Реферат: Проектирование сушильно-сортировочного цеха участки сушки, сортировки, починки и ребросклеивани
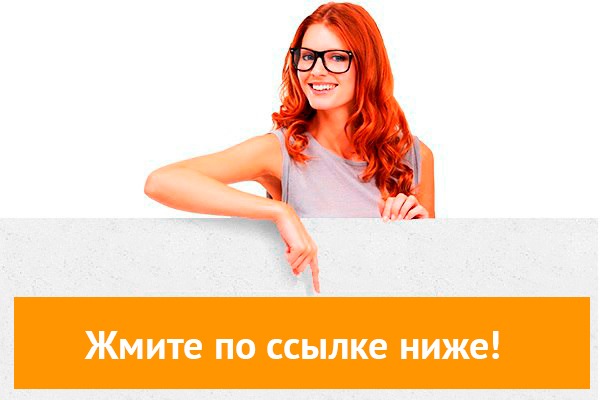
👉🏻👉🏻👉🏻 ВСЯ ИНФОРМАЦИЯ ДОСТУПНА ЗДЕСЬ ЖМИТЕ 👈🏻👈🏻👈🏻
ФЕДЕРАЛЬНОЕ АГЕНСТВО ПО ОБРАЗОВАНИЮ
СЫКТЫВКАРСКИЙ ЛЕСНОЙ ИНСТИТУТ
– ФИЛИАЛ
ГОСУДАРСТВЕННОГО ОБРАЗОВАТЕЛЬНОГО УЧРЕЖДЕНИЯ
ВЫСШЕГО ПРОФЕССИОНАЛЬНОГО ОБРАЗОВАНИЯ
«САНКТ-ПЕТЕРБУРГСКАЯ ГОСУДАРСТВЕННАЯ
ЛЕСОТЕХНИЧЕСКАЯ АКАДЕМИЯ имени С. М. КИРОВА»
ТЕХНОЛОГИЯ КЛЕЕНЫХ МАТЕРИАЛОВ И ДРЕВЕСТНЫХ ПЛИТ
Тема: Проектирование сушильно-сортировочного цеха (участки сушки, сортировки, починки и ребросклеивания шпона).
Проверил: Юрова Ольга Венедиктовна, доцент
1. ВВЕДЕНИЕ……………………………………………………………………………3
ООО «Сыктывкарский фанерный завод»
— один из крупнейших поставщиков фанеры на рынки России, стран СНГ, Европы, Азии и США. Предприятие специализируется на производстве большеформатной фанеры и ламинированной древесностружечной плиты.Ламинированная фанера SyPly™ и ЛДСтП Lamarty завоевали золотые медали на выставке-конкурсе "Всероссийская марка (III тысячелетие). Знак качества XXI век". Ведущим потребителем российской фанеры является Западная Европа, импортировавшая в 2005 году 730 тыс. куб. м этого продукта. Основные страны-импортеры – Италия, Великобритания, Германия, Финляндия, Швеция.
Численность персонала - 1 500 человек.
Проектирование лущильного участка (участки сушки, сортировки, починки и ребросклеивания шпона), изучение в связи необходимости его анализа.
Целью данной курсовой работы является анализ лущильного участка. Задачи работы – сделать технологический расчет лущильного участка, расчет потребного количества сырья и материалов, расчет потребности в оборудовании для выполнения производственной программы и расчет технико-экономических показателей лущильного участка. Ознакомиться со структурой технологического процесса данного участка, а также с применяемым оборудованием.
1.
Исходные данные по выполнению курсового проекта
выпуск в процентах к заданной выработке
количество к общему объему сырья, %
2.
Характеристика продукции марки ФК:
Фанера, склеенная карбамидо-формальдегидными клеями (ФК) - согласно EN636 предназначена для использования в сухих условиях (W* < 65%) и соответствует первому классу биологической стойкости.
* W - параметр относительной влажности атмосферы.
Фанера, при изготовлении которой использован карбамидный клей, является фанерой марки ФК. Аббревиатура ФК расшифровывается так, – Ф-фанера, К-карбамидный клей.
В зависимости от качества шпона наружных слоев, фанеру ФК
разделяют на пять сортов: Е (элита), I, II, III, IV.
По степени обработки поверхности фанеру ФК подразделяют на
: нешлифованную - НШ
; шлифованную с одной стороны - Ш1
; шлифованную с двух сторон - Ш2
.
· Формат в обрезном виде (длина ширина) 1830х1220 мм;
· Толщина, выпуск, в процентах к заданной выработке мм;
· Фанера ФК рекомендуется к использованию в конструкциях и изделиях предназначенных для эксплуатации внутри отапливаемых помещений.
