Участок производственного подразделения по изотермическому отжигу поковок. Курсовая работа (т). Другое.
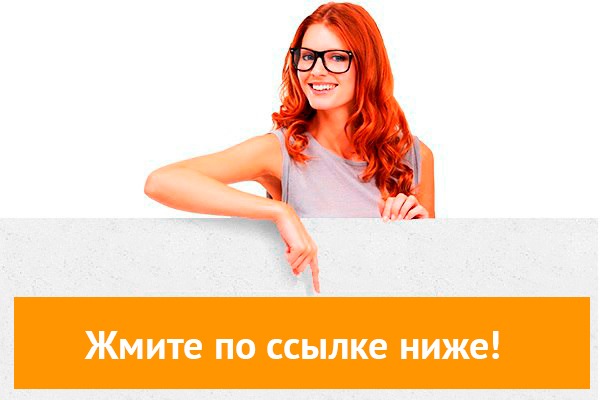
🛑 👉🏻👉🏻👉🏻 ИНФОРМАЦИЯ ДОСТУПНА ЗДЕСЬ ЖМИТЕ 👈🏻👈🏻👈🏻
Вы можете узнать стоимость помощи в написании студенческой работы.
Помощь в написании работы, которую точно примут!
Похожие работы на - Участок производственного подразделения по изотермическому отжигу поковок
Нужна качественная работа без плагиата?
Не нашел материал для своей работы?
Поможем написать качественную работу Без плагиата!
БЕЛОРУССКИЙ НАЦИОНАЛЬНЫЙ
ТЕХНИЧЕСКИЙ УНИВЕРСИТЕТ
Кафедра «Материаловедение
в машиностроении»
«Участок
производственного подразделения по изотермическому отжигу поковок»
ПОКОВКА, ОТЖИГ, СТАЛЬ, ТЕХНОЛОГИЧЕСКИЙ ПРОЦЕСС, ПЛАНИРОВКА,
СТРОИТЕЛЬНЯ ЧАСТЬ.
Цель курсового проекта - разработать технологический процесс,
планировку и спроектировать участок изотермического отжига поковок в условиях
ОАО «МАЗ».
В курсовом проекте последовательно разработаны основные этапы
проектирования участка изотермического отжига поковок, расчет программы цеха,
выбор марки стали, расчет производительности оборудования и определение его
количества, разработка планировки, проектирование технологического процесса,
теплотехнический расчет оборудования и строительная часть.
. Расчет
производительности и количества оборудования
. Проектирование
технологического процесса
. Определение
площади цеха и разработка планировки
. Тепловой
расчет оборудования
.1
Сравнительный расчет потерь тепла теплопроводностью через футеровку печи
.2
Определение суммарных тепловых потерь
Минский автомобильный завод является одним из старейших и
крупнейших автомобильных заводов на территории СНГ. Основная доля продукции
завода приходится на тяжёлые грузовики, но также выпускается и другая техника:
прицепы, спецтехника, автобусы. Минский автомобильный завод был основан 9
августа 1944 года с постановления Государственного комитета обороны об
организации автобусного завода в Минске. В октябре 1947 года на заводе были
собраны первые пять МАЗов.
Получение заданных свойств деталей автомобиля, адекватных
условиям её эксплуатации, всегда была актуальна, так как решение данной задачи
позволяло получить равнопрочную конструкцию автомобиля, что является оптимальным
как с технической, так и экономической стороны. Для деталей, которые в процессе
изготовления подвергаются различным видам технологических операций, связанных с
многократным нагревом, прогнозирование заданных свойств конечной детали следует
начинать на самых первых стадиях её изготовления. Это касается в первую очередь
процессов регулирования скоростей термического воздействия (нагрева, выдержки и
охлаждения) на операции горячего формообразования: ковке, штамповке. Известно,
что в процессе горячей штамповки или ковки детали предварительно подвергают
нагреву до интервала ковочных температур порядка 1150-1250 °С. Для достижения
равномерного температурного поля по сечению заготовки, в первую очередь
массивной заготовки, требуется длительная выдержка в интервале высоких
температур, что приводит к росту зерна и формированию грубой ковочной
структуры.
