Секция секционного пуансона. Курсовая работа (т). Другое.
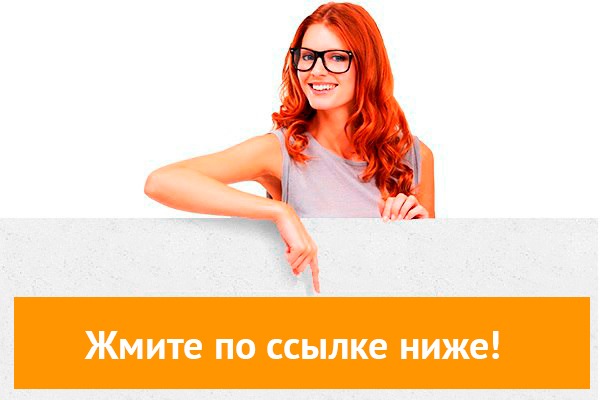
⚡ 👉🏻👉🏻👉🏻 ИНФОРМАЦИЯ ДОСТУПНА ЗДЕСЬ ЖМИТЕ 👈🏻👈🏻👈🏻
Вы можете узнать стоимость помощи в написании студенческой работы.
Помощь в написании работы, которую точно примут!
Похожие работы на - Секция секционного пуансона
Нужна качественная работа без плагиата?
Не нашел материал для своей работы?
Поможем написать качественную работу Без плагиата!
Инструмент 1512-5124 "Пуансон секционный" предназначен для
изготовления методом обработки давлением детали 914.45.007-0 "Щека".
Поверхность детали "Секция секционного пуансона" образована совокупностью
плоскостей и цилиндрических поверхностей (рисунок 1.1).
Рисунок 1.1 - Эскиз детали Секция секционного пуансона.
Основными поверхностями, определяющими положение секции пуансона в
пуансонодержателе являются: плоскость 1, группа гладких отверстий 5, паз 7,
плоская поверхность 3.
Вспомогательными поверхностями, определяющими положение других деталей,
присоединяемых к данной являются резьбовые отверстия 6.
Исполнительными поверхностями, которыми пуансон секционный выполняет своё
предназначение, являются: плоская поверхность 2 и контур пуансона 4 10 и 11,
образованный совокупностью плоскостей и сегментов цилиндрических поверхностей.
8 и 9 - свободные поверхности.
К основным поверхностям секции пуансона предъявляются высокие требования
по точности и шероховатости поверхности - IT7, шероховатость - Ra0.8. Исполнительные поверхности выполнены по IT9, шероховатость поверхности - Ra 6.3. Вспомогательные резьбовые отверстия изготовляются по
седьмой степени точности. Свободные поверхности - по IT14 и шероховатость - Rz80/
Секционный пуансон изготавливается из инструментальной углеродистой стали
У8А [1, с.414].
Механические характеристики стали У8А:
относительное удлинение при разрыве σ 5 =10%
Химический состав материала по ГОСТ 1435-99:
температура ковки: Начала 1180, конца 800. Охлаждение заготовок сечением
до 100 мм на воздухе, 101-300 мм - в яме.
свариваемость: не применяется для сварных конструкций. Способ сварки -
КТС.
обрабатываемость резанием при НВ 187-227 Ku тв.спл=1.2, Ku б.ст.=1.1.
склонность к отпускной способности: не склонна
флокеночувствительность: не чувствительна
Модуль нормальной упругости, Е: 209 ГПа
Модуль упругости при сдвиге кручением G: 81 ГПа
Коэффициент линейного расширения a: 11.4 10 -6 °С -1
Удельная теплоемкость С: 477 Дж/(кг · °С)
Для заготовок из стали У8А применяется отжиг с нагревом до 690°C -710°C и
последующим охлаждением с печью. При этом материал заготовки приобретёт
твёрдость не более 187 HB,
улучшится обрабатываемость резанием. После механической обработки - закалка до
температуры 780°C - 800°C с последующим охлаждением в воде, что обеспечит
твёрдость материала от 62 HRC.
Предварительно определим тип производства по массе детали и годовой
программе выпуска. Масса детали составляет 6.12 килограмма, программа выпуска
составляет 950 штук в год. Согласно [2 с. 24, табл. 3.1] это соответствует
среднесерийному типу производства.
