Расчет процесса получения алюминия. Курсовая работа (т). Другое.
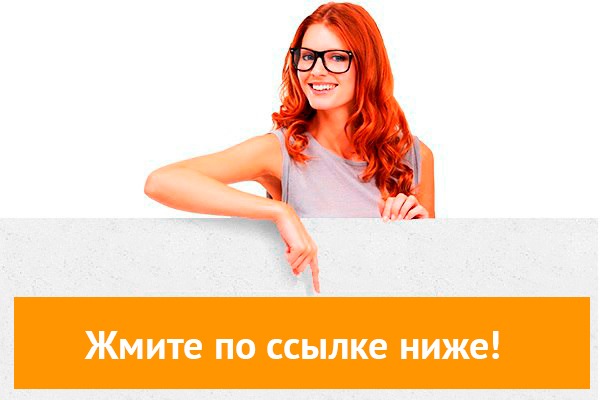
🛑 👉🏻👉🏻👉🏻 ИНФОРМАЦИЯ ДОСТУПНА ЗДЕСЬ ЖМИТЕ 👈🏻👈🏻👈🏻
Вы можете узнать стоимость помощи в написании студенческой работы.
Помощь в написании работы, которую точно примут!
Похожие работы на - Расчет процесса получения алюминия
Скачать Скачать документ
Информация о работе Информация о работе
Скачать Скачать документ
Информация о работе Информация о работе
Скачать Скачать документ
Информация о работе Информация о работе
Скачать Скачать документ
Информация о работе Информация о работе
Скачать Скачать документ
Информация о работе Информация о работе
Скачать Скачать документ
Информация о работе Информация о работе
Скачать Скачать документ
Информация о работе Информация о работе
Нужна качественная работа без плагиата?
Не нашел материал для своей работы?
Поможем написать качественную работу Без плагиата!
Министерство образования и науки РФ
Новосибирский государственный
технический университет
по дисциплине "Общая химическая
технология"
"Расчет процесса получения
алюминия"
Физико-химические основы процесса Байера
Расчет числа электролизеров и производительности серии
Конструктивный расчет электролизера
Энергетический расчет электролизера
Алюминий - мягкий, легкий, серебристо-белый металл с высокой
тепло- и электропроводностью. Температура плавления 660°C. По
распространенности в земной коре алюминий занимает 3-е место после кислорода и
кремния среди всех атомов и 1-е место - среди металлов.
К достоинствам алюминия и его сплавов следует отнести его малую
плотность (2,7 г/см3), сравнительно высокие прочностные характеристики, хорошую
тепло - и электропроводность, технологичность, высокую коррозионную стойкость.
Совокупность этих свойств позволяет отнести алюминий к числу важнейших
технических материалов.
Наряду с чистым алюминием большое значение имеют и
алюминиевые сплавы, в которых сохраняется основное свойство алюминия - малый
удельный вес и имеются новые ценные для целей практического применения
свойства, отсутствующие или недостаточно развитые у чистого алюминия. Все
сплавы алюминия можно разделить на две группы:
Деформируемые алюминиевые сплавы - предназначены для
получения полуфабрикатов (листов, плит, прутков, профилей, труб и т.д.), а
также поковок и штамповых заготовок путем прокатки, прессования, ковки и
штамповки.
а) Упрочняемые термической обработкой:
Дуралюмины, "дюраль" (Д1, Д16, Д20*, сплавы
алюминия меди и марганца [Al-Cu-Mg]) - удовлетворительно обрабатываются
резанием в закаленном и состаренном состояниях, но плохо в отожженном
состоянии. Дуралюмины хорошо свариваются точечной сваркой и не свариваются
сваркой плавлением вследствие склонности к образованию трещин. Из сплава Д16
изготовляют обшивки, шпангоуты, стрингера и лонжероны самолетов, силовые
каркасы, строительные конструкции, кузова автомобилей.
Сплав авиаль (АВ) удовлетворительно обрабатывается резанием
после закалки и старения, хорошо сваривается аргонодуговой и контактной
сваркой. Из этого сплава изготовляются различные полуфабрикаты (листы, профили,
трубы и т.д.), используемые для элементов конструкций, несущих умеренные
нагрузки, кроме того, лопасти винтов вертолетов, кованные детали двигателей,
рамы, двери, для которых требуется высокая пластичность в холодном и горячем
состоянии.
