Технологический процесс изготовления детали 'Корпус'. Курсовая работа (т). Другое.
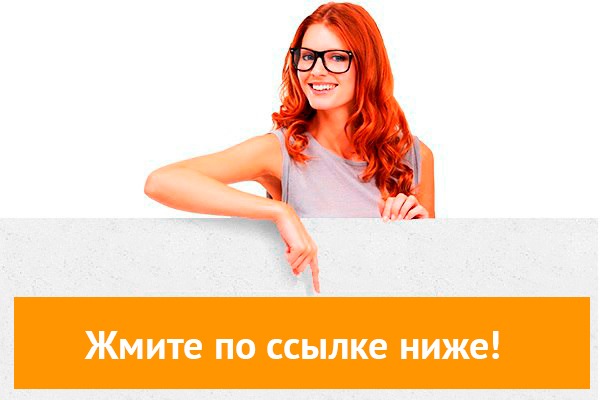
⚡ 👉🏻👉🏻👉🏻 ИНФОРМАЦИЯ ДОСТУПНА ЗДЕСЬ ЖМИТЕ 👈🏻👈🏻👈🏻
Вы можете узнать стоимость помощи в написании студенческой работы.
Помощь в написании работы, которую точно примут!
Похожие работы на - Технологический процесс изготовления детали 'Корпус'
Скачать Скачать документ
Информация о работе Информация о работе
Скачать Скачать документ
Информация о работе Информация о работе
Скачать Скачать документ
Информация о работе Информация о работе
Скачать Скачать документ
Информация о работе Информация о работе
Скачать Скачать документ
Информация о работе Информация о работе
Скачать Скачать документ
Информация о работе Информация о работе
Скачать Скачать документ
Информация о работе Информация о работе
Нужна качественная работа без плагиата?
Не нашел материал для своей работы?
Поможем написать качественную работу Без плагиата!
Деталь - корпус. Предназначен для промежуточного упора детали
вращения, например вала, посредством подшипника. Имеет сквозное отверстие для
установки подшипника. С торцов расположены резьбовые отверстия, по 6 с каждой
стороны, для крепления крышек подшипника, возможно с сальниками для удержания
смазки и предотвращения попадания посторонних веществ и материалов в деталь. На
основании для закрепления имеется продольный паз, в который упирается
соответствующая направляющая станины. Установка на такую направляющую позволяет
избавится от поперечных сил, действующих на крепежный элемент, и упрощает
монтаж. Имеются отверстия под установку крепежного элемента (винт, болт,
шпилька).
Данная деталь может испытывать различные нагрузки, и
статические, и динамические, и циклические, однако эти нагрузки имеют косвенный
характер, и относительно невелики. Поэтому серый чугун СЧ20 вполне
удовлетворяет требованиям к детали. Модуль упругости чугуна СЧ20 Е=80000МПа,
модуль сдвига G=42000МПа, плотность 7200 кг\куб. м, НВ170, и не применяется для
сварных конструкций.
. Выбор способа получения заготовки
Заготовки в большинстве случаев для штучного и мелкосерийного
производства, наиболее применимого в производстве оборудования для пищевой
промышленности, получают литьём, ковкой или штамповкой.
Учитывая необходимое качество детали, требования к
геометрическим размерам, шероховатости поверхностей, экономичность
производства, специфику материала детали, его хорошие литейные свойства,
жидкотекучесть и малую линейную усадку выбираем способ получения заготовки -
литьё в песчано-глинистую форму.
Конструкция отливок, изготовляемых в песчаных формах, должна
обеспечивать минимальное число поверхностей разъема модели или формы исключать
отъемные части формы и по возможности стержни. Необходимо стремиться к
использованию одной плоскости разъема. Возможность ее создания определяют по
правилу световых теней, согласно которому теневые участки при воображаемом
освещении детали параллельными лучами в направлении, перпендикулярном к плоскости
разъема формы или стержневого ящика, должны отсутствовать.
