Расчет шихты, материального и теплового балансов доменной плавки. Курсовая работа (т). Другое.
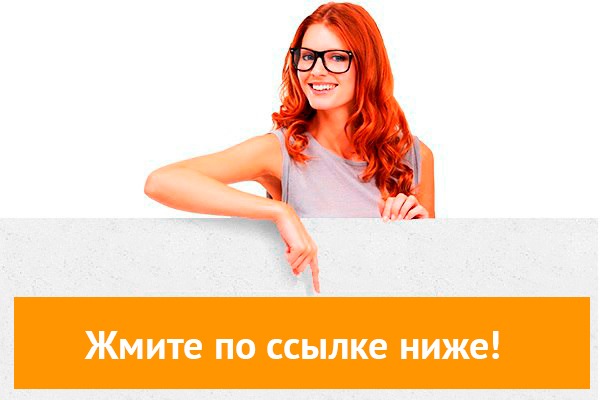
💣 👉🏻👉🏻👉🏻 ВСЯ ИНФОРМАЦИЯ ДОСТУПНА ЗДЕСЬ ЖМИТЕ 👈🏻👈🏻👈🏻
Вы можете узнать стоимость помощи в написании студенческой работы.
Помощь в написании работы, которую точно примут!
Похожие работы на - Расчет шихты, материального и теплового балансов доменной плавки
Скачать Скачать документ
Информация о работе Информация о работе
Скачать Скачать документ
Информация о работе Информация о работе
Скачать Скачать документ
Информация о работе Информация о работе
Скачать Скачать документ
Информация о работе Информация о работе
Нужна качественная работа без плагиата?
Не нашел материал для своей работы?
Поможем написать качественную работу Без плагиата!
. Расчёт шихты, материального и теплового балансов доменной
плавки
.2 Расчёт состава и количества колошникового газа и
количества дутья
.3 Материальный баланс доменной плавки
Цель доменного производства состоит в получении чугуна из железных руд
путем их переработки в доменных печах. Сырыми материалами доменной плавки
являются топливо, железные и марганцевые руды и флюс.
Топливом для доменной плавки служит кокс, получаемый из каменного угля.
Его роль состоит в обеспечении процесса теплом и восстановительной энергией. Кроме
того кокс разрыхляет столб шихтовых материалов и облегчает прохождение газового
потока в шихте доменной печи.
Железные руды вносят в доменную печь химически связанное с другими
элементами железо. Восстанавливаясь и науглероживаясь в печи, железо переходит
в чугун. С марганцевой рудой в доменную печь вносится марганец для получения
чугуна требуемого состава.
Флюсом называются добавки, загружаемые в доменную печь для понижения
температуры плавления пустой породы руды, офлюсования золы кокса и придания шлаку
требуемых технологией выплавки чугуна физико-химических свойств. Для руд с
кремнеземистой (кислой) пустой породой в качестве флюса используют материалы,
содержащие оксиды кальция и магния: известняк и доломитизированный известняк.
Для получения высоких технико-экономических показателей доменной плавки
сырьё и материалы предварительно подвергают специальной подготовке.
Чугун выплавляют в печах шахтного типа - доменных печах. Сущность
процесса получения чугуна в доменных печах заключается в восстановлении оксидов
железа, входящих в состав руды, оксидом углерода, водородом и твёрдым
углеродом, выделяющимся при сгорании топлива в печи.
Рисунок 1 - Устройство доменной печи: 1 - горячее дутьё; 2 - зона
плавления (заплечики и горн); 3 - зона восстановления FeO (распар); 4 - зона
восстановления Fe 2 O 3 (шахта); 5 - зона предварительного нагрева
(колошник); 6 - загрузка железорудных материалов, известняка и кокса; 7 -
доменный газ; 8 - столб железорудных материалов, известняка и кокса; 9 - выпуск
шлака; 10 - выпуск жидкого чугуна; 11 - сбор отходящих газов
Колошник - верхняя цилиндрическая часть, куда при помощи засыпного
аппарата загружаются проплавляемые материалы, а от боковых сторон его по
газоотводам удаляются колошниковые газы.
