Разработка методики и технических средств для ультразвукового контроля сварного изделия. Дипломная (ВКР). Другое.
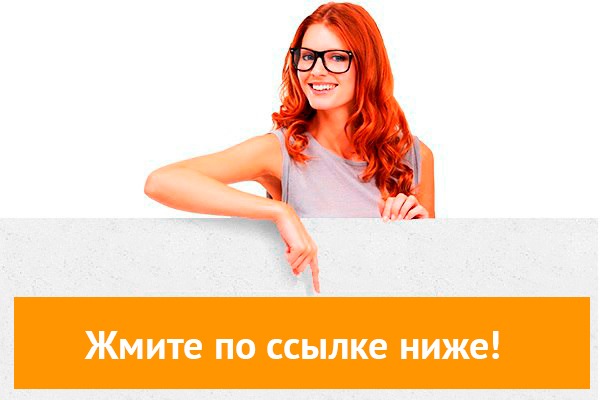
🛑 👉🏻👉🏻👉🏻 ИНФОРМАЦИЯ ДОСТУПНА ЗДЕСЬ ЖМИТЕ 👈🏻👈🏻👈🏻
Вы можете узнать стоимость помощи в написании студенческой работы.
Помощь в написании работы, которую точно примут!
Похожие работы на - Разработка методики и технических средств для ультразвукового контроля сварного изделия
Скачать Скачать документ
Информация о работе Информация о работе
Нужна качественная работа без плагиата?
Не нашел материал для своей работы?
Поможем написать качественную работу Без плагиата!
Разработка методики и технических
средств для ультразвукового контроля сварного изделия
1. Анализ характеристик объекта контроля
2. Сравнительный анализ известных методик ультразвукового контроля
сварных швов
3. Выбор метода контроля (теоретический анализ акустического
тракта)
4. Расчет и проектирование наклонного преобразователя
5.2 Выбор типа УЗ-волн и направления их распространения в изделии
5.4 Выбор мест ввода ультразвуковых волн и схемы сканирования
5.5 Выбор технических средств контроля
5.6 Выбор способа регистрации и расшифровки результатов контроля
5.7 Разработка метрологического обеспечения средств контроля
5.8 Описание мероприятий по технике безопасности и охране труда
6. Разработка вспомогательных средств для сканирования объекта
7. Расчет чувствительности и производительности контроля
Неразрушающие методы контроля имеют очень важное значение для
повышения качества и надежности изделий и материалов в различных областях
народного хозяйства республики. Широкое распространение этих методов
обусловлено тем, что они позволяют избежать больших потерь времени и
материальных затрат.
В настоящее время широкое применение на различных
машиностроительных предприятиях и предприятиях энергетики получили акустические
методы контроля, в частности ультразвуковая дефектоскопия. По сравнению с
другими методами неразрушающего контроля она обладает рядом важных преимуществ:
высокой чувствительностью к наиболее опасным дефектам типа
трещин;
возможностью проводить контроль непосредственно в ходе
технологического процесса, т.е. ультразвуковая дефектоскопия обладает большой
производительностью;
хорошей возможностью автоматизации контроля.
Возможность автоматизации контроля позволяет разрабатывать и
внедрять в производство различные автоматические комплексы для контроля изделий
в процессе производства. В состав таких комплексов могут входить не только автоматические
сканеры и блоки управления ими, дефектоскопы, но и ЭВМ. При разработке
автоматических устройств широко применяется интегральная электроника, что
существенно позволяет снизить количество применяемых элементов, габаритные
размеры блоков, повысить их надежность.
В конструктивных документах на ультразвуковой контроль
сварных соединений труб, выбор угла ввода и зоны перемещения преобразователя
установлен исходя из геометрических характеристик сварного соединения. При этом
предполагается, что скорости распространения поперечных волн постоянны по
сечению трубы и не зависят от направления прозвучивания.
