Разработка технологического процесса механической обработки шестерни ведущей. Курсовая работа (т). Другое.
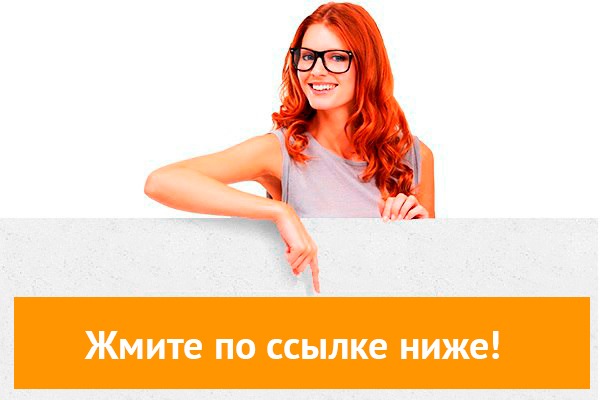
💣 👉🏻👉🏻👉🏻 ВСЯ ИНФОРМАЦИЯ ДОСТУПНА ЗДЕСЬ ЖМИТЕ 👈🏻👈🏻👈🏻
Вы можете узнать стоимость помощи в написании студенческой работы.
Помощь в написании работы, которую точно примут!
Похожие работы на - Разработка технологического процесса механической обработки шестерни ведущей
Скачать Скачать документ
Информация о работе Информация о работе
Скачать Скачать документ
Информация о работе Информация о работе
Скачать Скачать документ
Информация о работе Информация о работе
Скачать Скачать документ
Информация о работе Информация о работе
Скачать Скачать документ
Информация о работе Информация о работе
Скачать Скачать документ
Информация о работе Информация о работе
Скачать Скачать документ
Информация о работе Информация о работе
Нужна качественная работа без плагиата?
Не нашел материал для своей работы?
Поможем написать качественную работу Без плагиата!
Федеральное
государственное образовательное учреждение
высшего
профессионального образования
Новоуральский
технологический институт НИЯУ МИФИ
Разработка
технологического процесса механической обработки шестерни ведущей
. Исходные
данные по проекту и их анализ
.1 Описание и
конструкторско-технологический анализ объекта
.1.1
Назначение детали, краткие сведения
.1.4
Декодирование конструкторского кода детали шестерня ведущая
.1.5
Технологический код детали шестерня ведущая
.
Проектно-технологическая разработка
.1 Выбор вида
заготовки и метод её получения
2.2
Определение припусков на механическую обработку
.2.1
Определение исходного индекса поковки
.2.2 Определение
припусков на механическую обработку
.3 Разработка
маршрутного технологического процесса обработки заготовки и выбор оборудования
2.4
Определение промежуточных припусков, технологических размеров и допусков
.4.1
Аналитический метод определения припусков
.4.2
Статистический метод определения припусков
.5 Размерный
анализ технологического процесса
. Разработка
технологических операций
.1 Разработка
технологических переходов и выполнение операционных эскизов
.2.1 Режимы
резания при точении (0,15; 0,25)
.2.2 Режимы
резания при фрезеровании (0,10; 0,30)
.2.3 Режимы
резания при растачивании (0,35)
.2.4 Режимы
резания при шлифовании (0,50; 055; 060)
.4 Выбор и
определение потребного количества оборудования
В данной курсовой работе темой проекта является "Разработка
технологического процесса изготовления шестерни ведущей".
В ходе проектирования на первом этапе необходимо было подобрать методы
получения заготовки, посчитать технико-экономические показатели, себестоимость
продукции, а также другие затраты, которые не вошли в расчёты, и выбрать один,
который будет наиболее эффективным и рациональным.
На основе годовой программы выпуска 2500шт. изделий определяем тип
производства, такт выпуска.
Следующим этапом разработки курсового проекта будет разработка
маршрутного технологического процесса для данной детали. Необходимо обозначить
все операции, которые должны участвовать при изготовлении детали, а также
подобрать соответствующее оборудование, которое будет наиболее оптимальным из
выбранного нами источника.
Научимся определять припуски с помощью аналитического и статистического
методов, а также ещё припуски на механическую обработку. В размерном анализе с
помощью метода графов рассчитаем величину конструкторских размеров, припусков и
допусков, необходимых в изготовлении детали.
