Разработка технологического процесса для детали 'корпус'. Дипломная (ВКР). Другое.
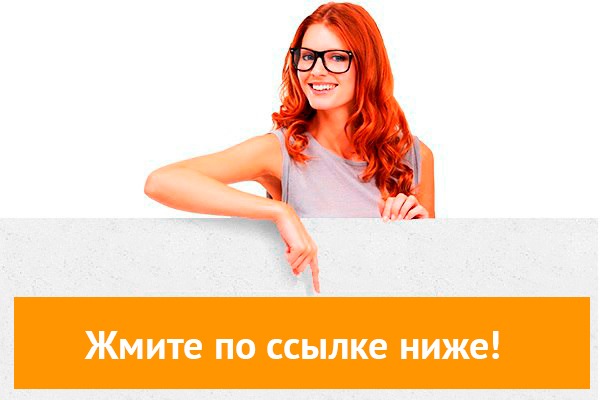
👉🏻👉🏻👉🏻 ВСЯ ИНФОРМАЦИЯ ДОСТУПНА ЗДЕСЬ ЖМИТЕ 👈🏻👈🏻👈🏻
Вы можете узнать стоимость помощи в написании студенческой работы.
Помощь в написании работы, которую точно примут!
Похожие работы на - Разработка технологического процесса для детали 'корпус'
Скачать Скачать документ
Информация о работе Информация о работе
Скачать Скачать документ
Информация о работе Информация о работе
Скачать Скачать документ
Информация о работе Информация о работе
Скачать Скачать документ
Информация о работе Информация о работе
Скачать Скачать документ
Информация о работе Информация о работе
Скачать Скачать документ
Информация о работе Информация о работе
Нужна качественная работа без плагиата?
Не нашел материал для своей работы?
Поможем написать качественную работу Без плагиата!
1.1 Описание и технологический анализ детали "Корпус"
2.1 Существующий технологический процесс изготовления детали
2.2 Определение типа производства и величины партии деталей
2.5Разработка технологического процесса изготовления детали
2.6 Краткая характеристика оборудования
2.7 Расчёт режимов резания на одну операцию расчетно-аналитическим
методом
2.8 Выбор режимов резания и их корректировка для остальных операций
по общемашиностроительным нормативам
2.10 Таблицы режимов резания и норм времени
2.11 Разработка управляющей программы на программную операцию
3.1 Расчёт специального режущего инструмента для поверхности
3.2 Расчёт специального контрольного инструмента для поверхности Ø80f7
4. Охрана труда и противопожарная безопасность
Технология машиностроения - область технической науки,
занимающаяся изучением связей и установлением закономерностей в процессе
изготовления машин. Она призвана разработать теорию технологического
обеспечения и повышения качества изделий машиностроения с наименьшей
себестоимостью их выпуска.
Объектом технологии машиностроения является технологический
процесс, а предметом - установление и исследование внешних и внутренних связей,
закономерностей технологического процесса.
Технологичность конструкции машины, как объекта производства.
. Технологические процессы, операции, установы,
позиции, технологические переходы и рабочие хода, обеспечивающие повышение
качества изделий и снижение их себестоимости.
. Математическое моделирование технологических
процессов и методов изготовления деталей и сборки изделий машиностроения.
3. Совершенствование существующих и разработка новых
методов обработки и сборки с целью повышения качества изделий машиностроения и
снижения себестоимости их выпуска.
. Методы проектирования и оптимизации технологических
процессов.
. Технологическая наследственность в машиностроении.
. Технологическое обеспечение и повышение качества
поверхностного слоя, точности и долговечности деталей машин.
. Проблемы управления технологическими процессами в
машиностроении.
Данный курсовой проект разрабатывался, как технологический
процесс изготовления детали "Корпус".
Важнейшие составляющие любого технического устройства -
корпусные детали. Они могут быть различны как по виду, по применяемому
материалу, так и по функциональному назначению.