Серийное производство характеризуется ограниченной номенклатурой изделий,
изготовляемых периодически повторяющимися партиями, и сравнительно большим
объёмом выпуска, чем в единичном типе производства. При серийном производстве
используются универсальные станки, оснащённые как специальными, так и
универсальными и универсально-сборными приспособлениями, что позволяет снизить
трудоёмкость и себестоимость изготовления изделия. В серийном производстве
технологический процесс изготовления изделия преимущественно дифференцирован,
то есть, расчленён на отдельные самостоятельные операции, выполняемые на
определённых станках. При серийном производстве обычно применяют универсальные,
специализированные, агрегатные и другие металлорежущие станки.
Исходя из служебного назначения детали в целом и отдельных поверхностей в
частности, установим технические требования (допуски относительного
расположения, расстояния) к отдельным поверхностям, которые позволят
поверхностям и их сочетаниям выполнять своё назначение.
перпендикулярность отверстий 5 плоскости 1;
расстояние от плоскости 3 до отверстий 5;
перпендикулярность отверстий 6 плоскости 1;
расстояние от плоскости 3 до отверстий 6;
расстояние между плоскостями 1 и 2;
расстояния от элементов, образующих контур 4 10 и11, до плоскости 3;
расстояния от осей отверстий 5 до плоскости симметрии пуансона и
поверхности 3;
расстояния от отверстий 5 до элементов, образующих контур 4;
-соосность цилиндрических поверхностей 9 с резьбовым отверстие 6;
соосность цилиндрических поверхностей 8 с опверстиями 5;
На чертеже детали указанны расстояние от плоскости 3 до отверстий 5,
расстояние от плоскости 3 до отверстий 6, расстояние между плоскостями 1 и 2,
расстояния от элементов, образующих контур 4, до плоскости 3.
Следующие технические требования даны в пределах поля допуска на
соответствующий размер:
перпендикулярность отверстий 5 плоскости 1;
перпендикулярность отверстий 6 плоскости 1;
Расстояния от осей отверстий 5 до осей отверстий 6 и расстояния от
отверстий 5 до элементов, образующих контур 4 проставлены не от отверстий 5, а
от горизонтальной оси штампа.
Представим технические требования к отдельным поверхностям детали в виде
таблицы 1.1, содержащей допуски на размер, относительное расположение,
отклонение формы, шероховатость.
Таблица 1.1 - Технические требования к поверхностям по чертежу детали
Все технические требования, указанные на чертеже, достижимы и могут быть
получены.
Зададимся нормальным уровнем А геометрической точности. Согласно этому
уровню степень точности допусков формы определяют как N-1, где N -
квалитет соответствующего размера. Таким образом, согласно [3 с.30 табл. 2,
с.40 табл. 3] заданные чертежом допуски формы и относительного расположения
соответствуют принятому уровню геометрической точности.
Для уровня А численное значение шероховатости поверхности составляет Ra ≤ 0.05∙Td, где Td - значение допуска на
соответствующий размер. Полученное значение необходимо округлить до значения из
ряда шероховатостей [1 с.44, табл. 1]. Согласно этой зависимости получаем:
для поверхности 1: 0.05∙0.1 = 0.005 мм = 5 мкм;
для поверхности 2: 0.05∙0.1 = 0.005 мм = 5 мкм;
для поверхности 3: 0.05∙0.03 = 0.0015 мм = 1.25 мкм;
для поверхности 4: 0.05∙0.052 = 0.0026 мм = 2.5 мкм;
для поверхности 5: 0.05∙0.018 = 0.0009 мм = 0.8 мкм;
для поверхности 6: 0.05∙0.018 = 0.0009 мм = 0.8 мкм;
для поверхности 7: 0.05∙0.018 = 0.0009 мм = 0.8 мкм;
для поверхности 8: 0.05∙0.52 = 0.026 мм = 25 мкм;
для поверхности 9: 0.05∙0.52 = 0.026 мм = 25 мкм;
для поверхности 10 и 11 значение шероховатости аналогично поверхности 4.
Таким образом, на поверхности 1, 2 и 3 значения шероховатости по требованиям
чертежа назначены более жёсткие, чем значения шероховатости обусловленные
допуском на размер.
