Теоретические основы науки о процессах и аппаратах и их практическое применение. Контрольная работа. Другое.
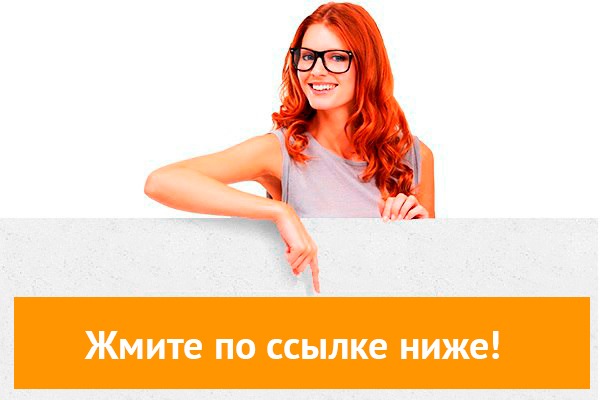
💣 👉🏻👉🏻👉🏻 ВСЯ ИНФОРМАЦИЯ ДОСТУПНА ЗДЕСЬ ЖМИТЕ 👈🏻👈🏻👈🏻
Вы можете узнать стоимость помощи в написании студенческой работы.
Помощь в написании работы, которую точно примут!
Похожие работы на - Теоретические основы науки о процессах и аппаратах и их практическое применение
Скачать Скачать документ
Информация о работе Информация о работе
Скачать Скачать документ
Информация о работе Информация о работе
Скачать Скачать документ
Информация о работе Информация о работе
Скачать Скачать документ
Информация о работе Информация о работе
Скачать Скачать документ
Информация о работе Информация о работе
Скачать Скачать документ
Информация о работе Информация о работе
Скачать Скачать документ
Информация о работе Информация о работе
Нужна качественная работа без плагиата?
Не нашел материал для своей работы?
Поможем написать качественную работу Без плагиата!
пищевой производство переработка зерно
Раздел 1.
Теоретические основы науки о процессах и аппаратах
.1 Основные
законы науки о процессах и аппаратах
.1
Оборудование для механической переработки зерна
Раздел 3. Гидромеханические
процессы
.1 Способы
сушки, реализуемые в сушилках
Раздел 1. Теоретические основы науки о процессах и аппаратах
1. На основе законов статики устанавливают начальные и конечные
значения параметров процесса и направление его течения.
2. На основе закона сохранения материи составляют материальный
баланс.
. На основе закона сохранения энергии составляют энергетический
(тепловой) баланс.
. На основе законов кинетики устанавливают движущую силу и
коэффициент скорости процесса.
. По полученным данным определяют основной размер аппарата.
. Рассчитывают несколько вариантов аппаратуры и на основе
технико-экономического анализа определяют оптимальный вариант.
Законы статики и кинетики, сохранения материи и энергии, являясь
фундаментальными законами природы, по сути сформировали дисциплину ПАПП в
качестве науки.
Наука отличается от других "учений" тем, что ответ на нарушение
закона на каком-либо производстве следует незамедлительно: авария, пожар,
взрыв, катастрофа и т.д. Во избежание этого техника безопасности (ТБ) проходит
через весь курс ПАПП. Рассмотрим изложенные выше пункты схемы чуть более
подробно.
Любой процесс протекает до тех пор, пока система не придет в состояние
равновесия. Статика рассматривает процесс в состоянии равновесия.
Различают гидростатику (учение о равновесии жидкостей), а также тепловое,
фазовое и химическое равновесие.
Например, фазовое или диффузионное равновесие для насыщенных растворов в
воде при 100°С (растворимость):
поваренная соль (хлористый натрий) - 39,8 г(100 г воды; 28,5% мас. сахар
- 487 г)100 г воды; 83% масс.
В общем виде его можно записать так:
где - количество веществ, поступающих на переработку;
- количество веществ, полученных в результате переработки
Современные технологии должны предусматривать, что потерь и отходов не
должно быть /безотходные технологии/. Но пока они есть.
Отходы в пищевой промышленности обычно используются для откорма животных
/дополнительный цех/.
