Разработка технологии изготовления цилиндрического аппарата. Курсовая работа (т). Другое.
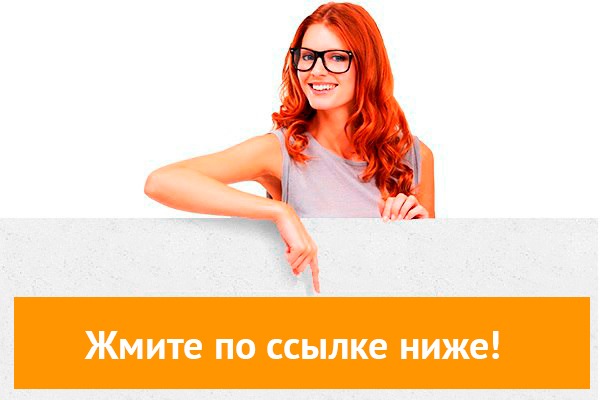
💣 👉🏻👉🏻👉🏻 ВСЯ ИНФОРМАЦИЯ ДОСТУПНА ЗДЕСЬ ЖМИТЕ 👈🏻👈🏻👈🏻
Вы можете узнать стоимость помощи в написании студенческой работы.
Помощь в написании работы, которую точно примут!
Похожие работы на - Разработка технологии изготовления цилиндрического аппарата
Скачать Скачать документ
Информация о работе Информация о работе
Скачать Скачать документ
Информация о работе Информация о работе
Скачать Скачать документ
Информация о работе Информация о работе
Скачать Скачать документ
Информация о работе Информация о работе
Скачать Скачать документ
Информация о работе Информация о работе
Скачать Скачать документ
Информация о работе Информация о работе
Скачать Скачать документ
Информация о работе Информация о работе
Нужна качественная работа без плагиата?
Не нашел материал для своей работы?
Поможем написать качественную работу Без плагиата!
Тема:
"Разработка технологии изготовления цилиндрического аппарата"
Курсовая работа содержит: 48 страниц, 12 рисунков, 1 приложение.
Объект исследования - цилиндрический аппарат.
Цель работы: закрепить теоретические знания и приобрести навыки решения
инженерных задач по разработке технологии изготовления цилиндрического
теплообменного аппарата, работающего под давлением.
В курсовой работе приведено описание типовых технологических процессов
изготовления элементов аппарата, порядок их выполнения и оснастка для них. Для
элементов корпуса приведены развертки.
РАСКОНСЕРВАЦИЯ, ПРАВКА, РАЗВЕРТКА, РАЗМЕТКА, РЕЗКА, ВАЛЬЦЕВАНИЕ, СВАРКА,
КАЛИБРОВАНИЕ, СБОРКА.
3.1 Расчет развертки корпуса цилиндрического (813-КЦ)
.2 Расчет развертки рубашки обогрева цилиндрической (813-РЦ)
.3 Расчет развертки патрубков (813-П-400 и 813-П-200)
.4 Расчет развертки корпуса конического и конической рубашки
обогрева (КК и РК)
.4.1 Расчет конического корпуса (813-КК)
.4.2 Расчет рубашки обогрева конической (813-РК)
.5 Расчет развертки ребер жесткости (813-РЖ)
.6 Расчет развертки эллиптической крышки (813-ЭК)
4.
Предварительный выбор оборудования
5.1 Расконсервация механическая, химическая
.1 Подготовка кромок, сборка и сварка заготовок
.4 Калибрование (правка) и подгибка кромок (отбортовка)
.7 Разметка, выполнение отверстий и скосов
цилиндрический теплообменный патрубок фланец
В химической промышленности широкое распространение получили
цилиндрические аппараты.
Их используют в качестве теплообменных агрегатов, емкостей для хранения и
аппаратов, в которых протекают различные химические реакции.
По причине высоких температур и давлений в этих аппаратах, они являются
потенциальными источниками опасности. Опасность заключается в том, что при
возможной аварии их содержимое попадает в окружающую среду.
Технология машиностроения рассматривает методы разработки и построения
рациональных технологических процессов, выбор способа получения заготовки,
технологического оборудования, инструмента и приспособлений, назначение режимов
резания и установление технически обоснованных норм времени.