Высокопрочный сплав (В95) имеет предел прочности 560-600
Н/мм2, хорошо обрабатывается резанием и сваривается точечной сваркой. Сплав
применяется в самолетостроении для нагруженных конструкций (обшивки, стрингеры,
шпангоуты, лонжероны) и для силовых каркасов в строительных сооружениях.
Сплавы для ковки и штамповки (АК6, АК8, АК4-1 [жаропрочный]).
Сплавы этого типа отличаются высокой пластичностью и удовлетворительными
литейными свойствами, позволяющими получить качественные слитки. Алюминиевые
сплавы этой группы хорошо обрабатываются резанием и удовлетворительно
свариваются контактной и аргонодуговой сваркой.
б) Не упрочняемые термической обработкой:
Сплавы алюминия с марганцем (АМц) и алюминия с магнием (АМг2,
АМг3, АМг5, АМг6) легко обрабатываются давлением (штамповка, гибка), хорошо
свариваются и обладают хорошей коррозионной стойкостью. Обработка резанием
затруднена, поэтому для получения резьбы используют специальные бесстружечные
метчики (раскатники), не имеющие режущих кромок.
Литейные алюминиевые сплавы - предназначенные для фасонного
литья (как правило, хорошо обрабатываются резанием).
Сплавы алюминия с кремнием (силумины) Al-Si (АЛ2, АЛ4, АЛ9)
отличаются высокими литейными свойствами, а отливки - большой плотностью.
Силумины сравнительно легко обрабатываются резанием.
Сплавы алюминия с медью Al-Cu (АЛ7, АЛ19) после термической
обработки имеют высокие механические свойства при нормальной и повышенных
температурах и хорошо обрабатываются резанием.
Сплавы алюминия с магнием Al-Mg (АЛ8, АЛ27) имеют хорошую
коррозионную стойкость, повышенные механические свойства и хорошо
обрабатываются резанием. Сплавы применяют в судостроении и авиации.
Жаропрочные алюминиевые сплавы (АЛ1, АЛ21, АЛ33) хорошо
обрабатываются резанием.
С точки зрения обработки фрезерованием, нарезания резьбы и
токарной обработки, алюминиевые сплавы также можно разделить на две группы. В
зависимости от состояния (закаленные, состаренные, отожженные) алюминиевые
сплавы могут относиться к разным группам по легкости обработки:
Мягкие и пластичные алюминиевые сплавы, вызывающие проблемы
при обработке резанием: а) Отожженные: Д16, АВ. б) Не упрочняемые термической
обработкой: АМц, АМг2, АМг3, АМг5, АМг6.
Сравнительно твердые и прочные алюминиевые сплавы, которые
достаточно просто обрабатываются резанием (во многих случаях, где не требуется
повышенная производительность, эти материалы могут обрабатываться стандартным
инструментом общего применения, но если требуется повысить скорость и качество
обработки, необходимо применять специализированный инструмент): а) Закаленные и
искусственно состаренные: Д16Т, Д16Н, АВТ.
в) Литейные: АЛ2, АЛ4, АЛ9, АЛ8, АЛ27, АЛ1, АЛ21, АЛ33.
Большинство алюминиевых сплавов имеют высокую коррозионную
стойкость в естественной атмосфере, морской воде, растворах многих солей и
химикатов и в большинстве пищевых продуктов. Последнее свойство в сочетании с
тем, что алюминий не разрушает витамины, позволяет широко использовать его в
производстве посуды. Конструкции из алюминиевых сплавов часто используют в
морской воде, изготовляют корпусы судов, палубные надстройки, коммуникацию и
различного рода судовое оборудование. Алюминий в большом объеме используется в
строительстве в виде облицовочных панелей, дверей, оконных рам, электрических
кабелей. Внедрение алюминиевых сплавов в строительстве уменьшает металлоемкость,
повышает долговечность и надежность конструкций при эксплуатации их в
экстремальных условиях (низкая температура, землетрясение и т.п.). Алюминиевые
сплавы не подвержены сильной коррозии в течение длительного времени при
контакте с бетоном, строительным раствором, штукатуркой, особенно если
конструкции не подвергаются частому намоканию. Алюминий, благодаря комплексу
свойств, широко распространен в тепловом оборудовании.
