Привод ковшового элеватора. Курсовая работа (т). Технология машиностроения.
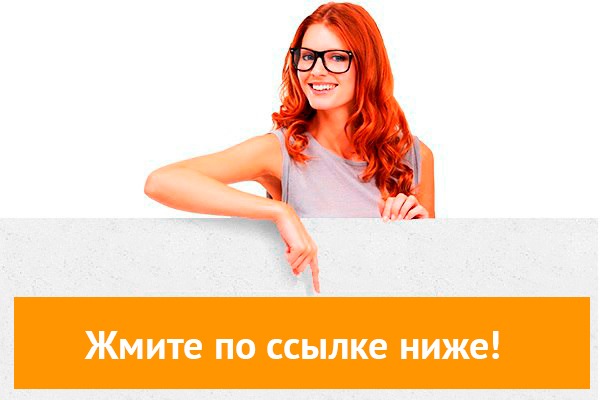
👉🏻👉🏻👉🏻 ВСЯ ИНФОРМАЦИЯ ДОСТУПНА ЗДЕСЬ ЖМИТЕ 👈🏻👈🏻👈🏻
Вы можете узнать стоимость помощи в написании студенческой работы.
Помощь в написании работы, которую точно примут!
Похожие работы на - Привод ковшового элеватора
Скачать Скачать документ
Информация о работе Информация о работе
Скачать Скачать документ
Информация о работе Информация о работе
Скачать Скачать документ
Информация о работе Информация о работе
Скачать Скачать документ
Информация о работе Информация о работе
Скачать Скачать документ
Информация о работе Информация о работе
Нужна качественная работа без плагиата?
Не нашел материал для своей работы?
Поможем написать качественную работу Без плагиата!
Министерство
образования Республики Беларусь
Белорусский государственный
технологический университет
по дисциплине: Основы конструирования и проектирования
на тему: Привод ковшового элеватора
Зубчатая передача (редуктор), выполненный
в виде отдельного агрегата, служит для передачи мощности от двигателя к рабочей
части машины.
Назначение редуктора – понижение угловой
скорости и повышение враща-ющего момента ведомого вала по сравнению с валом
ведущим.
Рассматриваемый
редуктор состоит из корпуса (литого чугунного), в котором помещены элементы
передачи – вал-шестерня, зубчатое колесо, подшипники и т.п.
Узлы соединяются между собой валами, через которые передаётся крутящий
момент.
Вал, передающий крутящий момент, называется ведущим и мощность
передаваемая этим валом является выходной. Вал, принимающий крутящий момент,
называется ведомым.
Задача 1. Разработка кинематической схемы машинного
агрегата
1.1 Условия эксплуатации
машинного агрегата
Устанавливаем привод к ковшовому элеватору
на стройплощадку. Агрегат работает на протяжении 3 лет в две смены.
Продолжительность смены 8 часов, нагрузка мало меняющаяся с малыми колебаниями,
режим работы реверсивный.
1.2 Срок службы
приводного устройства
где L r - срок службы привода, лет; t c -
продолжительность смены, ч; L c - число смен.
Принимаем время простоя машинного агрегата
15% ресурса. Тогда
Рабочий ресурс привода принимаем L h
= 15000 ч.
Таблица
1.1. Эксплуатационные характеристики машинного агрегата
Задача 2. Выбор двигателя. Кинематический расчет
привода
2.1 Определение
номинальной мощности и номинальной частоты вращения двигателя
1. Определим мощность рабочей машины P рм ,
кВт:
где F — тяговая сила ленты, кН; v, —
скорость ленты, м/с.
Подставляя значения в (2.1) получаем:
Р рм
= 2,72 · 1000 · 0,9 = 2,45 · 1000Вт=2,45 кВт
2. Определим общий коэффициент полезного
действия привода:
= пк 2 · пс ·
м · зп · ц
где пк ,
пс , м , зп , ц
— коэффициенты полезного действия подшипников качения (две пары), подшипников
скольжения (одна пара), муфты , закрытой зубчатой передачи , цепной передачи
=0,995 2 · 0,99 · 0,98 · 0,97 · 0,93 = 0,87 .
3. Определим требуемую мощность двигателя
Р дв , кВт:
4. Определим номинальную мощность
двигателя Р ном , кВт:
Значение номинальной мощности выбираем по
величине, большей, но ближайшей к требуемой мощности :
Принимаем номинальную мощность двигателя Р ном
= 3,0 кВт, применив для расчета четыре варианта типа двигателя, представленных
в табл.2.1:
Таблица
2.1. Технические данные различных типов двигателей
Каждому значению номинальной мощности Р ном
соответствует в большинстве не одно, а несколько типов двигателей с различными
частотами вращения, синхронными 3000, 1500, 1000, 750 об/мин. Выбор типа
двигателя зависит от типов передач, которые входят в привод, кинематических
характеристик рабочей машины и производится после определения передаточного
числа привода и его ступеней. При этом следует отметить, что двигатели с
большой частотой вращения (синхронной 3000 об/мин) имеют невысокий рабочий
ресурс, а двигатели с низкими частотами (синхронной 750 об/мин) металлоемки,
поэтому их нежелательно применять без особой необходимости в приводах общего
назначения малой мощности.