Шахта - расположена под колошником. В ней в определённой
последовательности идут процессы подготовки материалов, восстановление из
окислов руды железа и других элементов, науглероживание железа и плавление
образовавшегося сплава. Шахте придаётся форма расширяющегося книзу усечённого
конуса для облегчения опускания из колошника загруженных материалов.
Распар - самая широкая цилиндрическая часть печи, где происходит
плавление пустой породы руды и флюса с образованием из них шлака.
В заплечиках, следующей части печи в виде усечённого и расширяющегося
кверху конуса, процесса шлакообразования заканчивается. Здесь остается в
твёрдом состоянии только горючее и часть флюса.
В горне происходит горение спустившегося сверху топлива и накапливаются в
жидком состоянии чугун и шлак. Горячий воздух для сжигания топлива от
воздухонагревателей подводится к печи по кольцевому воздухопроводу через фурмы.
Чугун и шлак накапливаются на дне горна, называемом лещадью, расположенной на
мощном железобетонном фундаменте.
Чугун выпускается из печи через лётку, расположенную на дне лещади, по
желобам в ковши, а шлак в специальные ковши через две шлаковые лётки.
В верхней части печи имеется малый конус засыпного аппарата, на который
попадает шихта, при опускании его шихта попадает в чашу. Из чаши шихта попадает
на большой конус, при опускании которого шихтовые материалы попадают в доменную
печь, предотвращая при этом выход газов из доменной печи в атмосферу. Для
равномерного распределения шихты в доменной печи малый конус и приёмная воронка
после очередной загрузки поворачивается на угол кратный 60º.
При работе печи шихтовые материалы, проплавляясь, опускаются, а через
загрузочное устройство в печь попадаются новые порции шихты в таком количестве,
чтобы весь полезный объём печи был заполнен. Полезный объём печи - это объём,
занимаемый шихтой от лещади до нижней кромки большого конуса засыпного аппарата
при его опускании. Современные доменные печи имеют полезный объём 2000…50000 м³, полезная высота доменной печи
достигает 35 м, это более чем в три раза превосходит диаметр её поперечного
сечения.
Это позволяет доменной печи, работающей по принципу встречного движения
материалов и газов, иметь более высокий коэффициент полезного использования
тепла (до 85%).
Кладка лещади и горна выполняется из углеродистых блоков и
высокоглинозёмистых кирпичей, а заплечики, распар и шахта - из шамотных
кирпичей высшего качества.
Лещадь и горн заключены в мощный стальной кожух и интенсивно охлаждаются
водой при помощи специальных холодильников, к которым подведены две
водопроводные магистрали, из них одна находится в работе, а другая - в резерве.
Колошник футерован стальными неохлаждаемыми плитами, полости которых
заполнены шамотным кирпичом. Купол печи футерован чугунными плитами.
Основным продуктом доменной плавки является чугун.
Расплавленный чугун через одну-две лётки по 10-18 раз в сутки выпускают
из доменной печи. В ковшах-чугуновозах ёмкостью, 80…100 т, везут его по
железнодорожным путям, попадают либо в сталеплавильный цех для передела в
сталь, либо на разливочную машину. В первом случае чугун сливают в миксеры
(копильники), ёмкостью до 2000 т, отапливаемые газом. При выдержке в миксере
выравниваются химический состав и температура чугуна, происходит дополнительное
удаление серы.
Разливочная машина представляет собой конвейер с укреплёнными на нём
формами (мульдами); в них получают небольшие слитки - чугунные чушки (до 55
кг), которые направляют на другие заводы.
В доменных печах выплавляют передельные и литейные чугуны, а также
некоторые ферросплавы.
Наиболее распространены чугуны М1, М2, М3 содержат 3,8-4,4% C, 0,5…1,5% Si, 0,5…1,5% Mn,
0,15…0,3% P, 0,02…0,06% S. Чугуны этих марок применяют для выплавки стали мартеновским
и кислородно-конверторным способом.
