Проектирование предприятий сборного железобетона. Дипломная (ВКР). Строительство.
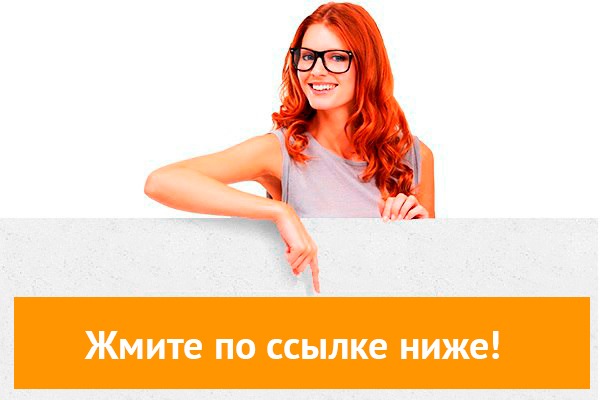
👉🏻👉🏻👉🏻 ВСЯ ИНФОРМАЦИЯ ДОСТУПНА ЗДЕСЬ ЖМИТЕ 👈🏻👈🏻👈🏻
Вы можете узнать стоимость помощи в написании студенческой работы.
Помощь в написании работы, которую точно примут!
Похожие работы на - Проектирование предприятий сборного железобетона
Скачать Скачать документ
Информация о работе Информация о работе
Скачать Скачать документ
Информация о работе Информация о работе
Скачать Скачать документ
Информация о работе Информация о работе
Скачать Скачать документ
Информация о работе Информация о работе
Скачать Скачать документ
Информация о работе Информация о работе
Скачать Скачать документ
Информация о работе Информация о работе
Скачать Скачать документ
Информация о работе Информация о работе
Нужна качественная работа без плагиата?
Не нашел материал для своей работы?
Поможем написать качественную работу Без плагиата!
1. ПРОЕКТИРОВАНИЕ СТРОИТЕЛЬСТВА,
РЕКОНСТРУКЦИЯ ИЛИ МОДЕРНИЗАЦИЯ ПРЕДПРИЯТИЯ
.1 Обоснование реконструкции
бетоносмесительного цеха
Предприятие ОАО “Гомельжелезобетон” планирует
произвести реконструкцию бетоносмесительного цеха. Принимая во внимание этот аспект
потребуется реконструкция существующего отделения приготовления химических
добавок, замена существующих дозаторов и бетоносмесителей, модернизирование
системы транспортирования бетонной смеси. Модернизация существующей системы
позволит обеспечить: стабильное водоцементное отношение на уровне требуемом для
работы формовочного оборудования, более точное дозирование и перемешивание
компонентов бетонной смеси, учет расхода компонентов и выхода готовой смеси и
многое другое. А также для получения бетона с определенными свойствами
понадобится организация отделения по приготовлению эффективных химических
добавок.
Реконструкцию следует производить путем
внедрения на предприятии систем автоматического управления дозированием сырья и
приготовления бетонной смеси, что позволяет увеличить точность подготовки
компонентов смеси, за счет чего повышается качество выпускаемой продукции,
уменьшается влияние "человеческого фактора" и повышается
производительность оборудования.
1.2 Характеристика проектируемого
предприятия
Абсолютная минимальная температура -35°С;
Абсолютная максимальная температура +35°С;
Средняя максимальная температура наиболее
жаркого месяца +24°С;
Период со среднесуточной температурой воздуха
8°С - 137 суток (средняя температура - 1,3°С);
Период со среднесуточной температурой воздуха
10°С - 212 суток (средняя температура - 0,8°С).
Средняя температура наружного воздуха:
Среднемесячная относительная влажность воздуха в
%:
Повторяемость направления ветра приведена на
листе №1
1.3 Условно-расчетная номенклатура и
объем производства
Таблица 1.1 - Условно-расчетная номенклатура и
объем производства
Способ
производства, технология, оборудование
1)Плиты
пустотного настила длиной до 6,3 м, шириной 1,5 м 2)Плиты ребристые покрытий
длиной 6,0 м, шириной 1,5 м 3)Плиты дорожные длиной до 6,0 м, шириной 2,0 м
Два
агрегатно-поточных поста с конвейером распалубки и подготовки форм
(полуконвейерный способ производства). Тепловая обработка - в ямных
пропарочных камерах
1)Плиты
пустотного настила длиной до 7,2м, шириной 1,5 м 2)Плиты пустотного настила
длиной до 7,2м, шириной 1,2 м
1)Панели
наружных однослойных стен промышленных зданий 2)Перегородки железобетонные.
