Реферат: Оборудование производства ИУ
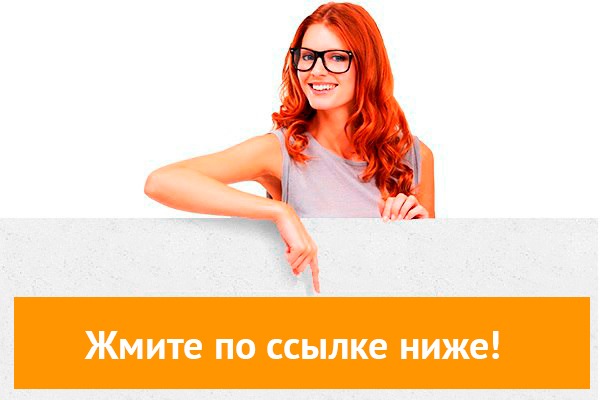
💣 👉🏻👉🏻👉🏻 ВСЯ ИНФОРМАЦИЯ ДОСТУПНА ЗДЕСЬ ЖМИТЕ 👈🏻👈🏻👈🏻
Содержание.............................................................................................. 1
Задание..................................................................................................... 2
Введение................................................................................................... 3
1. Расчет основных параметров роторной линии.................................. 4
1.1. Определение конструктивных параметров.................................. 4
инструментального блока.................................................................... 4
1.2. Выбор шага ротора...................................................................... 5
1.3. Расчет числа позиций технологического ротора........................ 5
1.4. Расчет конструктивных параметров роторов............................. 8
2. Расчет элементов инструментального блока.................................... 11
3. Расчеты на прочность элементов конструкции................................ 13
механического привода......................................................................... 13
3.1. Силы, действующие на элементы привода................................ 13
3.2. Расчет ползуна............................................................................ 15
3.3. Расчет перемычек барабана....................................................... 16
4. Расчет привода транспортного движения........................................ 19
4.1. Выбор схемы привода................................................................ 19
4.1. Определение крутящего момента на валу технологических и транспортных роторов............................................................................................... 19
4.1.1. Технологический ротор с механическим приводом рабочего движения.......................................................................................................... 19
4.1.2 Транспортный ротор............................................................ 20
4.2. Расчет мощности электродвигателя привода............................ 21
4.3. Выбор электродвигателя............................................................ 21
Список использованных источников.................................................... 22
Разработать автоматическую роторную линию для сборки спортивного патрона калибром 5.6 мм с производительностью 800 шт./мин.
В состав проектно-конструкторских задач, решаемых при проектировании любой автоматической машины, в том числе и роторной линии (АРЛ), входит параметрический синтез. Параметрический синтез решает задачу определения основных конструкционных (геометрических и механических) параметров машины в целом, ее отдельных механизмов, устройств и рабочих органов. Применительно к проектированию автоматических роторных линий параметрический синтез включает определение конструктивных размеров инструментальных блоков, установление шага ротора, расчет числа позиций (блоков, гнезд) рабочих роторов, радиусов начальных окружностей технологических и транспортных роторов, расчет транспортной скорости и частоты вращения роторов.
В большинстве случаев параметрический синтез является задачей оптимизационного типа: параметры роторной линии должны быть определены таким образом, чтобы заданный или выбранный критерий эффективности имел оптимальное значение. Руководствуясь определенными из расчетов параметрами машины, конструктор осуществляет эскизную, техническую и затем рабочую разработку.
Инструментальный блок (ИБ) это сменный узел технологического ротора для установки инструмента и обеспечения основных и вспомогательных переходов технологических операций. Инструментальный блок должен обеспечивать заданную точность взаимного расположения рабочего инструмента и обрабатываемой детали, обладать необходимыми прочностью и жесткостью, иметь минимальную массу, допускать быстрый съем из гнезда технологического ротора.
Типовая схема инструментального блока для штамповочной операции (см. рис.1) позволяет оценить его основные размеры.
Диаметр D бл
блока определяется с учетом максимальных поперечных размеров деформирующего инструмента
где D м
– диаметр поперечного сечения матрицы, мм.