Отливку считают технологичной, если ее конструкция
соответствует общим принципам обеспечения качества заготовок при литье и
сложившимся конкретным производственным условиям. Высокое качество отливки
обеспечивают: использование литейного сплава с высокой жидкотекучестью и
оптимальная конфигурация отливки, благодаря чему возможно применение простой
литейной (модельной) формы, предусматривающей одновременное или направленное
затвердевание сплава и свободное извлечение отливки (модели) из формы. В
конструкции отливки необходимо также учитывать реальные производственные
возможности: наличие определенного оборудования для подготовки сплава и
формирования отливки при заданном объеме выпуска продукции. Литье в песчаные
формы.
Конфигурация отливки проста, не требует сложной формы,
литейный сплав обладает необходимыми литейными свойствами и можно сделать
вывод, что отливка технологична.
Исходя из принципа базирования (совмещения и постоянства баз)
целесообразно сначала провести обработку плоскость базирования детали,
основание для установки, т.к. относительно данной плоскости происходит
определение необходимых геометрических размеров. Необходимое качество и
шероховатость достигается фрезерованием торцевой фрезой, применив черновое и
чистовое фрезерование. Обработка направляющего паза происходит с помощью
концевой фрезой в один проход (чистовое) не меняя закрепление заготовки. Далее
деталь базируется относительно обработанной поверхности на
горизонтально-расточном станке и подрезается торец (черновое + чистовое). Не
меняя базирования производится растачивание отверстия Ш120 мм (черновое +
чистовое) на том же станке, сменив режущий инструмент, и протачивается фаска.
Не меняя базирования, повернув деталь, с помощью, например, поворотного стола,
производится подрезка торца, и проточка фаски аналогично указанному выше. Далее
деталь устанавливается на вертикально-сверлильный станок и с помощью специального
приспособления (накладного кондуктора) производится сверление отверстий под
резьбу и нарезание резьбы. Потом деталь перебазируется и аналогичные операции
производятся на другой стороне. Наличие кондуктора необходимо для выполнения
требований к точности расположения отверстий. После деталь базируется
относительно основания и сверлятся отверстия Ш22 мм, происходит зенкование
поверхностей под крепёжные детали и зенкование фасок.
5. Определение межоперационных припусков на
механическую обработку
Припуск на размер рассчитывается по
следующей формуле [3]:
Н - наибольшая высота гребешков неровностей на обрабатываемой
поверхности, мм;
Т - наибольшая глубина дефектного поверхностного слоя на
обрабатываемой поверхности, мм;
Е - наибольшая суммарная погрешность установки, мм;
- наибольшая погрешность установки в плоскости поперечного
сечения, мм
- наибольшая погрешность установки в плоскости продольного
сечения, мм;
М - наибольший размер обрабатываемой поверхности, мм;
l - расчётная длина, погонные метры;
С - наибольшее значение искривления (остаточная деформация), мм;
С=m·l;
a, m, b - коэффициенты, зависящие от характера и
точности заготовки;
К - коэффициент перекрытия одних погрешностей другими, К=0,9.
Определим расчётным путём припуск на механическую обработку
отверстия диаметром 120 мм, выполненного по 7 квалитету с шероховатостью
поверхности Ra 2.5.
Данная точность и шероховатость достигается чистовым растачиванием
(7 квалитет, Ra 2,5), предварительно черновое
растачивание (15 квалитет, Ra 100) (табл.
3.38, 3.39 стр. 147-151 [4]).
Н 2 =0,225 мм; Т 2 =0,05 мм; а 2 =0,05;
b 2 =0,3; m 2 =0,2; М=120 мм; д 1 =1,6 мм.
Н 1 +Т 1 =0,5 мм; а 1 =0,1; b 1 =1;
m 1 =1; М=120 мм; д 1 =4 мм.
Таким образом, диаметр под чистовое растачивание: , диаметр под черновое растачивание
(диаметр заготовки) . Но так как литьём не может быть получен
такой размер (и такие размеры не задаются) принимаем диаметр заготовки равным
112 мм, и получаем припуск под черновое растачивание равным .
Общий
припуск на размер составляет 2,23+5,77=8 мм.
Черновое фрезерование плоскости основания
корпуса.