Из вышесказанного следует, что вторым важнейшим параметром,
определяющим качество поковок, после обеспечения размеров и минимальных
припусков, является формирование требуемой структуры металла, которое
достигается предварительной термической обработкой.
Введение в эксплуатацию современного автоматизированного
оборудования для изотермического отжига позволило существенно увеличить
производительность при предворительной ТО без увеличения производственных
площадей, обеспечить выполнение возросших требований к качеству, снижение
энергозатрат.
При проектировании термического цеха производственная
программа может быть: точной, приведенной и условной. В термических
подразделениях обработке подвергается большая номенклатура изделий, поэтому при
проектировании данных подразделений используется приведенная производственная
программа. При расчете приведенной производственной программы номенклатура
изделий разбивается на группы деталей, которые имеют близкие размеры, вес и
обрабатываются по одинаковым технологическим процессам.
Наименование, размеры и вес выпускаемых деталей представлены
в таблице 1.
Таблица 1 - Производственная программа
Масса детали представителя определяется по формуле:
где m - масса детали представителя, кг.;- количество деталей
в группе;- масса i-ой детали, кг;=146,08/11=13,28кг
В качестве детали-представителя принимаем вал-шестерню массой
13,28 кг, т.к. она является преобладающей деталью, которую обрабатывают на
данном агрегате.
Р вып = 425323шт; Р вып =5627,8 тонн.
Определяем программу запуска, т.е. необходимое количество
деталей для выполнения плана:
где k- коэффициент в долях единицы, учитывающий брак на всех
стадиях изготовления детали, k<=0,01;
Р зап =5627,8(1+0,01)=5684,0443 тонн.
Выбор марки стали осуществляется путем сравнения
механических, технологических свойств и стоимости различных марок стали.
Окончательной ТО поковок является цементация с последующей
закалкой и отпуском. Для цементации выбирают стали с пониженным содержанием
углерода, стали типа 20ХНР, 20ХГНМ, 12ХН3А. Предложенной сталью используемой на
заводе является сталь марки 20ХН3А. Сталь является универсальной для массового
производства цементации шестерен, но она не соответствует механическим
свойствам, которые необходимы для эксплуатации шестерен. Механические свойства
предъявляемые к изделию указаны в таблице 2.
Таблица 2 - Механических свойства предъявляемые к изделию с
учетом марки стали
Выбираем для изготовления вал-шестерни сталь 20ХГНР, т.к. она
удовлетворяет требуемым свойствам и более дешевая, чем 12Х2Н4А.
Химический состав стали, механические и технологические
свойства приведены ниже.
Таблица 3 - Химический состав стали 20ХГНР
Температуры критических точек, o C:=740, Ac3=830,
Ar3=725, Ar1=650, Mн=365
Таблица 4 - Технологические свойства
Начала 1150,
конца 800. Сечения долее 60 мм охлаждаются замедленно.
РДС.
Рекомендуется подогрев и последующая термическая обработка.
Таблица 5 - Механические свойства прутка
Твердость для
полос прокаливаемости, HRC Э
Агрегат изотермического отжига поковок, с газовым обогревом,
фирмы «Elterma» состоит из отдельных устройств, составленных в
последовательности, соответствующей их функциям. Работа агрегата
изотермического отжига автоматизирована; операции, связанные с транспортировкой
обрабатываемых изделий через составные части агрегата, совершаются
автоматически при контроле управляющей системой. Управляющая система включает
аппаратуру, регулирующую рабочие параметры всех узлов, включает приборы,
регистрирующие расход газа, состав и температуру отходящих газов.
При расчете времени нагрева деталей сложной формы
рассчитывается характеристический размер детали, учитывающий количество и
расположение деталей на поддоне, размеры поддона.
где m - масса детали,- количество деталей в садке,,b,c -
размеры садки.
Эффективный характеристический размер X эфф определяется
по формуле:
Схема контейнера и схема расположения деталей в контейнере
приведены на рисунке 1.