Объем применения ультразвукового контроля, как у нас, так и
за рубежом за последние годы достиг 70-80%. Это объясняется более высокой
чувствительностью и достоверностью к обнаружению дефектов, более высокой
производительностью, меньшей стоимостью и безопасностью в работе с
традиционными методами радиографического контроля. Кроме т ого, в таких
случаях, как, например, при контроле сварных швов большой толщины
ультразвуковая дефектоскопия является единственно приемлемым методом контроля.
ультразвуковой контроль сварной шов
В данном дипломном проекте необходимо разработать методику и
технические средства для УЗ контроля сварного изделия. В качестве сварного
соединения будем рассматривать тавровое соединение труб. Тавровым называют
сварное соединение, в котором торец одного элемента примыкает под углом и
приварен к боковой поверхности другого элемента. При тавровом соединении угол
между полкой и стенкой может быть как прямым, так и отличаться от него.
Сочетание толщин может быть различным. Они часто встречаются в строительных
конструкциях.
Различают несколько видов тавровых соединений: без скоса и со
скосом кромок с одной или двух сторон. Угол обычно принимают равным 55-60 о ,
а зазор между соединяемыми элементами 0,5-1 мм [4]. Внешний вид объекта
контроля представлен на рисунке 1.1.
Рисунок 1.1 - Внешний вид объекта контроля
Технология изготовления сварного соединения, представляющего
собой тавр, заключается в следующем: два листа, изготовленных из стали 20 (в
данном случае), соединены с трубой при помощи ручной дуговой сварки по ГОСТ
5264-80.
Материал изделия - сталь 20 - сталь конструкционная
углеродистая качественная, микроструктура такой стали, представляет собой зёрна
со средним размером, около 60 мкм.
Акустические характеристики материала изделия приведены в
таблице 1.2.
Таблица 1.2 - Акустические характеристики материала изделия
Волновое сопротивление z пр , Па×с/м 10
Коэффициент затухания ультразвука частотой f=2,5 МГц для
стали 20 равен d = 0,009 дБ/мм для продольных и поперечных волн.
Для обеспечения качественного провара и формирования сварного
шва выполняют подготовку кромок под сварку. Элементами геометрической формы
подготовки кромок под сварку являются угол разделки кромок α, зазор между стыкуемыми кромками b.
Существующие способы сварки позволяют сваривать без разделки
кромок металл ограниченной толщины - до 5 мм. Поэтому при сварке металла
большой толщины необходимо разделывать кромки для доступа сварочной дуги в
глубь соединения и полного проплавления кромок на всю их толщину.
Стандартный угол разделки кромок в зависимости от способа
сварки и типа соединения изменяется от 45±2 о до 12±2 о . От
типа разделки и величины разделки кромок зависят количество дополнительного
металла для заполнения разделки, а значит и производительность сварки.
Притупление с обычно составляет 2±1 мм. Его назначение -
обеспечить правильное формирование шва и предотвратить прожоги в корне шва.
Зазор b обычно равен 1-2 мм. Наличие зазора необходимо, чтобы
проварить корень шва [4].
Рисунок 1.4 - Элементы геометрической формы подготовленных
под сварку тавровых швов
Согласно ГОСТ 5264-80 существует несколько видов геометрической
формы подготовленных кромок под сварку тавровых швов. Наиболее подходящим видом
является соединение деталей с углом равным 90 о , толщиной изделия
(исходя из задания) S=16 мм.
На рисунке 1.4 сварка выполнена с двумя скосами одной кромки,
характер выполненного шва - двусторонний. Уловное обозначение соединения - Т8.
Геометрические размеры такого соединения: е=12±2 мм; b=3±2 мм; к=0,15Sч0.5S,
примем к=0,25S=4 мм; α=45 0 ±2 0 ; h=1-2
=9,5 мм. Для сварки соединения Т8 допускается притупление С=5±2 мм.
Основными дефектами сварного шва из данного материала
являются непровары в корне шва, несплавления по кромкам шва, вертикальные и
горизонтальные трещины, поры, цепочки пор и шлаковые включения [4].
Дефекты при сварке металлов образуются вследствие нарушения
требований нормативных документов к сварочным материалам, подготовке, сборке и
сварке соединяемых элементов, термической и механической обработке сварных
соединений и конструкции в целом.