2.2 Определение
передаточного числа привода и его ступеней
1. Определим частоту вращения приводного
вала рабочей машины:
где v — скорость
тягового органа, м/с; D — диаметр барабана, мм.
n рм
= 60 · 1000 · 0,9 / ( 3,14·250 ) = 69,0 об / мин.
2. Определим передаточное число привода
для всех приемлемых вариантов типа двигателя:
3. Производим разбивку общего
передаточного числа, принимая для всех вариантов передаточное число редуктора
постоянным U зп = 4:
В табл. 2.2 сведены все варианты разбивки
общего передаточного числа.
Таблица
2.2 Варианты разбивки передаточного числа
Из рассмотренных четырех вариантов
предпочтительнее 2-й тип двигателя: 4АМ112MАУ6З (Р ном = 3,0 кВт, n ном
= 955 об / мин).
Итак, передаточные числа для выбранного
двигателя будут иметь следующие значения: U = 13,84; U оп = 3,46 ;U зп
= 5,20 .
4. Определим максимально допустимое
отклонение частоты вращения приводного вала механизма:
∆n рм
= n рм · δ / 100 = 69,0 · 5 /100 = 3,45 об / мин.
5. Определим допускаемую частоту движения
приводного вала элеватора, приняв ∆n рм = 1,05 об / мин:
[n рм ]
= n рм + ∆n рм = 69+1,05=70,05 об / мин;
отсюда фактическое
передаточное число привода
U ф
= n ном / [n рм ] = 955 / 70,05 = 13,6.
Передаточное число открытой передачи
Таким образом, выбираем двигатель
4АМ112MА6УЗ c Р ном = 3,0 кВт, n ном = 955 об / мин);
передаточные числа: привода U = 13,6, редуктора U зп = 4, цепной
передачи U оп = 3,4.
2.3 Определение
силовых и кинематических параметров привода
Силовые (мощность и вращающий момент) и
кинематические (частота вращения и угловая скорость) параметры привода
рассчитывают на валах привода из требуемой (расчетной) мощности двигателя Р дв
и его номинальной частоты вращения n ном при установившемся режиме.
Расчеты проводятся в таблице 2.3.
Таблица
2.3. Определение силовых и кинематических параметров привода.
Р 1
= Р дв м пк = 2,8 · 0,98 ·
0,995 = 2,73 кВт
Р 2
= Р 1 зп пк = 2,73 · 0,97 ·
0,995 = 2,63 кВт
Р рм
= Р 2 ц пc = 2,63 · 0,93 ·
0,99 = 2,42 кВт
Т дв
= Р дв · 1000 / ω ном = 2800/100 = 28 Н· м
Т 1
= Т дв м пк = 28 · 0,98 ·
0,995 = 27,3 Н· м
Т 2
= Т 1 U зп зп пк =
=27,3 · 4 · 0,97 · 0,995 = 105,4 Н·м
Т рм
= Т 2 U ц ц пc =
=105,4 · 3,4 · 0,93 · 0,99 = 330Н·м
Табличный ответ к задаче представлен в
табл. 2.4:
Таблица
2.4. Силовые и кинематические параметры привода.
Тип
двигателя 4АМ112MА6УЗ Р ном = 3 кВт n ном = 955 об/мин
Задача 3. Выбор материала зубчатой передачи
3.1 Выбираем материал
зубчатой передачи
а) По таблицам определяем марку стали: для
шестерни — 40Х, твердость ≥ 45HRCэ; для колеса — 40Х, твердость ≤
350 HB.
б) Также определяем механические
характеристики стали 40Х: для шестерни твердость 45…50 HRC,
термообработка — улучшение, D пред = 125 мм; для колеса твердость
269…302 HB, термообработка — улучшение, S пред = 80 мм.
в) Определяем среднюю твердость зубьев
шестерни и колеса:
HB 1ср. = (50+45) / 2 = 47,5HRC=450
HB
3.2 Определяем
допускаемые контактные напряжения для зубьев шестерни [] H1 и
колеса [] H2 :
а) Рассчитываем коэффициент долговечности
К HL :
N 2
= 573· L h · 2 = 573 · 15000·
25 = 214,9 · 10 6 циклов,
N 1
= 573· L h · = 573 ·
15000· 100 = 859,5 · 10 6 циклов.
Число циклов перемены напряжений N Н0 ,
соответствующее пределу выносливости, находим по табл. 3.3 [1, с.51]
интерполированием:
N но1 = 68 · 10 6
циклов и N но2 = 22,7 · 10 6 циклов.