Основной задачей данной курсовой работы является изучение
технологического процесса изготовления цилиндрического аппарата,
сконструированного ранее, а также типовых технологических процессов и их
оснастки.
Необходимо изготовить цилиндрический аппарат из материала 12Х18Н10Т. В
зависимости от параметров (расчетного движения и температуры стенки) и
характера рабочей среды сосуды подразделяются на группы. При рабочем давлении
1,6 МПа и температуре рабочей среды 200˚С данный аппарат относится к
первой группе. Толщина стенки, эллиптической крышки и конического днища 10 мм.
Место соединения цилиндрической и конической части аппарата утолщения не имеет.
Толщина стенки рубашки обогрева 10 мм.
Патрубки диаметром 200 мм и 400 мм необходимые для подачи/удаления
рабочей среды и патрубок диаметром 400 мм, выполняющий функцию лаза,
изготавливают из листа толщиной 10 мм, патрубки для подачи пара в рубашку
обогрева диаметром 80 мм изготавливают из обрезков труб.
Аппарат изготавливают по принципу единичного производства. Листы металла,
для изготовления элементов аппарата, выбирают исходя из габаритов аппарата и
элементов.
Труба диаметром 200 мм, толщиной стенки 10 мм
Труба диаметром 80 мм, толщиной стенки 10 мм
.1 Расчет развертки корпуса цилиндрического (813-КЦ)
Применительно к ним расчетными размером является длина развертки по периметру
цилиндрической части с внутренним диаметром из стали толщиной , определяемая по диаметру
нейтральной поверхности :
Так как элементы должны быть изготовлены с повышенными требованиями к их
точности:
где - фактическая толщина листа, мм;
- допускаемое отклонение формы поперечного сечения
(овальность);
- припуск на обработку кромок, мм;
= 0,02 - величина усадки сварного шва, мм.
Высота цилиндрической части обечайки составляет 3200 мм, а внутренний
диаметр 2000 мм. Определяем длину заготовки:
Для изготовления цилиндрического элемента необходима заготовка с
размерами 3200´6345.
Изготовим обечайку из заготовки, имеющие следующие размеры: 813-КЦ размером L =
6345 мм; В = 3200 мм.
.2 Расчет развертки рубашки обогрева цилиндрической (813-РЦ)
Высота цилиндрической части рубашки обогрева составляет 3000 мм, а
внутренний диаметр 2200 мм. Определяем длину заготовки:
Для изготовления цилиндрической рубашки необходима заготовка размерами
30406976. Изготовим обечайку из заготовки, имеющую следующие размеры:
813-РЦ размером L = 6976 мм; В =3040 мм.
.3 Расчет развертки патрубков (813-П-400 и 813-П-200)
Длина патрубка 813-П-200 составляет 480мм, общая длина патрубков 813-П-400 равна 900мм.
Высота патрубка B=900
для (813-П-400),а для Æ 200 (813-П-200) B=480.
Для изготовления цилиндрических элементов необходимо: прокатная листовая
сталь с размерами 2х1600´6400 для 813-КЦ, 2´1500´7000 для
813-РЦ, для патрубков 813-П-200 и 813-П-400: 664´480 и 1295´900.
.4 Расчет развертки корпуса конического и конической рубашки обогрева (КК
и РК)
Рисунок 3.1 - Параметры развертки конического днища для корпуса (813-КК)
и рубашки обогрева (813-РК)
.4.1 Расчет конического корпуса (813-КК)
Размеры плоской заготовки конической обечайки (813-КК) рассчитывают по
следующим формулам:
где b 0 - высота конической части, мм. b 0 = 1250 мм; 1
- радиус аппарата, мм. Для аппарата диаметром 2 м R 1 = 1000 мм; 2
- радиус патрубка, мм. Для патрубка диаметром 400мм R 2 =200 мм.
Радиусы развертки (без учета отбортовки):
Коническая часть в месте крепления к корпусу имеет отбортовку. Величина
отбортовки 110 мм, следовательно:
Выберем стандартный лист для изготовления конической обечайки 813-КК с
размерами 1100х2000 толщиной 10мм.