В сварных соединениях, выполненных ручной дуговой сваркой,
различают дефекты в зависимости от причин возникновения и места их
расположения.
К первой относятся дефекты, связанные с металлургическими и
тепловыми явлениями, происходящими в процессе образования, формирования и
кристаллизации сварочной ванны и остывания сварного соединения. Это
кристаллизационные и холодные трещины в металле шва и околошовной зоне, поры,
шлаковые каналы, флокены, зона несплавления, утяжины и другие.
Ко второй группе дефектов, которая называется дефектами
формирования швов, т.е. дефекты, происхождение которых связано с нарушением
режима сварки, неправильной подготовкой и сборкой элементов конструкции под
сварку, неисправностью оборудования. К таким дефектам относят: непровары,
подрезы, наплывы, прожоги, кратеры, несимметричность расположения угловых швов,
уменьшение размеров швов и другие [4].
Наиболее опасными дефектами тавровых соединений являются
трещины и непровары. Размеры выявляемых дефектов: b min =1.5Ч10 -3
м, b max =6Ч10 -3 м.
Трещина - несплошность, вызванная местным разрывом шва,
который может возникнуть в результате охлаждения или действия нагрузок.
Чаще всего трещины образуются в жестко закрепленных
конструкциях, они могут располагаться вдоль и поперек сварного соединения, а
также в основном металле, в местах пересечения и сосредоточения швов.
Трещины являются наиболее опасными дефектами сварных швов.
Трещины могут возникать в сварном шве и в околошовной зоне. Трещины по
происхождению делятся на холодные и горячие, по расположению - на поперечные и
продольные, по размерам - на макро - и микроскопические. Трещины в сварных швах
образуются во время и после сварки. Образованию трещин способствует повышенное
содержание углерода в наплавленном металле, а также серы, фосфора и водорода.
Холодные трещины возникают при температурах 100-300°С в легированных сталях и
при нормальных температурах в углеродистых сталях.
Причинами образования трещин являются несоблюдение технологии
и режимов сварки, неправильное расположение швов в сварной конструкции, что
вызывает высокую концентрацию напряжений, приводящих к полному разрушению
изделия. Большие напряжения в сварных конструкциях возникают при несоблюдении
заданного порядка наложения швов. Поверхностные трещины в сварных швах вырубают
полностью и заваривают вновь. Чтобы в процессе вырубки трещина не
распространялась дальше по шву, необходимо перед вырубкой засверливать трещины
по концам.
Непровар - несплавление основного металла по всей длине шва
или на участке, возникающее вследствие неспособности расплавленного металла
проникнуть в корень соединения. Причинами образования непроваров являются:
плохая подготовка кромок свариваемых деталей, малое расстояние между кромками
деталей, неточное направление электродной проволоки относительно места сварки,
недостаточный сварочный ток или чрезмерно большая скорость сварки, неустойчивый
режим сварки и т.п.
Пора - несплошность сферической формы средним диаметром от 0,01
мкм до нескольких миллиметров в сплошном металле. Пористость в сварных швах
появляется в результате, того, что газы, растворенные в жидком металле, не
успевают выйти наружу до затвердевания поверхности шва. Поры делают сварной шов
неплотным и уменьшают его механическую прочность. Причинами образования пор
являются плохая зачистка свариваемых кромок и присадочной проволоки от грязи,
ржавчины, масла, повышенное содержание углерода в основном металле, большая
скорость сварки, неправильный выбор характера сварочного пламени и марки
проволоки. Газовые поры располагаются цепочкой на некотором расстоянии друг от
друга или в виде скоплений размером от сотых долей миллиметра до нескольких
миллиметров. Иногда поры выходят на поверхность, образуя свищи. Поры могут быть
внутренние, наружные и сквозные. Участки сварных швов с порами исправляют
вырубкой дефектных мест до основного металла с последующей заваркой. []
Внешний вид трещин представлен на рисунке 1.5.