Расчетные зависимости для определения геометрических размеров матриц для различных технологических операций приведены в таблице 1. [1]
Диаметр матрицы: D м
= 3 *
d d
= 3 *
5,6 = 16,8 мм
Диаметр блока: D бл
= 2 *
16,8 = 33,6 мм
Принимаем диаметр блока равный 36 мм
где L т
– технологическое перемещение инструмента, включающее подвод инструмента, рабочее перемещение и проталкивание детали из матрицы., мм;
L кр
, L зх
– размеры элементов ИБ, мм.
Технологическое перемещение на стадии эскизной проработки можно определить по формуле:
Величина L кр
определяется из соотношения:
Величина L зх
определяется из конструктивных соображений.
Шаг между гнездами ротора h р
выбирается в зависимости от размеров детали, инструментальных блоков и зазоров между ними (см. рис.2 [1]).
Для роторов штамповочного производства шаг ротора:
где Dh– зазор между инструментальными блоками, мм .
Величина Dh определяется размерами ИБ, их конструкцией и системой крепления в гнездах ротора (для роторов с механическим
приводом Dh= (0.1… 0.4)× D бл
):
Рассчитанную величину шага роторов с механическим и гидравлическим приводом округляем до ближайших значений
Общее число позиций (инструментальных блоков, гнезд) ротора определяем по минимально необходимой длительности технологического Т т
и кинематического Т к
циклов:
u p
= П т *
Т к
/60 < 1,33 *
П т *
Т т
/60 (3)
где П т
– теоретическая производительность ротора, шт/мин.
Теоретическую производительность выбираем по заданной фактической производительности П ф
с учетом цикловых потерь:
Для проектных расчетов коэффициент цикловых потерь
Длительность технологического цикла должна обеспечивать выполнение технологической операции, включая вспомогательные переходы (загрузку детали, ее закрепление и выдачу из ротора). Длительность кинематического цикла определяется, в основном, характеристиками привода рабочего движения ротора. На рис. 1 приведена цикловая диаграмма технологического ротора, показывающая соотношение технологического и кинематического циклов. Для роторных машин, осуществляющих вращение ротора с постоянной скоростью, время обработки t р
соответствует углу поворота j р,
а t 1
– углу j 1
и т.д.
Рис. 1. Цикловая диаграмма технологического ротора.
T T
= t 1
+ t 2
+ t p
+ t 3
+ t 4
,
где t 1
, t 4
– соответственно время на подачу детали и выдачу ее из ротора, с;
t 2
, t 3
– время, затрачиваемое на закрепление и освобождение детали при обработке, с;
t р
– технологическое время обработки детали, с;
t пд
,t отв
– интервалы времени подвода инструмента к детали и отвода, с;
t х
– время простоя инструментов в исходном положении (холостой ход), с.
Точные значения интервалов кинематического и технологического циклов можно определить только при расчете механизмов привода рабочего движения и механизмов захвата. На этапе параметрического синтеза эти интервалы определяются приближенно с учетом рекомендаций, полученных на основе практики конструирования роторных линий.
Для механического
(кулачкового) привода рабочего движения интервал t р
, соответствующий обработке детали инструментом, определяем по следующим формулам:
для операций чеканки, гибки, сборки
принимаем закон изменения ускорения по синусоиде, обеспечивающий к концу интервала плавное снижение скорости и ускорения рабочего органа до нуля:
где L р
, V р
max
, a р
max
– соответственно путь, допустимые скорость и ускорение за время обработки детали инструментом, м, м/с, м/с 2
;
Ориентировочно для указанных операций можно принимать а р
max
£
g, где g– ускорение свободного падения, м/c 2
.
Время подачи изделий в ротор t 1
принимаем равным времени удаления из него t 4
, а при определении числовых значений исходим из того, что угол сопровождения подающими и съемными устройствами не превышает 20°:
Величины интервалов t 2
и t 3
рассчитываем в зависимости от скорости срабатывания зажимных приспособлений, центрирующих и съемных механизмов. В первом приближении принимаем:
Время подвода и отвода инструмента определяем в зависимости от типа привода рабочего движения. Для механического
привода:
где L пд
,L отв
– соответственно перемещение инструмента при подводе к детали и отводе инструмента в исходное положение, м;
V max
, а max
– максимальные скорость и ускорение на участках подвода и отвода, м/с, м/с 2
.