.4.2 Расчет рубашки обогрева конической (813-РК)
Размеры плоской заготовки конической обечайки рубашки обогрева (318-РК): 0
- высота конической части, мм. b 0 = 1250 мм; 1 - радиус
аппарата, мм. Для аппарата диаметром 2200мм R 1 = 1100 мм; 2
- радиус патрубка, мм. Для патрубка диаметром 400мм R 2 = 200 мм.
Коническая часть в месте крепления к корпусу имеет отбортовку с двух
сторон. Принимаем величину отбортовки 110 мм. Следовательно:
Выберем стандартный лист для изготовления конической обечайки рубашки
обогрева 813-РК с размерами 1250х2000 толщиной 10мм.
Конические обечайки имеют непараллельные образующие, поэтому круговая
гибка конуса между цилиндрическими валками приводит к отклонению линий изгиба с
направлением образующих. Для согласования их и получения правильной формы
конуса необходимо гибку конических обечаек выполнять на вальцах с коническими
валками, вершина которых совпадала бы с вершиной угла конуса заготовки. Однако
такие условия требуют значительного усложнения конструкции и удорожания ее.
При изготовлении конических деталей аппаратов пользоваться листогибочными
машинами с цилиндрическими валками. Для этого осуществить наклон верхнего
(среднего) валка у симметричной трехвалковой машины или бокового валка у
асимметричной трех- и четырехвалковой машин.
.5 Расчет развертки ребер жесткости (813-РЖ)
Аппарат имеет пять ребер жесткости, которые имеют форму колец. Толщина
ребра жесткости составляет 10 мм, внутренний диаметр 2000 мм, внешний диаметр
2190 мм.
Рисунок 3.2 - Ребро жесткости и его развертка
Размеры заготовок ребер жесткости (813-РЖ) определяются по формулам:
Для снижения расхода металла на его изготовление, ребро делится на четыре
равные части.
.6 Расчет развертки эллиптической крышки (813-ЭК)
Эллиптическая крышка изготавливается из круга. Размеры развертки
определяются по формулам изложенным в ГОСТ 6533-78. Диаметр развертки днища с
внутренним базовым размером:
- высота цилиндрической части днища;
- коэффициент, который выбирают по графику.
где - технологический припуск на обработку
Заготовка диаметром 2600 мм не может быть вырезана из листа целиком,
вырезаем 2 части.
Элементы колец жесткости расположим на (813-РЖ1) листе с размерами 2000´8000 мм. На этом же листе расположим
и цилиндрические части патрубков (813-П200 и 813-П400) подачи/удаления
материала, смотрового люка (лаза) и эллиптическую крышку (813-ЭК).
4. Предварительный выбор оборудования
Исходя из марки стали и толщины стенки аппарата необхордимо
перед пластическими деформациями листов осуществлять предварительный нагрев их
до температуры, близкой к температуре рекристализации.
Для вальцовки целесообразно применять трехвалковые
листогибочные машины, так как они позволяют вальцевать и циллиндрические, и
конические обечайки.
Крышки можно изготовлять штамповкой на прессах, методом обкатки роликами,
электромагнитной штамповкой, ручным выдавливанием на станках и ручной
выколоткой. Наибольшее распространение в промышленности находят два первых
способа изготовления крышек. В нашем случае при диаметре корпуса 2 м для изготовления
эллиптической крышки целесообразно использовать метод обкатки роликами.
Так как стальные листы поставляются в смазке и могут иметь некоторые
дефекты, первой технологической операцией является расконсервация. Она состоит
из таких операций:
. Механическое удаление густых, консервационных смазок (пушечного сала,
солидола, вазелина и др.), бумаги и пленок металлическими, деревянными,
пластмассовыми и резиновыми скребками.
. Промывание горячей водой (70 - 90 0 С) в струйных камерах для
снятия оставшихся после первой операции консервационных смазок.
. Просушка обдувкой сжатым воздухом для удаления запахов растворителей и
влаги.
. Протирка насухо ветошью или салфетками.
. Струйная очистка стальной дробью, металлическим песком, рубленной
проволокой, абразивными порошками для удаления глубокой коррозии, царапин,
трещин, окалины, шлака, местных расслоений на большой плоскости с
шероховатостью Rz 20.
. Гидропескоструйная очистка для удаления глубокой коррозии, царапин,
трещин, окалины, шлака, местных расслоений на большой плоскости с
шероховатостью Rz 0.4 и
последующей сушкой.
