Ремонт тормозной системы КАМАЗ. Курсовая работа (т). Транспорт, грузоперевозки.
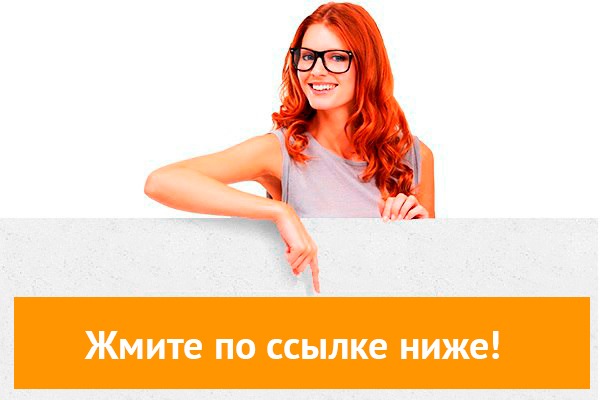
💣 👉🏻👉🏻👉🏻 ВСЯ ИНФОРМАЦИЯ ДОСТУПНА ЗДЕСЬ ЖМИТЕ 👈🏻👈🏻👈🏻
Вы можете узнать стоимость помощи в написании студенческой работы.
Помощь в написании работы, которую точно примут!
Похожие работы на - Ремонт тормозной системы КАМАЗ
Скачать Скачать документ
Информация о работе Информация о работе
Скачать Скачать документ
Информация о работе Информация о работе
Скачать Скачать документ
Информация о работе Информация о работе
Скачать Скачать документ
Информация о работе Информация о работе
Скачать Скачать документ
Информация о работе Информация о работе
Скачать Скачать документ
Информация о работе Информация о работе
Скачать Скачать документ
Информация о работе Информация о работе
Нужна качественная работа без плагиата?
Не нашел материал для своей работы?
Поможем написать качественную работу Без плагиата!
. Исходные
данные для расчета технических показателей задания
.1 Организация
и технология ремонта тормозной системы КАМАЗ
.2 Испытание
тормозной системы КАМАЗ
.4 Определение
годовых трудоемкостей
.5 Определение
сменных трудоемкостей
.6 Определение
сменных программ
.7 Определение
количества рабочих в цехе
.8 Определение
площадей цехов и зон
.9 Распределение
рабочих по квалификации и определение квалификационных характеристик
.1 Общие
требования безопасности
.2 Требования
безопасности перед началом работы
.3 Требования
безопасности во время работы
.4 Требования
безопасности в аварийных ситуациях
.5 Требования
безопасности по окончании работы
В удовлетворении постоянно растущих потребностей
народного хозяйства нашей страны в перевозках пассажиров и грузов автомобильный
транспорт занимает ведущее место.
Решение задач по дальнейшему развитию
автомобильного транспорта обеспечивается постоянным увеличением производства
автомобилей. Одним из резервов увеличением автомобильного парка страны является
ремонт автомобилей, поэтому его развитию и совершенствованию в нашей стране
уделяется большое внимание.
В процессе эксплуатации автомобиля его
надежность и другие свойства постепенно снижаются вследствие изнашивания
деталей, а также коррозии и усталости материала, из которого они изготовлены. В
автомобиле появляются различные неисправности, которые устраняются при
техническом обслуживании и ремонте.
При длительной эксплуатации автомобили достигают
такого состояния, когда затраты средств и труда, связанные с поддержанием их в
работоспособном состоянии и условиях автотранспортных предприятий, становится
больше прибыли, которую они приносят в эксплуатации. Такое техническое
состояние автомобилей считается предельным и они направляются в капитальный
ремонт на авторемонтные предприятии. Задача капитального ремонта состоит в том,
чтобы с наименьшими затратами восстановить утраченную автомобилями
работоспособность.
Существенное значение для решения проблемы
управления техническим состоянием автомобиля имеет планово-предупредительная
система ТО и ремонта подвижного состава, регламентирующая режимы и другие
нормативы по его содержанию в технически исправном состоянии. Важным элементом
решения проблемы управления техническим состоянием автомобилей и другого
специализированного оборудования является совершенствование технологических
процессов и организации производства ТО и ремонта автомобилей и оборудования,
включающее рационализацию структуры инженерно-технической службы, методов
принятия инженерных решений, технологических приемов, оборудования постов и
рабочих мест и научную организацию труда (НОТ).