Электропроводность алюминия сравнима с медью, при этом
алюминий дешевле. Поэтому он широко применяется в электротехнике для
изготовления проводов, их экранирования и даже в микроэлектронике при
изготовлении проводников в чипах. Правда, у алюминия как электротехнического
материала есть неприятное свойство - из-за прочной оксидной пленки его тяжело
паять.
Алюминий находит широкое применение в различных видах
транспорта. На современном этапе развития авиации алюминиевые сплавы являются
основными конструкционными материалами в самолетостроении.
Идут исследования по разработке пенистого алюминия как особо
прочного и легкого материала.
Глиноземом называется кристаллическая окись алюминия. Она
является основным сырьем для получения алюминия. Алюминий получают из глинозема
электролизом. Глинозем используется также и в других отраслях промышленности
(например, для отбеливания бумаги, производства специальных сортов цемента,
цеолитов - веществ, поглощающих определенный сорт молекул в присутствии других
молекул и пр.). Кроме того, иногда бывает рентабельно в состав производства
глинозема включать производство редких металлов, сопутствующих алюминию в руде
(таких, как галлий, ванадий и пр.).
Глинозем получают из руды, содержащей горную породу - боксит.
Бокситы имеют сложный химико-минералогический состав. Основной и полезной их
частью являются различные модификации гидрата окиси (гидроокиси) алюминия ( Аl
(ОН) 3 , AlOОН и др.). В состав бокситов входят обычно окислы
железа, кремния, в малом количестве - серы, титана, галлия, хрома, ванадия и
пр., а также карбонатные соли кальция, магния, железа, органические вещества
(остатки древних растений и животных) и пр. Чрезмерное содержание любых других
примесей также является вредным и приводит к повышению затрат на производство
глинозема.
Глинозем можно получить тремя методами: кислотным, щелочным и
электролитическим. Самым популярным и наиболее простым является щелочной метод,
предложенный Байером и называемый Байер-процессом. Суть метода заключается в
том, что алюминиевые растворы очень быстро начинают разлагаться при введении
гидроокиси алюминия, а раствор, который остался от разложения после выпаривания
при интенсивном перемешивании при температуре 170 С, может снова растворить
глинозем, который содержится в бокситах. Данный способ имеет такие главные
стадии:
. Подготовка боксита, которая подразумевает его дробление и
измельчение в специальных мельницах. В мельницы отправляют едкую щелочь, боксит
и немного извести. Пульпу, которая получилась, направляют на выщелачивание.
. Выщелачивания боксита подразумевает его химическое
разложение от соединения с водным раствором щелочи. При этом гидраты окиси
алюминия при соединении со щелочью в раствор переходят в форме алюмината
натрия, а кремнезем, который содержится в боксите, соединяясь со щелочью, в
раствор переходит в форме силиката натрия. В растворе эти соединения: алюминат
натрия и силикат натрия формируют нерастворимый натриевый алюмосиликат. В этот
остаток переходят окислы железа и титана, которые предают остатку красный
оттенок. Такой остаток - это красный шлам. Когда растворение полученного
алюмината натрия завершается, его разводят водным раствором щелочи при
понижении температуры до 100°С.
. Отделение красного шлама и алюминатного раствора друг от
друга происходит благодаря промывке в сгустителях. После чего красный шлам
оседает, а оставшийся алюминатный раствор фильтруют.
. Разложение алюминатного раствора. Его фильтруют и
отправляют в крупные емкости с мешалками. Из данного раствора при охлаждении до
60°С и постоянном перемешивании выделяется гидроокись алюминия. Из-за того, что
процесс протекает неравномерно и очень медленно, а рост кристаллов гидроокиси
алюминия очень важен при дальнейшей обработке, то в эти емкости с мешалками -
декомпозеры ещё добавляют много твердой гидроокиси.
. Получение гидроокиси алюминия осуществляется в
вакуум-фильтрах и гидроциклонах. Большую часть гидроокиси как затравочный
материал возвращают к процедуре декомпозиции. После водной промывки остаток
отправляется на кальцинацию; и фильтрат тоже возвращается в процесс.