Рисунок 1.5 - Внешний вид трещин сварного шва таврового
соединения
Непровар в тавровом соединении выглядит следующим образом:
Рисунок 1.6 - Внешний вид непровара сварного шва таврового
соединения
Пора в тавровом соединении выглядит следующим образом:
Рисунок 1.7 - Внешний вид поры сварного шва таврового
соединения
Дефекты в тавровых соединениях долгое время контролировали
визуально-оптическими методами контроля. В настоящее время существует множество
методов ультразвуковой дефектоскопии таких соединений. Наибольшее
распространение из ультразвуковых методов контроля получил эхо-метод. Он
обладает наибольшей чувствительностью и помехоустойчивостью. Другие методы
применяют в тех случаях, когда применение эхо-метода затруднено или
нецелесообразно.
Теневым методом контролируют изделия простой формы (например,
листы небольшой толщины) и некоторые слоистые материалы (например, паяные). Как
правило, он требует доступа к двум поверхностям изделия. Зеркально-теневой
метод применяют при доступе к одной поверхности, когда дефекты не дают
эхо-сигнала (например, из-за наличия "мертвой" зоны, или в связи с
неблагоприятной ориентацией дефекта).
- генератор; 2 - усилитель; 3 - ЭЛТ; 4 - ПЭП; 5 - шов
Рисунок 2.1 - Контроль зеркально-теневым методом
Ультразвуковой контроль сварных швов тавровых соединений,
может производится как со стороны основного элемента, так и со стороны
притыкаемого элемента. Способ контроля зависит от толщин этих элементов.
Контроль сварного шва таврового соединения с полным
проплавлением стенки ведется с применением трех схем (рисунок 2.1).
В зависимости от доступа к швам контроль ведут наклонными, а
также раздельно-совмещенными преобразователями.
Рисунок 2.2 - Схемы контроля двусторонних швов тавровых
соединений.
Наиболее эффективной является схема ввода ультразвуковых
колебаний через основной металл провариваемого листа (схема I), так как она
позволяет выявить все виды внутренних дефектов в сварных швах при минимальном
уровне ложных сигналов.
При контроле тавровых соединений появление ложных сигналов
может быть обусловлено только отражением от грубых неровностей на наружной
поверхности плоскости полки, встречающихся весьма редко и связанных с
повреждением металла. В тех случаях, когда затруднен доступ со стороны стенки,
то есть невозможно проведение контроля по схеме I, прозвучивание выполняют по
схемам II и III. контроль по схеме II обеспечивает выявление пор, шлаковых
включений, несплавлений и трещин, ориентированных перпендикулярно к
ультразвуковым лучам. Однако контроль по такой схеме осложняется необходимостью
ориентировки преобразователя относительно соединения и появлением ложных
эхо-сигналов от поверхности противоположного валика шва (рисунок 2.2), причем
амплитуда ложного эхо-сигнала обычно выше амплитуды сигнала от дефекта.
Разделение полезных и ложных сигналов производится по времени прохождения
ультразвуковых колебаний.
Выявить непровар в корне шва при контроле по схеме II
практически невозможно, так как ультразвуковые лучи испытывают зеркальное
отражение. Этот опасный дефект при доступе для контроля только с наружной
поверхности полки обнаруживается по схеме (рисунок 2.3) с помощью
раздельно-совмещенного преобразователя или двух жесткосоединенных наклонных
преобразователей, включенных по раздельной схеме.
а - с порой; б - с непроваром в корне шва; в - с трещиной; Л
- ложные эхо-сигналы; Н, Т, П - эхо-сигналы соответственно от непровара,
трещины, поры.
Рисунок 2.3 - Анализ схем контроля тавровых соединений
Одним из условий, обеспечивающих наиболее вероятное выявление
дефектов по сечению шва, является правильный выбор угла ввода УЗ-луча в
контролируемое соединение.
Целесообразно использовать преобразователи с такими углами α и стрелой n 0 , при которых обеспечивается контроль
нижней части шва прямым, в верхней - однократно отраженным лучом. Это считается
возможным, если центральный луч преобразователя при расположении его вплотную к
шву проходит через середину шва или выше ее [5].