Современное авторемонтное производство
располагает в настоящее время механизированными поточными линиями
разборки-сборки, совершенными способами ремонта деталей, высокопроизводительным
оборудованием, прогрессивными технологическими процессами. Основным источником
повышения производительности труда при капитальном ремонте автомобилей и
агрегатов является механизация и автоматизация производственных процессов на
основе концентрации производства. При этом особенно механизация разборочных,
моечных, дефектовочных и сборочных работ имеет первостепенное значение, т.к.
при этом также значительно повышается культура производства и как следствие
качество ремонта. Важное значение также имеет механизация трудоемких процессов
внутрицехового и межоперационного транспортирование автомобилей, агрегатов и
деталей, т.к. они оказывают непосредственное влияние на снижение себестоимости
и значительно облегчают труд рабочих.
Все эти направления определяют пути и методы
наиболее эффективного управления техническим состоянием автомобильного парка с
целью обеспечения регулярности и безопасности перевозок при наиболее полной
реализации технических возможностей конструкции и обеспечении заданных уровней
эксплуатационной надежности автомобиля, оптимизации материальных и трудовых
затрат, сведении к минимуму отрицательного влияния технического состояния
подвижного состава на персонал и окружающую среду.
2. Исходные данные для расчета
технических показателей задания
Таблица 1: Данные для расчета технических
показателей задания
Продолжительность
выпуска и возвращения в парк
.1 Организация и технология ремонта
тормозной системы КАМАЗ
Для повышения безотказности и надежности работы
тормозной системы ремонт ее приборов производится на специальном оборудовании
лицами, прошедшими необходимую специальную подготовку.
Принудительному ремонту и контрольным испытаниям
после ремонта подлежат тормозной механизм, тормозные камеры и
энергоаккумуляторы, компрессор, регулятор давления, регулятор тормозных сил,
одинарный, двойной и тройной защитные клапаны, ручной тормозной кран,
двухсекционный тормозной кран, клапаны ограничения давления, ускорительный
клапан и клапан управления тормозами прицепа, кран пневматический.
Основными операциями технологического процесса
ремонта приборов пневматической тормозной системы автомобилей семейства КамАЗ
являются наружная мойка приборов, разборка приборов тормозной системы, чистка и
мойка деталей, дефектация деталей, замена резинотехнических изделий и
неисправных деталей, сборка приборов и их испытание.
Ремонт передних и задних тормозных камер КАМАЗ
Ремонт тормозных камер средних и задних мостов
типа 20 отличается от ремонта передних тормозных камер типа 24.
Для снятия тормозной камеры с пружинным
аккумулятором с автомобиля необходимо:
Ø установить ручной тормозной кран в
положение «стояночный тормоз»;
Ø вывернуть до упора болт
механического растормаживания пружинного энергоаккумулятора, убедившись, что
шток тормозной камеры убран;
Ø отсоединить подводящие трубопроводы,
ослабить крепление тормозной камеры, отсоединить вилку штока от регулировочного
рычага.
После выполнения указанных операций снять
тормозную камеру.
Разборка энергоаккумулятора, показанного на рис.
1, б, производится на специальном стенде. Разборка энергоаккумуляторов вне
стенда категорически запрещается. При ослаблении винта пружина разжимается с
усилием 0,62-0,65 МПа и вылетает из цилиндра. Сущность работы приспособления
для разборки энергоаккумулятора состоит в том, чтобы после отвинчивания гайки
винта плавно разжать пружину.