Фанера ФК
является более безвредной, чем фанера ФСФ, так как при ее изготовлении используется клей на фенольной основе. Фанера ФК является легко обрабатываемым материалом и применяется в изготовлении мебели, для внутренней отделки помещений, для устройства полов, в изготовлении тар и упаковок. Так же фанера ФК имеет четкую древесную структуру и благодаря этому качеству она легко вписывается в любой интерьер. Так как фанера ФК имеет среднюю водостойкость, то не рекомендуется использовать ее для внешних отделок.
Фанера ФК
в основном производится из березы, но в нашем случае из сосны.
КФ-МТ
Карбамидный клей представляет собой водный раствор карбамидной смолы. Часто в состав клея входит отвердитель (щавелевая, фталевая, соляная кислоты или некоторые соли) и наполнитель (мука бобовых или злаков, крахмал, древесная мука, гипс и т.п.). Введение в клей аммиачной воды, уротропина, мочевины или меламина позволяет увеличить срок хранения К. к. в 2 раза.
При использовании К. к. горячего отверждения склеиваемые детали в прессе подвергают нагреву. К. к. образуют клеевые соединения, обладающие хорошей механической прочностью [10—13 Мн/м 2
(100—130 кгс/см 2
)] и удовлетворительной стойкостью к действию влаги.
3.
Характеристика сырья и материалов:
· Диаметр чурака, количество к общему объему сырья, % см;
· Сортовой состав сырья I, II, III сортов, % = 40 : 60 : 0
Как правило, хвойная фанера изготовляется из сосны. Свойства этого дерева позволяют сделать привлекательную на вид, лёгкую и особо прочную фанеру, которая активно используется при строительстве и отделке помещений. Наиболее часто фанеру хвойную применяют как основу под полы, для покрытия крыш и обшивки стен, а так же для сооружения перегородок. Фанера хвойная практически не гниёт и имеет большую устойчивость к заражению грибками. Этими свойствами хвойная фанера обладает благодаря пропитанной смолами хвое, склеенной с помощью синтетической смолы (КФ-МТ клей). Клей применяется при холодном склеивании, в него добавляют отвердитель (хлористый аммоний или щавелевая кислота) Хвойную фанеру активно используют при работах по устройству кровель зданий.
Карбамидоформальдегидные
смолы
— это продукт поликонденсациикарбамида с формальдегидом.
В качестве сырья для получения карбамидоформальдегидной смолы могут использоваться:
Мочевина ( карбамид
) — химическое соединение, диамидугольной кислоты. Белые кристаллы, растворимые в полярных растворителях (воде, этаноле, жидком аммиаке).
· карбамидоформальдегидный концентрат
Формалин — водный раствор, содержащий 40% формальдегида, 8% метилового спирта и 52% воды. Источник формальдегида, дезинфицирующее и дезодорирующее средство, жидкость для сохранения анатомических препаратов и дублениякож.
По своему внешнему виду представляет собой суспензию однородного белого цвета, хотя зачастую цвет может варьироваться от белого до светло-коричневого цвета в зависимости от дополнительных включений и срока ее хранения.
1. Массовая доля сухого остатка %, не менее — 51,0
3.Массовая доля свободного формальдегида %, не более 0,3
5.Концентрация водородных ионов (Pн) 7,5-8,5
6.Предельная смешиваемость смолы с водой при которой наблюдается коагуляция, по объему 1:1-1:10
7.Время желатинизации при 100 °C, с, не более 110
Срок годности смолы при надлежащем хранении должен составлять не менее 45 суток с момента изготовления.
4.
Рассчитываем годовую производственную программу клеевого участка цеха фанеры.
Горячий клеильный пресс марки «Китагава»
Производственная программа клеевого цеха составляется на основании расчетов производительности пресса. Марка пресса задана в исходных данных.
Для склеивания фанеры чаще всего используют горячие гидравлические многоэтажные прессы. Техническая характеристика приведена в таб. 8
4.1.
Определение основных технико-экономических показателей работы проектируемого участка
Количество выпускаемой продукции, м 3
/ смен
Количество перерабатываемого сырья, м 3
/ смен
Количество рабочих на участке, чел.
Съем продукции в смену с 1 м 2
площади участка, м 3
/ м 2
4.2.
Расчет производительности клеильного пресса
Производительность пресса для каждого вида фанеры
, П пр
, м 3
/ч, определяется по формуле [3]:
где F
0
– площадь обрезной фанеры заданного формата, м 2
;
n
– число пакетов, склеиваемых в рабочем промежутке пресса;
К и
– коэффициент использования рабочего времени. При расчетах можно принять К и
= 0,95;
t 0
– цикл работы клеильного пресса, с.