Выбираем горизонтально-фрезерный станок 6Н80, его
характеристики:
до стола………………………………………………………………20-320
до хобота……………………………………………………………….123
Наибольшее расстояние оси вертикальных направляющих до задней
кромки стола…………………………………………………………………240
Количество Т-образных пазов………………………………………….3
Ширина Т-образного паза…………………………………………14А 3
угол поворота стола в градусах……………………………………±45
продольное………………………………………………………………500
поперечное………………………………………………………………160
вертикальное…………………………………………………………….300
Конус Морзе отверстия шпинделя ГОСТ 836-62………………………2
Число ступеней шпинделя ……………………………………………12
Число оборотов шпинделя в минуту……….………………….50-2240
Число ступеней подач стола…………………………………………12
продольная ………………………………………………….…25-1120
поперечная……………………………………………………….18-800
вертикальная ……………………………………………………….9-400
Мощность главного электродвигателя в кВт…….……………………3
длина……….……………………………………………………………1360
ширина…………………………………………………………………..1860
высота …………………………………………………………………1530
Масса в кг……………………………………………………………1150
В качестве режущего инструмента принимается цилиндрическая
фреза из быстрорежущей стали L=50 мм, материал режущей части Т15К6.
Подача при фрезеровании цилиндрической фрезой из
быстрорежущей стали при мощности станка до 5 кВт, средней жесткости СПИД, для
чугуна 0,09-0,18 мм на один зуб. (6, таб. 32, с. 438)
Значение коэффициента и показателей степени в формуле
определения скорости резания при фрезеровании. (6, табл. 37, стр. 441). Для
серого чугуна.
Уточняем частоту вращения по данным станка: n ф =300
об/мин;
Уточняем скорость по фактической частоте вращения:
Значение коэффициента и показателей степени в формуле
определения силы резания при фрезеровании. (6, табл. 37, стр. 445). Для серого
чугуна
Чистовое фрезерование плоскости основания корпуса
Подача при чистовом фрезеровании торцовой фрезой из
быстрорежущей стали 1,0-2,3 мм на один оборот. (6, таб. 36, с. 440)
Глубина фрезерования принимается равной припуску на
механическую обработку. Для чистового фрезерования после чернового и длине
обрабатываемого участка 255 мм припуск равен 0,14 мм (6, табл. 37, стр. 193).
Значение коэффициента и показателей степени в формуле
определения скорости резания при фрезеровании. (6, табл. 37, стр. 442). Для
серого чугуна.
Уточняем частоту вращения по данным станка: n ф =350
об/мин;
Уточняем скорость по фактической частоте вращения:
Значение коэффициента и показателей степени в формуле
определения силы резания при фрезеровании. (6, табл. 37, стр. 445). Для серого
чугуна
Чистовое фрезерование направляющего паза корпуса
Производится на том же станке, не меняя базирования детали.
Осуществляется концевой фрезой из быстрорежущей стали с коническим хвостовиком
Глубина фрезерования равна глубине паза и составляет 13 мм.
Подача при чистовом фрезеровании концевой фрезой из
быстрорежущей стали 0,15-0,1 мм на один оборот.
Значение коэффициента и показателей степени в формуле
определения скорости резания при фрезеровании. (6, табл. 37, стр. 442). Для
серого чугуна.
Уточняем частоту вращения по данным станка: n ф =600
об/мин;
Уточняем скорость по фактической частоте вращения:
Значение коэффициента и показателей степени в формуле
определения силы резания при фрезеровании. (6, табл. 37, стр. 445). Для серого
чугуна
Выбираем станок горизонтально-расточной 2654
Тип компоновки станка …………………………….…………………..Б
Диаметр выдвижного шпинделя………………………………………150
Конус отверстия шпинделя …………………………..метрический 80
выдвижного шпинделя продольное…….….……………………..1240
радиального суппорта …………………………………………….….240
поперечное …………………………………………………………..1800
продольное……………………………………………………………1800
выдвижного шпинделя ………………………………………7,5-950
планшайбы …………………….………………………………. 3,75-192
выдвижного шпинделя ………………………………………….…2-150
шпиндельной бабки………………………………………………….1-750
Токарный проходной отогнутый для подрезки торцов резец с углом в
плане ц=45°, =10°. ГОСТ 18877-73
Т - период стойкости пластины, Т=30 мин (стр. 268 [6]);
t - глубина резания, равна припуску при обработке, t=1 мм;
- зависит от качества обрабатываемого материала;
- зависит от состояния поверхности заготовки;
- зависит от материала режущей части;
Подача (табл. 2 стр. 418 [6]) S=1,0…1,5 мм/об.