Для выполнения этих работ листовой прокат транспортируют на плиточный
стенд или на специально оборудованные настилы, покрытые деревом или пластиком
для предохранения от повреждения поверхности. Для транспортирования используют
стандартные листовые захваты и скобы. Места коррозии и дефекты обнаруживают
просмотром поверхностей через лупу и отмечают эти места мелом для последующего
удаления. Если слой консервационной смазки не позволяет выявить дефекты, то с
листов ее удаляют металлическими, пластмассовыми, деревянными или резиновыми
скребками или ветошью.
Данный этап работ должен обеспечить:
. Наличие и сохранение маркировки завода-поставщика материала и
соответствие ее сертификату.
. Отсутствие вкатанных окалин, шлака, волосовин, рисок, углублений,
царапин, трещин, местных расслоений, разнотолщинности, превышающих минусовые
предельные отклонения.
. Удаление консервационной смазки, затрудняющей обработку листа
вследствие понижения трения и ухудшения условий труда. Удаление мест
значительной коррозии.
. Проверку неровности листов и принятие решения о необходимости правки.
Листовой прокат имеет отклонения от геометрической формы вследствие
отступления от оптимальной технологии производства и неудовлетворительных
результатов правки на листопрокатных заводах, а также из-за нарушения
нормальных условий хранения проката на складах, погрузочно-разгрузочных и
транспортных операций на заводах.
Правка в аппаратостроении осуществляется для уменьшения или устранения
кривизны, серповидности, коробоватости (волнистости листа в продольном и
поперечном направлениях). Она контролируется стрелой прогиба на 1 м длины.
По соответствующим стандартам на листовой прокат (ГОСТ 19904-74 и ГОСТ
5520-69) для тонколистовой стали обыкновенного качества допускается кривизна
или коробоватость в пределах 15 мм на 1 м длины.
Правку листов в аппаратостроении преимущественно выполняют на
листоправильных роликовых машинах. Эти машины по сравнению с правильными
прессами имеют большую производительность при почти полном исключении ручного
труда. Правка на роликовых машинах представляет собой процесс многократного
знакопеременного пластического изгиба в обрабатываемом металле при напряжениях,
превосходящих предел текучести. Лист выправляется остаточной деформацией,
образуемой многократным знакопеременным изгибом листа при его прохождении между
роликами в прямом и обратном направлениях.
Для полного выпрямления листы пропускают через вальцы от 3 до 5 раз. В
машинах типа А (конструкции СКМЗ) с параллельными рядами правильных роликов
верхний ряд роликов регулируется вертикальным перемещением подвижной траверсы,
к которой прикреплены подшипники правильных и опорных роликов. Эти машины просты
по конструкции, но имеют существенный недостаток - равномерно искривляют лист
при выходе.
Для правки листов из стали Ст3 толщиной 14 мм и шириной до 1800 мм можно
применять листоправильную машину типа А с девятью роликами диаметром 260 мм
расположенных с шагом 300 мм.
При правке на данной машине траверса с верхними роликами опускается вниз
параллельно или наклонно к нижним роликам.
Расстояние между верхними и нижними валками при правке листа определяется
по формуле:
где: S - толщина стенки, мм, S=10 мм;
Е - модуль упругости, МПа, Е=1,9*10 5 МПа;
σ Т - предел текучести, МПа, σ Т =202 МПа;- расстояние между валками листоправильной
машины, мм, t≈500 мм.
Необходимо установит зазор между роликами 6,5 мм для листа толщиной 10
мм.
Настройку машины ведут по таблицам, указывающим деления циферблата в
зависимости от толщины выправляемого листа и требуемой деформации.
Операцию перенесения необходимых для изготовления детали размеров с
рабочего чертежа (813-КЦ, 813-РЦ) или образца на металл с учетом припусков для
последующем обработки называют разметкой. Разметку различают поверхностную и
пространственную.
Поверхностную разметку выполнять методом геометрических построений; по
шаблону; оптическим методом; с помощью приспособлений.
Пространственную разметку в аппаратостроении выполняют по пространственным шаблонам; с помощью
специальных приспособлений и устройств: комбинированным способом.