Рис. 1 Тормозные камеры пневматической системы
автомобиля КамАЗ:
а - тормозная камера тормозов переднего моста
типа 24; 1 - бобышка; 3 - диафрагма; 4 - диск; 5 - пружина; 6 - хомут; 7 -
шток; 8 - корпус; 9 - фланец; 10 - гайка; 11 - защитный чехол; 12 - вилка; 13 -
болт; 14 - подвод сжатого воздуха; б - тормозная камера тормозов задней тележки
типа 20; 1 - корпус тормозной системы; 2 - подпятник; 3 - уплотнительное кольцо;
4 - толкатель; 5 - поршень; 6 - уплотнение поршня; 7 - цилиндр
энегоаккумулятора; 8 - силовая пружина; 9 - винт механизма аварийного
растормаживания; 10 - упорная гайка; 11 - патрубок цилиндра; 12 - дренажная
трубка; 13 - упорный подшипник; 14 - фланец; 15 - патрубок тормозной камеры; 16
- диафрагма тормозной камеры; 17 - опорный диск; 18 - шток; 19 - возвратная
пружина
При капитальном ремонте тормозного механизма
заменяются новыми:
Ø резиновые уплотнительные кольца разжимного
кулака в кронштейне; после их замены уплотнительные кромки кольца не должны
иметь каких-либо повреждений;
Ø металлопластмассовые втулки
разжимного кулака, усилие запрессовки втулок должно быть не менее 6000 Н; после
замены втулки растачиваются до диаметра 38,0-38,027 мм;
Ø фрикционные тормозные накладки
колодок тормоза.
Новые фрикционные накладки приклепываются к
колодкам тормоза на специальном прессе, приспособленном для клепки тормозных
накладок. Клепка накладок к колодке должна быть выполнена таким образом, чтобы
зазор между накладками и колодкой в районе заклепок отсутствовал. Тормозные
колодки с накладками в сборе обрабатываются (обтачиваются) под диаметр
расточенного тормозного барабана на станке, показанном на рис. 2. Радиус
колодок с фрикционными накладками должен быть 199,6-200 мм.
Рис. 2. Станок для расточки тормозных барабанов
и обточки тормозных колодок: 1 - станина станка; 2 - маховик поперечного
перемещения суппорта; 3 - суппорт станка; 4 - резцедержатель; 5 - конусы для
установки ступицы тормозного барабана; 6 - оправка с зажимной ганкой конусов; 7
- шпиндель станка; 8 - рукоятка переключения передач в коробке скоростей
шпинделя; 9 - рукоятка переключения подач, 10 - рукоятка продольной подачи суппорта
Для обточки колодок на станке изготавливается
приспособление для их крепления. Приспособление с закрепленными на нем
тормозными колодками устанавливается на шпиндель станка.
Тормозные барабаны после мойки и очистки
подвергаются дефектации. При выработке рабочей поверхности более 1 мм
растачиваются на станке для расточки тормозных барабанов, показанном на рис. 2.
В верхней части станины 1 станка расположен
шпиндель 7, привод шпинделя осуществляется через ременную передачу от
электромотора. В шпинделе станка закреплена оправка 6. На оправке установлены
два конуса 5, которые являются базовыми поверхностями для наружных обойм
подшипников ступицы колеса. Для расточки барабан приворачивается гайками к
ступице. Вместе со ступицей барабан устанавливается на конусные оправки станка.
На боковой стороне станины имеются направляющие для установки и перемещения
суппорта 3. В суппорте закрепляется резцедержатель 4 для крепления резца.
Поперечное перемещение суппорта с
резцедержателем по направляющим суппорта осуществляется маховиком 2. Продольное
перемещение суппорта с резцедержателем по направляющим станины осуществляется
рукояткой 10. Для расточки тормозных барабанов применяются резцы с
твердосплавными пластинами ВК-3, ВК-б. Барабан вращается на шпинделе станка. Скорость
резания в пределах 80-100 м/мин.
При расточке тормозных барабанов внутренний их
диаметр не должен превышать 406 мм. Для колес одной оси автомобиля диаметры
тормозных барабанов должны быть одинаковы.
Разжимной кулак подвергается восстановлению,
если на рабочем профиле его имеются выработки, коррозия, выбоины, вмятины
глубиной до 0,5 мм. Разница радиусов профиля на одноименном луче не должна
превышать 0,6 мм. Восстановление рабочей поверхности разжимного кулака
производится наплавкой или плазменным напылением с последующей механической
обработкой. Шлицы разжимного кулака не должны иметь следов выработки.
