Технология изготовления пространственных кожгалантерейных изделий. Дипломная (ВКР). Другое.
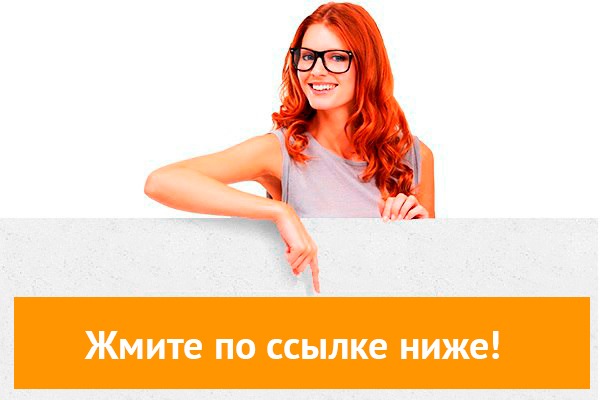
💣 👉🏻👉🏻👉🏻 ВСЯ ИНФОРМАЦИЯ ДОСТУПНА ЗДЕСЬ ЖМИТЕ 👈🏻👈🏻👈🏻
Вы можете узнать стоимость помощи в написании студенческой работы.
Помощь в написании работы, которую точно примут!
Похожие работы на - Технология изготовления пространственных кожгалантерейных изделий
Нужна качественная работа без плагиата?
Не нашел материал для своей работы?
Поможем написать качественную работу Без плагиата!
В настоящее время, когда
отечественная экономика все в большей степени переходит к рыночным условиям
функционирования, возникает необходимость расширения производства
конкурентоспособных отечественных товаров, потребительские свойства которых отвечали
бы высоким современным требованиям. При этом повышение качества товаров,
расширение ассортимента невозможно без совершенствования существующих
технологических процессов и разработки нового оборудования и оснастки.
В настоящее время уровень производства
изделий кожгалантерейной промышленности не отвечает требованиям
научно-технического прогресса. Это, прежде всего, связано с недостаточной
механизацией и автоматизацией технологических процессов, отсутствием гибкости в
перестройке производства при частой сменяемости ассортимента, ограниченным
применением широкодоступных материалов, отсутствием соответствующего
оборудования для их переработки. Вместе с тем использование натуральных кож
связано с большим количеством ручных операций, высокой материалоемкостью и
энергоемкостью существующих процессов, ограничивает разработку и внедрение
ресурсосберегающей технологии./ 1 /
Решение поставленных задач требует
комплексного подхода на основе системного анализа конструктивных и
эксплуатационных особенностей кожгалантерейных изделий, технического и
организационного уровня их производства, научных достижений в смежных областях
промышленности.
Одним из главных путей
совершенствования кожгалантерейной отрасли является расширенное применение
синтетических материалов.
Технико-экономические показатели
изготовления деталей кожгалантерейных изделий из натуральных и искусственных
кож, пленочных и текстильных материалов, в ряде случаев, не отвечает
требованиям сегодняшнего дня. Это связано с дороговизной и дефицитностью
натуральных кож, плохой формоустойчивостью деталей из натуральных кож и
пленочных материалов, их низкой эксплуатационной надежностью. Кроме того,
разнообразие технологий и применяемое оборудование без возможности перестройки
рабочего цикла значительно сдерживает ассортиментные возможности производства
кожгалантерейных изделий.
Изготовление цельноформованных
деталей из полимерных материалов позволяет расширить ассортимент и улучшить
качество таких изделий как чемоданы, дорожные и хозяйственные сумки,
ученические ранцы и т.п., снизить себестоимость кожгалантерейных изделий за
счет замены отдельных деталей из натуральных кож на полимерные материалы. Это
позволяет сократить такие подготовительные операции, как увлажнение,
проклеивание, тиснение, перфорацию, разметку и др.