Корпусные детали предназначены для крепления деталей
агрегата, имеют: отверстия, отверстия для установки подшипников, втулок,
вкладышей, валов, гильз, штифтов и резьбовые отверстия для крепления деталей;
плоскости и технологические плоскости. Общим конструктивно - технологическим
признаком для большинства корпусных деталей является наличие плоских
поверхностей и двух установочных отверстий, используемых в качестве
установочной базы, как при изготовлении, так и при восстановлении деталей
данного класса.
В процессе эксплуатации корпусные детали подвергаются
химическому, тепловому и коррозионному воздействию газов и охлаждающей
жидкости, механическим нагрузкам от переменного давления газов, динамическим
нагрузками, вибрации, контактным нагрузкам, влиянию абразивной среды и т.д. Для
данного класса деталей основными видами износа являются
коррозионно-механический и молекулярно-механический, которые характеризуются
следующими явлениями - молекулярным схватыванием, переносом материала,
разрушением возникающих связей, вырыванием частиц и образованием продуктов
химического взаимодействия металла с агрессивными элементами среды.
Любое сложное устройство может состоять из сотен или тысяч
(иногда - десятков тысяч) деталей, и детали корпусов - одни из самых сложных,
ответственных, дорогих изделий. Особенно это касается таких деталей, как
элементы коробок передач (шестерни, валы, втулки, подшипники, прокладки),
элементы трансмиссии, мосты. В случае если речь идет о промышленных механизмах
и установках - узлы передачи вращающего момента, ротационные узлы машин
(турбин, насосов, электродвигателей) также относятся к числу наиболее
ответственных и технологически трудных для изготовления.
Деталь - "Корпус" предназначена для закрепления
деталей.
Деталь изготовлена из стали 45 ГОСТ 1050-88. Сталь 45 - Сталь
конструкционная углеродистая, для изготовления вал-шестерней, коленчатых и
распределительных валов, шестерен, шпинделей, бандажей, цилиндров, кулачков и
других нормализованных, улучшаемых и подвергаемых поверхностей.
Таблица 1 Химический состав Стали 45 в %
Таблица 2 Физико-механические свойства стали 45
Конструкция детали, точность размеров и шероховатость
поверхностей, материал детали обеспечивают удовлетворительную обрабатываемость
заготовки и надёжную работу детали в течение всего ресурса работы изделия.
Технологичность - это совокупность свойств изделия,
определяющих приспособленность его конструкции к достижению оптимальных затрат
ресурсов при его производстве, ремонте и утилизации. Анализ детали на
технологичность производится двумя методами: качественной и количественной
оценкой.
Конструкция корпуса обеспечивает свободный вход и выход
инструмента, и удобство выполнения обработки. Обрабатываемые поверхности
доступны для обработки.
Метод получения заготовки - штамповка, поэтому деталь можно
получить с минимальными припусками. Деталь невозможно обработать от одной базы,
деталь необходимо переворачивать. Вследствие большого перепада диаметров,
повышается трудоёмкость и расход материала. Возможно использование стандартного
режущего инструмента, т.к. имеются стандартные поверхности. Возможно
использовать унификацию, так как необходимо сделать фаски.
Количественную оценку технологичности конструкции детали
производят по следующим коэффициентам:
Коэффициент унификации конструктивных
элементов детали рассчитывается по формуле
где Q э. у. - число унифицированных элементов детали,
шт.; э. - общее число конструктивных элементов детали, шт.
Коэффициент использования материала рассчитывается по формуле
где Gд - масса детали по чертежу, кг;з - масса заготовки с
неизбежными технологическими потерями, кг
Низкий коэффициент использования материала и низкий коэффициент
унификации конструктивных элементов говорят о не технологичной конструкции
детали.
Существующий технологический процесс изготовления детали
отсутствует.
Для определения типа производства по
таблице 3 использовали массы деталей и годовой объём выпуска:=1,85 кг=48000 шт
Таблица 3. Зависимость типа производства
от объема выпуска и массы детали
Выбрали тип производства - среднесерийный.
