Вакуумный электрический миксер для приготовления сплава 7075. Курсовая работа (т). Другое.
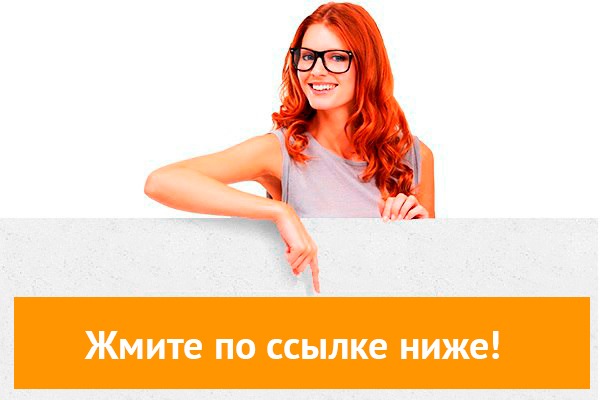
💣 👉🏻👉🏻👉🏻 ВСЯ ИНФОРМАЦИЯ ДОСТУПНА ЗДЕСЬ ЖМИТЕ 👈🏻👈🏻👈🏻
Вы можете узнать стоимость помощи в написании студенческой работы.
Помощь в написании работы, которую точно примут!
Похожие работы на - Вакуумный электрический миксер для приготовления сплава 7075
Нужна качественная работа без плагиата?
Не нашел материал для своей работы?
Поможем написать качественную работу Без плагиата!
.1 Государственные стандарты на
шихтовые материалы и готовую продукцию
.2 Описание сущности процесса,
обоснование рабочих параметров
.3 Выбор основного оборудования
(миксер). Описание конструкции
.5 Возможные виды брака, способы их
устранения
.6 Контроль основных параметров и
качества готовой продукции
.7 Требования безопасности при
обслуживании оборудования
2.2 Конструктивный расчет оборудования
Алюминий важнейший химический элемент. Легкий
металл, который имеет 13 номер в периодической системе Менделеева.
Алюминий обладает следующими физическими
свойствами: плотность 2,7г/см 3 ,температура плавления 685 0 С,
температура кипения 2500 0 С.
У алюминия высокая тепло и электропроводность,
хорошая пластичность и способность к сплавооброзованию. Оксидная пленка на
поверхности обеспечивает хорошую коррозионную стойкость на воздухе и вводе, в
контактах с нефтепродуктами и органическими веществами.
Обладая такими свойствами, алюминий по масштабам
применения занимает второе место после чёрных металлов.
Его применяют в электрод и радиотехнике в
качестве проводящего металла. Сплавы на основе алюминия применяют в авиации
ракето- и судостроение, машиностроение и т.д.
В данном проекте рассматривается сплав алюминия
с кремнием силумин.
Сплав 7075 - самый прочный из всех алюминиевых
сплавов: он включает в себя цинк и магний и широко используется в
аэрокосмической промышленности. Ученые постоянно работают над улучшением его
характеристик.
Исследуя взаимосвязь между свойствами этого
материала и его атомной структурой, ученые неожиданно обнаружили, что один из
образцов обладает гораздо большей прочностью и пластичностью, чем следовало
ожидать.
Чтобы выяснить причину этого неожиданного
успеха, исследователи использовали томографию с помощью атомного зонда, что
является новым словом в науке. Наночастицы сплава в несколько десятков
нанометров в диаметре поместили в раствор и наблюдали, как они взаимодействуют
между собой, и какая именно форма граней частиц позволяет создавать максимально
прочный.
В результате австралийские ученые выяснили, что
неожиданный скачок характеристик сплава обусловлен двумя факторами. Во-первых,
легирующие элементы расположились внутри зерен металла, что увеличивает
плотность дислокации металла. Во-вторых, объединение элементов зерен в кластеры
(группа взаимодействующих частиц, атомов или молекул) ограничивает рост нанокристаллов,
повышает прочность зерен и уменьшает хрупкость и старение сплава.