Несмотря на перечисленные
преимущества изготовления полимерных деталей и общей тенденции замены
натуральных материалов в изделиях легкой промышленности их применение в
отечественном кожгалантерейном производстве ограничено. Это сопряжено с
отсутствием технологического оборудования и сложностью его проектирования, в
недостаточной изученностью процессов переработки полимеров, отсутствием
исследований по их эксплуатационной надежности.
Поэтому для устранения недостатков
необходимо выполнить разработку технологических процессов и конструктивных
параметров механизмов для формования изделий мелкой кожгалантереи с
использованием отверждающего покрытия.
Основными задачами разработки
явились:
·
выбор материалов и метода формования кожгалантерейных изделий
пространственной формы;
·
теоретическое и экспериментальное исследование процессов
формования;
·
разработка устройства для формования.
На сегодняшний момент
кожгалантерейная отрасль легкой промышленности находится в сложных условиях. С
одной стороны возрос спрос на отечественные кожгалантерейные изделия, с другой
стороны существует конкуренция с импортными изделиями. Это выдвигает требования
перестройки технологических процессов и модернизации существующего
оборудования. Положение осложняет сложное экономическое состояние предприятий,
отсутствие средств для проведения научно-исследовательских
опытно-конструкторских работ для разработки и изготовления оборудования и
технологической оснастки.
Одним из наиболее востребованных
ассортиментов является мелкая кожгалантерея и, в частности, изделия, имеющие
каркасную пространственную конфигурацию: футляры, чехлы и т.д. До настоящего
времени эти изделия изготавливались либо из дорогостоящей относительно толстой
натуральной кожи путем ее формования, либо из искусственной кожи со вставкой
вкладышей для обеспечения каркасности. Все это с одной стороны удорожает
изделие, с другой стороны ограничивает возможности моделирования и улучшения
качества. Поэтому в настоящей работе приводятся результаты исследования
процесса изготовления пространственных деталей кожгалантерейных изделий из
материалов с отверждающим слоем. В этой связи ниже рассмотрены вопросы:
·
анализ существующих технологий и оборудования для формования
изделий пространственной конфигурации;
·
разработка конструкции устройства для формования.
1.
Выбор материала и метода формования деталей мелкой кожгалантереи
кожгалантерейный текстильный
формование
Кожгалантерейная промышленность
обеспечивает население и народное хозяйство предметами культурно-бытового,
хозяйственного, спортивного, производственного назначения.
Часть этих изделий имеют
пространственную конфигурацию, которая образуется путем объемного формования
кожевенных и искусственных материалов.
Совершенствование существующей и
разработка новой технологии и механизмов для получения таких деталей может
осуществляться на основе научно-обоснованного выбора материала и метода его
переработки, а также анализа ассортимента. выпускаемых кожгалантерейных
изделий.
1.1 Анализ конструкций
формованных деталей мелкой кожгалантереи
Формованные детали находят
применение в изделиях жесткой и полужесткой конструкции. Их форма и
функциональное назначение весьма разнообразны. Такие детали могут служить в
качестве основных каркасных образований или выполнять роль вспомогательных
частей изделия.
В кожгалантерейных изделиях
формованные детали могут быть наружными и внутренними.
К наружным каркасным деталям
относятся стенки, ботаны, фальды, дно, клинчики чемоданов, портфелей типа «дипломат»,
сумок «пилот», различных футляров и т.п./ 1 /
Дополнительные наружные детали могут
выполнять роль карманов, элементов закрывания и ношения изделия, использоваться
для отделки и украшения.
Внутренние детали, например,
вкладыши и ученические ранцы, тоже могут быть каркасными, служить для
упрочнения изделия, придания ему формоустойчивости и жесткости.
А также, в современном
кожгалантерейном производстве выпускается большое количество мелких
кожгалантерейных изделий различного назначения: бумажники, портмоне, кошельки,
обложки, портсигары, кобуры, очечники и т.д.
Вся совокупность мелких
кожгалантерейных изделий разделена следующим образом.