Серийное производство - тип производства,
характеризующийся ограниченной номенклатурой изделий, изготавливаемых или
ремонтируемых периодически повторяющимися партиями, и сравнительно большим
объемом выпуска. Серийное производство является основным типом современного
производства, и предприятиями этого типа выпускается в настоящее время 75-80 %
всей машиностроительной продукции. По всем технологическим и производственным
характеристикам серийное производство занимает промежуточное положение между
единичным и массовым производством. Используется универсальное, специальное и
частично специализированное оборудование. Широко используются станки с ЧПУ,
обрабатывающие центры, находят применение гибкие автоматизированные системы
станков с ЧПУ, связанными транспортирующими устройствами и управляемых с
помощью ЭВМ. Технологическая оснастка, в основном универсальная. При
проектировании технологического процесса для серийного производства определяем
размер партии деталей.
Размер партии деталей определяется по
формуле
где N - годовая программа, шт;- число дней, на которое необходимо
иметь запас деталей, дн.;для мелких деталей массой меньше 2 кг, t=5÷10дн
- число рабочих дней в году, ф=253дн.
На выбор метода получения заготовки
оказывает влияние: материала детали, ее назначение и технические требования на
изготовление; объем и серийность выпуска; форма поверхностей и размеры детали.
Оптимальный метод получения заготовки определяет на основании
всестороннего анализа названных факторов и технико-экономического расчета
технологической себестоимости детали. Метод получения заготовки, обеспечивающий
технологичность изготавливаемой из нее детали, при минимальной себестоимости
последней считается оптимальным. Сравниваем два метода получения заготовки:
прокат и штамповка.
Штамповка - процесс пластической деформации материала с
изменением формы и размеров тела. Чаще всего штамповке подвергаются металлы или
пластмассы. Для процесса штамповки используются прессы - устройства, позволяющие
деформировать материалы с помощью механического воздействия.
Прокат - процесс обжатия слитка металла в горячем или
холодном состоянии между вращающимися валками прокатного стана, для получения
того или иного профиля.
При расчётах пользуемся литературой [3]
За основу расчёта промежуточных припусков выбираем наружный
диаметр 103Н14×100мм.
Диаметр заготовки определяется по формуле
где D дет - диаметр обрабатываемой
детали, мм;
z o - общий припуск на
обработку, мм
Длина заготовки определяется по формуле
где L дет - длина обрабатываемой детали, мм; 2z o
- общий припуск на обработку, мм
По ГОСТ 2590−88 выбираем допуски на размеры , ,
Объём заготовки определяется по формуле
где D - диаметр заготовки, мм- длина заготовки, мм
Масса заготовки определяется по формуле
где γ -
плотность материала, кг/см 3 ; V з - объем заготовки, см 3
Расход материала на одну деталь с учетом всех технологических
неизбежных потерь определяем по формуле
где G − масса заготовки, кг, 15% -неизбежные технологические
потери для проката
Коэффициент использования материала рассчитывается по формуле (2)
Стоимость заготовки из проката определяется по формуле
С з. п. =C м ·G з − (G з −G д )
·C отх , (9)
где С м − стоимость 1кг материала заготовки, руб.
С отх − стоимость 1 кг отходов, руб.
С з. п. = 12·8,63− (8,63−1,85) ·4=76,44руб
Масса детали m=1,85кг, Степень сложности С1
Точность изготовления штамповки − Iкл;
Размеры заготовки определяются по формулам (4,5)
22=22+1,2·2=24,4 мм, L55=55+1,3·2 =57,6 мм
80=80+1,3·2=82,6 мм, L30=30+1,2·2=32,4 мм
103=103+1,3·2=105,6 мм, L15=15+1,2·2=17,4 мм
Предельные отклонения на размеры заготовки определяем по ГОСТ
7505-89:
Объёмы отдельных элементов заготовки V 1 , V 2, V 3
определяются по формуле (6)
Общий объем заготовки рассчитывается по формуле
где V 1 ,V 2 ,V 3 -объёмы отдельных
элементов заготовки, см 3
Масса штампованной заготовки рассчитывается по формуле (7)
Принимаем неизбежные технологические потери при горячей объемной
штамповке равными 10% и определяем массу заготовки с учетом потерь по формуле
(8)
Коэффициент использования материала на одну штамповку определяется
по формуле (2)
Стоимость заготовки, изготовленная методом штамповки, определяется
по формуле (9)
Экономический эффект по использованию материала рассчитывается по
формуле
где G з1 - масса заготовки, полученная первым способом,
кг, G з2 - масса заготовки, полученная вторым способом, кг, - годовая
программа выпуска, шт.
