Производство карбомида. Дипломная (ВКР). Другое.
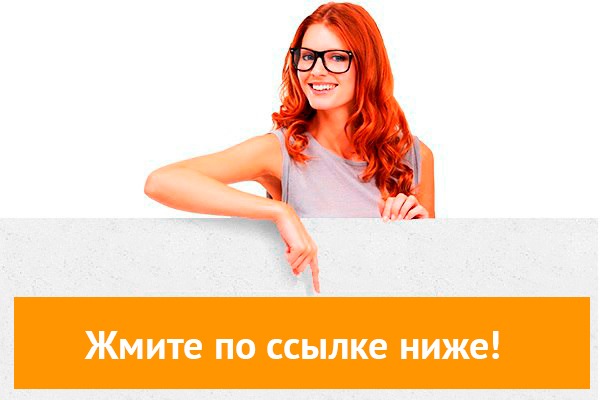
👉🏻👉🏻👉🏻 ВСЯ ИНФОРМАЦИЯ ДОСТУПНА ЗДЕСЬ ЖМИТЕ 👈🏻👈🏻👈🏻
Вы можете узнать стоимость помощи в написании студенческой работы.
Помощь в написании работы, которую точно примут!
Похожие работы на - Производство карбомида
Скачать Скачать документ
Информация о работе Информация о работе
Скачать Скачать документ
Информация о работе Информация о работе
Скачать Скачать документ
Информация о работе Информация о работе
Нужна качественная работа без плагиата?
Не нашел материал для своей работы?
Поможем написать качественную работу Без плагиата!
1.1 Выбор
метода производства. Существующие методы производства готового продукта и их
краткая характеристика
1.2 Основные физико-химические
свойства сырья, вспомогательных материалов, готовой продукции, Государственные
стандарты
.3 Теоретические основы процесса.
Выбор оптимальных условий
.3.1 Теоретические основы получения
готового продукта
.4 Описание технологической схемы
установки. Нормы технологического
режима
.5 Автоматизация производства.
Аналитический контроль
.7 Конструкции основного аппарата и
вспомогательного оборудования
.8 Охрана труда и промышленная
экология
2.1.1
Определяем часовую производительность установки
2.1.2 Теоретические расходные
коэффициенты
.1.3 Практические расходные
коэффициенты
.1.4 Материальный баланс выпарной
установки
2.1.5
Материальный баланс стадии кристаллизации
2.2 Тепловой баланс выпарки в
аппарате пленочного типа
карбамид мочевина
выпарной кристаллизация
Карбамид или мочевина СО(NH 2 ) 2
является конечным продуктом белкового обмена в организме человека,
млекопитающих, рыб, птиц, и некоторых пресмыкающихся. Она выделяется почками и
частично потовыми железами позвоночных.
Карбамид был открыт в XVIII столетии известными
химиками Бургаве, А. Мариграф и К. Шиле. Однако определить его состав им не
удалось.
Первый синтез карбамида был осуществлен в 1828
году немецким химиком Ф. Вёлером. Он показал, что при выпаривании раствора
циановокислого аммония (смеси сульфата аммония и цианита калия) последний
превращается в карбамид. Открытие Ф. Вёлера положило начало современной
органической химии. Основываясь на том, что карбамат аммония является продуктом
прямого взаимодействия аммиака и диоксида углерода, а карбамат аммония по
составу отличается от карбамида только одной молекулой воды, русский химик А.
И. Базаров пришел к выводу, что можно отщепить эту молекулу воды и получить карбамид.
В настоящее время карбамид производят в
промышленном масштабе из аммиака и диоксида углерода по методу А. И. Базарова.
Синтез карбамида, впервые осуществленный им в 1870 г., протекает в две стадии:
вначале образуется карбамат аммония, во второй стадии в результате отщепления
воды образуется карбамид. Данные реакции обратимы; равновесные концентрации и
скорости процессов определяются температурой, давлением, соотношением NH 3 ,
С0 2 и количеством Н 2 0 в смеси. Ускоряемые темпы
наращивания производственных мощностей по карбамиду в наиболее развитых странах
обусловлены необходимостью покрытия все возрастающих потребностей в
промышленности и сельском хозяйстве. Быстрый рост промышленного производства
создает предпосылки для его технического совершенствования,
а следовательно для улучшения технико-экономических
показателей,
повышения качества и удешевления стоимости продукта, что в свою очередь
обеспечивает благоприятные условия для расширения потребления карбамида.