Для обеспечения максимальной синхронности работы приводных механизмов технологического и транспортного движений следует соблюдать неравенства t пд
£ t 1
+ t 2
, t отв
£ t 3
+ t 4
:
После определения интервалов кинематического и технологического циклов и проверки соблюдения неравенств определяем общее число позиций ротора
u р
= П т
× Т к
/ 60£ 1,33× П т
× Т т
/ 60
Полученное число позиций технологического ротора u р
округляем в большую сторону и принимаем соответственно параметрическому ряду 4, 5, 6, 8, 9, 10, 12, 16, 18, 20, 24 (см. таблицу 3 [1])
Принимаем количество инструментальных блоков u р
= 8
Число инструментальных блоков, находящихся одновременно в рабочей зоне ротора, определяем по формуле:
Радиус начальной окружности технологического ротора:
Величину радиуса R р
проверяем с учетом конструктивных размеров вала ротора и инструментальных блоков (см. рис.2):
Рис. 2. Схема к расчету свободного пространства технологического ротора
V тр
= П т*
h p
/60 = p *
n p*
R p
/30
Для удобства компоновки и обеспечения установленной окружной скорости роторов рекомендуется принимать диаметры начальных окружностей зубчатых колес привода транспортного движения равными диаметрам начальных окружностей роторов. Поэтому полученное значение диаметра начальной окружности ротора D р
уточняем с учетом параметров зубчатого зацепления
Конструктивные параметры транспортных роторов определяем аналогично технологическим. С целью удобства размещения технологических роторов, обеспечения доступа к рабочей зоне, простоты ремонта и обслуживания число позиций и диаметры транспортных роторов рекомендуется брать больше технологических (u тр
= (1,25… 1,33)× u ð
).
Для всех технологических и транспортных роторов, входящих в роторную линию, соблюдаем основное условие компоновки:
D p
/D тр
= R p
/R тр
= u р
/u тр
= n р
/n тр
= const (8)
Из соотношения (8) определяются радиус начальной окружности R тр
и частота вращения n тр
транспортного ротора:
Рис. 3. Расчетная схема инструментального блока:
1– ползун; 2– корпус; 3– пуансон; 4– заготовка;
Элементы инструментальных блоков (ИБ) рассчитываются на прочность в опасных сечениях от действия растягивающих (сжимающих) сил и изгибающих моментов. Расчетная схема ИБ для штамповочных операций представлена на рис. 3.
Корпус блока рассчитывается на растяжение и изгиб в сечении А-А:
где Р т
– номинальное технологическое усилие, Н;
F – площадь расчетного сечения А–А, мм 2
;
y c
– координата центра тяжести сечения, мм;
y max
– ðàññòîÿíèå от центра тяжести до наиболее удаленной точки сечения, мм;
[s]– допускаемые напряжения материала корпуса блока, МПа.
Площадь сечения F, момент инерции I x
, координата центра тяжести y c
и координата y max
рассчитываются по формулам:
J x
= (D бл
4
- d пр
4
)/128 (pa/180+sin a);
y c
= 120/pa ((D бл
3
- d пр
3
)/ (D бл
2
- d пр
2
) sin (a/2));
где D бл
– диаметр инструментального блока, мм;
d пр
– диаметр приемника детали, мм.
Размеры D бл
и d пр
определяются по чертежу инструментального блока.
Опорные поверхности крепления ИБ в блокодержателе рассчитываются на смятие в сечении Б–Б:
где F оп
– площадь опорных поверхностей, мм;
[s см
]– допускаемое напряжение на смятие материала корпуса, МПа.
Площадь опорных поверхностей определяется по приближенной формуле:
Для определения напряжений, возникающих в элементах механического (кулачкового) привода рабочего движения роторных машин под действием заданной технологической силы Р т
(см. рис. 4.а.), необходимо установить величины полной реакции R и ее осевой и окружной составляющих R z
è R x
. Полная реакция R необходима для расчета на срез и смятие оси ролика ползуна. Составляющая R x
необходима для расчета ползуна на изгиб. Составляющая R z
воспринимается осевыми опорами вала ротора и необходима для выбора осевых подшипников ротора. Конструктивными размерными элементами, от которых при заданной величине технологической силы Рт зависят значения R, R x
, R z
являются: вылет ползуна а, длина направляющей барабана b и угол подъема копира b.
Полная реакция копира R нагружает ползун изгибающим моментом, вызывающим нормальные к оси ползуна силы N 1
и N 2
(рис. 4.а). Эти силы являются реакциями направляющей поверхности барабана и учитываются при расчете на прочность перемычки между направляющими отверстиями.