Чугуны марок Б1, Б2, содержащие фосфора £0,06% (класс А) и серы £0,04%(категория III), используют для передела в сталь
кислым процессом.
Фосфористые чугуны МФ1, МФ2 и МФ3 содержат 1…2% P, их переделывают в сталь в мартеновских качающихся печах.
Высококачественные чугуны ПВК1, ПВК2, ПВК3 имеют минимальное содержание
вредных примесей (например, класс А ³0,02% P,
категория I - 0,015% S) и используют для выплавки качественных сталей в
электродуговых печах и других.
Литейные чугуны ЛК0…ЛК5 применяют для получения литых деталей. В этих
чугунах содержится до 3,75% Si (ЛК0), 0,5…1,3% Mn, 0,02..0,07% S (категории I, II, III). Обычные литейные чугуны содержат
0,1…0,3% P, для художественного литья применяют
фосфористые чугуны, содержащие до 1,2% P.
Доменные ферросплавы: зеркальные чугуны ЗЧ1, ЗЧ2, ЗЧ3 содержат 10…25% Mn, ферромарганец Мн6, Мн7 (70…75% Mn), доменный ферросилиций Си10, Си15
(9…13% Si иногда и больше) и до 3% Mn. Эти сплавы применяют при выплавке
сталей для раскисления и легирования.
В доменных печах из руд некоторых месторождений выплавляют также
природно-легированные чугуны, содержащие Cr, V, Ni и т.п.
Доменный процесс имеет также и побочные продукты: доменный шлак, доменный
(колошниковый) газ, колошниковая пыль.
Доменный шлак - побочный продукт плавки и применяется для получения
строительных материалов. Широкое применение нашла мокрая грануляция шлаков:
шлак выливают в воду, и он превращается в мелкозернистый материал.
Гранулированный шлак используют для производства цемента, шлаковых строительных
кирпичей и блоков, и т.д.
Доменный или колошниковый газ. При сгорании 1 т кокса выделяется примерно
5000 м³ газа. Таким образом, в крупных печах
V = 3000…3200 м³ в сутки выделяется примерно 15…17
млн. м³ газа. Он содержит значительное
количество горючих составляющих (26…32% CO и до 4% H 2 ), его теплотворная способность
примерно 850…950 кал/м³. После очистки от пыли (частицы руды, флюса, кокса)
доменный газ используют как топливо для нагрева воздухонагревателей доменных
печей, водяных и паровых котлов, в смеси с природным газом используют для
отопления мартеновских и нагревательных печей. Колошниковая пыль содержит
45…50% Fe и её используют при агломерации.
2. Расчёт шихты, материального и теплового балансов доменной
плавки
. Химический состав сырых материалов приведён в таблице 1.
Состав кокса: 12,84% A;
1,83% S; 1,61% V. В органической массе кокса содержится: 81,2% C; 2,52% H 2 O
(сверх 100%).
. Расход сухого кокса без выноса 420 кг.
где 1000 - количество чугуна, кг; 0,945; 0,007; 0,007 - содержание в
чугуне соответственно Fe, Mn и Si (в долях единицы).
где 0,128 - содержание в коксе золы, доли ед.;
где 0,1855 - содержание железа в золе кокса, доли ед.;
в) в соответствии с составом шихтовых материалов и опытными данными
принимаем выход шлака равным 480 кг, в содержание FeO в нём 0,5% (оно обычно изменяется от 0,3 до 0,7%);
где
56 - атомная масса железа; 72 - молекулярная масса FeO;
д)
должно быть внесено железа агломератом
где
0,5392 - содержание железа в агломерате, доли ед.;
ж)
расход агломерата с учётом выноса в колошник (принимаем вынос равным 2%, он
определяется качеством агломерата и технологией доменной плавки и изменяется от
1 до 10%) составляет
3. Расчёт количества шлакообразующих приведён в таблице 2.