Карбамид представляет собой концентрированное
азотное удобрение, содержащее азот в амидной форме. По сравнению с другими
твердыми удобрениями карбамид содержит 46,6 % азота, т.е. наибольшее количество
азота, что в основном и определяет экономическую целесообразность его
использования в середине ХХ века в качестве удобрения. Его можно применять
также для внекорневой прикормки растений, т. к. он в отличие от аммиачной
селитры не вызывает ожогов листьев.
Карбамид очень широко применяется также для
технических целей. Для приготовления продуктов ее конденсации с формальдегидом.
Карбамид нашел применение в фармацевтической промышленности для приготовления
успокаивающих и снотворных. Его используют при изготовлении дезинфицирующих
средств, в качестве смягчителя, в производстве косметических кремов. В нефтяной
промышленности оказалось возможным эффективно использовать карбамид для
разделения нефтепродуктов методом экстрактивной кристаллизации.
В настоящее время в промышленных масштабах
карбамид производят по следующим схемам: схемы с рециклом непрореагировавших
горячих газов NH 3
и С0 2 ; схемы с жидкостным рециклом NH 3
и С0 2 в виде масляной суcпензии
карбамата аммония; схемы с газовым рециклом разделяемых NH 3
и
СО 2 ; схемы с жидкостным рециклом NH 3
и С0 2 в виде водных растворов аммонийных солей; схемы с полным жидкостным
рециклом и с применением стриппинг-процесса.
В данном дипломном проекте выбрана схема
получения карбамида с полным жидкостным рециклом и с применением
стриппинг-процесса.
Всвязи с увеличением потребности в карбамиде как
в промышленности так и сельском хозяйстве считается
целесообразным строительство нового производства.
1.1 Выбор
метода производства. Существующие методы производства готового продукта и их
краткая характеристика
Физико-химические основы
производства карбамида по всем известным схемам в основном принципиально
сходны. Главное отличие современных схем друг от друга состоит по существу в
методах использования газов дистилляции - аммиака и двуокиси углерода -
непрореагировавших за один проход через колонну синтеза мочевины.
По методам использования
непрореагировавших NH 3
и СО 2 все современные схемы производства мочевины можно разделить на
следующие группы:
1 Разомкнутые - это схемы
однопроходные, т.е. без рециркуляции непревращенных в карбамид газов.
Полузамкнутые - схемы с
частичным рециклом.
Замкнутые - схемы с полным
рециклом.
Здесь в свою очередь можно
выделить:
а) схемы с прямым
рекомпримированием смеси непрореагировавших газов;
б) схемы с предварительным
разделением возвращаемых в процесс NH 3
и СО 2 ;
в) схемы с жидкостным рециклом NH 3
и СО 2 в виде карбамата аммония в масле;
г) схемы с жидкостным рециклом NH 3
и СО 2 в виде водных растворов аммонийных солей.
Основная особенность
однопроходных, или разомкнутых схем состоит в том, что непревращенные в
карбамид аммиак и двуокись углерода после их выделений из плава в процессе
дистилляции не возвращаются на повторное использование для получения мочевины,
а направляются в виде отхода производства на переработку в другие продукты.
Они просты по аппаратурному
оформлению и требуют наименьших капитальных затрат по сравнению со всеми
другими схемами.
Однако указанные преимущества
однопроходных схем справедливы лишь применительно к установкам сравнительно
небольшой мощности. Поэтому основным недостатком этого процесса является низкая
степень использования сырья (30-35% NH 3 ,
45-50% СО 2 ), что вызывает необходимость кооперирования с
производством по переработке аммиака в другие продукты. Двуокись углерода при
этом не утилизируется, т.к. потребность в бикарбонате аммония, в которой она
могла бы быть переработана, относительно невелика.
Основная особенность
полузамкнутых схем состоит в том, что NH 3
и СО 2 , не превращенные за один проход в карбамид, после их выделения
из плава в процессе дистилляции выводятся из цикла производства не полностью,
как в однопроходных схемах, а лишь частично. А другая часть возвращается в
колонну синтеза и, следовательно, остается в цикле производства.