Потери химической промышленности довольно часто отравляют окружающую
среду, в том числе и население. Например, Ярославский НПЗ /Славнефть/ ежегодно
"теряет" в атмосферу 100 тыс. т углеводородов. В 1999 году выбросы
загрязняющих веществ /не только от химической промышленности/ в атмосферу
города Ярославля составили 270 тыс. т.
Из Западной Европы с попутным ветром в Россию ежегодно поступает 2 млн. т
сернистого газа и 10 млн. т сульфатов.
где - тепло, поступающее с исходными веществами,
- тепло, уходящее с конечными продуктами,
- потери тепла в окружающую среду.
Потери тепла неизбежны; но они должны быть сведены к минимуму (подбор
тепловой изоляции) или утилизированы (тепловые потери аппаратов учитываются в
системе отопления цеха). Одним из лучших теплоизоляторов считается стекловолокно
(маты), плотность 120-200 кг/м 3 , коэффициент теплопроводности 0,04
Вт/м.
Потери тепла в виде "дымовой завесы" от печей, котельных и
тепловых электростанций (ТЭС) связаны с загрязнением окружающей среды. Так,
ТЭС, работающие на каменном угле, на 1 млн. кВт-ч вырабатываемой электроэнергии
выбрасывают в атмосферу: 15 т сернистого газа, 10 т золы и 3 т оксидов азота.
Дисциплина ПАПП имеет обширный арсенал аппаратуры для очистки (до ПДК -
предельно допустимая концентрация) дымовых газов от пыли и вредных газовых
компонентов, а также для утилизации из них тепла: аппараты пылегазоочистки,
контактные теплообменники, абсорберы, адсорберы и др.
Кинетика рассматривает процессы в их развитии, в их стремлении к
состоянию равновесия.
Степень отклонения системы от состояния равновесия выражает движущую силу
процесса.
Для процессов дисциплины ПАПП применима основная кинетическая
закономерность:
Скорость процесса прямо пропорциональна движущей силе и обратно
пропорциональна сопротивлению.
Для механических и химических процессов эта закономерность не
применяется. Но эти процессы подчас находятся на производстве в одной
технологической линии с основными процессами, например, сахарную свеклу перед
выщелачиванием измельчают или шинкуют. Поэтому в некоторых вузах указанные
процессы вводят в дисциплину ПАПП.
Для гидромеханических процессов основная кинетическая закономерность
принимает вид:
где V - объем протекающей жидкости, м 3 ,- сечение аппарата, м 2 ,
ρ - плотность жидкости, кг/м 3 ,=
9,81 м/с 2 , Г - гидравлическое сопротивление, кг/м 2 .с, Г -
коэффициент скорости, м 2 .с/кг,
ΔH d - разность полных гидродинамических
напоров, м.
Последняя величина определяется по уравнению Бернулли:
В учебной и технической литературе за гидравлическое сопротивление часто
ошибочно принимаются потери напора в аппарате (Δp n или h n ).
Для тепловых процессов кинетическое уравнение записывается:
где Q - количество переданного тепла, Дж,- поверхность теплопередачи, м 2 ,
Δt - разность температур между
теплоносителями, К или °С,- термическое сопротивление, м 2 .К/Вт,-
коэффициент теплопередачи, Вт/м 2 .К.
где М - количество вещества, перенесенного из одной фазы в другую, кг или
кмоль,- поверхность контакта фаз (массопередачи), м 2 , Y -
коэффициент массопередачи, кг/м 2 .c. , Y - диффузионное
сопротивление, м 2 .с. /кг,
Например, если для растворения сахара при 100 °С принимается чистая вода
(Y=0), то в начальный момент времени движущая сила процесса растворения
составит:
ΔY = Y нас. - Y = 487/100 - 0 = 4,87 отн. мас.
долей [1, с. 11-14].
При производстве муки процесс измельчения зерна и промежуточных продуктов
является одним из главных, так как в значительной мере влияет на выход и
качество готовой продукции, на эффективность и стабильность работы последующего
оборудования для сортирования продуктов размола.
Измельчение зерна - одна из наиболее энергоемких операций.
Технологические приемы и машины, применяемые для измельчения, в значительной
степени определяют техникоэкономические показатели мукомольного завода.
