Проект цеха по производству древесностружечных плит. Курсовая работа (т). Другое.
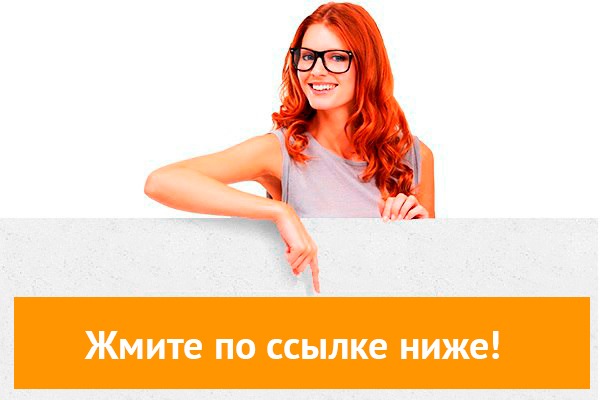
🛑 👉🏻👉🏻👉🏻 ИНФОРМАЦИЯ ДОСТУПНА ЗДЕСЬ ЖМИТЕ 👈🏻👈🏻👈🏻
Вы можете узнать стоимость помощи в написании студенческой работы.
Помощь в написании работы, которую точно примут!
Похожие работы на - Проект цеха по производству древесностружечных плит
Скачать Скачать документ
Информация о работе Информация о работе
Скачать Скачать документ
Информация о работе Информация о работе
Скачать Скачать документ
Информация о работе Информация о работе
Скачать Скачать документ
Информация о работе Информация о работе
Скачать Скачать документ
Информация о работе Информация о работе
Скачать Скачать документ
Информация о работе Информация о работе
Скачать Скачать документ
Информация о работе Информация о работе
Нужна качественная работа без плагиата?
Не нашел материал для своей работы?
Поможем написать качественную работу Без плагиата!
ПРОЕКТ ЦЕХА ПО ПРОИЗВОДСТВУ
ДРЕВЕСНОСТРУЖЕЧНЫХ ПЛИТ
Выбор
принципиальной схемы производства ДСтП
. Выбор
исходных технологических данных для проектирования
.
Пооперационный расчёт перерабатываемого материала в производстве
древесностружечных плит
. Разработка
технологической схемы производства ДСтП, подбор и расчёт количества основного
технологического оборудования
. Описание
технологического процесса производства трехслойных ДСтП
Древесностружечные плиты (ДСтП) применяются в мебельной промышленности,
строительстве, а также в других отраслях народного хозяйства. Они имеют ряд
преимуществ перед другими древесными материалами. Для их получения используются
низкокачественная древесина и отходы деревообрабатывающих производств. В
условиях переменной влажности размеры плит меняются незначительно. Возможно
получать плиты с одинаковыми и различными свойствами вдоль и поперек пласти
(анизотропные и изотропные), с повышенной огнестойкостью и устойчивостью к
действию дереворазрушающих грибов и насекомых-вредителей, пониженными
показателями водо- и влагопоглощения. Процесс производства плит характеризуется
высокой экономичностью и почти полной автоматизацией.
Развитию производства ДСтП способствует высокая эффективность их
применения.
Производство ДСтП, организованное первоначально лишь для использования
отходов деревообработки, превратилось в самостоятельную отрасль промышленности.
Исследования
возможности использования древесных отходов для изготовления плит проводились
еще в конце XIX в.. Промышленное производство таких плит началось и
развивалось по мере повышения дефицитности деловой древесины. Однако основной
рост промышленности по производству плит из древесных частиц относится к
пятидесятым годам, когда было создано специализированное оборудование и
улучшена технология, обеспечившая хорошее качество плит. В 1950 г. мировое
производство плит составляло 20 тыс. , а в
дальнейшем росло исключительно быстрыми темпами и к началу 80-х годов превысило
4 млн. плит.
В
СССР научно-исследовательские работы в области производства ДСтП начались в
1952 г., а первый экспериментальный цех был пущен в 1955 г. Отрасль быстро
развивалась и уже значительно обогнала по объему производства некоторые отрасли
деревообрабатывающей промышленности, выпускающие традиционные плитные материалы
(столярные и полутвердые древесноволокнистые плиты и др.).