Экономический эффект изготовления заготовки рассчитывается по формуле
где С з1 - стоимость заготовки, полученной первым
способом, руб.
С з2 - стоимость заготовки, полученной вторым способом,
руб. годовая программа, шт.
Э= (76,44-93,72) ·48000=829440 руб.
Таблица 4 Сравнительная таблица двух
методов получения заготовки
Коэффициент
использования материала
Экономический
эффект изготовления заготовки, руб
Расчеты показывают, что заготовка,
полученная методом горячей объемной, более экономична по массе, чем заготовка
из проката, поэтому принимаем заготовку, изготовленную методом штамповки.
Выбранный метод изготовления заготовки обеспечивает минимальные припуски на
механическую обработку заготовки и экономию материала за счёт этого. За счёт
уменьшения припусков на обработку снижается трудоёмкость изготовления детали.
При расчётах пользуемся литературой [3]
Расчёт припусков на поверхность можно
произвести двумя методами: табличным и расчётно-аналитическим методом, которые
приведены в таблицах 5 и 6.
Таблица 5 Расчёт припусков табличным методом
Вид заготовки и
переходы обработки пов-ти
Проверка: определяется разность
суммы максимального и минимального предельных припусков. Она должна быть равна
разности допусков заготовки и детали
где Тзаг - допуск на заготовку, мм;
Таблица 6 Расчётно-аналитический метод определения припусков
на обработку
Вид заготовки и переходы обработки пов-ти Точность
обрабат. пов-ти Элементы припуска, мкм Расчет. припуск
ммРасчет.
размер, ммДопуск Т, ммПред. размеры, ммПред. припуски, мм
Значение расчетного припуска определяется
по формуле
2Zmin i =2 [
(Rz+h) i-1 +√Δ i-1 2 + έ 2 i ] (14)
где Z min i - припуск для
расчетной операции или перехода, мм;
(Rz+h) i-1 - высота неровностей
для предшествующей операции или перехода, мкм; Δ i-1 - отклонение профиля для
предшествующей операции или перехода, мкм;
έ i - погрешность установки
для расчетной операции или перехода, мкм.
Проверка: определяется
разность суммы максимального и минимального предельных припусков. Она должна
быть равна разности допусков заготовки и детали.
где Тзаг - допуск на заготовку, мм; Т дет - допуск на деталь в мм;
Разрабатываем схему расположения полей припусков и допусков
(рисунок 2)
Рисунок 2 Схема расположения полей припусков и допусков
Заготовка - штамповка, материал заготовки - 45 ГОСТ 1050-88
. Точить Ø22f9 начерно и начисто;
точить фаску 1х45º
Оборудование: станок токарно-винторезный 16К20
Приспособление: самоцентрирующийся трёхкулачковый патрон
Режущий инструмент: проходной упорный резец Т5К10 ГОСТ
18869-73; проходной упорный резец Т15К6 ГОСТ 18869-73; проходной отогнутый
резец Т15К6 ГОСТ18868-73; сверло центровочное Ø2,5 ГОСТ 14952-75
Мерительный инструмент: ШЦІ 0,1,175 ГОСТ 166-80; калибр-скоба
Ø22f9 ГОСТ 18362-72
. Точить Ø80f7 на l=30 c припуском под
шлифование начерно и начисто; точить фаску 1х45º
Оборудование: станок токарный программный 16К20Ф3
Приспособление: самоцентрирующийся трёхкулачковый патрон с
пневмоприводом
Режущий инструмент: проходной отогнутый резец Т15К6 ГОСТ
18868-73; проходной упорный резец Т5К10 ГОСТ 18869-73; проходной упорный резец
Т15К6 ГОСТ 18869-73; канавочный резец Т14К8 ГОСТ 18884-73; сверло центровочное Ø5 ГОСТ 14952-75.