Основной измельчающей машиной в процессе производства муки, определяющей
режим работы, производительность и эффективность последующего технологического
и транспортного оборудования, служит вальцовый станок. Дополнительные
(вспомогательные) операции измельчения осуществляют в результате ударного
воздействия в вымольных машинах, энтолейторах, деташерах. Рабочими органами
вальцовых станков являются парноработающие вальцы, вращающиеся навстречу друг
другу с разными скоростями. Рабочая часть вальцов представляет собой выполненный
из чугуна цилиндр диаметром чаще всего 250 мм и длиной 600, 800 и 1000 мм.
Изготавливают вальцы также диаметром 185 и 300 мм и длиной 400 и 1250 мм, а
также 1500 мм. Основные факторы, влияющие на процесс измельчения зерновых
продуктов в вальцовых станках,- это структурномеханические и технологические
свойства зерна, кинематические и геометрические параметры парноработающих
вальцов и нагрузка на машину. Наибольшее влияние на эффективность процесса
измельчения в вальцовых станках оказывают стекловидность и влажность зерновой
массы.
Вальцовые станки. В мукомольной промышленности используются несколько
основных типов станков, как отечественного производства, так и импортных.
Принцип действия и рабочие органы станков идентичны, но имеются отличия в устройстве
ряда узлов.
Вальцовые станки, как правило, имеют две пары вальцов, работающих
автономно. В каждой секции кроме вальцов установлены питающий механизм,
привально-отвальное устройство, автомат управления, приемные и выпускные
устройства. Основной моделью вальцового станка является станок марки А1-БЗН,
имеющий несколько модификаций (рис. 1).
При поступлении продукта в станок срабатывает установленный в приемной
трубе датчик уровня, сигнал которого подается на механизмы привала-отвала и
питающие валики. Питающий механизм начнет подавать продукт на рабочие вальцы,
механизм привала-отвала установит заданный зазор между вальцами. При
прекращении подачи продукта электронная схема разомкнет электропневматический
клапан и через систему рычагов произойдет отвал мелющих вальцов и остановка
питающего механизма.
Рис. 1. Вальцовый станок А1-БЗН: 1,2 - мелющие вальцы; 3 - дозирующий
валик; 4 - питающий шнек; 5 - датчики питания (шторки); 6 - приемная труба; 7 -
горловина; 8 - сигнализатор уровня; 9 - заслонка; 10 - регулятор питающего
зазора; 11 - ножи-очистители; 12 - выпускной буикер; 13 - щетки-очистители
Отличительная особенность станка - охлаждение водой быстровращающегося
вальца. Охлаждение вальцов оказывает положительное влияние на технологические
показатели помола. Снижение температуры в зоне измельчения предотвращает
подсушивание и чрезмерное измельчение оболочек, а также перегрев продуктов
размола. Расход воды на охлаждение не превышает 0,2 м 3 /ч для одного
вальцового станка.
Измельчение в машинах ударно-истирающего действия
На различных этапах производства муки наряду с основным измельчением и
сортированием используют вспомогательные операции в машинах ударно-истирающего
действия: вымольной машине А1 -БВГ, энтолейторе РЗ-БЭР, деташере А1-БДГ. Как
правило, такие машины устанавливают после основных, они функционально связаны с
последующими технологическими операциями.
На заключительном этапе последовательного измельчения зерна и извлечения
из него большей части эндосперма остаются продукты измельчения, которые
содержат основное количество оболочек и остатки сросшихся с ними частиц
эндосперма. Отделение частиц эндосперма от оболочек является важной
технологической операцией - вымолом, который производится в машине А1-БВГ. В результате
этого получают две фракции: сходовую - отруби и проходовую - трудносыпучую
смесь, содержащую муку. Эту фракцию подвергают обработке в виброцентрофугале
РЗ-БЦА.
Размол продуктов на микрошероховатых вальцах хотя и улучшает качество
муки по сравнению с рифлеными, но в количественном отношении уступает им.
Поэтому с целью повышения извлечения муки после вальцовых станков продукты
измельчения обрабатываются в энтолейторах РЗ-БЭР или деташерах А1-БДГ. Причем
энтолейторы применяют для дополнительного измельчения продуктов с относительно
малым содержанием оболочечных частиц. Поэтому в результате интенсивного
измельчения продуктов в энтолейторах практически не происходит изменения
зольности муки. На последующих системах наблюдается тенденция агрегатирования,
сплющивания частиц более высокой зольности и большей влажности. Для разрушения
образовавшихся после вальцов так называемых лепешек устанавливают деташеры
А1-БДГ с более низкой, чем у энтолейторов, окружной скоростью (11 м/с).