Классификация кожгалантерейных
изделий по принадлежности к изделиям ЛП показана на рис.1, а также в таб. 1./ 2
/
Кроме того, мелкая кожгалантерея
может быть классифицирована по следующим признакам:
по методу изготовления - прошивные,
клеевые, в оплетку, формованные, методом сварки ТВЧ, литьевые, клепанные,
комбинированные;
по конструкции - жесткие,
полужесткие и мягкие; с прокладкой и без прокладки; с подкладкой и без
подкладки;
по способу изготовления -
выворотные, невыворотные;
по виду обработки наружных краев - в
загибку, в обрезку;
по способу закрывания - на рамочный
замок, застежку-молнию, замок-задвижку, замок-защелку, замок-кнопку и др.,
открытые.
Изделия изготавливают из натуральной
и искусственной кожи, полимерных пленок, тканей, комбинированные.
Требования, предъявляемые к
изделиям, разнообразны. Размеры бумажников, обложек для паспорта, удостоверений
должны соответствовать размерам вкладываемых документов. Кроме того,
предъявляют повышенные требования к качеству изготовления и внешнему виду
изделий: они должны отвечать функциональному назначению, быть удобными в
эксплуатации, иметь презентабельный внешний вид и т.д.
Классификация деталей кожгалантерейных изделий
Процесс изготовления изделий состоит
из обработки узлов и деталей и их последующей сборки. В процессе изготовления
данного ассортимента имеется много общего, хотя и имеются некоторые различия.
1.2 Выбор материала для отверждающего
слоя
Из вышесказанного следует, что
корпусные детали кожгалантерейных изделий изготавливают формованием из
дорогостоящей натуральной кожи толщиной более 3 мм или с применением различных
вставок из картона или пластика. Формование в обувной промышленности идет с
применением более тонких кож, но толщина этих кож не менее 1 мм. При формовании
более тонких кож, а также искусственных кож не удается достичь требуемой
формоустойчивости.
Идея заключается в том, чтобы
соединить кожу с подкладом с помощью склеивающего отверждающегося слоя, чтобы в
процессе технологии соединить слои и придать форму изделию, а так же получить
необходимые характеристики изделия.
Рассмотрим варианты склеивающих
отверждающих слоев:
клей на основе растворителей
(наиритовые);
клей с отверждающими компонентами
(полиуретановые, эпоксидные);
термопластичный прокладочный
материал.
Выделим и обозначим некоторые
параметры эксплуатации клеев:
·
работа с клеями на основе растворителей требует в технологическом
процессе время на отверждение:
а) первый этап начальное
поверхностное отверждение с активным выделением растворителя;
б) второй этап более длительное
время окончательного высыхания, то есть испарение растворителя из глубинных
слоев клеящей массы. На этом этапе происходит сильная деформация изделия
связанная с испарением растворителей;
·
в процессе отверждения клея необходима активная вентиляция из
рабочей зоны. Иначе концентрация растворителя не дает высыхания;
·
клеи на растворителях чаще всего вредны экологически для
операторов, ведущих технологический процесс;
·
при охлаждении изделия требуют дополнительных усадочных размеров
на изделии;
·
организовать аккуратную чистую технологию процесса промазывания
клеем, чтобы не измазать изделие практически не возможно и поэтому требует
операции очистки изделия в процессе или после изготовления.
Клей двухкомпонентный на основе
эпоксидных смол и отвердителей:
·
работа с такими клеями требует большое время на отверждение;
·
деформации при отверждении изделия достаточно ощутимы и требуют
усадочных размеров на изделии;
·
изделия получаются недопустимо жесткие и хрупкие;
·
все работы необходимо проводить в специально оборудованном
помещении и на специальном оборудовании;
·
высокая токсичность самих смол, а также их растворителей и
отвердителей небезопасна для здоровья, а так же требует активной вентиляции;
·
размягчители для эластичности отверждающей массы со временем или
упрочняют жесткость, или приводят к хрупкому разрушению.