При разработке технологических операций мы нашли все параметры,
участвующие в режиме резания данной операции, и последним этапом в курсовой
работе определили необходимое количество оборудования на каждой операции.
1. Исходные данные по проекту и их анализ
.1 Описание и конструкторско-технологический анализ объекта
.1.1 Назначение детали, краткие сведения
В данном курсовом проекте используется чертёж вала-шестерни ведущей из
стали 25ХГТ ГОСТ 4543-71, который служит для установки сопрягаемых деталей и
передачи вращающего момента. Вал устанавливается в корпусе с помощью двух
подшипников Æ50 мм и Æ55 мм. Вращение передается через
зубчатое соединение.
Точность обработки имеют следующие поверхности:
Поверхности 2, 3, 7, 8, 13, 16, 17 - 6 квалитет
Все остальные размеры свободные по 14 квалитету.
Радиальное биение поверхностей 3, 7, 8 и 16 относительно баз А и Б
составляет 0,03 мм.
Радиальное биение поверхности 12 относительно баз А и Б составляет 0,15
мм.
Отклонение от круглости на поверхностях 2 и 17 составляет 0,01.
Шероховатость поверхностей 2, 3, 7, 8, 13, 16, 17 составляет Ra 1.25, а
остальные поверхности с шероховатостью Ra 12.5.
.1.2 Материал детали и его свойства
Химические и механические свойства стали 25ХГТ приведём в таблице 1.1 и
1.2
Таблица 1.1 - химические свойства стали 25ХГТ
Таблица 1.2 - механические свойства стали 25ХГТ
Твердость: HRC 57-63; цементация 920-950 0 C - воздух; закалка
840-860 0 C - масло; отпуск 190-210 0 C - воздух.
а) Качественный анализ технологичности
Поверхность детали удобна для обработки. Она представляет собой в
основном совокупность цилиндрических и торцевых поверхностей, не требующих
сложной формы заготовки и инструмента.
Допуски и шероховатость поверхностей назначены обосновано.
б) Количественный анализ технологичности
Для данной оценки надо рассчитать два коэффициента (показатели по
признакам обработки):
К т ч - коэффициент точности обработки;
К ш - коэффициент шероховатости поверхности.
где, Тi - квалитет (точность);i - число поверхностей детали одинакового
квалитета.
где, mi - число поверхностей детали с одинаковым параметром
шероховатости;i - параметр шероховатости поверхности детали
Вывод: Значение полученных коэффициентов близко к единице, что
свидетельствует о не высокой точности большинства поверхностей детали и большой
шероховатости их. Это также подтверждается средними значениями квалитета
точности и шероховатости.
.1.4 Декодирование конструкторского кода детали шестерня ведущая
Для возможности разработки и внедрения унифицированных ТП на основе
группирования деталей необходимо кодирование деталей с использованием
конструкторско-технологического кода детали.
Описание детали выполняется по рабочему чертежу детали и служит для
лучшего усвоения конструкции детали. Краткое первоначальное описание детали по
основным конструкторским элементам можно получить путем декодирования
конструкторского кода детали.
Декодирование конструкторского кода детали, таблица 1.5. Задан чертеж
шестерни ведущей (рисунок 1.1); ее обозначение ТМ.151001.КП.ШВ-10.00.00. Для
декодирования используем источник [1].
Таблица 1.5 - декодирование конструкторского кода детали
Результат декодирования и
пояснения
Класс деталей по
классификатору ЕСКД тела вращения типа валов, осей, колонок и т.п. с элементами
зубчатого зацепления
Подкласс деталей тела
вращения, у которых длина примерно равна 2-м диаметрам, с наружными
цилиндрическими поверхностями.
Группа деталей без закрытых
уступов с поверхностью ступенчатой двухсторонней без наружной резьбы.
Подгруппа деталей без
центрального отверстия, причем наличие технологических центровых отверстий не
учитывается.
Вид деталей с пазами (или
шлицами) на наружной поверхности и без отверстий вне оси детали.
.1.5 Технологический код детали шестерня ведущая
Пользуясь приложениями источника [2] запишем технологический код детали:
Точность детали - это точность размеров, точность геометрической формы и
точность относительного расположения поверхностей. Принимаем во внимание и
величину шероховатости поверхности, как параметр, увязываемый с точностью.