Уточняем частоту вращения по паспортным данным станка: n ф =400
об/мин;
Уточняем скорость по фактической частоте вращения:
- зависит от качества обрабатываемого материала;
Т - период стойкости пластины, Т=30 мин (стр. 268 [6]);
t - глубина резания, равна припуску при обработке, t=0,23 мм;
S - подача; - поправочный коэффициент;
- зависит от качества обрабатываемого материала;
- зависит от состояния поверхности заготовки;
- зависит от материала режущей части;
Подача (табл. 2 стр. 418 [6]) S=, 25…0,40 мм/об.
Уточняем частоту вращения по паспортным данным станка: n ф =900
об/мин;
Уточняем скорость по фактической частоте вращения:
- постоянные для данной операции; - поправочный коэффициент; - зависит от качества обрабатываемого материала; , , - зависит от параметров резца; табл. 22,
стр. 274 [6]:
Выбираем станок горизонтально-расточной 2654
Тип компоновки станка …………………………….…………………..Б
Диаметр выдвижного шпинделя………………………………………150
Конус отверстия шпинделя ………………………………метрический 80
выдвижного шпинделя продольное…….….……………………..1240
радиального суппорта ………………………………………….…….240
поперечное ………………………………………………….……..1800
продольное……………………………………….…………………1800
выдвижного шпинделя ……………………………………………7,5-950
планшайбы …………………….……………………………. 3,75-192
выдвижного шпинделя ………………………………………….…2-150
шпиндельной бабки……………………………………………….1-750
Резец расточной державочный с пластиной из твердого сплава.
ГОСТ 9795-84
Т - период стойкости пластины, Т=30 мин (стр. 268 [6]);
t - глубина резания, равна половине припуска на диаметр при
обработке, t=2,61 мм;
- зависит от качества обрабатываемого материала;
- зависит от состояния поверхности заготовки;
- зависит от материала режущей части;
Подача (табл. 12 стр. 267 [6]) S=0,8…1,1 мм/об, следуя
рекомендациям примечания выбираем подачу из середины диапазона и сравниваем её
с паспортными данными станка, S=1 мм/об.
Уточняем частоту вращения по паспортным данным станка: n ф =500
об/мин;
Уточняем скорость по фактической частоте вращения:
l 1 -
величина врезания, l 1 =t/tgц=2,76/tg95°=0,25 мм;
l 2 -
величина перебега, l 2 =1…3 мм;
- зависит от качества обрабатываемого материала;
Т - период стойкости пластины, Т=30 мин (стр. 268 [6]);
t - глубина резания, равна половине припуска на диаметр при
обработке, t=1,16 мм;
- зависит от качества обрабатываемого материала;
- зависит от состояния поверхности заготовки;
- зависит от материала режущей части;
Подача (табл. 12 стр. 267 [6]) S=0,25…0,4 мм/об
Уточняем частоту вращения по паспортным данным станка: n ф =900
об/мин;
Уточняем скорость по фактической частоте вращения:
l 1 -
величина врезания, l 1 =t/tgц=2,76/tg95°=0,25 мм;
l 2 -
величина перебега, l 2 =1…3 мм;
- зависит от качества обрабатываемого материала;
Выбираем вертикально-сверлильный станок 2Н125:
Наибольший условный диаметр сверления.………………………25
Размеры рабочей поверхности стола….……………………400*500
от торца шпинделя до поверхности стола ……………………..60-700
от торца шпинделя до поверхности фундаментной плиты……650-1060
от пси шпинделя до стойки (вылет шпинделя)……………………300
вертикальное перемещение сверлильной головки …………………300
ход шпинделя………………………………………………………..170
Конус Морзе отверстия шпинделя………………………………..3
Число ступеней оборотов шпинделя….…………………………..12
Число ступеней механических подач шпинделя ……………………9
Мощность главного электродвигателя в кВт…………………………2,2
длина……………….………………………………………………….1130
высота……………….………………………………………………….2290
Вес в кг.…………………………………………………………….….980
Сверло спиральное с пластинками из твердых сплавов для
обработки чугуна. Угол заточки для сверл диаметром до 12 мм. По рекомендациям
(6, табл. 41, стр. 198) сверление под резьбу М10 с крупным шагом выбираем
диаметр сверла 8,5 мм.