Изучение структуры материалов на наноуровне -
очень перспективное направление металлургии, так как позволяет понять связь
между характеристиками материала и его строением, а также определить пути
изменения его свойств. Но, к сожалению, распространенным методом сканирующей
электронной микроскопии редко можно получить изображение тех или иных связей в
структуре зерна в нужном масштабе.
Именно поэтому больше всего ученых впечатлил не
сам сплав, а новейший метод проектирования и контроля результатов, который
сулит огромные перспективы в создании уникальных материалов необходимых в
различных областях науки и техник.
Алюминий. Его плотность в твёрдом состояние (20 0 С)
2,7 гр./см 3 , а в расплавленном (800 0 С) 2,35гр./см 3 .
Плотность алюминиевых сплавов от 2,5 до 3,0 гр./см 3 . Температура
плавления технического алюминия 658 0 С. Хорошая теплопроводность и
электропроводность.
Кремний один из наиболее распространённых
легирующих компонентов сплавов на основе алюминия. Температура плавления 1440 0 С,
плотность 2,49 гр./см 3 . Обладает очень высокими механическими
свойствами.
Данный курсовой проект «Вакуумный электрический
миксер» для приготовления сплава 7075.
.1
Государственные стандарты на шихтовые материалы и готовую продукцию
Алюминиево-магниевые сплавы относятся к группе
термически, неупрочняемых алюминиевых деформируемых сплавов. В настоящее время
в промышленности нашла применение большая группа сплавов этой системы 7075 . Из
его изготавливают все виды полуфабрикатов: слитки и плиты, прессованные изделия
(прутки, профили, панели), поковки и штамповки, проволоку заклепочную и
сварочную.
Предел
прочности на растяжение (МПа)
Содержание компонентов в сплаве 7075 (5,1 - 6,1
Zn; 2,1 - 2,9 Mg; 1,2 -2,0 Си) аналогично их содержанию в сплаве В95 (5,1 - 6,1
Zn; 2,1 - 2,9 Mg; 1,2 - 2,0 Си). Основное различие в химическом составе
обусловлено разными добавками переходных металлов: сплав 7075 легирован Сг
(0,18 - 0,28 %), сплав В95 легирован Мп (0,2 - 0,6 %) и Сг (0,1 - 0,25 %).
Содержание в сплаве 7075 примесей Fe и Si не более 0,5 % и 0,4 %; в сплаве В95
- не более 0,4 % и 0,3 % соответственно. механических свойств термообработанных
плит осложняли и делали практически невозможным внедрение в серийное
производство проката крупногабаритных плит из сплава 7075 с ценными
эксплуатационными свойствами.
В литейных цехах по
производству алюминиевых сплавов шихтовыми материалами являются:
алюминий первичный в слитках
любых форм и размеров ГОСТ 11069-01, ГОСТ 11070-74, ГОСТ 19437-81, ТУ
48-5-278-87, а также жидкий алюминий ГОСТ 11069-74
Таблица 2 - Химический состав первичного
алюминия (ГОСТ 11070-00)
Таблица 3 - Химический состав первичного магния
(ГОСТ 804-76)
Таблица 4 - Химический состав меди (ГОСТ 859-78)
1.2
Описание сущности процесса, обоснование рабочих параметров
Металл из печи сливают на сухо, чтобы уровень
металла в печи не превышал 10 см, время слива составляет 10 минут;
рафинирование проводят для очистки металла от примесей время, рафинирование
составляет 30-60 минут в зависимости от сплава; шлак образуется в процессе
рафинирования, он находиться на поверхности зеркала металла и его сгребают из
миксера специальными гребками на снятие шлака требуется 10-15 минут;
отстаивание сплава и доводка температуры необходимы для получения требуемых
свойств сплава, время отстаивание 30-45 минут; литье производится на литейных
машинах до полного слива из миксера. Отливку слитков можно начинать после
полной готовности расплава, оснастки, инструмента и рабочего места.