Объект анализа - вал-шестерня на рисунке 1.1. На рисунке 1.2 дан эскиз
вала шестерни ведущей с нумерацией поверхностей. Результаты анализа приведены в
таблица 1.6.
В таблице 1.6 также заложены точность размера, точность формы и
шероховатость поверхности.
Рисунок 1.1 - Чертеж шестерни ведущей
Рисунок 1.2 - Эскиз шестерни ведущей с нумерацией поверхностей
Таблица 1.6 - Данные о поверхностях
предварительно проточить
окончательно шлифовать
предварительно подрезать
окончательно шлифовать
предварительно подрезать
окончательно шлифовать
предварительно проточить
окончательно шлифовать
предварительно проточить
окончательно проточить
предварительно нарезать
зубья, окончательно шлифовать зубья
предварительно подрезать
окончательно шлифовать
предварительно проточить
окончательно шлифовать
На основе годовой программы 2500 штук и массы детали 10.06 кг необходимо
приблизительно установить вид производства.
Исходя из массы детали и годовой программы, принимаем среднесерийное
производство (таблица 1.7).
Таблица 1.7 - выбор типа производства.
Для серийного производства определяется партия запускаемых деталей:
где n запуска - партия запускаемых деталей, штук;=2500шт. - годовая
программа;
- число рабочих дней в году;- число дней запаса, в течение которых должны
быть заготовлены детали. Эта величина колеблется в пределах 5-8 дней.
Такт выпуска определяется по формуле:
где FD - действительный годовой фонд времени работы оборудования, равный
2030 часам.
2. Проектно-технологическая разработка
.1 Выбор вида заготовки и метода ее получения
Деталь - шестерня ведущая. Материал - сталь 25ХГТ.
Годовой объем выпуска N=2500 штук/год.
Факторы, определяющие выбор заготовки:
· материал детали - сталь 25ХГТ (конструкционная сталь);
· конфигурация детали - вал с буртиками;
· тип производства - среднесерийное.
Для получения данной заготовки в условиях среднесерийного производства
можно применить поковку, изготовляемую горячей объёмной штамповкой на
горизонтально - ковочных машинах с соответствующей термообработкой и
последующей очисткой. Рациональнее при этом типе производства выбрать
заготовку, форма которой максимально приближена к форме готовой детали (рис.
2.1). Это сведет к минимуму обработку резанием и отходы в стружку.
На рисунке 2.1 изображен упрощенный эскиз заготовки.
Рис. 2.1 - упрощенный эскиз заготовки
Если Dmax < L, то для деталей типа втулок рациональнее выбрать горячую
объемную штамповку на ГКМ. Предельная длина отверстия при штамповке на ГКМ до
трех диаметров.
С учетом применения газопламенного нагрева класс точности поковки Т5 по
ГОСТ 7505-89.
.2 Определение припусков на механическую обработку
.2.1 Определение исходного индекса поковки
Факторы, определяющие исходный индекс заготовки, который является ключом
к нахождению общих припусков и допусков для поковок:
1. Расчетная масса поковки Мп.р., кг.
. Степень сложности С1, С2, СЗ, С4.
. Класс точности. для штамповки на ГКМ Т4 и Т5.
Приведем формулу определения расчетной массы поковки [2].
где Мд - масса детали (определяется по чертежу), кг;
Кр - расходный коэффициент. Для деталей круглых в плане (ступицы,
шестерни и т.п.) - Кр = 1,5-1,8.
Примем Кр=1,8. Тогда Мп.р. = 10,06·1,8=18,108 кг.
Группы стали определяются по процентному содержанию углерода: М1 - до
0,35%; М2 - (0,35-0,65)%; М3 - 0,65% и более [2]. В нашем случае для стали
25ХГТ группа стали будет М2.
Степень сложности определяют, находя отношение объема Vп - поковки к
объему VФ - элементарной геометрической фигуры, в которую вписывается поковка.
Либо можно взять отношение расчетной массы поковки Мп.р. к массе элементарной
геометрической фигуры Мф. Для нашего случая это будет цилиндр. Габаритные
размеры детали (Dmax и Н) необходимы при расчете. Будем определять степень
сложности по отношениям масс. Ориентировочные размеры элементов фигуры
определяется увеличением в 1,05 раза.
Это соответствует [2] С2 (диапазон 0,32-0,63).