Процессы с частичным рециклом
аммиака, основанные на возврате аммиака, были реализованы во многих странах и
дали возможность разработать более совершенные схемы с полным рециклом аммиака
и двуокиси углерода.
Сущность процесса с
рециркуляцией горячих газов (замкнутые схемы) состоит
в том, что NH 3
и СО 2 , непревращенные в карбамид, направляются после их выделения из
плава в колонне дистилляции непосредственно в газовый компрессор и возвращаются
в производственный цикл. Способ проверялся на опытной установке, но вследствие
высоких энергетических затрат промышленного распространения не получил.
Схемы с предварительным
разделением возвращаемых в цикл NH 3
и СО 2 , заключается в том, что их выделение из плава в процессе
дистилляции подвергаются разделению именно путем избирательной абсорбции одного
из компонентов, а только потом раздельно возвращаются в колонны синтеза. Но
сложность
процесса и громоздкость аппаратурного оформления схем являются недостатками.
Указанные недостатки схемы с предварительным разделением возвращаемых в цикл NH 3
и СО 2 находят свое отражение в технико-экономических показателях,
которые значительно уступают показателям более совершенных современных схем с
жидкостным рециклом NH 3
и СО 2 в виде водных растворов аммонийных солей. В основу схемы с
жидкостным рециклом NH 3
и СО 2 в виде карбамата аммония в масле положен метод, разработанный
французской фирмой "Пешине". По этому методу газы дистилляции,
содержащие NH 3
и СО 2 , обрабатываются легким парафиновым маслом. Исходным сырьем для
процесса служит жидкий аммиак и газообразная СО 2 , компримируемые до
давления 225 ат.
Достоинства этой схемы: высокая
степень конечного превращения NH 3
и СО 2 в карбамид, возможность в присутствии масла регулировать
температуру в колонне синтеза и сравнительная небольшая коррозия в аппаратуры.
Но применение значительных количеств масла в процессе синтеза карбамида по
схеме "Пешине" обусловливает высокие технико-экономические показатели
этой схемы, что делает ее мало перспективной по сравнению с другими, более
совершенными схемами.
Основной технологический
принцип схемы с жидкостным рециклом NH 3
и СО 2 в виде водных растворов аммонийных солей состоит в том, что не
превращенные в карбамид аммиак и двуокись углерода после их выделения из плава
в процессе двухступенчатой дистилляции адсорбируются водой и возвращается в
цикл в виде водно-аммиачных растворов аммиачных солей.
Впервые процесс производства
карбамида с рециркуляцией водного раствора углеаммонийных солей по способу
Миллера был осуществлен в 1932 г. концерном "Дюпон" (США). Этот
способ имел ряд существенных недостатков - низкий съем продукции с единицы
реакционного объема, интенсивная коррозия вследствие высоких температур и
давлений, большие расходы на эксплуатацию. Однако за последнее время в процессе
с рециклом водного раствора
углеаммонийных солей было внесено много усовершенствований, что позволило почти
полностью ликвидировать эти недостатки и, таким образом, обеспечить этому
способу ведущую роль в области промышленного производства карбамида во всем
мире. Процесс с рециркуляцией водных растворов аммонийных солей разработан
также и другими фирмами как, "Монтекатини" (новая схема),
"Тоё-коацу" и "Стамикарбон". Схемы основанные на этом
способе, различаются между собой технологическими параметрами (давлением,
температурой, соотношением СО 2 , NH 3
и
H 2 O
в исходной смеси) и конструктивными особенностями аппаратуры.
В последнее время очень широко
начал применяться процесс стриппинга, который заключается в том, что разложение
карбамата аммония в плаве после колонны синтеза ведут при давлении, близком к
давлению на стадии синтеза, продувкой плава сжатым диоксидом углерода или
сжатым газообразным аммиаком. В этих условиях карбамат аммония диссоциирует,
т.к. при продувке плава диоксидом углерода резко снижается порциальное давление
аммиака и нарушается равновесие процесса. Стриппинг - процесс позволяет:
упростить технологическую схему, использовать тепло образования карбамата,
снизить расходы энергии, сократить количество оборотной воды, поэтому является
более экономичным.