Деталь секция секционного пуансона относится к классу корпусных.
Конфигурация детали несложная. Секция секционного пуансона представляет собой
пластину с двумя группами отверстий, периметр которой очерчен совокупностью
плоскостей и секторов цилиндров.
На детали отсутствуют поверхности, к которым затруднён подвод
инструмента. При сверлении отверстий врезание и выход сверла будут происходить
по плоскости, перпендикулярной оси сверла, что уменьшает вероятность поломки
инструмента, предотвращает разбивку отверстий и уменьшает увод сверла.
Резьбовые отверстия - сквозные, что облегчает нарезание резьбы. Конфигурация детали
позволяет использовать оборудование с ЧПУ. Наиболее точные протяжённые
поверхности могут быть обработаны на проход. На детали присутствуют удобные
базирующие поверхности в виде протяжённых точных плоскостей, позволяющих
выдержать при обработке технические требования перпендикулярности отверстий и
контура.
Учитывая ранее приведенные свойства материала детали и её геометрическую
форму, наиболее технологичной будет поковка. Такой способ получения заготовок
позволит достичь необходимой производительности и уменьшить объём механической
обработки, увеличить коэффициент использования металла.
В целом конструкция детали технологична, но сборка двух секций пуансона в
пуансонодержателе нетехнологична, так как у секций пуансона отсутствуют
поверхности, позволяющие при сборке придавать секциям правильное положение
относительно друг друга.
С учётом свойств материала заготовки и формы её поверхности
проанализируем возможность и целесообразность получения заготовки различными
методами. Так как сталь У8А является сталью, обрабатываемой давлением, то
составим матрицу влияния факторов, в которую включим методы обработки металлов
давлением (таблица 1.2).
Таблица 1.2 - Матрица влияния факторов
Согласно матрице влияния факторов сравним методы ковки и штамповки на
КГШП, определив их технико-экономические показатели.
Определим технико-экономические показатели для штамповки на КГШП.
Предварительно найдём массу поковки по формуле 1.1:
где mд - масса детали, равная 6.12
килограмм;
Кр - расчётный коэффициент, зависящий то формы детали, принимаем Кр =
(1.3÷1.7).
Подставив в формулу 1.1 значения, получим:
По материалам [2] определяем группу стали - М3, класс точности - Т4.
Определим коэффициент сложности:
Где
m ф - масса
простой фигуры наименьшего объёма, в которую можно будет вписать поковку. В
качестве такой фигуры примем параллелепипед со сторонами 0.12м, 0.22м, 0.05м.
Таким образом, коэффициент сложности составит С1.
С
учётом предварительной массы поковки, класса точности, коэффициента сложности
исходный индекс - 14.
Поверхность
разъёма штампа с учётом формы поковки принимаем таким образом, чтобы вся
поковка находилась в одной половине штампа.
Так
как все отверстия в детали относительно длинные и их диаметр менее 30
миллиметров, их получение или наметка в процессе штамповки нецелесообразна.
Назначим
припуски на все механически обрабатываемые поверхности поковки и сведём их в
таблицу 1.3.
У
размеров 220, 120, 140, 65, 85, 170, 50 припуски увеличивают длину размера, у
размеров 60, 115 один припуск увеличивает размер, другой уменьшает.
Штамповочные
уклоны на наружные поверхности - 1°;
Минимальный
радиус скругления - 2.5мм, принимаем 3мм.
Объём
выходной заготовки определяют по формуле 1.2:
V выг - расход металла по выгар, мм 3 ;
V об - расход металла на облой, мм 3 ;
Таблица
1.3 - Припуски на поверхности поковки
Затраты металла на выгар определяют по формуле 1.3:
Где
k выг -
коэффициент выгара, при нагреве в газовых печах k выг = 1%. Подставив в формулу объём поковки V п =1095242 мм 3 , получим:
Расход
металла на облой определяются по формуле:
Где
Пп - периметр поковки в плоскости разъёма штампа, Пп= 1197.38 мм;
Fоб - площадь
поперечного сечения облоя, мм 2 , для прессов находят по формуле
(1.5):
Где
z - коэффициент, учитывающий заполнение облойной
канавки. Для прессовых штампов z=1.5;
F м - площадь поперечного сечения мостика, мм 2 ,определяют
в зависимости от номера облойной канавки.