Таблица 2 - Количество шлакообразующих
4. Израсходовано кремнезёма на Si, переходящий в чугун по реакции
,01 (1737,6 · 0,33 + 420 · 1,83) = 13,42 кг,
где 1737,6 и 420 - расход агломерата и кокса соответственно, кг; 0,33 и
1,83 - содержание в них S, %;
б) принимаем, что в шлак переходит 85% серы, т. е.
,01 (1737,6 · 0,33 + 53,76 · 0,31) = 23,28 кг;
б) восстанавливается и переходит в чугун 7,0 кг марганца;
в) принимаем, что в шлак (в виде MnO) переходит 46% марганца шихтовых материалов, т. е.
где
71 - молекулярная масса MnO; 55 - атомная масса марганца.
9. Улетучивается Mn 3 O 4 с колошниковыми газами:
где
229 - молекулярная масса Mn 3 O 4 ; 55 -
атомная масса марганца.
11. Количество и состав шлака приведены в таблице 3.
. Проверка содержания фосфора в чугуне:
0,01
(1737,6 · 0,07 + 53,76 · 0,24) = 1,34 кг или · 100 =
0,134%.
Содержание
фосфора не выходит за допустимые пределы.
13. Окончательный состав чугуна (на величину разницы в содержании фосфора
в окончательном и заданном составах чугуна изменить содержание углерода), %:
. Расход материалов составляет, кг:
* Принимаем вынос кокса в колошнике равны 1%. Расход влажного (2,52% H 2 O)
кокса с учётом выноса
. Количество влаги шихтовых материалов и пыли, выносимых из доменной
печи, равно 1773,06 - 1737,6 = 35,46 кг.
.2 Расчёт состава и количества колошникового газа и
количества дутья
. Состав летучих веществ кокса, %:
CH 4 C 2 H 6 C 3 H 8 C 4 H 10 C 5 H 12
. На образование метана расходуется 0,8% углерода кокса.
4. Степень прямого восстановления rd = 0,35.
5. Расход природного газа 120 м³.
6. Влажность дутья 1%; в сухом дутье содержится 24% O2.
а) вносится коксом 420 · 0,812 = 341,04 кг;
б) растворяется в чугуне 1000 · 0,0395 = 35,5 кг;
в) расходуется на образование метана 341,04 · 0,008 = 2,73 кг;
г) окисляется шихтой и дутьём 341,04 - (39,5 + 2,73) = 298,81 кг.
. Окисляется шихтой, т. е. расходуется на прямое восстановление
кремния, марганца, фосфора и железа:
а) на восстановление 7 кг кремния по реакции
где
12 - атомная масса углерода; 28 - атомная масса кремния;
б)
на восстановление 7 кг марганца по реакции
в)
на восстановление 1,34 кг фосфора по реакции
г)
на восстановление железа прямым путём
где 56 - атомная масса железа; 0,35 - степень развития прямого
восстановления;
д) всего расходуется на прямое восстановление
+ 1,53 + 1,297 + 70,88 = 79,71 кг C.