В этом случае не преследуется цель интенсивного разрушения частиц, что
привело бы к повышению зольности.
Вымольная машина А1-БВГ сочетает ударно-истирающее воздействие бичей
различной интенсивности с процессом просеивания. Ударное воздействие бичей в
совокупности с трением между частицами и о ситовую поверхность нарушает связь
между оболочками и эндоспермом, способствует измельчению частиц эндосперма. При
просеивании через ситовой цилиндр под действием центробежных сил инерции,
возникающих от вращения ротора, продукты измельчения разделяются на две
фракции: сходовую, содержащую относительно крупные частицы отрубей, и
проходовую с большим содержанием эндосперма.
Основными механико-технологическими параметрами бичевых просеивающих
машин служат окружная скорость бичевого ротора и размер отверстий сит. Важную
роль играют нагрузка, продолжительность обработки продукта и степень
использования ситовой поверхности.
В вымольной машине А1-БВГ определяющий процесс - измельчение,
соответственно окружная скорость ротора составляет 22...24 м/с. Наряду с общими
для всех машин показателями работы - производительностью и энергоемкостью, в
соответствии с выполняемой технологической операцией по размолу оценивается
эффективность каждой машины. Технологическая эффективность машин А1-БВГ
характеризуется увеличением зольности сходовой фракции и уменьшением проходовой
сравнительно с исходными показателями, а также дополнительным извлечением муки.
Режим работы обеих машин должен обеспечивать суммарное извлечение муки в
количестве 2-6% к массе продукта, поступающего на размол.
Основными рабочими органами вымольной машины А1-БВГ (рис. 2) служат
вращающийся бичевой ротор и ситовой полуцилиндр. Исходная смесь I через
приемный патрубок 1 поступает в приемную камеру с регулируемыми спаренными
клапанами 2, которые направляют смесь в рабочую зону. Вращающиеся бичи ротора 3
подхватывают продукт и отбрасывают его к поверхности ситового полуцилиндра 4.
Рис. 2. Технологическая схема вымольной машины А1-БВГ 1 - приемный
патрубок, 2 - клапаны, 3 - бичи ротора; 1 - ситовой полуцилиндр, I - исходная
смесь, II - мучнистая смесь, III - отрубянистые частицы [2, с. 125-140]
Раздел 3. Гидромеханические процессы
Схемы смесителей. Схема смесителя определяется
способом перемешивания. Используют следующие способы перемешивания:
механический, поточный, пневматический. Им соответствуют аппараты для
перемешивания - мешалки, смесители жидкостных потоков и пневматические
смесители.
Мешалки могут быть лопастными, планетарными, пропеллерными,
турбинными и др.
Лопастные мешалки перемешивают жидкие продукты
лопастями, прикрепленными к валу привода, вращающемуся в любой плоскости.
Лопасти могут быть развернуты к направлению вращения, их число и схема
закрепления на валу различны (рис. 3).
Рис. 3. Схемы лопастных мешалок: а -устройство лопастей; б - парные
лопасти; в -мешалка с отражателями; г -решетчатая мешалка; д - якорная мешалка
Чтобы предотвратить движение жидких смесей, особенно
вязких, на неподвижных стенках корпуса устанавливают отражатели. Для
перемешивания систем, выделяющих осадок, применяют якорные мешалки. Обычная
частота вращения якоря мешалок 20...80 об/мин, но могут применяться и более
скоростные устройства (до 400 об/мин).
Планетарные мешалки применяют для перемешивания вязких
смесей (рис. 4).
Пропеллерные мешалки (рис. 5, а) в качестве рабочего
органа используют пропеллер (винт). Диаметр его составляет 1/3... 1/4 диаметра
сосуда. Различают двух- и трехлопастные винты. Пропеллерные мешалки
обеспечивают образование сложного поля скоростей, что улучшает перемешивание.