В азотной промышленности
стриппинг-процесс применяется в агрегатах большой единичной мощности-330 и 495
тыс. т/год карбамида.
В данном дипломном проекте
рассматривается именно эта схема, так как имеет ряд преимуществ: использование
тепла образования карбамата, более низкие расходные коэффициенты, меньшее
количество выбрасываемого в атмосферу диоксида углерода не связанного в
карбамид, возврат в процесс непрореагировавших NH 3
и СО 2 и отсутствие необходимости в их сжатие, что может вызвать
засорение и коррозию трубопровода. Также в данной схеме большое внимание
уделяется глубокой очистке газов,
выбрасываемых в атмосферу, от диоксида углерода и особенно от аммиака, а также
очистке воздуха, выходящего из грануляционной башни, от пыли и очистке сточных
вод до санитарных норм перед их сбросом. Все это значительно снижает
загрязнение окружающей среды.
Поэтому в дипломном проекте
разработана схема получения карбамида с полным жидкостным рециклом с
применением стриппинг-процесса (по схеме "Стамикарбон", стриппинг-газ
СО 2 ).
1.2 Основные физико-химические свойства сырья,
вспомогательных материалов, готовой продукции (характеристика и качество
согласно Государственных стандартов и технических условий )
Исходным сырьем для промышленного синтеза
карбамида служат жидкий аммиак и диоксид углерода.
В обычных условиях аммиак(NH 3 )
- бесцветный газ с резким удушливым запахом, молекулярный вес - 17, удельный
вес 0,77 г/л, в 1,7 раз легче воздуха, хорошо растворим в воде. Температура
кипения -33°С. Жидкий аммиак - бесцветная жидкость, сильно преломляющая свет,
удельный вес - 0,63 г/см 3 , молекулярный вес - 17.
В соответствии с ГОСТ 6221-90 он должен
удовлетворять следующим требованиям:
Массовая доля аммиака, % масс.………………………………… н/м
99,6
Массовая доля воды (остаток после испарения)
%,.. …….0,2-0,4
Массовая концентрация масла, мг/дм 3 ……………………….н/б
2
Массовая концентрация железа, мг/дм 3 ……………………...1,0-1,6
Давление,Мпа (кгс/см 2 )………………………….239-298
Температура, К (°С) ……………………………(-34;+25)
Современные методы промышленного получения
аммиака основаны на взаимодействии водорода и азота, протекающем при высоких
давлениях и температурах в присутствии катализатора:
Эта реакция является обратимой. Равновесная
концентрация аммиака зависит от
условий проведения процесса(температура, давление, соотношение Н 2 :N 2 ).
В ходе реакции, идущей с уменьшением обьема (из 3 обьемов Н 2 и 1
обьема N 2 образуются
2 обьема NH 3 ),выделяется
значительное количество тепла.
Диоксид углерода(С0 2 ) - бесцветный
газ со слегка кисловатым запахом и вкусом, молекулярный вес - 44, удельный вес
- 1,96 г/л, значительно тяжелее воздуха. С0 2 не горит и применяется
для пожаротушения. При 0°С и абсолютном давлении 35,54 атм. он сгущается в
бесцветную жидкость, не смешивается с водой, но растворяется в спирте, эфире и
маслах. При сильном охлаждении двуокись углерода застывает в белую
снегообразную массу. Диоксид углерода растворяется в воде, но определенного
гидрата не образует, кислотные свойства проявляются в его способности
непосредственно поглощаться растворами щелочей и образовывать в результате
взаимодействия с ними соли.
В соответствии с ГОСТ 8050-85 он должен
удовлетворять следующим требованиям:
Обьемная доля СО 2 ,%
об……………………………………………..99,5
Обьемная доля инертов, % об………………………………………..
0,5.
В азотной промышленности для многотонных
установок по производству карбамида применяется диоксид углерода, получаемый в
качестве отхода при очистке азотоводородной смеси, направляемый на синтез
аммиака.