При сборке тормозного механизма все трущиеся
поверхности деталей (опорные поверхности разжимного кулака, ролик, оси ролика и
опорные оси колодок) смазываются тонким слоем смазки «Литол-24». Кроме того,
разжимной кулак дополнительно смазывается через пресс-масленку, находящуюся в
кронштейне. Попадание смазки на поверхность трения колодок не допускается.
После сборки тормозного механизма на ступицу устанавливается тормозной барабан
и производится регулировка затяжки подшипников ступиц колес.
Заключительной операцией ремонта тормозного
механизма является полная его регулировка. Полная регулировка тормозных
механизмов всех колес осуществляется в следующей последовательности. После
ослабления гайки 4 крепления осей 1 тормозных колодок сближаются эксцентрики,
их оси поворачиваются таким образом, чтобы метки, поставленные на наружных,
выступающих под гайками торцах осей находились одна против другой. После этого
отпускаются болты крепления кронштейна разжимного щитка 3.
В тормозную камеру подается сжатый воздух под
давлением 0,1-0,15 МПа и замеряется выход штоков тормозных камер. Величина
выхода штока определяется разностью замеров полного его выхода после подачи
воздуха в тормозную камеру и положением его в исходном состоянии. Разность
полученных результатов должна быть 20-30 мм. Если величина хода штока будет
отличаться от указанной, то ее следует регулировать вращением оси 1 (18)
червяка регулировочного рычага 3 (14).
Рис. 3. Тормозной механизм колесного тормоза
автомобиля КамАЗ: а - расположение регулировочного рычага тормозного механизма
и окна в тормозном диске для проверки зазоров между тормозными колодками и
барабаном: 1 - ось червяка с четырехгранной головкой для вращения червяка при
регулировке хода штока тормозной камеры; 2 - окно для проверки зазоров между
тормозными колодками и барабаном; 3 - рычаг вала разжимного кулака; 4 -
соединительная ось; 5 - вилка штока тормозной камеры; б - поперечный разрез
тормозного механизма: 1 - ось эксцентрика тормозной колодки; 2 - диск
тормозного механизма, жестко закрепленный на фланце моста; 3 - щиток; 4 - гайка
оси; 5 - накладка оси колодок; 6 - чека оси колодки; 7 - колодка тормоза; 8 -
пружина; 9 - фрикционная накладка; 10, 21 - кронштейн разжимного кулака; 11 -
ось ролика; 12, 16 - разжимный кулак; 13 - ролик; 14 - регулировочный рычаг; 15
- ось разжимного кулака; 17 - тормозная колодка (внутренний вид); 18 -
регулировочная головка вала червяка; 19 - фиксатор положения вала червяка; 20 -
пружина фиксатора; 22 - червяк; 23 - заглушка; 24 - шестерня вала разжимного
кулака; 25 - шлицованный наконечник вала разжимного кулака
Для одновременного торможения правых и левых
колес ход штоков тормозных камер одной оси должен быть одинаковым.
Барабан должен вращаться свободно, не касаясь
колодок. После регулировки между барабаном и колодками должны быть зазоры: у
разжимного кулака - 0,4 мм; у осей колодок - 0,2 мм.
Величина хода штока тормозных камер замеряется
линейкой.
Мерная линейка устанавливается торцом в корпус
тормозной камеры ближе к штоку и параллельно ему. Положение крайней точки штока
отсчитывается по шкале линейки. Нажимается тормозная педаль до упора (при
нормальном давлении воздуха в системе) и отмечается новое положение крайней
точки штока.
Регулировка свободного и рабочего хода педали
рабочего тормоза производится в следующей последовательности. Масштабная линейка
устанавливается торцом в пол кабины рядом с педалью тормоза перпендикулярно к
верхней ее плоскости. На шкале линейки фиксируется местонахождение верхней
плоскости педали. Плавно нажимается на тормозную педаль до момента начала
выдвижения штоков тормозных камер. Снова измеряется местонахождение верхней
плоскости педали. Разность полученных результатов дает величину хода педали
(25-30 мм).