Для Мп.р. = 10,06 кг (10,0-20,0), М2 идем по горизонтали до C2, далее
спускаемся по наклонной до вертикали С2 и снова движемся по горизонтали до Т4 и
опять спускаемся по наклонной до вертикали Т5 и по горизонтали выходим на
индекс 17.
.2.2 Определение припусков на механическую обработку
В таблицах [2] припуски заданы на сторону. Величина припуска будет
определяться:
2. Размером, связывающим поверхности.
. Шероховатостью поверхностью готовой детали.
. Способом формирования поверхностей, связанных линейным размером.
Эти же факторы, кроме третьего, будут определять и величину допустимого на
размеры отклонения.
Общий припуск на механическую обработку включает в себя основной и
дополнительный припуски. Определение основных припусков отражено в табл. 2.1.
Дополнительные припуски в табл. 2.2. Учитывают смещение поковок, изогнутость,
отклонение от плоскостности и прямолинейности. Определение размеров, допусков и
предельных отклонений исходной заготовки приведено в табл. 2.3
Таблица 2.1 - Определение основных припусков
Таблица 2.2 - Определение общих припусков и расчетных размеров исходной
заготовки
Таблица 2.3 - Назначение допусков, предельных отклонений и определение
размеров исходной заготовки.
Таблица 2.4 - Определение этапов и методов обработки поверхностей.
Стартовый вариант маршрута
.3 Разработка маршрутного технологического процесса обработки заготовки и
выбор оборудования
В таблице 2.3 приведен маршрутно-операционный технологический процесс
Таблица 2.3 - Маршрутно-операционный технологический процесс
Наименование операции,
оборудование
Фрезерно-центровальная,
станок мод. 6Р83
Фрезеровать торцы 1 и 18,
сверлить центровые отверстия по эскизу.
Токарно-винторезный
(черновая), станок мод. 16К20
Точить поверхности 2, 6 и
торец 3 по эскизу; Переустановить; Точить поверхности 8, 12, 15, 17 и торцы
7, 9, 11, 14, 16 по эскизу.
Токарно-винторезный
(получистовая), станок мод. Commodor E230
Поправить центральные
отверстия; Точить поверхности 2, 4 и торцы 3, 5 по эскизу; Выполнить канавку;
Переустановить; Точить поверхности 8, 12, 17 и торцы 7, 9, 11, 14, 16 по
эскизу; Выполнить канавку и радиусы по эскизу.
Зубофрезерная (предварительная),
станок мод. 5Д32
Фрезеровать поверхность
зубьев 13 по эскизу.
Координатно-расточная,
станок мод. 2450
Цементировать h1..h1,4мм;
Калить поверхность зубьев ТВЧ 59..63 HRC.
Круглошлифовальная
(предварительная), станок мод. 3151
Шлифовать поверхности 2, 3,
7, 8, 12, 16, 17 по эскизу за два установа.
Круглошлифовальная
(окончательная), станок мод. 3151
Шлифовать поверхности 2, 3,
7, 8, 16, 17 по эскизу за два установа.
Шлифовать поверхность
зубьев 13 по эскизу.
Выполнение всех операций
согласно технологическому процессу. Контроль геометрических параметров;
контроль за отсутствием забоин и острых кромок.
.4 Определение промежуточных припусков, технологических размеров и
допусков
.4.1 Аналитический метод определения припусков
Для определения припусков, используем методику [5, стр. 175] со следующим
порядком расчёта:
Односторонний припуск при последовательной обработке противолежащих
поверхностей рассчитывается по формуле:
глубина дефектного поверхностного слоя;
отклонение расположения поверхности;
Двусторонний припуск при обработке наружных и внутренних поверхностей
рассчитывается по формуле:
2) Расчётный минимальный размер определяется по следующим формулам:
2.) Допуск на изготовление определяется по таблице, в зависимости от
квалитета и размера.
3.) Принятые размеры по переходам :
Округление производится до того же знака десятичной дроби, с каким дан
припуск на размер для каждого перехода.
5.) Полученные предельные припуски:
Результаты расчётов припусков сведены в таблицу 2.4.1.
Таблица 2.4.1 - Расчёт припусков по диаметрам поковки
Элементарная поверхность и
технологический маршрут её обработки
Определяем расчетно-аналитическим методом припуск для обработки
поверхностей 2, 6, 8, 12, 15,17. Расчет выполняется по ГОСТ 7505-89.