При контроле нижней части шва таврового соединения (рисунок
2.1) это условие может быть проверено по соотношением:
Верхнюю часть шва этих соединений целесообразно проверять
преобразователями с таким углом ввода:
Тавровые соединения с технологическим непроваром определенной
ширины в корне контролируют со стороны полки. При этом ширину непровара
определяют по испытательному образцу.
При изготовлении ряда тавровых конструкций в центре допускается
конструктивный непровар, размер которого требуется определить. Существует 2
метода измерения ширины непровара в шве и модели непровара, выполненных в СОП,
сравнением амплитуд эхо-сигналов от непровара в шве и бесконечной плоскости
(безэталонный метод, предложенный Гурвичем). В обеих методиках используют ПЭП
конструкции НИИ мостов, которые представляют собой призму с приклеенным к ней
пьезоэлементами, наклоненными под углом, обеспечивающим пересечение диаграмм
направленности искателей на глубине, равной толщине полки.
При перемещении ПЭП по наружной поверхности полки в случае полного
провара и отсутствия других крупных дефектов ультразвуковые колебания от
передающего ПЭП через зону наплавленного металла переходят без отражений в лист
стенки. Если же в соединении окажется непровар, то часть УЗ-колебаний отразятся
от него к приемному ПЭП. Амплитуды эхо-сигнала зависят в основном от ширины
непровара 2b. При измерении ширины непровара по первому способу применяют
специальный СОП, изготовленный из того же материала, что и полка. В СОП делают
прорези различной ширины на глубине, соответствующей толщине полки Н.
Соединения с недопустимой величиной непровара 2b конструируют на
такой чувствительности, при которой в СОП выявляются прорези шириной 2b мм. При
таком уровне чувствительности дефектоскопа будут уверенно выявляться непровары,
ширина которых превосходит допустимую величину на 1 мм и более. Практикой
установлено, что погрешность в определении ширины непровара не превышает 1-1.4
мм. Влияние качества поверхности на результаты измерения и необходимость
использования СОП исключаются при безэталонном методе.
Безэталонный метод основан на сравнении амплитуды эхо-сигнала от
непровара А с амплитудой эхо-сигнала от бесконечной плоскости Ао, расположенной
на той же глубине, что и непровар. В качестве такой плоскости следует
использовать полки. Безэталонный метод может быть реализован с помощь
дефектоскопов, имеющих калиброванный аттенюатор. В связи с тем, что этот метод
основан на сравнении амплитуд эхо-сигналов от непровара А и плоскости Ао,
контролю должен предшествовать расчет зависимости или ее экспериментальное построение.
Проанализировав все вышеописанные методики ультразвукового
контроля сварных швов тавровых соединений можно сделать вывод о методе контроля
и схемах прозвучивания.
Для выявления дефектов будем использовать эхо-импульсный метод
контроля, который осуществляется со стороны полки наклонным преобразователям
прямым и однократно отраженным лучом. Схемы прозвучивания соединения для
выявления трещин и несплавлений по кромкам выглядит следующим образом:
В данном случае используется контактный наклонный совмещенный ПЭП.
Контроль ведется прямым и однократно-отраженным лучом. Такой способ позволяет
прозвучивать изделия с одной стороны, а также прозвучать мертвую зону.
Недостаток этого способа - зависимость предельной чувствительности к дефектам,
выявляемым отраженным лучом, от состояния поверхности.
Для выявления непровара в корне шва и технологического непровара
будем использовать контактный прямой совмещенный ПЭП и контроль будем вести
прямым лучом. Преобразователь располагается на полке таврового соединения.
Сегодня на практике для осуществления эхо-метода возможно
использование широкого перечня приборов. Опишем некоторые из них.
Дефектоскоп GE Phasor XS переводит испытанные преимущества
технологии фазированной решетки на новый - и доступный - уровень. Этот переносной
и прочный прибор объединяет преимущества фазированной решетки с обычным
ультразвуковым дефектоскопом, отвечающим принятым нормам. Он прост в
использовании, легок в обучении и предлагает специально разработанные
практичные и важные функции.