Рис. 4. Слив конденсата из воздушных баллонов: а
- общий вид; б - разрез клапана для слива конденсата; 1 - шток клапана слива
конденсата; 2 - пружина; 3 - корпус; 4 - опорное кольцо; 5 - шайба; 6 - клапан
Нажимается тормозная педаль до упора и таким же
образом определяется величина рабочего хода. Ход педали должен быть 75-100 мм и
ограничиваться упорным винтом в двухсекционном тормозном кране, а не полом
кабины. Если свободный и рабочий ход педали не соответствует норме, то он
регулируется вилкой тяги педали, навинчивая ее на тягу педали или свинчивая ее
с тяги, предварительно отсоединив от нижнего рычага педали.
Слив конденсата из воздушных баллонов
производится следующим образом. При работающем двигателе давление воздуха в
системе доводится до 0,7 МПа; открываются сливные краны на каждом из пяти
баллонов оттягиванием штока за кольцо или цепочку в сторону, как показано на
рис. 4; после полного слива конденсата из баллона выпускается воздух без
капелек жидкости. После слива конденсата система заполняется воздухом. Давление
воздуха в системе доводится до номинального и только после этого
останавливается двигатель.
Наличие масла в конденсате указывает на
неисправность компрессора.
Место утечки воздуха обнаруживается на слух или
с помощью мыльного раствора, которым смачивается место предполагаемой утечки.
.2 Испытание тормозной системы КАМАЗ
Полное регулирование тормозного механизма
проводите после замены тормозных накладок в следующем порядке:
Ø выключить стояночную тормозную
систему;
Ø ослабить гайки крепления осей
колодок и сблизить эксцентрики, повернув оси метками друг к другу. Метки
поставить на наружных торцах осей;
Ø подать в тормозную камеру сжатый
воздух под давлением 49... 68,8 кПа (0,5... 0,7 кгс/см2) (нажать тормозную
педаль при наличии воздуха в системе или использовать сжатый воздух из
установки). При отсутствии сжатого воздуха вынуть палец штока тормозной камеры
и, нажимая регулировочный рычаг в сторону хода штока тормозной камеры при
торможении, прижмите колодки к тормозному барабану. Поворачивая эксцентрики в
ту и другую стороны, сцентрировать колодки относительно барабана, обеспечив
плотное прилегание их к барабану. Прилегание колодок к барабану проверить щупом
через окна в тормозном щитке, расположенные на расстоянии 20... 30 мм от
наружных концов накладок. Щуп толщиной 0,1 мм не должен проходить вдоль всей
ширины накладки;
Ø не прекращая подачи сжатого воздуха
в тормозную камеру, а при отсутствии сжатого воздуха не отпуская
регулировочного рычага и удерживать оси колодок рт проворачивания, надежно
затянуть гайки осей;
Ø прекратить подачу сжатого воздуха, а
при отсутствии сжатого воздуха отпустить регулировочный рычаг и присоединить
шток тормозной камеры;
Ø повернуть оси червяка
регулировочного рычага так, чтобы ход штока тормозной камеры был 20... 30 мм.
Убедиться, что при включении и выключении подачи воздуха штоки тормозных камер
перемещаются быстро, без заеданий;
Ø проверить вращение барабанов. Они
должны вращаться свободно и равномерно, не касаясь колодок. После указанной
регулировки между тормозным барабаном и колодками могут быть следующие зазоры:
у разжимного кулака 0,4 мм, у осей колодок 0,2 мм.
При установке регулятора тормозных сил после
замены промежуточного и заднего мостов необходимо обратить внимание на то,
чтобы регулятор и штанга, соединяющая рычаг регулятора с упругим элементом,
были установлены вертикально, упругий элемент должен быть в горизонтальном
положении (нейтральном). Установив необходимую длину рычага, затянуть болт
крепления рычага на регуляторе. После установки проверить выходное давление
регулятора тормозных сил. Для этого пневмосистему заполнить сжатым воздухом до
контрольного давления, равного 637,5 кПа (6,5 кгс/см2). При полностью
нажатой педали давление в клапане контрольного вывода Е должно быть 215,8...
245,2 кПа (2,2... 2,5 кгс/см2) (для порожнего автомобиля). Если в клапане
вывода давление отличается от указанного, то привести его в соответствие
изменением длины вертикальной штанги, перемещая ее в резиновой соединительной
муфте. Проверить стабильность выдаваемого регулятором тормозных сил давления,
нажимая неоднократно тормозную педаль, после чего затянуть хомут на
соединительной муфте.
