Understanding Plastic Extrusion Machines: A Beginner’s Guide
nazamachineryPlastic extrusion machines are essential tools in the manufacturing industry, used to create a wide range of plastic products with consistent cross-sectional profiles. Whether you're new to the concept or looking to deepen your understanding, here’s a comprehensive guide to plastic extrusion machines:
1. What is Plastic Extrusion?
- Definition: Plastic extrusion is a process where raw plastic material is melted and formed into a continuous profile.
- Applications: Used to produce items such as pipes, tubing, sheets, films, profiles, and rods used in various industries including construction, packaging, automotive, and electronics.
2. Components of a Plastic Extrusion Machine
- Extruder: Core component that melts and forces the plastic material through a shaped die to form the desired profile.
- Hopper: Container that holds and feeds raw plastic material into the extruder barrel.
- Barrel: Enclosed cylinder where the plastic material is heated and mixed before being forced through the die.
- Screw: Rotating component inside the barrel that transports, melts, and mixes the plastic material.
- Die: Shaped opening at the end of the extruder where the molten plastic exits to form the desired shape.
- Cooling System: Ensures the formed plastic profile cools and solidifies correctly after leaving the die.
3. Types of Plastic Extrusion Processes
- Single-Screw Extrusion: Uses a single rotating screw to transport and melt the plastic material.
- Twin-Screw Extrusion: Uses two intermeshing screws to improve mixing, compounding, and processing capabilities.
- Co-Extrusion: Simultaneously extrudes multiple layers of different materials or colors to create complex products with varied properties.
4. Key Parameters and Control Systems
- Temperature Control: Precise heating and cooling systems maintain optimal temperatures for melting and shaping the plastic.
- Pressure and Speed: Adjustments control the rate at which plastic is extruded and the force applied.
- Die Design: Determines the shape and dimensions of the final extruded product, influencing its properties.
5. Materials Used in Plastic Extrusion
- Thermoplastics: Most commonly used due to their ability to soften and reform upon heating, including PVC, HDPE, LDPE, PP, and ABS.
- Thermosets: Less common, these materials undergo irreversible curing upon heating and are used for specialized applications.
6. Advantages of Plastic Extrusion
- Cost-Effective Production: Efficient for producing continuous lengths of plastic products with minimal waste.
- Versatility: Capable of creating a wide range of shapes, sizes, and profiles to meet diverse industry needs.
- Consistency: Provides uniform product dimensions and properties across production batches.
7. Quality Control and Maintenance
- Quality Assurance: Monitoring and testing ensure that extruded products meet specified dimensions, tolerances, and quality standards.
- Maintenance: Regular cleaning, lubrication, and inspection of components like screws, barrels, and dies to optimize performance and longevity.
8. Environmental Considerations
- Recyclability: Many thermoplastics used in extrusion are recyclable, contributing to sustainability efforts.
- Energy Efficiency: Modern extrusion machines are designed to minimize energy consumption during operation.
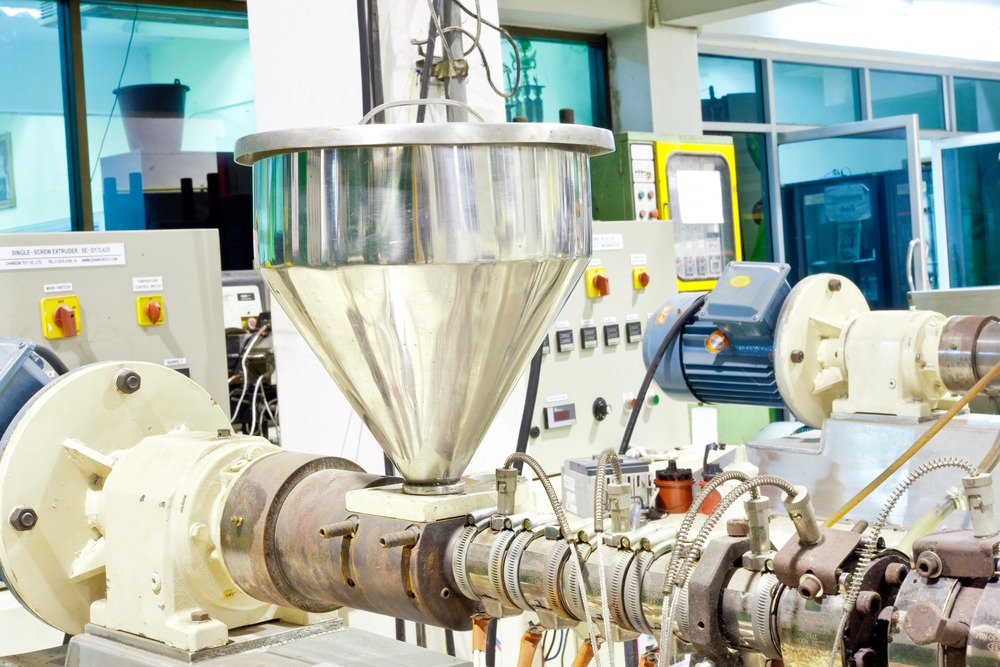
Conclusion
Plastic extrusion machines are versatile tools that play a crucial role in various manufacturing processes, offering efficiency, versatility, and consistency in producing plastic products. By understanding the components, processes, materials, and applications involved in plastic extrusion, beginners can grasp the fundamentals and explore the potential of this essential manufacturing technique in their respective industries.