При использовании в режиме фазированной решетки, оператор может
электронным образом контролировать несколько лучей от одного датчика. Точное
управление лучом, включая угол, фокус и размер, приводит к повышению
вероятности обнаружения (POD), а также улучшению определения размеров дефектов.
С помощью одного скана от одного контактного положения, охватывается большая
площадь, а исчерпывающие данные могут просматриваться в реальном времени на
полноценном секторном дисплее. В сравнении с обычными ультразвуковыми средствами
контроля, производительность и снижение затрат при использовании дефектоскопа
Phasor XS очевидны.
Если при проведении обычного ультразвукового контроля требуется
другой угол, оператор должен заменить свой датчик и вновь визуализировать
интеграцию новой информации. При этом отображается другая временная развертка и
другой уровень чувствительности. Несмотря на то, что такая операция не
представляет проблем для опытного оператора, на это требуется время. Благодаря
возможностям дефектоскопа Phasor XS, эти неудобства минимизируются радикально.
Формирование цветного изображения в реальном времени дефектоскопом
Phasor XS обеспечивает интегрированную перекрестную визуализацию детали,
благодаря использованию нескольких лучей. Кроме того, для отображения в комбинации
с изображением, может быть выбран одиночный А-скан. С использованием одного
датчика вы можете достичь больших результатов, чем когда-либо ранее - и за
более короткое время.
Новый универсальный ультразвуковой дефектоскоп позволяющий
воспользоваться всем богатством возможностей современной цифровой техники:
выводить сигнал в виде А,B - сканов, подключать датчик пути для построения
координатной развертки изделия (в специализированных версиях), записывать
большой объем данных, автоматически формировать отчеты и протоколы. Позволяет
измерять толщину изделий с высокой точностью, проводить ручной,
автоматизированный контактный и иммерсионный (специальная и-зона) контроль.
Универсальная архитектура прибора позволяет строить на его базе
механизированные и роботизированные комплексы контроля (до 32-х каналов)
Дефектоскоп сочетает в себе последние достижения аналоговой и
цифровой техники, широкую универсальность, богатые функциональные возможности,
удобство и простоту пользования, высокую надежность.
Технические характеристики дефектоскопа:
. Максимальная длина контролируемого материала
радиоимпульс, амплитудой 50 или 200 В,
с изменяемой длительность от 16 до 500 нс,
регулируемый от 0 до 15 полупериодов
с задержкой демпфирования от 0 до 7 полупериодов
. Временная Регулировка Чувствительности (ВРЧ)
с построением кривой по 32 опорным точкам
введенным вручную или от контрольных отражателей
. Кривая Амплитуда-Расстояние (АРК)
построение по 32 точкам, регулируемая по высоте
положительная или отрицательная полуволна,
полное, радиосигнал (во всем диапазоне развертки), B-scan, C-скан
компенсированная, 0 - 90% высоты экрана
три независимых зоны, начало и ширина
изменяются во всем диапазоне развертки,
уровни порогов задаются от 0 до 95%
от - 95% до +95% при радиосигнале с шагом
%, индивидуальная логика определения дефектов.
Одна из зон (и-зона) предназначена для синхронизации от
поверхностного сигнала при иммерсионном контроле
. Автоматическая Сигнализация Дефектов (АСД)
световая для каждой зоны отдельно и звуковая,
индивидуальная логика определения дефекта в зоне
от 0 до первого сигнала в зоне или между
сигналами в зонах, по фронту или по максимуму
в дБ относительно уровня порога в зоне,
в дБ относительно опорного сигнала,
в дБ относительно кривой амплитуда-расстояние
протоколов контроля (сигнал, огибающая, результат измерения,
параметры работы прибора, дата, время и название протокола)
Предназначен для контроля продукции на наличие дефектов типа
нарушения сплошности и однородности материалов, готовых изделий, полуфабрикатов
и сварных (паяных) соединений, измерения глубины и координат залегания дефектов,
измерения отношений амплитуд сигналов, отражённых от дефектов.