Число единичных пакетов, n
, загружаемых в один промежуток пресса, зависит от толщины изготовляемой фанеры.
Цикл работы клеильного пресса складывается из времени, затрачиваемого на ряд операций, и определяется технологией, видом применяемого клея, толщиной склеиваемого пакета, породой древесины, наличием механизмов загрузки и выгрузки, этажностью пресса, организацией работ.
Время, потребное на загрузку пакетов
, t 1
, определяется по формуле:
где l
1
– ход толкателя загрузочной этажерки, мм; 1220 + 80 + 200 = 1500 мм;
u
1
– скорость движения толкателя загрузочной этажерки, мм/с (выбирается из задания, таблица П1.1, приложение 1).
Ход толкателя обычно принимается равным наименьшему размеру листа обрезной фанеры с припусками на обрезку (75 – 80 мм
), увеличенному на 150– 200 мм
.
Время, затрачиваемое на подъем стола пресса
, t 2
, определяется по формуле:
Из приложения 2, таблица П2.2 – Величина упрессовки (%) пакетов шпона при склеивании
. Из таблицы берем оптимальные значения для толщин фанеры равных 9, 12, 15 мм ; марки ФК ; для хвойных пород (по условию) – при толщине 9 = 9; 12 = 10; 15 = 12.
где S ш
- толщина склеиваемого материала, мм; S n
– толщина пакета шпона, помещаемого в один промежуток пресса, мм; у – упрессовка пакета при склеивании, %; n 1
– слойность фанеры.
S ш
– толщину шпона берем из приложения 2, таблица П2.1. Берем для хвойных пород = 1,9 мм. Определяем количество толщин шпона для выработки заданного ассортимента фанеры, выбираем одну толщину;
Полученный результат округляем от четного и выше – в сторону большего нечетного значения.
Время, затрачиваемое на создание рабочего давления на пакет
, t 3
, определяется по формуле:
где t п
– время подъема давления, отнесенное к одному этажу пресса (t п
= 0,2–0,3 с); берем наибольшее значение 0,3
Время выдержки пакетов под давлением
, t 4
, и снижения давления, t 5
, выбираем по таблицам П2.3, П2.6 приложения 2 в зависимости от вида склеиваемой продукции, породы древесины, вида клея, толщины и слойности пакета, принятой температуры плит пресса. Время t 4
дано в минутах, поэтому его нужно перевести в секунды.
Время снижения давления
, t 5
, состоит из двух периодов. Продолжительность второго следует выбрать из приложения 2, таблица П2.7.
Время, затрачиваемое на опускание стола пресса
, t 6
, определяется по формуле:
где у – величина упрессовки пакета, % (таблица П2.1, приложение 2);
u
6
– скорость опускания стола пресса, мм/с (выбирается из таблице П1.1, приложение 1).
Время, затрачиваемое на выгрузку фанеры из пресса
, t 7
, определяется по формуле:
где l
2
– ход экстрактора разгрузочной этажерки, равный ходу толкателя загрузочной этажерки, мм;
u
7
– скорость движения экстрактора, мм/с (выбирается из таблицы П1.1, приложение 1).
Цикл работы пресса
, t 0
, составит:
Так как t 1
≥ t 7,
то t 7
не включают в цикл работы пресса.
Результаты расчета производительности пресса вносятся в таблицу
9.
в) скорость движения толкателя загрузочной этажерки
г) скорость подъема и опускания стола
б) продолжительность выдержки пакетов под давлением
в) продолжительность снижения давления
Продолжительность части операций цикла пресса:
Средневзвешенная производительность пресса
, П ср
:
где , , – производительность пресса при изготовлении продукции определенной толщины, м 3
/ч;
, , – процент выпуска фанеры данной толщины от общего ее количества, таблица 1 ( + + = 100 %).
Объем производства каждого вида продукции в смену
,
где – количество установленных прессов в цехе (таблица П1.1, приложение 1) К
= 2;
7,7 ч – средняя продолжительность смены, ч.
Годовая производственная программа для каждого вида продукции
, Q i
год
, м 3
, определяется по формуле:
Q i
год
(9) =
Q i
см
Д С = 37,3 260 3 = 29094
Q i
год
(12) =
Q i
см
Д С = 37,3 260 3 = 29094
Q i
год
(15) =
Q i
см
Д С = 8,28 260 3 = 6458,4
гдеД – число рабочих дней в году, можно принять 260 дней;
С – число смен: принимаем три смены, так как фанерные предприятия работают по непрерывному циклу.
Полученные результаты заносим в таблицу 10.
Таблица 10 – Производственная программы клеевого участка цеха фанеры
производительность пресса, П ср
, м 3
/ч
4.3.