3. Сгорает у фурм (окисляется дутьём):
требуется
кислорода 219,1 · = 204,49
м³,
где
22,4 - объём килограмм-молекулы кислорода, м³;
б)
на сжигание углерода углеводородов 1 м³ природного газа до оксида углерода требуется кислорода дутья
0,5CH 4 + C 2 H 6 + 1,5C 3 H 8
+ 2C 4 H 10 + 2,5C 5 H 12 - 0,5H 2 O
- 0,5CO 2 - O 2 = 0,5 · 0,9 + 0,03 + 1,5 · 0,01 + 2,0 ·
0,01 + 2,5 · 0,05 - 0,0 - 0,0 - 0,0 = 0,64 м³;
в)
при расходе природного газа 120 м³ расход кислорода составит
г)
содержание кислорода во влажном дутье
где
0,01 - содержание влаги в дутье, доли ед.; 0,5 - количество кислорода, %,
получающееся при разложении 1% влаги дутья
5. Количество метана в колошниковом газе:
где
22,4 - объём килограмм-молекулы метана, м³;
а) образуется водорода при разложении природного газа и влаги дутья,
расходуемого на сжигание 1 м³ природного газа
H 2 O + H 2 + 2CH 4 + 3C 2 H 6
+ 4C 3 H 8 + 5C 4 H 10 + 6C 5 H 12
+ =
0,0 + +0,0 + 1,8 · 0,09 + 0,04 + 0,05 + 0,25 + =
2,306 м³,
где φ - содержание водяного пара в дутье, доли ед.; ω - расход кислорода на сжигание углерода 1 м³ природного газа в окись углерода, м³;
б)
образуется водорода при разложении 120 м³ природного газа
в)
образуется водорода из влаги дутья, расходуемого на сжигание углерода кокса
г)
всего образуется водорода 276,7 + 8,42 = 285,12 м³;
д)
на основании опытных данных принимаем, что 1/3
водорода, получающегося на фурмах, участвует в реакциях косвенного
восстановления
е)
количество водорода, переходящее в газ 285,12 - 95,04 = 190,08 м³;
водород
летучих веществ кокса 420,0 · 0,01 · 0,04 · = 1,9 м³;
водород
органической массы кокса 420,0 · 0,0033 · = 15,5 м³,
где
2 и 22,4 - молекулярные массы и объём килограмм-молекулы водорода;
з)
расходуется водорода на образование метана по реакции
и)
количество водорода в колошниковом газе
190,08 + 1,9 +
15,5 - 10,2 = 197,28 м³.
7. Количество двуокиси углерода в колошниковом газе:
а) количество Fe 2 O 3 в шихтовых материалах (учитывается Fe 2 O 3 агломерата. Железо в коксе находится в виде FeO, а Fe 2 O 3 образуется при сжигании кокса для
определения содержания в нём золы) составляет
б) часть Fe 2 O 3 восстанавливается водородом по реакции
Условно считаем, что весь водород, участвующий в реакциях косвенного
восстановления, восстанавливает Fe 2 O 3 до FeO.
Количество Fe2O3, восстанавливающееся водородом
где
160 - молекулярная масса Fe 2 O 3 ; 22,4 -
объём килограмм-молекулы H 2 , м³;
в)
образуется воды 95,04 · = 76,4
кг,
г)
количество Fe2O3, восстанавливающееся оксидом углерода
д)
образуется диоксида углерода при восстановлении по реакции
е)
количество диоксида углерода, образующееся при восстановлении железа из
где
0,65 - степень косвенного восстановления;
ж)
образуется диоксида углерода от непрямого восстановления
8. Количество оксида углерода в колошниковом газе:
а) образуется оксида углерода от окисления углерода кокса шихтой и дутьём
б)
образуется оксида углерода при горении 1 м³ природного газа
CO 2 + CO + CH 4 + 2C 2 H 6
+ 3C 3 H 8 + 4C 4 H 10 + 5C 5 H 12
= 0,0 + 0,0 + 0,9 +2 · 0,03 + 3 · 0,01 + 4 · 0,01 + 5 · 0,05 = 1,28 м³;
в)
из 120 м³ природного газа образуется оксида углерода
г)
остаётся в газе оксида углерода после расхода части её на непрямое восстановление
607,6 + 153,6 - 280,4 = 480,8 м³;
9. Количество азота в колошниковом газе:
а) содержание азота во влажном дутье 76,0 (1,00 - 0,01) = 75,2%;
б) дутьё вносит азота 1157,57 · 0,752 = 870,5 м³;
в) коксом вносится азотом примерно 2 м³ (можно не учитывать);
г) всего азота в колошниковом газе 870,5 + 2,0 = 872,5 м³.