Т.к. N 1 > N но1 и
N 2 > N но2 , то коэффициенты долговечности K HL1 =
1 и K HL2 = 1.
б) Определяем допускаемое контактное
напряжение [] H соответствующее числу циклов перемены
напряжений N но : для шестерни
[] но1
= 14 HRC
ср. +170=14·47,5 +170=835 Н/мм 2
[] но2
= 1,8· HB 2ср +67
= 1,8 · 285,5 + 67 = 580,9 Н/мм 2
в) Определяем допускаемое контактное
напряжение:
для шестерни [] н1 =
K HL1 · [] но1 = 1 · 835 = 835 Н/мм 2 ,
для колеса [] н2
= K HL2 · [] но2 = 1 · 580,9 = 580,9 Н/мм 2 .
Т.к. HB 1ср - HB 2ср
> 70 и HB2ср =285,5<350HB, то значение [] н рассчитываем по
среднему допускаемому значению из полученных для шестерни и колеса:
[] н
=0,45([] н1 +[] н2 ) = 637,2 Н/мм 2 .
При этом условие [] н <
1.23· [] н2 соблюдается.
3.3 Определяем
допускаемые напряжения изгиба для зубьев шестерни [] F1 и
колеса [] F2.
а) Рассчитываем коэффициент долговечности
K FL .
Наработка за весь срок службы : для
шестерни N 1 = 859,5 · 10 6 циклов, для колеса N 2 =
214,9 · 10 6 циклов.
Число циклов перемены напряжений,
соответствующее пределу выносливости, N F0 = 4· 10 6
для обоих колес.
Т.к. N 1 > N F0 и N 2
> N F0 , то коэффициенты долговечности K FL1 = 1 и K FL2
= 1.
б) По табл. 3.1 /1/ определяем допускаемое
напряжение изгиба, соответствующее числу циклов перемены напряжений N F0 :
для шестерни [] Fo1 =
310 Н/мм 2 , в
предположении, что m<3 мм;
для колеса [] Fo2
=1,03· HB 2ср =1,03 · 285,5 = 294 Н/мм 2
в) Определяем допускаемые напряжения
изгиба:
для шестерни [] F1 =
K FL1 · [] Fo1 = 1 · 310 = 310 Н/мм 2 ,
для колеса [] F2 =
K FL2 · [] Fo2 = 1 · 294 = 294 Н/мм 2 .
Т.к. передача реверсивная, то [] F
уменьшаем на 25%: [] F1 = 310 · 0,75 = 232,5 Н/мм 2 ; [] F2 = 294 · 0,75 =
220,5 Н/мм 2 .
Табличный ответ к задаче представлен в
табл. 3.1:
Таблица3.1.
Механические характеристики материалов зубчатой передачи.
Задача 4. Расчет зубчатых передач редуктора
4.1 Расчет закрытой
цилиндрической зубчатой передачи
1. Определяем главный параметр — межосевое
расстояние а W , мм:
Производим определение межосевого
расстояния а W , мм по формуле:
a w =
K нβ K a (U+1) 3 √(T 2 10 3 )/( a
U 2 [] 2 H ), (4.1)
где а) К а —
вспомогательный коэффициент. Для косозубых передач К а = 43;
б) ψ a
= b 2 / a w — коэффициент ширины венца колеса, равный
0,28...0,36 — для шестерни, расположенной симметрично относительно опор в
проектируемых нестандартных одноступенчатых цилиндрических редукторах. Примем
его равным 0,32;
в) U — передаточное число
редуктора (см. табл.2.4.);
г) Т 2 —
вращающий момент на тихоходом валу редуктора, Н· м (см. табл.2.4.);
д) [] Н
- допускаемое контактное напряжение колеса с менее прочным зубом или среднее
допускаемое контактное напряжение, [] Н = 637,2 Н/мм 2 ;
е) К Н
— коэффициент неравномерности нагрузки по длине зуба. Для прирабатывающихся
зубьев К Н = 1.
a w =
43· ( 4 + 1)· 3 √( 105400 / ( 0,32 ·
4 2 · 637,2 2 )· 1 = 79,6 мм.
Полученное значение a w
округляем до 80 мм.
2. Определяем модуль зацепления m, мм:
m ≥
2 K m T 2 10 3 /(d 2 b 2 [] F )
,(4.2)
где а) К m —
вспомогательный коэффициент. Для косозубых передач К m = 5,8;
где d 2 —
делительный диаметр колеса, мм;
в) b 2 = a a W
— ширина венца колеса, мм:
Полученное значение b 2
округляем до 26 мм.
г) [] F
— допускаемое напряжение изгиба материала колеса с менее прочным зубом, [] F
= 294 Н/мм 2 ;
m =
2· 5,8 · 105,4 · 10 3 /( 128,0 · 25,6 · 294 )
= 1,3 мм.