В химическом аппаратостроении вследствие индивидуального и мелкосерийного
характера производства, наиболее распространена разметка методом геометрических
построении с помощью универсальных приспособлений, для пространственной
разметки и шаблонов. Различают два метода разметки: камеральный - перенос
размеров на материал по предварительно разработанным в бюро эскизам: плановый -
разметка в натуральную величину непосредственно на металле, расположенном
на специально подготовленной плоскости - плазе; этот метод применить для
сложных и крупногабаритных деталей аппаратов.
При разметке обычными измерительными и разметочными инструментами,
устанавливаемыми "на глаз", степень точности разметки находится в
пределах 0,2-0,5 мм. При использовании инструмента с большей степенью точности
(штангенциркулей, штангенрепсмусов, индикаторов, угломеров с нониусом, синусных
линеек, точных кернеров) точность разметки составляет от 0,1-0,3 мм. И только
разметка на специальных разметочно-сверлильно-расточных станках может иметь
точность до = 0,01 мм.
При разметке нанести и прокернить следующие линии, необходимые для
вырезки контроля точности деталей: контрольные контуры детали, контуры выреза и
отгиба, припусков, фасок и скосов, центров закругления прямоугольных вырезов и
отверстий
В производстве разметку или наметку на листе произвести не одной детали,
а нескольких. В этих случаях от расположения размеченных заготовок зависит
эффективность использования листа, т. е. расход материала на заготовки.
Расположение заготовок деталей на бумаге или материале называют раскроем.
Различают три способа раскроя листов; индивидуальный, смешанный и групповой.
Рациональный раскрои позволяет не только уменьшать расход материала, но и ускорять
изготовление заготовок. При большой номенклатуре выпускаемых изделий и
разнообразии форм и размеров их заготовок для обеспечения рационального раскроя
требуется много времени и расчетов.
В настоящее время задача рационального раскроя решается использованием
метода линейного программирования и ЭВМ.
Сущность резки заключается в отделении части материала от входного
проката, поковки или отливки с целью получения заготовок, для удаления лишнего
припуска в деталях или подготовка кромок под сварку. Разделительную резку
металлов выполняют двумя способами: механическим (холодным) и тепловым
(термическим, огневым).
Механическая резка может быть двух видов: без снятия стружки
(гильотинные, дисковые, комбинированные пресс-ножницы), и со снятием стружки
(отрезание резцом, фрезерование, резка дисковой пилой). По производительности
процесса и затратам на технологические материалы предпочтительной является
резка без снятия стружки.
Из всех способов тепловой резки, резка металлов с использованием электрической
дуги имеет ряд преимуществ перед газокислородной и кислородно-флюсовой резкой.
Например, она позволяют резать металлы и сплавы, не разрезаемые кислородом,
более безопасны и производительны, позволяют использовать стандартное
электросварочное оборудование.
Сам процесс является разновидностью кислородной резки низкоуглеродистых,
низколегированных и термоупрочненных сталей, обеспечивающей низкую
шероховатость поверхности реза и повышенные механические свойства металла в
месте резания при которых исключается последующая обработка кромок.
Кромки под сварку подготавливают для получения заданной геометрической
формы кромки и удаления дефектного слоя с измененными структурой и свойствами,
появившегося на предшествующих операциях. Форма кромок обеспечивает правильное
формирование сварного шва и может быть различной. Форма, размеры и отклонения
кромок под сварку должны соответствовать стандартам, требованиям чертежа и
технологическим условиям. Способы подготовки кромок свариваемых деталей должны
исключать механическое повреждение кромок.
Подготовка кромок абразивным кругом предусматривает зачистку с двух
сторон поверхности листа в местах разделки кромок и будущей сварки на ширине 40
мм от торцов. Кромки зачищаем до полного удаления окалины и ржавчины, трещин.
Операцию выполняем на плиточном стенде с использованием электрической
шлифовальной машины С-475 с применением шлифовальных кругов плоских
прямоугольного профиля.
Подготовку кромок фрезерованием выполняем на заготовках, надежно
закрепляемых на столах универсально- , продольно- и вертикально-фрезерных
станков. В качестве инструмента для фрезерования кромок используют фрезерные
головки, торцевые, концевые, цилиндрические, дисковые и фасонные фрезы.