. Количество и состав колошникового газа:
2.3 Материальный баланс доменной плавки
где
23,8; 75,2; 1,0 - содержание в дутье соответственно O 2 , N 2 и H 2 O, %;
32, 28, 18 - молекулярная масса O 2 , N 2 и H 2 O соответственно;
б)
дутьё весит 1,288 · 1157,57 = 1490,95 кг.
где
90,0; 3,0; 1,0; 5,0 и 16, 30, 44, 58, 72 - содержание и молекулярные массы
отдельных углеводородов природного газа;
б)
масса 120 м³ природного газа 0,89 · 120 = 106,8 кг.
где
15,27; 26,19; 47,52; 10,74; 0,28 и 44, 28, 28, 2, 16 - содержание и
молекулярные массы отдельных составляющих колошникового газа;
б)
колошниковый газ весит 1,234 · 1836,08 = 2254,7 кг.
4. Данные материального баланса приведены в таблице 4.
Mn 3 O 4 ,
улетучивающейся в колошник
влаги кокса 424,24 · 0,0252 = 10,69 кг;
колошниковой пыли 35,46 - 10,69 = 24,77 кг.
Невязка составляет (допустимое отклонение равно 0,5%):
17899 · 280,4 + 5250 · 327,2 = 6736679,6 кДж,
где 280,4 и 327,2 - соответственно количество CO 2 , образующееся при непрямом восстановлении, и CO, образующееся при окислении углерода
кокса шихтой и дутьём, за вычетом CO, расходуемой в реакциях косвенного восстановления, м³; 17899 и 5250 - тепло, выделяющееся
при горении углерода соответственно в CO 2
и CO, кДж/м³.
. Тепло сгорания природного газа с образованием CO и H 2 :
а) при сгорании 1 м³ природного газа выделяется тепла
1658CH 4 + 6050C 2 H 6 + 10121C 3 H 8
+ 13796C 4 H 10 + 18053C 5 H 12 - 12642CO 2
- 10806H 2 O = 1658 · 0,9 + 6050 · 0,03 + 10121 · 0,01 + 13796 · 0,01
+ + 18053 · 0,05 - 0,0 - 0,0 = 2815,5 кДж;
б) при сгорании 120 м³ природного газа выделяется тепла
. Тепло окисления водорода в реакциях косвенного восстановления
железа: 10806 · 95,04 = 1027002,2 кДж,
где 10806 - тепло, выделяющееся при сгорании 1 м³ H 2 , кДж.
а) теплоёмкость сухого воздуха при температуре дутья 1200° C 1,4373, водяного пара 1,7672 кДж/(м³·°C);
б) водяных паров в дутье содержится 1157,57 · 0,01 = 11,58 м³;
в) сухого дутья подаётся 1157,57 - 11,58 = 1146 м³;
г) приход тепла (1,4373 · 1146 + 1,7672 · 11,58) 1200 = 2001132 кДж.
,6 + 337860 + 1027002,2 + 2001132 = 10102673,8 кДж.
. На диссоциацию оксидов и перевод серы в шлак:
а) количество FeO, вносимое
шихтовыми материалами
Агломератом - 1737,6 · 0,2074 = 360,380
Золой
кокса - 53,76 · 0,1855 · = 18,82
где
72 и 56 - молекулярная масса FeO и атомная масса железа соответственно;
б)
условно считаем, что в золе кокса весь FeO, а в
офлюсованном агломерате 10% FeO связаны в силикатных соединениях. Количество FeO,
связанного в силикаты, магнетита и свободного Fe 2 O 3 составляет:
,82
+ 360,38 · 0,1 = 48,86 кг FeOсил,
(1737,6
· 0,5317) - 720,76 = 203,12 Fe2O3св,
в)
тепло на диссоциацию оксидов железа
(48,86
- 2,44) + 4800 · 1045,1 + 5154 · 203,12 = 6252568,4 кДж,
где
4076, 4800, 5154 - расход тепла на разложение соответственно FeO
силикатных соединений, магнитного Fe 2 O 3 и Fe 3 O 4 кДж/кг;
г)
тепло на диссоциацию оксидов марганца (в агломерате они находятся в виде
силикатов)
где
7360 и 532 - расход тепла на разложение MnO и силиката
марганца на MnO и SiO2 соответственно, кДж/кг Mn;
где
31079 - тепло разложения SiO 2 , кДж/кг Si;
е)
тепло на диссоциацию P 2 O 5 из
фосфорно-кальциевой соли
где
35755 - тепло разложения P 2 O 5 ,
входящей в состав фосфорно-кальциевой соли, кДж/кг P;
ж)
тепло на перевод серы в шлак 5728 · 11,4 = 65299,2 кДж,
где
5728 - расход тепла на перевод серы в шлак, кДж/кг S;
з)
всего по первой статье расходуется тепла
,4
+ 55244 + 217553 + 47911,7 + 65299,2 = 6638576,3 кДж.