Таблица 2.5 - Карта расчета припусков на обработку и предельных размеров
по технологическим переходам
Элементарная поверхность
детали и технологический маршрут ее обработки
Принятые (округленные)
размеры по переходам, мм
.4.2 Статистический метод определения припусков
При статистическом методе определения промежуточных припусков на
обработку поверхностей заготовки используются таблицы технологического
справочника [6].
Результаты заносим в таблицу 2.4.2.
Минимальный припуск по
табличным данным, мм
Точение черновое Точение
чистовое Шлифование предвар. Шлифование окончат.
Точение черновое Точение
чистовое Шлифование предвар. Шлифование окончат.
Точение черновое Точение
чистовое Шлифование предвар. Шлифование окончат.
2.5 Размерный анализ технологического процесса
Размерный анализ технологического процесса выполняется с помощью метода
графов.
В соответствии с принятым технологическим процессом производится
размерный анализ детали. Конструкторские K и технологические L размеры, а также
размеры заготовки L и припуски Z показаны на рисунке 2.5.1.
По схеме рисунка 2.5.1. составляем граф, представленный на рисунке 2.5.2,
2.5.3 по которому составляются расчётные уравнения, приведённые в таблице
2.5.4.
Рисунок 2.5.1 - Размерная схема технологического процесса
Метод графов показан на рисунках 2.5.2, 2.5.3.
Назначения допусков приведены в таблице 2.5.4.
Выявление размерных цепей показано в таблице 2.5.5.
Таблица 2.5.5 Выявление размерных цепей
Последовательность вершин
производного графа
108; 142; 163; 27; 9; 181;
10; 180; 109
Результаты определения промежуточных припусков показаны в таблице 2.5.6.
Таблица 2.5.6 Промежуточные припуски на обработку торцов
Определяем колебание и максимальное значение
припуска
Где ωZi -колебание припуска;- допуск на линейный размер.
Где ωZi -колебание припуска;, max - минимальное и
максимальное значение i-го припуска
Рассчитываем колебание и максимальное
значение припуска
2. ωZ28=TL1+TL2+TL8+TL9+TL10=5,6+4,0+0,3+0,3+0,12=10,32
Z28max=Z28min+ ωZ28=1,8+10,32=12,12
3. ωZ29=TL10+TL16=0,12+0,046=0,166
Z29max=Z29min+ ωZ29=0,55+0,166=0,716
4. ωZ30=TL16+TL22=0,046+0,019=0,065
Z30max=Z30min+ ωZ30=0,3+0,065=0,365
5. ωZ70=TL17+TL23=0,054+0,022=0,076
Z70max=Z70min+ ωZ70=0,3+0,076=0,376
6. ωZ71=TL11+TL17=0,140+0,054=0,194
Z71max=Z71min+ ωZ71=0,55+0,194=0,744
7. ωZ72=
TL1+TL2+TL3+TL8+TL11=5,6+4,0+3,6+0,3+0,14=13,64
Z72max=Z72min+ ωZ72=1,8+13,64=15,44
8. ωZ90=TL12+TL18=0,300+0,300=0,600
Z90max=Z90min+ ωZ90=0,45+0,600=1,050
9. ωZ91=TL1+TL2+TL4+TL8+TL12=5,6+4,0+3,6+0,3+0,300=13,8
10. ωZ109=TL1+TL2+TL5+TL6+TL7+TL8+TL9+TL13=5,6+4,0+4,0+3,6+5,0+0,3+0,3+
+0,3=23,1
Z109max=Z109min+ ωZ109=1,3+23,1=24,4
Z110max=Z110min+ ωZ110=0,45+0,6=1,05
Z140max=Z140min+ ωZ140=0,45+0,6=1,050
13. ωZ141=TL1+TL2+TL6+TL7+TL8+TL14=5,6+4,0+3,6+5,0+0,3+0,3=18,8
Z141max=Z141min+ ωZ141=1,3+18,8=20,1
14. ωZ160=TL21+TL24=0,046+0,019=0,065
Z160max=Z160min+ ωZ160=0,25+0,065=0,315
15. ωZ161=TL15+TL21=0,12+0,046=0,166
Z161max=Z161min+ ωZ161=0,45+0,166=0,616
16. ωZ162=TL1+TL2+TL7+TL8+TL15=5,6+4,0+5,0+0,3+0,12=15,02
Z162max=Z162min+ ωZ162=1,3+15,02=16,32
Конструкторский размер, обеспеченный технологическим процессом
представлен в таблице 2.5.7
Таблица 2.5.7 Учет полученных запасов точности
Конструкторский размер
обеспеченный Т.П.