Для
этого производится реконструкция действующих предприятий, направленная на
увеличение объема производства и повышение качества продукции при условиях
снижения ее материалоёмкости и комплексного использования сырья. Одновременно
осуществляется строительство и освоение мощности новых предприятий.
В
дальнейшем производство ДСтП будет развиваться еще быстрее на основе
рационального и комплексного использования сырья. Это позволит в большей
степени, чем в настоящее время, удовлетворять потребность в плитах различных
отраслей народного хозяйства. В настоящее время основная масса выпускаемых ДСтП
используется в производстве мебели; в то время как в ряде стран Западной Европы
использование плит в строительстве составляет значительную часть в общем,
объеме их потребления.
1.
Выбор
исходных технологических данных для проектирования
до 10 мг формальдегида на 100 г абсолютно сухой плиты
Для производства мебели, в строительстве, машиностроении,
радиоприборостроении и в производстве тары.
Физико-механические показатели выпускаемой плиты марки П-Б
Разбухание не более,% при повышенной водостойкости
Предел прочности при изгибе, МПа, для плиты толщиной 16 мм
Предел прочности при растяжении перпендикулярно пласти
плит, МПа,
Состав сырья по виду,% технологическая щепа
Средневзвешенная
условная плотность древесного сырья , (кг/м 3 ),
определяется по формуле:
где
-средневзвешенная условная плотность одной породы,
кг/м 3 ;
r др , r к , r гн - соответственно условная плотность здоровой
древесины, коры, гнили (r гн = 0,65 r др );
Р др ,
Р к , Р гн - соответственно доля здоровой древесины
(r др = 100-Р к -Р гн ),
коры, гнили в общем объеме сырья,%.
Средневзвешенная
плотность древесного сырья при определенной влажности , (кг/м 3 ), определяется по формуле:
гдеr w др , r w к , r w гн - соответственно условная плотность
здоровой древесины, коры, гнили (r гн = 0,65 r w др ) при влажности W, кг / м 3 .
Физико-механические свойства смолы
СФЖ - 3014
Однородная прозрачная жидкость от красновато- коричневого
до темно вишневого цвета
Массовая доля свободного формальдегида,%, не более
Вязкость условная по ВЗ-4 (сопло 4,000 ± 0,015 мм), с
Массовая доля свободного фенола,% не более
Разрушающее напряжение при скалывании по клеевому слою
образца после кипячения в воде в течение 1 часа, Мпа, не менее
Нормы расхода связующего устанавливаются в зависимости от породного
состава сырья, слоя и конструкции плиты, %. [1, приложение 1, табл. 1.3]
Число рабочих дней в году А, определяется по формуле:
Где р - фонд рабочего времени (304 дня);- число рабочих смен в сутки (3);
Т - продолжительность рабочей смены (8 часов).
Цикл прессования t ц, мин,
определяется по формуле:
где
t уд -
удельная продолжительность прессования зависит от ряда факторов, с учетом
которых подбирается по табл. 2.1 (приложение 2), мин/мм; (t уд =
0,24);-толщина прессуемой плиты, мм;
DS -припуск по
толщине плиты на шлифование, (DS =0)
t всп - продолжительность вспомогательных операций на один
цикл работы пресса (загрузка и разгрузка, смыкание и размыкание плит, подъем
давления), принимается равным 1,0 - 1,5 мин;
t пр - продолжительность прессования (время с момента
достижения максимального давления, до начала раскрытия плит пресса), мин.
t ц = (0,24×1,1× 16)+1,0= 5,62 мин;
П год, м 3 /год, определяется по формуле:
Где
П ч , П год - соответственно часовая и годовая
производительность. пресса, м 3 /ч, м 3 /год;
А
- число рабочих часов в году определяется по формуле (2.1);- число рабочих
промежутков пресса;, b, S- соответственно длина, ширина, толщина готовых
чистооб
Кu
- коэффициент использования всех агрегатов главного принимается равным 0,8 -
0,9;
t ц - цикл прессования определяется по формуле (2.2), мин.