Азот (N 2 )
по ГОСТ 9293-74 - бесцветный газ, без запаха и вкуса, молекулярный вес - 28, не
горит и не поддерживает горение, применяется как средство пожаротушения и как
вытесняющая инертная среда при продувке аппаратов и трубопроводов. Мало
растворим в воде. Азот оказывает удушающее воздействие на человека.
Карбамидоформальдегидная смола (КФС) - прозрачная
вязкая
жидкость. Плотность при 20 °С - 1,3 г/см 3 , температура замерзания -
40 °С,pH при 20 °С
равна 6,547. Массовая доля карбамида в КФС 22,5423 %, массовая доля
формальдегида 56,5457 %.
В таблице 1 приведены требования, предъявляемые
к вспомогательным материалам и полупродуктам.
Таблица 1 - Требования, предъявляемые к
вспомогательным материалам и полупродуктам.
Наименование
сырья, материалов, полупродуктов
Государственный
или отраслевой стандарт, СТП, технические условия, регламент
Показатели
по стандарту, обязательные для проверки
1
.Массовая доля карбамида 2.Массовая
доля формальдегида,%
1.Давление
на входе в цех, Мпа, кгс/см 2 2.Температура, К (°С)
0,35
- 0,5 (3,5 - 5) н/б 301 (н/б 28)
1.Давление
на выходе из цеха, Мпа, кгс/см 2
2.Температура, К (°С)
0,25
- 0,4 (2,5 - 4) 413-423 (140-150)
1
.Массовая концентрация солей жидкости, Nам.,
мг/дм 3 не более 2.Молярная концентрация солей жесткости, ммоль/дм 3
не более З.Рн 4.Массовая концентрация карбамида, мг/дм 3 5.
Массовая концентрация солей, мг/дм 3
Карбамид (мочевина,диамид угольной кислоты,
амидкарбаминовой кислоты) СО (NH 2 ) 2 ,
- белое кристаллическое вещество, содержащее 46,6% азота температура плавления
132,7°С, плотность 1335 кг/м 3 . Карбамид выпускают в гранулированном
или кристаллическом виде, хорошо растворим в воде и в жидком аммиаке. Так,
растворимость его в воде при 20°С равна 51,83 масс. %, а при 95°С - 87 масс. %.
Растворение карбамида в воде сопровождается поглощением тепла, а кристаллизация
из раствора - выделением тепла.Карбамид кристаллизуется в виде длинных
шелковисто-белых игл. Кристаллический карбамид обладает довольно высокой
гигроскопичностью, повышением температуры растворимость ее увеличивается и при
температуре плавления (132,6°С) становится практически неограниченной.
Значительно хуже растворяется карбамид в
спиртах. В эфире и бензоле он растворяется плохо, а в хлороформе и большей
части других органических растворителей он совсем не растворяется. Карбамид
обладает свойством повышать растворимость ряда веществ, поэтому его используют
в фармацевтической промышленности для приготовления инъекционных растворов.
Добавление карбамида к некоторым гидратированным солям вызывает их ожижение.
Карбамид хорошо растворяется в жидком аммиаке
при повышенных температурах растворимость его в жидком аммиаке несколько
меньше, чем в воде, при температуре более 30°С растворимость его превышает
растворимость в воде.
В растворах сильных кислот карбамид ведет себя
как слабое основание, а в растворах сильных оснований он ведет себя как слабая
кислота.Техническое наименование производимой продукции - карбамид (мочевина)
по ГОСТ 2081 - 92, карбамид - побочный продукт производства по ТУ
113-03-0203762-19-88 , карбамид кристаллический по ТУ 2181-059-00203766-99.
По физико-химическим показателям карбамид
(мочевина) должен соответствовать требованиям ГОСТ 2081-92, указанным в таблице
2.
Таблица 2 - Показатели ГОСТ 2081-92.
Массовая
доля азота в пересчете на сухое вещество, %, не менее
Массовая
доля свободного аммиака, %, не более для карбамида: кристаллического
гранулированного
Массовая
доля воды, %, не более: метод высушивания метод Фишера
Гранулометрический
состав, %: массовая доля гранул, размером, мм: от 1 до 4, не менее от 2 до 4,
не менее не менее 1, не более остаток на сите 6 мм, не более
Статическая
прочность, гранул кгс/гранулу, не менее
С каждым годом спрос на карбамид в мировом
сельском хозяйстве непрерывно возрастает. Это объясняется рядом достоинств,
которыми он обладает. Одним из основных требований к карбамиду, выпускаемому в
качестве азотного удобрения, является его дешевизна.