Определение расхода шпона и сырья, потребного на изготовление заданного количества фанеры
Расчеты ведутся в направлении, противоположном ходу технологического процесса, – от готовой продукции к исходному сырью.
1. Расчет выхода шпона из чурака и количества образующихся отходов при лущении.
2. Расчет количества сухого шпона, необходимо для изготовления заданного количества нешлифованной фанеры.
3. Расчет количества кряжей, необходимых для изготовления заданного количества шпона.
В процессе лущения получается большое количество отходов в виде шпона-рванины и карандашей. Выход шпона из чурака (форматного и неформатного) зависит от размеров и формы чураков: качества древесины; точности базирования чураков при установке их в лущильный станок; диаметра остающегося карандаша.
Расчет ведут для двух размеров длин чураков (с целью получения продольного и поперечного шпона), по среднему диаметру. Результаты расчетов заносим в таблицу 11.
Для определения выхода шпона пользуются эмпирическими формулами.
Диаметр средне взвешенного чурака
, d
св
,
м:
Длина чурака
, м, 1,830 + 0,080 = 1,9
Объем чурака
, м 3
; Приложение 3, таб. П3.1
Диаметр в верхнем отрубе = 0,27 = Объем чураков, м 3
, при длине в м
Продольное = 0,125 ; Поперечное = 0,082.
Сортовой состав
сырья
I
,
II
,
III
сортов
, %; равен по условию 40 : 60 : 0.
Коэффициент выхода шпона для сорта
, К В.
; Приложение 3, таб. П3.2. При длине чурака 1,3 м табличные значения коэффициентов умножаются на 1,02; при длине чурака 1,9 и 2,2 м – на 0,98.
- I сорта: Поперечное = 0,9045 1,02 = 0,92259 ; Продольное = 0,9045 0,98 = 0,88641
- II сорта: Поперечное = 0,8985 1,02 = 0,91647 ; Продольное = 0,8985 0,98 = 0,88053;
Коэффициент выхода форматного шпона для сырья сортов
, К Л
; Приложение 3, таб. П3.2. При длине чурака 1,3 м табличные значения коэффициентов умножаются на 1,02; при длине чурака 1,9 и 2,2 м – на 0,98.
- I сорта: Поперечное = 0,866 1,02 = 0,88332 ; Продольное = 0,866 0,98 = 0,84868
- II сорта: Поперечное = 0,857 1,02 = 0,87414 ; Продольное = 0,857 0,98 = 0,83986;
Диаметр остающихся карандашей
, d
к
, м, для сырья:
При расчетах значение d
0
можно принять равным 0,065 м.
Объем неформатного шпона, получаемого из 1 м 3
сырья
, V
1
:
где l
ч
– длина чурака, м. Определяется исходя из размеров формата фанеры: к размерам фанеры необходимо прибавить припуск на обработку (60¸80 мм) и привести результат к стандартному размеру (стандартные размеры можно посмотреть в приложении 3, таблица П3.1);
К в
– коэффициент выхода шпона, определяется по таблице П3.2;
К л
– коэффициент выхода форматного шпона, определяется по таблице П3.2;
V
ч
– объем чурака, определяется по таблице П3.1.
Объем форматного шпона, получаемого из 1 м 3
сырья
, V
2
:
Всего объем шпона, получаемого из 1 м 3
сырья
, V
ш
:
где V
1
– объем неформатного шпона, м 3
;
Объем карандашей, получаемых из 1 м 3
сырья
, V
к
, м 3
, вычисляют по формуле для каждого сорта сырья:
Объем шпона-рванины, получаемой из 1 м 3
сырья
, V
р
, м 3
, вычисляют по формуле:
Средневзвешенное значение объемов
, V
ср
, находится по формуле:
где a
1
, a
2
, a
3
– сортовой состав сырья, % (таблица П1.1);
V
1
, V
2
, V
3
– объем шпона, соответствующего определенному сорту.
Количество фанеры каждой толщины определяется с учетом ее выпуска в процентах к заданной выработке. Расчет производится на сменную программу выпуска заданной продукции.
Количество переобрезанной фанеры
, Q
0
, определяется по формуле:
где Q
1
–годовая программа выпуска продукции, м 3
(таблица 3, графа 12);
– процент отходов при переобрезе; можно принять равным 2 %.
Объем отходов, получаемых при переобрезе
, q
1
, устанавливают из выражения:
Полученные данные заносят в графы 8 и 9 таблицы 11.
