UNDERSTANDING THE CORROSIVE NATURE OF LIQUID CAUSTIC SODA ON DIFFERENT MATERIALS
Hossein Moshiri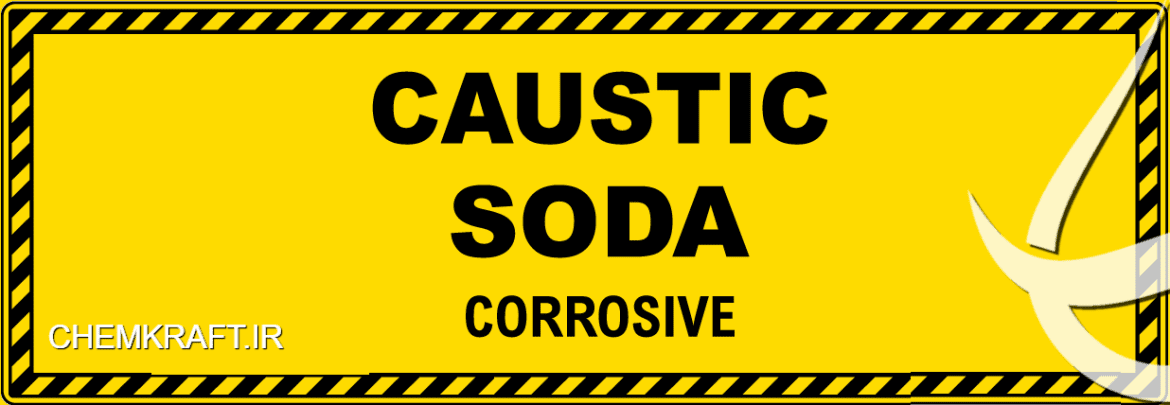
1. Introduction to Liquid Caustic Soda
Liquid caustic soda, also known as sodium hydroxide (NaOH), is a highly corrosive and versatile chemical compound widely used in various industries for its alkaline properties. Understanding the corrosive nature of liquid caustic soda on different materials is crucial for ensuring the safety, integrity, and longevity of equipment, infrastructure, and storage systems. This article delves into the mechanisms of corrosion caused by liquid caustic soda, examines its effects on various materials, explores corrosion resistance of metals and non-metallic materials, discusses protective measures and prevention techniques, addresses proper handling and storage procedures, and examines real-life case studies. By gaining a comprehensive understanding of how liquid caustic soda interacts with different materials, professionals can effectively mitigate corrosion risks and ensure the continued operation of critical processes and facilities.
1. Introduction to Liquid Caustic Soda
Liquid caustic soda, also known as sodium hydroxide, is a powerful chemical compound that has a wide range of applications across various industries. It is an extremely versatile substance with strong alkaline properties. But before we dive into its corrosive nature, let’s get acquainted with what liquid caustic soda actually is.
1.1 What is Caustic Soda?
Caustic soda, or sodium hydroxide (NaOH), is a highly caustic and reactive compound. It is usually found in its solid form as white crystalline flakes, pellets, or powder. When dissolved in water, it forms liquid caustic soda, which is the focus of our exploration today.
1.2 Common Uses and Applications
Liquid caustic soda is used in a multitude of industries and processes. It is a key ingredient in the production of various chemicals, including detergents, soaps, and textiles. It is also widely used in water treatment, pulp and paper manufacturing, aluminum production, and numerous other industrial applications.
1.3 Importance of Understanding its Corrosive Nature
Given its strong alkaline nature, it is crucial to understand how liquid caustic soda interacts with different materials. Its corrosive properties can cause significant damage to various substances, leading to safety hazards, structural failures, and financial losses. Therefore, it is essential to know the corrosion mechanisms and effects of liquid caustic soda on different materials to ensure proper handling and prevent potential accidents.
2. Corrosion Mechanisms and Effects on Different Materials
Now that we have a grasp of liquid caustic soda, let’s delve into how it corrodes different materials and the consequences of such corrosion.
2.1 Chemical Reactions with Different Material Types
Liquid caustic soda can react with a wide range of materials, including metals, alloys, plastics, ceramics, and elastomers. The specific reactions depend on the chemical composition and properties of the material. For example, with metals, caustic soda can cause a process called saponification, where the metal hydroxide is formed, accompanied by the release of hydrogen gas.
2.2 Factors Affecting Corrosion Rates
Several factors can influence the rate of corrosion caused by liquid caustic soda. These include concentration and temperature of the solution, exposure duration, presence of impurities, and the material’s susceptibility to alkaline attack. Understanding these factors can help determine the risks associated with using caustic soda in specific applications.
