Проектирование технологического процесса и оснастки для изготовления детали 'корпус водила нижнего'. Курсовая работа (т). Другое.
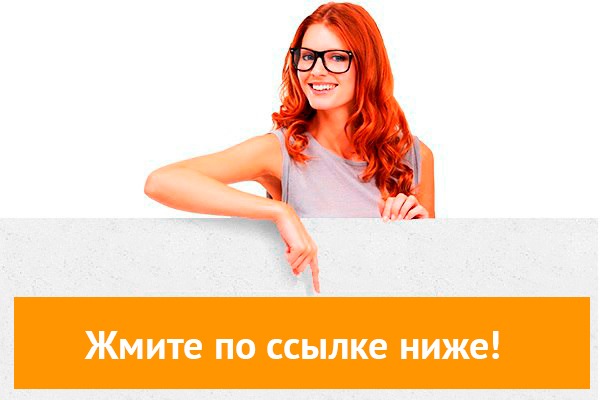
⚡ 👉🏻👉🏻👉🏻 ИНФОРМАЦИЯ ДОСТУПНА ЗДЕСЬ ЖМИТЕ 👈🏻👈🏻👈🏻
Вы можете узнать стоимость помощи в написании студенческой работы.
Помощь в написании работы, которую точно примут!
Похожие работы на - Проектирование технологического процесса и оснастки для изготовления детали 'корпус водила нижнего'
Скачать Скачать документ
Информация о работе Информация о работе
Скачать Скачать документ
Информация о работе Информация о работе
Скачать Скачать документ
Информация о работе Информация о работе
Скачать Скачать документ
Информация о работе Информация о работе
Скачать Скачать документ
Информация о работе Информация о работе
Скачать Скачать документ
Информация о работе Информация о работе
Скачать Скачать документ
Информация о работе Информация о работе
Нужна качественная работа без плагиата?
Не нашел материал для своей работы?
Поможем написать качественную работу Без плагиата!
Министерство
образования и науки Российской Федерации
Санкт-Петербургский
государственный политехнический университет
Пояснительная
записка к выпускной квалификационной работе
на присвоение
квалификации "бакалавр"
Проектирование
технологического процесса и оснастки для изготовления детали "корпус
водила нижнего"
Стр. 119, рис. 27, табл. 10, прилож. 3
Переход, рабочий ход, установка, операция, технология, степень свободы,
конструкторская база, тип производства, технологическая база, погрешность
базирования, опорная точка, технологическая размерная цепь, замыкающее звено,
припуск, допуск, режимы резания.
Представлен технологический процесс изготовления детали "корпус
водила нижнего"; разработаны маршрутные, операционные карты и карты
эскизов; рассчитан наладочный размер для одной из операций и припуск на
механическую обработку; назначены режимы резания; рассчитаны составляющие
штучно-калькуляционного времени.
Работа содержит в себе последовательное решение основных технологических
задач по подготовке к производству изделия на предприятии и проектированию новых
и совершенствования существующих технологических процессов изготовления и
ремонта изделий.
Проект содержит отработанный в соответствии с действующей
нормативно-технической документацией чертеж детали "корпус водила
нижнего". В проекте разработан маршрутный технологический процесс
изготовления детали и технологическая операция для фрезерования пазов, выбрано
оборудование и режущий инструмент для данной операции. Рассчитаны параметры
режима резания.
1.
Проектирование технологического процесса изготовления детали "корпус водила нижнего"
1.1 Исходные
данные для выполнения проекта
.3 Выбор типа
заготовки и способа ее получения
1.4 Назначение припусков на обработку
.6 Разработка технологического маршрута
изготовления детали
1.8
Проектирование технологических операций
2.
Проектирование приспособления для детали "корпус водила нижнего"
2.1
Техническое задание на проектирование приспособления
.2 Маршрутный
технологический процесс
2.3 Разработка заданной технологической
операции с назначением режима резания и расчётом действующих сил процесса
2.4 Разработка схем базирования и
закрепления заготовки. Расчёт погрешности базирования
2.5 Элементы
конструкции и расчет пневмодвигателя
2.10
Принципиальная схема пневмопривода
3.