Рисунок 1 - Схема контейнера и схема расположения деталей в
контейнере
Отжиг проводят с температуры t отж =880 O C,
тогда Т м к =1153 К; Т м н =293К,
Температура в печи равна: Т 0 = Т м к +50=1203К
Определяем критерий Био по формуле:
в которой необходимо найти 2 неизвестные. Для этого найдём среднюю
температуру поверхности садки в процессе нагрева (Т ср ). С учетом
того, что зависимость Т(τ) нелинейная
Т ср найдём по формуле:
Т ср = 2/3(Т м к + Т м н )
= 2/3(1153+293) = 963К = 690 о С
Найдём теплопроводность при температуре 690 о С:
λ 600 =37,1Вт/мК; λ 700 =34,2 Вт/мК (табл.)
λ 690 =37,1-((37,1-34,2)/100)90=34,5 Вт/мК
Рассчитаем суммарный коэффициент теплоотдачи :
где - коэффициент теплоотдачи излучением;
- коэффициент теплоотдачи конвекцией.
Найдём коэффициент теплоотдачи излучением по формуле:
Тогда суммарный коэффициент теплоотдачи равен:
Т.к. критерий био равен 0,28 что попадает в промежуточную область,
то расчет ведём по формулам для теплотехнически массивных тел используя
номограммы Будрина.
Находим критерий Фурье по номограммам Будрина: F 0 =7.5
(для центра)
Определяем время нагрева по формуле:
где а - среднее значение коэффициента температуропроводности.
а 600 =6,3910 -6 м 2 /с; а 700 =510 -6
м 2 /с. (табл.)
Примем время выдержки 3ч, тогда время пребывания садки в печи
равно T в =6ч 35мин = 395мин.
Определяем темп толкания: T т =Т в /n *,
где n * = n/2. N- количество поддонов в печи (загрузка по 2 поддона).
Производительность агрегата определяем по формуле:
где N c - вес деталей (без учета веса поддонов) в 1
загрузке.= 20213,98/ 0,5 = 1118,4 кг/ч.
Определяем требуемое количество оборудования. Для этого
определяем суммарное количество агрегато-часов по рассчитываемому оборудованию.
Берем программу запуска (кг) и делим на производительность агрегата.
Определяем расчетное количество оборудования по формуле:
где Ф д - действительный годовой фонд работы
оборудования.
где К - коэффициент, К = 0,9 при данном режиме работы;
Ф н - время, в течении которого оборудование может
работать при заданном режиме.
П - число праздничных дней в году, П=8;
В - количество выходных дней в году, В=104;
Принимаем количество оборудования N пр =1.
Под технологическим процессом понимают совокупность операций,
связанных с изменением структуры детали путем нагрева, выдержки, охлаждения, с
целью получения требуемых свойств.
При разработке тех. процесса ТО необходимо выбирать наиболее
целесообразный тепловой режим нагрева и охлаждения изделий, а также правильно
подбирать среду, взаимодействующую с поверхностью изделия. В большинстве
случаев наиболее длительными являются операции нагрева, поэтому их
продолжительность часто предопределяет производительность и количество
необходимого основного оборудования: печей и нагревательных устройств.
Увеличение скорости нагрева существенно повышает производительность
оборудования, снижает себестоимость продукции и в ряде случаев улучшает
механические свойства обрабатываемых изделий.
Схемы технологического процесса (отжиг поковок из стали
20ХГНР) представлены на рисунке 2:
Рисунок 2 - Варианты технологического процесса.
Из схем видно что отжиг поковок можно провести по 3
вариантам:
Варианты 1 и 2 экономически нецелесообразны так как
достижение необходимой скорости охлаждения (10..30 о С в час) влечет
за собой большие экономические потери чем в варианте 3, обусловленные
удлинением тех. процесса и необходимостью поддержания и контроля скорости
охлаждения.
Третий график (в) является наиболее удачным для данной марки
стали (20ХГНР), позволяет добиться хорошего уровня механический свойств,
минимального брака, и является достаточно технологическим, что позволяет
снизить себестоимость и повысить качество продукции.