Мерительный инструмент: ШЦІ 0,1,175 ГОСТ 166-80
Оборудование: станок вертикально-фрезерный 6Р12
Приспособление: тиски машинные с гидроприводом
Режущий инструмент: фреза дисковая двухсторонняя со вставными
ножами из твердого сплава ГОСТ 6469-69
Мерительный инструмент: ШЦІ 0,1,175 ГОСТ 166-80
Оборудование: станок круглошлифовальный 3Б12
Режущий инструмент: круг шлифовальный 44А ШК 200х40 ГОСТ
28654-90
Мерительный инструмент: калибр-скоба Ø80f7 ГОСТ 18362-72
Учитывая тип производства (среднесерийный), годовую программу
выпуска - 48000 шт., а так же габариты детали выбираем следующее оборудование:
. Токарно-винторезный станок с ЧПУ модели 16К20Ф3
Выбор данного станка обусловлен характером обработки,
размерами рабочей поверхности, а так же его мощностью.
Применение станка с ЧПУ позволит уменьшить долю
вспомогательного времени, которое растрачивается в рассматриваемых операциях на
приёмы, связанные с изменением режимов резания, переходом с обработки одной
поверхности на другую, сменой режущего инструмента и т.п. Данный станок
позволяет обрабатывать нескольких аналогичных деталей, на одном станке и этим
сократит время на переналадку оборудования.
Техническая характеристика станка 16К20Ф3
Наиб. диаметр изделия, устанавливаемого над станинной: 500мм
Наиб. диаметр изделия, обрабатываемого изделия над станиной:
320мм
Наиб. ход суппорта поперечный: 210мм
Мощность привода главного движения: 11кВт
Габаритные размеры станка: 3700х2260х1650мм
Мощность привода главного движения: 11кВт
Масса станка (без стружкоудаления): 4000кг
. Токарно-винторезный станок модели 16К20
Станок предназначен для выполнения различных токарных работ,
а также для нарезания резьб.
Техническая характеристика станка 16К20
Наиб. диаметр изделия, устанавливаемого над станинной: 400мм
Наиб. Длины обрабатываемой заготовки: 710,1000,1400, 2000мм
Частота вращения шпинделя: 12,5−1600мин -1
Пределы подач продольных: 0,05−2,8 мм/об
Пределы подач поперечных: 0,025−1,4 мм/об
Габаритные размеры станка: 3795х1198х1600мм
. Вертикально-фрезерный станок модели 6Р12
Предназначен для выполнения разнообразных фрезерных работ при
обработке деталей любой формы из стали, чугуна, цветных металлов и их сплавов.
Перемещение стола: продольное (х) 800 мм;
Частота вращения основного шпинделя: 31,5−1600 об/мин;
Мощность главного двигателя: 7,5 кВт;
. Станок круглошлифовальный универсальный 3Б12
Полуавтомат предназначен для наружного шлифования цилиндрических и
пологих конических поверхностей в условиях серийного производства. Шлифование
производится в неподвижных центрах и в патроне
Класс точности станка по ГОСТ 8-82: П;
Диаметр обрабатываемой детали: 200 мм;
Пределы частоты вращения шпинделя: 2250-16750 об/мин
Габаритные размеры станка: 2650 1750 1750 мм;
Расчёт режимов резания производится по литературе [10]
Выбор времени производится по литературе [8], [9] 010Токарная
. Точить Ø22f9 начерно и начисто;
точить фаску 1х45º
Выбираем резец проходной отогнутый. Материал пластины -
твёрдый сплав Т15К6.
. Глубина резания при подрезке торца определяется по формуле:
где L заг - длина детали до
обработки, мм; д - длина детали после обработки, мм.
. Подача на оборот выбирается по [10]= 0.5мм/об
. Скорость резания расчетная определяется по формуле
где Т - среднее значение стойкости, мин; (Т=60мин).