Проектирование металлорежущих инструментов
.2 Проектирование комплекта метчиков
.3 Проектирование червячной фрезы для
цилиндрических зубчатых колес
Технология машиностроения - наука, занимающаяся изучением закономерностей
процессов изготовления машин, с целью использования этих закономерностей для
обеспечения выпуска машин заданного качества, в установленном производственной
программе количестве и при наименьших хозяйственных затратах.
Эффективностью производства, его технический прогресс, качество
выпускаемой продукции во многом зависят от опережающего развития производства
нового оборудования, машин, станков и аппаратов, от всемирного внедрения
методов технико-экономического анализа, обеспечивающего решение технических
вопросов и экономическую эффективность технологических и конструкторских
разработок.
В данной работе представлены основные этапы разработки технологических
процессов изготовления типовых деталей.
Цель курсового проекта заключается в приложении теоретических знаний,
полученных на лекциях, в решении практических задач, а также в знании структуры
и элементов технологического процесса, умения производить расчеты при решении
различных технологических задач, знание правил составления технологической
документации и правил оформления технологических эскизов и чертежей.
Для достижения поставленной цели были использованы знания, полученные на
лекциях и практических занятиях по одноимённой дисциплине.
.1 Исходные данные для выполнения проекта
Исходными данными для курсового проекта служат чертёж детали (приложение
3) и количество деталей в партии - 25000 шт.
На первом этапе проектирования тип производства ориентировочно может быть
определен в зависимости от массы детали и объема выпуска по таблице 1.1 [16, с.
182.]
Годовая программа выпуска деталей по типам производств
годовой объем выпуска деталей одного наименования, шт
Поскольку объем выпуска 25000 шт., а масса детали 1,97 кг, производство -
крупносерийное.
потребностью деталей на определенном промежутке времени и условием
быстрого их использования;
затраты на наладку должны быть минимальными.
Практически величину партии определяют из условия бесперебойной работы
сборочного подразделения. Бесперебойная работа обеспечивается определенным
запасом деталей на промежуточном складе. В зависимости от размеров детали запас
составляет: для крупных деталей - 2-3 дня, для мелких - 5-10 дней. На основании
этого рекомендуется упрощенно определять количество деталей в партии по формуле
[3]:
где П - количество деталей в партии; Q - годовой объем выпуска деталей
одного наименования вместе с запчастями; τ - нормативный срок хранения деталей
на складе 7 дней; Ф - число рабочих дней в году по обработке данной детали: 273
дня.
Крупносерийное производство характеризуется узкой номенклатурой и большим
объемом выпуска изделий, непрерывно изготавливаемых или ремонтируемых в течение
продолжительного времени.
Основные признаки крупносерийного производства:
Изделия изготавливают в большом количестве длительное время, конструкция
изделия меняется плавно. Рабочая сила низкой квалификации при наличии
настройщиков, оборудование автоматизированное, полная взаимозаменяемость при
сборке.
Массовому производству присуща поточная форма организации производства,
при которой операции обработки или сборки машины закреплены за определенным
оборудованием или рабочими местами, оборудование распложено в порядке
выполнения операций, а изготовляемая деталь передается с одной операции на
следующую сразу после выполнения предшествующей операции, как правило, с
помощью специальных транспортных устройств.
1.3 Выбор типа заготовки и способа ее получения
От выбора заготовок в значительной степени зависит характер
технологического процесса обработки заготовки и эксплуатационные свойства
детали. Чем в большей степени приближается форма заготовки к форме готовой
детали, тем меньше расходуется материала при обработке и тем меньше
затрачивается при этом средств и времени.
Материал детали - сталь конструкционная легированная хромистая 40Х ГОСТ
4543-71.
Рассмотрим два метода получения заготовки:
. Литьем в песчано-глинистые формы.