Перед началом литья литейщик должен:
ввести поддон в кристаллизатор на высоту от 40
до 50 мм от нижней, кромки кристаллизатора, при использовании «теплых» поддонов
последние ввести в кристаллизатор на расстоянии от 40 до 50 мм от нижней части
втулки, которая закреплена в распределительной коробке;
просушить поддон и стенку кристаллизатора сжатым
воздухом или ветошью до полного удаления влаги;
при необходимости уплотнить зазор между поддоном
и кристаллизатором асбестовой тканью или стекловолоконным шнуром;
нанести тонким слоем на кристаллизаторы смазку;
включить воду, подаваемую в системы охлаждения;
подготовить лотки, распределительные сита и
распределительные кольца, фильтры из стеклоткани и установить их в рабочее
положение.
Отверстия втулок в процессе литья должны быть
погружены в расплав с таким расчетом, чтобы металл вытекал из отверстий под
покровом окисной плены. В процессе литья не допускается оголение рабочей
поверхности стеклоткани распределительного сита. Распределительное кольцо при литье
полых слитков должно обеспечивать подачу металла в зону равную половине толщины
стенки слитка и равноудаленную от стержня кристаллизатора. На всем протяжении
движения металла от летки до кристаллизатора должна быть обеспечена плавность
движения его под окисной пленкой. Круглые слитки складировать поплавочно в
стеллажи литниковой частью Равномерное распределение металла в кристаллизаторе
при литье плоских слитков осуществлять за счет фильтра-распределителя сшивного.
В процессе литья уровень металла в кристаллизаторе должен поддерживаться
постоянным. Постоянный уровень металла в кристаллизаторе поддерживается с
помощью регулятора поплавкового, пневморегулятора и распределительных поплавков
из асботермосиликата. Разрешается ручная регулировка с помощью стопора и пики.
В процессе литья при необходимости смазывать рабочую поверхность
кристаллизатора прогретой смазкой. Смазку подогревать на доливочной печи в
специальном сосуде. Запрещается производить обильную смазку.
В течение всего цикла литья литейщик обязан строго
выдерживать технологические параметры литья.
Разливку металла плавки необходимо производить в
возможно короткий срок.
Время нахождения металла в миксере от начала
заливки до конца литья должно быть не более 16 часов. При достижении заданной
длины слитков леточное отверстие перекрыть пикой, снять лоток, сита,
распределительную коробку с остатками жидкого металла. Рабочий ход литейной
машины отключить, когда литниковая часть слитка достигнет 1/2 высоты
кристаллизатора. Литниковую часть слитка очистить от шлака и окислов. После
полного затвердевания слитка перекрыть подачу воды. Выемку слитков производить
краном с помощью клещей или троса. Отлитые слитки складировать в литейном
пролете согласно планировкам к центральному проходу согласно планировке. При складировании
плавку разделять с помощью прокладок на части, не превышающие по массе 20 тонн.
После отливки каждого залива рабочую поверхность кристаллизаторов тщательно
протереть cyкoнным, асбестовым или другим грубым полотном. Перед каждым заливом
проверить надежность крепления поддонов и исправность рабочего хода литейной
машины. Слитки каждой отдельной плавки как правило должны складироваться в
отдельный стеллаж или в отдельную стопу. Допускается совместное складирование
не более двух плавок в один стеллаж с разделением плавок между собой
прокладками (кроме свинцово содержащих сплавов).
Удалить остатки шнурового асбеста с донной части
слитка. Образующиеся при литье обрывы, остатки, слитки промывных плавок,
переплава должны иметь четкую маркировку: марка сплава, номер миксера, номер
плавки. Слитки промывных плавок и переплавов дополнительно клеймить номером
слитка. Вместо марки сплава промывка должна быть заклеймена буквами «п-ка».
После рафинирования литейщик производит съем
шлака с поверхности металла. Шлак должен быть сухим. В таре со шлаком не должно
быть посторонних предметов (огнеупоры, проволока, тряпки, деревянные предметы и
др.). Ответственность за выполнение указанных требований при сборе шлаков несет
литейщик. При необходимости производится отстой расплава.
При подготовке к литью литейщик должен проверить
установку и размеры литейной системы, ( кристаллизатора, стержня), температуру
металла в миксере, скорость литья, давление охлаждающей воды, равномерность
поступления воды на слиток, скорость подачи модифицирующего прутка. Подбор
скорости литья должен производить слесарь по ремонту литейных машин.