2. Шихта не содержит карбонатов и тепло на их разложение не
расходуется.
3. Тепло разложения влаги дутья:
где 10806 - расход тепла на разложение 1 м³ H 2 O,
кДж.
(2261 + 419) 0,0252 · 424,24 = 28651,47 кДж
где 2261 - скрытая теплота испарения, кДж/кг H 2 O; 419
- расход тепла на нагрев влаги до 100° C, кДж/кг H 2 O.
. Тепло, уносимое чугуном, равно:
где 1130 - энтальпия чугуна, кДж/кг.
. Тепло, уносимое шлаком, составляет:
где 1675 - энтальпия шлака, кДж/кг.
. Тепло, уносимое колошниковым газом, водяным паром и пылью при
температуре 250° C (в зависимости
от условий работы печи температура колошниковых газов изменяется от 150° C до 350° C):
а) теплоёмкость при этой температуре газа 1,3858 кДж/(м³·°C); колошниковой пыли 0,7536 кДж/(кг·°C);
,3858 · 1836,08 · 250 + 1,5302 · 10,69 (250 - 100) + 0,7536 · 24,77 · 250
= 643230,27 кДж;
,3 + 125133,48 + 28651,47 + 1130000 + 703851,75 + 643230,27 = 9269443,27
кДж.
. Тепло, теряемое с охлаждающей водой и во внешнее пространство
радиацией и конвекцией, определяется по разности между приходом и расходом
тепла по статьям 1-7:
. Данные теплового баланса приведены в таблице 5.
Диссоциация оксидов Fe,
Mn, Si, P и перевод серы в шлак
Исходные данные . Суточная производительность 6500 т чугуна, к. и. п. о. 046
т. сут/м³. Полезную высоту принимаем равной
32170 мм, полную 34920 мм.
. Определим полезный объём доменной печи:
. Определим диаметр распара, принимая коэффициент k ’ равным 0,53:
3. Принимаем относительный расход кокса 0,42 на 1 т чугуна (печь будет
работать с применением высоконагретого комбинированного дутья и полностью
офлюсованного агломерата, с высоким содержанием железа). Расход кокса составит
6500 · 0,42 = 2730 т/сут.
. Принимая по суточному расходу кокса рекомендуемую М.А. Павловым
интенсивность сгорания кокса на 1 м² сечения горна 26,4 т/(м²·сут), определяем площадь горна: 2730
: 26,4 = 103,41 м².
.
Диаметр колошника определим из соотношения d к : D р = 0,67 ÷ 0,75. Принимаем это соотношение равным 0,67, тогда:
.
Высоту горна определим из условия, что на 1 т суточной выплавки чугуна
необходимо 0,062 м³ объёма горна, что вполне достаточно при частых
выпусках чугуна: h г = (6500
· 0,062) : 103,41 = 3,9 м.
где
6500 - суточная производительность печи, т чугуна.
.
На основании опытных данных принимаем высоту заплечиков равной 3,4 м.
.
Определяем угол наклона заплечиков:
tgβ = 3,4 : 0,5 (12,71 - 11,48) = 5,5284;
.