3. Определяем угол наклона зубьев min
для косозубых передач:
min = arcsin(3,5· 1,5 / 25,6) = 11,834 °
4. Определяем суммарное число зубьев
шестерни и колеса для косозубых колес:
z = z 1 + z 2
= 2 a w cos min / m,(4.5)
z
= 2· 80 · cos(11,834 °)/ 1,5 = 104,4
Округляем полученное значение в меньшую
сторону до целого числа:
5. Уточняем действительную величину угла
наклона зубьев для косозубых передач:
=arccos( 104 · 1,5/(2· 80) = 12,83857 °.
6. Определяем число зубьев шестерни:
8. Определяем фактическое передаточное
число U ф :
Проверяем отклонение фактического
передаточного числа от заданного U:
U
= |U ф - U| / U · 100 % =|3,95 - 4| / 4 100 % =1,25 % ≤
4 %.
9. Определяем фактическое межосевое
расстояние для косозубых передач:
a w
= (z 1 + z 2 ) m / (2 cos ).(4.9)
a w = (21 + 83) · 1,5/(2 · cos 12,83857 °) = 80 мм.
10. Основные геометрические параметры
передачи представлены в табл. 4.1:
Таблица
4.1. Расчет основных геометрических параметров передачи.
a w
= (d 1 +d 2 )/2 = (32,31 + 127,69) / 2 ≈ 80 мм.(4.10)
Проверяем пригодность заготовок колес:
Условие пригодности заготовок колес: D заг
D пред ; S заг S пред . Диаметр
заготовки шестерни
D заг = d а1 + 6 мм =
35,31 + 6 = 41,31 мм.
Толщина диска заготовки колеса S заг
= b 2 + 4 мм = 26 + 4 = 30 мм. D пред = 125 мм, S пред
= 80 мм. 41,31<125 и 30 < 80, следовательно, условие выполняется.
13. Проверяем контактные напряжения σ н ,
Н / мм 2 :
H
= K√F t (U ф + 1) K H K
K / (d 2 b 2 ) ≤ [] H .(4.11)
где а) К
вспомогательный коэффициент, равный 376;
б) F t = 2 T 2
10 3 / d 2 - окружная сила в зацеплении, Н:
F t
= 2 · 105,4 · 1000 / 127,69 = 1650,87 H;
в) К Н
коэффициент, учитывающий распределение нагрузки между зубьями. Для
косозубых колес К Н определяется по графику на рис. 4.2 /1/ в
зависимости oт окружной скорости колес v м/с, и степени точности передачи
(табл. 4.2 /1/). Окружная скорость колес определяется по формуле
v
= 2 d 2 /(2· 10 3 ) = 25 ·
127,69 / (2 · 1000) ≈ 1,6 м/с.(4.12)
Данной окружной скорости соответствует 9-я
степень точности передачи. По указанной степени точности передачи и окружной
скорости определяем коэффициент К H = 1,114 ;
г) К Hυ
коэффициент динамической нагрузки, зависящий от окружной скорости
колес и степени точности передачи (табл. 4.3 /1/), равный 1,022 .
Подставив все известные значения в
расчетную формулу (4.11), получим:
H
= 376 · √1650,87 · (3,95 + 1) · 1,114 · 1 ·
1,022 /(127,69 · 26) = 629,4 Н / мм 2 .
14. Проверяем напряжения изгиба зубьев
шестерни σ F1 и колеса σ F2 , Н/мм 2 :
F2
= Y F2 Y F t K F K F
K Fv / ( b 2 m ) ≤ [] F2 ,(4.13)
F1
= F2 Y F1 / Y F2 ≤ [] F1 ,(4,14)
где a) m — модуль
зацепления, мм; b 2 — ширина зубчатого венца колеса, мм; F t
— окружная сила в зацеплении, Н;
б) K Fa —
коэффициент, учитывающий распределение нагрузки между зубьями. Для косозубых
колес К Fa зависит от степени точности передачи. К Fa = 1;
в) К F
— коэффициент неравномерности нагрузки по длине зуба. Для прирабатывающихся
зубьев колес К F = 1;
г) К F
— коэффициент динамической нагрузки, зависящий от окружной скорости колес и
степени точности передачи (см. табл. 4.3 /1/), равный 1,058 ;
д) Y F1 и Y F2
— коэффициенты формы зуба шестерни и колеса. Для косозубых определяются в
зависимости от эквивалентного числа зубьев шестерни
z v 1 = z 1
/ cos 3 21 /
0,92686 = 22,7 (4.15)
z v 2 = z 2
/ cos 2 83 /
0,92686 = 89,5 (4.16)
е) Y
= 1 - / 140 = 1 – 12,83857 / 140 = 0,9083 — коэффициент,
учитывающий наклон зуба;
ж) [] F1
и [] F2 — допускаемые напряжения изгиба шестерни и колеса,
Н/мм 2 .