. Обезвоживание гидроокиси алюминия - завершающая стадия
производства глинозема. Она проходит в трубчатых, постоянно вращающихся печах.
Сырая гидроокись алюминия, когда проходит через печь, полностью высушивается и
обезвоживается. (Схема 1).
В окончательно прокаленном глиноземе содержится 30-50% α-Al2O3 (корунд), остальное γ-Al2O3.
Этим способом извлекается 85-87% от всего получаемого
глинозема. Полученная окись алюминия представляет собой прочное химическое
соединение с температурой плавления 2050 о С.
Необходимым условием производства глинозема является контроль
и соблюдение параметров веществ и процессов на всех этапах производства,
начиная от подачи в него боксита и кончая выгрузкой готового глинозема. К ним,
в частности, относятся: тонкость помола, концентрация щелочи, температура,
давление, расход жидких и твердых веществ, расход энергоносителей и их
параметры, крупность затравки и многое другое. Получают эти данные еще на
стадии проектирования завода посредством многочисленных теоретических расчетов
и экспериментальных проверок и корректируют их после пуска производства.
Контроль за соблюдением технологии осуществляется постоянно специально
лабораторией, а соблюдение условий производства является основной функцией
инженерно-технического персонала и рабочих.
Важной составной частью производства является энергетическое
хозяйство, поставляющее электроэнергию, тепло и пар для подогрева растворов и
сухих веществ.
Глиноземное производство эксплуатирует очень большое число
различных насосов и единиц запорной арматуры, и от их надежности существенным
образом зависит стабильность производства.
Сегодняшнее производство глинозема в значительной мере
автоматизировано.
Это существенно облегчает управление процессами, но требует
более квалифицированного персонала для обслуживания.
Схема 1. Схема производства глинозёма по Байеру.
В основе способа Байера лежит химическая реакция Al (OH) 3 +
+NaOH ?
NaA1O 2 +2H 2 O. В условиях выщелачивания равновесие этой
реакции сдвинуто вправо, т.е. гидроксид алюминия из боксита 'переходит в
раствор в виде алюмината натрия. В условиях декомпозиции равновесие сдвигается
в обратную сторону, т.е. происходит гидролиз алюминатного раствора с выделением
в осадок гидроксида алюминия.
Затраченная при выщелачивании щелочь освобождается при
декомпозиции и возвращается в голову процесса-на выщелачивание новых порций
боксита. Таким образом, в способе Байера цикл по щелочи замкнут.
Она направлена к точке Al 2 O 3 *ЗH 2 O
при выщелачивании гиббситовых бокситов и к точке Al 2 O 3 *H 2 O-при
выщелачивании бемитовых и диаспоровых бокситов.
После выщелачивания раствор (пульпу) разбавляют. Разбавление
конденсатом в зависимости от способа нагрева пульпы может начинаться еще в
процессе выщелачивания. Состав раствора при этом перемещается из точки Б в
точку В. Далее следует разбавление пульпы промывными водами. Так как при
разбавлении каустический модуль не изменяется, то точка Г, отвечающая составу
раствора после разбавления, должка лежать на линии постоянного каустического
модуля. Линия БГ, характеризующая изменение концентрации раствора при
разбавлении, называется линией разбавления. Раствор в точке Г имеет температуру
порядка 95-100°С; он практически стойкий.
Смешение алюминатного раствора с затравкой ведет к изменению
его каустического модуля, так как вместе с затравкой вносится некоторое
количество маточного раствора, имеющего высокий каустический модуль. Состав
раствора при этом из точки Г переходит в точку Д. Линия ГД называется линией
смешения с затравкой.
Рис. 7. Цикл процесса Байера в системе Al 2 O 3 -Na 2 O
- H 2 O.
При декомпозиции раствор охлаждается до температуры порядка
50 ºС и оказывается в области пересыщенных глиноземом растворов.
Пересыщенный раствор гидролитически разлагается, что сопровождается снижением
концентрации глинозема в нем и повышением каустического модуля. Составу
маточного раствора после декомпозиции отвечает точка Е. Линия ДЕ называется
линией декомпозиции. Она направлена к точке Al 2 O 3 *ЗH 2 O.