Процент отходов на обрезку фанеры
, а
2
, определяют из выражения:
где F
н
– площадь необрезанного листа фанеры, м 2
= 1,91 1,3
F
0
–площадь обрезного листа фанеры, м 2
=1,83 1,22
Припуски на обработку по длине и ширине листов фанеры обычно равны 60–80 мм (на обе стороны). С учетом величины отходов при обрезке а
2
определяют количество необрезной фанеры
, Q
2
, из выражения:
Объем отходов, образующихся при обрезке фанеры
, q
2
, составит:
Полученные данные вносят в графы 10, 11, 12 таблицы 11.
Графу 13 заполняют данными о потере на упрессовку фанеры во время ее склеивания, которую выбирают из таблицы П2.2, приложение 2.
Количество сухого шпона
, Q
3
, поступающего на участок сборки пакетов с учетом потерь на упрессовку, а
3
, определяют из выражения: а
3
: 9 = 9; 12 = 10; 15 = 12,
Потери шпона на упрессовку при склеивании
, q
3
:
Количество сухого шпона, выходящего из сушилок
, с учетом отходов, образующихся при сортировании, ребросклеивании, транспортировке, изготовлении ленточек шпона для починочных станков ( а
4
= 2÷3 %), Q
4
, можно определить из выражения
Объем отходов шпона
, образующихся на участке сортирования, починки ребросклеивания шпона, q
4
:
Общее количество шпона при изготовлении неквадратной фанеры разделяют на продольный и поперечный с учетом слойности и строения пакета.
Слойность берем лицевую продольную, толщиной фанера = 9, 12, 15. Слойность, в «Таблица 9 – Расчет производительности клеильного пресса».
Расчет следует вести в табличной форме (см. таблицу 13).
В графу 1 переносят размеры листов шпона, определяемые исходя из размеров листов фанеры с учетом припуска на обрезку, и их строения.
Толщину листов шпона
, S
ш
, определяют с учетом упрессовки и слойности пакета из выражения
Данные заносят в графу 2. В графу 3 переносят данные граф 19 и 20 таблицы 4. Для каждой толщины шпона приводят количество продольного и поперечного шпона.
Потери шпона на его усушку
, а
5
, по ширине а
т
и толщине а
р
можно принять равными
При конечной влажности шпона 5–10 % усушку шпона в тангенциальном направлении, т. е. по ширине листа (поперек волокон) можно принять равной а
т
= 7–9 % по толщине а
р
= 5–6 %.
Количество сырого шпона
, Q
5
, определяется с учетом суммарных потерь на усушку в тангенциальном и радиальном направлениях
Суммарные потери на усушку шпона по толщине и ширине листов
, q
5
:
Для заполнения последующих граф необходимо определить количество потребных чураков
, N
, по формуле:
где V
шср
– средневзвешенный выход всего шпона из 1 м 3
сырья среднего диаметра и требуемой длины, м 3
(таблица 11);
К
0
– коэффициент, учитывающий организационные потери древесины на участке лущения чураков, К
0
= 0,975–0,995.
Объем сырья
, Q
6
, определяется по формуле:
Количество отходов на карандаши
, q
6
, определяют по формуле:
q 6
(9) = Q 6
V K
= 38762,989 0,05198= 2014,9
q 6
(12) = Q 6
V K
= 37327,317 0,05198 = 1940,274
q 6
(15) = Q 6
V K
= 8474,38 0,05198= 440,498
q 6
(9) = Q 6
V K
= 22648,455 0,0645 = 1460,825
q 6
(12) = Q 6
V K
= 24535,82 0,0645 = 1582,56
q 6
(15) = Q 6
V K
= 0,0645 = 359,867
где V
к
–
объем карандашей, получаемых из 1 м 3
сырья, м 3
.
Количество отходов на шпон-рванину
, :
q
′ 6
(9) =
Q
6
V
Р
= 38762,989 0,3231 =
q
′ 6
(12) =
Q
6
V
Р
= 37327,317 0,3231 = 12060,456
q
′ 6
(15) =
Q
6
V
Р
= 8474,38 0,3231 = 2738,07
q
′ 6
(9) =
Q
6
V
Р
= 22648,455 0,2361 = 5347,3
q
′ 6
(12) =
Q
6
V
Р
= 24535,82 0,2361 = 5792,907
q
′ 6
(15) =
Q
6
V
Р
= 0,2361 = 1315,16
где V
р
–
объем шпона-рванины, получаемой из 1 м 3
сырья, м 3
.
При расчетах величина отходов при раскрое кряжей, а
7
, может быть принята в пределах 1–3 %.
Потребное количество сырья в кряжах
, Q
7
, м 3
:
Объем отходов, образующихся при раскрое кряжей на чураки
, q
7
:
Определяем расход сырья на изготовление фанеры, сырого и сухого шпона.