Температура охлаждающей воды должна быть не более 30 0 С.
На рабочем месте должен быть подготовлен
комплект аварийных (не менее трех на каждую летку) и рабочих пик в зависимости
от количества леток.
Отлитые слитки должны иметь маркировку: марка
сплава, номер миксера, номер плавки, номер слитка. Слитки должны клеймиться
номером слева направо по отношению к литейщику. Клейма наносить непосредственно
на литнике слитка или на алюминиевом ярлыке, который крепится к литнику слитка.
Качество расплава во многом зависит
от литейных миксеров, атмосфера которых должна содержать минимальное количество
водяных паров. Глубина ванны желательна возможно большая; заданную температуру
металла необходимо поддерживать с достаточной точностью, а перепад температур
по объему расплава должен быть минимальным. В настоящее время миксеры работают на двух видах обогрева -
пламенном и вакуумные.
Настоящая технологическая инструкция определяет
оборудование, подготовку его к работе, технологический процесс вакуумирования
металла и его контроль, технологию литья слитков на вакуумных миксерах. Отливка
слитков осуществляется на электрических вакуумных миксерах, оборудованных
тросовыми литейными машинами полунепрерывного литья.
Требования, предъявляемые к вакуумным миксерам
Конструкция миксера и материалы, применяемые для
их изготовления, должны соответствовать требованиям технических проектов,
утвержденных Главным инженером. Подины и стены миксера не должны иметь глубоких
выбоин, грубых шлаковых наростов и иметь исправный свод. Миксер оборудован
исправными электронагревательными элементами, обеспечивающими режимную температуру
металла в миксере. Миксер оборудован двойными летками. Нижняя летка расположена
на уровне подины, верхняя - приподнята относительно уровня подины на высоту от
50 до 70 мм. Верхнее леточное отверстие перекрыто с помощью пики, изготовленной
согласно чертежу № 2062, нижнее - перекрыто пикой, изготовленной согласно
чертежу № 2066. Во время литья регулирование уровня металла производится с
помощью пики, изготовленной согласно чертежу № 1961 или системой вакуумного
регулирования расхода расплава из миксера проект 5767.8.
Один раз в месяц комиссия в составе: старшего
мастера плавильно-литейного участка корпуса № 1, ведущего технолога и механика
по вакуумному оборудованию устанавливает необходимость замены леточного камня
миксера с отметкой в специальном журнале, который хранится у старшего мастера
плавильно-литейного участка. Система водоохлаждения элементов миксера в
исправном состоянии. Контроль поступления воды в охлаждаемые элементы
осуществлять с помощью системы патрубков, выведенных к сливной воронке.
Включать сушку миксера и разогрев футеровки,
чистку в горячем состоянии, промывку расплавом. Технологические требования,
режимы сушки и разогрева футеровки миксера определены инструкциями 313.66.0286
и 500.36.0092.
В процессе эксплуатации промывку миксера
расплавом производят при переходе с одной марки сплава на другую, отличающиеся
по химическому составу. Необходимость проведения промывки при переходе с одной
марки сплава на другую определять в соответствии с ТИ 303.36.0105, количество
промывного расплава имеет не менее 30 % емкости миксера. Для проведения
промывок использован расплав, приготовленный на алюминии или его отходах,
отходы мягких сплавов или отходах сплава, на который осуществляется переход.
Разрешается производить промывку миксера частью приготовляемого сплава. После
заливки всего металла промывки в миксер расплав подвергать вакуумированию
насосом РВH-6 в течение 20 минут. Расплав промывной плавки выдерживают в
миксере при температуре от 730єС до 800є С не менее трех часов и разливать в
слитки. Время нахождения промывочного расплава в миксере не превышает 24 часов.
В случае вынужденного нахождения промывочного расплава в миксере более 24 часов
производят дополнительное ежесменное вакуумирование его в течение 10 минут насосом
РВH-6. Количество промывных плавок при переходе с одной марки сплава на другую
определяется их химическим составом. Остаток металла последней перед переходом
на другой сплав плавки и расплав промывных плавок сливают" насухо "
через нижнюю летку миксера с отметкой контролером в карте плавки.