3. Термопластичный прокладочный
материал:
·
относительно низкая температура плавления +400 - +420 К;
·
высокая адгезия в вязко-текучем состоянии;
·
высокая формоустойчивость после стеклования;
·
высокая прочность и эластичность при - 233 + 333 К
·
восстановление термопластичных свойств при повторном нагревании.
Анализ отмеченных параметров
позволил выявить технологические требования к формованию изделий с
термопластичным отверждающим слоем:
·
минимальное время формования, которое определяется в основном
конструкцией формующей оснастки и способами нагрева и охлаждения заготовки;
·
возможность использования простых способов формования методом
расплавления и отверждения;
·
способность лицевого покрытия к формованию в разогретом состоянии
(растяжение, вытяжка, усадка);
·
обеспечение жесткости и эластичности изделий за счет регулирования
толщины термоклея;
·
сохранение свойств и внешнего вида лицевого покрытия изделия:
а) лаковое покрытие кожи должно
сохранять свой цвет и блеск;
б) на коже должно сохраняться тиснение;
в) структура кожи должна не
нарушаться (не считая необходимого проникновения термоклея на внутренней
поверхности);
·
должна обеспечиваться экологическая чистота технологии;
·
простые требования по технике безопасности;
·
должна обеспечиваться безопасность при работе.
Физико-механические свойства
термопластичных прокладочных материалов приведены в таб. 2./ 3 /
Физико-механические свойства
термопластичных прокладочных материалов
Модуль упругости при растяжении, Мпа
Сравнительный экономический анализ
возможных к применению в качестве отверждающего слоя термопластичных полимерных
материалов показал, что наиболее дешевым и удовлетворяющим вышеперечисленным
требованиям является полиэтилен высокого давления.
1.3. Разработка технологии
формования деталей мелкой кожгалантереи
Технология изготовления изделий с
термопластичным отверждающим слоем представлена на рис. 2 и содержит следующие
операции:
1. Соединение термопласта с
кожей под давлением с одновременным расплавлением термопласта.
2. Раскрой деталей из кожи (с
нанесенным термопластом) и подкладочной ткани.
. Сшивание чехла из кожи и
внутреннего чехла из подкладочной ткани лицевой стороной вовнутрь.
. Выворотка заготовки верха.
. Собрать изделие. В кожаный
чехол вложить чехол из подкладочной ткани. Вывернуть край кожаного чехла
вовнутрь изделия и прострочить по краю.
. Установка заготовки
изделия на форму (пуансон).
. Установка обжимного
устройства (матрицу с пневмокамерой) на заготовку.
. Нагрев термоформы до
температуры плавления и выше для расплавления термоклея, выдержать время для
его абсорбции в материалы (теплопередачей).
. Охлаждение формы ниже
температуры отверждения (теплопередачей).
. Съем обжимного устройства.
Операции 1-5 выполняются в
соответствии с аппаратным обеспечением технологических процессов существующего
производства и в данной работе не рассматриваются. Далее рассмотрена только
технология формования на проектируемом устройстве.
В технологии изготовления для
нагрева формы можно использовать:
·
электрический нагрев (283 - 1283 К);
·
нагрев формы горячим паром (при температуре выше 383 К);
·
нагрев формы горячим воздухом (283 - 683 К);
Электрический нагрев имеет следующие
достоинства и недостатки:
Электрический нагрев предполагает
встройку теплоэлектрических нагревателей в форму.
Достоинства - это самый эффективный
нагрев, т.к. минимум переходных сред для тепловых процессов (максимальный коэффициент
теплопередачи);
Недостатки - резко усложняет форму,
следовательно в несколько раз увеличивает теплоемкость формы, что потребует
больше энергетических затрат на разогрев и охлаждение формы и во много раз
увеличивает время на переходные тепловые процессы.
