Telescopic Cylinders: Chrome Plating & Counterbalance Valves
RHK Hydraulic CylindeIn the intricate world of hydraulic systems, understanding the nuances of chrome plating, counterbalance valves, hydraulic cylinder rod materials, and telescopic hydraulic cylinders is paramount. These components are the unsung heroes that ensure the seamless operation of various industrial applications, ranging from construction machinery to aerospace equipment.
I. Introduction
A. Importance of Chrome Plating in Hydraulic Systems
Chrome plating plays a pivotal role in enhancing the durability and performance of hydraulic components. The process involves electroplating a thin layer of chromium onto a metal surface, providing excellent corrosion resistance and increased hardness. In hydraulic systems, where components are subjected to harsh conditions, chrome plating acts as a shield, prolonging the lifespan of vital parts.
B. Role of Counterbalance Valves in Hydraulic Systems
Counterbalance valve, also known as over-center valve, are essential in hydraulic systems to control the motion of loads. These valves ensure that loads are held in position when the directional control valve is in the neutral state, preventing load drifting and potential accidents. Their precise functionality is indispensable in applications where heavy loads need to be controlled safely.
C. Overview of Hydraulic Cylinder Rod Materials
Selecting the appropriate material for hydraulic cylinder rods is crucial for the longevity and reliability of hydraulic systems. Various materials, including stainless steel, chrome-plated steel, and hard chrome, are used based on specific requirements. Factors such as corrosion resistance, strength, and cost influence the choice of material, making it a critical decision for engineers and manufacturers.
D. Understanding Telescopic Hydraulic Cylinders
Telescopic hydraulic cylinders are a marvel of engineering, offering the ability to provide an exceptionally long stroke from a compact retracted length. These cylinders find applications in dump trucks, cranes, and other heavy machinery, where extended reach is essential. Understanding the design and maintenance of telescopic hydraulic cylinders is vital to ensuring their optimal performance.
II. Chrome Plating: Enhancing Durability and Performance
A. Benefits of Chrome Plating in Hydraulic Components
Chrome plating enhances the surface hardness of hydraulic components, making them resistant to wear and abrasion. This process significantly reduces friction, leading to smoother operation and reduced energy consumption. Additionally, chrome-plated surfaces are easier to clean and maintain, making them ideal for applications in demanding environments.
B. Process of Chrome Plating in Hydraulic Systems
The chrome plating process involves several steps, including cleaning, etching, electroplating, and polishing. Each step is crucial to achieving a uniform and durable chrome layer. Proper surface preparation and precise control of plating parameters are essential to ensure the quality and integrity of the chrome-plated surface.
C. Importance of Corrosion Resistance in Hydraulic Applications
Hydraulic systems often operate in harsh environments where exposure to moisture, chemicals, and abrasive materials is common. Corrosion resistance is paramount in preventing degradation of hydraulic components over time. Chrome plating provides an effective barrier against corrosion, ensuring the longevity of hydraulic parts even in challenging conditions.
III. Hydraulic Counterbalance Valves: Balancing Act in Hydraulic Systems
A. Functionality of Counterbalance Valves
Counterbalance valves serve a critical function in hydraulic systems by regulating loads in motion. As a load descends, these valves generate backpressure, halting uncontrolled drops. Conversely, during the upward movement of the load, the valves permit unrestricted flow, facilitating smooth and efficient operation without unnecessary hindrance. Their active role in controlling the movement of loads ensures safety and stability, preventing accidents and equipment damage. This dynamic operation allows operators to manage heavy loads with precision, enhancing overall productivity and operational efficiency in various industrial applications. Counterbalance valves, through their proactive regulation of hydraulic pressure, exemplify a key element in maintaining controlled and secure movements, vital for the reliable functioning of hydraulic systems across different industries.
B. Types of Counterbalance Valves and Their Applications
There are various types of counterbalance valves, including pilot-operated, direct-acting, and differential area valves. Each type has specific applications, ranging from mobile hydraulic systems to industrial machinery. Proper selection and installation of the appropriate valve type are essential for safe and effective load control.
C. Significance of Counterbalance Valves in Preventing Load Drifting
Counterbalance valves are crucial components in hydraulic systems, specifically designed to prevent the unwanted movement of loads. They achieve this by balancing the force exerted by the load, ensuring that it remains stationary even when external forces act upon it. By maintaining a consistent pressure in the hydraulic circuit, these valves effectively counteract the gravitational and inertial forces that could cause load drifting.
In scenarios where heavy loads need to be suspended or controlled, such as in construction equipment, manufacturing machinery, or material handling systems, preventing load drifting is essential for both safety and operational efficiency. Load drifting can lead to accidents, equipment damage, and even injuries to operators or bystanders. Counterbalance valves provide a reliable solution to this problem, offering stability and control over the loads being handled.