Расчет коэффициента использования материала и сравнение результатов для
различных вариантов получения заготовки [4]:
Коэффициент использования материала можно найти по формуле:
где - масса детали, - масса заготовки.
Допуски и размеры штампованной заготовки определим по ГОСТ 7505-89
(поковки стальные штампованные).
Материал - сталь 40Х (по ГОСТ 4543-71), масса детали - 1,97 кг.
Подставим в формулу (1.2) найденную массу поковки:
Так как сталь 40Х не льется, то заменяем ее на похожую по своим свойствам
литейную сталь - сталь Л50. Масса детали - 1,97 кг.
Подставим в формулу (1.2) найденную массу отливки:
Коэффициент использования материала достаточно высок и вполне
удовлетворяет требованиям серийного производства.
Коэффициент использования материала у штампованной заготовки больше.
Сравнение методов получения заготовки на основании расчета стоимости
заготовки с учетом ее черновой обработки
Расчет стоимости заготовки производится по формуле [15,стр.195]:
где - средняя часовая зарплата основных рабочих по тарифу,
руб./чел.-ч; - цена 1 кг отходов, руб.; - оптовая цена на материал в
зависимости от метода получения заготовки; - масса отходов материала, кг; Т -
время черновой обработки заготовки, ч; - цеховые накладные расходы.
) Расчет стоимости заготовки из литья.
= 3,8 кг; =27000 руб./т; = 1,83 кг; = 2980руб./т; = 250 руб./ чел.-ч; = 70%.[4. с. 32]
Расчет основного времени на черновую обработку литой заготовки,
включающего точение 7 поверхностей, сверление, фрезерование пазов, сверление
девяти отверстий, по формуле: [3. с. 172]:
По формуле (1.6) определим стоимость заготовки:
) Расчет стоимости штампованной заготовки.
= 2,87 кг; = 31500 руб./т; = 0,9 кг; = 2980 руб./т; = 250 руб./ чел.-ч; = 70%. [3. с. 32]
Расчет основного времени на черновую обработку штампованной заготовки,
включающего точение 7 поверхностей, зенкерование, фрезерование пазов, сверление
девяти отверстий, по формуле: [3,с.172]:
По формуле (1.6) определим стоимость заготовки:
После расчета коэффициента использования материала и стоимости заготовки,
полученные данные заносим в таблицу для сравнения.
Сравнение расчета коэффициента использования материала и стоимости
заготовки.
В результате сравнения видно, что коэффициент использования материала
выше и стоимость меньше у штампованной заготовки. Целесообразнее выбрать
штамповку.
.4 Назначение припусков на обработку
Так как заготовкой для изготовления детали является штампованная поковка,
то необходимо определить припуски на обработку. Припуски штампованной заготовки
регламентируются ГОСТ 7505-89.
Припуски необходимо назначить только на обрабатываемые поверхности. Те
поверхности, которые не подвергаются обработке, изготавливаются по номинальным
размерам детали.
В таблице.1.3 приведены значения припусков на обрабатываемые поверхности:
Припуск на механическую обработку, мм
Данная деталь относится к классу фланец, т.е. деталь, круглой формы с
равномерно расположенными отверстиями для болтов и шпилек, где L/D<2. Для
обеспечения требуемой твердости необходима закалка с низким отпуском, а также
необходимо химическое оксидирование поверхности.
Обработка поверхностей на токарных операциях окончательно недопустима,
т.к. необходимая точность не будет полностью обеспечена. Конструкция фланца
обеспечивает свободный подвод и отвод инструмента.
Выделим основные виды поверхностей (рис. 1.5):
,6,9, - наружные цилиндрические поверхности;
,10,14,15,17,18 - внутренние цилиндрические поверхности;
,5,8,11,13, - торцевые поверхности;
В зависимости от вида обрабатываемой поверхности могут использоваться:
для обработки наружных и внутренних цилиндрических, и торцовых
поверхностей - токарно-револьверные станки на этапах - черновом, получистовом,
чистовом;
круглошлифовальные станки на этапах повышенной, высокой и особо высокой
точности;
для обработки фигурных пазов - вертикально-фрезерный станок;
В зависимости от вида применяемого оборудования, установка детали может
производиться в трехкулачковом патроне, с упором в торец, цанговом патроне,
специализированные приспособления.