Нагрев паром имеет следующие
достоинства и недостатки:
Достоинства - теплопередающая среда
«пар» более энергоемка, чем воздух, хотя и меньше, чем вода;
·
система нагрева по герметичным трубам усложнит установку;
·
возможно образование конденсата на более низкотемпературных
поверхностях и образование капель и потеков воды на установке.
Нагрев горячим воздухом имеет
следующие достоинства и недостатки
·
форма остается минимальной по теплоемкости, а, следовательно,
более производительной;
·
теплоемкость воздуха меньше теплоемкости формы, а, следовательно,
не влияет на временной тепловой процесс;
·
возможность регулировать температуру воздуха в достаточном для нас
диапазоне (283 - 683 К);
·
простой способ нагрева воздуха с помощью ТЭНов (теплоэлектрических
нагревателей);
·
простота включения, отключения подачи воздуха, переключения
воздуховодов на охлаждение;
·
не опасна утечка воздуха из системы нагрева-охлаждения;
·
окончательное охлаждение воздухом из помещения с температурой +293
+313 К;
Недостатки - низкая теплоемкость
термопередающей среды (может быть компенсирована повышением скорости потока
воздуха).
Таким образом, проанализировав
различные методы нагрева, выявили наиболее рациональный способ нагрева - нагрев
формы горячим воздухом.
В результате анализа возможных
методов нагрева формы горячим воздухом были разработаны следующие схемы
технологического процесса.
Установка для изготовления
единичного изделия представлена на рис 3а. При такой технологии формования
придется каждый раз попеременно нагревать и охлаждать форму до определенной
температуры, что требует больших затрат энергии и не обеспечивает достаточную
производительность. Отсюда вытекает идея нагрева формы теплопередачей от уже
нагретой формы. Схема процесса на технологической линии представлена на рис.
3б.
Технология изготовления может
незначительно меняться в зависимости от формы детали или изделия, удобства
сборки и технологичности.
Особенностью предполагаемой
технологии и конструкции устройства для формования изделий из материалов с
отверждающим покрытием является их энергетическая экономичность. Разработка
технологии и конструкции устройства для формования предшествовали расчеты
теплообменных процессов. Главным параметром обеспечивающим выбранный
технологический процесса является показатель кратности времени нагрева и
охлаждения обрабатываемой заготовки. От данного параметра зависит
продолжительность технологического цикла и позиционность машины.
Зададимся следующими обозначениями:
Т С - температура среды (Т С
= const);
Количество теплоты, необходимое для
нагрева данного тела, пропорционально его массе и изменению температуры.
где Q - количество
тепла, с - удельная теплоемкость тела, m - масса тела, ∆Т Т -
изменение температуры, происходящее в результате подвода к телу количества
тепла Q.
Схемы технологических
процессов нагрева формы
а - изготовление единичного изделия,
б - технологическая линия
Жидкие или газообразные тела,
вступающие в контакт с твердым телом, находящимся при другой температуре, либо
отдают ему тепло, либо получают тепло от него. Такое явление называют теплоотдачей
и описывают уравнением
где Q - количество
тепла, проходящее через границу сред, α - коэффициент
теплоотдачи, А - площадь поверхности, через которую происходит теплоотдача, Δt
- продолжительность процесса теплоотдачи, ΔТ
- разность температур поверхности твердого тела и окружающей среды.
Так как в обоих
уравнениях Q - это равное количество тепла, то мы можем приравнять правые части
уравнений (1.1) и (1.2),
Запишем это уравнение в
дифференциальном виде:
Решив это дифференциальное уравнение
получим:
постоянную k определяем
из граничных условий T T = 0 и t = 0
Примем ,
где τ - временнáя постоянная, характерная для каждого вещества, тогда
На рис. 4б представлен график этого
уравнения
Рассмотрим процесс теплопередачи от
одного тела к другому через воздушную среду.(Рис. 4в)
В нашем случае предположим, что
нагретый воздух хорошо перемешан и его температура одинакова во всех точках, а
вся разница температур лежит на границе сред. Начальное значение температуры
среды Т С равно среднему значению между Т 1 и Т 2 .