Маршрутная технология представлена на рисунке 3:
термические
операции механические операции
Кондиционирование
структуры после ХТО структуры структуры
Окончательная
мех. обработка обработка
Разрабатываем технологическую карту термической обработки на
агрегате API - 1800G.
Таблица 7 - Технологическая карта термической обработки на
агрегате API - 1800G.
Кран мостовой
Q=5т Автопгрузчик Q=5т
Тара: Ор
613-00000 Ор 893-00000 Ор 981-00000 Ор 877-00000 Ор 2598-00000
Подать поковки
с участка складирования к агрегату изотермического отжига
Контроль
но-изме рительный инстру мент в соответ ствии с КТИ
Наличие
загрязн.поверхностей, трещин, волосовин и щтампов. дефектов Проверить
соответствие поступивших поковок чертежу
3% от
операционной партии При наличии дефектов или несоответст вий чертежу, вернуть
партию на участок-отправитель
Кран консоль
ный, стол загрузоч ный Приспособление 13325.12
Произво дить
загрузку вручную или при помощи крана консольного
Положение
поковок в корзине: вертикальное Расстояние между поковками: 15-40 мм
Поковки не
должны выступать за габариты корзины.
Опустить стол в
крайнее нижн. полож., загрузить поковки, поднять стол в исходн.полож. нажать
контрольную кнопку загрузки.
Произвести
выбор программы согласно КТИ
Режимы ТО в
программе устанавливает инжененр-технолог
Печь
аустенизации PPN-1800G Приспособление 13325.12
Контроль
температуры для каждой партии поковок не менее 2-х раз в смену с записью в
журнале
Все операции
выполняются автоматическиПри несоответств. темпер. режима КТИ сообщить
мастеру
Боковой
перегрузочный стол Приспособление 13325.12
Все операции
выполняются автоматически
Камера
подстуживания Приспособление 13325.12
Контроль для
каждой партии поковок температур ный режим охлаждения
Все операции
выполняются автоматическиПри несоответств. темпер. режима КТИ сообщить
мастеру
Загрузоч ный
толкатель Приспособление 13325.12
Все операции
выполняются автоматически
Печь
изотермической выдержки PPI-1800G
Все операции
выполняются автоматически
Все операции
выполняются автоматически
камера быстрого
охлажде ния КО-2 Приспособление 13325.12
Все операции
выполняются автоматически
Приспособление
13325.12 Приспособление 072941-01
Тара: Ор
613-00000 Ор 893-00000 Ор 981-00000 Ор 877-00000 Ор 2598-00000
Застрявшие
поковки из корзины извлекаются приспособлением 072941-01 При заполнении тары,
повесить на неё индификационную бирку.
Перемещение
поддона в опрокидыва тель и выгрузка поковок в тару происходит автоматически
после нажатия контрольной кнопки выгрузки.
Станок мод.
3М-636 Круг шлифов. 1600х63х х305
Стол
металлический черт. 9788-1404 Твердомер ТШ-2М
Сколы, трещины
и др. внешние дефекты HB
Визуально проверить
состояние поверхности Измерить твердость
Не менее 1 раза
в неделю сдавать в ЦЗИЛ для металлограф. анализа поков ки согласно указаниям
КТИ и утвержденному графику проверки. После остановки и запуска агрегата сдавать
поковку в ЦЗИЛ для проверки качества изотермического отжига
Тара: Ор
613-00000 Ор 893-00000 Ор 981-00000 Ор 877-00000 Ор 2598-00000
Не допускается
транспортировка тары с поковками, выступающи ми за её габариты
Подать
термообработанные поковки на участок очистки
Дробеметная
установка мод.В10х 12,5S/W2C/SK/MS
Произвести
очистку согласно указаниям в КТИ
Тара: Ор
613-00000 Ор 893-00000 Ор 981-00000 Ор 877-00000 Ор 2598-00000
Не допускается
транспортировка тары с поковками, выступающи ми за её габариты
Подать
термообработанные поковки на участок готовой продукции
В курсовом проекте определяем производственную и
вспомогательную площадь, необходимую для разработки планировки.