Расход сырья на 1 м 3
готовой фанеры
,
R
:
Расход сухого шпона на изготовление 1 м 3
готовой фанеры
,
R
4
:
Расход сырого шпона на изготовление 1 м 3
сырого шпона
,
R
5
:
Расход сырья на изготовление 1 м 3
сырого шпона
,
R
6
:
Проверить правильность расчетов можно из выражения:
на усушку в тангенциальном и радиальном направлениях
Баланс сырья составляют на основании расчетов по расходу сырья.
Общее количество перерабатываемого сырья в смену выбирается из таблицы 13, графа 12.
Количество выпускаемой фанеры – таблица 12, графа 6.
Количество отходов берется из соответствующих граф таблиц 5 и 6.
Количество выпускаемой фанеры, отходов и потерь в сумме соответствует количеству перерабатываемого сырья (в м 3
и %). Баланс сырья сводят в таблицу 14.
При изготовлении фанеры определяется производственный расход клея в кг на 1 м 3
, учитывающий все возможные потери клея как при его изготовлении, так и при использовании.
Потребное количество жидкого клея на 1 м 3
фанеры
, Q
ж
, определяется по формуле:
где q
– техническая норма расхода, г/м 2
;
К о
– коэффициент, учитывающий потери клея при обрезке материала, К о
= F
н
/ F
о
;
F
н
– площадь листа склеиваемого материала до его обрезки, м 2
;
F
о
– площадь листа фанеры после его обрезки, м 2
;
К п
– коэффициент, учитывающий потери клея при его изготовлении и последующем использовании, К п
= 1,03–1,05;
Техническая норма расхода клея выбирается из таблицы П4.1, приложение 4. Полученные результаты заносим в таблицу 15.
Задание для проектируемого участка составляется согласно расчетам расхода сухого, сырого шпона и сырья на заданную годовую программу выпуска фанеры.
Производственной программой склада сырья является количество кряжей определенного размера в год (таблица 13, графа 12).
Производственной программой участка окорки и разделки кряжей является количество кряжей и чураков определенного размера в год (таблица 13, графа 9).
Производственной программой лущильного участка является количество выпускаемого сырого шпона в год определенного размера и направления волокон (таблица 13, графа 6).
Производственной программой участка сушки является количество сухого шпона в год определенного размера и направления волокон. Количество шпона для ребросклеивания и починки задано в исходных данных (таблица 12, графа 18).
Производственной программой участка изготовления фанеры является количество выпускаемой фанеры в год (таблица 12, графа 6).
Производственную программу составляют по таблице 16.
8. Выбор и расчет потребности в оборудовании на проектируемом участке
Выбор оборудования производится по заданному участку. Ниже приведены технические характеристики оборудования для всех участков фанерного производства [4]. Технические характеристики выбранного оборудования следует привести в курсовом проекте.
Сушилки для шпона отличаются теплоносителем (воздушные или газовые), направлением циркуляции воздуха (продольная, поперечная или сопловое дутье), по количеству этажей, по принципу работы (периодического или непрерывного действия). Технические характеристики сушильных агрегатов приведены в таблицах 10, 11.
Сортировка шпона осуществляется на сортировщиках, они устанавливаются непосредственно у сушилок.
Техническая характеристика механизированных сортировщиков типа ViLK фирмы «Рауте» (Финляндия) приведена в таблице 18.
Таблица 18 – Техническая характеристика сортировщиков типа ViLK фирмы «Рауте»
Техническая характеристика различных моделей ребросклеивающих станков представлена в таблице 19.
Примечание – * – число нитей правой/левой стороны.
Для усования шпона используются станки разных моделей. Техническая характеристика усовочных станков приведена в таблице 20. Соединение шпона на «ус» производят на узкоплитных прессах. Техническая характеристика узкоплитных прессов приведена в таблице 21.
Примечание – Станок 2FVS – двухсторонний, усует одновременно два противоположных торца шпона и наносит на один усованный торец слой клея. Наибольшая рабочая длина шпона 1850 мм, наименьшая – 450 мм.
Таблица 21 – Техническая характеристика узкоплитных прессов
Примечание – Установка IPHL-66 финской фирмы «Рауте» включает в себя насосную станцию, узкоплитный пресс, гидравлические ножницы и рабочий стол с кареткой подачи. Фирма также выпускает установки с размерами плит пресса 1460 ´1970 мм.
Для починки шпона с целью повышения сорта, используют шпонопочиночные станки. Техническая характеристика шпонопочиночных станков приведена в таблице 22.
Примечание – * – с гидроприводом (российского производства).
Расчет производительности выполняем по методике [4]. Ниже приведены формулы для расчета производительности для оборудования фанерного производства. Для расчета потребности в оборудовании необходимо определить часовую производительность оборудования.