Так как есть две границы,
следовательно, есть два процесса:
Так как теплопотери не
учитываются, следует, что Q 1 = Q 2 ,
ΔT 1 = ΔT 2 и ΔT 1 +
ΔT 2 = ΔT
В процессе теплообмена первое тело
охлаждается, второе тело нагревается. Так как тела одинаковы, m 1 = m 2
и теплопотери отсутствуют, то насколько нагрелось второе тело, настолько остыло
первое.
Процесс изменения температур
описывается уравнением
Среднее значение между
текущими величинами Т Т1 и Т Т2 не меняется
а, следовательно, Т С
величина постоянная и энергетических затрат на изменение температуры среды не
требуется.
Так как Т С величина
постоянная, то для описания процесса теплообмена двух форм можно использовать
уравнение (1.12).
На рис.4г представлен совмещенный
график нагрева и охлаждения для обоих тел.
Тепловой процесс охлаждения первого
тела описывается уравнением
Тепловой процесс нагрева
второго тела описывается уравнением
Разница температуры
между телами описывается уравнением
То есть происходит
выравнивание температур.
Все тепловые процессы можно привести
к экспоненциальному процессу.
Основной характеристикой этого
процесса является временнáя постоянная τ. Ниже приведен ее расчет.
Примем массу формы с учетом массы
изделия m τ = 0.1 кг.
По справочнику / 4 / выбираем
коэффициент теплопередачи при системе «воздух - гладкая поверхность» α = 5,6 + 4v * , где v * - скорость. Примем скорость равной v * =
0,5 м/с. α = 7,6 Вт/Н 2 ·К. Площадь теплопередачи А = 0,02 м 2 .
Теплоемкость железа с = 0,46
кДж/кг·К.
При рассмотрении данного процесса
взяты следующие допущения:
·
не рассмотрены процессы внутри тел;
·
принято отсутствие теплопотерь из системы;
·
теплоемкость передающей среды из-за ее малой величины не
учитывалась;
·
температура внутри передающей среды равномерна.
Для того чтобы определить количество
позиций в процессе необходимо задаться температурой нагрева формы за время
одного цикла t и разницей температур форм после процесса теплоотдачи ΔT. На рис. 5 представлен
векторно-графический способ определения рационального количества позиций в
процессе.
На рис. 6 представлена диаграмма
теплового процесса формования одной позиции на технологической линии за все
время рабочего цикла.
Процесс нагрева и охлаждения показан
на рис. 7. При разных температурах нагрева энергопотери определяются только
последним циклом.
Энергопотери на последней ступени
охлаждения в технологической линии определяются уравнением:
Векторно-графический
метод выбора рационального количества позиций
Процесс нагрева и охлаждения
различных по длительности и максимальной температуре нагрева процессов
Энергопотери в единичном
производстве определяются уравнением:
Энергозатраты
определяются энергопотерями, потому что, сколько энергии выделяется при
охлаждении, столько энергии необходимо затратить на нагрев.
Сравним энергопотери Q Е.И.
и Q Т.Л.
Таким образом,
технологическая линия в 4 раза менее энергозатратна.
1.4 Тематический поиск по источникам
патентной и научно-технической информации
В ходе патентного исследования было
просмотрено и изучено около 20 документов и среди них: авторские свидетельства,
патенты, выложенные заявки и другая научно-техническая литература и
документация. Те из них, в которых заложены наиболее соответствующие
направлению исследования технологии и технические решения были отобраны для
дальнейшего более глубокого изучения и анализа.
Анализ показал, что в качестве
аналогов разработанному устройству можно выбрать следующие устройства.
Формование механическим обжимом на
пуансоне. (Авторское свидетельство СССР № 825460, кл. В 68 F 1/00, 30 апреля
1981г.)(Рис. 7)
Устройство содержит парные пуансоны
1 с упорами 2 и парные матрицы, каждая из которых содержит верхний прижим 3 и
боковые прижимы 4, соединенные шарнирами 5. Боковые прижимы 4 подпружинены
пружинами 6 и имеют рычаги 7.