В качестве инструмента в серийном типе производства с небольшим объемом
выпуска, в основном, используется универсальный режущий инструмент. Однако на
определенных операциях возможно применение специализированного и специального
режущего инструмента.
Деталь - Фланец выполнен из низколегированной конструкционной хромистой
стали 40Х ГОСТ 4543-71 и проходит термическую обработку.
Изготавливается штамповкой, поэтому конфигурация наружного контура и
внутренних поверхностей не вызывает значительных трудностей при получении
заготовки.
Деталь достаточно технологична, допускается применение
высокопроизводительных методов обработки.
Технологические задачи изготовления детали
Исходя из чертежа (приложение 3) были выявлены следующие
) Точность размеров поверхностей: наружная цилиндрическая поверхность
ш60k6, внутренние цилиндрические поверхности ш116Н7, ш15Н7 и ш12Н7. Так же
габаритные размеры ш125h11и размер 63h11. Остальные
) Точность формы. Особые требования к точности формы поверхностей не
предъявляется, т.е. погрешность формы не должна превышать 1/3 поле допуска на
размер.
) Точность взаимного расположения задана допусками радиального биения в
пределах 0,02 мм.
) Качество поверхностного слоя. Шероховатость ответственных
цилиндрических поверхностей: для наружных Ra =1,25 мкм, внутренних Ra=3,2.
Определение класса детали и выбор типового технологического
Данная деталь относится к классу фланец, т.е. деталь, круглой формы с
равномерно расположенными отверстиями для болтов и шпилек.
Типовой маршрут для изготовления деталей класса фланец, включает в себя
следующие операции:[17]
Базирование по наружной поверхности к торцу в патроне - подрезка
свободного торца, зенкерование отверстия , точение наружных поверхностей (с
припуском под шлифование), растачивание канавок и фасок.
Базирование по отверстию и торцу в цанговом патроне - подрезка второго
торца, точение наружных поверхностей, растачивание внутренних поверхностей,
точение фасок.
Фрезерование фигурных пазов. Базирование по отверстию и торцу в цанговом
патроне
Фрезерование плоскостей. Базирование по отверстию и торцу в цанговом
патроне
Сверление, зенкерование, развертывание отверстий, нарезка резьбы.
Базирование по отверстию и торцу в цанговом патроне
Закалка, низкий отпуск, для получения заданной твердости.
Шлифование наружной поверхности после токарной обработки.
По аналогии с типовым маршрутом изготовления шкивов составим маршрут
обработки детали "корпус водила нижнего".
Для этого необходимо разработать теоретическую схему базирования и схему
установки заготовки на первой операции, используя чертежи заготовки и
соответствующей ей детали, выбрать черновые базы для первой операции
механической обработки.
За черновую базу на первой операции целесообразно выбрать самую развитую
поверхность детали, а именно поверхность 9 на рис. 5. Выбор данной черновой
технологической базы позволяет за один установ подготовить наибольшее
количество промежуточных баз для последующей обработки. Выбор данной черновой
базы также обусловлен тем, что она совпадает с конструкторской базой и связана
размером с необрабатываемой поверхностью. Первая операция по обработке данной
детали будет производиться на токарно-револьверном станке.
Закрепление заготовки будет производиться в трехкулачковом патроне, за
поверхность 9.
Рис. 1.6. Теоретическая схема базирования на операцию 015
Чистовую базу выбираем из соображений обеспечения устойчивости и
наименьших деформаций детали от сил зажима и усилий резания. Выбрав в качестве
чистовой технологической базы торец и отверстие, мы обеспечим выполнение
принципа постоянства баз, тем самым избавимся от погрешностей. Спроектируем
технологический маршрут так, чтобы максимально использовать, получаемую на
начальных операциях, технологическую базу.