3)Панели ограждений. 4)Плиты перекрытия каналов.
5)Фундаменты
и фундаментные стаканы и балки 6)Лотки 7)Утяжелители 8)Балки перекрытия,
покрытия и прогоны 9) Опоры освещения 10) Плиты ребристые длиной 6м, шириной
1,5м
Агрегатно-поточный
пост. Тепловая обработка - в ямных пропарочных камерах.
1)Трехслойные
наружные стеновые панели 2)Двух- и однослойные наружные стеновые панели
3)Плиты перекрытия каналов 4)Фундаменты и фундаментные плиты 5)Дорожные плиты
6)Сваи 7)Диафрагмы жесткости 8)Панели ограждения 9)Панели стеновые
резервуаров 10)Внутренние стеновые панели 11)Колонны
Конвейерная
9-постовая линия с подпольными щелевыми камерами тепловой обработки.
Стендовая технология
Обозначение
серии и выпуска рабочих чертежей
Производство
элементов нулевого цикла:
Длина
0,9-2,4 Ширина 0,3-0,6 Высота 0,3-0,6
Для
устройства фундаментов, стен подвалов и технических подполий, а также для
опирания наружных и внутренних стен в зданиях различного назначения
Для
свайных фундаментов зданий и сооружений
Длина
до 3 Ширина 0,6-3,2 Высота 0,3-0,5
Для
устройства фундаментов, стен подвалов и технических подполий, а также для
опирания наружных и внутренних стен в зданиях различного назначения
Серия
1.020-1/83, ГОСТ 24022-80,по чертежам КЖИ)
Для
устройства фундаментов под колонны
Производство
элементов несущего каркаса зданий:
Плиты
перекрытия многопустотные ПК, предварительно напряженные и с ненапряженной
стальной арматурой для зданий и сооружений
Серия
Б1.041.1-1.2000 Серия 1.041.1-3 серияБ1.202.1-7в.5-1,88Р10.12-1.2 КЖИ
разработки ОКУП Институт «Гомельгражданпроект»
Длина
2,4-6,3 Ширина 1,5 Высота 0,22
Для
перекрытия жилых, общественных производственных зданий, эксплуатируемых в
условиях неагрессивной и среднеагрессивной степени воздействия газовой среды
Плиты
перекрытия многопустотные предварительно напряженные, армированные стальными
канатами 2 ПТМ с применением безопалубочной технологии формования на
оборудовании итальянской фирмы «Weiler Italia»
Длина
2,4-9,0 Ширина 1,5-12 Высота0,22
Для
перекрытия жилых, общественных производственных зданий, эксплуатируемых в
условиях неагрессивной и среднеагрессивной степени воздействия газовой среды
Железобетонные
плиты покрытий сельскохозяйственных производственных зданий 2ПГ 6-5
Для
покрытия сельскохозяйственных промышленных зданий, эксплуатируемых в условиях
неагрессивной, слабоагрессивной и среднеагрессивной степени воздействия
газовой среды
Колонны
прямоугольные для сельскохозяйственных и промышленных зданий
Серия
1.423.1-3/88 Серия 3.015.-1694 в.1 Серия 1.020-1/83 Серия 1.832.1-2
Длина
до 9 Ширина 0,3-0,4 Толщина 0,3-0,4
Предназначены
для каркасов одно - и многоэтажных зданий и сооружений различного назначения
Длина
до 6 Высота до 0,4 Ширина до 0,4
Для
использования в сборномонолитных перекрытиях зданий различного назначения
Производство
элементов ограждающих конструкций:
Наружные
техслойные стеновые панели на гибких связях с эффективным утеплением, ПСТ
Длина
0,28-7,18 Высота 0,585-1,785 Ширина 0,3
Для
наружных стен общественных , производственных и вспомогательных зданий и
сооружений промышленного и сельскохозяйственного назначения, эксплуатируемых
в условиях неагрессивной, слабоагрессивной и среднеагрессивной степени
воздействия газовой среды
Панели
стеновые ПС наружные однослойные (керамзитобетонные)
Длина
1,5-6,6 Высота 0,885-1,785 Ширина 0,25-0,3
Длина
до 6 Высота до 1,5 Ширина 0,25
Длина
до 6 Высота до 1,8 Ширина 0,08
КЖИ
разработки ОКУП Институт «Гражданпроект»
Длина
до 7,2 Ширина 0,16 Высота 2,56
Предназначены
для применения в жилых и общественных зданиях с неагрессивной,
слабоагрессивной и среднеагрессивной степени воздействия газовых сред
Экраны
ограждения балконов и лоджий
Дина
до 6,2 Высота до 1 Ширина 1,41
Ограждение
балконов и лоджий жилых и общественных зданий
Длина
до 7,2 Ширина 0,16 Высота 2,56
Разделение