Значения сил R, R x
, R z
, N 1
и N 2
определяются формулам:
R=P т
К т
; R x
=P т
K x
; R z
=P т
K z
где К т
, К õ
, Ê z
– коэффициенты пропорциональности,учитывающие
конструктивные особенности крепления ролика.
Рис. 4. Расчетная схема элементов механического привода:
а– силы, действующие в элементах кулачкового привода;
б– схема с консольным расположением ролика;
в– схема с торцевым расположением ролика
В механическом (кулачковом) приводе применяются два типа конструкций ползуна – с консольным расположением ролика (рис. 4.á) и торцевым расположением (рис.4.в). Консольное крепление рекомендуется применять при технологическом усилии не более 1000 Н, а торцевое– для усилий до 10 кН.
Коэффициенты К т
, К õ
, Ê z
определяются по формулам:
где f пр
– приведенный коэффициент трения (f пр
= 0,15), учитывающий трение качения ролика по копиру и трение скольжения отверстия ролика относительно его оси.
Для привода с пазовый (консольным) кулачком значение коэффициента В рассчитывается по формуле:
B = 2.3 *
f 1*
(1-3 *
(e/b) *
f 1
) *
(1-f пр
*
tgb)-(tgb+ f пр
)
где е– величина консоли в расположении ролика, мм;
f 1
– коэффициент трения ползуна о направляющие барабана (f 1
= 0,2).
Так как полная реакция и ее составляющие быстро возрастают с увеличением отношения а/b, ýòî îòíîøåíèå ñëåäóåò âûáèðàòü äîñòàòî÷íî ìàëûì. Ïðàêòè÷åñêè îòíîøåíèå а/b äëÿ ïðèâîäîâ ñ òîðöîâûì êîïèðîì íå äîëæíî ïðåâûøàòü 1/3. Ïðè ýòîì âåëè÷èíà à ÿâëÿåòñÿ çàäàííîé ñàìèì çíà÷åíèåì òåõíîëîãè÷åñêîãî ïåðåìåùåíèÿ ðàáî÷åãî èíñòðóìåíòà L ò
, ò. å. à= L ò
è b³ 3× L ò
.
При консольном расположении ролика (рис. 4.б) диаметр оси определяется из условия прочности на изгиб:
где [n]– допускаемый коэффициент запаса ([n] = 1,5...2,0);
Ê s
– эффективный коэффициент концентрации напряжений (Ê s
= 1,8...2,0);
s –1
– предел выносливости при симметричном цикле нагружения (s –1
= (0,4... 0,45)×s в
, МПа);
s в
- предел прочности материала оси, МПа.
Наружный диаметр ролика определяется из условия проворачиваемости (d ð
³ 1,57× d 0
).
После определения параметров ползуна необходима проверка условий контактной прочности ролика и проверка на удельное давление и нагрев кинематической паре ролик-ось.
Наибольшее контактное напряжение при цилиндрическом ролике и выпуклом профиле кулачка определяется по формуле Герца:
где r д
– радиус кривизны действительного профиля кулачка, мм;
Условие контактной прочности выполняется
Проверка кинематической пары ролик-ось на удельное давление и нагрев производится по формулам:
где D 0
и D ê
– начальный диаметр ротора и средний диаметр кулачка, мм ;
П т
– теоретическая производительность ротора шт/мин,
[ð]– допускаемое удельное давление для трущихся поверхностей, МПа;
[ð× V è
]– допускаемое значение износо- и теплостойкости трущихся поверхностей, МПа× ìì/с.
Для материалов сталь по стали [ð]= 15…18 МПа, [ð× V è
]= 30…40 МПа× ìì/с.
Для практически наиболее важного случая, когда одновременно с копиром взаимодействует только один ползун, к одной перемычке приложено по одной силе: к передней по направлению вращения ротора перемычке приложена сила N 2
, а к задней– N 1
(см. рис. 5). N 1
> N 2
, поэтому более нагруженной является перемычка, к которой приложена сила N 1.
Составляющая N õ
ñилы N 1
, направленная параллельно линии, соединяющей центры направляющих отверстий, вызывает в перемычке напряжения изгиба s 1
, кручения t 1
и среза t 2
. Соответствующие нормальные и касательные напряжения определяются из соотношений:
где d п
– диаметр направляющего отверстия для ползуна, мм;
b– высота перемычки (длина направляющего отверстия барабана), мм.