Разработка технологических маршрутов изготовления точных поверхностей
детали
Наиболее точными поверхностями являются:
· три глухих отверстия диаметром Ш15Н7;
· три глухих отверстия диаметром Ш10Н7;
· три отверстия l=14 диаметром Ш12Н7.
· цилиндрическая поверхность Ш60k6
· цилиндрическая поверхность Ш116H7
Для получения заданных параметров точности необходимо назначить на
поверхности следующие операции:
Для цилиндрической поверхности Ш60k6:
Для цилиндрической поверхности Ш116H7:
Характеристика термической обработки
После заготовительной операции заготовку необходимо подвергнуть
термической обработке, а именно отжиг - вид термической обработки металлов и
сплавов, заключающийся в нагреве до определённой температуры, выдержке и
последующем, обычно медленном, охлаждении. Цели отжига - снижение твёрдости для
повышения обрабатываемости, улучшение структуры и достижение большей
однородности металла, снятие внутренних напряжений.
Для того чтобы получить необходимую твердость после механической
обработки необходимо включить термообработку, она включает в себя:
1. Закалка - нагрев до 830-8500 С и охлаждение в масле. При закалке вала
из стали 40Х с охлаждением в масле возникают меньшие остаточные напряжения, а
следовательно, и меньшая деформация. Структура стали после закалки - мартенсит;
твердость HRС не ниже 56.
. Отпуск - с нагревом до 550-5800С. Для предупреждения отпускной
хрупкости вал после отпуска следует охладить в масле. Структура стали после
отпуска - сорбит, твердость HRС не ниже 63.
Разработка дифференцированного маршрута изготовления детали
Для каждой поверхности назначается типовой план ее обработки, выбираются
экономически целесообразные методы и виды обработки при выполнении каждого
технологического перехода в соответствии с принятым оборудованием.
Назначаются основные этапы обработки основных поверхностей заданной
детали. Определяется необходимость введения отделочного этапа (шлифование,
развертывание, хонингование, притирка, полирование, суперфиниширование и т.д.)
Устанавливается необходимость специального этапа обработки детали (термическая
обработка, покрытие, ультразвуковой контроль, и т.д.).
На этапе черновой обработки необходимо снять дефектный слой с заготовки,
подготовив тем самым комплект промежуточных технологических баз для последующей
обработки детали. Этап включает в себя обработку торцевых поверхностей 1, 8,11
,13 цилиндрических поверхностей 3,6,9,17; фаски 20,21,22,23,24,25,обработку
плоскостей 12,19 и расточку отверстий 7,10,18. Данная операция выполняется на
токарно-револьверном станке, вертикально-фрезерном, вертикально сверлильном с
ЧПУ.
После этапа черновой обработки следуют этапы чистовой обработки детали,
которые включают в себя операции: токарно-револьверную,
вертикально-сверлильную.
Чистовая токарно-револьверная операция включает в себя обработку
цилиндрических поверхностей фасонным резцом 2,3,4,5,6; зенкерования отверстия
14; обработку цилиндрических поверхностей 9,24 .
Заключительным этапом чистовой обработки является вертикально-сверлильная
операция с ЧПУ, на которой получаются отверстия, предварительно обработанные на
предыдущих этапах отверстия 18,7,10, зенкерованием.
На этапе отделочной обработки протягиваем отверстия 7,10,18 на
Вертикально сверлильном станке с ЧПУ, предварительно обработанные.
Затем Шлифуем цилиндрическую поверхность 3 на кругло-шлифовальном станке.
Заключительным этапом отделочной работы является расточка внутренней
цилиндрической поверхности 17 на алмазно-расточном станке.
Рис 1.7. Схема дифференцированного маршрута изготовления детали
"корпус водила нижнего"
Для каждой поверхности назначается типовой план ее обработки, выбираются
экономически целесообразные методы и виды обработки при выполнении каждого
технологического перехода в соответствии с принятым оборудованием.
