Propelling Creativity with Tailored Injectable Approaches
In today's fast-paced manufacturing landscape, companies continually seek to improve their offerings and streamline manufacturing workflows. One proven strategy for achieving these objectives is through the utilization of tailored injection molding solutions. This innovative manufacturing method not only accelerates production but also allows for unparalleled flexibility in product design and material choices, catering to the specific needs of different industries.
By choosing custom injection molding, businesses can harness the capabilities of customized designs that match precisely with their requirements. This means that from the starting idea all the way to the final product, the injection molding process can be fine-tuned to meet specific requirements, ensuring high-quality results that stand out in a crowded marketplace. As a result, investing in custom injection molding becomes a critical factor of innovation, expanding the limits of what is possible in product development and production efficiency.
Understanding Tailored Molding Molding
Custom molding molding is a manufacturing technique that enables for the production of specific polymeric parts crafted to meet specific functional requirements. Utilizing this method, producers can create incredibly elaborate structures with exactness and consistency. The technique entails injecting molten plastic into a mold cavity, that cools and sets to create the intended part. This technique is especially helpful for creating items in high numbers, making it a popular method in sectors such as car manufacturing, healthcare, and retail goods.
One of the main pros of personalized injectable molding is the capability to fabricate detailed shapes that are challenging or not feasible to achieve with other manufacturing processes. The adaptability of substances used in molding, ranging from thermoplastic materials to thermosets, allows for a diverse range of uses. Manufacturers can choose specific substances based on the needed durability, flexibility, or thermal tolerance, ensuring that the end output fulfills both functional and aesthetic criteria.
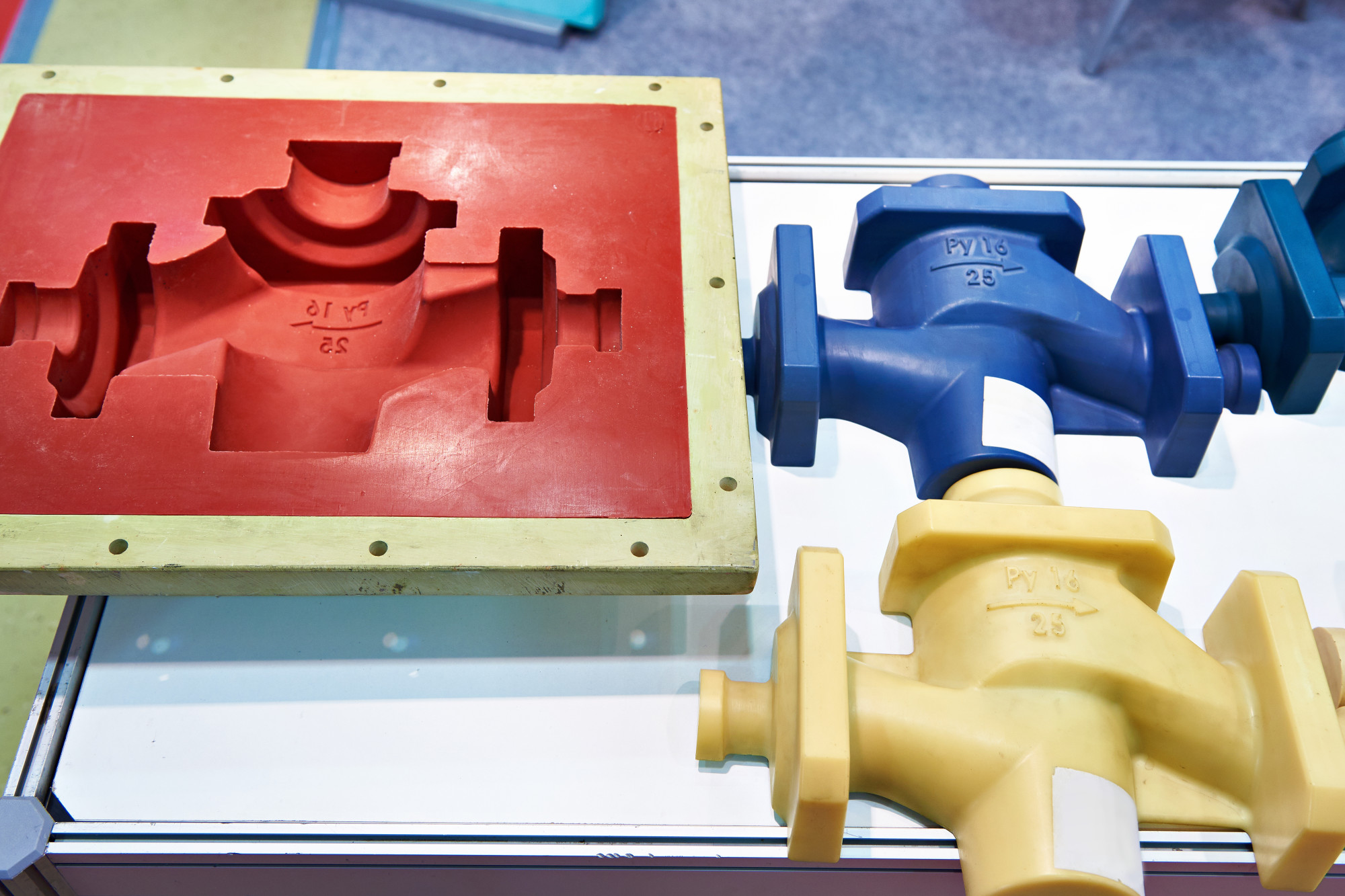
Moreover, personalized molding proves to be known for its productivity. After the design and form are set, the technique can manufacture a large quantity of parts in a reasonably brief duration. This efficiency not only decreases production time but also reduces expenditures per unit, making it an appealing choice for organizations seeking to innovate and simplify their operations. Utilizing leveraging tailored molding, companies can respond promptly to industry demands and foster creativity through personalized solutions.
Advantages of Customized Solutions