Далее следует выпаривание маточного раствора. При выпаривании концентрация
раствора повышается, каустический же модуль остается постоянным, поэтому состав
раствора из точки Е перемещается, но линии постоянного каустического модуля в
точку Ж. Линия ЕЖ называется линией выпаривания. После добавки свежей щелочи
состав оборотного раствора переходит в точку А, в которой цикл заканчивается и
начинается новый.
Электролитическое восстановление окиси алюминия, растворенной
в расплаве на основе криолита, осуществляется при 950-970°С в электролизере.
Электролизер состоит из футерованной углеродистыми блоками ванны, к подине
которой подводится электрический ток. Выделившийся на подине, служащей катодом,
жидкий алюминий тяжелее расплава соли электролита, поэтому собирается на
угольном основании, откуда его периодически откачивают. Сверху в электролит
погружены угольные аноды, которые сгорают в атмосфере выделяющегося из окиси
алюминия кислорода, выделяя окись углерода (CO) или двуокись углерода (CO 2 ).
На практике находят применение два типа анодов:
а) самообжигающиеся аноды Зедерберга, состоящие из брикетов,
так называемых "хлебов" массы Зедерберга (малозольный уголь с 25-35%
каменноугольного пека), набитых в алюминиевую оболочку; под действием высокой
температуры анодная масса обжигается (спекается);
б) обожженные, или "непрерывные", аноды из больших
угольных блоков (например, 1900×600×500 мм массой около 1,1 т).
Нормальная работа алюминиевых электролизных ванн
характеризуется параметрами энергетического и технологического режима,
рассчитанными при проектировании в зависимости от конструктивных особенностей
электролизеров. К этим параметрам относятся сила тока, рабочее и среднее
напряжение, температура электролита, количество металла и электролита, перепад
напряжения в подине ванны, состав электролита, частота и продолжительность
анодных эффектов, форма рабочего пространства, а также технологические
параметры формирования самообжигающихся анодов.
Силу тока серии устанавливают в зависимости от размеров,
конструкции н технологического состояния электролизеров, а регулируют её,
исходя из технических возможностей оборудования преобразовательной подстанции.
Среднюю силу тока серии вычисляют на основании средней мощности, потребляемой
серией, и среднего напряжения. Среднюю мощность, потребляемую серией,
определяют по величине расхода электроэнергии постоянного тока, технологической
электроэнергии переменного тока и коэффициента преобразования, включающего
расход электроэнергии подстанцией на собственные нужды и потерю энергии в
шинопроводе от подстанции до электролизной серии. При наличии достаточно точных
средств учета силы тока среднесуточную силу тока определяют
по показаниям счетчиков ампер-часов. Среднемесячное значение
силы тока рассчитывают по потребляемой мощности постоянного тока.
Среднее напряжение серии вычисляют по показателям серийных
счетчиков вольт-часов. Расчет и контроль силы тока и напряжения серии
осуществляются персоналом преобразовательной подстанции.
Рабочее напряжение электролизера контролируют по показателям
вольтметров, установленных на электролизерах, и поддерживают в пределах,
оговоренных в рабочих технологических инструкциях. Для различных типов
электролизеров рабочее напряжение составляет 3,8-4,3В. Рабочее напряжение
электролизеров, как правило, регулируется автоматически и поддерживается в
пределах заданной установки по сопротивлению.
Среднее напряжение электролизера состоит из рабочего
напряжения, напряжения анодных эффектов и перепада напряжения в ошиновке между
электролизерами; рассчитывается по показанию серийных вольтметров.
Температуру электролита на нормально работающем электролизере
поддерживают в пределах 950-965°С. Этот параметр оказывает наибольшее влияние
на производительность электролизера, поэтому все операции технологического
процесса подчинены одной цели - поддержанию температуры электролита на нижнем
пределе, вплоть до снижения силы тока по серии.
Количество технологического алюминия в электролизере
характеризуется высотой столба (уровнем) металла в шахте ванны. Уровень металла
в силу высокой теплопроводности алюминия позволяет регулировать теплоотдачу
электролизера: чем выше этот уровень, тем больше тепла отводится через боковые
поверхности катодного узла электролизера. Увеличение уровня металла
способствует интенсификации (повышению силы тока) процесса электролиза.
