Технологический процесс механической обработки детали 'муфта подвижная'. Дипломная (ВКР). Другое.
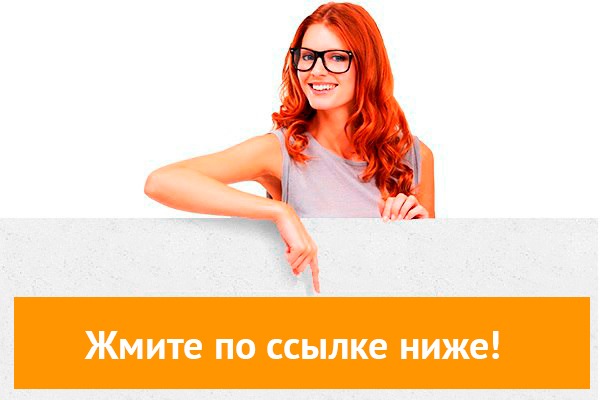
⚡ 👉🏻👉🏻👉🏻 ИНФОРМАЦИЯ ДОСТУПНА ЗДЕСЬ ЖМИТЕ 👈🏻👈🏻👈🏻
Вы можете узнать стоимость помощи в написании студенческой работы.
Помощь в написании работы, которую точно примут!
Похожие работы на - Технологический процесс механической обработки детали 'муфта подвижная'
Скачать Скачать документ
Информация о работе Информация о работе
Скачать Скачать документ
Информация о работе Информация о работе
Скачать Скачать документ
Информация о работе Информация о работе
Скачать Скачать документ
Информация о работе Информация о работе
Скачать Скачать документ
Информация о работе Информация о работе
Скачать Скачать документ
Информация о работе Информация о работе
Скачать Скачать документ
Информация о работе Информация о работе
Нужна качественная работа без плагиата?
Не нашел материал для своей работы?
Поможем написать качественную работу Без плагиата!
Одним из путей повышения производительности труда и снижения
себестоимости изготовления изделий является совершенствование действующих
технологических процессов и их замена более прогрессивными.
Эта работа проводится на основе комплексного анализа, как конструкции
изделий (деталей), так и технологии их изготовления, начиная с выбора более
прогрессивных видов заготовки.
Учитывая то, что предприятия Республики Беларусь на сегодняшний день не
имеют достаточных средств на приобретение нового технологического оборудования,
основное внимание уделяется совершенствованию технологических процессов на
основе имеющегося оборудования, применению более совершенных приспособлений и
инструментов. Серьёзное внимание должно уделяться повышению качества выпускаемых
изделий, повышению их надёжности и долговечности.
В курсовом проекте разрабатываются: технологический процесс механической
обработки заданной детали, специальная оснастка, а также ряд непосредственно
связанных с ним вопросов. Курсовой проект делится на графическую часть,
пояснительную записку и техдокументацию.
Муфта подвижная предназначена для постоянного соединения валов,
допускающая их относительное смещение, а также для соединения валов с
пересекающимися осями.
Деталь муфта подвижная имеет массу 0,13 кг и габаритные размеры 89х52 мм.
Программа выпуска 5000 штук.
Данная деталь имеет шлицевые соединения Ø60Н9 и Ø 90Н9. Остальные поверхности вала
выполняют по 14 квалитету точности.
Для повышения твердости рабочей поверхности зубьев цементированию на
глубину 1,0…1,4 мм до 56…64 HRC.
Для обеспечения необходимых рабочих параметров в качестве материала для
муфты подвижной выбрана Сталь 12ХН3А ГОСТ 4543-71.
Таблица 1- Механические свойства стали 12ХН3А
Химический состав стали 12ХН3А приведем в таблице 2.
Таблица 2- Химический состав стали 12ХН3А
2. Анализ технологичности конструкции
детали
Анализ технологичности является одним из важных этапов в разработке
технологического процесса, от которого зависят его основные
технико-экономические показатели: металлоемкость, трудоемкость, себестоимость.
Выполним качественную оценку технологичности конструкции детали.
Формы и размеры заготовки максимально приближены к форме и размерам
детали, что повышает коэффициент использования материала. На токарных операциях
деталь может быть обработана проходными упорными резцами. Жесткость вала
обеспечивает достижение необходимой точности при обработке.