Глубина резания равна половине диаметра сверла t=0,5D=4,25 мм.
Подача при сверлении серого чугуна (табл. 27, стр. 433) S=0,36-0,57 мм. Расчёт
скорости резания:
Уточняем частоту вращения по паспортным данным станка: n ф =2500
об/мин;
Уточняем скорость по фактической частоте вращения:
крутящий момент и осевую силу при сверлении определяем по
следующим формулам:
Нарезание происходит с помощью метчика. Режущая часть из
быстрорежущей стали, хвостовик - сталь 40Х. Машинно-ручной ГОСТ 3266-81
Уточняем частоту вращения по паспортным данным станка: n ф =200
об/мин;
Уточняем скорость по фактической частоте вращения:
. Нормирование технологического процесса
В процессе расчётов режимов резания для каждой операции было
определено машинное время То. Время на выполнение операции равно:
Твсп - вспомогательное время, Твсп=10-15% То;
Тобс - время обслуживания станка, Тобс=3-5% То;
Тпер - время перерывов, Тпер=3-5% То.
Кроме того, определяется оперативное время
8. Описание спроектированной конструкции
приспособления. Расчет приспособления
Проектируется приспособления, позволяющее точно провести операцию
сверления, т.е. точно произвести определение мест сверления, необходимое
расположение отверстий. В данном случае применим накладной кондуктор. В момент
начала сверления, когда необходимо обеспечить надежный прижим, на заготовку
действует момент резания М, стремящийся повернуть заготовку вокруг ее оси, и
осевая сила подачи , прижимающая заготовку к опорной
поверхности. Величину необходимой силы зажима:
- наружный радиус поверхности соприкосновения основания заготовки
с поверхностью кондуктора, мм;
- радиус отверстия заготовки или внутренний радиус
соприкосновения поверхностей заготовки с поверхностями кондукторной плиты и
кондуктора, мм;
-наружный радиус поверхности соприкосновения кондукторной плиты с
поверхностью заготовки, мм;
Проектируемым металлорежущим инструментом в данной работе является
цилиндрическая зенковка для обработки опорных поверхностей под крепежные детали
с направляющей цапфой под сквозное отверстие. Зенковки отличаются наличием
цапфы с углом равным 90°, четырьмя зубьями у всех типов. В остальном
конструкция зенковок аналогична конструкции зенкеров. Угол наклона стружечных
канавок зенковок из быстрорежущих сталей - 15°, зенковок, оснащенных твердым
сплавом - 10° (совпадает с углом врезания пластины, т.е. = 10°). Данный инструмент необходим для создания обработанной
плоскости, перпендикулярной оси отверстия, для оптимального соприкосновения
крепежного элемента с корпусом, чтобы не было перекосов, сдвигов и прочего.
Цилиндрическая цапфа позволяет достичь соосности зенковки и самого отверстия. С
помощью хвостовика с конусом Морзе инструмент крепится в шпинделе станка.
10. Расчёт исполнительных размеров предельного калибра
1. По ГОСТ 25437-82 определяются предельные отклонения
отверстия:
. В соответствии с ГОСТом 24853-81 строятся схемы расположения
полей допусков калибров относительно границ расположения поля допуска
отверстия.
Из этого же стандарта определяются следующие величины:
Н - допуски на изготовление калибра пробки;
Z - отклонение середины поля допуска на изготовление
проходного калибра пробки;
У - допустимый выход размера изношенного проходного калибра
(пробки) за границу поля допуска; а также допуски на форму калибров:
. По формулам из стандарта ГОСТ 248553-81 (приложение 20
[12]) рассчитываются размеры предельных и изношенных калибров, а так же
исполнительные размеры калибров:
Р-ПРmax=D-EI+Z+H/2=120-0+0,006+0,008/2=120,01 мм;
Р-ПРmin=D+EI+Z-H/2=120+0+0,006-0,008/2=120,002
мм;
Р-ПРизн=D+EI-У=120+0-0,004=119,996 мм;
Р-ПРисп=(Р-ПРmax) - H =120,01 -0.008 мм;
Р-НЕmax=D+ES+H/2=120+0,035+0,008/2=120,039
мм;
Р-НЕmin=D+ES-H/2=120+0,035-0,008/2=12,031 мм;
Р-НЕисп=(Р-НЕmax) -H =120,039 -0.008
мм.