Однако повышенный уровень металла осложняет ведение
технологического процесса - увеличивается образование глиноземистых осадков на
подине, наблюдается образование пологих подовых настылей, что снижает выход по
току и в конечном итоге - производительность электролизера. Поэтому для каждой
конструкции электролизеров в зависимости от выбранной технологии процесса в
рабочей технологической инструкции указывается оптимальный уровень
технологического металла - уровень металла в шахте ванны после очередной
выливки.
Состав электролита наиболее существенно влияет на
технико-экономические показатели работы электролизера. Многочисленными
научно-исследовательскими работами установлено, а промышленной практикой
подтверждено, что при прочих равных условиях лучшие показатели технологического
процесса достигаются при электролите с криолитовым отношением 2,6-2,85 в
зависимости от типа электролизеров и суммарном содержании добавок до 9,0 %.
Наиболее часто в практике алюминиевой промышленности в качестве добавок к
электролиту используют фтористые соли лития, кальция и магния; иногда -
хлористый натрий.
Анодные эффекты (вспышки) подразделяются на
"тусклые" (менее 10В), "средние" (менее 25В),
"мигающие” (напряжение вспышки резко изменяется) и "ясные" (выше
25В). По характеру вспышек контролируют работу электролизера. В нормально
работающем электролизере напряжение анодного эффекта мгновенно поднимается от
4,3-4,5 до 25 В, а иногда и выше. Возникновение вспышек другого характера
указывает на отклонения от нормальной работы электролизера.
Анодные эффекты оказывают существенное влияние на тепловой
режим электролизера и при необходимости могут быть использованы для разогрева
расплава. Вместе с тем следует постоянно помнить, что во время анодного эффекта
и сразу же после его устранения резко снижается производительность
электролизера (одна из причин снижения выхода по току), а расход электрической
энергии в этот период при неизменной силе тока возрастает во столько раз, во
сколько величина напряжения анодного эффекта выше величины рабочего напряжения
на нормально работающем электролизере. Следовательно, производительность
электролизера (серии, цеха, завода) находится в прямой зависимости от
продолжительности и (частоты) анодных эффектов. Величина потери
производительности электролизера (серии, цеха, завода) для определенной
продолжительности и частоты анодных эффектов, выраженная в процентах,
постоянна.
Форма рабочего пространства нормально работающего
электролизера характеризуется обязательным наличием защитных гарниссажей в зоне
электролита, крутопадающей настылью в зоне металла и отсутствием осадка и
настыли на подине под анодом. Создание и постоянное поддержание указанной формы
рабочего пространства - задача обслуживающего персонала.
Перепад напряжения в подине электролизера во многом зависит
от формы рабочего пространства ванны и определяется путем измерения
специальными щупами падения напряжения на участке жидкий алюминий - катодный
стержень. На нормально работающем электролизере перепад напряжения в подине
составляет 0,3-0,4 В; увеличение перепада свидетельствует о наличии на подине
осадков или пастылей.
При определении характера работы ванны необходимо принимать
во внимание, что по мере увеличения срока эксплуатации электролизера перепад напряжения
в подине имеет тенденцию к увеличению.
В современной практике ведения процесса электролиза алюминия
наблюдаются две тенденции. Там, где стоимость электрической энергии
относительно низка, предпочитают работать в интенсифицированном режиме-со сравнительно
высоким уровнем технологического металла (300-450 мм). В районах с дорогой
электроэнергией предпочитают работать в менее интенсифицированном режиме-с
уровнем металла 150-250 мм. Развитие техники и технологии отечественной
алюминиевой промышленности в основном идет по пути максимальной интенсификации
процесса электролиза.
Схемы электролизеров приведены в приложении.
Расчетная величина среднего напряжения, В:
,335 - электрохимический эквивалент, г/ (А∙ч), W - расход электроэнергии,
кВт∙ч/т; η Т - выход по току, %.
Для электролизеров с боковым подводом тока к аноду (БТ) W = 14500 - 18000 кВт∙ч/т,
с верхним подводом тока (ВТ) W = 14200 - 16500 кВт∙ч/т, с обожженными анодами (OA) W = 13800 - 15000 кВт∙ч/т.