Фрезерованием подготавливаем заготовки 813-ЭК 2 штуки (стороны b =2600 мм), 813- РК 2 штуки (стороны b = 900 мм),
813-КК 2 штуки (стороны b =960 мм), 813-РЖ 15 штук (стороны b =940 мм), 813-КЦ
(сторона b = 6345 мм), 813-РЦ (сторона b = 6976 мм).
Заготовки под сварку следует собирать на выверенных стеллажах,
обеспечивающих точное взаимное положение элементов и их фиксацию. При сборке
стыкуемые элементы выравнивают по упорам или при помощи линейки и угольника, а
необходимый зазор в стыке получают при помощи кронштейна, толщина стенки
которого соответствует величине зазора между заготовками. При стыковых
соединениях элементов разной толщины необходимо предусмотреть плавный переход
от одного элемента к другому путем постепенного утонения более толстого
элемента в соответствии с ГОСТ 8713-70, ГОСТ 5264-69, а в случаях, не
предусмотренных стандартами, угол скоса элементов разной толщины должен быть не
более 15°. После сварки эти планки срезают механическим способом или газовым
пламенем.
а) схема сборки стыкового соединения;
б) схема выравнивания стыкуемых листов
Стыкуемые листы в горизонтальной плоскости выравнивают при помощи
клиньев. При сборке не допускается подгонка кромок, вызывающая дополнительные
напряжения в металле и повреждение металла. Закрепляют стыкуемые детали
механическими, магнитными или пневматическими прижимами, обеспечивающими
плоскостность стыкуемых кромок. Одновременно со сборкой стыкового соединения
устанавливают технологические планки для начала и окончания сварки шва. Для
соединения плоских разверток (813-ЭК, а также 813-РЖ 3 раза) применяем
электродуговую автоматическую сварку.
Операцию вальцевания или круговую гибку выполняют в холодном состоянии до
пределов, не вызывающих явления наклепа и роста зерна в результате
рекристаллизации. Гибка является пластической деформацией металла путем
непрерывного перемещения заготовки - это обработка между деформирующими валками
давлением при напряжении более предела текучести.
Рисунок 7.2 - Схема гибки конической обечайки на трехвалковой машине
Вальцевание выполняем на трехвалковой листогибочной машине с симметричным
расположением валков. Вальцуются следующие заготовки - 813-КЦ, 813-КК, 813-РЦ,
813-РК, 813-П-200, 813-П-400.
Рисунок 7.3 - Подгибка кромок в трехвалковой машине
Она является наиболее простой по конструкции, однако не обеспечивает
подгибку кромок. Передняя и задняя кромки листа остаются прямыми на длине,
равной половине расстояния между нижними валками. Схема гибки обечаек приведена
на рис. 7.4.
Рисунок 7.4 - Схема гибки обечайки на трехвалковой листогибочной машине с
симметричным расположением валков и вертикальной регулировкой верхнего валка
Эта операция предусматривает работу по сборке продольного стыка обечаек
под сварку и должна обеспечить: удобное и надежное положение обечайки под сварку,
необходимый зазор под сварку в месте стыка, качественную подготовку стыкуемых
кромок, нормированные смещения кромок по длине и по торцам.
Используемая для этих целей установка (рис. 7.5) имеет роликоопору 1,
портальную раму 2, две гидравлические струбцины 4 для совмещения и соединения
продольных кромок, выдерживая зазор под сварку и смещение кромок, а также
стяжку 5 для выравнивания торцевых кромок. Струбцины 4 с помощью пружинных
подвесок 6 закреплены на тележках 7, передвигающихся по раме 2. На этих же
тележках закреплены и панели управления 3. В современных струбцинах винты
заменены гидроцилиндрами - двумя зажимными 8, одним выравнивающим 9 и одним
стягивающим 10.
Рисунок 7.5 - Установка для сборки продольных стыков обечаек (I-III - встречные движения гидроцилиндров и штоков; Iа-IIIа - соответствующие движения кромок)
При сборке продольного стыка обечаек (813-КЦ, 813-КК, 813-РЦ, 813-РК,
813-П-200, 813-П-400) обечайки устанавливаем на роликоопорах - приводных, холостых
или рычажных. При этом продольный стык должен находиться в верхнем положении.