Сила N ó
вызывает в перемычке изгиб в горизонтальной и вертикальной плоскостях и растяжение. Нормальные напряжения этих деформаций составят:
Суммарное нормальное напряжение будет максимальным в точке А, где все составляющие имеют один знак: s å
A
= s 1
+ s 2
+ s 3
+ s 4
.
Касательное напряжение в этой точке равно t 2
.
Суммарное касательное напряжение максимально в точке В, где t å
B
= t 1
+ t 2
. Суммарное нормальное напряжение в точке В составит s å
B
= s 1
+ s 2
+ s 4
.
Расчет перемычки на прочность, поскольку барабаны изготавливаются из чугуна, следует вести по I теории прочности, принятой для хрупких материалов:
где [s]– допускаемое напряжение материала барабана, МПа ([s]= (0,16...0,18)× s в
) .
Материалы элементов конструкции роторной машины выбираем по таблице 8 [1]
В автоматических роторных линиях реализуются четыре принципиально различных конструктивных варианта схем привода вращения технологических и транспортных роторов.
Первый вариант характерен для АРЛ с небольшим числом слабо нагруженных роторов, выполняющих операции небольшой энергоемкости (запрессовка, сборка, термохимическая обработка, контроль, таблетирование порошковых материалов). В этом случае вращение роторов осуществляется от электродвигателя посредством редуктора через ведущий (наиболее нагруженный или средний по расположению) технологический ротор Остальные технологические и транспортные роторы кинематически соединяются между собой зубчатыми колесами. Эта схема наиболее проста, но неосуществима в случае различных шаговых расстояний роторов входящих в линию. Кроме того, возможен неравномерный износ зубчатых колес привода при существенно отличающихся нагрузках на главных валах роторов.
Более распространенной является схема привода технологических групп роторов, объединяемых в линии, посредством червячных редукторов (рис.6 б.) . Входы редукторов связаны с приводным валом 6, а выходы– с наиболее нагруженными роторами технологических групп либо непосредственно, либо через зубчатую передачу. Внутри каждой технологической группы вращение передается цилиндрическими зубчатыми колесами. Настройка взаимного углового расположения групп роторов производится зубчатыми муфтами 5, устанавливаемыми на приводном валу. Этот вариант привода широко применяется в АРЛ с восемью-десятью технологическими роторами и производительностью линии до 200 шт / мин.
Недостатки схемы: неравномерная нагруженность элементов привода, низкий КПД привода (0,6...0,7), сложность защиты привода линии от перегрузок. Наличие одного скоростного режима затрудняет использование привода в высокопроизводительных АРЛ.
Суммарный момент M на валу технологического ротора с механическим (кулачковым) приводом складывается из момента технологических сил М т
, момента сил трения М тр
, момента на преодоление инерции вращающихся масс ротора при пуске линии М и
.
Момент технологических сил определяется по формуле:
где Р г
– технологическое усилие, Н;
R р
– радиус начальной окружности ротора, м;
u осн
– число инструментальных блоков в рабочей зоне ротора.
R п
– средний радиус подшипников ротора, м;
m п
– коэффициент трения в подшипниках (m п
= 0,06…0,1);
a п
– угол, определяющий направление усилия в подшипниках
Момент инерции масс ротора можно приближенно определить по формуле:
где e– среднее угловое ускорение ротора при пуске линии, с -2
;
g– ускорение свободного падения, м / с -2
.
где n р
– число оборотов ротора, об / мин;
Момент на валу транспортного ротора приближенно определяется как сумма моментов сил трения в подшипниках М тр
и момента инерции М и
:
Моменты М тр
и М и
определяются по формулам (18) и (19)
Мощность электродвигателя (кВт) привода транспортного движения роторной линии, включающей несколько технологических групп роторов можно определить по формуле:
N э.д.
= 0,105 *
10 -4
[(М пр
j
n б
j
)/(h 4
m
h рем
)] (21)
где m– количество кинематически объединенных групп роторов;
М пр
– момент, приведенный к валу базового ротора, НЧм;
n б
– угловая скорость вращения базового ротора, об / мин;
h рем
, h ч
– КПД, учитывающие потери в клиноременной передаче
Приведенный момент на валу базового ротора определяется выражением:
М пр
= М 0
+M 1*
i 01
/h 01
+ M 2*
i 02
/h 02
+... M k-1*
i 0,k-1
/h 0,k+1
i– передаточное отношение от i-ого ротора к базовому;
h– КПД зубчатой передачи от i-ого ротора к базовому;
М 1
, М 2
– моменты на валу роторов, НЧм;
М 0
– момент на валу базового ротора, НЧм.