балконов и лоджий жилых и общественных зданий
Длина
до 7,2 Ширина 0,16 Высота 2,56
Предназначены
для применения в жилых и общественных зданиях с неагрессивной,
слабоагрессивной и среднеагрессивной степени воздействия газовых сред
Длина
2,98 Высота 2,4-6 Ширина 0,14-0,35
Длина
3,58 Высота 2,8; 2,55 Ширина 0,12;0,16
Для
ограждений территорий предприятий и организаций, строительных площадок,
земляных участков
Для
фиксации в проектном положении и обеспечения устойчивости панелей ограждения
Плиты
дорожные напряженные ПДН АТ800
Предназначены
для устройства сборных покрытий постоянных и временных автомобильных дорог
Предназначены
для строительства подземных каналов под трубопроводы различного назначения
Длина
до 3 Ширина до 2,8 Высота до 0,18
Длина
0,76;1 Высота 0,9;0,7 Ширина 1,3;0,3
Для
балластировки трубопроводов диаметром от 159 до 1420 мм, проходящих через
болота, обводненные участки и поймы рек
Элементы
лестниц 1ЛМ 27-12-14 Лестничная площадка
Серия
1.152.1-3 в.1 Серия 1.151.1-6 в.1
Для
устройства внутренних и наружных лестниц в отапливаемых и не отапливаемых
зданиях
Стойки
для опор линий электрообеспечения СВ 100.10 АТ 500с
Стойки
используются в качестве опор наружного освещения с кабельной подводкой
питания, оборудованных консольными или подвесными светильниками.
Кольца
железобетонные КС-10-9-м КС -15-9-м
Для
устройства колодцев канализационных, водопроводных и газонапорных сетей.
Ограждения
под контейнерные установки
КЖИ
разработки ОКУП Институт «Гражданпроект»
Длина
2,98 Высота 2,4-6 Ширина 0,14-0,35
Ограждающая
конструкция контейнерных установок для сбора бытовых отходов
Длина
1 Ширина 0,3;0,2 Высота 0,15;0,08
Для
отделения проезжей части от тротуаров, газонов, площадок, а также ограждения
пешеходных дорожек и тротуаров от газонов
Длина
0,21 Высота 0,105 Ширина 0,08
Предназначены
для устройства покрытий тротуаров ,пешеходных и садово-парковых дорожек.
Арматурные
каркасы, арматурные сетки
Длиной
до 6 Ширина до 2,5 Шаг 100*100 мм 100*200 мм 200*200 мм 200*300 мм
Гнутые
арматурные элементы различной конфигурации
Производство
бетонных и растворных смесей
Класс
бетона от с8/10 до с 32/40,осадка конуса 1-4 см, 5-9 см, с применением
химических добавок по водонепроницаемости и морозостойкости, что повышает
долговечность и прочность
Для
производства железобетонных изделий, а также для продажи предприятиям и
населению
Все основные материалы необходимые для
производства продукции поставляются с заводов изготовителей Республики
Беларусь.
Таблица 1.2 - Сырьевая база и транспорт
РУПП
«Гранит», Брестская обл., г.п. Микашевичи
Песок
строительный кварцевый Мк 1,5-2,0
КУП
УПТК Гомельского исполнительного комитета
Портландцемент
ПЦ-500 Д0, ПЦ-500 Д20
ПРУП
«Белорусский цементный завод», ПРУП «Гродненский цементно-шиферный завод»,
ПРУП «Кричевский цементно-шиферный завод»
Арматура
Ø3 - Ø40, классов
S500, S240, S400, S800
склады - цемента, заполнителей, готовой
продукции, арматуры;
основные цеха - бетоносмесительный, арматурный,
формовочный;
вспомогательные узлы - компрессорная,
мастерские;
Принимаем следующий режим работы предприятия:
5-ти дневная рабочая неделя и 6-ти дневная рабочая неделя каждую восьмую
неделю.
Согласно принятому режиму работы: номинальная
количество рабочих суток в год - 260; количество рабочих смен в сутки 2;
длительность рабочего дня 16 часов.
1.7 Проектирование технологии
производства
Принимаем бетоносмесительный цех циклического
действия - одноступенчатый; по схеме расположения смесительных машин в плане -
гнездовой; по способу управления - механизированный.
где Q - производительность предприятия, м3;П.СМ
- коэффициент, учитывающий потери бетонной смеси;
tр - расчетное число рабочих суток в году;см -
число рабочих смен в сутки;см - длительность рабочей смены, ч;з - нормативное
число замесов в час;
Кч.н. - коэффициент часовой неравномерности
выдачи бетонной смеси.