На основании опытных данных высоту цилиндрической части колошника принимаем
равной 3,0 м, а высоту распара - равной 2,2 м.
h ш = 32,1 - (3,9 + 3,2 + 3,0 + 2,0) = 20 м.
tgα = 20 : 0,5 (12,71 - 8,52) = 9,547;
V з = · 3,14 ·
3,2 (6,362 + 6,36 · 5,77 + 5,742) = 368,7 м³;
V ш = · 3,14 ·
20 (6,362 + 6,36 · 4,26 + 4,262) = 1793,8 м³;
V пол = 403,5 + 368,7 + 253,6 + 1793,8 + 171 = 2990,6 м³.
Черная металлургия - ведущая отрасль народного хозяйства, от которой существенно
зависит благополучие страны. С позиций сегодняшнего дня, когда новым
технологиям уделяется первейшее внимание, произошло много изменений в
металлургических технологиях. Установившаяся технология производства чугуна,
стали и проката к началу XX века принципиально сохранилась до настоящего
времени, хотя агрегатное оформление стало другим. Доменная печь за первые 50
лет XX века приобрела современный профиль, её объём возрос от нескольких сотен
кубических метров до 1-3 тысяч, а за следующие 50 лет до 5 и более тысяч м³. За это время доменная печь получила
современную систему загрузки, подготовленное сырьё, высокую температуру дутья с
добавкой кислорода, природного газа и других заменителей кокса, повышенное
давление.
В данном курсовом проекте был рассчитан материальный и тепловой баланс
доменной плавки. По подсчётам выяснилось, что для получения 1 т чугуна
потребуется 2197 кг шихтовых материалов, 1491 кг дутья и 107 кг природного
газа.
. Воскобойников В.Г., Кудрин В.А, Якушев A.M.: Общая металлургия, 6 изд., переработанный и доп. - М., ИКЦ
"Академкнига", 2002 - 768 с.
2. Полтавец В.В.: Доменное производство - М.,
"Металлургия", 1981 - 416 с.
3. Е.Ф. Вегман, Б.Н. Жеребин, А.Н. Похвиснев, Ю.С. Юсфин,
И.Ф. Курунов, А.Е. Пареньков, П.И. Черноусов: Металлургия чугуна, М.,
"Академкнига", 2004 - 774 с.
4. Павлов М.А.: Сборник трудов по теории доменной плавки, т.
1, М., "Металлургия", 1957.
5. Готлиб А.Д.: Доменный процесс, 2 изд. М.,
"Металлургия", 1966.
Похожие работы на - Расчет шихты, материального и теплового балансов доменной плавки Курсовая работа (т). Другое.
Промышленное Производство В Странах Зарубежной Европы Реферат
Реферат Про Австралийских Животных
Контрольная работа по теме Державно-правовий розвиток Німеччини другої половини XIX століття
Контрольная работа по теме История экономической этики
Практическая Работа 1 11 Класс
Сочинение Чему Учит Литература 18 Века
Сочинение О Памятном Событии План
Реферат: Государственное правовое регулирование Российской империи в первой половине XIX века
Школа Моей Мечты Сочинение 6 Класс
Курсовая работа по теме Влияние СМИ на социализацию личности детей раннего возраста
Реферат Выбор Субд
Музеи Реферат
Контрольная работа по теме Развитие словесно-логического мышления у школьников в процессе изучения математики
Контрольная работа: Планирование и прогнозирование экономики
Бесплатные Банки Рефератов И Курсовых
Эссе На Тему Настоящие Друзья
Контрольная Работа По Химии 9 Класс Растворы
Курсовая Работа На Тему 8 Марта
Реферат: Соседи восточных славян. Кочевники и Византия. Скачать бесплатно и без регистрации
Помню Горжусь Эссе
Реферат: Реферат: содержание и правила написания
Похожие работы на - Средняя Азия в XVI—XIX вв.
Похожие работы на - Сигаретный цех проектируемой табачной фабрики: основные технико-экономические показатели