Производственной площадью называется площадь отделений и
участков, непосредственно предназначенных, для осуществления технологических
процессов и включает площади, занимаемые, площади хранения изделий до и после
ТО, а также площади занимаемые тележками и конвейерами.
Агрегат API - 1800G является многофункциональным
технологическим оборудованием.
Определяем площадь, приходящуюся на единицу оборудования: ’ об
= A/S q = 5684.0443/12=473 м 2
Так как используется только 1 агрегат, то суммарная площадь,
занимаемая оборудованием, равна площади приходящейся на единицу оборудования: об
= S ’ об = 473 м 2 .
Определяем общую производственную площадь с учетом
вспомогательной. Вспомогательная площадь включает кладовые хранения деталей,
вспомогательный материалов, технологической оснастки. Вспомогательную площадь
обычно принимают 25…35% от величины производственной площади: ’ общ
= (1,25..1,35). S об = 1,35.473 = 639 м 2 .
Все полученные данные сводим в таблицу 8:
Таблица 8 - Определение площади участка
В таблице 9 представлены позиции оборудования и оснастки,
находящиеся на участке.
Таблица 9 - Список единиц оборудования и оснастки
Наименование
составных частей и узлов агрегата
1 2 3 4 5 6 7 8
9 10 11 12 13 14 15 16, 17
Загрузочный
стол с поворотным стендом, с возможностью подъема и опускания; Конвейер
поковок; Загрузочный толкатель печи аустенизации; Печь аустенизации; Конвейер
разгрузки поддонов из печи аустенизации; Боковой перегрузочный стол;
Воздушная камера подстуживания для изотермической выдержки; Загрузочный
толкатель печи изотермической выдержки; Печь изотермической выдержки;
Воздушная камера быстрого охлаждения; Конвейер разгрузки поддонов из печи
изотермической выдержки; Опрокидыватель; Боковой прегрузочный стол; Конвейер
поковок; Шкаф управления Контейнеры с поковками до и после ТО
- температура внутренней поверхности стенки 880 °С,
Определение теплового потока через футеровку по варианту 1:
Распределение температур показано на рисунке 4:
q t 2
δ 1
δ 2
Рисунок 4 - Распределение температур по сечению кладки (δ 1 =δ 2 =230мм).
λ 1 = 0,7+0,00064t; λ 2 = 0,116+0,00015t; 1 = 930°С; t 4 = 20°С;
Примем t 3 = 70°С.
т.к. λ зависит от температуры,
то необходимо брать среднее значение теплопроводности для каждого слоя, для
каждого слоя, для этого необходимо знать температуры на границах слоев t 2 ,
t 3 и t 4.
λ 1 =
0,7+0,00064.677,5=1,134Вт/м 2 К;
λ 2 =
0,116+0,00015.272,5=0,157 Вт/м 2 К;
Поскольку найденное значение плотности теплового потока было
определено при допущении, что температура от t 1 до t 3
меняется по прямой линии, то необходимо проверить вычисления:
λ 1 =
0,7+0,00064.830=1,231Вт/м 2 К;
λ 2 =
0,116+0,00015.417,5=0,179 Вт/м 2 К;
Т.к. ошибка превышает 5%, то проводим уточнение.
λ 1 =
0,7+0,00064.828=1,23Вт/м 2 К;
λ 2 = 0,116+0,00015.419=0,179
Вт/м 2 К;
Таким образом, тепловой поток равен 557 Вт/м 2 ,
выделяющийся через двухслойную футеровку.
Определение теплового потока через футеровку по варианту 2:
Распределение температур показано на рисунке 5:
q t 2
δ 1
δ 2 δ 3
Рисунок 5 - Распределение температур по сечению кладки (δ 1 =δ 2 =230мм, δ 3 =40мм)
λ 1 = 0,7+0,00064t; λ 2 = 0,116+0,00015t; λ 3 = 0,081+0,00023t 1
= 930°С; t 5 = 20°С; Примем t 4 = 30°С.