Принимаем KП.СМ=0,67 и Кч.н.=0,8, nз=35, tр=253
дней [2], Nсм=2, tсм=8 ч.
где VЗ - общий объем одного замеса, м3;см -
число смесителей;
bб - коэффициент выхода бетонной смеси, bб=0,67;
Принимаем 2 бетоносмесителя типа
СБ-35 [3, c. 168].
Дозаторы принимаем циклического
действия.
Принимаем для расчета дозаторов и
складов заполнителя и цемента, максимальный расход цемента 400 кг/м3.
Расход песка максимальный для
тяжелого бетона 0,45 м3/м3;
Расход щебня максимальный 0,9 м3/м3.
Определяем расход компонентов на 1
замес.
Коэффициент выхода бетона Кс=0,8 м3;
Плотность песка и щебня 1500 кг/м3.
Принимаем дозатор цемента АВДЦ-425; дозатор
песка и щебня 6АВДЧ-1200; дозатор воды АВДЖ-425.
Вместимость складов заполнителей и цемента
определяем по формуле
СКЛ=nсм∙Vсм∙bб
nз∙Qсм ∙tсм ∙Nсм ∙зс, м3 (1.3)
где nсм - число смесителей;см - объем смесителя;
bб - коэффициент выхода бетонной смеси;см -
расход материала на 1 м3 бетона, м3;
зс - запас заполнителей или цемента на заводских
складах, расчетные рабочие сутки.
Для цемента Qсм=400 кг/м3=0,4 м3/м3;
Для песка Qсм=675 кг/м3=0,45 м3/м3;
Для щебня Qсм = 1350 кг/м3=0,9 м3/м3;
зс =10 суток.скл.цем=2×0,5×0,67×35×0,4×8×2×10=1500,8
м3.
С учетом коэффициента заполнения емкостей 0,9
Vскл.цем=1668 м3=1668 т.
Принимаем 6 силосных банок емкостью 285 т
каждая.скл.песка=2×0,5×0,67×35×0,45×8×2×7=1182
м3.
С учетом коэффициента заполнения: Vскл.песка=1313
м3.скл.щебня=2×0,5×0,67×35×0,9×8×2×10/0,9=3752
м3.
Из вагонов цемент в силоса выгружается
разгрузчиком всасывающе-нагнетательным ТА26 с производительностью 20 т/ч. В
бетоносмесительный цех цемент подается пневматическим камерным насосом ТА23
производительностью 30 т/ч.
Для щебня и песка принимаем прирельсовый
силосный склад с шифром 708-18-85 вместимостью 6000 м3.
Заполнители подаются в расходные бункера БСЦ
ленточным конвейером ТК-3 с шириной ленты 650 мм и производительностью
горизонтального 90 т/ч, наклонного под углом 18º - 45 т/ч.
Число отсеков расходных бункеров принимаем
равным по ОНТП-7-80 для: цемента -2, для песка - 2, для щебня - 4.
Объем отсеков расходных бункеров для
заполнителей и цемента определяется по формуле:
отс=2∙Vсм ∙bб
∙nз ∙зч ∙Qсм/nотс, м3 (1.4)
где Vсм - объем смесителя по загрузке, м3;
bб - коэффициент выхода бетонной смеси;з -
нормативное число замесов в час;
зч - запас материалов в расходных бункерах, ч;см
- расход материала на 1 м3 бетона, м3;отс - число отсеков.
Для цемента запас - 3 ч, для заполнителей - 2 ч.
отс=2×0,5×0,67×35×2×0,45/2=10,55
м3.
Транспортируется бетонная смесь из БСЦ в
формовочный цех по бетоновозной эстакаде, оборудованной тремя тележками.
Механизмами дозировочного управления отделения и
бетоносмесительного отделения управляет оператор с центрального пульта,
дозирование осуществляется автоматическими циферблатными дозаторами. Они
работают в паре с вторичными приборами, установленными в помещении оператора.
Управление выпускными затворами дозаторов и бетоносмесителей осуществляется
пневмоприводами с электромагнитными клапанами. Всеми производственными
процессами управляет оператор из центрального пульта, в котором кроме пульта
управления размещен щит технологической световой сигнализации.
Исходные
данные. Таблица 1.3 - Потребность в бетонной смеси
Таблица 1.4 - Пооперационная продолжительность
подачи бетонной смеси (замеры операций производились по факту)
Выгрузка
б/с: 1,2 пролет, пост колец, вибропресс 3,4 пролет
Расчет I смены (самая загруженная).