Поднять наконечник упругого элемента на величину
статического прогиба подвески, убедиться, что давление в тормозных камерах
задней тележки стало равно контрольному давлению, т.е. 588,4 кПа (6 кгс/см2);
если этого не происходит, откорректироватье длины рычага и штанги. При этом
необходимо помнить, что штанга должна входить в соединительную муфту регулятора
на глубину не менее 45 мм. Окончательно закрепить все соединения.
При снятии тормозной камеры с пружинным
энергоаккумулятором:
установить ручной тормозной кран в положение
«стояночный тормоз»;
вывернуть до упора болт механического
растормаживания пружинного энергоаккумулятора, убедиться при этом, чтобы шток
тормозной камеры убрался; отсоединить проводящие трубопроводы, ослабить
крепление тормозной камеры, отсоединить вилку штока от регулировочного рычага;
Определение коэффициентов корректирования
пробегов до ТО и трудоемкости ТР
а) Категория условий эксплуатации (КУЭ),
принимаем К 1 =0,9, К 2 =1,1 (определяем по таблице №3
методических рекомендаций)
б)Климатические условия эксплуатации, принимаем
К 3 = 1 (определяем по таблице №4 методических рекомендаций)
Корректируем нормативные пробеги до ТО-1 и ТО-2
где -
нормативный пробег до ТО-1=4000 или ТО-2=15000 (определяем по таблице №2
методических рекомендаций)
- коэффициентные
корректирования К 1 =0,9, К 3 =1 (определяем по таблице №3 и
№4 методических рекомендаций)
Корректируем периодичностьТО-1 по крайности к
среднесуточному пробегу
где -
коэффициент кратности периодичности ТО-1,
Определяем расчетную периодичность ТО-1 по
формуле:
Корректируем периодичность ТО-2 по кратности к
периодичности ТО-1
Определяем расчетную периодичность ТО-2 по
формуле:
Определяем пробег до капитального ремонта
- нормативный
пробег до кр (определяем по
таблице №6 методических рекомендаций
Определяем величину кратности капитальных
ремонтов по ТО-1
где -
пробег до КР скорректированный;
Определяем расчетный пробег до капитального
ремонта по формуле:
где -
скорректированный пробег до ТО-1
Определение годового пробега АТП производим по
формуле:
- количество дней
работы в году на предприятии; дн.
- коэффициент
выпуска автомобилей, - принимаем
среднюю величину 0,9;
- коэффициент
технической готовности парка, принимаем среднюю величину 0,93;
Определяем количество ТО-1 - в год по формуле:
Определяем количество ТО-2 в год по формуле:
где -
расчетный пробег до ТО-2; - количество ТО-2
в год
Определяем количество КР в год по формуле:
где -
расчетный пробег до капитального ремонта.
Определяем количество ТО-1 в смену по формуле:
где -
количество рабочих дней в году (задание); -
количество ТО-1 в год
Определяем количество ТО-2 в смену по формуле:
4.4 Определение годовых
трудоемкостей
Определяем нормативную трудоемкость ТО-1 в год
по формуле:
где -
общая трудоемкость ТО-1 в год
- трудоемкость
ТО-1 (определяем по таблице №8 методических рекомендаций.)
Определение нормативной трудоемкости ТО-2 в год
производим по формуле:
где -
трудоемкость ТО-2 (определяем по таблице №8 методических рекомендаций.)
Определяем нормативную трудоемкость ТР в год
где -
нормативная трудоемкость ТР на 1000 км пробега. (%)
Определим скорректированную трудоемкость ТО-1 в
год
где -
коэффициент корректированной трудоемкости (определяем по таблице №3
методических рекомендаций.)
-климатические
условия (определяем по таблице №4 методических рекомендаций.)
- коэффициент
учитывающий пробег с начала эксплуатации (определяем по таблице №5 методических
рекомендаций)
Определим скорректированную трудоемкость ТО-2 в
год по формуле:
где -
нормативная трудоемкость ТО-2 в год
-( определяем по
таблице №8 методических рекомендаций.)