Определяем массу готовой стружечной плиты (кг), определяется по формуле:
Где
l,b -длина, ширина плиты, м;-толщина плиты, мм;
Расход
абсолютно сухих древесных частиц на одну плиту , (кг),
определяется по формуле:
где
q пл -определяется по формуле (3.1.); пл -влажность готовых
плит [1, табл. 4.1 ],%;
Расход
стружки с некоторой влажностью на одну плиту , (кг),
определяется по формуле:
где
W - влажность сухой стружки, принимается равной 2-3%.
Определяем количество абсолютно сухой стружки на 1 м 3 плит q н абс.с,
(кг), определяется по формуле:
где
r пл -
плотность плиты, кг/м 3 ; пл - влажность готовых плит,%;
Количество
стружки с некоторой влажностью на 1 м 3 плит без учета потерь q н w,
(кг), определяется
3.3
Расчет расхода древесины на 1 м 3 плит
Расход
древесины на 1 м 3 плит V др, (кг / м 3 ),
определяется по формуле:
где
r пл
-плотность изготовляемых плит, кг / м3;
Р
-норма расхода связующего; пл -влажность готовых плит,%;
r усл -средневзвешенная условная плотность древесного
сырья, кг / м 3 ;
К п
-коэффициент, учитывающий потери и отходы сырья на отдельных технологических
операциях, определяется по формуле (3.7).
Коэффициент
К п , учитывающий технологические потери и отходы древесины на
отдельных технологических опреациях при изготовлении плит определяем по
формуле:
К п
= К разд К сорт.щ К с К тр К суш
К обр К шл , (3.7)
где
К разд - коэффициент потерь при разделке сырья. При разделке сырбя на
метровые отрезки К разд =1,01, при отсутствии разделки К разд =1;
К сорт.щ
-коэффициент потерь сырья при сортировке щепы, в расчетах принимается К сорт.щ =
1,06. При отсутствии сортировки щепы К сорт.щ =1;
К с
- коэффициент, учитывающий вид сырья. К с = 1,12;
К тр
- коэффициент потерь сырья при транспортировке стружки, в расчетах принимается
К тр =1,01;
К суш
- коэффициент потерь стружки в период сушки, в расчетах принимаются потери К суш =1,03;
К обр
- коэффициент потерь сырья при обрезке плит по периметру зависит от формата
плиты до и после обрезки, разница между которыми составляет 5 см по длине и
ширине на обе стороны.
К п
= 1 × 1 × 1 × 1,01 × 1,03 × 1,04 ·1 = 1,082;
Расход смолы (в пересчете на сухой остаток) на одну плиту q сух . см,
(кг), определяется по формуле:
Расход смолы (в пересчете на сухой остаток) на 1 м 3 плит q сух.см,
(кг), опрделяется по формуле:
Расход
смолы стандартной концентрации q ст.см, (кг), опрделяется по формуле:
где
К - стандартная концентрация смолы,%, (К = 50%):
4. Пооперационный расчет перерабатываемого материала в
производстве древесностружечных плит
Для определения количества единиц технологического оборудования необходимо
знать, сколько материала перерабатывается на каждой технологической операции.
Данный расчет позволяет определить расход сырья и связующего для выполнения
заданной программы. Расход сырья состоит из его полезного выхода, вошедшего в
готовую продукцию, и отходов, часть которых теряется безвозвратно, а другая
часть может быть собрана и использована в основном производстве.
.1 Определение массы абсолютно сухого материала в готовых чистообрезных
плитах, кг/ч
где
П ч - часовая производительность цеха, м 3 /ч;
,08
- коэффициент, учитывающий влажность плиты (W пл =8%).
.2
Определение массы абсолютно сухого материала в нешлифованных плитах, кг/ч
По
заданию выпускаемые плиты не шлифуются.
.3
Определение массы абсолютно сухого материала в необрезной плите, кг/ч
где
К обр - коэффициент потерь сырья при обрезки плит по периметру.