Цикл производства товарных смесей составляет 180
сек (3 мин), следовательно часовая производительность второй секции, работающей
на улицу составляет (60/3)х1=20 м3 при замесе 1 м3, но т.к. бетоносмеситель
второй секции позволяет производить замесы V=1,25 м3, производительность второй
секции составит (60/3)х1,25=25 м3 , что в полной мере обеспечит часовую
потребность в товарных смесях.
Цикл подачи бетонной смеси на I пролет
составляет, примерно 370 сек.
Для обеспечения часовой потребности I пролета
понадобится (3,3/1,6)х370=764 сек (13 мин).
Цикл подачи бетонной смеси на II пролет
составляет, примерно 440 сек.
Для обеспечения часовой потребности II пролета
понадобится (6,2/1,6)х440=1705 сек (28,5 мин).
Цикл подачи бетонной смеси на III пролет
составляет, примерно 660 сек для самоходных бункеров с бетоном V= 1,5 м3 (1,5
м3 - средний объем заказа бетонной смеси при замесе за два раза), и 510 сек для
самоходных бункеров с бетоном V=0,7 м3 (0,7 м3 - средний объем заказа при
замесе за один раз). (потребность: 70% V=1,5 м3, 30% V=0,7 м3).
Для обеспечения часовой потребности III пролета
(кроме вибропресса) понадобится (1,9х0,7/1,5)х660=585 сек (10 мин)
Цикл подачи бетонной смеси на пост формования
колец составляет, примерно 582 сек. Для обеспечения часовой потребности поста
формования колец понадобится (1,3/1,6)х582=473 сек (8 мин). Цикл подачи
бетонной смеси на IV пост колец составляет, примерно 793 сек для самоходных
бункеров с бетоном V=1,5 м3, и 620 сек для самоходных бункеров с бетоном V=0,7
м3. (потребность: 40% V=1,5 м3, 60% V=0,7 м3)..
Для обеспечения часовой потребности IV пролета
понадобится:
ж/б (1,1х0,4/1,5)х793=233 сек (4 мин);
ж/б (1,1х0,6/0,7)х620=585 сек (10 мин);
к/б (0,2х0,4/1,5)х793=43 сек (0,7 мин);
к/б (0,2х0,6/0,7)х620=106 сек (1,7 мин);
Следовательно, общее время составляет
13+28,5+17+8+14+2,5=83 мин, с учетом поправочного коэффициента 83х1,1=92 мин
(при работе одной продольной тележкой).
БСЦ может отправлять тележку загруженную 1,6 м3
б/с примерно каждые 320 сек. Средний срок оборачиваемости одной тележки
составляет 580 сек, следовательно БСЦ способно загрузить две бетоновозные
телеги на 90% во времени.
Таким образом, при равномерной загрузке
бетоновозных тележек общее время требуемое для обеспечения формовочного цеха
бетонной смесью для стабильной работы в течении часа составит:
/2=46 мин. (коэффициент запаса более 20%).
Цикл подачи бетонной смеси на участок
вибропрессования составляет, примерно 320 сек.
Для обеспечения часовой потребности поста
вибропресса понадобится (0,6/0,8)х320=240 сек (4 мин), с учетом поправочного
коэффициента время увеличивается до 5 мин.
Кроме того, 1-й смеситель может отдавать
цементный раствор на все посты существенно не увеличивая свою загрузку и
уменьшая загрузку 2-й секции.
Цикл подачи бетонной смеси на I пролет
составляет, примерно 370 сек.
Для обеспечения часовой потребности I пролета
понадобится (3,3/1,6)х370=764 сек (13 мин).
Цикл подачи бетонной смеси на II пролет
составляет, примерно 440 сек.
Для обеспечения часовой потребности II пролета
понадобится (6,2/1,6)х440=1705 сек (28,5 мин).
Цикл подачи бетонной смеси на III пролет
составляет, примерно 660 сек для тележек с бетоном V=1,5 м3, и 510 сек для
тележек с бетоном V=0,7 м3. (потребность в телегах: 70% V=1,5 м3, 30% V=0,7
м3).
Для обеспечения часовой потребности III пролета
(кроме вибропресса) понадобится (1,9х0,7/1,5)х660=585 сек (10 мин)
Цикл подачи бетонной смеси на IV пост формования
колец составляет, примерно 793 сек для тележек с бетоном V=1,5 м3, и 620 сек
для тележек с бетоном V=0,7 м3. (потребность в тележках: 40% V=1,5 м3, 60%
V=0,7 м3)..