2.3 Corrosion Products and Damage Assessment
As liquid caustic soda corrodes materials, it forms various corrosion products. These corrosion by-products can further contribute to material degradation and increase the risk of failures. Assessing the damage caused by caustic soda corrosion is crucial to ensure the integrity and safety of structures or equipment, allowing for timely repairs or replacements.
See also Main Aluminum Fluoride Exporters: Market Outlook
3. Corrosion Resistance of Metals and Alloys
While liquid caustic soda can be corrosive to many materials, some metals and alloys exhibit better resistance than others. Let’s explore a few examples.
3.1 Stainless Steel and its Resistance
Stainless steel is renowned for its exceptional resistance to corrosion, making it a popular choice in industries where liquid caustic soda is used. The high chromium content in stainless steel forms a protective oxide layer that acts as a barrier against the corrosive effects of caustic soda.
3.2 Corrosion Resistance of Carbon Steel
Unlike stainless steel, carbon steel is more susceptible to corrosion by liquid caustic soda. However, by implementing proper surface treatments, such as protective coatings or inhibitors, the corrosion resistance of carbon steel can be significantly improved.
3.3 Other Metals and Alloys
Other metals and alloys, such as nickel, titanium, and certain nonferrous alloys, also exhibit varying degrees of resistance to caustic soda corrosion. Understanding the performance of these materials in contact with liquid caustic soda is crucial for selecting the most suitable materials for specific applications.
4. Corrosion Behavior of Non-Metallic Materials
Liquid caustic soda not only corrodes metals and alloys but also impacts various non-metallic materials. Let’s take a look at a few examples.
4.1 Corrosion of Plastics and Polymers
Certain plastics and polymers can experience degradation when exposed to liquid caustic soda. The alkaline conditions can cause swelling, softening, or even complete disintegration of these materials. Choosing the right plastics or polymers with high chemical resistance is crucial to avoid such corrosion-related failures.
4.2 Corrosion of Ceramics and Glass
Ceramics and glass generally exhibit good resistance to caustic soda corrosion. However, prolonged exposure to concentrated solutions or elevated temperatures can lead to surface etching or other forms of degradation. Understanding the limitations of ceramics and glass under specific caustic soda conditions is vital for their proper utilization.
4.3 Corrosion of Rubber and Elastomers
Rubber and elastomeric materials can also be affected by liquid caustic soda. The alkaline environment can cause swelling, loss of elasticity, and overall deterioration of these materials. Selecting the right type of rubber or elastomer resistant to caustic soda is essential to maintain their functionality and integrity.
Understanding the corrosive nature of liquid caustic soda on different materials allows us to make informed decisions in selecting appropriate materials and implementing proper measures to mitigate corrosion risks. By doing so, we can ensure the safety, reliability, and longevity of various structures, equipment, and products in caustic soda-related industries. So, let’s dive into the world of caustic soda corrosion and embark on a journey of knowledge and wit—why not make it an adventure?
5. Protective Measures and Corrosion Prevention Techniques
5.1 Coatings and Surface Treatments
When it comes to protecting materials from the corrosive nature of liquid caustic soda, coatings and surface treatments are your best friends. Think of them as the armor that shields your materials from the relentless attack of the soda. Applying corrosion-resistant coatings such as epoxy or polyurethane can provide a barrier between the soda and the material, preventing any damage. Surface treatments like passivation can also be effective in creating a protective layer on the material’s surface.
5.2 Cathodic Protection
Cathodic protection is like having a bodyguard for your materials. It involves using sacrificial anodes or impressed current systems to provide an electrical charge that counteracts the corrosive effects of liquid caustic soda. It’s like creating a force field around your materials, ensuring they remain unharmed. This technique is particularly useful for buried or submerged structures that are exposed to the soda’s corrosive powers.
See also Caustic Soda in Dairy Industries
5.3 Material Selection and Compatibility
Choosing the right materials for the job is key to winning the battle against corrosion caused by liquid caustic soda. Not all materials are created equal, and some are more resistant to the soda’s aggressive tendencies. Stainless steel, for example, is often a preferred choice due to its high corrosion resistance. It’s like picking the perfect weapon for the fight. Additionally, understanding the compatibility between the soda and the material is crucial. Conducting compatibility tests can help determine if they will be allies or enemies.
5.4 Monitoring and Inspection
In the war against corrosion, knowledge is power. Regular monitoring and inspection of equipment and structures can help identify early signs of corrosion and prevent more extensive damage. Think of it as conducting routine check-ups to catch any potential problems before they spiral out of control. Using tools like ultrasonic thickness gauges or visual inspections can give you a better understanding of the battlefield and take appropriate action to mitigate corrosion.