Стоимость единицы питательного вещества - азота
в карбамиде должна быть близка к стоимости единицы азота в других видах
удобрений.
Ценные свойства карбамида как удобрения были
обнаружены давно. Однако почти до 50-х годов прошлого столетия карбамид мог
лишь условно считаться удобрением, по существу же он даже не числился в
номенклатуре основных видов минеральных удобрений. Причиной этого была весьма
высокая стоимость продукта, обусловленная несовершенством методов его
получения. Благодаря серьезному техническому прогрессу, достигнутому в производстве
карбамида за последние годы, его стоимость по сравнению с довоенным уровнем
значительно снизилась. В настоящее время стоимость единицы азота в карбамиде
всего на 20% больше, чем в аммиачной селитре.
При оценке агрохимических свойств любого
азотного удобрения современная сельскохозяйственная наука предъявляет
требование, заключающееся в том, чтобы азот находился в такой форме, которая
легко усваивается растениями. Практически это определяется по скорости и
степени растворения азотного удобрения в воде. Карбамид удовлетворяет этому
требованию. Его рекомендуют применять для внесения в почву для удобрения ряда
овощных, плодовых и других культур.
Карбамид также нашел применение и в
животноводстве в качестве азотсодержащей (белковой) добавки к кормам для скота.
Так как рост и нормальная жизнедеятельность любого животного осуществляется за
счет питательных веществ, потребляемых с кормом. Для обеспечения
жизнедеятельности своего организма животные вынуждены восполнять
недостаток
белков в составе кормового рационапоеданием большого количества малобелкового
корма и переваривать избыточные количества других, менее важных питательных
веществ. Таким образом, применение неполноценных по белковому составу кормов
ведет к нерациональному их перерасходу (примерно на 30-50 %), к бесполезному
напряжению организма животного, к повышению стоимости продукции животноводства.
Многообразно применение карбамида в
промышленности. Наибольшее количество карбамида, применяемого для технических
целей, используется при приготовлении продуктов его конденсации с
формальдегидом. Состав и свойства получаемых карбамидных смол, характеризуются
большим разнообразием и зависят от условий синтеза. Путем рационального выбора
соответствующих условий и параметров процесса можно синтезировать различные
продукты, используемые в ряде отраслей промышленности. Особо широкое применение
карбамидные смолы нашли в промышленности пластических масс для изготовления
огромного ассортимента изделий, потребляемых в технике и быту.
Карбамид нашёл применение в фармацевтической
промышленности для приготовления успокаивающих, снотворных и мочегонных
средств, составов для заживления ран и др. Его используют при изготовлении
дезинфекционных средств, в качестве смягчителя в производстве косметических
кремов, он входит в состав некоторых зубных паст и т. п.
Таким образом, ускоренные темпы наращивания
производственных мощностей по карбамиду в наиболее развитых странах обусловлены
необходимостью покрытия все возрастающих потребностей промышленности и
сельского хозяйства. Быстрый рост промышленного производства создает
предпосылки для его технического совершенствования, а следовательно, для
улучшения технико-экономических показателей, повышения качества и удешевления
стоимости продукции, что в свою очередь обеспечивает благоприятные условия для
расширения потребления карбамида.
1.3 Теоретические основы процесса. Выбор
оптимальных условий
Синтез карбамида из аммиака и диоксида углерода
протекает в две стадии. Вначале в результате их взаимодействия образуется
карбамат
аммония:
2CO2
(газ) + NH3 (газ) = NH2COONH4
(ж) + 125, 6 кДж (2)
Во второй стадии в результате отщепления воды
образуется карбамид
2COONH4
(ж) = СО(NН 2 ) 2(ж)
+ Н 2 О (ж) - 15,5кДж (3)
Суммарная реакция синтеза карбамида имеет вид:
2 + 2NH3
= СО(NН 2 ) 2
+ Н 2 О + 110,1кДж (4)
Реакции (2) и (3) обратимы; равновесие реакции
сдвигается вправо вследствие избытка аммиака, вводимого с исходными
компонентами. Карбамат аммония, образующийся по реакции, представляет собой
кристаллическое вещество белого цвета, сильно пахнущее аммиаком сильно
гигроскопичное. Содержание в нем аммиака составляет - 43,6 %, содержание
двуокиси углерода - 56,4 %, содержание связанного азота - 35,87 %. Карбамат
аммония - соединение весьма нестойкое, диссоциирующее при атмосферном давление
на исходные компоненты, аммиак и диоксид углерода, давление паров которых
значительно даже при обычной температуре. Выделившееся тепло используется для
образования карбамида по реакции (3), протекающей с поглощением тепла.