Рассчитываем допуска линейных размеров
К1=TL9=0.3К2=TL9+TL22=0.3+0.019=0.319К3=TL9+TL22+TL23=0.3+0.019+0,022=0.341К4=TL9+TL18+TL22=0.3+0.3+0.019=0.619К5=TL9+TL19+TL20=0.3+0.3+0.3=0.9К6=TL20+TL24=0.3+0.019=0.319К7=TL9+TL22+TL24=0.3+0.019+0.019=0.338
Расчеты размерных цепей представлены в таблице 2.5.8.
Таблица 2.5.8 Расчет размерных цепей
. TL23=BOL23-HOL23=-0,32-(-0,34)=0,02
. TL18=BOL18-HOL18=-0,32-(-0,62)=0,3
. TL24=BOL24-HOL24=-0,32-(-0,34)=0,02
. TL20=BOL20-HOL20=-0,02-(-0,32)=0,3
. TL16=0,046max=L16min+TL16=205,82+0,046=205,866
. TL10=0,12max=L10min+TL10=206,416+0,12=206,536
. TL17=0.054max=L17min+TL17=55,48+0,054=55,534
. TL11=0,14max=L11min+TL11=56,084+0,14=56,224
Расчет одиннадцатой размерной цепи:
. TL12=0,3max=L12min +TL12=71,63+0,3=71,93
. TL14=0,3max=L14min+TL14=187,93+0,3=188,23
. TL21=0,046max=L21min +TL21=209,43+0,046=209,476
Расчет четырнадцатой размерной цепи:
. TL15=0,12max=L15min +TL15=209,926+0,12=210,046
. TL8=0,3max=L8min +TL8=252,3+0,3=252,6
Расчет шестнадцатой размерной цепи:
. TL19=BOL19-HOL19=-0,28-(-0,58)=0,3
. TL1=5,6max=L1min +TL1=253,9+5,6=259,5
Расчет восемнадцатой размерной цепи:
1. Z28min=L1min+L9min-L2max-L8max -L10max
. 1,8=253,9+250,7-L2max-252,6-206,536
. L2max=253,9+250,7-252,6-206,536-1,8=43,664
. TL2=4,0min=L2max-TL2=43,664-4,0=39,664
Расчет девятнадцатой размерной цепи:
. Z72min=L8min +L2min+L3min-L11max -L1max
2. 1,8=252,3+39,664+L3min-56,224-259,5
. L3min=-252,3-39,664+56,224+259,5+1,8=25,56
. TL3=3,6max=L3min +TL3=25,56+3,6=29,16
. Z91min=L8min +L2min+L4min-L12max -L1max
2. 1,3=252,3+39,664+L4min-71,93-259,5
. L4min=-252,3-39,664+71,93+259,5+1,3=40,766
. TL4=3,6max=L4min +TL4=40,766+3,6=44,366
Расчет двадцать первой размерной цепи:
4. TL13=0,3max=L13min +TL13=138,67+0,3=138,97
Расчет двадцать второй размерной цепи:
1. Z162min=L8min +L2min+L7min-L15max -L1max
. 1,3=252,3+39,664+L7min-209,926-259,5
. L7min=-252,3-39,664+209,926+259,5+1,3=178,762
. TL7=5,0max=L7min +TL7=178,762+5,0=183,762
Расчет двадцать третей размерной цепи:
1. Z141min=L8min +L2min+L7min-L14max -L1max -L6max
. 1,3=252,3+39,664+178,762-188,23-259,5-L6max
. L6max=252,3+39,664+178,762-188,23-259,5-1,3=21,696
. TL6=3,6max=L6min +TL6=21,696+3,6=25,296
Расчет двадцать четвертой размерной цепи:
1. Z109min=L5min +L6min+L1min+L9min -L7max -L2max -L8max
-L13max
. 1,3= L5min +21,696+253,9+250,7-183,762-43,664-252,6-138,97
. L5min=1,3-21,696-253,9-250,7+183,762+43,664+252,6+138,97=94,0
. TL5=4,0max=L5min +TL5=94,0+4,0=98,0
3. Разработка технологических операций
.1 Разработка технологических переходов и выполнение операционных эскизов
В приложениях данной пояснительной записки представлены операционные
эскизы в последовательности выполнения технологических операций (см. далее).