Подставив все значения в формулы (4.13 -
4.14), получим:
F2
= 3,60 · 0,91 · 1650,87 · 1 · 1 · 1,058 /(26 ·1,5)
= 146,46 ≤ F2
F1
= 146,46 · 3,959 / 3,60 = 161 ≤ F1
15. Составим табличный ответ к задаче 4:
Таблица
4.2 Параметры зубчатой цилиндрической передачи, мм
5 .1 Расчет открытой цепной передачи
p =
2,8 3 √T 1
10 3 K э /(v z 1 [p ц ])
, (5.1)
где а) Т 1
- вращающий момент на ведущей звездочке,Т 1 = 105,4 Н· м;
б) К э —
коэффициент эксплуатации, который представляет собой произведение пяти
поправочных коэффициентов, учитывающих различные условия работы передачи:
где К д —
коэффициент динамичности нагрузки, К д = 1;
К с —
коэффициент, учитывающий способ смазывания, К с = 1;
K —
коэффициент угла наклона линии центров шкивов к горизонту, C
= 1;
K рег —
коэффициент, учитывающий способ регулировки межосевого расстояния, К рег
= 1;
K р —
коэффициент, учитывающий режим работы, К р = 1,25;
в) z 1 -
число зубьев ведущей звездочки
где u — передаточное
число цепной передачи, u = 3,4;
Полученное значение округляем до целого
нечетного числа (z 1 = 23 ), что в сочетании с нечетным числом зубьев
ведомой звездочки z 2 и четным числом звеньев цепи l p
обеспечит более равномерное изнашивание зубьев и шарниров;
г) [p ц ] —
допускаемое давление в шарнирах цепи, Н/мм 2 , зависит от частоты
вращения ведущей звездочки и ожидаемого шага цепи, который принимается равным
из промежутка р = 19,05..25,4 мм. Учитывая это получаем [p ц ] = 25,5
Н/мм 2 ;
д) — число
рядов цепи. Для однорядных цепей типа ПР = 1;
p =
2,8 3 √
105,4 · 1000 · 1,25 /(1 · 23 · 25,5) = 17,02 мм,
Полученное значение шага р округляем до
ближайшего стандартного
2. Определим число зубьев ведомой
звездочки z 2 :
Полученное значение z 2
округляем до целого нечетного числа (z 2 = 79 ). Для предотвращения
соскакивания цепи максимальное число зубьев ведомой звездочки ограничено: z 2
120.
3. Определим фактическое передаточное
число u ф и проверим его отклонение u:
Подставляя в значения в формулы (5.5 -
5.6), получим
u
= |3,43 - 3,4|/3,4 · 100% = 1 % ≤ 4 %.
4. Определяем оптимальное межосевое
расстояние а, мм:
Из условия долговечности цепи а =
(30...50) р = 40 · 19,05 = 762 мм,
Тогда а р = а/р = 30...50 = 40 —
межосевое расстояние в шагах, мм.
5. Определяем число звеньев цепи l р :
l p =
2 a p + (z 2 + z 1 ) / 2 + [(z 2 - z 1 )
/ 2] 2 / a p , (5.7)
l p
= 2 · 40 + (102) / 2 + [(79 - 23) / (2 · 3,14)] 2 / 40 =
133.
Полученное значение l p
округляем до целого четного числа ( l p =132).
6. Уточняем межосевое расстояние а р
в шагах:
a p
= 0,25 { l p - 0,5(z 2 + z 1 ) + √[ l p -
0,5(z 2 + z 1 )] 2 - 8[(z 2 - z 1 )
/ (2 )] 2 }, (5.8)
a p
= 0,25 · { 132 - 0,5 · (102) + √[132 - 0,5 · (102)] 2
- 8 · [( 79 - 23) / (2 · 3,14)] 2 } = =39,5
7. Определяем фактическое межосевое
расстояние а , мм:
Значение а не округляем до целого числа.
Так как ведомая (свободная) ветвь цепи должна провисать примерно на 0,01а, то
для этого при монтаже передачи надо предусмотреть и возможность уменьшения
действительного межосевого расстояния на 0,005а. Таким образом, монтажное
межосевое расстояние а м = 0,995а.
Полученное значение l не округляют.
9. Определяем диаметры звездочек, мм.