Окончательный технологический маршрут приведен в таблице 1.4.
Окончательный технологический маршрут
Полная запись содержания элемента технологической операции
Точить поверхности 2,3,4,5,6 начисто
Полная запись содержания элемента технологической операции
Для уточнения типа производства необходимо произвести расчёт коэффициента
закрепления операции (Кзо), [3. с. 20]:
Такт выпуска рассчитывается по формуле[3, стр. 21]:
где FД - фонд рабочего времени (примем 4015 часов) [3. с. 23]- количество
деталей в партии
при расчете FД учтем потери от нормального фонда 11 %,
Среднее штучное время по расчетам на операциях составляет:
крупносерийный, изменений в технологическом процессе не требуется
.8 Проектирование технологических операций
Нормирование технологических операций
Необходимо определить общий и операционные припуски и размеры на
обработку поверхности диаметром ш60k6 детали "Корпус водила нижнего"
расчетно-аналитическим методом. Заготовкой для детали является штамповка.
Технологический маршрут изготовления заданной поверхности детали и
технологическая оснастка
Трехкулачковый самоцентрирующий патрон
Трехкулачковый самоцентрирующий патрон
Технологический маршрут обработки поверхности ш60к6 :
Схема расположения операционных и общих припусков на размер
Рис. 1.9. Схема расположения операционных и общих припусков.
Принимаемый операционный размер, D, мм
Рис. 1.10. Схема пространственных отклонений.
Определение остаточных пространственных отклонений ρост для последующих переходов:
где ky- коэффициент уточнения формы
Определение расчетного размера заготовки на предыдущем технологическом
переходе
Определение общего максимального и минимального припусков
Заготовку подвергают термической обработке - отжигу, для обеспечения
равномерной структуры металла и снятия внутренних напряжений.
На данной операции необходимо лишить заготовку пяти степеней свободы.
Установочной технологической базой является самая развитая часть заготовки -
торец. Данная база лишает заготовку трех степеней свободы и совпадает с
конструкторской базой, что благоприятно влияет на точность механической
обработки. Трехкулачковый патрон лишает двух степеней свободы в радиальном
направлении.
Для выполнения данной операции был выбран токарно-револьверный станок
1Г325. Данный станок полностью удовлетворяет нас габаритами, ценой и его
мощности хватит для обработки данной детали.
Для выполнения операции необходимо использовать 6 резцов с материалом
режущей части Т15К6, фасонный резец Р18 и зенкер Р6М5 . Прямой проходной резец
используется для подрезки торцов, для обработки цилиндрических поверхностей.
Зенкер для обработки отверстия. Отогнутый проходной резец для снятия фасок.
Расточной резец используется для снятия фаски в отверстии. Твердый сплав Т15К6
режущей части резцов выбран исходя из того, что он обладает приемлемой
стойкостью. Контроль размеров осуществляется штангенциркулем, для
цилиндрических поверхностей , и калибром-пробкой для отверстия.
Согласно операционной карте, операция включает в себя 10 переходов.
Режимы резания выбраны из условий жесткости технологической системы, а именно:
глубина резания обеспечивает съем большей части припуска, подача выбрана
максимально возможная, ограниченная мощностью станка и параметром шероховатости
на обрабатываемые поверхности.
Основное времяτо рассчитано с учетом перебега и длины обрабатываемого
участка детали.
Суммарное основное время данной операции - τо=3,669 мин.
Вспомогательное время - τв=2,28 мин.
На данной операции необходимо лишить заготовку пяти степеней свободы.
Установочной технологической базой является торец. Трехкулачковый патрон лишает
двух степеней свободы в радиальном направлении.
Для выполнения данной операции был выбран токарно-револьверный станок
1Г325. Данный станок полностью удовлетворяет нас габаритами, ценой и его мощности
хватит для обработки данной детали.