Определим скорректированную трудоемкость ТР в
год
где -
нормативные трудоемкости ТР в год (определяем по таблице №7 методических
рекомендаций.)
.5 Определение сменных трудоемкостей
Определяем суточную трудоемкость ТО-1
где -
годовая скорректированная трудоемкость ТО-1;
Определяем суточную трудоемкость ТО-2
где -
годовая скорректированная трудоемкость ТО-2;
Определяем суточную трудоемкость ТР
- трудоемкость
1-го ТО-1 (определяем по таблице №7 методических рекомендаций.);
- трудоемкость
1-го ТО-2 (определяем по таблице 7 методических рекомендаций.);
.7 Определение количества рабочих в
цехе
Определение количества рабочих в цехе производим
по формуле:
- коэффициент
использования рабочего времени, принимаем 0,92.
Определяем трудоемкость работ в цехе (суточную)
где -
сумма % к ТР по видам работ в цехе. (определяем по таблице №9 методических
рекомендаций)
4.8 Определение площадей цехов и зон
Для более эффективной работы принимаем условие
при которых 1 рабочий работает на 1 посту
Определяем площадь цехов и участков
где -
площадь занимаемая автомобилем (м 2 );
- количество
постов в зоне (шт.); 10 шт
- площадь
оборудования суммарная (м 2 ); м 2
- коэффициент
плотности расстановки оборудования (определяем по таблице №11 методических
рекомендаций).
4.9 Распределение рабочих по
квалификации и определение квалификационных характеристик
Участок предназначен для ремонта тормозной
системы автомобиля КАМАЗ а также для их и испытания общей площадью 841 м 2
В цехе выполняются следующие работы: разборка, дифектовка и комплектовка
аппаратов, сборка тормозной аппаратуры, а также испытания тормозной аппаратуры.
Режим работы участка по ремонту тормозной
системы односменный. Планировка участка с расстановкой оборудования приведена
на листе формата А1
Благодаря расчетам определено количество рабочих
равное 10 человек. Приняты тарифно-квалификационные характеристики для рабочих
3 и 4 разряд описание которых приведены в пункте 4.9.2.
Проектирование цеха по ремонту тормозной системы
КАМАЗ, позволяет получить следующие преимущества: эффективнее использовать
высокопроизводительное оборудование; повысить надежность восстановленных
изделий, снизить потребность в новых узлах и аппаратах тормозной системы, а так
же уменьшить материальные расходы на запчасти и ремонт, представить возможность
определить коэффициент сменности практически для всех узлов и аппаратов
тормозных систем и тем самым правильно планировать потребность в запасных
частях и сменных узлах и аппаратах; создать возможность совершенствовать
производственные навыки и специализацию исполнителей; повысить
производительность и качество ремонта.
При расстановке оборудования и оснастки нужно
руководствоваться размерами (разрывами) между ними и расстояниями от стен и
колонн. Эти размеры должны гарантировать удобство работ, безопасность рабочих,
достаточную свободу движения людей.
Расстояние между оборудованием регламентируется
правилами охраны труда и существующими нормативами, которые учитывают удобство
и безопасность при их эксплуатации.
При компоновке участка нужно согласовать его с
противопожарными, санитарно-гигиеническими и другими нормами.
Каждый вид оборудования имеет условное
обозначение, форма которого соответствует его контурам на плане, а размеры
габаритам в соответствующем масштабе.
В целях пожарной безопасности имеются
огнетушители, пожарные щиты с необходимым оборудованием и ящики с песком. Для
оказания первой медицинской помощи при травмах участок оборудован аптечкой.
.9.2 Тарифно-квалификационная
характеристика
Характеристика работ.
Разборка дизельных и специальных грузовых автомобилей и автобусов длиной свыше
9,5 м. Ремонт, сборка грузовых автомобилей, кроме специальных и дизельных,
легковых автомобилей, автобусов длиной до 9,5 м. Ремонт и сборка мотоциклов,
мотороллеров и других мототранспортных средств. Выполнение крепежных работ
резьбовых соединений при техническом обслуживании с заменой изношенных деталей.