Диаметр делительной окружности ведущей
звездочки d ∂1 , мм:
d ∂1 = 19,05 / sin(180 /23) = 140 мм;
диаметр делительной
окружности ведомой звездочки d ∂2 , мм:
d ∂2 = 19,05 / sin(180 /79) = 480 мм;
диаметр окружности
выступов ведущей звездочки D e1 , мм:
D e1
= p(K + K z1 - 0,31 / ), (5.13)
диаметр окружности
выступов ведомой звездочки D e2 , мм:
D e2
= p(K + K z2 - 0,31 / ), (5.14)
где К = 0,7 —
коэффициент высоты зуба; K z — коэффициент числа зубьев:
K z1 =
ctg(180°/z 1 ) = ctg( 180°/23) = 7,28 — ведущей звездочки,
K z2 =
ctg(180°/z 2 ) = ctg(180°/ 79) = 25,14 — ведомой звездочки;
= р /
d 1 — геометрическая характеристика зацепления (здесь d 1 —
диаметр ролика шарнира цепи), =19,05 / 5,94 = 3,21
Подставив значения в формулы (5.13 -
5.14), получим
D e 1 = 19,05 · (0,7 + 7,28 -
0,31/3,21) = 150,2 мм,
D e 2 = 19,05 · (0,7 + 25,14 -
0,31/3,21) = 490,4 мм,
диаметр окружности
впадин ведущей звездочки D i1 :
D i1
= d ∂1 - (d 1 - 0,175 √ d ∂1 ) ,
(5.15)
D i1
= 140 - (5,94 - 0,175· √140) = 136,1 мм,
диаметр окружности
впадин ведомой звездочки D i2 :
D i2
= d ∂2 - (d 1 - 0,175 √ d ∂2 ) ,
(5.16)
D i2
= 480 - (5,94 - 0,175· √480) = 477,9 мм
10. Проверяем частоту вращения меньшей
звездочки n 1 об/мин:
где n 1 —
частота вращения тихоходного вала редуктора, об/мин (на этом валу расположена
меньшая звездочка);
[n] 1 =
15000 / p = 15000 / 19,05 = 787,4 об/мин — допускаемая частота вращения.
11. Проверяем число ударов цепи о зубья
звёздочек U, c -1 :
где U = 4 z 1 n 1
/ (60 l p ) = 4 · 23 · 239 / (60 · 132) =
2,78 c -1 — расчетное число ударов цепи;
[U] = 508 / p = 508 /
19,05 = 26,667 c -1 —допускаемое число ударов.
12. Определяем фактическую скорость цепи v ,
м/с:
23
· 19,05 · 239 /60000 = 1,74 м/с. (5.19)
13. Определяем окружную силу, передаваемую
цепью F t , Н:
где Р 1 —
мощность на ведущей звездочке кВт; v , м/с .
14. Проверяем давление в шарнирах цепи p ц ,
Н/мм 2 :
а) А — площадь
проекции опорной поверхности шарнира, мм 2 :
где d 1 и b 3
— соответственно диаметр валика и ширина внутреннего звена цепи, мм;
б) допускаемое
давление в шарнирах цепи [р ц ] уточняют соответствии с
фактической скоростью цепи v м/с. [р ц ] = 25,5 Н/мм 2
p ц
= 1511,5 · 1,25 / 75,4 = 25 Н/мм 2 ≤ 25,5 Н/мм 2
15. Проверяем прочность цепи. Прочность
цепи удовлетворяется соотношением S[S], где [S] — допускаемый
коэффициент запаса прочности для роликовых (втулочных) цепей; S—расчетный
коэффициент запаса прочности,
S =
F p / (F t K д + F 0 + F )
, (5.23)
где a) F p –
разрушающая нагрузка цепи, Н, зависит от шага цепи р, F p = 31800 H;
б) F t –
окружная сила, передаваемая цепью, Н; К д – коэффициент, учитывающий
характер нагрузки
в)F o —
предварительное натяжение цепи от провисания; ведомой ветви (от ее силы
тяжести), Н,
где К f =3 –
коэффициент провисания; a – межосевое расстояние, м; q = 1,9 – масса 1 м цепи,
кг/м; g =9,81 м/с 2 – ускорение свободного падения.
г) F
— натяжение цепи от центробежных сил, Н; F = q v 2
,
где v —
фактическая скорость цепи, м/с.
F o = 3 ·
1,9 · 0,7525 · 9,81 = 42,01 H,
S = 31800 / (1511,5 · 1 + 42,01 +5,75) = 20,4
[S] = 8,156; 20,4 ≥ 8,156 - зн.
условие выполняется.
16. Определение силы давления цепи на вал
F оп , Н:
где k в =
1,05 – коэффициент нагрузки вала,
F оп
= 1,05 · 1511,5 + 2 · 42,01 = 1671,2 H.
Таблица
5.1 Параметры цепной передачи, мм
Редукторные валы испытывают два вида
деформации — изгиб и кручение. Деформация кручения на валах возникает под
действием вращающих моментов, приложенных со стороны двигателя и рабочей
машины. Деформация изгиба валов вызывается силами в зубчатом зацеплении
закрытой передачи и консольными силами со стороны открытых передач и муфт.
6.1 Определение сил в зацеплении
закрытых передач
Значения сил приведены в табл. 6.1.
Таблица
6.1 Силы в зацеплении закрытой передачи
=2 ·
105,4 · 1000 / 127,69 = 1650,8 H
=1650,8
· tg20 / cos 12,83857 = 616,2 H
Значения консольных сил приведены в табл.