Принимается равным как и в формуле 3.7. К обр =1,04.
q г - масса абсолютно сухого материала в готовых
чистообрезных шлифованных плитах, кг/ч.
Отходы
материала при обрезки измельчаются и на 90% возвращаются в бункер сухой или
сырой стружки внутреннего слоя. Количество возвращаемого материала после
обрезки определяется по формулам
где
0,9 - коэффициент возврата отходов после обрезки в производство.
Остальные
обозначения такие же, как и в предыдущих формулах.
.4
При формировании стружечного ковра на ленте коэффициент потерь равен 1,005. Он
возникает при разделении ковра на пакеты. Тогда масса абсолютно сухого
материала, проходящего через формирующие машины, q вф, (кг / ч),
определяется:
Масса
абсолютно сухого материала в разделительной коробке определяется по формуле
где
q необ -
масса абсолютно сухого материала в наружных слоях не обрезной плиты, кг/ч.
Определяется
масса абсолютно сухого материала до формирующей машины с учетом возврата
стружечной массы из разделительных коробок в бункер формирующих машин, кг/ч
где
q необ -
масса абсолютно сухого материала в наружных слоях не обрезной плиты, кг/ч.
q вф - масса абсолютно сухого материала наружных слоев,
проходящего через формирующую
у ф
- масса абсолютно сухого материала в разделительной коробке, кг/ч.
q доф = 9385,25 - 1224,16 = 8161,09 кг/ч.
.5
Определяется масса абсолютно сухого связующего, находящегося в массе абсолютно
сухого материала, и поступающего в смесители, кг/ч
где
Р, Р- расход связующего соответственно в наружных и внутреннем слое,%.
.6
Определяется масса абсолютно сухой стружки, находящейся в массе абсолютно
сухого материала, поступающей в смеситель, кг/ч
где
q связ , q доф , - определяются по формулам (4.16-4.12).
q см = 8161,09 - 708,04 = 7453,05 кг/ч;
.7
Определяется масса абсолютно сухой стружки, поступающей в бункер с учетом
возврата шлифованной пыли в бункер наружного слоя и дробленки от форматной
обрезки в бункер внутреннего слоя, кг/ч
где
q см , -
масса абсолютно сухой стружки, находящейся в массе абсолютно сухого материала,
поступающей в смеситель, кг/ч;
у ш -
количество шлифованной пыли, возвращаемой в производство, кг/ч;
q б = 7453,05 - 282,5 = 7170,65 кг/ч
.8
Потери стружки при сепарации отсутствуют. Может отделяться часть крупной
стружки и сколов, которые дополнительно измельчаются и возвращаются на
сортировку. При такой технологии возможен вариант, когда часть мелких древесных
частиц и пыли отбирается из внутреннего слоя и направляется в наружные, а часть
крупных древесных частиц, отделяемых при сепарации стружки наружного слоя,
отправляется в стружку внутреннего слоя. Следовательно необходимо выполнить
расчет для определения количества древесных частиц, перебрасываемых на другие
потоки.
.9
Определяется (условно) масса абсолютно сухой стружки, поступающей в сушилки,
кг/ч
где
К суш , - коэффициент потерь при сушке стружки. Принимается: К суш =1,03;.
q б , - масса абсолютно сухой стружки, поступающей в
бункер, кг/ч.
q суш = 7170,55∙1,03 = 7385,67 кг/ч
.10
Определяется потребность производства в абсолютно сухой древесине с учетом
потерь при раскрое и измельчении сырья, изготовлении и транспортировке стружки,
кг/ч
q др =q суш *К разд *К сортщ *К с *К тр ,
(4.13)
где
q суш , -
масса абсолютно сухой стружки, поступающей в сушилки,, кг/ч;
К разд ,
К сортщ , К с , К тр - коэффициенты, учитывающие
потери сырья соответственно на участке разделки сырья, сортировки щепы,
учитывающий вид сырья и транспортировки стружки.
q др = 7385,67*1,01 = 7459,53 кг/ч;
.11
Определяется расход материалов данной влажности при каждой технологической
операции, кг/ч
где
q абс.с -
расход абсолютно сухого материала на каждой технологической операции, кг/ч;
W- влажность
материала на каждой технологической операции,%.