т.к. λ зависит от температуры,
то необходимо брать среднее значение теплопроводности для каждого слоя, для
каждого слоя, для этого необходимо знать температуры на границах слоев t 2 ,
t 3 и t 4.
λ 1 =
0,7+0,00064.685=1,138Вт/м 2 К;
λ 2 = 0,116+0,00015.294=0,160
Вт/м 2 К;
λ 3 =
0,081+0,00023.64=0,096Вт/м 2 К;
Поскольку найденное значение плотности теплового потока было
определено при допущении, что температура от t 1 до t 4 меняется
по прямой линии, то необходимо проверить вычисления:
λ 1 =
0,7+0,00064.839=1,234Вт/м 2 К;
λ 2 =
0,116+0,00015.510=0,193Вт/м 2 К;
λ 3 = 0,081+0,00023.138=0,113
Вт/м 2 К;
Т.к. ошибка превышает 5%, то проводим уточнение.
λ 1 = 0,7+0,00064.826=1,229
Вт/м 2 К;
λ 2 = 0,116+0,00015.499=0,191
Вт/м 2 К;
λ 3 = 0,081+0,00023.141=0,113
Вт/м 2 К;
Таким образом, тепловой поток равен 472 Вт/м 2 ,
выделяющийся через двухслойную футеровку.
Потери тепла через футеровку печи найдём по формуле: Q кл =F.q,
где F- средняя площадь футеровки. Зная размеры рабочего пространства печи
(1,9х2,06х9,8м) и толщину футеровки найдём F.
кл = 86,2 . 557 = 48013 Вт = 48,013 кВт
кл = 86,9 . 472 = 41017 Вт = 41,017 кВт
Для определения тепловых потерь необходимо составить тепловой
баланс который основан на законе сохранения энергии:
Теплота, от сжигания топлива и вносимая с подогретым воздухом
определяется по формуле:
где G - производительность печи в кг/с;
Теплота, расходуемая при работе печи определяется по формуле:
где - тепло, расходуемое на нагрев металла;
- потери тепла с уходящими дымовыми газами;
- потери тепла от химического недожога топлива;
- потери тепла от химической неполноты нагрева;
- потери тепла в окружающую среду;
- потери тепла на разогрев кладки печи;
- тепло, расходуемое на нагрев поддонов.
Подбором конструкций горелок, а также условий сжигания топлива
можно добиться минимальных потерь . Так как агрегат полностью остывает очень редко(только при плановых
ремонтах и авариях), потери тепла - не рассчитываются так как они играют небольшую роль в общих
потерях тепла. С учетом вышесказанного теплоту, расходуемую при работе печи,
определяем по формуле:
Найдём тепло, расходуемое на нагрев металла и тепло, расходуемое
на нагрев поддонов.
где G - производительность печи кг/с;
- конечное и начальное теплосодержание металла.
Найдём потери тепла с уходящими дымовыми газами:
Найдём потери тепла в окружающую среду:
где - потери тепла через отверстие печи;
- относительное время открывания отверстия.
Найдём потери тепла через крышки. Матерал крышки - динас легковес
ДНА. Толщина 230мм. λ = 0,29+0,00037.t. t 2 примем 70 о С.
λ = 0,29+0,00037.475 = 0,466 Вт/м 2 К;
λ = 0,29+0,00037.503,7= 0,476 Вт/м 2 К;
Площадь крышки: F кр = 2,06.1,9=3,9м 2 .
Тепловые потери и КПД соответственно равны.
Агрегат «API -1800G» занимает размеры участка цеха для
цементации равные 11,4x28,9 метра. Для таких цехов ориентируются на сборные
железобетонные конструкции, они значительно дешевле, требуют меньшего расхода
металла, несгораемые, меньше подвержены коррозии. На колоннах имеются консоли,
на которые размещаются подкрановые балки. Используем трехопорный кран.