Выход по току для электролизеров с боковым токоподводом
составляет η Т =85 - 87%, с верхним
токоподводом η т =84 - 86%, с обожженными
анодами η т =87 - 92%.
U cp =0,335∙14000∙90∙10 -5 =4,221
В.
Число работающих электролизеров в серии определяется средним
напряжением выпрямительных агрегатов.
При этом учитываются: потери напряжения в шинопроводах
преобразовательной подстанции (принимаются 1 %), резерв напряжения для
предупреждения снижения силы тока при возникновении анодного эффекта
(принимается 30 В) и резерв напряжения для компенсации возможных колебаний во
внешней электросети (принимается 1 %).
Напряжение на подстанции задано (825 или 850 В). Тогда
напряжение, которое определяет число устанавливаемых в серии электролизеров,
составляет, В:
U действ. = U подстанции - 30 - U подстанции ∙0,02 = 0,98 ∙
U подстанции - 30.
Подставим известное значение напряжения на подстанции в
формулу:
При работе в режимах, когда допускается один анодный эффект в
сутки продолжительностью 1,5 мин с напряжением 35 В, составляющая часть от
анодных эффектов в среднем напряжении электролизера будет равна, В:
где m - количество анодных эффектов в сутки
(1); - продолжительность анодного эффекта, мин (1,5 мин); U а. э. - напряжение анодного эффекта, В (35 В); 24
- число часов в сутках, 60 - число минут в часах. Тогда число рабочих
электролизеров в серии составит, шт.:
(4) n раб = U действ. / (U cp - ∆U a . э.) = 803/ (4,221 - 0,036) = 191,876 округляем до 192 (Т.к.
это число округляется до ближайшего большего целого значения).
Фактическое число электролизеров в серии больше (с учетом числа
резервных).
Число резервных электролизеров в серии определяется
продолжительностью межремонтной эксплуатации (принимается 3 года) и
длительностью простоя на ремонте (принимается 18 суток). Тогда число резервных
электролизеров составит, шт.:
n рез =n раб ∙18/ (3∙365) = 192∙18/ (1095) =3.
Общее число устанавливаемых в серии электролизеров составит, шт.:
n общ =n раб + n рез = 192+3=195 округляем до 196 (т.к. чаще
всего электролизеры (число которых в серии достаточно велико) устанавливаются в
цехе в 2 ряда.
Тогда общее число электролизеров, полученное при расчете n o бщ , доводится до ближайшего большего четного числа.)
Годовая производительность серии определяется, т/год:
P= I∙8760∙0,335∙ η Т ∙ n раб ∙10 -8 = 155∙10 3 ∙8760∙0,335∙90∙192∙10 -8 =1228,13,
где I - сила тока серии, А (задано); 8760 -
число часов в году; 0,335 - электрохимический эквивалент, г/ (А∙ч); η Т - выход по току, %; n раб - число работающих электролизеров в
серии, шт.
Размеры анода определяются следующим образом. В электролизере
находится по одному само обжигающемуся аноду (с боковым (БТ) или с верхним (ВТ)
токоподводом). Площадь сечения анода, см 2 :
где I - сила тока, А (задано); d a - анодная плотность
тока, А/см 2 (определяется по графику на рис.1).
Зависимость анодной плотности тока от силы тока: 1 - для
электролизера ВТ; 2 - для электролизера OA
Из графика определяем d a = 0,792 А/см 2 ,
подставим:
S a =155∙10 3 /0,792= 195,707∙10 3
см 2 .
Зависимость анодной плотности тока для электролизера БТ имеет
такой ж вид, как и для других электролизеров, и занимает промежуточное
положение между кривыми 1 и 2.
Далее (для самообжигающегося анода) задаются его шириной (В а =
260-280см) и определяется длина анода, см:
L a =S a /B a =195,707∙10 3 /260=0,753∙10 3 .
Высота анода равна, см: H a =h к +hж, где h к - высота конуса
спекания, см (принимается 90-110см); h ж - уровень жидкой анодной массы, см (принимается
25 - 30см). Зададимся величинами, подставим в формулу:
Для электролизеров с обожженными анодами (OA) в ванне также находим:
один анод, но он представляет собой анодный массив из отдельных блоков шириной
b а =50-110см и длиной l а =135-145см. По известной величине S a (см. выше) количество
блоков в обожженном аноде, шт.:
n бл = S a / (b a ∙l a ) =196,707∙10 3 /
(50∙135) =28,99 округляем до 28, (т.к. число блоков в аноде четное.