1. Картавов С.А. Технология машиностроения, К.:
Вища школа, 1984 - 272 стр.;
2. Технология машиностроения. В 2 т. Т.1
Основы технологии машиностроения. Под ред. А.М. Дальского. - М. Изд-во МГТУ им.
Н.Э. Баумана, 1999-564 с.
. Сушков О.Д., Методические указания к
выполнению курсовых работ по курсу «Технологические основы машиностроения», Керчь,
КМТИ, 1998 - 57 стр.;
. Балабанов А.Н., Краткий справочник
технолога машиностроителя, М.: Издательство стандартов, 1992 - 464 стр.;
. Кирилюк Ю.Е. Допуски и посадки.
Справочник, К.: Вища школа, 1989 - 135 стр.;
. Косилова А.Г., Справочник технолога-машиностроителя
Т.2, М.:Машиностроение, 1985 - 496 стр.;
. Орлов П.Н., Краткий справочник
металлиста, М.: Машиностроение, 1987 - 960 стр.;
. А.Н. Малов, Справочник технолога
машиностроителя Т.2, М.: Машиностроение, 1972 - 568 стр.;
. Косилова А.Г., Справочник
технолога-машиносторителя Т.1, М.: Машиностроение, 1973. - 696 стр.;
. Нефедов Н.А. Сборник задач и примеров по
резанию металлов и режущему инструменту, М.: Машиностроение, 1977 - 88 стр.;
. ГОСТ 14822-69, ГОСТ 14823-69
. Ангел Г.Н. Взаимозаменяемость, стандартизация
и технические измерения: методические указания по выполнению курсовой работы. -
Калининград.: Калининградский технический институт рыбной промышленности и
хозяйства, 1988. - 94 стр.;
. Добрыднев И.С. Курсовое проектирование
по предмету «Технология машиностроения»: учебное пособие для техникумов по
специальности «Обработка металлов резанием», М.: Машиностроение, 1985. - 184
стр.
. Справочник инструментальщика. Под ред.
И.А. Ординарцева. - Л: Машиностроение, Ленинградское отделение. 1987-846 с.
Похожие работы на - Технологический процесс изготовления детали 'Корпус' Курсовая работа (т). Другое.
Курсовая На Тему Инновационная Деятельность Предприятия
Готовая Курсовая Работа Вилка
Реферат: Антиматерия и Ативещество. Скачать бесплатно и без регистрации
Реферат: Характеристика торгового оборудования гастронома Особый
Реферат: Генетический скрининг
Реферат: Органи дізнання
Банкротство Гражданина Курсовая Работа
Сочинение На Тему Патриотизм 9.3 Огэ
Реферат по теме Мировой опыт моделирования потребительского поведения
Критерии Оценивания Контрольных Работ Огэ 2022
Эволюция Государственного Аппарата В Рф Реферат
Реферат: Дианетика современная наука душевного здоровья. Скачать бесплатно и без регистрации
Статья На Тему Антисоветское Движение В Чечне В 1920–1930-Е Годы
Реферат: Культурное строительство в годы семилетки. Скачать бесплатно и без регистрации
Сочинение Про Осень На Калмыцком Языке
Реферат Сестринский Уход В Нефрологии
Реферат по теме Положение геев и лесбиянок в современной России
Дипломная работа: Организация оперативно-розыскной работы оперативных аппаратов в колониях-поселениях
Реферат: Кадусии
Реферат по теме Яды и противоядия
Реферат: Французскі фізік Андрэ Мары Ампер
Похожие работы на - Профессиональная деятельность участковой медицинской сестры
Реферат: Методические положения по анализу деловой активности Современное состояние спк «Кава» иорганизация в нём аналитической работы