6. Handling and Storage of Liquid Caustic Soda
6.1 Safety Precautions and Regulations
When dealing with liquid caustic soda, safety should always be your top priority. It’s like playing with fire, except the fire is a highly corrosive chemical. Adhering to safety precautions and regulations is essential to protect yourself and others. This includes wearing appropriate personal protective equipment, ensuring proper ventilation, and following guidelines for handling hazardous materials.
6.2 Proper Handling Procedures
You wouldn’t juggle dynamite, and you shouldn’t mishandle liquid caustic soda either. Proper handling procedures are crucial in minimizing the risk of accidents and corrosion damage. This means using suitable equipment, such as chemical-resistant gloves and goggles, and being mindful of potential hazards. It’s like handling a delicate glass sculpture – one wrong move, and things could shatter.
6.3 Storage Recommendations
Storing liquid caustic soda requires a bit of strategic planning. Just like organizing your pantry, you need to keep incompatible materials separate and ensure proper containment. Storing the soda in corrosion-resistant containers or tanks can prevent leaks and spills, minimizing the risk of damage to the surrounding environment and materials. Proper labeling and signage are also essential to avoid any confusion or mishaps.
7. Case Studies and Real-Life Examples of Corrosion Damage
7.1 Corrosion in Chemical Processing Plants
Imagine a chemical processing plant as a battleground, where liquid caustic soda wages war on various materials. Corrosion in chemical processing plants can lead to equipment failure, leaks, and even safety hazards. Real-life examples highlight the importance of implementing corrosion prevention techniques and choosing the right materials to withstand the soda’s relentless attacks.
7.2 Corrosion in Transportation and Storage Facilities
Transporting and storing liquid caustic soda is no easy task. Corrosion damage in transportation and storage facilities can impact not only the materials but also the surrounding environment. Case studies demonstrate the potential consequences of corrosion and emphasize the need for proper handling, storage, and preventive measures to ensure the safe transport and containment of the soda.
7.3 Environmental Impact and Accidental Spills
When the battleground expands beyond plants and facilities, the environment becomes a casualty of corrosion. Accidental spills or leaks can have severe environmental consequences, contaminating soil and water, endangering wildlife, and disrupting ecosystems. Real-life examples serve as a reminder of the importance of responsible handling, storage, and prompt response to prevent or mitigate such incidents.
See also Caustic soda flakes bags considerations
8. Conclusion and Future Perspectives in Managing Corrosion with Liquid Caustic Soda
In conclusion, understanding the corrosive nature of liquid caustic soda and implementing protective measures is crucial to safeguard materials and prevent damage. Coatings, cathodic protection, material selection, monitoring, and inspection are valuable tools in the fight against corrosion. Proper handling, storage, and adherence to safety regulations are essential to ensure the safe use and transport of the soda. Real-life case studies provide valuable lessons and emphasize the need for proactive measures. As we move forward, continued research and innovation will play a vital role in developing new techniques and materials to better combat corrosion caused by liquid caustic soda. So, let’s raise our epoxy-coated glasses and toast to a future where corrosion is a thing of the past! Cheers!
In conclusion, understanding the corrosive nature of liquid caustic soda on different materials is paramount for maintaining the integrity and safety of various industries. By recognizing the mechanisms of corrosion, the effects on different materials, and implementing appropriate protective measures, professionals can effectively manage corrosion risks associated with liquid caustic soda. With proper handling, storage, and adherence to preventive techniques, the potential for damage and the resulting financial and environmental consequences can be minimized. By staying vigilant and proactive in corrosion management, we can ensure the longevity and reliability of equipment, infrastructure, and facilities in which liquid caustic soda is utilized.
FAQ
1. Is liquid caustic soda corrosive to all materials?
Yes, liquid caustic soda is highly corrosive and can cause damage to a wide range of materials. However, the extent and rate of corrosion may vary depending on the specific material and its resistance to caustic soda.
2. How can I protect equipment and infrastructure from corrosion caused by liquid caustic soda?
There are several protective measures that can be implemented to mitigate corrosion risks. These include using corrosion-resistant materials, applying coatings or surface treatments, implementing cathodic protection systems, and monitoring and inspecting equipment regularly.
3. What safety precautions should be taken when handling liquid caustic soda?
When handling liquid caustic soda, it is important to wear appropriate protective clothing, including gloves, goggles, and a face shield. Adequate ventilation should be ensured, and spills should be promptly cleaned up using suitable neutralizing agents. Proper training and adherence to safety protocols are crucial to minimize the risks associated with handling liquid caustic soda.
4. Are there any environmental concerns associated with the use of liquid caustic soda?
Yes, the improper handling or accidental spills of liquid caustic soda can have significant environmental impacts. It can lead to the contamination of soil, waterways, and groundwater, posing a threat to aquatic life and ecosystems. Strict adherence to safety guidelines and proper containment measures are essential to prevent environmental incidents.
Hossein Moshiri
WA +989124311007