Часовая производительность роликовой сушилки
, П ч
, м 3
/ч:
L
– рабочая длина сушилки, м (секции сушки плюс секции охлаждения);
z
– продолжительность прохождения шпона по рабочей длине сушилки, мин:
где l
– длина секции охлаждения, м;
t
– продолжительность сушки в сушильной зоне, мин:
где W
нач
, W
кон
– соответственно начальная и конечная влажность шпона, %;
N
– скорость сушки в первом периоде, %/мин;
k
– коэффициент продолжительности второго периода, 1/мин;
Коэффициенты N
, k
определяют формулами:
- для роликовых сушилок с продольной циркуляцией:
- для роликовых сушилок с поперечной циркуляцией:
- для роликовых сушилок с сопловым дутьем при ширине сопловой щели 8 мм и
шаге расположения сопел вдоль сушилок 300–350 мм и расстоянии от среза
а
= 1 – при паровом (воздушном) обогреве;
а
= 0,75 – при обогреве топочными газами;
а
1
= 1,18 – для радиационно-сопловых паровых сушилок;
а
1
= 1 – для газовых сопловых сушилок;
t
– средняя температура воздуха или газовоздушной смеси, °С; для сушилок с продольной циркуляцией или для сушилок с поперечной циркуляцией равна полусумме температур на входе и выходе, для сушилок с сопловым дутьем применяется средняя температура воздуха (газовоздушной смеси) на выходе в сопловые короба;
V
– средняя скорость воздуха, м/с; В роликовых паровых сушилках: с продольной циркуляцией 1÷2 м/с, с поперечной циркуляцией 2 м/с, с сопловым дутьем 12 м/с.В роликовых газовых сушилках 2,5 м/с, газовых сопловых 10м/с.[3]
C
п
– поправочный коэффициент на породу древесины.
При сушке шпона в роликовых сушилках C
п
= (600 + p
0
)/1200,
при сушке шпона в конвективных сушилках C
п
= p
0
/600;
здесь p
0
– плотность абсолютно сухой древесины заданной породы, кг/м 3
(для березы – 600, ольхи – 490, сосны – 470, лиственницы – 630, тополя – 430, осины – 480, бука – 620, кедра – 410);
К р
– коэффициент использования рабочего времени;
К ш
– коэффициент заполнения ширины сушилки;
К дл
– коэффициент заполнения длины сушилки.
Техническая характеристика отечественных и импортных сушильных агрегатов приведена в таблицах 16, 17.
Производительность реброрсклеивающих станков в зависимости от подачи
, м 3
/ч, определяется по формулам:
где – часовая производительность ребросклеивающих станков соответственно в листах и в м 3
;
К с
– коэффициент проскальзывания шпона, принимается равным 0,96;
b
– ширина листа сухого форматного шпона, м;
n
– число клеевых швов в форматном листе шпона: n
= ( b
/ b n
) – 1, где b n
– средняя ширина полосы кускового шпона (принимается 0,2–0,25 м);
где – часовая производительность ребросклеивающих станков соответственно в листах и в м 3
;
V
– скорость подачи шпона, м/мин (берется из технической характеристики станка с учетом скорости отверждения применяемого клея);
b
– ширина листа сухого форматного шпона, м;
Производительность узкоплитного пресса
, П ч
, склейка/ч:
t
1
– продолжительность выдержки при склеивании на «ус», с, определяют по данным технологических инструкций в зависимости от толщины склеиваемого шпона (фанеры), вида применяемого клея, температуры плит пресса ( t
плит
); например, для шпона S
= 1,5 мм, t
плит
= 145–150 °С и для фенольного клея t
1
= 40–25 с, для карбамидного клея t
1
= 5–10 с;
t
2
– продолжительность ручных операций по укладке, выравниванию и подаче шпона (фанеры), обычно t
2
принимают равной 20–30 с.
Производительность шпонопочиночного станка
, П ч
, лист/ч, определяют по формуле:
t
1
– продолжительность ручных операций, приходящихся на один лист шпона (подача листа шпона на стол станка, снятие листа со стола станка), с, принимают 6–7 с;
m
– число дефектных мест в одном листе шпона, подлежащих починке, принимают от 5 до 15;
t
2
– машинное время, затрачиваемое на вырубку одного дефекта и установку одной вставки, с, выбирается в зависимости от модели станка, составляет 1,0–2,2 с;
t
3
– время на перемещение листа шпона под просечной от одного дефектного листа к другому, с, составляет 0,4–0,8 с.