Таким образом, можно сказать, что с качественной стороны деталь
технологична.
Выполним количественную оценку технологичности конструкции изделия.
Средний квалитет точности обработки детали рассчитываем по формуле [3]
где
- номер квалитета точности i-ой
поверхности;
-
количество размеров деталей, обрабатываемых по -му
квалитету.
Для
расчета составляем исходную таблицу точности.
Таблица
3 - Точность поверхностей вала-шестерни
Коэффициент
точности обработки рассчитываем по формуле [3]
Коэффициент
точности обработки близок к нормативному (ГОСТ 14.201-83), следовательно по
точности деталь технологична.
Средняя
шероховатость поверхностей рассчитываем по формуле [3]
где
- значение шероховатости i-ой
поверхности;
-количество
поверхностей, имеющих шероховатость .
Для
расчета составляем исходную таблицу 4 шероховатости детали.
Таблица
4 - Шероховатость поверхностей детали
Коэффициент
шероховатости поверхностей меньше нормативного (ГОСТ 14.201-83) ,а значит
деталь по шероховатости поверхностей нетехнологична.
Определим коэффициент использования материала:
Так
как коэффициент использования материала меньше нормативного, то с
количественной оценки конструкция вала нетехнологична.
Проанализировав технологичность детали с качественной и количественной
стороны можно сделать вывод о том, что в общем деталь достаточно технологична,
чтобы ее получение не требовало применения сложных и дорогостоящих методов
обработки.
В связи с тем, что в задании отсутствует базовый техпроцесс изготовления
детали, тип производства предварительно определяем по таблице [1]. Из таблицы
видно, что производство серийное.
В серийном производстве детали изготавливаются партиями, размер партии
рассчитывается по формуле [1]:
Ф
- количество рабочих дней в году ( );
По
размеру партии детали устанавливаем, что производство будет среднесерийным.
Для
получения данной заготовки в условиях среднесерийного производства можно применить
прокат.
Стоимость
заготовки из проката рассчитывается по формуле:
где
M - затраты на материал заготовки, руб.;
-
технологическая себестоимость правки, калибровки, разрезки, р.
Расчеты
затрат на материалы и технологической себестоимости выполнят по формулам:
S - цена 1 кг
материала заготовки, (S = 1085 руб.);
S отх - цена 1 кг отходов, (S отх = 940 руб.).
где
C п.з -
приведенные затраты на рабочим месте, руб./ч;
t шт.(шт-к) - штучное или штучно-калькуляционное время выполнения
заготовительной операции, мин.
Штучное
или штучно-калькуляционное время рассчитывается по формуле:
где
L рез -
длина резания при разрезании проката на щтучные заготовки (может быть принята
равной диаметру проката: L рез = D),
мм;
y - величина
врезания и пробега (при разрезании дисковой пилой y= 6-8 мм);
S м - минутная подача при разрезании (S м = 50-80 мм/мин);
φ - коэффициент, показывающий долю вспомогательного времени в штучном (φ = 1,84 - для мелко- и среднесерийного производства).
5.
Принятый маршрутный технологический процесс
В
принятом технологическом процессе на всех операциях, требующих большой точности
изготовления, базовыми поверхностями являются центровые отверстия. При этом
технологические и конструкторские базы совпадают. Базы изменены лишь на тех
операциях, где нет возможности использовать центровые отверстия, и вводятся
дополнительные базовые поверхности там, где это необходимо
(радиально-сверлильная).
Таблица 5 - Принятый технологический процесс
Номер операции, ее
наименование (по назначению станка), содержание
Операционный эскиз
обработки, схематичное обозначение опор, зажимных устройств и обрабатываемых
поверхностей
Технологическое оснащение
операции (станочное приспособление, режущий инструмент, средства контроля)
Операция 000
Заготовительная (прокат)
Операция 005 Токарная с ЧПУ
Черновое и чистовое обтачивание
1)Точить
поверхности 1 начерно. 2)Расточить поверхность 2 начерно 3)Точить поверхность
1 начисто. 4)Расточить поверхность 2 начисто.
Операция 015 Токарная с ЧПУ
Черновое и чистовое обтачивание
1)Точить поверхности 1,4 начерно. 2)Точить
поверхности 1,4 начисто и фаску 3. 3)Расточить поверхность 5 начерно.