Суммарный тепловой эффект реакции (2) и (3)
положительный. Равновесные концентрации и скорости процессов определяются
температурой, давлением, соотношением NH3
и CO2 и количеством H2O
в смеси.
При повышении температуры степень дегидратации
(конверсии) карбамата аммония в карбамид увеличивается (рисунок 1) .
Рисунок 1 - Зависимость степени конверсии
карбамата аммония от температуры.
Однако такое увеличение продолжается лишь до
определенного максимума, в дальнейшем степень превращения начинается снижаться.
Это объясняется довольно интенсивным увеличением давления диссоциации карбамата
аммония при повышении температуры:
Температура, о С . . . 60,4 . . 77,2 .
. 106,0 . . 130,2 . . 167,0 . . 197,6
Давление, ат . . . . . . 1,21 . . 2,99 . . 12,64
. . 38,4 . . . 113,4 . . 259,9
Образование карбамата аммония при атмосферном
давлении и обычной температуре идет довольно медленно. Ускорить этот процесс
только путем повышения температуры процесса не представляется возможным, т. к.
карбамат аммония - нестойкое соединение и легко разлагается на аммиак и диоксид
углерода. Так, при температуре 57 - 59°С давление паров аммиака и диоксида
углерода над карбаматом аммония равно атмосферному, а при 175°С оно составляет
17,5 МПа. Поэтому реакцию образования карбамата аммония необходимо вести при
повышенной температуре и давлении. С повышением давления при постоянных объеме
и загрузке степень конверсии карбамата
аммония в карбамид значительно вырастает (рис. 2).
Рисунок 2 - Влияние давления на степень
конверсии карбамата аммония в карбамид.
С увеличением избытка аммиака степень конверсии
карбамата аммония в карбамид также возрастает. Для
технологического процесса в нижней части колонны синтеза наиболее целесообразно
поддерживать температуру 183°С, давление 14,4 МПа, избыток аммиака 225% и
мольное соотношение NH 3
: С0 2 : Н 2 О = 4,5 : 1 : 0,5 [2, с38]. При этом степень
превращения диоксида углерода в карбамид составляет 57 %. В стриппере
поддерживается температура 160°С, в ректификационной
колонне поддерживается температура 130-140°С.
Рисунок 3 - Влияние избытка
аммиака на степень конверсии карбамата аммония в карбамид.
Выпаривание - процесс концентрирования растворов
твердых нелетучих веществ путем частичного испарения растворителя при кипении
жидкости, т. е. когда давление пара над раствором равно давлению в рабочем
объеме аппарата.
Выпаривание применяют для концентрирования
растворов нелетучих веществ, выделения из раствора чистого растворителя
(дистилляция) и кристаллизации растворенных веществ, т. е. выделения нелетучих
веществ, в твердом виде.
Выпаривание для концентрирования растворов
используют в производстве минеральных удобрений, сахара, белкововитаминных
концентратов, кормовых дрожжей, т. е. органических полупродуктов. Выпаривание
применяют также при концентрировании водных растворов щелочей (едкий калий и
едкий
натр),
солей (NaCl, NH 4 N0 3 ,
Na 2 S0 4 ),
для регенерации различных растворов с целью возврата их в технологический цикл,
термического обезвреживания промышленных стоков и т. п.
В качестве примера выпаривания с выделением
чистого растворителя из раствора можно привести опреснение морской воды, когда
образующийся водяной пар конденсируют и полученную воду используют для
различных целей.
Для получения нелетучих веществ в твердом виде
выпаренный раствор подвергают последующей кристаллизации, что значительно
облегчает хранение, транспортировку и переработку.