Из стандартного ряда трехфазных асинхронных двигателей серии 4А по расчетным данным выбираем электродвигатель 80А с номинальной мощностью 1,1 кВт. Определяем суммарное передаточное число привода:
Выбираем передаточное число редуктора i р
= 12 (РЧ 12-8)
1. Автоматические роторные линии / И. А. Клусов, Н. В. Волков, В. И. Золотухин и др. – М. : Машиностроение, 1987.
2.Анурьев В. И. Справочник конструктора-машиностроителя. – М.: Машиностроение, 1982.
3.Клусов И.А.., Сафарянц А.Р. Роторные линии. – М.: Машиностроение, 1969.
4.Кольман-Иванов Э.Э. Машины-автоматы химических производств. –М.: Машиностроение, 1972.
5.Кошкин Л. Н. Комплексная автоматизация производства на базе роторных линий. – М. Машиностроение, 1972.
6.Кошкин Л.Н. Роторные и роторно-конвейерные линии. – М. Машиностроение, 1986.
7.Расчет на прочность деталей машин / И. А. Биргер, Б. Ф. Шорр, Г. Б. Иосилевич. – М. : Машиностроение, 1979.
8.Романовский В.П. Справочник по холодной штамповке. – Л.:Машиностроение, 1979.
Название: Оборудование производства ИУ
Раздел: Рефераты по технологии
Тип: реферат
Добавлен 21:28:38 01 августа 2005 Похожие работы
Просмотров: 255
Комментариев: 16
Оценило: 4 человек
Средний балл: 5
Оценка: неизвестно Скачать
Срочная помощь учащимся в написании различных работ. Бесплатные корректировки! Круглосуточная поддержка! Узнай стоимость твоей работы на сайте 64362.ru
Если Вам нужна помощь с учебными работами, ну или будет нужна в будущем (курсовая, дипломная, отчет по практике, контрольная, РГР, решение задач, онлайн-помощь на экзамене или "любая другая" учебная работа...) - обращайтесь: https://clck.ru/P8YFs - (просто скопируйте этот адрес и вставьте в браузер) Сделаем все качественно и в самые короткие сроки + бесплатные доработки до самой сдачи/защиты! Предоставим все необходимые гарантии.
Привет студентам) если возникают трудности с любой работой (от реферата и контрольных до диплома), можете обратиться на FAST-REFERAT.RU , я там обычно заказываю, все качественно и в срок) в любом случае попробуйте, за спрос денег не берут)
Да, но только в случае крайней необходимости.
Реферат: Оборудование производства ИУ
Доклад по теме Мужчины терпеть не могут женщин, не любящих получать оральный секс
Реферат: Стратегическая модель Портера: стратегии ценового лидерства, дифференциации и концентрации
Контрольная работа по теме Память человека
Реферат: Генезис и основные вехи в развитии философии экстремальности. Скачать бесплатно и без регистрации
Контрольная работа по теме Создание теста на Visual Basic
Краткое Сочинение Обломов
Реферат На Тему Византийская Культура
Вексель Как Форма Безналичных Расчетов Курсовая
Реферат: Adventures Of Huckleberry Finn 2 Essay Research
Контрольная работа по теме Управление документооборотом
Реферат: Животноводство и земледелие
Реферат: Цилиндр. Скачать бесплатно и без регистрации
Реферат по теме Республика Марий Эл. Рафтинг
Доклад: Бизнес-план открытия нового магазина женской одежды в городе Невьянске
Реферат На Тему Физическая Культура В Семье
Реферат К Дипломной Работе Образец
Реферат: Обработка материалов полевых измерений в разомкнутом теодолитном ходе
Курсовая работа по теме Право собственности на жилые помещения. Приватизация жилья
Сочинение: Образ Пьера Безухова в романе Л.Н.Толстого
Курсовая Работа Маркетинговая Стратегия
Реферат: Жизнь и творчество Дэвида Духовны
Реферат: Доколумбовы цивилизации Америки
Реферат: Эволюционный миф и современная наука