Полный слив металла и чистку миксера производят
при остановке его на профилактический осмотр не более чем через 10 суток работы
при разливке на миксере сплавов цинковой группы и не более чем через 18 суток -
других сплавов, через 10 плавок- при отливке сплава1960.По истечение указанных
сроков работы миксера произвести очистку нагревательных элементов от
пылеобразных окислов, после чего снять шлак с поверхности остатка металла и
сливают остаток через нижнюю летку.
Продувку каналов проводят при снятии крышек
выводов нагревательных элементов с двух сторон (при условии отсутствия
нагревателей).
Профилактический осмотр производится в течение
не более 48 часов под руководством механика участка по вакуумному оборудованию.
Осмотр проводится согласно инструкции по эксплуатации 500.36.0092, после чего
производить чистку миксера. Чистку миксера производят в горячем состоянии.
Стенки и подину миксера тщательно очищают от окисных и шлаковых наростов.
Чистку заливочного кармана миксера производят не
реже, чем через одну плавку перед заливкой очередной плавки.а поддоне и стенах
миксера допускаются отдельные выбоины и местные наросты шлака.
После чистки миксер предъявляют контролеру
службы качества. Контролер делает отметку о приемке миксера после чистки в
карте плавки и в журнале литья слитков.
Первую плавку после чистки миксера при
профилактическом осмотре сливают "насухо".
Металл данной плавки, приготовленный и отлитый
по соответствующему технологическому режиму, разрешается запускать на
изготовление прутков, профилей, труб, листов, не предназначенных для
изготовления полуфабрикатов паспортного назначения, "спец целей" , на
"экспорт " и авиацию.
Ввиду высокой химической активности алюминия и
ряда легирующих элементов в отливках и заготовках, предназначенных для
деформирования, всегда в том или ином количестве присутствуют неметаллические
включения (окислы металлов, карбиды, нитриды, сульфиды, карбонитриды), водород,
интерметаллические соединения, частицы диспергированной неметаллической и
флюсовой фаз, не растворяющиеся в расплавах. Кроме того, алюминиевые сплавы
содержат металлические примеси (железо, натрий, литий, титан и др.). Исходная
загрязненность алюминиевых расплавов указанными примесями определяется
качеством шихтовых материалов (главным образом, их чистотой и компактностью),
степенью совершенства технологического процесса и уровнем культуры
производства.
Вакуумирование алюминиевых сплавов как метод
рафинирования, позволяющий получить в современных условиях
наиболее низкий стабильный уровень содержания газа в металле, получил широкое
развитие и распространение в промышленности за последние десятилетие. В
фасонно-литейном производстве этот способ используется для дегазации сравнительно
небольшим объемов металла (до 650 кг). При производстве слитков вакуумной
обработке подвергают большие массы расплава. Процесс ведут в вакуумных миксерах
емкостью от 10 до 25 т. Исследование показывают, что вакуумирование в миксере
снижает содержание водорода в металле примерно в 2 раза и приводят к резкому
уменьшению внутренних дефектов, обнаруживаемых при ультразвуковом контроле, а
следовательно, и количества забракованных полуфабрикатов. С понижением внешнего
давления над расплавом равновесие системы металл - растворенный газ,
образовавшееся во время плавки, смещается в сторону меньших концентраций газа,
что создает благоприятные условие не только для диффузии водорода к свободной
поверхности, но и для возникновения и роста газовых пузырьков. В период
выделения пузырьков, которые характерно для начального периода дегазации,
скорость газоулавливания примерно в 2-3 раза выше, чем при диффузионном
выделение. Однако при вакуумной обработке больших масс, расплава выделение
пузырьков имеем место лишь в поверхностных слоях расплава. Поэтому с
увеличением глубины ванны скорость дегазации уменьшается.