Произведём расчёты для режимов резания при токарной обработке (операция
015; 025), фрезеровании (операция 010; 030), координатно-расточной (операция
035), шлифовальная (операция 050; 055; 060). Результаты расчётов сведены в
таблицы 3.2.1.1, 3.2.1.2, 3.2.2.1, 3.2.2.2, 3.2.3, 3.2.4.1, 3.2.4.2, 3.2.4.3.
.2.1 Режимы резания при точении (0,15; 0,25)
Методика расчета приведена в источнике [5].
Принимаем равной припуску обработки.
Принимаем согласно табличным данным.
3). Скорость резания вычисляем по формуле:
) Силу резания вычисляем по формуле:
). Мощность резания вычисляем по формуле:
6.) Частоту вращения детали при обработке вычисляем по формуле:
Таблица 3.2.1.1 - Результаты расчётов для операции 015
№ поверхности детали на
рассчитываемой операции
Согласно расчётным данным принимаем станок: токарно-винторезный 16К20.
Таблица 3.2.1.2 - Результаты расчётов для операции 025
№ поверхности детали на
рассчитываемой операции
Согласно расчётным данным принимаем станок: токарно-винторезный Commodor
E230.
3.2.2 Режимы резания при фрезеровании (0,10; 0,30)
1.) Глубина фрезерования принимаем по чертежу.
.) Подача . Принимаем согласно табличным данным.
.) Скорость резания вычисляем по формуле:
.) Сила резания , H вычисляем по формуле:
.) Мощность резания N, кВт вычисляем по формуле:
.) Частоту вращения инструмента при обработке вычисляем по формуле:
Таблица 3.2.2.1 - Результаты расчётов для операции 010
№ поверхности детали на
рассчитываемой операции
Согласно расчётным данным принимаем станок: фрезерно-центровальный 6Р83.
Проведем расчет для операции 030 (зубофрезерная):
Методика расчета приведена в источнике [5].
1). Глубину резания принимаем по чертежу.
2). Подача . Принимаем согласно табличным данным.
). Скорость резания вычисляем по формуле:
4). Частоту вращения инструмента при обработке вычисляем по формуле:
5). Мощность резания вычисляем по формуле:
Таблица 3.2.2.2 - Результаты расчётов для операции 030
№ поверхности детали на
рассчитываемой операции
Согласно расчётным данным принимаем станок:
.2.3 Режимы резания при растачивании (0,35)
Методика расчета приведена в источнике [5].
Принимаем равной половине диаметра отверстия.
Принимаем согласно табличным данным.
). Скорость резания вычисляем по формуле:
4). Крутящий момент , Нм вычисляют по формуле:
). Мощность резания вычисляем по формуле:
6). Частоту вращения детали при обработке вычисляем по формуле:
Таблица 3.2.3 - Результаты расчётов для операции 035
№ поверхности детали на
рассчитываемой операции
Согласно расчётным данным принимаем станок: координатно-расточной 2450.
.2.4 Режимы резания при шлифовании (0,50; 055; 060)
Методика расчета приведена в источнике [5].
Таблица 3.2.4.1 - Результаты расчётов для операции 050
№ поверхности детали на
рассчитываемой операции
Согласно расчётным данным принимаем станок: круглошлифовальный 3151.
Таблица 3.2.4.2 - Результаты расчётов для операции 055
№ поверхности детали на
рассчитываемой операции
Согласно расчётным данным принимаем станок: круглошлифовальный 3151.
Методика расчета приведена в источнике [5].
1). Глубину резания принимаем по чертежу.
2). Подача . Принимаем согласно табличным данным.
3). Скорость резания вычисляем по формуле:
4). Частоту вращения инструмента при обработке вычисляем по формуле:
5). Мощность резания вычисляем по формуле:
Таблица 3.2.4.3 - Результаты расчётов для операции 060
№ поверхности детали на
рассчитываемой операции
Согласно расчётным данным принимаем станок: зубошлифовальный 5715.