Номер
облойной канавки определяют в зависимости от необходимой толщины облоя h o
Где
S п.п -
площадь поковки в плане, равная 20095.328430 мм 2 . подставив
найденные значения, получим:
В
соответствии с толщиной облоя принимаем номер облойной канавки 4 с площадью
поперечного сечения F м =30мм 2
, тогда площадь поперечного сечения облоя будет равна:
С
учётом этого потери на облой составят:
Определим
показатели эффективности использования металла:
Определим
себестоимость штампованной поковки по формуле :
Где
Sз - базовая себестоимость 1 кг штампованной поковки,
грн. Для поковок, получаемых на КГШП Sз=40 грн/кг;
m вых - масса выходной заготовки, m вых = 8.564 кг;
N - годовая
программа выпуска, N=950;
Кс
- коэффициент, учитывающий сложность поковки, принимаем Кс=0.7;
Км
- коэффициент, учитывающий материал поковки, принимаем Км=1.6;
Кв
- коэффициент, учитывающий массу заготовки, принимаем Кв=1.04;
Sв -
себестоимость отходов, принимаем Sв=1 грн/кг.
Подставив
величины в формулу 1.6, получим:
Определим
технико-экономические показатели для ковки на молотах. Определяем тип поковки.
В соответствии с рекомендациями ГОСТ 7829-70 принимаем тип поковки - пластина.
Заготовка
технологична, так как имеет простую геометрическую форму, ограниченную
совокупностью плоских поверхностей. Отсутствуют такие элементы
нетехнологтчности как пересечение нескольких цилиндрических поверхностей,
пересечение призматических поверхностей с цилиндрическими, рёбра жёсткости,
короткие уступы.
Назначим
припуски и допуски на поковку из углеродистой стали, изготавливаемой на молотах
по ГОСТ 7829-70.
В
качестве исходной заготовки для поковки выбираем прокат. Необходимый объём
металла определяем по формуле:
Где
Vп - объём поковки, см 3 , Определяем, исходя
из номинальных размеров поковки с учётом напусков и припусков: Vп=1336.1212
см 3 ;
Vпр, Vд -
объёмы прибыльной и донной частей слитка, так как ранее был принят прокат, то Vпр=0,
Vд=0;
Vобс - объём
отходов на обсечку. Составляет 1-20%. Большие значения соответствуют более
сложным поковкам. Принимаем Vобс=200.42 см 3 ;
Vуг - объём
отходов на выгар металла при нагреве поковки. Принимаем Vуг=26.72
см 3 ;
Vв - объём
выдры. Так как отверстия не могут быть получены в заготовке, принимаем Vв=0.
Подставив значения в формулу, получим:
Определим
показатели технологичности заготовки:
Определим
технологическую себестоимость заготовки
Где
С - базовая стоимость 1 тонны поковок, принимаем С=5550 грн/т;
kс - коэффициент
сложности, зависящий от формы поковки. Принимаем kс=1;
kм -
коэффициент, зависящий от материала заготовки, для углеродистых сталей
принимаем kм=1;
Sотх - стоимость
1 кг отходов, для углеродистой стали принимаем Sотх=1 грн. Подставив
найденные значения в формулу 1.7, получим:
Окончательно
принимаем штампованную поковку.
Выбор технологических баз. Поверхностью, от которой заданно больше всего
технических требований является плоскость 1 (рисунок 1.1). От этой плоскости
задан точный размер 50n7,
параллельность точной поверхности 2, перпендикулярность групп отверстий 5 и 6,
перпендикулярность элементов контура секции пуансона. При установке заготовки
на эту поверхность присутствует возможность полной обработки отверстий 5 и 6 с
одной установки. Поверхность 1 может быть обработана первой и позволяет
устанавливать заготовку на всех последующих операциях, соблюдается принцип
единства баз, так как поверхность 1 является основной поверхностью,
определяющей положение секции пуансона.