4)Расточить поверхность 5. 5)Расточить канавку 2 начерно. 6)Расточить канавку
2 начисто.
Токарный станок с ЧПУ
16К20Ф3. Резцы проходной, расточной канавочный.
Операция 020
Шлицефрезер-ная. Фрезерование шлицев.
Шлицефрезерный станок
5350А, червячная модульная фреза
Операция 025 Долбежная.
Долбление шлицев.
Вертикально-протяжной
станок 7Б74. Инструмент- протяжка
Операция 030
Зубозакругляю-щая. Закругляем зубья.
Зубозакругляющий станок
5Е580, пальцевая фреза
Цементация (закалка +
низкий отпуск)
Операция 040
Шлицешлифовальная. Шлифование шлицев.
Шлицешлифовальный станок.
Круг шлифованльный
Операция 045
Шлицешлифовальная. Шлифование шлицев.
Шлицешлифовальный станок.
Круг шлифованльный
Операция 050 Моечная.
Промывка детали
Расчет
необходимого количества операций проведем для поверхности .
Допуск
заготовки согласно ГОСТ 7505-89 составляет 2,5 мм, т.е.
Необходимую величину уточнения определим по формуле [15]
С
другой стороны, уточнение определяется как произведение уточнений, полученных
при обработке поверхности на всех операциях(переходах) принятого техпроцесса:
где
- величина уточнения, полученного на i-ой
операции (переходе);
n - количество
принятых в техпроцессе операций (переходов).
Для
обработки данной поверхности в маршрутном технологическом процессе
предусмотрены следующие операции:
Промежуточные
значения рассчитываются по формулам[15]
где
- допуски размеров, полученные при обработке детали
на первой, второй и т.д. операциях.
Определяем
общее уточнение для принятого маршрута обработки:
Полученное
значение показывает, что при принятом маршруте точность
обработки поверхности обеспечивается, т.к. , т. е.
6.
Расчёт припусков на обработку поверхности
Заготовка
вала-шестерни получена штамповкой на горячековочной машине. Маршрут обработки
включает следующие операции (переходы):
На
всех операциях обработка рассчитываемой поверхности ведется в центрах, из чего
следует, что погрешность установки детали в радиальном направлении равна нулю,
т.е. e=0.
Погрешность
заготовки определяем по формуле [3]
где
- погрешность заготовки по смещению, мм;
-
погрешность заготовки по короблению, мм;
где
- удельная кривизна заготовки, мкм/мм;
l - расстояние
от торца до середины заготовки, мм.
Погрешность
зацентровки определяем по формуле [3]
где
- допуск
на размер поковки, 3,0 мм.
Величина
остаточных пространственных отклонений [3]
Выписываем
параметры шероховатости и глубины дефектного слоя Т для всех операций:
Расчёт
минимальных значений припусков производим по формуле [3], предварительно
заполнив расчётную таблицу 3.7.
где
- высота неровностей, полученных на предыдущей
операции;
- глубина
дефектного слоя, полученного на предыдущей операции;
-
пространственное отклонение, полученное на предыдущей операции.
Определяем
расчетный размер путем последовательного прибавления расчетного
минимального припуска каждого технологического перехода, начиная с минимального
размера:
В
графу записываем расчётные размеры. Графу "допуск"
заполняем в соответствии с достигнутой точностью при обработке деталей на
данной операции. Наибольшие предельные размеры определяем прибавлением допуска к наименьшему
предельному размеру:
Предельные
значения припусков определяем как разность наибольших предельных размеров
и - как разность наименьших предельных размеров
предыдущего и выполняемого переходов:
Общие
припуски Z 0 max и Z 0 min рассчитываем, суммируя их промежуточные значения и записывая их внизу
соответствующих граф
Величину
номинального припуска определяем с учётом несимметричности расположения поля
допуска заготовки.
где
- нижнее отклонение заготовки =1 мм;
- нижнее
отклонение размера детали Н з =0,016 мм.
Производим
проверку правильности расчётов по формуле [3]
Проверка показывает, что расчёты припусков выполнены правильно.