,x,y,m-коэффициент и показатели степени, в зависимости от вида
обработки ( =350; х=0,15; y=0,35; m=0,2)
− общий поправочный коэффициент на скорость резания;
где − коэффициент, учитывающий влияние
физико-механических свойств обрабатываемого материала;
. Частота вращения шпинделя расчетная определяется по формуле
где V−скорость резания, м/мин− диаметр детали, мм
Корректируем частоту вращения по паспорту станка n п =630
. Скорректированная скорость резания определяется по формуле
где n−частота вращения, об/мин− диаметр детали, мм
где С р , x, y, n − коэффициент и показатели
степени
С р = 300, x = 1, y = 0,75, n = −0,15.
. Мощность резания определяется по формуле
где P z − тангенциальная сила резания, Н;−
скорректированная скорость резания, м/мин
Так как мощность станка N ст =10 кВт, то необходимо чтобы
соблюдалось условие
. Основное время обработки определяется по формуле
где n - cкорректированное значение вращения шпинделя, мин -1 ;-
скорректированное значение подачи, мм/об;− число проходов;−
расчетная длина обработки, мм.
. Расчётная длина обработки определяется по формуле
где 1 − длина обрабатываемой поверхности, мм; 1 −
величина врезания и перебега, мм
. Точить Ø22f9 на l=55 начерно и
начисто; точить фаску
Выбираем резец проходной упорный. Материал пластины - твердый
сплав Т15К6 для чистовой обработки, Т5К10 для черновой обработки.
. Глубина резания определяется по формуле
где D заг − диаметр заготовки, мм; дет −
диаметр детали, мм
. Подача на оборот выбирается по [10]
Корректируем подачу по паспорту станка = 0.6мм/об и = 0,4мм/об
. Скорость резания расчетная определяется по формуле (17)
. Частота вращения шпинделя определяется по формуле (20)
Корректируем частоты вращения по паспорту станка = 630 и =1000
. Скорректированная скорость резания определяется по формуле (21)
. P z рассчитывается по формуле (22)
. Мощность резания рассчитывается по формуле (23)
Так как мощность станка N ст =10 кВт, то необходимо чтобы
соблюдалось условие (24)
8. Расчётная длина обработки определяется
по формуле (26)
. Основное время обработки
определяется по формуле (25)
. Центровать отверстие Ø2,5 на l=2,5
Выбираем сверло центровочное ГОСТ 14952-75 D=2,5
. Глубина резания определяется по формуле
. Подача на оборот выбирается по
[10]=0,06мм/об
Корректируем подачу по паспорту станка S п =0,06мм/об
. Скорость резания определяется по формуле
где Т - среднее значение стойкости, мин; (Т=15мин)
,q,y,m - коэффициент и показатели степени, в зависимости от вида
обработки ( =7; q=0,4; y=0,7; m=0,2); - коэффициент, влияющий на скорость
резания; определяется по формуле
где − коэффициент, учитывающий влияние
физико-механических свойств обрабатываемого материала;
− коэффициент на инструментальный материал ( =1);
− коэффициент, учитывающий глубину сверления ( =1)
. Частота вращения шпинделя n ф
определяется по формуле (20)
Корректируем частоту вращения по паспорту станка =1200
. Крутящий момент определяется по формуле
где ,q,y,m - коэффициент и показатели степени, в зависимости от вида
обработки ( =0,0345; q=2; y=0,8)
. Осевая сила определяется по формуле
где ,q,y - коэффициенты и показатели степени, в зависимости от вида
обработки ( =68; q=1; y=0,7)
. Мощность резания N определяется по
формуле
Так как мощность станка N ст =10 кВт, то необходимо чтобы
соблюдалось условие (24)
. Основное время обработки определяется по формуле (25)
. Основное время рассчитывается по формуле
. Вспомогательное время рассчитывается по формуле
где время на установку, мин, время на измерения, мин
время, связанное с переходом, мин,
поправочный коэффициент на вспомогательное время.
. Оперативное время рассчитывается по формуле
где основное время; вспомогательное время.
. Время на обслуживание рабочего места, отдых и личные надобности
. Штучное время определяется по формуле
где оперативное время; время на обслуживание рабочего места, отдых и личные надобности.
. Подготовительно-заключительное время определяется по нормативам
. Штучно-калькуляционное время определяется по формуле
подготовительно-заключительное время;
Выбор режимов резания производится по литературе [6], [7]
Выбор времени производится по литературе [8], [9]
. Точить Ø80f7 на l=30 с припуском под
шлифование начерно и начисто; точить фаску 1х45º
Выбираем резец проходной отогнутый. Материал пластины -
твёрдый сплав Т15К6.