Для выполнения операции необходимо использовать 8 резцов с материалом
режущей части Т15К6 для черновых поверхностей и Т5К10 для чистовых. Прямой
проходной резец используется для подрезки свободного торца, для обработки
цилиндрических поверхностей на чистовую и черновую обработки. Отогнутый
проходной резец для снятия фасок. Расточные резцы используется для расточки как
черновых так и чистовой поверхности. Твердый сплав Т15К6 режущей части резцов
выбран исходя из того, что он обладает приемлемой стойкостью. Контроль размеров
осуществляется штангенциркулем и калибр-скобой.
Согласно операционной карте, операция включает в себя 10 переходов.
Режимы резания выбраны из условий жесткости технологической системы, а именно: глубина
резания обеспечивает съем большей части припуска, подача выбрана максимально
возможная, ограниченная мощностью станка и параметром шероховатости на
обрабатываемые поверхности.
Основное времяτо рассчитано с учетом перебега и длины обрабатываемого
участка детали.
Суммарное основное время данной операции - τо=1,65 мин.
Вспомогательное время - τв=1,67 мин.
На операции 20 будем использовать схему базирования по торцу и
внутреннему диаметру.
В качестве установочной базы примем торец детали; ось отверстия будет
служить направляющей базой, лишающей заготовку еще двух степеней свободы.
Рис. 1.11. Схема базирования и закрепления заготовки
Из-за несовпадения конструкторской и технологической баз возникает
погрешность базирования. В этом случае погрешность базирования неизбежна,
необходимо построить размерную цепь.
Основными соотношениями, используемыми при расчете технологических
размерных цепей методом на максимум и минимум, являются [8]:
где nи p - соответственно числа увеличивающих и уменьшающих звеньев
размерной цепи, m- полное число звеньев.
В операции 20 возникает погрешность базирования, вызванная несовпадением
конструкторской и технологической баз. Проведем проверку, определим допуск на
наладочный размерАН:
Допуск получился отрицательным, значит необходимо произвести перерасчет
допусков составляющих звеньев. Замыкающим звеном размерной цепи является
конструкторский размер, определим допуски и предельные отклонения составляющих
звеньев размерной цепи по способу равных квалитетов точности из следующего
соотношения:
где a- коэффициент, определяющий точность, с которой следует получать все
составляющие звенья размерной цепи; единица допуска, характеризующая ту
часть допуска, которая изменяется с изменением размера.
полученное значение числа единиц допуска находится между квалитетами
точности IT6, IT7.
Выполним размер А2 по 7 квалитету точности (39-0,025), а допуск на
наладочный размер определим из формулы:
Искомый размер АН является уменьшающим, для определения отклонений
воспользуемся равенствами (1.15).
Окончательные данные: необходимо ужесточить размер 39h12до 39h7, а
наладочный размер для операции 20 принимается со следующими отклонениями АН = мм.
Снятие получившихся после обработки приливов.
Необходимо лишить заготовку 6ти степени свободы. Установочной базой
является торец. Цанговый патрон лишает двух степеней свободы в радиальном
направлении. Подводимая опора лишает вращения относительно оси.
Фрезерование пазов выполняется на вертикально фрезерном станке модели
6Н81Г. Инструмент для фрезерования - концевая фреза ш28. Материал фрезы -
быстрорежущая сталь Р6М5. Контроль полученных размеров осуществляется
калибр-скобой и штангенциркулем.
Суммарное основное время данной операции - τо=7,17 мин.
Вспомогательное время - τв=0,42 мин.
Пример расчета режимов резания для операции 30
) Инструмент: Фреза концевая(цельная) материал Р6М5;
) Глубина резания при фрезеровании t = 1,4 мм; [15, стр. 282].
) Подачу для фрезерования выбираем по таблице 35 [15].= 0,16 мм/об
) Период стойкости фрезы выбираем по таблице 40 [15]. T=90мин.
) Скорость резания определяем по формуле [15]:
где D = 28 мм - диаметр фрезы, B=22мм - ширина обработки,=3 - число
зубьев фрезы.