Рис. 4. Схема планетарной мешалки: 1- зубчатое колесо привода; 2-
планетарное зубчатое колесо; 3 - водило; 4-месильный орган
Такие мешалки могут иметь и несколько винтов на одной
оси с разным наклоном лопастей. Частота вращения 150...1000 об/мин. При
направлении потока на дно сосуда он хорошо "взмучивает" осадок с
относительно крупными частицами (размерами до 150мкм). Такие мешалки могут иметь
и несколько винтов на одной оси с разным наклоном лопастей. Их применяют при
умеренной вязкости жидкости (до 6 Па с). Недостаток - большое потребление
энергии.
Рис. 5. Схемы пропеллерной (а) и турбинной (б) мешалок
Турбинные мешалки (рис. 5, 6) представляют собой турбинные колеса,
закрепленные на вертикальном валу и вращающиеся со скоростью 200-2000 об/мин.
Турбины похожи на колеса центробежных насосов и могут иметь часть их статора.
Такие мешалки эффективны и применяются для перемешивания и маловязких, и вязких
жидкостей (до 500 Па • с). Они хорошо "взмучивают" осадки твердой фазы и применяются для перемешивания в
жидкостях твердых сыпучих материалов с размерами частиц до 25 мкм и их
содержанием до 60% по массе. Строго говоря, термин "турбинные колеса" неудачный, так как турбины в данном
случае не применяются как устройства, преобразующие поступательное движение
потока во вращательное движение ротора. Так называемые турбинные колеса мешалок
остаются по своей сути пропеллерами, преобразующими вращательное движение вала
в движение среды. Пневматическое перемешивание заключается в барботировании
(течении) воздуха или пара через слой смешиваемых продуктов. Этот процесс
течения газа через жидкость и их перемешивания рассматривается подробнее при
изучении брагоперегонного процесса. Применяют пневматическое перемешивание при
вязкости продукта до 200 Па • с, при замачивании зерна в воде для приготовления
солода и др. Для перемешивания высоколетучих компонентов этот способ не рекомендуется,
так как при этом вместе с воздухом уносится много летучих веществ.
Схема пневматического смесителя показана на рисунке 6.
Поточные (или эжекторные) смесители применяют для
организации непрерывного или поточного перемешивания продуктов. Они представляют
собой колонны с горизонтальными решетчатыми перегородками, разделяющими потоки
на части и создающими возможность их нового соединения. Устройство таких колонн
многообразно.
Расчет расхода энергии на перемешивание. Расход
энергии на привод механических мешалок определяют на основании
экспериментальных исследований однотипных конструкций. Результаты исследований
для каждого типа мешалок обобщают с помощью критериальных зависимостей, которые
выводят с использованием метода теории размерностей. Получим их.
Первый шаг метода - составление перечня действующих
факторов. В данном случае эта задача относительно проста. Очевидно, что на
потребляемую мешалкой мощность N влияют (для фиксированного типа мешалки):
характерный размер, в данном случае диметр лопастей d; частота вращения л;
динамическая вязкость μ и плотность р жидкости:
Перечень определяющих параметров: N, d, п, μ, ρ, т. е. всего 5 переменных.
Второй шаг метода - определение числа независимых размерностей.
Для этого выпишем единицы измерения всех величин перечня параметров:
Независимые размерности в этом перечне - килограмм,
метр и секунда - всего три размерности.
Рис. 6. Схема пневматического смесителя (барботера): 1 - корпус; 2-
барботер
Согласно π-теореме данное явление определяется двумя
безразмерными комплексами параметров, так как
На третьем шаге составим из приведенного перечня
параметров два независимых безразмерных комплекса. Это можно сделать простым
подбором. Однако помощь здесь может оказать и предварительный анализ искомых
зависимостей. Перемешивание - гидродинамический процесс, в который входит
образование поля скоростей и давлений в жидкой среде и на который влияют силы
вязкости и инерции. На основании анализа известных критериев гидродинамического
подобия можно предположить, что на процесс влияют только два критерия:
Рейнольдса и Эйлера. Все критерии, характеризующие свободное движение, здесь
неприменимы, так как исследуемое движение вынужденное, а критерий Фруда не может
быть использован в анализе, так как влиянием движения под действием силы
тяжести в исследуемом процессе пренебрегаем.