6.2.
Задача 7. Проектный расчет валов. Эскизная
компоновка редуктора
Основными критериями работоспособности
проектируемых редукторных валов являются прочность и выносливость.
Они испытывают сложную деформацию —
совместное действие кручения, изгиба и растяжения (сжатия). Но так как
напряжения в валах от растяжения небольшие в сравнении с напряжениями от
кручения и изгиба, то их обычно не учитывают.
В проектируемых редукторах рекомендуется
применять термически обработанные среднеуглеродистые и легированные стали 45,
40Х. В качестве материала применяем термически обработанную сталь 40Х со
следующими механическими характеристиками:
7.2 Выбор допускаемых напряжений на
кручение
Проектный расчет валов выполняется по
напряжениям кручения (как при чистом кручении), т. е. при этом не учитывают
напряжения изгиба, концентрации напряжений и переменность напряжений во времени
(циклы напряжений). Поэтому для компенсации приближенности этого метода расчета
опускаемые напряжения на кручение применяют заниженными: [t] к =
10...20 Н/мм 2 .
При этом меньшие значения [t] к
— для быстроходных валов, большие — для тихоходных.
7.3 Определение геометрических
параметров ступеней валов
Редукторный вал представляет собой
ступенчатое цилиндрическое тело, количество и размеры ступеней которого зависят
от количества и размеров установленных на вал деталей.
Определяем расчетные ориентировочные
геометрические размеры каждой ступени вала, мм.
Результаты вычислений представлены в табл.
7.1.
Таблица
7.1 Определение размеров ступеней валов одноступенчатого редуктора
d 1
= 3 √(M k · 10 3 / 0,2[t] k )
=
d 1
= 3 √(M k · 10 3 / 0,2[t] k )
=
l 2
= 1,25 d 2 = 1,25 · 35 = 44 мм
d 3
= d 2 + 3,2r = 35 + 3,2 · 2,5 = =42 мм
l 3
– определяем графически на эскизной компоновке
7.4 Предварительный выбор подшипников
качения
Выбор наиболее рационального типа
подшипника для данных условий работы редуктора весьма сложен и зависит от
целого ряда факторов: передаваемой мощности редуктора, типа передачи,
соотношения сил в зацеплении, частоты вращения внутреннего кольца подшипника,
требуемого срока службы, приемлемой стоимости, схемы установки. По табл. 7.2
/1/ выбираем подшипники для валов.
Для быстроходного вала выбираем роликовые
конические однорядные подшипники типа 7205 со схемой установки 3 (враспор).
Для тихоходного вала выбираем роликовые
конические однорядные подшипники легкой серии типа 7207 со схемой установки 3
(враспор).
Составляем после вычерчивания эскизной
компоновки табличный ответ к задаче (см. табл. 7.2).
Таблица 7.2 Параметры ступеней валов и подшипников
Задача 8. Проверочный расчет подшипников
Проверочный расчет предварительно
выбранных в задаче 7 подшипников выполняется отдельно для быстроходного и
тихоходного валов. Пригодность подшипников определяется сопоставлением
расчетной динамической грузоподъемности С rр , Н, с базовой С r ,
Н, или базовой долговечности L 10h , ч, (L 10 , млн.
оборотов), с требуемой L h , ч, по условиям:
Базовая динамическая грузоподъемность
подшипника С r представляет собой постоянную радиальную нагрузку,
которую подшипник может воспринять при базовой долговечности L 10h ,
составляющей 10 6 оборотов внутреннего кольца.
8.1 Определение
пригодности подшипников на быстроходном валу
Проверить пригодность подшипника 7205
быстроходного вала.
Осевая сила в зацеплении F a = 376,2 Н. Реакции в подшипниках
Характеристика подшипников: С r = 23,9 кН; С 0 r = 17,9 кН; Х=0,40, V=1,0 , К б =1,1, К T =1. Требуемая долговечность
подшипников L h = 15 ∙10 3 ч.
1. Определяем составляющие
радиальных реакций:
R s 1 =0,83еR r 1 =0,83·0,36·856,3=255,86 Н
R s 2 =0,83еR r 2 =0,83·0,36·912,2=272,56 Н
2.Определяем осевые нагрузки
подшипников
Так как R s 1 < R s 2 и F a > R s 2 - R s 1 , то R а1 = R s 1 =255,86 Н,
R а2 = R а1 + F a =255,86 +376,2=632 Н
R a 1 /(VR r 1 ) =255,86/(1· 856,3) =0,29
R a 2 /(VR r 2 )
= 632 / (1 · 912,2) = 0,69
4. По соотношениям R a 1 /(VR r 1 )<е
и R a 2 /(VR r 2 )>е
выбираем соответствующие формулы для определения R Е
R E 1 =VR r 1 К б К Т =1 ·856,3·
1,1·1=942 Н
R E 2 = (X V R r 2 + Y R а2 ) K б
K т =(0,4 · 1 · 912,2 + 1,67 ·
632) · 1,1 · 1 = 1562Н
5. Производим расчет динамической
грузоподъемности по формуле:
С rp
= R E2 m √60 · n · L h /( а 1 ·10 6
· а 23 )= 1562 · 3,33 √60 · 955 ·
15· 10 3 /( 0,7· 10 6 )= =13217,5 H < С r
=23900 H — подшипник пригоден.