Коэффициенты Сv, q, x, y, u, p, m выбираются из таблицы 39 [15] .
Сv = 46,7; q = 0,45; x=0,5; y = 0,5; u=0,1; p=0,1; m = 0,33.
где - коэффициент, учитывающий влияние физико-механических
свойств обрабатываемого материала на скорость резания; таблица 1 [6]
= 1 - коэффициент, учитывающий влияние инструментального
материала на скорость резания; таблица 6[15]
коэффициент, учитывающий влияния состояния поверхности
заготовки на скорость резания; таблица 5 [15]
6) Определим частоту вращения шпинделя станка: [15]
Выбираем частоту вращения меньшую по паспорту станка= 600об/мин.
) Пересчитаем скорость резания: [15]
) Оперделим минутную подачу: [6]
) Определим силы резания: [15]
Коэффициенты Сp, x, y, u, q, w выбираются из таблицы 41 [15] .
Сp = 68,2; x=0,86; y = 0,72; u=1,0; q=0,86; w = 0.
Мощность резания определяется по формуле [15]:
Мощность двигателя станка 6Н81Г 4 кВт,
следовательно, станок обеспечивает необходимую мощность резания.
) Рассчитаем основное время : [3]
Штучно-калькуляционное время в серийном производстве определяется по
формуле:
Тшк = То + Тв + Торг + Ттех + Тотд + Тпз / n
Основное время для переходов было определено ранее в пункте 11.
Определим составляющие штучного времени:
где tуст - время на установку и снятие детали; tупр - время на управление
станком, связанное с переходом; tиз - время на контрольное измерение.
Определим по таблицам [5] составляющие вспомогательного времени:
Топер = То + Тв = 7,17+0,42 = 7,59 (мин)
Время организационного обслуживания:
Подготовительно - заключительное время, затраченное на партию
изготовленных изделий [13]:
Для фрезерных операций Тпз = 12 мин.
Тшк = 7,17 + 0,42 + 0,6 + 0,46 + 0,23 + 12/642 = 8,9 (мин)
Необходимо лишить заготовку 6ти степени свободы. Установочной базой
является торец. Цанговый патрон лишает двух степеней свободы в радиальном
направлении. Подводимая опора лишает вращения относительно оси.
Фрезерование пазов выполняется на вертикально фрезерном станке модели
6Н80Г. Инструмент для фрезерования - концевая фреза ш28. Материал фрезы -
быстрорежущая сталь Р6М5. Контроль по
Похожие работы на - Проектирование технологического процесса и оснастки для изготовления детали 'корпус водила нижнего' Курсовая работа (т). Другое.
Учебное пособие: Компьютерные технологии при изучении темы "Молекулярные перегруппировки"
Реферат На Тему Общественное Движение В России Xix Века
Сочинение По Музыке Лунная Соната
Реферат На Тему Конфлікт
Реферат: Конфликты 6
Реферат по теме Обследование зданий и сооружений
Реферат: Маллум, Феликс
Сочинение На Тему Почему Перемены Неизбежны
Иван Царевич На Сером Волке Сочинение Отзыв
Реферат На Тему Графическая Схема Черепа Человека
Ұлы Дала Бабалар Аманаты Эссе
Почему Я Люблю Свеклу Сочинение
Курсовая работа по теме Метод Монте-Карло и его применение
Диссертация Происхождение Слова
Доклад по теме Автомобильный рынок России
Афо Лиц Пожилого И Старческого Возраста Реферат
Реферат На Тему Структура Документа
Годовые Контрольные Работы По Математике
Дипломная работа по теме Структурная схема автогенератора
Гринев И Савельич Сочинение На 150 Слов
1999 г. ознаменовался количественным и качественным ростом вексельного рынка.
Реферат: A Mid Overlook Of Shakespeare Essay Research
Курсовая работа: Государственное управление и его принципы в ситуации социального и политического конфликта