Комбинируя параметры (с возможным учетом данной
подсказки), получим два безразмерных комплекса параметров:
Первый из этих комплексов совпадает по физическому
смыслу с критерием Эйлера (Ей), т. е.
где v - скорость жидкости, м/с; Δp - перепад давлений, Па.
С учетом переводных коэффициентов, используемых при
преобразовании параметров, можно утверждать, что первый из выписанных
безразмерных комплексов пропорционален критерию Эйлера и может быть назван
критерием мощности - для данной задачи К N = Eu m .
Второй из этих комплексов пропорционален критерию
Рейнольдса, т. е.
Таким образом, связь параметров можно искать в
критериальной форме
Обобщение экспериментальных данных для ряда
конструкций мешалок, схемы которых приведены на рисунке 7, дано на рисунке 8.
Эти зависимости более точные, чем аппроксимируемые степенной зависимостью
Букингема-Рейнера
где C=const; a = const. Поэтому использование зависимости в графическом виде
предпочтительнее.
Расчет выполняют следующим образом. По заданному типу
расчетной мешалки выбирают наиболее подходящую и определяют соотношения
характерных параметров мешалки. Далее, вычислив значение критерия Рейнольдса,
по графикам, изображенным на рисунке 16.8, для соответствующего типа мешалки
находят значение критерия Эйлера и по нему вычисляют мощность N, затрачиваемую
на перемешивание. Это значение мощности увеличивают на величину пусковой
мощности, затрачиваемой на преодоление инерции жидкости в пусковой момент, и на
компенсацию других потерь.
Рис. 7. Схемы рассчитываемых мешалок: 1-двухлопастной; 2 - пропеллерной
без перегородок; 3 - пропеллерной с четырьмя перегородками при S/d =1; 4-
шестилопастной; 5-пропеллерной с четырьмя перегородками при S/d=2
Рис. 8. Критериальные зависимости потребляемой мощности от типа и
параметров мешалок: 1 - двухлопастной; 2- пропеллерной без перегородок; 3 -
пропеллерной с четырьмя перегородками при S/d= 1; 4- шестилопастной; 5 -
пропеллерной с четырьмя перегородками при S/d= 2
где v - скорость жидкости, м/с; v = 2πrn; r- расстояние площадки от оси
вращения, м; n - частота вращения вала, об/с; ρ - плотность жидкости, кг/м 3 .
Мощность dN K , затрачиваемая на приведение
этой массы в движение, определяется выражением
Интегрируем это выражение по лопасти, т. е. от r = r 0
до r = R,
где r 0 , R- начальный и конечный радиусы
лопасти, м:
Для гарантии работоспособности мощность двигателя
выбирают больше этого значения - на 50% для лопастных мешалок и на 10-15% для
пропеллерных и турбинных.
Расход энергии при пневматическом перемешивании
находят следующим образом.
При пневматическом перемешивании расход воздуха
составляет 0,4-1,0 м 3 /мин на 1 м 2 свободной поверхности
жидкости.
Давление воздуха на выходе из воздуходувки тратится на
преодоление гидравлического сопротивления магистралей Δр 1 (Па) и давления столба
жидкости над барботерной решеткой в сосуде Δр 2 (Па). Мощность
воздуходувки (Вт)
где V- объемный расход воздуха, m 3 /c; η - КПД воздуходувки [3, с. 221-227].
Рассмотрим построение процесса сушки на I-х - диаграмме. Сделаем
построение для случая, когда (приход тепла больше чем расход). Сначала построим график
теоретического процесса для заданных условий работы сушилки (линии ).
При состояние воздуха в сушильной камере изменяется не в
соответствии с линией , а по какой-то линии, лежащей выше этой линии и имеющей
начало в точке , например, в соответствии с линией . Если воздух выходит из сушилки при
одной и той же относительной влажности, то теплосодержание его в точке больше чем в точке .
По этому выражению можно определить положение линии при известном .
При заданных условиях сушки строим линии теоретического процесса. Через
произвольную точку на линии проводим линию и измеряем (в мм). По формуле определяем (в мм).
где - соотношение масштабов теплосодержания и влагосодержания.