Таблица
6 - Расчёт припусков на обработку поверхности
Строим
схему графического расположения припусков и допусков поверхности (рисунок 6.1).
Рисунок
6.1 - схема графического расположения припусков и допусков на обработку
вала-шестерни
На
остальные поверхности заготовки припуски назначаем по ГОСТ 7505-89 и результаты
сводим в таблицу 7.
Таблица
7 - Припуски и допуски на обрабатываемые поверхности вала-шестерни
муфта подвижный технологический резание
Расчёт режимов резания аналитическим методом
Расчет режимов резания для операции 005 (фрезерно-центровальная). На
данной операции фрезеруются торцы и сверлятся центровые отверстия. Обработка
ведется на фрезерно-центровальном полуавтомате модели МР-75. Фрезерование
производится торцовыми фрезами с механическим креплением круглых пластин из
твердого сплава Æ63 мм (ГОСТ22085 - 76), материал режущей части Т15К6. Отверстия сверлятся
сверлом Æ6,3 мм из быстрорежущей стали Р6М5.
Назначаем подачу при фрезеровании S z =0,15 мм/зуб.
Скорость резания при фрезеровании определяем по формуле
где
С V - коэффициент, зависящий от материала заготовки [3
таб. 39, стр. 286];
D - диаметр
фрезы [3 таб. 96, стр. 187], мм;
T - период
стойкости инструмента [3 таб. 40, стр. 290];
S z -
подача на зуб, мм/зуб [3 таб. 34, стр. 283];
Z - число зубьев
фрезы [3 таб. 96, стр. 187];
К v
- общий поправочный коэффициент.
x, у, u, q, p, m -
показатели степени [3 таб. 39, стр. 286].
Согласно
формуле , скорость резания при фрезеровании будет равна
Производим
расчет числа оборотов шпинделя, соответствующего
где
V - скорость резания при фрезеровании;
Согласно
формуле частота вращения шпинделя будет равна
Корректируем
полученное значение по паспорту станка, принимаем n=750 мин -1 .
Уточняем
скорость резания по принятым оборотам шпинделя
Рассчитываем
минутную подачу по принятым оборотам шпинделя по формуле
Корректируем
минутную подачу по паспортным данным станка, принимаем S M =400
мм/мин.
Назначаем
подачу при центровании S=0,04 мм/об.
Определяем
скорость резания при центровании по формуле
T - период
стойкости инструмента [3 таб. 30, стр. 279]
у,
q, m - показатели степени [3 таб. 29, стр. 279]
Согласно
формуле скорость резания при центровании будет равна
Согласно
формуле частота вращения шпинделя будет равна
Корректируем
полученное значение по паспорту станка, принимаем n=1125 мин -1 .
По
формуле уточняем скорость резания по принятым оборотам шпинделя
Определяем
мощность резания, затрачиваемую на данной операции по формуле [3 стр.290]
где
Р z - главная составляющая силы резания;
Главную
составляющую силу резания - окружную силу - определяем по формуле [3 стр.282]
где
С р - коэффициент, зависящий от материала заготовки [3 таб. 41, стр.
291];
К мр
- общий поправочный коэффициент;
x, у, u, q, w -
показатели степени [3 таб. 41, стр. 291].
Согласно
формуле окружная сила будет равна
По
формуле определяем мощность резания
Сравниваем
мощность резания с мощностью главного электродвигателя, для чего должно
выполняться условие
Так
как 14,5<14,95, то условие выполняется.
Определяем
составляющую, по которой рассчитывают оправку на изгиб, по формуле [3 стр.
290];
где
Р y - радиальная сила резания [3 таб. 42, стр. 293].
Согласно
формуле определяем составляющую, по которой рассчитывают оправку на изгиб
Операция 10 - токарная с ЧПУ. Чистовое точение Æ60, Æ70. Станок модели 16К20Т1. Резец
проходной с пластиной из твердого сплава Т15К6.
Скорость
резания рассчитываем по формуле [12]
Поправочный
коэффициент рассчитываем по формуле[12]
где
- коэффициент, учитывающий влияние материала
заготовки;
-
коэффициент, учитывающий состояние поверхности;
-
коэффициент, учитывающий материал заготовки.