Матрицы смонтированы на винтовом
прессе, содержащем винт 8 и электродвигатель 9.
Для сушки деталей в отверстиях
пуансонов установлены электронагревательные элементы.
Устройство работает следующим
образом.
В исходном положении матрицы
подняты. Увлажненную заготовку детали укладывают на нагретые пуансоны 1 между
боковыми ограничителями 2, при этом пуансоны слегка обтягивают заготовкой.
Включают электродвигатель 9
винтового пресса, матрицы опускаются. Боковые прижимы 4, касаясь рычагами 7
упоров 2, поворачиваются, огибая закругленные края пуансонов, вытягивая
заготовку и придавая ей форму. При этом выступы матрицы вдавливаются в
заготовку, образуя линии для шва на формуемой детали.
·
неравномерность обжатия на всех участках формы, отсюда плохое
качество изделия;
Пневмовакуумное
формование.(Авторское свидетельство СССР № 639204, кл. В 29 С 17/04, 15 марта
1982г.) (Рис.8)
Устройство имеет пневматическую
камеру 1 с перфорированной прижимной плитой 2, размещенный внутри камеры
электронагреватель 3, матрицу 4 с отверстиями 5 для вакуумирования или подачи
сжатого воздуха
Устройство снабжено линией 6 для
подачи сжатого воздуха в пневматическую камеру и линией 7 для подачи сжатого
воздуха в матрицу. Все линии сжатого воздуха снабжены пневморегулирующей
аппаратурой. В пневматической камере установлен кран 8 для сброса воздуха из
полости матрицы.
Для вакуумирования матрицы последняя
снабжена линией 9.
Устройство работает следующим
образом.
Термопластичный лист 10 укладывают
на матрицу 4 и пневматическую камеру 1 электротельфером опускают до полного
смыкания с матрицей, зажимая лист. Затем устройство плотно запирают. Далее
включают электронагреватели 3 и подают сжатый воздух по линии 6 в
пневматическую камеру 1, который нагревается электронагревателями. Термопластичный
лист 10 нагревается плитой 2.
После окончания нагрева листа
осуществляют формование изделия сжатым воздухом по линии 6 и вакуумированием по
матрицы 4 по линии 7. По окончании формования электронагреватели отключают и
подают для охлаждения изделия холодный воздух. После охлаждения изделия его
выталкивают из матрицы сжатым воздухом по линии 7.
Анализ работы позволил выявить
следующие недостатки:
·
происходит утончение материала и вследствие неравномерности
структуры материала - его разрыв
·
остаточная (релаксация) усадка материала, которая нарушает
линейные размеры изделия после формования
Пневмоформование.(Авторское
свидетельство СССР № 288401, кл. В 29 С 17/04, 8 сентября 1981г.) (Рис. 9)
Устройство имеет пуансон 1, на
котором осуществляют выкладку пакета слоев, прижимную матрицу 2 и пневмокамеру
3.
Устройство работает следующим
образом: на пуансон 1 осуществляют выкладку пакета слоев заготовки 4, которую
собирают предварительно на том оборудовании, которое имеется. Затем поджимают
матрицей 2 с образованием боковых клиновидных зазоров, в которых находятся
полости пневмокамеры 3. Для лучшего обжатия создают давление в пневмокамере 3 и
выдерживают время технологического процесса. По прошествии времени в матрицу 2
подводят хладагент. После этого матрицу отводят, а заготовку снимают с
пуансона.