Откладываем и через точки и проводим линию действительного
процесса . Аналогично находим линию
действительного процесса сушки при .
Удельный расход тепла в подогревателе:
Кроме нормального сушильного процесса могут быть построены иные процессы,
отличающиеся способом подвода тепла к сушильному агенту.
Рис. 9. Процесс в сушилке с подогревом внутри камеры
Применение того или иного варианта определяется свойствами материала и
стремлением создать наиболее экономичный сушильный процесс.
А) Сушилка с подогревом воздуха в сушильной камере.
Теплота может вноситься не только в подогревателе, но также частично в
сушильную камеру. Крайним случаем будет, когда вся теплота вводится в сушильную
камеру (линия АС на рис. 9). Между двумя крайними положениями линий сушки (ВС и
АС) могут быть расположены линии процессов с последовательно увеличивающимся
количеством теплоты, вводимой в подогреватель. Процесс АВС соответствует
случаю, когда в сушилку введено такое количество теплоты, которое компенсирует
потери в окружающее пространство.
Одним из промежуточных положений линий сушки будет линия В 1 С,
которая совпадает с изотермой, проходящей через точку С. В этом случае процесс
будет протекать при постоянной температуре. Часть теплоты в этом случае будет
введена в калорифер, а остальная часть в сушилку.
Данный вариант сушильного процесса имеет то преимущество, что может
протекать при низкой температуре. Это важно при работе с материалами, которые
при высоких температурах разлагаются.
Б) Сушилка с многократным промежуточным нагреванием воздуха.
Рис.10. Схема сушилки с многократным промежуточным подогревом воздуха (а)
и изображение процесса на i-x диаграмме (б).
Температура сушильного агента может быть снижена при сушке с
промежуточным подогревом воздуха (рис. 10). Воздух, отработанный в первой
камере, направляется в первый промежуточный подогреватель; подогретый воздух
поступает во вторую сушильную камеру и т.д. Вертикальные отрезки АВ 1 ,
С 1 В 2 , С 2 В 3 и С 3 В 4
изображают подогрев в основном и в трех промежуточных подогревателях, когда
воздух, выходящий из камер, имеет температуру t и D=0. Удельный расход воздуха в этой
сушилке будет
Расход воздуха и теплоты мог бы быть таким же в нормальном процессе сушки
АВС (пунктирные линии рис. 9), но только при значительно более высокой
температуре. Такую схему применяют для сушки пищевых материалов, не
выдерживающих высоких температур (макаронные изделия, сушки и т.д.).
В) Сушилка с частичной рециркуляцией отработанного воздуха.
Исходный воздух (точка А рис. 11), смешивается с частью отработанного
воздуха (линии АС и ВС), затем смесь нагревается в калорифере до температуры
сушки и взаимодействует с высушиваемым
материалом.
Конечные параметры воздуха определяет точка В. По сравнению с сушкой при
однократном проходе воздуха, для этого варианта характерны пониженная
температура воздуха при сушке вместо , повышенное начальное влагосодержание вместо и большая линейная скорость газа в
сушилке. Эти параметры зависят от кратности смешения
Рис.11. Схема сушилки с возвратом отработавшего воздуха (а) и изображение
процесса на i-x диаграмме (б).
Расходы теплоты будут одинаковы как и в сушилке без циркуляции. Однако
этот процесс обеспечивает мягкий режим сушки (пастила, мармелад, макароны). В
этом случае высокое парциальное давление водяных паров в циркулирующем воздухе
уменьшает движущую силу процесса, что ведет к его замедлению. Этот вариант
позволяет очень точно и гибко регулировать влажность и температуру воздуха в
сушилке.
Г) Сушилка с частичной рециркуляцией отработанного воздуха и
промежуточным нагревом.
Является сочетанием описанных выше вариантов. Для этого варианта
характерны пониженная температура воздуха, повышенное начальное влагосодержание
и относительная влажность воздуха, большая линейная скорость газа в сушилке за
счет увеличения количества циркулирующего воздуха в сушилке [4, с. 74-77].
α - угол наклона барабана к горизонту,
6є;
μ - коэффициент разрыхления материала,
0,7;- число оборотов барабана, 9 об/мин;- радиус барабана, 0,5 м;- высота слоя
материала на сите, 0,08 м.