Название: Проектирование сушильно-сортировочного цеха участки сушки, сортировки, починки и ребросклеивани
Раздел: Промышленность, производство
Тип: реферат
Добавлен 19:53:49 09 июля 2011 Похожие работы
Просмотров: 196
Комментариев: 14
Оценило: 3 человек
Средний балл: 5
Оценка: неизвестно Скачать
Сушки, сортировки, починки и ребросклеивания
б) формат в обрезном виде (длина ширина), мм
3. Характеристика прессового оборудования:
б) скорость движения толкателя загрузочной этажерки, мм/с
в) скорость подъема и опускания стола, мм/с
г) скорость движения экстрактора, мм/с
а) число пакетов в рабочем промежутке
в) объем починки, в процентах к общему количеству шпона
г) объем ребросклеивания, в процентах к общему количеству шпона
Скорость смыкания плит пресса, мм/с
Таблица 9 – Расчет производительности клеильного пресса
Количество фанеры данной толщины от общего ее объема
Суммарная продолжительность цикла работы пресса
Производительность клеильного пресса
Средневзвешенная производительность пресса
Количество чураков данного сорта в партии сырья
Коэффициент выхода шпона для сорта:
Коэффициент выхода форматного шпона для сырья сортов:
Диаметр остающегося карандаша из чураков сорта:
Объем неформатного шпона из чураков сорта:
Объем форматного шпона из чураков сорта:
Объем шпона-рванины из чураков сорта:
Таблица 12 – Расчет количества сухого шпона на годовую программу
Сухой шпон, поступающий на участок сборки пакетов
Таблица 13 – Расчет количества сырья
Количество перерабатываемого сырья, м 3
Таблица 16 – Годовая производственная программа для проектируемого участка
Ассортимент выпускаемой продукции проектируемого участка
Количество выпускаемой продукции, м 3
Таблица 10 – Технические характеристики паровых сушилок для шпона [1]
Производительность для шпона 1,5 мм, м 3
/ч
Таблица 11 – Технические характеристики газовых сушилок для шпона
Производительность для шпона 1,5 мм, м 3
/ч
Таблица 19 – Техническая характеристика ребросклеивающих станков с подачей шпона поперек волокон
Наибольшая длина стыкуемых полос, мм
Наибольшая длина обрезаемой ленты шпона (ширина листа), мм
Скорость подачи, м/мин (регулируется бесступенчато)
Рабочее давление привода шпоноукладчика, МПа
Общая мощность электродвигателей, кВт
Таблица 20 – Техническая характеристика усовочных станков
Рабочее давление в гидросистеме, МПа
Регулировка температуры в диапазоне, °С
Размер плит (длина ´ ширина ´ толщина), мм (для импортных только длина ´ ширина)
Наибольший просвет между плитами, мм
Таблица 22 – Техническая характеристика шпонопочиночных станков
Ширина полосы шпона для вставок, мм
Срочная помощь учащимся в написании различных работ. Бесплатные корректировки! Круглосуточная поддержка! Узнай стоимость твоей работы на сайте 64362.ru
Привет студентам) если возникают трудности с любой работой (от реферата и контрольных до диплома), можете обратиться на FAST-REFERAT.RU , я там обычно заказываю, все качественно и в срок) в любом случае попробуйте, за спрос денег не берут)
Да, но только в случае крайней необходимости.
Реферат: Проектирование сушильно-сортировочного цеха участки сушки, сортировки, починки и ребросклеивани
Реферат Функции Таможни
Имидж Делового Человека Контрольная Работа
Соболянская Елизавета Диссертация По Некромагии 2 Торрент
Курсовая работа: Реферування в обробці документації
Курсовая работа по теме Сущность денег и их роль в экономике
Реферат: Старение организма
Реферат: Организация выставочных мероприятий в Геленджике. Скачать бесплатно и без регистрации
Леса России Реферат 4 Класс
Беденко М В Математика Контрольные Работы Купить
Ответ на вопрос по теме Плотности материалов
Курсовая работа по теме Формирование познавательного интереса у младших школьников на уроках математики посредством использования занимательных игр
Эсс Перевод
Реферат: Древнегреческий костюм. Скачать бесплатно и без регистрации
Реферат: Американская и Мировая Науки: их развитие и проблемы
Курсовая работа по теме Создание компьютерной игры 'Крестики и нолики'
Налоговый Период Реферат
Курсовая работа по теме Организация работы горячего цеха в ресторане 'Кубань' г. Краснодра и пути ее совершенствования
Курсовая работа по теме Особенности государственной регистрации субъектов предпринимательской деятельности
Реферат по теме Высшие цветковые растения. Корневые паразиты и полупаразиты
Курсовая работа по теме Исследование социальной защиты различных групп населения РФ в области лекарственного обеспечения бесплатно или со скидкой
Реферат: Государство и гражданское общество. Формы нх взаимодействия
Реферат: Толстой Упустишь огонь - не потушишь
Реферат: Место права в правовой надстройке