Для определения затрачиваемого времени на каждую операцию предлагается
следующая последовательность расчёта:
1). Определение основного времени:
где основное время отдельного перехода данной операции, мин.
где длина обрабатываемой поверхности, ;
2). Определение вспомогательного времени:
вспомогательное время на установку и снятие детали, ;
вспомогательное время, связанное с переходом, ;
вспомогательное время на контрольные измерения, .
3). Определение оперативного времени:
Таблица 3.3.1. Определение оперативного времени для операций
технологического процесса.
Операция 010.
Фрезерно-центровальная.
2. Фрезеровать торец 1
окончательно
3. Фрезеровать торец 18
окончательно
2. Фрезеровать 14 зубьев
(m=6) пов. 13 предварительно
Операция 035.
Координатно-расточная.
2. Расточить 12 отверстий (ø10,2) пов.19 окончательно
2. Шлифовать 14 зубьев
(m=6) пов. 13 окончательно
4). Определение вспомогательного времени с учётом поправочного
коэффициента:
По карте 1 определяется поправочный коэффициент на вспомогательное время
в зависимости от размера партии обрабатываемых деталей и оперативного времени.
5). Определение времени на обслуживание рабочего места и отдых:
где время на обслуживание рабочего места принимается в % от
оперативного времени, ;
время перерывов на отдых и личные надобности принимается в %
от оперативного времени, .
6). Определение подготовительно-заключительного времени на 1 деталь:
Нормативами подготовительно-заключительного времени предусматривается
выполнение следующей работы:
а) наладка станка, инструмента и приспособлений;
в) получение инструмента, приспособлений и сдачу их после окончания
обработки.
где подготовительно-заключительное время на партию деталей, ;
7). Определение нормы штучного времени:
Определение штучного времени предусматривает калькуляционное время на
операцию:
8). Штучно-калькуляционное время Tш-к для шлифовальных операций в
серийном производстве будет
Результаты расчётов нормирования операций сведены в таблицу 3.3.2.
Таблица 3.3.2 - Нормативы времени на обработку детали
Суммарное время обработки Т = 45,39 мин.
3.4 Выбор и определение потребного количества оборудования
1). Коэффициент загрузки станка
где расчётное количество станков, ;
2). Коэффициент использования оборудования по основному времени
). Коэффициент использования станков по мощности привода
где необходимая мощность привода станка для обработки
(расчётная), ;
мощность привода станка по паспорту, .
Результаты расчётов сведены в таблицу 3.4.1.
Таблица 3.4.1 - Данные по использованию оборудования
Коэфф. использования
оборудования по tо, в %
Коэфф. использования
станков по мощности, в %
Графики зависимости использования оборудования в процентном соотношении
представлены на рисунках 3.4.1, 3.4.2, 3.4.3.
Рисунок 3.4.1 - График загрузки оборудования
Рисунок 3.4.2- График использования оборудования по основному времени
Рисунок 3.4.3 - График использования оборудо
Похожие работы на - Разработка технологического процесса механической обработки шестерни ведущей Курсовая работа (т). Другое.
Дипломная работа по теме Крупный бизнес в рыночной экономике
База Данных Склад Товаров Курсовая Работа
Исследовательские Работы Практическая Часть
Примеры Настоящей Любви Из Литературы Для Сочинения
Контрольная Работа Страница
Правильный Реферат
Реферат по теме Византия в VI в. Окончание войны с готами
Курсовая Молочная Промышленность
Дипломная работа: Фармацевтическая химия стероидных гормонов
Типичные Ошибки Работодателя Реферат
Реферат: Биологическое действие радиоактивных излучений
Купава Огинская Практическая Работа
Дипломная Работа На Тему Правовое Регулирование Использования Участков Лесного Фонда
Контрольная работа: Налоги в системе государственного регулирования экономики
Найти Готовую Курсовую Работу
Контрольная работа: Формирование ресурсов банками США. Управление активами американских банков
Курсовая работа по теме Информационные правоотношения
Реферат: Командующий Каспийской военной флотилией Раскольников. Скачать бесплатно и без регистрации
Реферат: Разрушение личности
Курсовая работа: Преступления против общественного порядка. Скачать бесплатно и без регистрации
Похожие работы на - Государственное регулирование предпринимательства
Реферат: Виникнення фотографії
Похожие работы на - Исследование концептов в лингвистике