Сначала устанавливают на торцах обечайки крюки винтовых или гидравлических
стяжек для выравнивания торцов, закрепляют с двух сторон стяжные струбцины.
Затем выравниваем зазор - под сварку, размечаем места прихватки, после чего
очищаем их от коррозии, масел, грязи и обезжириваем. Прихватываем стык
электродуговой сваркой с последующей его зачисткой. При сборке продольных
стыков необходимо соединить кромки стыка, совместив их в одной касательной
плоскости и выровнять торцевые кромки.
Отбортовке подлежат следующие заготовки 813-КК, 813-РК, 813-РЦ - верхняя
часть. Правке подвергают обечайки с жестким контуром . Эти обечайки не прогибаются под
собственной массой. Формы поперечного сечения нежестких обечаек исправляют с помощью установки
разжимных приспособлений непосредственно перед сборкой и сваркой кольцевых
швов. Многообразие обечаек по типоразмерам и маркам металлов вызвало
необходимость применения различных методов правки: на валковых листогибочных
машинах, гидрораздачей на прессах - расширителях, радиальным растяжением и
энергией взрывчатых веществ. В химическом аппаратостроении наибольшее
распространение находит метод правки обечаек на валковых листогибочных машинах.
Наибольшее влияние на точность радиуса и формы поперечного сечения
обечаек после их правки оказывают первоначальный диаметр, величина радиуса
изгиба, форма контура и толщина обечайки. Для получения по всему круговому
контуру одинаковой кривизны необходимо, чтобы при вращении обечайки между
валками радиус изгиба (в процессе правки) был меньше радиуса кривизны любого
участка по контуру обечайки. Это условие является основным для точной правки.
Оптимальной формой в местах подгибки кромок считают прямые участки или
участки, несколько вогнутые внутрь. Различная кривизна участков по контуру
обечайки и усиления сварного шва усложняют процесс правки. Кривизна контура
должна быть одинаковой или иметь небольшие отклонения, а внутренний сварной шов
обязательно зачищается. Для большей точности правки все технологические и
силовые параметры следует рассчитывать исходя из фактической толщины листа. Для
правки обечаек используют трехвалковые и четырехвалковые листогибочные машины.
Правка на четырехвалковых машинах обеспечивает более высокую точность обечаек -
наименьшую погрешность формы поперечного сечения.
Правка обечайки на трехвалковых машинах. Эту операцию выполняют в
следующей последовательности: выверяют параллельность валков, устанавливают
деталь, выставляют средний и боковые валки для получения определенного радиуса
правки и выкатывают - калибруют обечайки в течение трех-четырех оборотов с
последующим медленным разводом валков и съемом обечайки с машины. При
калибровании обечайки сварочные швы не зачищаются. Для получения более точных
(отклонение менее 0,01 D в ) обечаек
перед правкой следует снимать усиление внутреннего сварного шва обечайки.
Правка конических обечаек имеет особенности, изложенные выше при описании
их гибки. Для правки конических обечаек рекомендуется применять специальное
приспособление.
Для обеспечения ориентации заготовки в процессе правки за базу принимают
кромку заготовки, образующую малый диаметр конуса. Приспособление устанавливают
пластинами 2 на верхний валок машины. От поворота на верхнем валке
приспособление удерживается двумя щеками 4 , охватывающими нижний валок 5
листогибочной машины. На корпусе 1 приспособления закреплены два базовых
опорных ролика 3 . Заготовку устанавливают на машину таким образом, что
ее передняя кромка опирается на базовые ролики приспособления и зажимается
между верхним и нижним валками машины. При движении заготовки опорный ролик 3
со стороны входящего края заготовки постоянно разворачивает ее, создавая момент
реактивных сил, равный моменту сил трения между листом и валками машины. При
реверсировании вращения аналогично работает симметрично расположенный ролик.
Лучшим вариантом правки конических обечаек является применение машин с
конусными валками. При этом верхний валок машины является сменным, вследствие
чего достигается высокое качество правки обечаек различных типоразмеров.
Рисунок 7.5 - Приспособление для правки конусов на четырехвалковых
После калибровки необходимо еще раз проверить сваренные швы обечаек. В нашем случае это обечайки
813-КК, 813-РЦ, 813-РК.