Частоту
вращения шпинделя при обработке рассчитываем по формуле
Принимаем
по паспорту станка =800мин -1
Силу
резания рассчитываем по формуле [12]
Поправочный
коэффициент рассчитываем по формуле[12]
Мощность
резания рассчитываем по формуле [12]
Мощность
двигателя главного привода станка =10 кВт,
К.П.Д. привода станка =0,85. Тогда
Таким образом, привод станка обеспечивает обработку при заданных режимах.
Расчёт режимов резания по нормативам
Операция 20 - вертикально-фрезерная. Фрезерование шпоночного паза 14N9 длиной 60мм . Станок модели 6Р13Ф3.
Инструмент фреза шпоночная из быстрорежущей стали Р6М5.
Длину рабочего хода рассчитываем по формуле[10]
длина
подвода, врезания и перебега, мм.
Подачу
на зуб фрезы назначаем по таблице стр.86[10]
Определяем
стойкость инструмента по нормативам Т в
минутах резания.
Где
Т -стойкость инструмента наладки.
К -коэффициент, учитывающий количество инструментов в
наладке.
-
коэффициент времени резания инструмента
Скорость
резания назначаем по таблице стр.98 24м/мин
Частоту вращения инструмента рассчитываем по формуле[10]
По
паспорту станка принимаем частоту вращения n=545 мин -1
Рассчитываем минутную подачу по принятому значению числа оборотов
шпинделя.
n-частота
вращения шпинделя по паспорту станка, мин .
По
паспорту станка принимаем s =30мм/мин.
Мощность
резания находим по формуле[10].
Где
Е-величина, определяемая из таблицы стр.102 [10].
К -коэффициент, зависящий от обрабатываемого материала.
Мощность
двигателя главного привода станка =3 кВт,
К.П.Д. привода станка =0,85. Тогда
Операция
025 Шлицефрезерная. Фрезерование шлицев на валу-шестерне на станке 5350А.
Режущий инструмент: фреза червячная модульная Ø90; Р6М5.
у
- длина подвода, врезания и перебега, мм [7, с. 304].
где
- коэффициент, зависящий от обрабатываемого материала
[7, с. 149, карта З-2];
-
табличное значение подачи, мм/об [7, с. 148, карта З-2].
Принимаем
по паспорту станка Sо= 2 мм/об
Определяем
нормативную скорость резания
где
v табл - табличная скорость резания, [7, с. 148, карта З-2];-
коэффициент, учитывающий материал обработки, [7, с. 149, карта З-2];
К2
- коэффициент, учитывающий стойкость резца, [7, с. 149, карта З-2].
Определяем
рекомендуемую частоту вращения шпинделя:
где
D - диаметр обрабатываемой детали, мм.
Пересчитываем
скорость резания по принятой частоте вращения:
Определим
основное машинное время обработки
Таким образом, привод станка обеспечивает обработку при заданных режимах.
Аналогично рассчитываем режимы резания на остальные операции и результаты
сводим в таблицу 8.
Таблица 8 - Сводная таблица режимов резания
Фрезерно-центровальная
1.Фрезерование торцов 2. Сверление центровочных отверстий Æ6,3.
Токарная с ЧПУ 1.Черновое
точение поверхностей Æ60 Æ70, 2. Чистовое точение
поверхности Æ60, 3.Точение канавки Æ59,5
Токарная с ЧПУ 1.Черновое
точение поверхностей Æ50 Æ55 Æ70 Æ80 Æ108 2. Чистовое точение поверхности Æ50 Æ55 Æ70 Æ108 3.Точение канавки Æ54,5 4.Точение канавки Æ69,5
0,5 0,5 0,5 0,5 0,5 0,2 0,2
0,2 0,2 0,2 0,2
0,5 0,5 0,5 0,5 0,5 0,2 0,2
0,2 0,2 0,2 0,2
98,3 96,5 91,9 89,5 84,3
159,7 156,7 149,3 136,9 112,5 114,2
78,5 86,35 87,9 79,1 67,8
157 138,2 138,5 136 108 109
636,6 558,5 418 356 248
1017 907 679,2 403,7 657 523,1
500 500 400 315 200 1000
800 630 400 630 500
250 250 200 157,5 100 200
160 126 80 126 100
0,31 0,13 0,6 0,28 0,44
0,39 0,21 0,96 0,55 0,02 0,02
Вертикально-фрезерная 1.