Несмотря на то что коэффициент диффузии водорода
в расплавленном алюминии сравнительно высок (на 2-3 порядка выше коэффициентов
диффузии легирующих элементов), именно массоперенос водорода в расплаве при
вакуумной дегазации глубоких ванн без перемешивания является лимитирующей
статьей. Направленное движение расплава от дна к поверхности позволяет
существенно ускорить дегазацию.
Движение расплава в ванне может быть получено
как в результате естественной конвекции за счет охлаждения объемов расплава у
поверхности ванны и стен миксера, так и вынужденной конвекции - за счет
удаления газов из футеровки через толщу расплавленного металла при создании
разрежения в рабочем пространстве миксера и применение перемешивания расплава
специальными устройствами.
Для повышения производительности агрегатов,
оборудованных вакуумными миксерами, используют вакуумирование расплава в струе
при заливке в миксер, в котором предварительно создана заданная глубина
разрежения. Получаемые высокие скорости дигазации при этом обусловлены
неблагоприятными условиями газовыделения: выделение пузырьков интенсивно
развивается при отсутствии метоллостатического давления, а массоперенос
водорода к возникающим пузырькам укоряется вследствие высокой турбулизации
входящей в вакуум струи расплава. Однако этот процесс пока не вышел из стадии
опытного опробования.
В практике производства сплавов один из методов
очистки от неметаллических включений - отстаивание. Ввиду разницы в плотности
металла и включений выдержка перегретого расплава без перемешивания
способствует всплыванию или осаждению включений. Большая часть неметаллических
включений осаждается на дно миксера. Скорость осаждения зависит от
газосодержания расплавов; с увеличением газосодержания скорость осаждения
уменьшается. Ускорению осаждения способствует обработка расплава флюсами.
Существенный недостаток способа - то, что он проводится на такой стадии
технологического процесса, когда не исключается последующее загрязнение
расплава при переливке из миксера в кристаллизатор. Чаще применяется в
сочетании с другими методами.
Сущность метода состоит в пропускании жидких
расплавов через фильтры, изготовленные из нейтральных или активных по отношению
к металлу материалов. При этом взвешенные включения задерживаются и механически
и в результате химического или физического взаимодействия с материалом фильтра.
Фильтрация через пенокерамические фильтры (ПКФ). Эти фильтры изготавливаются из
пористого керамического материала по специальной технологии. При очистке
металла движение происходит по капиллярам внутри фильтра, где происходит
очистка от неметаллических включений и газообразование примесей. Фильтрование
расплава через сетчатые материалы (стеклоткань, металлическая сетка). Этот вид
очистки широко используется в промышленности при отливке слитков из большинства
деформированных сплавов. В основе его лежит механическое отделение
макроскопических крупных неметаллических включений. Для очитки алюминиевых
сплавов чаще всего используют фильтры из стеклоткани с размером ячейки от
0,6х0,6 до 1,7х1,7 мм. В целях предотвращения взаимодействия с алюминием
стеклоткань изготовляют из специального (с присадкой бора) стекла или покрывают
силикоалюминатной керамикой. Значительно реже используют металлические
(титановые) сетки. В практических условиях фильтрования алюминиевые расплавы не
проходят через стеклоткань с размером ячейки менее 0,5х0,5 мм.
- кристаллизатор; 2 - распределительная коробка;
3 - желоб; 4 - фильтр из стеклоткани; 5 - лёточная коробка; 6 - регулированный
стопор; 7 - пика; 8 - миксер.
Рисунок Схема расположения фильтра.
- кристаллизатор; 2 - распределительная воронка;
3 - фильтр из стеклоткани
Для сплава 7075 применяется комплексное
рафинирование:
1.5
Возможные виды брака, способы их устранения
Поры в слитках появляются по границам зерен
вследствие усадки, а также при высоком содержании водорода в сплаве. На
образование пористости оказывает влияние состав и качество шихтовых материалов,
температура и влажность окружающего воздуха, атмосфера плавильной печи и
миксера, способы рафинирования расплава, технология литья, температура и время
нагрева слитков.
недостаточная просушка футеровки печи и миксера;
применение влажных шихтовых материалов;
перегрев расплава в печи и миксере;
непросушенная, непрогретая оснастка.