два независимых измерительных строба
система автоматической сигнализации дефектов
возможность запоминания: 100 программ настроек, 100 изображений
экрана, 2000 результатов измерения параметров сигналов
протоколирование процедуры контроля с использованием программного
обеспечения "Ultra UD2-70".
Предназначен для ручного и механизированного ультразвукового
контроля материалов, заготовок, изделий и оборудования, съема и сохранения
томограмм.
работа с любыми типами пьезоэлектрических преобразователей;
измерение эквивалентных и условных размеров дефектов;
синхронизация: внутренняя, внешняя, от датчика пути;
различные формы детектирования: РЧ / 2п. п. / +п. п. / - п. п.;
набор функций регулировки усиления, в том числе АРУ, ВРЧ;
интерфейс автоматической калибровки параметров ПЭП и объекта
контроля;
несколько режимов работы с АРД диаграммами;
два независимых трехуровневых измерительных строба;
два дополнительных специальных строба;
возможность контроля акустического контакта;
система АСД по всем уровням стробов;
индикация АСД на ярких трехцветных светодиодах;
усовершенствованный режим пиковой кривой;
режим наложения текущего сигнала на зафиксированный ранее (режим
"стоп-кадр");
динамическое изменение характеристик генерирующего тракта в
зависимости от включаемых частотных фильтров;
разметка экрана по отражениям сигнала в объекте контроля;
возможность использования специального программного интерфейса;
возможность выбора структуры меню по двум схемам:
"Пользователь" / "Эксперт";
возможность создания голосовых комментариев ко всем типам
сохраняемых данных;
большой высокоскоростной TFT дисплей;
сохранение и вызов настроек контроля;
Основные технические характеристики:
частотный диапазон - частота УЗК 0,4; 0,62; 1,25; 1,8; 2,5; 5,0 и
10,0 МГц. Область низких частот может оказаться полезной для контроля чугунов,
пластмасс и других материалов с большим затуханием УЗК, а частота 10,0 МГц -
для контроля изделий малой толщины и выявления мелких дефектов;
предусмотрен специальный режим толщиномера с индикацией сигналов
на А-развертке. При этом предусмотрена возможность измерения как по первому,
так и по двум донным сигналам. На экране дефектоскопа может индицироваться как
среднее, так и минимальное из измеренных значений. Разрешающая способность
толщиномера до 0,01 мм. Для сохранения результатов измерений толщины в памяти
дефектоскопа предусмотрен специальный отчет, который может быть сохранен в ПЭВМ
и (или) распечатан;
расширен динамический диапазон ВРЧ (до 60 дБ);
по требованию потребителя может быть предусмотрена возможность
подключения дополнительной аккумуляторной батареи для увеличения времени работы
дефектоскопа в полевых условиях;
режим "вихреток" * - частототный диапазон до 100,0 кГц.
Динамический и статический режимы контроля. Метод контроля - фазовый и
амплитудный.
Ультразвуковой дефектоскоп А1214 ЭКСПЕРТ - полностью цифровой,
малогабаритный ультразвуковой дефектоскоп общего назначения. Обеспечивает
реализацию типовых и специализированных методик ультразвукового контроля,
высокую производительность и точность измерений.
поиск мест коррозии, трещин, внутренних расслоений и других
дефектов
определение координат и оценка параметров дефектов типа нарушений
сплошности и однородности материала в изделиях из металлов и пластмасс
Технология ручного УЗ-контроля состоит из ряда простых и сложных
операций. Оператор перемещает преобразователь в околошовной зоне по сложной
траектории, непрерывно наблюдает за экраном дефектоскопа и выполняет логические
операции по переработке полученной информации и оценке качества контролируемого
изделия. Такая напряженная работа приводит к быстрому физическому утомлению
оператора, вследствие чего происходит пропуск дефектов.
Одним из основных недостатков ручного контроля является то, что
после него не остается объективных документов (дефектограмм), по которым можно
было бы контролировать работу операторов. Это обусловливает зависимость оценки
качества контролируемого изделия от квалификации, физического состояния и
условий работы оператора.