IV. Hydraulic Cylinder Rod Materials: Choosing the Right Material for Longevity
A. Common Materials Used in Hydraulic Cylinder Rods
Hydraulic cylinder rods are typically made from materials such as stainless steel, chrome-plated steel, and hard chrome. Each material has unique properties, making it suitable for specific applications. Stainless steel offers excellent corrosion resistance, while chrome-plated steel provides enhanced surface hardness. Hard chrome, on the other hand, combines high wear resistance with smooth operation.
B. Factors Influencing Material Selection
When selecting the material for hydraulic cylinder rods, engineers consider factors such as the operating environment, load requirements, and budget constraints. Stainless steel is ideal for applications where corrosion resistance is crucial, such as marine and food processing industries. Chrome-plated steel is commonly used in industrial machinery, while hard chrome finds applications in hydraulic cylinders subjected to heavy wear.
C. Impact of Material Selection on Cylinder Performance
The choice of material significantly impacts the performance and longevity of hydraulic cylinders. Proper material selection ensures that cylinders operate smoothly, withstand wear, and resist corrosion. Engineers must carefully evaluate the specific requirements of each application to select the most suitable material, guaranteeing optimal performance and minimizing maintenance costs.
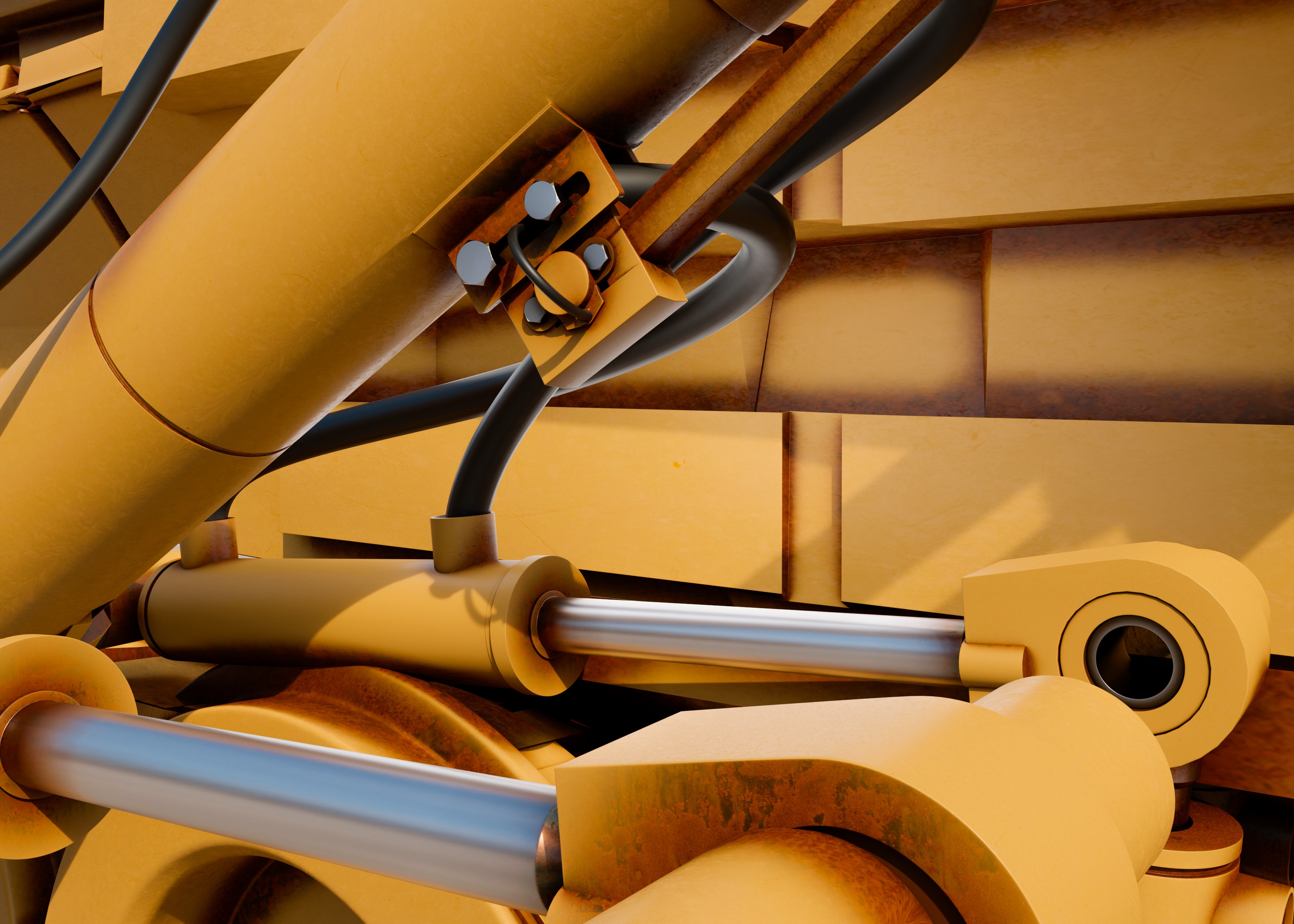