Для обеспечения часовой потребности IV пролета
понадобится:
ж/б (1,1х0,4/1,5)х793=233 сек (4 мин);
ж/б (1,1х0,6/0,7)х620=585 сек (10 мин);
к/б (0,2х0,4/1,5)х793=43 сек (0,7 мин);
к/б (0,2х0,6/0,7)х620=106 сек (1,7 мин);
Следовательно, общее время составляет
13+28,5+17+14+2,5=75 мин, с учетом поправочного коэффициента 75х1,1=83 мин
(работа одной продольной тележки).
/2=42 мин (работа двумя продольными тележками)
Цикл подачи бетонной смеси на участок
вибропрессования составляет, примерно 320 сек.
Для обеспечения часовой потребности поста
вибропресса понадобится (0,6/0,8)х320=240 сек (4 мин), с учетом поправочного
коэффициента время увеличивается до 5 мин.
Цикл подачи бетонной смеси на I пролет
составляет, примерно 370 сек.
Для обеспечения часовой потребности I пролета
понадобится (3,3/1,6)х370=764 сек (13 мин).
Цикл подачи бетонной смеси на II пролет
составляет, примерно 440 сек. Для обеспечения часовой потребности II пролета
понадобится (2,5/1,6)х440=688 сек (12 мин). Цикл подачи бетонной смеси на III
пролет составляет, примерно 660 сек для тележек с бетоном V=1,5 м3, и 510 сек
для тележек с бетоном V=0,7 м3. (потребность в тележках: 70% V=1,5 м3, 30%
V=0,7 м3). Для обеспечения часовой потребности III пролета (кроме вибропресса)
понадобится (1,9х0,7/1,5)х660=585 сек (10 мин)
Цикл подачи бетонной смеси на IV пост формования
колец составляет, примерно 793 сек для телег с бетоном V=1,5 м3, и 620 сек для
телег с бетоном V=0,7 м3. (потребность в телегах: 40% V=1,5 м3, 60% V=0,7 м3)..
Для обеспечения часовой потребности IV пролета
понадобится:
ж/б (1,1х0,4/1,5)х793=233 сек (4 мин);
ж/б (1,1х0,6/0,7)х620=585 сек (10 мин);
к/б (0,2х0,4/1,5)х793=43 сек (0,7 мин);
к/б (0,2х0,6/0,7)х620=106 сек (1,7 мин);
Следовательно, общее время составляет
13+12+17+14+2,5=58,5 мин, с учетом поправочного коэффициента 58,5х1,1=65 мин
(работа одной продольной тележкой).
/2=33 мин (работа двумя продольными тележками).
Как видно из представленного расчета, мощности
оборудования бетоносмесительного цеха должно быть достаточно для полного
обеспечения предприятия бетонной смесью с учетом увеличения мощностей. В
случае, если фактическая ситуация не будет соответствовать полученным данным,
необходимо пересмотреть загрузку смесителей бетоносмесительного цеха. Так, для
бесперебойной подачи бетонной смеси на II пролет формовочного цеха можно
использовать смеситель №1, загрузка которого составит примерно 50%, при этом
2-я секция БСЦ полностью сможет обеспечивать потребность в бетонной смеси
остальных постов. Бетонную смесь на участок вибропрессования возможно также
подавать смесителем №1, несущественно увеличивая его загрузку, либо одним из
смесителей 2-й секции.
Основные положения технологии арматурного цеха
Для армирования железобетонных конструкций
применяется горячекатаная круглая сталь гладкая и периодического профиля
классов S240, S400, соответствующая требованиям ГОСТ 5781-82. В качестве
напрягаемой арматуры применяется стержневая горячекатаная сталь периодического
профиля S800 по ГОСТ 10884-94.
Стержни класса S240 диаметром до 12 мм, класса
S400 диаметром до 10 мм включительно изготавливаются в мотках или стержнях, а
больших диаметров - в стержнях. Стержни изготавливаются длиной от 6 до 12 м
(при согласовании с производителем возможно изготовление стержней большей
длины). Для правки арматуры, поступающей в мотках, принимаем правильно-отрезные
установки, которые одновременно производят очистку стали. Принимаем
правильно-отрезной станок СМЖ-357, имеющий следующие характеристики:
диаметр арматуры гладкой 4-10 мм, периодического
профиля 6-8 мм;
скорость подачи и правки арматуры 31 м/мин;
мощность электродвигателя 12,6 кВт.