Рис. 12. Схема барабанного сита: 1 - вал привода; 2 - барабан-короб; 3 -
сито
α - угол наклона барабана к горизонту;
μ - коэффициент разрыхления материала;-
число оборотов барабана;- радиус барабана;- высота слоя материала на сите.
= 0,72·0,7·800·9·tg(2·6)· = 3628,8· 0,2 = 725,76· 0,008 = 5,8 т/ч
Сравним полученное значение производительности барабанного сита с 3,0
т/ч, приведенными в условии: 5,8 < 3,0 т/ч, значит барабанное сито с
заданными параметрами пригодно для просеивания 3,0 т/ч муки.
α - угол наклона пружинного грохота к
вертикали, 18є;- коэффициент трения материала о сито, 0,4;
ρ - насыпная масса материала, 1,0 т/м 3
= 1000 кг/м 3 ;- высота слоя материала на сите, 20 мм = 0,020 м;
φ - коэффициент заполнения, учитывающий
неполную загрузку несущей поверхности материалом, 0,5.
Рис. 13. Схема гирационного грохота: 1 - пружина; 2 - сито; 3 -
вал-вибратор; 4 - эксцентриситет
Частота вращения вала гирационного грохота:
α - угол наклона пружинного грохота к
вертикали.
Скорость продвижения материала по ситу:
α - угол наклона пружинного грохота к
вертикали;- коэффициент трения материала о сито.
Площадь сечения материала на грохоте S:
- площадь сечения материала на грохоте;- скорость продвижения материала
по грохоту;
φ - коэффициент заполнения, учитывающий
неполную загрузку несущей поверхности материалом.
- внутренний диаметр
барабана, 1200 мм = 1,2 м;- высота барабана, 500 мм = 0,5 м; н = r 2
- наружный радиус барабана, 600 мм = 0,6 м- частота вращения барабана, 980
об/мин; б - масса барабана, 260 кг;- диаметр шейки вала, 120 мм =
0,12 м;
Рис. 14. Схема к определению
величины давления на стенки барабана
Перевод частоты вращения барабана
в угловую скорость:
ω
- угловая скорость вращения барабана; н
= r 2 - наружный радиус барабана; б - масса барабана;
- высота барабана; н
= r 2 - наружный радиус барабана;
Внутренний радиус кольца
утфеля (по рисунку 14):
н = r 2 - наружный радиус барабана.
Мощность на сообщение кинетической энергии утфелю:
ω
- угловая скорость вращения барабана; 1
- внутренний радиус барабана; 2 - наружный радиус барабана;
τ р - время
разгона барабана. с - масса суспензии;
Контрольная работа. Другое.
Сочинение Тихий Дон Мелихов
Критерии Итогового Сочинения 2022 Года
Курсовая работа: Исследование организации стратегического планирования в российских организациях. Скачать бесплатно и без регистрации
Гаевой Усик Дипломное Проектирование
Реферат по теме XVIII век - век модернизации и просвещения
Реферат На Тему Соответствие Между Молекулами И Группами Симметрии
Курсовая работа по теме Организация прогнозирования национальной экономики
Курсовая работа: Національно-культурне відродження на західноукраїнських землях в кінці ХVІІІ – на початку ХХ ст.
Курсовая Работа На Тему Портрет Специалиста По Связям С Общественностью
Курсовая На Тему Федерация
Ответ на вопрос по теме Проблемы философии
Курсовая работа по теме Проектировка коробки скоростей привода главного движения горизонтально фрезерного станка модели 6Н81
Образование И Обучение Эссе
Контрольная Работа Письменная Часть Английский 7 Класс
Контрольная Работа 1 По Истории 7 Класс
Курсовая работа по теме Характеристика монополизма в России
Реферат по теме Международные валютные отношения
Реферат: Регресс в эволюции многоклеточных животных. Скачать бесплатно и без регистрации
Реферат: Характеристика криміналізації кредитно-фінансової системи України
Реферат: Бегущая волна в линии связи. Скачать бесплатно и без регистрации
Похожие работы на - О К.Н. Леонтьеве
Реферат: Сведения об обеспеченности образовательного процесса учебной литературой, иными информационными ресурсами и материально-техническом оснащении