4.12
Определение удельного расхода древесного сырья и смолы с учётом всех потерь на
1 плит
Удельный
расход древесного сырья на 1 плит , :
Удельный
расход смолы на изготовление 1 плит , :
Удельный
расход смолы стандартной концентрации на изготовление 1 плит, , :
Годовая
потребность в древесном сырье , :
Годовая
потребность в смоле стандартной концентрации , кг:
Часовой расход абсолютно сухого материала и при данной влажности на
каждой технологической операции при изготовлении ДСтП
Расход абсолютно сухого материала, кг/ч
Расход материала заданной влажности, кг/ч
До измельчения (потребность в сырье)
Исходя их задания на курсовое проектирование (конструкции плит, области
их применения, вида сырья) и опираясь на принципиальную схему производства ДСтП
и технологические расчеты, разрабатывается технологическая схема производства
ДСтП.
Выбор оборудования зависит от применяемой технологической схемы,
технологической характеристики и загрузки станка или установки.
Количество единиц оборудования на каждой технологической операции
рассчитывается по следующей формуле:
где
q - часовой расход материала на каждой технологической операции (см. табл.), кг
/ ч;
П ч
- часовая производительность оборудования, выбирается из технической
характеристики или рассчитывается по эмпирическим формулам;
К u
- коэффициент использования оборудования, принимается равным 0,8 - 0,9.
Принимаем
число единиц оборудования (n), путем округления (до ближайшего целого числа)
расчетного количества оборудования (m).
Определим
процент загрузки оборудования по формуле:
Где
m -число станков, полученное по расчету;-принятое число станков.
где
τ - время, в течении которого бункер обеспечивает
бесперебойную работу потока на
-
коэффициент заполнения рабочего объёма бункера;
=0,95 -
с.49[1] для вертикальных бункеров.
Принимается
1 бункер ДБО-150 с коэффициентом загрузки 40%.
где
- часовая производительность оборудования, ;
-
коэффициент использования оборудования.
=4300 - таблица 7.8[2] для ДС-7 B с толщиной
стружки 0,4 мм.
Принимается
2 станок ДС-7 B с коэффициентом загрузки 96%.
.3
Бункерование влажной стружки после её измельчения
Принимается
=100 -
с.148[2] для ДБО-100;
= 140 - приложение 4[1] для древесных частиц от центробежных станков с W=80%.
Принимается
1 бункер ДБО-100 с коэффициентом загрузки 107%.
Требуемое
количество зубчато-ситовых мельниц , шт:
Принимается
=6000 -
с.161[2] для ДМ-8 и стружки = 80%.
Принимается
2 зубчато-ситовых мельницы ДМ-8 с коэффициентом загрузки 73%.
Требуемое
количество бункеров для влажной стружки m, шт:
где
- насыпная масса влажной стружки, кг¤м 3 .
Принимается
=60 -
с.148[2] для ДБО-60;
= 135
кг ¤ м 3 - приложение 4 [ 1 ] для
древесных частиц от мельниц с W =80%.
Принимается
2 бункера ДБО-60 с коэффициентом загрузки 93%.
Принимается
=5900 - таблица
11.1[2] для наружных слоёв сушилки Н167-66;
Принимается
2 сушильных барабана “Прогресс” Н167-66 с коэффициентом загрузки 70%.
.7
Сортировка и доизмельчение сухой стружки
.7.1
Механическая сортировка стружки
Требуемое
количество сортировок , шт:
Принимается
=8000 -
с.187[2] для ДРС-2;
Принимается
1 механическая сортировка ДРС-2 с коэффициентом загрузки 99%.
.7.2
Пневматическая сортировка стружки
Требуемое
количество оборудования для сортировки стружки по толщине m,
шт:
Принимается
=8000 -
с.194[2] для ДПС-1.
Принимается
1 пневматическая сортировка ДПС-1 с коэффициентом загрузки 99%.