. Глубина резания при подрезке торца определяется по формуле
(16)
. Выбираем по нормативам табличное значение подачи мм/об.
Фактическое значение подачи рассчитывается по формуле
где - поправочные коэффициенты на подачу.
Корректируем значении подачи по паспорту станка мм/об.
. Выбираем по нормативам табличное значение скорости резания м/мин. Фактическая скорость резания рассчитывается по формуле
где поправочные коэффициенты на скорость.
. Фактическая частота вращения шпинделя рассчитывается по формуле
(20)
Корректируем частоту вращения шпинделя по паспорту станка об/мин.
. Скорректированная скорость резания рассчитывается по формуле
(21)
. По скорректированным значениям подачи S п и скорости
резания V п выбирается мощность резания N рез . кВт
Так как мощность станка N ст =11 кВт, то необходимо чтобы
соблюдалось условие (24)
Выбираем резец проходной упорный. Материал пластины - твердый
сплав Т15К6.
2. Выбираем по нормативам табличное значение подачи мм/об.
Фактическое значение подачи рассчитывается по формуле (40)
Корректируем значении подачи по паспорту станка мм/об.
. Выбираем по нормативам табличное значение скорости резания м/мин.
Фактическая скорость резания определяется по формуле (41)
. Фактическая частота вращения шпинделя определяется по формуле
(20)
Корректируем частоту вращения шпинделя по паспорту станка об/мин.
. Скорректированная скорость резания рассчитывается по формуле
(21)
. По скорректированным значениям подачи S п и скорости
резания V п выбирается мощность резания N рез .
Так как мощность станка N ст =11 кВт, то необходимо чтобы
соблюдалось условие (24)
. Точить Ø80f7 на
l=30 начерно и начисто; точить фаску 1х45º
Материал пластины - твердый сплав Т15К6 - для чистовой обработки,
Т5К10 - для черновой обработки.
. Глубина резания определяется по формуле (26)
на черновую обработк у , на чистовую обработку мм
. Выбираем по нормативам табличные значения подач мм/об и мм/об. Фактическое значение подачи рассчитывается по формуле (40)
Корректируем фактические значения подач по паспорту станка мм/об мм/об.
. Выбираем по нормативам табличное значение скорости резания м/мин и м/мин.
Фактическая скорость резания рассчитывается по формуле (41)
. Фактическая частота вращения шпинделя определяется по формуле
(20)
Корректируем частоту вращения шпинделя по паспорту станка об/мин и об/мин.
. Скорректированная скорость резания рассчитывается по формуле
(21)
По скорректированным значениям подачи S п и скорости
резания V п выбираем мощность резания при черновой обработке N рез .
Так как мощность станка , то необходимо чтобы соблюдались условие (34)
Выбираем резец канавочный ГОСТ 18884-73, материал пластины -
твердый сплав Т14К8.
. Глубина резания определяется по формуле (26)
. Выбираем по нормативам табличное значение подачи мм/об.
Фактическое значение подачи рассчитываем по формуле (40)
Корректируем значение подачи по паспорту станка мм/об.
. Выбираем по нормативам табличное значение скорости резания
Фактическая скорость резания рассчитывается по формуле (41)
. Фактическая частота вращения шпинделя определяется по формуле
(20)
Корректируем частоту вращения шпинделя по паспорту станка
. Скорректированная скорость резания рассчитывается по формуле
(21)
. Выбираем по нормативам мощность резания
Так как мощность привода , то необходимо чтобы соблюдались условия словие выполнено.
Выбираем сверло центровочное ГОСТ 14952-7 D=5 7
. Глубина резания определяется по формуле (27)
. Выбираем по нормативам табличное
значение подачи от =0,05мм/об
Корректируем подачу по паспорту станка об/мин.