Водород попадает в сплав из влаги попавшей в
рабочее пространство печи с шихтой, огнеупорами и парами воды, присутствующими
в воздухе, при сливе - из футеровки сифона. В печном пространстве при высокой
температуре вода взаимодействует с металлом, образуя оксиды и свободный
водород, который растворяется в расплаве. 2Аl + ЗН20=А120з+6Н. Источником
водорода в металле также являются углеводороды, образованные при горении
топлива.
Газы, растворенные в жидком металле, образуют
газовые раковины и пористость. Слитки с такими дефектами имеют недостаточную
механическую прочность и склонны к образованию горячих и холодных трещин.
Пористость в слитках снижает механические свойства полуфабрикатов, способствует
появлению рыхлоты и расслоений в штамповках, поковках и прессованных изделиях.
Снижение водорода в расплаве путем рафинирования
и вакуумирования;
Соблюдение технологии подготовки шихты,
приготовления сплава и литья слитков.
Ликвационные наплывы образуются в процессе
формирования корочки слитка. Сначала образовавшаяся корочка отходит от стенок
кристаллизатора, но потом, под действием давления жидкого расплава, ее снова
прижимает к стенкам кристаллизатора. Так образуется наплыв. Расстояние между
наплывами от2 до 60мм.
непостоянен уровень металла в кристаллизаторе;
нестабильная работа литейных машин;
Улучшение поверхности кристаллизаторов;
Качественная смазка и правильное ее нанесение;
Рифленая поверхность кристаллизаторов для
уменьшения усадки слитка.
Трещины в слитках образуются как на внешней их
поверхности, так и внутри, и являются результатом термических напряжений и
деформаций, возникающих в процессе литья. При охлаждении слитков во время литья
создается резкий перепад температур в разных частях слитка, и соответственно,
процесс усадки слитка проходит не одновременно во всех участках слитка. Т.е.,
одни участки слитка уже затвердели, остывают и дают усадку металла, другие
участки - нагретые, третьи - еще жидкий расплав. Когда остаточные термические
напряжения превышают предел прочности сплава, в слитке появляются трещины.
Горячие (возникают при кристаллизации
слитка); Отличаются от холодных трещин окисленной поверхностью по трещине.
Холодные (возникают при охлаждении уже
закристаллизовавшегося слитка, излом по трещине блестящий, ровный)
Внутренние (центральные или
скоростные): (из-за высокой скорости литья, неравномерного охлаждения слитка
водой, несимметричного распределения металла т.д.)
Поверхностные радиальные: (из-за низкой
скорости литья для дуралюминов, высокой скорости для остальных, неправильная
установка стержня, переохлаждение слитка)
Внутренние круговые: (из-за неравномерного
охлаждения слитка у стенок кристаллизатора и в середине слитка)
Поперечные: (характерны для
высокопрочных сплавов при низких температурах и скоростях литья, неравномерное
охлаждение слитка)
Рисунок №3 - Виды брака в круглых слитках
Донные (холодные, возникают при низкой
скорости литья, высокой температуре металла, наличием посторонних включений на
начало литья, некачественной подливке);
Боковые (из-за низких скорости и
температуры литья у высокопрочных сплавов, непостоянства уровня металла в
кристаллизаторе, наличие в расплаве окисных и шлаковых включений);
Литниковые (наличие в расплаве окисных
и шлаковых включений, нарушение технологии отжига, переохлаждение литника);
Поверхностные (горячие, возникают при
высокой скорости литья и неравномерного охлаждения слитка водой и неправильного
соотношения химических элементов в сплаве);
Рисунок №4 - Виды брака в плоских слитках
.Увеличение скорости литья (центральные
трещины);
.Пониженная скорость литья (поверхностные
трещины);
.Неравномерное распределение металла в
кристаллизаторе;
.Неправильное соотношение химических элементов в
сплаве;
.Нестабильная работа литейных машин;
.Некачественная подливка в донную или литниковую
часть (если задана технологией).
К методам предупреждения относится исключение
всех возможных причин возникновения трещин.