А также правильно-отрезной станок И-6118:
диаметр гладкой арматуры 2,5 - 6,3 мм;
скорость подачи и правки арматуры 25 м/мин; *
Для резки арматурной стали, поставляемой в
прутках, принимаем станок СМЖ-1725, имеющий следующие характеристики:
наибольший диаметр арматуры класса S240 - 40 мм;
S400-25мм;
Для гибки стержневой арматуры принимаем станок
СМЖ-173А;
максимальный диаметр изгибаемого прутка из стали
класса S240 - 40 мм, S400 - 32мм;
Для резки коротких стержней принимаем станок
АРС-М:
диаметр отрезаемых стержней 3-55 мм;
длина отрезаемых стержней, наименьшая - 50 мм,
наибольшая - 1000 мм;
габаритные размеры 1160x1040x665 мм.
Для сварки сеток и каркасов прижимаем
крестообразный тип сварных соединений, выполняемых контактной точечной сваркой.
Этот способ позволяет механизировать и автоматизировать процесс изготовления
плоских сварных изделий. Для сварки сеток принимаем одноточечную сварочную
машину МТ-2102:
наибольший диаметр свариваемой арматуры 22x22
мм;
Для монтажных сварочных операций при сборке
элементов каркасов для дуговой электрической сварки принимаем сварочный аппарат
переменного тока:
Для изготовления объемных арматурных каркасов
принимаем установку СМЖ-56:
положение сборки каркасов - вертикальное;
число одновременно собираемых каркасов -1;
максимальные размеры каркасов 7200x3600x300 мм,
диаметры свариваемой арматуры от 5×5 до
12×16
мм;
габаритные размеры установки 8400x3180x4600 мм.
Для изготовления закладных деталей тавровыми
соединениями под флюсом принимаем сварочный автомат АДФ-2001 [10, с.62];
диаметр привариваемых анкерных стержней 8-40 мм;
Для высадки головок стержней напрягаемой
арматуры принимаем установку СМЖ-128Ам:
наибольший диаметр арматуры класса S800 - 25 мм;
число стержней на которых одновременно
производится высадка - 1;
максимальная длина стержней - 14000 мм;
производительность - 80 стержней/ч.
Число установок для высадки арматурных стержней
определим по формуле:
где Q - годовая производительность
завода, шт.;ст - приведенное количество стержней в изделии, шт;у -
производительность установки по высадке, шт/ч.
Для плит перекрытия предварительно
напряженных Nст=8 шт;
Для плит покрытия предварительно
напряженных Nст=2 шт;
Основные положения технологии
формовочного цеха
Бетонные и железобетонные изделия на
предприятии ОАО «Гомельжелезобетон» выпускаются по конвейерной,
полуконвейерной, агрегатно-поточной и стендовой технологиям. Основным
технологическим оборудованием являются бетоноукладчики, виброплощадки,
конвейера, тележки для вывоза готовых изделий, самоходные бетоновозные бункера.
На каждом пролёте работают по два мостовых крана, а полигон обслуживается
козловым. Для ускорения твердения принимаем ямные и щелевые пропарочные камеры
в зависимости от технологии.
В качестве формы для плит покрытия
принимаем разборную стальную форму на 1 изделие, для наружных стеновых панелей
- форму-вагонетку. Формы должны быть изготовлены в соответствии с ГОСТ 25781 и
ГОСТ 18104; точность размеров форм должна быть на класс выше точности размеров
изготавливаемых в них изделий, внутренние размеры собранной формы должны
находиться в пределах минусовых допусков размеров изделий.
Для чистки рабочих поверхностей форм
и отсеков кассет и стендов применяют пневмоскребок и металлическую щетку. Для
смазки используют смазку на основе пасты ОПЛ-СМ и эмульсол. Смазку наносят
щеткой.
В начале производят армирование форм
и отсеков кассет и стендов, затем подаётся бетонная смесь.
Бетонная смесь от бетоносмесителя в
формовочный цех транспортируется по бетоновозной эстакаде и выгружается в
промежуточный или непосредственно в бункер бетоноукладчика или. Бетонирование
изделий производят при помощи бетоноукладчика или бадьи (в зависимости от
технологии). Для уплотнения бетонной смеси принимаются виброустановки и
глубинные вибраторы.
Для бетона с маркой М250 на портландцементе
с отпускной прочностью 85% (плиты покрытия) принимаем следующий режим твердения
в ямной пропарочной камере:
Для керамзитобетона наружных стеновых
панелей твердеющих в щелевой камере:
Температура изотермической выдержки
80 ºС. После ТВО
изделия подвергаются распалубке. После освобождения изделия от действия
формообразующего приспособления, оно стропится и при помощи крана
устанавливается на пост отделки и мелкого ремонта, а форма или кассета снова
снова готова к началу цикла.