. Скорость резания определяется по формуле
Выбираем по нормативам табличное значение скорости резания м/мин
. Частота вращения шпинделя n ф определяется по формуле
(20)
Корректируем расчетное значение частоты вращения шпинделя по
паспорту станка n n =1000мин -1
5. Фактическая скорость резания определяется по формуле (17)
. Мощность резания N определяется по
формуле
Необходимо выполнение условие (34): 0,32<7.5, условие
выполнено.
Расчеты производятся по литературе [2]
. Основное время определяется по формуле
где n - cкорректированное значение
вращения шпинделя, мин -1 ;- скорректированное значение подачи,
мм/об;- число проходов;
Вспомогательное автоматическое время
определяется по формуле
где -длина холостых ходов по оси х, мм
- длина холостых ходов по оси z, мм
-ускоренная минутная подача по оси х.
- ускоренная минутная подача оси z.
. Основное время на операцию определяется по формуле (26)
Т всп = (t уст +t изм )
k всп , (49)
где t уст - время на установку и
снятие заготовки, мин изм - вспомогательное время на контрольные
измерения, мин всп - поправочный коэффициент на вспомогательное
время, мин
уст =0,18, t изм
=0,12, k всп =0,76
Т всп = (0,18+0,76+0,12)
0,76=0,8мин
. Оперативное время определяется по
формуле (37)
. Время на обслуживание рабочего места,
отдых и личные надобности от оперативного
. Штучное время определяется по формуле
(38)
. Подготовительно - заключительное время Т пз
. Штучно-калькуляционное время рассчитывается по формуле (39)
м/мин мм/об об/мин м/мин мм/об об/мин
1. Подрезать
торец окончательно 2. Точить Ø22f9 начерно начисто 3. Центровать отверстие
Ø2,5
1. Подрезать
торец в размер 100 2. Точить Ø103на l=15 Точить Ø80f7 на l=30 c припуском под шлифование
начерно 3. Точить Ø80f7
на l=30 c припуском под шлифование начисто; точить фаску 1х45º
4. Точить канавку Ø79 на b=3 5. Центровать отверстие Ø5
, мин , мин , мин , мин , мин , мина, , мин , мин , мин
1. Подрезать
торец окончательно 2. Точить Ø22f9 Начерно Начисто Точить фаску 1х45º 3. Центровать отверстие Ø2,5
1. Подрезать
торец в размер 100 2. Точить Ø81.6 на l=30 начерно Точить Ø103 на l=15 3. Точить Ø80,6 на l=30 начисто Точить фаску 1х45º
4. Точить канавку Ø79 на b=3 5. Центровать 1отв. Ø5 на l=5
Похожие работы на - Разработка технологического процесса для детали 'корпус' Дипломная (ВКР). Другое.
Ерлігі Еліне Арналған Эссе Қобыланды Батыр
Цветочный Бизнес Диссертация
Дипломные Работы На Заказ Заказать
Контрольная Работа По Биологии 5 Класс Клетка
Реферат по теме Особенности лицензирования предпринимательской деятельности
Контрольная работа по теме Прийоми варіювання геометричних задач
Дипломная работа по теме Особенности денежной системы Республики Казахстан
Реферат: Традиционная система снабжения
Контрольная работа по теме Разработка элементов автоматизации управления процессами текущего ремонта автотранспортных средств
Реферат: Методические рекомендации по проведению 1 сентября первого урока и мероприятий, посвященных Дню знаний
Курсовая работа по теме Средства и методы развития силовых способностей
Правовое Государство Это Высшая Форма Эссе
Права И Обязанности Адвоката Реферат
Турфирма Лицей Трэвел Спб Отчет По Практике
Реферат по теме Человечество на пороге эры бескризисной энергетической экономики
Реферат: Алгоритмы вывода кинетических уравнений для стационарных и квазистационарных процессов. Скачать бесплатно и без регистрации
Реферат по теме Термоядерные реакции
Курсовая работа по теме Роль инноваций в управлении предприятием
Контрольная Работа На Тему Архитектура Древнего Рима
Реферат: Влияние кредитных историй на работу компаний
Реферат: Потребительские рынки и покупательское поведение потребителей сельскохозяйственной продукции
Реферат: Судовые холодильные установки
Доклад: Инки – история