Custom injection molding gives manufacturers the ability to design parts that meet particular requirements, enhancing product functionality. By tailoring the materials and designs, companies can increase durability, weight, and functionality. This level of personalization ensures that products not only fit the specific application perfectly but also exceed user expectations in terms of durability and longevity.
Another significant plus lies in the opportunity for reduced costs. When products are designed with exactness using custom injection molding, there is frequently a reduction in material waste and production inefficiencies. This leads to decreased manufacturing costs over time, making it an economically viable option for businesses looking to improve their production processes. The ability to create complex shapes and intricate designs without excessive expenditure also cements the financial benefits of tailored solutions.
In conclusion, custom injection molding fosters innovation by enabling the development of unique products that stand out in the marketplace. Businesses can expand the boundaries of design, introducing new functionalities that competitors may not offer. This innovation can lead to a enhanced market presence and the ability to seize niche segments, ultimately driving business growth and customer loyalty through distinct products.
Uses and Examples
Tailored injection molding is extensively used across multiple industries, demonstrating its flexibility and efficiency. In the automotive sector, manufacturers utilize custom molds to create complex components including dashboards, bumpers, and cabin components. These components not only require precision but also need to meet strict safety and regulatory standards. By leveraging custom injection molding, companies can achieve high levels of detail and consistency, resulting in improved performance and reduced assembly time.
The healthcare industry also greatly benefits from custom injection molding. Medical devices and components, such as syringes, drug delivery systems, and medical instruments, require dependable and sterile manufacturing processes. Custom molds allow for the production of intricate shapes and designs, ensuring that the final products meet the specific needs of healthcare professionals while adhering to stringent regulations. This capability helps to foster innovation in medical technologies and improves patient outcomes.
In consumer electronics, custom injection molding is crucial for producing lightweight yet robust casings for devices like smartphones and tablets. The ability to create customized designs has enabled brands to distinguish their products in a extremely competitive market. Custom injection molds support rapid prototyping and production runs, allowing companies to bring new products to market quickly. This flexibility not only enhances product features but also promotes continuous development in consumer technology.