Анализ работы позволил выявить
следующие недостатки:
·
неточное формообразование в связи с образованием клиновидных
зазоров между матрицей и пуансоном
Анализ существующих конструкций
устройств для формования полых деталей пространственной конфигурации из
композиционных материалов показал, что имеющиеся недостатки в конструкциях
данных устройств и их целевое назначение не позволяет применить перечисленные
устройства для изготовления деталей и узлов кожгалантерейных изделий. Поэтому
ниже рассматриваются вопросы разработки конструкции устройства для формования
кожгалантерейных изделий с термопластичным отверждающим слоем.
1) Наименование разработки:
устройство для формования кожгалантерейных изделий;
2) Область применения: легкая
промышленность;
) Основание разработки:
задание на дипломный проект;
) Цель и назначение
разработки: исследование возможности получения изделий мелкой кожгалантереи с
использование термопластичного отверждающего слоя и разработка устройства для
формования таких изделий;
·
производительность машины - 80 изделий в смену;
·
метод обработки - последовательно-параллельный метод с
использованием многопозиционного стола;
·
количество обслуживающего персонала - 1 чел.;
·
величина и скорость перемещения обрабатываемого изделия - поворот
на 45 о со скоростью 0.46 с -1 ;
·
мощность и тип привода - электродвигатель мощностью 10 Вт и
ременная передача для поворота стола; пневмоцилиндры для подъема и опускания
стола; пневматическая система для формования; электродвигатель мощностью 6 Вт
для вентиляционной системы;
толщина отверждающего слоя - до 2
мм;
толщина лицевой детали: натуральная
кожа - до 2.5 мм;
3. Исследование процесса формования
деталей из материалов с отверждающим покрытием
Для выбора технологического режима
формования изделий из полимерного материала с отверждающим слоем необходимо
проведение исследований процесса, которые позволили бы определить температурный
диапазон высокоэластического состояния полимера и температурно-временные режимы
формования. Исходными данными для этих расчетов являются сведения о
реологических параметрах материала (температура плавления,
температуропроводность).
.1 Теоретическое исследование
температурно-временных зависимостей термоформования
Формование полимерных деталей
кожгалантерейных изделий является многофакторным процессом, в котором
совокупность свойств изготавливаемого изделия, а именно: форма, размеры,
качество поверхности, физико-механические свойства; и производительность труда
на операции связаны с условиями взаимодействия полимерной массы с оснасткой и
установленными режимами сварки / 5 / В формализованном виде такую зависимость
можно представить в следующем виде:
где Y- функция, характеризующая
качество получаемой детали; Т н - температура нагревателя; t н
- продолжительность нагрева; х - толщина прогреваемого слоя полимера.
Среди факторов, наиболее значимо
влияющих на процесс формования, является температура нагревателя. Размягчение
материала в зоне контакта будет происходить лишь тогда, когда температура в
зоне разогрева достигнет значений, превышающих нижнюю границу т
Похожие работы на - Технология изготовления пространственных кожгалантерейных изделий Дипломная (ВКР). Другое.
Курсовая работа по теме Оцифровка и реставрация аудиоматериала
Дипломная работа по теме Финансовая стратегия предприятия
К Чему Может Привести Внутренний Разлад Сочинение
Контрольная работа: Множественность в преступлении
Реферат: Компьютерная зависимость 2
Курсовая работа: Проектирование зерносклада
Сочинение Больше Дела Меньше Слов
Доброму Добрая Память Сочинение
Итоги Великой Отечественной Войны Реферат
Реферат: Екологічне страхування
Курсовая Работа На Тему Анализ Ошибок Заочной Математической Школы
Сша Моими Глазами Сочинение
Контрольная работа по теме Гигиена продуктов питания
Контрольная Работа 2 Законы Ньютона
Реферат: Print Media Essay Research Paper Phil Smith
Реферат Разработки Сайтов
Реферат: Частотные и переходные характеристики систем авторегулирования
Реферат: Психология труда и человеческого достоинства
Военные Суды Эссе
Обучение Пожарных Требованиям Охраны Труда Реферат
Дипломная работа: Механизация ручного труда технологического процесса формования заготовок кондитерских изделий
Реферат: Taming Of The Shrew 2