Для
доизмельчения сухой стружки принимается одна зубчато-ситовая мельница ДМ-8.
Принимается
=60 -
с.148[2] для ДБОС-60;
=100 - прил. 4[1] для сухих мелких древесных частиц от
мельниц.
Принимается
3 бункера ДБОС-60 с коэффициентом загрузки 84%.
Для
дозирования сухой стружки потоке принимается выравнивающий бункер- питатель
ДБД-2.
Требуемое
количество оборудования m, шт:
Принимается
=10000 - таблица
13.3[2] для “Бизон” (ФРГ).
Принимается
1 смеситель “Бизон” (ФРГ) с коэффициентом загрузки 83%.
Требуемое
количество оборудования m, шт:
Принимается
=12000 - таблица
15.1[2] для “Бэре и Гретен”.
Принимается
1 формирующая машина с коэффициентом загрузки 97%.
Для
подпрессовки стружечного пакета принимается пресс ПР-5
Для
взвешивание пакетов принимаются контрольные весы ВЛВ-5
Производительность
форматнообрезных станков П, :
-
коэффициент использования станка;
-
коэффициент использования рабочего времени.
Принимается
U =10 м⁄мин - c.287[3] для
станка ДЦ-3М;
где
П ч - часовая производительность многоэтажного пресса, .
Для
охлаждение принимается веерный охладитель.
Для
снятия внутренних напряжений производится выдержка на складах в плотных пачках.
Для
нормальной работы оборудования требуются правильно подобранные транспортные
связи, которые должны учитывать состояние и геометрические размеры древесных
частиц, а также дальность и профиль перемещения. Как правило, для
транспортировки технологического сырья применяются цепные и ленточные транспортеры,
для транспортировки щепы, стружки - ленточные, скребковые, с погружными
скребками, пневмотранспортные установки; для транспортировки плит - роликовые
транспортеры.
В наиболее распространенных цехах, т. е. средних по мощности, где
применяется однотипное оборудование, организуют производство трехслойных ДСтП.
При этом создают два потока подготовки стружки: один-для наружных слоев плиты,
другой - для внутреннего слоя. Это связано с некоторым усложнением
технологического процесса, но позволяет получать трехслойные ДСтП высокого
качества.
Технологическая щепа поступает по скребковому конвейеру 1 в вертикальный
бункер ДБО-150 2.
Поток подготовки стружки наружных слоев начинается с подачи щепы к
центробежному стружечному станку ДС-7 3. Полученная стружка наружных слоев
пневмотранспортом подается в бункер для операционного запаса ДБО-100 4, откуда
далее поступает на доизмельчение в зубчато-ситовую мельницу ДМ-8 5, а затем
подается в бункеры влажной стружки ДБО-60 6. Оттуда стружка попадает в
сушильные установки с вращающимся барабаном “Прогресс” марки Н-167-66 7.
Высушенная стружка пневмотранспортом через циклон подается в противопожарный
бункер 8 и далее на механическую сортировку качающегося типа ДРС-2 9 для
обеспечения разделения стружки по площади её поверхности. Затем для разделения
по толщине, стружка попадает на пневматический двухступенчатый сепаратор ДПС-1
11. Крупная стружка, превышающая допустимые параметры, отправляется на доизмельчение
в зубчато-ситовую мельницу ДМ-8 10. Высушенная и отсортированная стружка
пневмотранспортом через циклон подаётся в вертикальные бункеры сухой стружки
ДБОС-60 12. От сюда она подается в выравнивающий бункер-питатель ДБД-2 13,
служащий для дозирования сухой стружки в смеситель ДСМ-7 13, в котором она
смешивается со связующим. Осмоленная стружка ленточным конвейером 15 подается в
формирующие машины ДФ-6 16 наружных слоев.
Формирование пакетов и прессование плит осуществляются на общей поточной
автоматической линии, управляемой с общего пульта. Процесс формирования
стружечных пакетов начинается с подачи поддонов конвейером 27 на формирующий
конвейер 28 через определенные промежутки времени, соответствующие заданному
ритму главного конвейера. Кромки поддонов механически перекрываются траверсами
(отсекателями), обеспечивающими прямоугольность передней и задней кромок
пакета. Просыпавшаяся между поддонами стружка падает на ленточные конвейеры, с
которых пневмотранспортом возвращается в формирующие машины.