6. Рассчитываем долговечность подшипника:
L 10h
= (а 1 ·10 6 · а 23 /(60· n)) · (С r / R E 2 ) 3,33
= 10 6 · 0,7·( 23900 / 1562) 3,33 / (955 ·
60) = =10 5 > 15000 ч. — подшипник пригоден.
8.2 Определение пригодности подшипников на
тихоходном валу.
Проверить пригодность подшипника 7207
тихоходного вала.
Осевая сила в зацеплении F a = 376,2 Н. Реакции в подшипниках
R r 1 = 1019,5 H; R r 2 = 4102,5 H.
Характеристика подшипников: С r = 35,2 кН; С 0 r = 26,3 кН; Х=0,40, V=1,0 , К б =1,1, К T =1. Требуемая долговечность
подшипников L h = 15 ∙10 3 ч.
1. Определяем составляющие радиальных
реакций:
R s 1 =0,83еR r 1 =0,83·0,36·1019,5=313 Н
R s 2 =0,83еR r 2 =0,83·0,36·4102,5=1260 Н
2.Определяем осевые нагрузки
подшипников
Так как R s 1 < R s 2 , то R а1 = R s 1 =313 Н,
R а2 = R а1 + F a =313 +376,2=689,2 Н
R a 1 /(VR r 1 ) =313/(1· 4102,5) =0,076
R a 2 /(VR r 2 )
= 689,2 / (1 · 1019,5) = 0,67
4. По соотношениям R a 1 /(VR r 1 )<е
и R a 2 /(VR r 2 )>е
выбираем соответствующие формулы для определения R Е
R E 1 =VR r 1 К б К Т =1 ·1019,5·
1,1·1=1121 Н
R E 2 = (X V R r 2 + Y R а2 ) K б
K т =(0,4 · 1 · 4102,5 + 1,62 ·
689,2) · 1,1 · 1 = =3033,3Н
5. Производим расчет динамической
грузоподъемности по формуле:
С rp
= R E2 m √60 · n · L h /( а 1 ·10 6
· а 23 )= 3033,3 · 3,33 √60 · 239 ·
15· 10 3 /( 0,7· 10 6 )= =16940 H < С r
=35200 H — подшипник пригоден.
6. Рассчитываем долговечность подшипника:
L 10h
= (а 1 ·10 6 · а 23 /(60· n)) · (С r / R E 2 ) 3,33
= 10 6 · 0,7·( 35200 / 3033,3) 3,33 / (239 ·
60) = =171·10 3 > 15000 ч. — подшипник пригоден.
Таблица
8.1Основные размеры и эксплуатационные характеристики подши
Похожие работы на - Привод ковшового элеватора Курсовая работа (т). Технология машиностроения.
Контрольная работа по теме Античная натурфилософия: проблема субстанций
Сочинение 7 Класс Недоросль Вступление
Ликург И Его Законы Реферат
Курсовая работа по теме Системы компенсации внешних возмущений
Курсовая работа по теме Общее учение о педагогическом процессе
Реферат Про Современную Москву Для Школы
Реферат: Отход Корнуоллиса
Дипломная работа по теме Развитие ценностных ориентаций подростков средствами театральной деятельности
Курсовая работа: Доходы населения России и их дифференциация
Реферат по теме Современное состояние качества воды р.Оби в пределах Тюменской области
Реферат по теме Актуальные вопросы нового акционерного законодательства
Курсовая Работа На Тему Международные Стандарты Учета И Финансовой Отчетности
Реферат по теме Социально-экономическое совершенствование Ботсваны
Контрольная Работа На Тему Автоматизированные Банки Данных
Презентация На Защиту Диссертации Магистра
Прекрасная Дама В Стихотворении Незнакомка Сочинение
Отчет Производственной Практики Бухгалтера Образец
Курсовая работа: Составление и использование бизнес-плана. Скачать бесплатно и без регистрации
Диссертации По Варикозной Болезни
Дипломная работа по теме Значение маркетинга в управлении предприятием на примере гостиницы 'Катерина-Сити' (г. Москва)
Шпаргалка: Шпаргалка по Языковедению
Похожие работы на - Нетрадиционные виды спорта в адаптивной физкультуре
Похожие работы на - Оздоравливающие свойства природной среды и гигиенические факторы, дополняющие комплекс средств физического воспитания