will be in very tight supply or even out of stock for a long time, so please schedule your crucial projects of 2021 beforehand.
: For more details, please have an alert to this news, down load Electronic Components Price Increase Reminder_Weller Technology Co., Limited
Dear customers, Please kindly have an alert that according to our project experience, we foresee that many ICs will be in very tight supply or even out of stock for a long time, so please schedule your crucial projects of 2021 beforehand.
: For more details, please have an alert to this news, down load Electronic Components Price Increase Reminder_Weller Technology Co., Limited
+86 755 2828 2776
service@wellerpcb.com
Guidelines to via holes treatment method in PCB design
Home
Blog
Guidelines to via holes treatment method in PCB design
Laser drilling holes filling copper
Attachment: ( a .zip or .rar file, max 25MB )
An experienced and professional electronics contract manufacturer with core mission to provide high quality PCB assembly service to our 2000+ customers on the foundation of high technology PCB fabrication capabilities, such as HDI PCB, RF PCB, hybrid PCB, backplane PCB, heavy copper PCB, rigid-flex PCB, via in pad, stacked via, micro via, embedded copper coin technology etc
Like Us
on
facebook
Subscribe
To
RSS
Feeds
Copyrights © 2005 - 2022 All Rights Reserved by Weller Technology Co. Ltd.
Weller Technology has been providing Electronic Manufacturing Services (EMS) and Printed Circuit Board (PCB) assembly more than 10 years.
Weller has been focusing on prototypes and volume production of technologically advanced PCB assemblies,backplane PCB assemblies as well as electronics manufacturing services.
Weller’s experts in PCB fabrication & PCB assembly division is dedicated to providing complete customized manufacturing and engineering services to worldwide’s customer.
Except PCB assemblies,we are also a truly vertically integrated service provider in network communication,medical system,telecommunication, and industrial embedded system…
When you finish your PCB layout design and then you can send it to PCB manufacturers who provide custom circuit board service to have your PCB board manufactured. And, you can plan your final electronic PCB assembly after custom circuit board printing process finished.
Normally, the designer provides PCB Gerber and extra manufacturing specification document to manufactures for a better guideline to manufactures.
Firstly, the PCB manufacturer will review the electronic PCB purchase order with Gerber files and some special requirements for manufacturing specification document (If any).
Secondly, the engineers from PCB board house will perform regular DFM review such as “surface finishing, minimum via holes size, minimum track width/spacing, and whether customer’s PCB stackup is upon standard PCB thickness or not, etc”.
In this article we will focus on talking about the Via holes design issue frequently asked by manufactures.
So, it is very important to you to have your Gerber design match the information in your manufacturing specification document. Any mis-matched information will questionnaire the PCB manufacture’s engineer. Such as ” In the Gerber data, the via holes designed as solder mask plugging on both side but in your specification you require via holes to be not covered by Solder mask”
As we know via holes is usually referring to smaller size of PTH holes (generally,the via hole size are smaller than 0.6mm) to carry the conductive features in the loop of circuit diagram, which are not used for through hole components soldering.
Generally, the manufactures will be always following the designer’s original Gerber data with it’s manufacturing specification to manufacture the PCB board. Most of electronic PCB board designed as via holes plugged by solder mask (without solder mask openings on both sides) . Few of them designed as via holes with solder mask opening on top and bottom side.
The via holes are without solder mask openings both sides to all surface treatments is OK.
For ENIG (chemical gold/immersion gold) or OSP (Entek) , it is no problem for single side solder mask openings for via holes; also no problem with both sides solder mask opening for via holes.
For HAL (or HAL lead-free) , it is not good to design it as single side solder mask openings for via holes. Since solder from electronic PCB assembly may get trapped in holes and plug the via holes, the trapped soldering will take a potential risk of circuit shortage between via holes and tracks. If the via holes size is too small(smaller than 0.45mm), it is not good to design it as solder mask opening on both sides, as the soldering from PCB assembly process may plug the via holes, also soldering may plug the small NPTH holes(NPTH holes size smaller than 0.6mm, like the stamp holes some times are smaller than 0.6mm).
For immersion Tin or immersion silver , it is OK to design via holes as solder mask opening at both sides(top and bottom side). But it is not good to design it as single side solder mask openings (the other is plugging) for via holes, since the chemical liquid of immersion Tin or immersion Ag may get trapped in small via holes and survive to erode the hole copper, this will cause via holes lack of copper and take potential risk of open circuit.
Sometimes, there are some via holes are touched the solder mask openings pads, or partially overlapped with the solder mask openings pads. The partial older mask openings of via holes is not convenience to filling via holes with solder mask openings, and the solder mask may encroach the solder pads cause solder mask on pad,which will take extra problem to PCB assembly process. To avoid this :
If the solder mask overlapped pads smaller than 1/2 holes size, PCB manufacture house often suggest to shave the solder mask openings to get about 0.1mm away from via hole edge.