От поверхности 3 заданны расстояния до точно обрабатываемых поверхностей
5 и 6, эта поверхность является основной поверхностью, определяющей положение
секции пуансона. Эта поверхность может быть обработана после получения заготовки,
может в дальнейшем использоваться как технологическая база для других операций,
что позволит соблюсти принцип единства баз.
Группа отверстий 5 является поверхностями, определяющими положение секции
пуансона. После окончательной обработки отверстия 5 могут выступать в качестве
технологических баз при дальнейшей обработке контура пуансона. Размеры,
задающие положение элементов контура секции пуансона задаются от поверхности 3
по одной координате и от оси штампа по другой. На операциях обработки контура возможно
использовать поверхность 3 в качестве базы, но невозможно использовать ось
штампа. Следовательно, при обработке контура пуансона не будет соблюдаться
принцип единства баз.
При несовмещении технологической и конструкторской баз возникает
дополнительная погрешность вследствие несовмещения конструкторской базы с
соответствующей технологической базой. Величина погрешности несовмещения баз ω нб в данном случае эта разность равна
допуску на размер, связывающий конструкторскую базу с соответствующей технологической.
Сумма погрешности технологической системы и погрешность несовмещения баз должны
быть меньше допуска на получаемый размер. Величина погрешности технологической
системы в данном случае равна средней экономической точности выбранного метода
обработки - 30 мкм:
Смена
баз также возникает при обработке поверхности 11. Размер 60 при обработке
поверхности 11 может быть получен при установке заготовки на контур. Размер 80
не может быть получен, при такой установке реально получается размер 140.
Рассмотрим погрешность, возникающую в следствие несовмещения баз. Величина
допуска на размер 80 составляет 0,074. Экономическая точность фрезерования
размера 140 составляет 0,04мм. Допуск размера 220, соединяющего базу, от
которой указан размер 80 с базой, от которой формируется размер 140 составляет
0,072. Если выполняется неравенство Т>ω ТС +ω НБ , то
смена баз возможна:
Так
как неравенство не выполняется, смена баз невозможна. Для осуществления смены
баз ужесточим допуск на размер 220: 0,046 мм (IT7), применим
другой способ получения размера 140 - фрезерование тонкое, которым возможно
достижение IT6 (для размера 140 - 0,025мм). Рассмотрим неравенство
с учётом изменений планов обработки поверхностей:
Последовательность
обработки поверхностей заготовки. После получения поковки для уменьшения
твёрдости материала, улучшения обрабатываемости и снятия остаточных напряжений
необходимо произвести предварительную термическую обработку - отжиг с нагревом
до 710°С с последующим охлаждением с печью, после чего материал поковки
приобретает твёрдость до 187HB.
После
предварительной термообработки происходит предварительная обработка комплекта
технологических баз.
Первой
обрабатывается поверхность 1, базой при этом служит поверхность 2:
Затем
обрабатывается поверхность 3, при этом базами служат поверхности 1 и плоскость
контура 4, противоположная поверхности 3:
При
обработке поверхности 2 базой служит поверхность 1:
При
обработке отверстий 5 в качестве технологических баз выступают поверхности 1, 3
и необработанная поверхность 4.
Отверстия
5 обрабатываются окончательно.
При
обработке паза 7 в качестве технологических баз выступают поверхности 1, 3 и
необработанная поверхность 4.
Резьбовые
отверстия 6 обрабатываются от тех же баз, что и поверхности 7 и 5.
Фрезерование
контура 4 осуществляется с применением в качестве баз поверхностей 1, 3 одного
из отверстий 5.
При
фрезеровании поверхности 10 в качестве баз используются поверхности 1 и контур
пуансона 4.
После
предварительной механической обработки осуществляют окончательную термическую
обработку - закалку с нагревом до температуры 800°С с последующим охлаждением в
воде. После термообработки материал секции пуансона приобретёт твёрдость 62-64HRC,
что позволит увеличить долговечность пуансона, упростит дальнейшую абразивную
обработку.
Окончательная
механическая обработка заключается в точной абразивной обработке предварительно
обработанных поверхностей.
Поверхность
1 обрабатывается от базы 2.
При
обработке поверхности 2 базой служит поверхность 1.
При
обработке поверхности 10 в качестве баз используются поверхности 1 и контур
пуансона 4.