Неслитины - несплошность на поверхности слитка,
когда на застывшую поверхность наплывает жидкий расплав, превращающийся
сплошную твердую корочку.
Возникшие при литье неслитины, повторяются
периодически.
Пониженная температура литья;
Пониженная скорость литья;
Колебания уровня расплава в
кристаллизаторе;
Неправильное распределение расплава в
кристаллизаторе;
Нестабильный ход литейной машины;
Нарушение режимов охлаждения слитков
при кристаллизации.
Неглубокие неслитины удаляются мехобработкой
слитков, глубокие приводят к браку полуфабрикатов. К методам предупреждения
относится исключение всех возможных причин возникновения трещин, а также
изготовление кристаллизаторов с рифленой поверхностью для уменьшения отвода
тепла от слитка и литье с «теплым» верхом.
1.6
Контроль основных параметров и качество готовой продукции
Качество слитка зависит от скорости литья,
температуры металла, количества воды для охлаждения слитка и условий начала и
конца литья. Скорость литья должна быть выбрана таким образом, чтобы слитки не
имели диаметрических и радиальных трещин, а также неслитин. Повышение скорости
литья уменьшает возможность образования радиальных трещин и улучшает качество
поверхности слитков - сокращается число неслитин. Чрезмерное увеличение скорости
литья приводит к образованию диаметральных трещин и ликвационных наплывов.
Кроме того, при этом увеличивается переходная (двухфазная) область
кристаллизирующегося слитка, снижаются его плотность и механические свойства.
Температура расплава, подаваемого в
кристаллизатор, влияет на глубину лунки, качество поверхности и структуру
слитка. Повышение температуры расплава приводит к углублению лунки, что в свою
очередь может вызвать образование трещин при литье. При высоких температурах
литья возможна образование пористости и увеличение ликвационных наплывов на
поверхности слитка. При заниженной температуре литья увеличивается глубина
неслитин и появляются условия для объемной кристаллизации и возникновения
неоднородности строения слитка. На основании и указанных соображений
температуру расплава в миксере поднимают на 50-100 град выше температуры
ликвидуса. Более высокую температуру литья применяют для сплавов, в которых
первичными могут быть кристаллы интерметаллических соединений. Скорость и
температура литья - взаимно связанные между собой параметры. Увеличение
скорости литья должно сопровождаться снижением температуры расплава в миксере,
и наоборот.
Большое значение для получения слитков без
трещин имеют условия начала и конца литья. И в начале, и в конце литья
вследствие того, что процесс не установился, возникает дополнительные
термические напряжения. Поэтому необходимо стремится повысить пластичность
донной и
Похожие работы на - Вакуумный электрический миксер для приготовления сплава 7075 Курсовая работа (т). Другое.
Сочинение Рассуждение Как Оформить Диалог На Письме
Мини Сочинение На Тему Читать Это Модно
Сочинение Народные Песни В Произведениях Русской Литературы
Производственные Предприятия Реферат
Реферат: Институты власти и право Османской империи
Курсовая работа по теме Технология изготовления газосиликатных блоков
Курсовая работа по теме Разработка и оформление электронного издания – учебного сайта 'HTML5&CSS3'
Шпаргалки На Тему Педагогика
Реферат по теме История и характеристика газеты 'The Times'
Контрольная работа: Основы статуса человека и гражданина в РФ
Показать Реферат На Тему Моя Профессия Сварщик
Контрольная Работа На Тему Русский Язык
Угрозы Информационной Безопасности Реферат
Как Назывались 1 Исторические Сочинения На Руси
Реферат по теме Портрет в русской живописи 19 века
Пособие по теме Кубанская вышивка
Курсовая Работа На Тему Организация Работы Кафе
Отчет По Практике Рекомендации
Глобальное Экономическое Неравенство В Меняющемся Мире Реферат
Реферат: Вредные выбросы прокатного производства. Скачать бесплатно и без регистрации
Реферат: Петровские реформы 2
Реферат: Современные технологии обеспечения информационной безопасности
Похожие работы на - Жизнь и деятельность А.Ф. Смирдина