В технологических процессах химической
промышленности наиболее часто выпаривают водные растворы различных нелетучих
веществ.
Для нагревания выпариваемых растворов до кипения
используют топочные газы, электрообогрев и высокотемпературные теплоносители,
но наибольшее применение находит водяной пар, характеризующийся высокой
удельной теплотой конденсации и высоким коэффициентом теплоотдачи. Пap,
используемый для обогрева аппарата, называют первичным, а пар, образующийся при
кипении раствора, - вторичным.
Нагревание выпариваемого раствора в большинстве
аппаратов осуществляется путем передачи теплоты через стенку и только при
обогреве топочными газами - путем непосредственного соприкосновения с
нагреваемым раствором.
Выпаривание ведут под вакуумом, при атмосферном
и повышенном давлениях.
При выпаривании под вакуумом снижается
температура кипения раствора, что дает возможность использовать для обогрева
аппарата пар низкого давления. Этот способ применим при выпаривании растворов,
чувствительных к высокой температуре. Кроме того, уменьшаются
потери теплоты в окружающую среду и увеличивается полезная разность температур
греющего пара и кипящего раствора, что позволяет сократить поверхность
теплообмена и габариты аппарата. При выпаривании под атмосферным давлением,
образующийся вторичный пар обычно не используется и выбрасывается в атмосферу.
Выпаривание под повышенным давлением вызывает повышение температуры кипения
раствора и дает возможность использования вторичного пара для обогрева других
корпусов выпарной установки с меньшим
давлением. Кроме того, вторичный пар может быть использован для других
теплотехнических целей (экстра-пар).
Процесс выпаривания проводится в выпарных
аппаратах. При работе с небольшими количествами растворов при атмосферном
давлении, а часто и под вакуумом применяют одиночные выпарные аппараты,
называемые однокорпусными выпарными установками. В этом случае теплота греющего
пара используется однократно, а теплота вторичного пара обычно не используется.
Для экономии греющего пара применяют многокорпусные выпарные установки, которые
состоят из нескольких выпарных аппаратов, где вторичный пар, уходящий из любого
предыдущего корпуса, является греющим паром для последующего.
Еще недавно при производстве
мелкокристаллического карбамида на старых установках небольшой мощности
выпаривание растворов осуществлялось в периодически действующих вакуум-выпарных
аппаратах с выносными или встроенными греющими камерами. В таких аппаратах при
выпаривании под разрежением (остаточное давление 100-110 мм рт. ст.) и
температуре не бол
Похожие работы на - Производство карбомида Дипломная (ВКР). Другое.
Топик: Children and Toxicomania
Реферат по теме Торговые пассажи, теория и практика строительства
Реферат: Особенности Mac os
Контрольная работа: Банковские риски. Скачать бесплатно и без регистрации
Реферат по теме Понятие и особенности социально-психологического тренинга
Реферат по теме Армия в политической системе
Как Оформлять Реферат Список Литературы Ссылки
Учебное пособие: Методические указания к выполнению контрольной работы для студентов специальности 260704 (280300) "Технология текстильных изделий" заочной формы обучения Составитель
Курсовая работа по теме Игровые технологии в учебно-воспитательном процессе современной школы
Теория И Практика Написания Сочинения
Курсовая работа по теме Состояние системы риск-менеджмента в современных коммерческих банках
Контрольная работа: Прогнозирование развития фирмы: возможности и ограничения. Скачать бесплатно и без регистрации
Статья На Тему Эффективность Суда Присяжных В Рф
И Шишкин Осенний Лес Сочинение
Правила Соревнований По Волейболу Реферат
Налогообложение Физических Лиц Реферат
Сочинение Описание Помещения Комнаты Кухни
Признаки Монтажа Видеозаписей Курсовая Работа
Дипломная работа по теме Развитие коммуникационных способностей глухих и слабослышащих детей
Реферат: Терапия адинамических депрессий различного генеза. Скачать бесплатно и без регистрации
Реферат: Проектная деятельность как способ развития, воспитания и обучения учащихся английскому языку
Курсовая работа: Управленческий учет производственной деятельности
Доклад: Алексей I Комнин