If the solder mask overlapped pads bigger than 1/2 holes size(or equals 1/2 holes size), engineers often suggest to add a whole solder mask opening(size bigger than via hole 0.1mm per side) for the via hole. If all via holes(hole size smaller than 0.7mm) are need to be filled by resin, there is no problem with all of above questions, but this increase the cost, and need extra production time (about extra 1-2 days).
If your PCB is HDI printed circuit boards with laser drilling holes in it, normally the HDI PCB manufacturer will plug the laser drilling holes filling copper and then plate copper over it to be shut up (as copper capped).
We’ll do our best to get back to you ASAP.
An experienced professional electronics contract manufacturer with core mission that to provide high quality PCB assembly service to our 2000+ customers at the foundation of high technology PCB's fabrication such as HDI,Via in Pad,RF,Hybrid PCB,Back planes,heavy copper PCB,rigid-flex PCB assembly,stacked via,micro via,embedded copper coin technology...
We are 24/7 available. Our expert staff is standing by to answer your questions. You can also contact by email: service@wellerpcb.com
From Wikipedia, the free encyclopedia
This article includes a list of general references , but it lacks sufficient corresponding inline citations . Please help to improve this article by introducing more precise citations. ( December 2017 ) ( Learn how and when to remove this template message )
The Wikibook Practical Electronics has a page on the topic of: PCB Layout#Holes
^ Through-holes per core. It is possible, though more expensive, to create blind or buried vias by using additional cores and lamination steps. It is also possible to backdrill and remove the plating from one side through to the desired layer, which leaves the physical hole as a through-hole, but creates the electrical equivalent of a blind via. If a PCB needs enough layers to justify blind and buried vias, it is probably also using small enough traces packed tightly enough to require (laser-drilled) microvias.
^ "PCB Vias: An In-Depth Guide" . ePiccolo Engineering .
^ "PCB design: A close look at facts and myths about thermal vias" .
^ Gautam, Deepak; Wager, Dave; Musavi, Fariborz; Edington, Murray; Eberle, Wilson; Dunford, Willa G. (2013-03-17). A review of thermal management in power converters with thermal vias . 2013 Twenty-Eighth Annual IEEE Applied Power Electronics Conference and Exposition (APEC). Long Beach, California, U.S.A: IEEE. doi : 10.1109/APEC.2013.6520276 .
^ "Castellated Holes / Edge Plating PCB / Castellations" . Hi-Tech Corp. 2011. Archived from the original on 2016-05-26 . Retrieved 2013-01-02 .
^ C. Hillman, Understanding plated through via failures, Global SMT & Packaging – November 2013, pp 26-28, https://www.dfrsolutions.com/hubfs/Resources/services/Understanding_Plated_Through_Via_Failures.pdf?t=1514473946162
^ C. Hillman, Reliable Plated Through Via Design and Fabrication, http://resources.dfrsolutions.com/White-Papers/Reliability/Reliable-Plated-Through-Via-Design-and-Fabrication1.pdf
^ "Plated Through Hole (PTH) Fatigue calculator" . DfR Solutions . Retrieved 2017-12-17 .
^ "Progress and Application of Through Glass Via (TGV) Technology" (PDF) . corning.com . Retrieved 2019-08-08 .
A via (Latin for path or way ) is an electrical connection between copper layers in a printed circuit board . Essentially a via is a small drilled hole that goes through two or more adjacent layers; the hole is plated with copper that forms electrical connection through the insulation that separates the copper layers.
Vias are important for PCB manufacturing. [1] This is because the vias are drilled with certain tolerances and may be fabricated off their designated locations, so some allowance for errors in drill position must be made prior to manufacturing or else the manufacturing yield can decrease due to non-conforming boards (according to some reference standard) or even due to failing boards. In addition, regular through hole vias are considered fragile structures as they are long and narrow; the manufacturer must ensure that the vias are plated properly throughout the barrel and this in turn causes several processing steps.
In printed circuit board (PCB) design, a via consists of two pads in corresponding positions on different copper layers of the board, that are electrically connected by a hole through the board. [ citation needed ] The hole is made conductive by electroplating , or is lined with a tube or a rivet . [ citation needed ] High-density multilayer PCBs may have microvias : blind vias are exposed only on one side of the board, while buried vias connect internal layers without being exposed on either surface. Thermal vias carry heat away from power devices and are typically used in arrays of about a dozen. [2] [3]
A via, sometimes called PTV or plated-through-via, should not be confused with a plated through hole (PT
9 Holes
French Lesbian Sex Videos
Strokes Handjob