Маршруты обработки поверхностей секции пуансона приведены в таблице 1.4.
Таблица 1.4 - Маршруты обработки поверхностей
Назначение припусков аналитическим способом на поверхность 2 (рисунок
1.1). Принимаем заготовку, полученную методом горячей ковки в штампах, тогда по
[4 мягков] принимаем точность размеров поковки - IT16, шероховатость поверхности - Rz200.
Установим маршрут обработки поверхности, пользуясь данными [4] и
следующими положениями:
при обработке происходит повышение точности на черновых переходах на 3-4
квалитета, на получистовых и чистовых - 1-2 квалитета;
качество поверхности повышается на черновых переходах в 3-4 раза, на чистовых
- в 1.5-2 раза;
термическая обработка ухудшает точность размеров примерно на 1 квалитет и
качество поверхности - в 2 раза.
Принятый маршрут приведён в таблице 1.2
Таблица 1.2 - Маршрут обработки поверхности 2
Так как в ходе обработки поверхности будет сниматься односторонний
припуск, то минимальный операционный (межпереходный) припуск на обработку
поверхности можно определить по формуле [5, с.7, формула 1.6]:
где
Rz ( i -1) - шероховатость поверхности, достигнутая на
предыдущем переходе, мкм;
h ( i -1) - толщина дефектного
слоя полученного на предыдущем переходе, мкм;
Δ ( i -1) - суммарные отклонения расположения поверхностей,
полученные на предыдущем переходе, мкм;
ε i
- погрешность установки заготовки, полученная на данном переходе, мкм;
Таблица
1.3 - Расчёт припуска на обработку поверхности 2
Если
расчёты выполнены верно, должно выполнятся условие:
Подставим
в выражение 1.2 необходимые значения:
Так
как условие выполняется, припуска назначены верно.
Назначение
припусков аналитическим способом на поверхность 5 (рисунок 1.1). Установим
маршрут обработки поверхности, пользуясь данными [4]. Принятый маршрут приведён
в таблице 1.2
Таблица
1.4 - Маршрут обработки поверхности 2
Так как в ходе обработки поверхности будет сниматься двухсторонний
припуск, то минимальный операционный (межпереходный) припуск на обработку
поверхности можно определить по формуле [5, с.8, формула 1.8]:
Найдём
по данным [5, с 17-45] и [6, с. 180-190] значения величин, входящих в формулу
1.1,межпереходные припуски, межпереходные размеры и сведём их в таблицу 1.5.
Если
расчёты выполнены верно, должно выполнятся условие 1.9:
Таблица
1.5 - Расчёт припуска на обработку поверхности 5
Так
как условие выполняется, припуски назначены верно.
При обработке секции секционного пуансона на формирование операций
технологического процесса влияют факторы, обусловленные принятым ранее
среднесерийным типом производства и особенностями формы и технических
требований, предъявляемых к детали.
К большинству поверхностей секции пуансона предъявляются высокие
требования по точности размеров и качеству поверхности, соответствующие
седьмому квалитету, в связи с чем целесообразно произвести разделение операций
технологического процесса на предварительные и окончательные. На предварительных
операциях будут удалены основные припуски и созданы поверхности, которые
невозможно было получить на заготовке. На операциях окончательной обработки
будут удаляться меньшие припуски, что позволит уменьшить основное время этих
операций, и будут обеспечиваться технические требования, предъявляемые
чертежом. Предварительные операции обработки будут осуществляться разнообразным
лезвийным инструментом, окончательные операции будут выполнены преимущественно
абразивным инструментом. Требования к твёрдости материала детали требуют
осуществления термообработки. Поэтому целесообразно предварительные операции
выполнить до термообработки, что улучшит условия работы инструмента, позволит
назначить более интенсивные режимы резания. Окончательные операции следует
выполнять после термообработки, так как термообработка ухудшает качество
поверхности, достигнутое на предыдущих операциях, а после термообработки
увеличится твёрдость материала детали, что улучшит условия работы абразивного
инструмента.
Так как отверстия 5 и 6 (рисунок 1.1) окончательно обрабатываются осевым
лезвийным инструментом, то эта обработка должна происходить до термообработки
для улучшения условий термообработки. Плоскость 3 служит базой для обработки
отверстий 5,6, паза 5 и контура 4 и поэтому должна быть обработана до их
обработки.
