The Impact If Cold Working Machines Affects The Mechanical Properties Of Metals Is Widely Studied
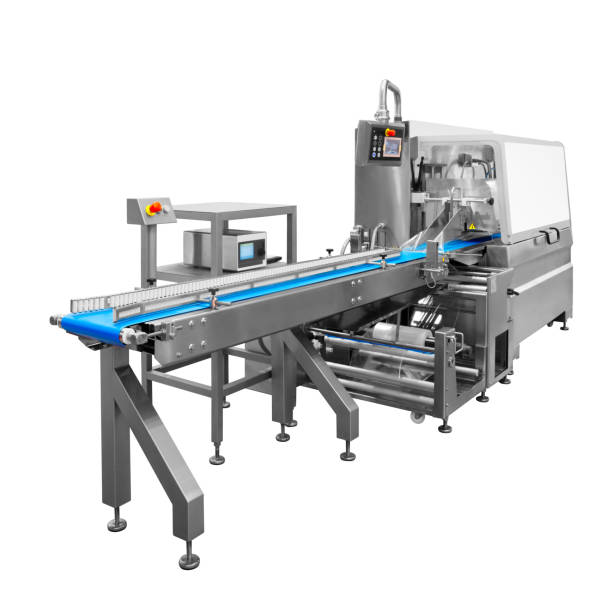
The mechanics and optical characteristics exhibited by metal materials are crucial to assessing their suitability to particular applications. Cold working is widely employed by the metalworking industry for manipulating the tensile strength and stiffness characteristics. However, how can these devices influence the mechanics and strength characteristics associated with metal products? This blog will analyze the impacts that cold working machinery has had upon the mechanics of metalworking.
Section 1:1: Introduction to cold working machines.
Cold working refers specifically and specifically to the term "cold working." The cold working process involves using cold working machinery, including a rolling mill, drawing machine, or forge machine. These machinery applies pressure to the material, thereby resulting in its shape, size, or modification due to the changes. The degree to which this deformity occurs impacts the strength, ductility, as well as toughness associated with the material.
Section 3: The effect of cold working (CWO) on metal properties.
During cold working, a material's grain structures become increasingly complex, resulting in dislocation. Consequently, the material becomes significantly stronger while also becoming harder. The amount and type of cold working affect the metal's ductility. The greater the deformation, the lower the ductility, and thus, the greater the tendency toward cracks. Additionally, the cold working process causes the toughness to decrease. Nevertheless, there exists Cold drawing machine of cold working that a material can endure before it deteriorates significantly, causing it to become brittle, causing potential failure.
Section 4: Types of cold working Processed
The cold working capacity for a particular metal depends on numerous variables, such as its composition, its starting state, or the straightening machine used. Depending on the metal, cold working is required to obtain particular structural characteristics. Consequently, alloy that exhibits higher work hardener requirements may necessitate higher cold working to obtain the desired strength compared to alloy that exhibits lower hardening rates.
The cold working process is also influenced by the start state and final state. Metal that has already been work-hardened may take more effort to deflect compared to those which haven't been. The cold working machine type employed can also affect the amount and type of cold working a material can withstand. Similarly, for instance, using spiraling or cutting tools, we can produce a finer grain structure.
Section 4.1: Benefits of cold working machines.
Regardless of the difficulties that come along, cold working offers many advantages for the metalworking industry. Cold working strengthens the weldability, resulting in greater durability which is highly resistant to damage. They help to maintain the quality level for metal surfaces by improving their surface finishes along with ensuring more precise metering. Ultimately, using swaging machine can be a cost-effective alternative for transforming metal into a desired shape than previously employed sophisticated or costly processes.
Conclusion:
Cold working machinery is vital for the metalworking industry, allowing for manipulation and modification of tensile strength and rigidity. The degree cold affects all aspects related to the physical property, namely strength, ductility, or toughness. Factors like a material's composition, its initial state, or the cold working machine used determine the cold working that varies between different metals.
Despite the difficulties of cold working involving brittleness and susceptibility to failure, the advantages of cold working, resulting in increased structure strength, far outweigh the inherent risk.