По выходе из зоны формирующих машин стружечные пакеты проходят через
металлоулавливатель 29 и далее подаются к прессу для подпрессовки ПР-5 30, где
предварительно уплотняются. Вышедший из пресса 30 стружечный брикет поступает
на площадку контрольных весов ВЛВ-5 31, где проверяют точность формирования
брикетов по массе. С контрольных весов брикеты передаются в загрузочную
этажерку. После заполнения всех этажей происходит загрузка пресса ПР-6Б 32 и
одновременно выгрузка из пресса готовых плит в разгрузочную этажерку.
Из нее плиты по одной с помощью конвейеров направляются к
форматно-обрезному станку ДЦ-3М 33. Поступившие в станок плиты обрезаются
сначала по поперечным кромкам, затем по продольным, после чего они поступают
для охлаждения в веерный охладитель 34 и далее в штабелеукладчик 35, где
собираются в пакеты объемом 2,5 м 3 . Эти пакеты перевозят в отделение
выдержки.
В данном курсовом проекте был произведен выбор принципиальной схемы
производства ДСтП и исходных технологических данных, расчёт производительности
цеха, расходов сырья и материалов, пооперационный расчёт сырья, разработка
технологической схемы производства ДСтП. Также осуществлен подбор, расчёт
количества основного технологического оборудования и описан технологический
процесс производства ДСтП.
1. Евдокимов М.И., Ковальчук Т.А.,
Твердохлебова В.Н. Технология древесных плит и пластиков: Метод. указ. к
курсовому и дипломному проектированию. - Красноярск: КГТА, 1996.-56 с.
2. Справочник по производству
древесностружечных плит/ Под редакцией Отлева И.А. и др.- 2-е изд. - М: Лесная
промышленность, 1990.-З84 с.
3. Шварцман Г.М., Щедро Д.А.
Производство древесностружечных плит.- М.: Лесная промышленность, 1987.-320 с.
4. ГОСТ 10632-89. Плиты древесностружечные.
Технические условия.
5. Ермолина Т.В. Оформление текстовых
документов: Методические указания для студентов специальности 26.02. -
Красноярск: СТИ, 1996.-28с.
Похожие работы на - Проект цеха по производству древесностружечных плит Курсовая работа (т). Другое.
Курсовая работа по теме Інтертекстуальність в поемі Шекспіра 'Гамлет'
Курсовая работа: Формы и методы профилактики детской беспризорности и безнадзорности
Контрольная Работа По Теме Основы Комплексной Безопасности
Забвению Не Подлежит Темы Сочинений
Управление Финансами Курсовая Работа
Сочинение Труд В Наше Время
Реферат по теме Вы готовы стать лидером?
Курсовая работа по теме Решение задачи Неймана для уравнения Пуассона в прямоугольной области
В Чем Является Сила Духа Сочинение
Контрольная Работа По Геометрии 8 Класс 2022
Гордость Мешает Человеку Быть Счастливым Сочинение
Сочинение: Россия в лирике Блока и Есенина
Курсовая работа по теме Проектирование организационной структуры ЗАО 'Фарминдастриаз'
Реферат: Artificial Intelligence Essay Research Paper Artificial IntelligenceArtificial
В Аптеке Сочинение Егэ
Реферат: Уроки весёлой науки. Скачать бесплатно и без регистрации
Контрольная Работа 8 Класс Рациональные
Реферат На Тему Портретное Искусство
Реферат: The Life Of Johannnes Kepler Essay Research
Курсовая работа по теме Разработка стратегии развития организации EriellGroup
Реферат: Авторские права и Интернет
Реферат: Freedom Essay Research Paper FREEDOM The definition
Реферат: Физиология (РЕГУЛЯЦИЯ РЕГИОНАЛЬНОГО КРОВООБРАЩЕНИЯ)