Так как поверхности 5,6 и 7 обрабатываются от одних и тех - же баз,
целесообразно объединить их обработку на одной операции.
Предварительную обработку поверхностей 1 и 2 целесообразно разделить на
две операции, так как в противном случае из-за повышенного износа режущего
инструмента при обдирке ухудшится качество поверхности и снизится стабильность
размеров на последующих переходах.
Учитывая особенности выбранного среднесерийного типа производства
выбираем последовательную структуру операции с позиции выполняемых переходов,
так как это упростит наладку станков, позволит использовать переналаживаемую
оснастку и универсальный инструмент, что позволит применить групповую
обработку.
Для среднесерийного производства следует выбирать универсальное
переналаживаемое оборудование, которое позволит применить групповой принцип
организации производства, что обеспечит высокую загрузку оборудования.
На операции 005, 010, 015 принимаем горизонтально-фрезерный станок 6Р82.
На операцию 020 принимаем плоскошлифовальный станок 3Б724.
На операции 025 и 030 принимаем вертикально-фрезерный станок 6Н13МФ3-2.
На операции 035 и 040 принимаем вертикально-фрезерный станок 6Р12.
На операции 050 и 055 принимаем плоскошлифовальный станок 3Б724.
В серийном производстве следует стремиться применять переналаживаемую
оснастку, если этому не препятствует форма, размеры и другие технические
требования детали.
На операциях 010 и 015 следует применять специальное приспособление,
которое позволит надёжно закреплять на станке заготовку сложной конфигурации,
будет обладать быстродействующим механизмом зажима заготовки, обеспечит удобную
установку, съём заготовки и уборку стружки.
На операциях 30 и 35 необходимо применение специальных приспособлений,
так как иначе невозможно выдержать технические требования, предъявляемые
чертежом.
На операции 020, 040 и 045 принимаем тиски станочные с пневматическим
приводом по ГОСТ 1409-80.
Расчёт режимов резания на операцию 001 Горизонтально-фрезерную. Принимаем
фрезу цилиндрическую 2200-0209 по ГОСТ 3752-59 тип 2 [7, с. 323]. Диаметр фрезы
100 мм, длинна 160 мм, число зубьев - 12, материал режущей части - Р18.
Операция выполняется на станке 6Р12. Назначаем и определяем режимы резания по
[6, т2, с.281]:
Определим скорость резания по формуле 1.11:
для
ранее выбранных и определённых величин найдём значения коэффициентов в формуле:
Подставив
найденные значения в формулу 1.11 получим:
Скорректируем
скорость резания в соответствии с возможностями станка. Найдём число оборотов,
соответствующее найденной скорости резания:
Выбранный
станок имеет 18 скоростей вращения шпинделя и диапазон 31.5-1600 об/мин. Найдём
знаменатель геометрического ряда:
Окончательно
примем ближайшую меньшую скорость вращения шпинделя из найденного
геометрического ряда ряда n=200 об/мин. Для принятой скорости вращения шпинделя
скорость резания составит:
Выбранный
станок имеет 18 скоростей продольных и поперечных подач и диапазон 25-1250
мм/мин. Найдём знаменатель геометрического ряда:
Окончательно
примем ближайшую меньшую скорость подачи из найденного геометрического ряда: Sмин=250м/мин.
Для принятой минутной подачи подача на зуб составит:
По
приняты данным найдём силу резания Pz по формуле 1.12 [6, т2, с.
282]:
По
[6, т2, с. 291, табл. 41] назначим входящие в формулу величины:
Подставим
найденные значения в формулу:
Найдём
эффективную мощность резания по формуле 1.13 [6, т2, с. 290]:
подставим
в формулу необходимые величины:
Выполнение
операции на выбранном станке возможно, так как эффективная мощность меньше
мощности электродвигателя главного привода.