Подкрановые балки применяем Т-образного сечения с шириной полки 0,57м и высотой
0,8м при кранах грузоподъемностью 5т. Размер подошвы фундамента, определяется
крановой нагрузкой, массой конструкции и характером грунта. Заглубление подошвы
фундамента должно быть ниже промерзания грунта.
Фермы перекрывающие пролет выполняют металлическими. Наружные
стены здания термических цехов делают из блоков легковесного бетона марки не
ниже 75, толщиной 400 - 500мм.
Окна для термических цехов следует делать с одинарным
остеклением со стальными переплетами с рамами шириной 1,5 и 2м, высотой кратной
1,2.
Двери промышленного здания термического цеха делают высотой
2,3м и шириной 1,4м. Размеры цеховых ворот делают 3x3м или 4х4м, в воротах
устраивают двери для прохода людей.
Пол делаем металлический на бетонной стяжке.
Для освещения берутся продольные фонари с вертикальным
остеклением - являются простыми по конструкции и обеспечивают более равномерное
освещение.
Высота пролета Н до подкрановых путей определяется высотой
оборудования, длинной обрабатываемых изделий, грузоподъемностью крана.
Максимальная высота оборудования h = 4794 мм, таким образом, расстояние от уровня пола до верха головки
рельса Н = 9000 мм. Высота h =1200 мм включает размер крана и 200-250
мм, которые учитывают прогиб фермы. Тогда высота цеха H = 10,8 м.
Железобетонные фермы, тип колонн с подвесными кранами при L=18м,
H=10,8 м крайние колонны=0,5х0,5; средние=0,6х0,6. Фундамент под колонны
проектируется в виде отдельно стоящих железобетонных конструкций. Сечение
колонн b*a=500*500, сечение подколонн b *a =1200*1200, размеры подошвы B*A=1800*3000;
1. М.В.
Логачев, Н.И. Иваницкий, Л.М. Давидович Расчеты нагревательных устройств. -
Минск, 2007.
. К.Н.
Соколов, И.К.Коротич Технология термической обработки и проектирование термических
цехов. - М.: Металлургия, 1988.
. Р.И.
Коплун Проектирование термических цехов. - Санкт-Петербург, 1971.
. Г.Ф.
Протасевич, В.А. Стефанович, В.А. Смёткин Учебно-методическое пособие по
дипломному проектированию. - Минск, 2002.
Похожие работы на - Участок производственного подразделения по изотермическому отжигу поковок Курсовая работа (т). Другое.
Приложение Диссертации Пример
Фгос 10 11 Класс Спотлайт Контрольные Работа
Реферат по теме Важнейшие трематодозы человека. Методы их диагностики и профилактики
Реферат по теме Конституционное право Австрийской Республики
Курсовая работа по теме Країни Близького Сходу та Північної Африки у першій половині ХХ ст. (1900–1945 рр.)
Сочинение Вред И Польза Инерции
Краткое Сочинение На Тему Слово
Реферат по теме Как упорядочить процесс разработки стратегии
Реферат по теме Философские проблемы математики
Дипломная работа по теме Художественная обработка материалов на уроках технологии
Юшка Пример Сочинение
Реферат: Платежно-расчетные отношения во внешнеэкономической деятельности субъектов хозяйствования
Сочинение Про Одноклассницу Описание 7 Класс
Курсовая работа: Становление системы Российского законодательства
Курсовая работа: История болезни по пропедевтике. Рак пищевода. Скачать бесплатно и без регистрации
Реферат: The Catcher In The Rye Holden And
Реферат: Основные направления проверки и источники информации при аудите вложений банка в ценные бумаги
Заключение В Сочинении О Характере Героя
Курсовая работа по теме Разработка технической документации на проведение монтажных и ремонтных работ солодосушилки
Сәнді Киіну Заман Талабы Эссе
Курсовая работа: Порівняльний аналіз ефективності та складності алгоритмів пошуку елементів у масивах
Похожие работы на - Методика оценивания качества продукции 'шорты'
Реферат: Буржуазныя рэформы 1860 - 70-х гадоў і контррэформы 1880 - 90-х гадоў