Расстояние между блоками по продольной стороне электролизера
а (принимается 5 см), между рядами b (принимается 5 см). Тогда длина анода, см:
L a = (n бл ∙b а /2) +a [ (n бл /2) - 1] = (28∙50/2) +5∙ [ (28/2) -
1] =765.
Высота блоков (и всего анода) h a = 60см.
Внутренние размеры шахты электролизера (электролизной ванны)
определяются из найденных размеров (длины и ширины) анода и расстояния до
стенок бортовой футеровки.
Опытом эксплуатации электролизеров с самообжигающимися
анодами установлено, что оптимальное расстояние от продольной стороны анода до
боковой футеровки с должно составлять 50 - 6 5 см (для электролизеров с OA расстояние с = 30 см, а
от поперечной стороны анода до торцевой футеровки d = 50 - 65см (для
электролизеров всех типов).
Тогда внутренние размеры шахты составят
Ширина, см: В ш =В а + 2с=275+2∙30=335.
Длина, см: L ш =L a +2∙d=765+100=865.
где h ал - высота слоя алюминия, см (обычно 25 - 45см), h эл - высота слоя
электролита, см (обычно 15-20см) (уровень электролита h, n для электролизеров с OA 20-22 см, для других
15-18 см), h г - толщина корки застывшего электролита с глиноземом (обычно
5-10см).
Основные размеры подины (катодного устройства) определяются
найденными геометрическими размерами шахты ванны, а также стандартными
размерами выпускаемых отечественной промышленностью угольных блоков. Они имеют
высоту h б = 40см, ширину b б =55см и длину 1 б от 60 до 240 см.
Схема укладки блоков приведена на рис.2.
Рис. 2. Схема укладки подовых блоков
Подину собирают из блоков 3 разной длины, а между ними
набивают продольные и поперечные швы 4. Между бортовой футеровкой 1 и торцами
блоков 3 набивают периферийные швы 2. Такие же периферийные швы набивают и с
торцов. Толщина межблочных швов f, как правило, составляет 4 см, а периферийных 10-20см.
Исходя из этих соображений число блоков, необходимое для
создания подины, шт.:
n бл =2∙ L ш / (b б +f) =2∙865/ (55+4)
=29,32 округляем до 28,
Похожие работы на - Расчет процесса получения алюминия Курсовая работа (т). Другое.
Реферат: по краеведению на тему
Контрольная работа по теме Экономическая характеристика действующих свободных экономических зон на территории РФ
Отчет по практике по теме Производственно-организационная деятельность ООО 'КовровЛесПром'
Курсовая работа по теме Локальные вычислительные сети. Топология ЛВС
Курсовая Работа По Психологии Младшего Школьника
Курсовая работа: Образовательные возможности компьютерной сети
Реферат: Проектирование технического обслуживания дорожно-строительных машин и оборудования в полевых усл
Курсовая работа по теме Взаємозв’язок рівня емпатії та самоставлення особистості
Реферат: Русские праведники в произведениях Н.С.Лескова. Скачать бесплатно и без регистрации
Дипломная работа по теме Проектирование заземляющего устройства подстанции, входящей в состав Ленинградского предприятия магистральных электрических систем
Реферат по теме Обучение
Реферат: Фразеологический каламбур в современной публицистике
Контрольная работа: Ф’ючерсні контракти
Сочинение На Тему Любви Гранатовый Браслет
Реферат: Эффекты слоев в Photoshop 6. Скачать бесплатно и без регистрации
Контрольная Работа На Тему Банківські Ризики
Курсовая работа: Бюджетно-налоговая политика государства и ее функциональная роль
Курсовая Работа Цена Туито
Дошкольное образование в Китае
Сильная Личность И Общество Сочинение
Реферат: James Douglas Morrison Essay Research Paper The
Реферат: Фонетика элитарной культуры речи
Похожие работы на - Сейсморазведочные работы МОГТ-3D на Восточно-Мичаюской площади