Автоматизация контроля значительно повышает его производительность
и достоверность. Повышение достоверности достигается тем, что фиксация
обнаруженных дефектов производится не визуально оператором, а за счет получения
дефектограммы на бумажной ленте с помощью какого-либо регистрирующего
устройства.
Автоматизированное устройство для УЗ-контроля должно включать
следующие основные узлы: акустический блок с преобразователями и механизмом для
их перемещения по поверхности контролируемого изделия; система слежения за швом
соединений и качеством акустического контакта; электронный блок для
генерирования зондирующих импульсов и приема эхо-сигналов; систему подачи и
сбора контактной жидкости; электронный блок для логической обработки информации
о дефекте, включая ЭВМ, регистраторы информации на дефектограмме в аналоговой
или цифровой форме; систему обратной связи для управления траекторией и
скоростью сканирования в зависимости от полученной информации о дефекте;
систему автоматической отбраковки и др.
Уровень автоматизации установки определяется наличием в ней
упомянутых систем. Если все эти системы входят в конструкцию установки, то
достигается полная автоматизация контрольных операций. Такие установки называют
автоматическими стендами. Стенды - весьма сложное, громоздкое и дорогостоящее
оборудование, поэтому применять их на производстве не всегда целесообразно.
Автоматизации обычно предшествует разработка и внедрение методов и
средств механизации. Вначале отдельные операции ручного контроля должны быть
заменены механизмами и устройствами с механическим двигателем. Во многих
случаях достаточно механизировать (частично автоматизировать) контрольные
операции, передав автоматизированному устройству, например, функции поиска и
регистрации дефектов. Такие устройства менее сложны по конструкции и могут быть
выполнены в виде малогабаритных дефектоскопов.
Важно отмстить, что применение этих упрощенных устройств не должно
влиять на достоверность контроля. Поэтому выбор конструкции установки и
оптимизация параметров автоматического контроля должны производиться на основе
закономерностей статистического распределения дефектов в контролируемых
изделиях по местоположению, ориентации, типу, величине и другим признакам.
Сканер HSFCS-XY01 (рисунок 2.18). Это гибкий сканер, обладает
необходимой гибкостью для контроля неровных и наклонных поверхностей. Система
множественных чашечных присосов держит сканер на детали. HSFCS-XY01 также может
быть оснащен чашечными присосами, активируемыми вручную, что исключает
необходимость исполь
Похожие работы на - Разработка методики и технических средств для ультразвукового контроля сварного изделия Дипломная (ВКР). Другое.
Курсовая работа по теме Европейская валютная интеграция
Реферат На Тему Международный Туризм В России
Дипломная работа по теме Развитие ипотечного кредитования физических лиц
Курсовая работа по теме Расчёт технико-экономических показателей по электроснабжению цеха станков с ЧПУ
Что Такое Счастье Сочинение Огэ
Как Можно Развить Свои Способности Сочинение
Реферат по теме Динаміка та показники розвитку банківської системи України
Контрольная Работа На Тему Диаграмма Состояния Системы Алюминий-Медь
Заявление На Итоговое Сочинение 2022 Ворде
Реферат по теме Основы сканирования изображений
Дипломная работа по теме Социальная защита детей с ограниченными возможностями
Реферат по теме Саморазвитие личности на уроках физической культуры
Курсовая работа по теме Заходи щодо профілактики та ліквідації чуми м’ясоїдних в умовах приватної ветеринарної лікарні 'Друг' м. Луганськ
Дипломная Работа На Тему Внедрение Системы Спутникового Мониторинга Транспорта На Примере Организации
Курсовая работа: Unemployment: reasons and main forms
Контрольная работа по теме Отраслевая структура в современных условиях
Статья: Глава 25 НК РФ новое понятие Налоговый учет
Реферат по теме Дерматомиозит. Подагра
Сочинение По Литературе Егэ 8 Задание
Реферат: Плакат. Специфика художественного языка плаката
Курсовая работа: Внешнеэкономическая среда и ее влияние на функционирование предприятия
Реферат: Fight Or Die Essay Research Paper Dee