В сварных соединениях не допускаются следующие наружные дефекты: трещины
всех видов и направлений; свищи и пористость наружной поверхности шва; подрезы,
наплывы, прожоги и незаплавленные кратеры; смещение и совместный увод кромок
свариваемых элементов выше норм; несоответствие форм и размеров швов требованиям
стандартов, технических условий или чертежей на изделие.
Не допускается в сварных соединениях внутренние дефекты: трещины вех
видов и направлений, расположенные в металле шва, по линии сплавления и в
околошовной зоне основного металла, в том числе и микротрещины; непровары,
расположенные в сечении соединения (между отдельными валками и слоями шва и
междду основным металлом и металлом шва); свищи; поры в виде сплошной сетки;
единичные шлаковые и газовые включения по группе А (ГОСТ 7512-75) глубиной свыше
10% от толщины стенки; цепочки пор шлаковых включений по группе Б (ГОСТ
7512-75), имеющих суммарную длину дефектов более тлщины стенки на участке шва,
равном десятикратной толщине стенки, а также имеющие отдельные дефекты с
размерами, превышающими указанные выше; скопление газовых пор и шлаковых
включений по группе В (ГОСТ7512-75) в отдельных участках шва свыше 5 шт. на 1
см 2 площади шва; максимальный линейный размер отдельного дефекта по
наибольшей протяженности не должен превосходить 1,5 мм, а сумма их линейных
размеров не должна быть более 3 мм.
Дефекты сварки удаляются механически с помощью шлифовальных и эльборовых
кругов, фрез, зубил, металлических щеток.
Эту операцию (рис. 7.6) выполняют для подрезки торцов в размер по длине
обечайки и перпендикулярно образующей ее, а также для снятия фасок под сварку.
Обработки на токарно-карусельном станке требуют круговые кромки на
цилиндрических и конических: 813-КЦ, 813-КК, 813-РЦ, 813-РК, 813-П-200,
455-П-400.
Рисунок 7.6 - Схема подрезки торцов обечайки.
В тех случаях, когда обечайка имеет искаженную цилиндрическую форму
поперечного сечения или может деформироваться при закреплении ее кулачками на
столе станка, применяют разжимные приспособления: радиальные распорки и
разжимные кольца. Эти приспособления позволяют исправить погрешность фо
Похожие работы на - Разработка технологии изготовления цилиндрического аппарата Курсовая работа (т). Другое.
Лекция по теме Задачи и проблемы международного менеджмента
Темы Итогового Сочинения 2022 По Регионам
Курсовая работа по теме Финансовая система РФ и ее роль в стабилизации экономики
Дипломная работа по теме Финансовые ресурсы предприятия их формирование и эффективное использование
Реферат по теме Политическое и социально-экономическое совершенствование Германских земель в XIV-XV вв. Ганзейский союз
Курсовая работа по теме Оценка состояния социальной сферы Приднестровской Молдавской Республики
Реферат: Дидактичні основи процесу навчання
Реферат: УЧПУ. Скачать бесплатно и без регистрации
Реферат по теме Загрязнение атмосферы как одна из важнейших экологических проблем современности
Реферат по теме Схожесть и различия характера и деятельности Воланда и Мефистотеля
Курсовая работа по теме Понятие и особенности удержания
Сочинение На Тему Мое Представление О Будущем
Автореферат На Тему Метаболізм Заліза Та Диференційована Корекція Його Порушень У Дітей Раннього Та Дошкільного Віку, Хворих На Залізодефіцитну Анемію
Отчет Производственной Практики В Отделе Мвд
Сочинение Образ Самсона Вырина 7 Класс
Реферат: Избирательное право и избирательные системы 3
Дипломная работа по теме Права и обязанности субъектов нотариального права
Реферат: Уравнение Шредингера, его свойства.
Реферат: Пропозиції щодо реформування чинного українського правопису
Контрольная работа по теме Особенности принятия решений в сфере управления персоналом
Реферат: Эмоции и их роль в жизни человека 2
Похожие работы на - Организация расследования изнасилований
Реферат: Факультет: Кибернетики Кафедра: Биомедицинская Электроника работа “Расчёт асцитной гепатомы Зайдела” Дисциплина: “Моделирование в медицине”