Техническое обслуживание: резка, ремонт, сборка, регулировка и испытание
агрегатов, узлов и приборов средней сложности. Разборка агрегатов и
электрооборудования автомобилей. Определение и устранение неисправностей в
работе узлов, механизмов, приборов автомобилей и автобусов. Соединение и пайка
проводов с приборами и агрегатами электрооборудования. Слесарная обработка
деталей по 11-12 квалитетам с применением универсальных приспособлений. Ремонт
и установка сложных агрегатов и узлов под руководством слесаря более высокой
квалификации.
Должен знать:
устройство и назначение узлов, агрегатов и приборов средней сложности; правила
сборки автомобилей и мотоциклов, ремонт деталей, узлов, агрегатов и приборов;
основные приемы разборки, сборки, снятия и установки приборов и агрегатов
электрооборудования; регулировочные и крепежные работы; типичные неисправности
системы электрооборудования, способы их обнаружения и устранения; назначение и
основные свойства материалов, применяемых при ремонте электрооборудования;
основные свойства металлов; назначение термообработки деталей; устройство
универсальных специальных приспособлений и контрольно-измерительных
инструментов; систему допусков и посадок; квалитеты и параметры шероховатости.
. Автомобили легковые, грузовые, автобусы
всех марок и типов - снятие и установка бензобаков, картеров, радиаторов,
педалей тормоза, глушителей, замена рессор.
. Валы карданные, цапфы тормозных
барабанов - подгонка при сборке.
. Вентиляторы - разборка, ремонт, сборка.
. Головки блоков цилиндров, шарниры
карданов - проверка, крепление.
. Головки цилиндров самосвального
механизма - снятие, ремонт, установка.
. Двигатели всех типов, задние, передние
мосты, коробки передач, кроме автоматических, сцепления, валы карданные -
разборка.
. Крылья легковых автомобилей - снятие,
установка.
. Насосы водяные, масляные, вентиляторы,
компрессоры - разборка, ремонт, сборка.
. Обмотки изоляционных приборов и
агрегатов электрооборудования - пропитка, сушка.
. Реле-регуляторы, распределители
зажигания - разборка.
. Седла клапанов - обработка шарошкой,
притирка.
. Фары, замки зажигания, сигналы -
разборка, ремонт, сборка.
Характеристика работ.
Ремонт и сборка дизельных, специальных грузовых автомобилей, автобусов,
мотоциклов, импортных легковых автомобилей, грузовых пикапов и микроавтобусов.
Разборка, ремонт, сборка сложных агрегатов, узлов и приборов и замена их при
техническом обслуживании. Обкатка автомобилей и автобусов всех типов на стенде.
Выявление и устранение дефек
Похожие работы на - Ремонт тормозной системы КАМАЗ Курсовая работа (т). Транспорт, грузоперевозки.
Контрольная работа по теме Интеллектуальный ресурс современной экономики
Темы Рефератов Введение В Логистику
Реферат по теме Стандартные методы сжатия видеосигналов
Реферат по теме “Оруженосцы нации”: вермахт и части особого назначения СС (1934-1939 гг.)
Реферат: Основные механические характеристики материалов. Скачать бесплатно и без регистрации
Курсовая работа по теме Разработка архитектурно-конструктивного проекта жилого одноквартирного дома
Реферат: Статистическая оценка рынка труда и качества рабочей силы
Курсовая работа по теме Основные проблемы и задачи бюджетной политики
Реферат по теме Метод Винера-Хопфа и его приложения в физических задачах
Контрольная работа по теме Расчет водоподготовительной установки
Реферат: Tarahumara Essay Research Paper The Tarahumara or
Реферат: Red Hat Linux
Реферат Введение Умзч С Оос По Току
Реферат Виды Наказания
Конфликт Дипломная Работа
Курсовая Работа На Тему Психология Цвета В Рекламе
Расчет Электродвигателя Курсовая
Кислотах Реферат
Реферат По Обж На Тему Чс
Контрольная Работа По Математике 10 11 Класс
Реферат: Філософські ідеї Аврелія Августина
Похожие работы на - Менеджмент продуктивности
Реферат: Фразеологизмы русского языка со значением качественной оценки действий и манеры поведения человека