Фрезеровать шпоночный паз
Зубошевинговальная
1.Шевинговать зубья
Вертикально-сверлильная 1.
Сверлить отверстие Æ9,4; 2. Зенковать фаску; 3. Нарезать резьбу
Торцекруглошлифовальная 1.
Шлифовать поверхность Æ60 и торец
Торцекруглошлифовальная 1.
Шлифовать поверхность Æ50 и торец
Расчёт нормы времени на операцию 10 - токарная с ЧПУ
Тип производства изготовления вала-шестерни соответствует среднесерийному
производству, в котором в качестве нормы времени рассчитывается
штучно-калькуляционное время [15]
время на
обслуживание рабочего места;
-
подготовительно-заключительное время;
Основное
время рассчитываем по формуле [15]
величина
врезания и перебега, 4мм [11]
Основное
время на черновое точение Æ60
Основное
время на черновое точение Æ70
Основное
время на чистовое точение Æ60
Основное
время на чистовое точение Æ70
Основное
время всей операции рассчитаем как сумму основных времен переходов.
Вспомогательное
время рассчитываем по формуле [15]
где
время на установку и снятие детали, 0,15мин;
время на
закрепление и открепление детали; 0,19мин
время на
приемы управления станком;
Время
на приемы управления детали состоит из:
1) времени включения станка кнопкой - 0,01мин;
2) времени подвода или отвода инструмента к детали при обработке -
0,016мин
Время
на измерение детали состоит из времени измерения скобой односторонней
диаметров: Æ60, Æ70, Æ59,5.
Для
среднесерийного производства вспомогательное время рассчитываем по формуле
где
коэффициент, зависящий от типа производства, 1,85.
Оперативное
время рассчитывается по формуле[15]
Время
на обслуживание и отдых в серийном производстве по отдельности не определяются.
Оно задается в процентах от оперативного времени
Подготовительно
заключительное время
Штучно-калькуляционное
время составляет
Расчёт нормы времени на операцию 20 -вертикально-фрезерную
Тип производства изготовления вала-шестерни соответствует среднесерийному
производству, в котором в качестве нормы времени рассчитывается
штучно-калькуляционное время [15]
время на
обслуживание рабочего места;
- время
на отдых; -
подготовительно-заключительное время;
величина
врезания и перебега, 6мм [11]
Вспомогательное
время рассчитываем по формуле [15]
где
время на установку и снятие детали, 0,121мин;
время на
закрепление и открепление детали, 0,024мин;
время на
приемы управления станком;
время на
измерение детали,t =0,16мин.
Время
на приемы управления детали состоит из:
1) времени включения станка кнопкой - 0,01мин;
2) времени подвода или отвода инструмента к детали при обработке -
0,035мин;
Для
среднесерийного производства вспомогательное время рассчитываем по формуле
где
коэффициент, зависящий от типа производства, 1,85.
Оперативное
время рассчитывается по формуле[15]
Время
на обслуживание составляет 1,4% от оперативного времени:
Подготовительно
заключительное время =14 мин;
Штучно-калькуляционное время составляет
Расчеты
норм времени на остальные операции выполняется аналогично и сводятся в таблицу
9.
Таблица
9-Сводная таблица норм времени.
Расчет точности выполняем на токарную операции 10, где выполняется
чистовое точение поверхностей Æ70 и Æ60. Допуск на обрабатываемые поверхности Т=120 мкм.
Суммарную погрешность обработки рассчитываем по формуле
Где
- погрешность, обусловленная износом режущего
инструмента;
- поле
рассеяния погрешности обработки, обусловленных технологическими факторами
случайного характера, =35 мкм;
Определим
погрешность, обусловленная износом режущего инструмента по формуле
где
- относительный износ инструмента, =9мкм/км;
где
- подача на оборот шпинделя, =0,18 мм/об;
Определим
погрешность настройки станка по
формуле
где
- смещение центра группирования размеров пробных
деталей относительно по рассеяния размеров;
- погрешность
регулирования положения режущего инструмента на станке, =20 мкм;
-
погрешность измерения пробных деталей;
где
m - количество пробных деталей, m=5;
При
использовании микрометра первого класса точности =9 мкм
Требуемая
точность обработки обеих поверхностей Æ70 и Æ60 обеспечивается, так как
Антонюк В.Е. Конструктору станочных приспособлений: Справ.