Расчёт
режимов резания на операцию 015 Вертикално-фрезерную с ЧПУ. Принимаем развёртку
машинную из быстрорежущей стали Р18 диаметром 13мм и коническим хвостовиком
(Морзе 1) 2360-0119 ГОСТ [7, с. 309]. Число зубьев - 8, материал режущей части
- Р18. Операция выполняется на станке 6Р11Ф3-1. Назначаем и определяем режимы
резания по [6, т2, с.281]:
Определим
скорость резания по формуле 1.14:
для
ранее выбранных и определённых величин найдём значения коэффициентов в формуле:
Подставив
найденные значения в формулу 1.14 получим:
Найдём
скорость вращения шпинделя, соответствующую рассчитанной скорости резания:
Скорректируем
найденную скорость вращения шпинделя в соответствии и возможностями выбранного
станка. Найдём знаменатель геометрического ряда скоростей шпинделя:
Для
данного знаменателя геометрического ряда ближайшее меньшее значение скорости
вращения составит n=315об/мин. Найдём действительную скорость резания:
Найдём
крутящий момент развёртывания по формуле 1.15:
Выберем
входящие в формулу величины по [6, т2, с. 273]:
Подставим
найденные значения в формулу:
Найдём
мощность резания по формуле 1.16 [6, т2, с. 273]:
Подставив
в формулу значения, получим:
Выполнение
операции на выбранном станке возможно, так как эффективная мощность резания
меньше мощности электродвигателя главного привода.
Рассчитаем нормы времени на операцию 010 Горизонтально-фрезерную. Затраты
времени Т шт на выполнение операции определяются по формуле 1.17 [9]:
Где
n - количество деталей в партии, обрабатываемой с одной
наладки станка, определяется по формуле 1.18:
Где
N зм -
месячная программа запуска деталей, с учётом годовой программы в 950 деталей,
принимаем N зм =80
деталей в месяц;
a - необходимый
запас для обеспечения непрерывной работы сборочного цеха, принимаем a=4
дня;
F эф - эффективный месячный фонд времени работы в днях, F эф =20 дней.
Подставив
значения в формулу, получим:
Т шт
- штучное время определяется по формуле 1.19:
Где
Т о - основное время на выполнение операции, определяется выражением
1.20:
Где
Т о i - основное время на выполнение i-го
перехода, для фрезерной обработки определяется по формуле 1.21:
Где
l 1 - длинна
врезания инструмента, мм;
l 2 - длинна перебега инструмента, мм;
L - длинна
обрабатываемой поверхности, мм;
Подставив
в формулу 1.22 известные величины, получим:
Подставив
времена в формулу 1.20 получим:
Т в
- вспомогательное время, затрачивается на переходы, сопутствующие процессу
обработки, по рекомендациям [9] с учётом специального приспособления и модели
станка принимаем Т в = 1,62 минуты.
Т об
- время обслуживания рабочего места и поддержания его в рабочем состоянии.
Согласно [9] принимаем Т об = 0,43 минуты.
Т доп
- время на отдых и личны
1.1 Служебное
назначение детали Курсовая работа (т). Другое.
Реферат: Акцентуации характера в подростовком возрасте. Скачать бесплатно и без регистрации
Диссертация Власть
Дипломные Работы По Кинологии
Реферат по теме Організація охорони праці в Японії
Реферат: Род Перси
Реферат: Arab Music Essay Research Paper Arab MusicThe
Реферат по теме Физическая подготовка юных пловцов на суше
Rainbow English 5 Класс Контрольные Работа
Реферат по теме Банковский кризис 2004 г.: причины возникновения и пути преодоления
Реферат: Епископ Антоний Малецкий. Скачать бесплатно и без регистрации
Характеристика Студента Журналиста С Места Практики
Реферат: Конус. Скачать бесплатно и без регистрации
Советы По Подготовке К Итоговому Сочинению
Сочинение По Картине Остроухова Золотая
Курсовая работа: Формирование товарного ассортимента предприятий розничной торговли
Курсовая работа по теме Адвокат в суде Росийской Федерации с участием присяжных заседателей
Курсовая работа по теме Эмиссия ценных бумаг коммерческими банками и ее роль в формировании ресурсов банка (активы, их состав, структура)
Доклад по теме Мышление и ответственность
Мультимодальные И Интермодальные Перевозки Реферат
Учебное пособие: Учебно-методическое пособие по выполнению курсовой работы Гомель 2010
Похожие работы на - Образование и эволюция Земли