На посту доводки изделие
осматривается, производится очистка закладных деталей и доводка поверхности
изделия до требуемой категории. Затем изделие стропится и перемещается на
тележку вывоза готовой продукции, где производится контроль качества
изготовления. Там же производится приёмка изделий ОТК.
Для вывоза изделий используется
телега СМЖ-151. Продолжительность выдерживания готовых изделий в цехе при
температуре наружного воздуха ниже 0°С составляет 12 ч.
Определение количества основного и
вспомогательного оборудования
Число камер ТВО определяется по
формуле:
где Nи - число одновременно
твердеющих изделий в камере;
Коб - оборачиваемость камер
Коб=Тк/tпр,
Тк - продолжительность работы камер
за сутки, ч;пр - длительность полного цикла тепловлажностной обработки, включая
затраты времени на загрузку и выгрузку изделий, ч.
Выбираем камеру с одним изделием в
плане и семью по высоте.
Продолжительность работы камер за
сутки 24 ч.
Время на загрузку одной камеры 7∙0,204=1,43
ч.
Разгрузка камеры осуществляется за
1,43 ч
Коб=24/15,86=1,51и=7 шт.к=4582/(7∙1,51∙255)=1,7
шт.
Коб.ф=2∙8/16,064=0,996ф=1,05∙4582/(0,996∙255)=18,9.
Для фундаментов под трёхшарнирные рамы:
Выбираем камеру с одной формой в плане и двумя
формами по высоте.
Габаритные размеры формы 5,3×1,68×1,82.
Время на загрузку одной камеры 2·0,5/2+0,15=0,65
ч.
Коб=24/13,95=1,72и=4
изделияк=2400/(4·1,72·255)=1,4
Коб.ф=2∙8/14,2=1,13ф=1,05∙2400/(1,13∙255)=8,8.
Число ведущих агрегатов определяется по формуле:
где Q - годовая производительность,
шт.;- максимальная продолжительность ритма работы линии, мин;
τр - расчетное число рабочих
суток в году;и - число одновременно формуемых изделий;см - длительность рабочей
смены, ч;см - число рабочих смен в сутки.
Для производства железобетонных
ребристых плит покрытия принят полуконвейерный способ производства.
Согласно табл.14 [2] максимальный
ритм работы составляет 15 мин.
Для производства железобетонных
фундаментов под трёхшарнирные рамы принят агрегатно-поточный способ
производства.
Согласно табл.14 [2] максимальный
ритм работы составляет 20 мин.
Для производства двухслойных наружных стеновых
панелей для сельхоз зданий принят конвейерный способ производства.
Согласно табл.15 [2] максимальный ритм работы
составляет 12 мин.
Для производства трёхшарнирных рам
принят кассетный способ производства.
Число кассетных установок
определяется по формуле:
где nотс - число отсеков в кассетной
установке (принимаем равным 10);цк - продолжительность технологического цикла
изготовления изделия, ч;
Определение необходимой
производственной площа
Похожие работы на - Проектирование предприятий сборного железобетона Дипломная (ВКР). Строительство.
Реферат по теме Экономическая эффективность инвестиций, направленных на расширение парка ПС АТП
Курсовая Работа На Тему Теории Памяти
Путешествия Расширяют Кругозор Сочинение
Курсовая работа: Предметная область информационной безопасности
Курсовая работа: Анализ правовых основ и содержания общего прокурорского надзора Российской Федерации
Реферат по теме Электромагнитные волны
Реферат Министерства Российской Федерации
Курсовая работа по теме Теория детского коллектива в трудах А.С. Макаренко
Контрольная работа: Обучение и воспитание детей с фонетико-фонематическим недоразвитием
Реферат: The Black Cat Literary Criticism Essay
Дипломная работа: Исследование правового статуса защитника в уголовном судопроизводстве
Реферат: Стратегия предприятий зрелых отраслей на примере ОАО "Саратовстройстекло". Скачать бесплатно и без регистрации
Курсовая работа: Физическое воспитание детей дошкольного возраста
Физика 9 Класс Лабораторные Работы 6
Реферат: Expository Essay On Lord Of The Flies
Реферат: English Outline Essay Research Paper I The
Реферат На Тему Контекстуальные Аспекты В Исследовании И Изучении Конфликтологической Культуры Специалиста
Контрольная работа по теме Проблема формирования личности
Роль Социализации В Становлении Личности Эссе
Методология сравнительного правоведения: общая характеристика.
Похожие работы на - Д.Рикардо о факторах, определяющих стоимость товара
Реферат: The Characterization Of Macbeth In Relation To
Доклад: Информационно - деятельностная структура знания и информационный подход