пособие.- Мн.: Беларусь, 1991.
Афонькин М.Г. Производство заготовок в машиностроении / М.Г.
Афонькин, М.В. Магницкая.- Л: Машиностроение, 1987.
Горбацевич А.Ф. Курсовое проектирование по технологии
машиностроения / А.Ф. Горбацевич, В.А. Шкред.- Мн.: Выш. шк., 1983.
Горошкин А.К. Приспособления для металлорежущих станков:
Справ. - М: Машиностроение, 1979.
Дипломное проектирование по технологии машиностроения / Под
общ. ред. В.В. Бабука. - Мн.: Выш. шк., 1979.
Общемашиностроительные нормативы режимов резания для
технического нормирования работ на металлорежущих станках. Зуборезные,
горизонтально-расточные станки. - М.: Машиностроение, 1974.
Общемашиностроительные нормативы режимов резания для
технического нормирования работ на шлифовальных и доводочных станках. - М.:
Машиностроение, 1974.
Общемашиностроительные нормативы времени вспомогательного на
обслуживание рабочего места и подготовительно-заключительного для технического
нормирования. Серийное производство. - М.: Машиностроение, 1974.
Прогрессивные режущие инструменты и режимы резания металлов:
Справ. / В.И. Баранчиков, А.В. Жаринов, Н.Д. Юдина и др.; Под общ. ред. В.И.
Баранчикова. - М.: Машиностроение, 1990.-400с.: ил.
Режимы резания металлов: Справ. / Под ред. Ю.В. Барановского
- М.: Машиностроение, 1972.
Справочник технолога-машиностроителя. Т.1 / Под ред. А.Г.
Косиловой, Р.К. Мещерякова.- М.: Машиностроение, 1985.
12 Справочник технолога-машиностроителя. Т.2 / Под ред. А.Г.
Косиловой, Р.К. Мещерякова.- М.: Машиностроение, 1985.
Станочные приспособления: Справ. Т.1 / Под ред. Б.Н.
Вардашкина и А.А. Шатилова. - М.: Машиностроение, 1984.
Технология автоматизированного производства. Т.2 / Под ред.
А.А. Жолобова. - Мн.: Дизайн ПРО, 1997.
Курсовое проектирование по технологии станкостроения.
Методические указания для студентов специальности Т.03.01.00 - Могилев: МГТУ,
2003. - 34с.
Похожие работы на - Технологический процесс механической обработки детали 'муфта подвижная' Дипломная (ВКР). Другое.
Курсовая работа по теме Розничный товарооборот - один из важнейших показателей в торговле
РАСЧЕТ ЭЛЕКТРОДВИГАТЕЛЯ ПОСТОЯННОГО ТОКА МАЛОЙ МОЩНОСТИ
Курсовая Работа На Тему Электрические Аппараты
Реферат: Buying A New Car Essay Research Paper
Методы Управление Риском Реферат
Дипломная работа: Особенности социального интеллекта младших школьников, воспитывающихся в условиях учреждения интернатного типа
Курсовая работа по теме Программная реализация разложения временного процесса в тригонометрический ряд
Реферат: Электрогенераторы Фарадея
Отчет По Практике Зао Корпорация Тюменьстрой
Философия Наука Или Искусство Эссе
Курсовая работа по теме Психолого-педагогические основы развития творческого мышления младших школьников
Курсовая работа по теме Проектирование машин и аппаратов перерабатывающей промышленности
Контрольная Работа На Тему Курорти Крима
Реферат: Предприятие организация как объект экономического анализа
Контрольная Работа Для Студентов Специальности
Курсовая работа по теме Концепция и профиль объектов общественного питания
Доклад: Жуки
Контрольная работа по теме Методы антикризисного управления на предприятии
Цитаты Для Эссе По Экономике
Сложное предложение
Доклад: Пролеткульт: страницы истории
Курсовая работа: Состояние, развитие, пути повышения эффективности молочного скотоводства в СПК имени К
Контрольная работа: Правове регулювання захисту прав споживачів в Україні