Основы машиностроения. Контрольная работа. Другое.
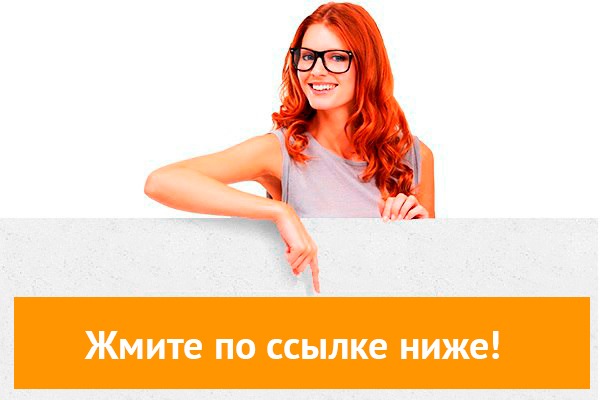
💣 👉🏻👉🏻👉🏻 ВСЯ ИНФОРМАЦИЯ ДОСТУПНА ЗДЕСЬ ЖМИТЕ 👈🏻👈🏻👈🏻
Вы можете узнать стоимость помощи в написании студенческой работы.
Помощь в написании работы, которую точно примут!
Похожие работы на - Основы машиностроения
Скачать Скачать документ
Информация о работе Информация о работе
Скачать Скачать документ
Информация о работе Информация о работе
Скачать Скачать документ
Информация о работе Информация о работе
Скачать Скачать документ
Информация о работе Информация о работе
Скачать Скачать документ
Информация о работе Информация о работе
Скачать Скачать документ
Информация о работе Информация о работе
Скачать Скачать документ
Информация о работе Информация о работе
Нужна качественная работа без плагиата?
Не нашел материал для своей работы?
Поможем написать качественную работу Без плагиата!
Задача 1.1 Определение по заданной посадке основных параметров гладкого
цилиндрического соединения. Построение схем полей допусков заданных посадок. Даны по заданию соединения:
. Соединение осуществляется в системе посадка, посадка с зазором.
Верхнее предельное отклонение: ES = + 87 мкм;
Нижнее предельное отклонение: EI = 0 мкм;
Верхнее предельное отклонение: es = -72 мкм.
Нижнее предельное отклонение:ei = - 126 мкм;
. Определяем предельные размеры отверстия и вала:
D min = D ном + EI, min = 90 + 0 = 90 мм.
d max =
90 + (-0,072) = 89,028 мм. min = d ном + ei, min =
90 + (- 0,0126)= 89,0874 мм.
3. Определяем допуски
размеров деталей:
TD = 90,087 - 90 = 0,087 мм = 87 мкм.
ВАЛ Td = d max - d min ,= 89,028 -
89,087 = 0,059 = 59 мкм.
Или: Td = es - ei,= -72 - (- 126) = 54 мкм.
4. Определяем предельные
значения зазоров и допуски посадок:
S max =
D max - d min,max = 90,087 - 89,0874 = 0,9996 мм =
999 мкм. min = D min - d max , min
= 90 - 89,028 = 0,972 мм = 97 мкм.= S max - S min,
TS = 0,9996 - 0,972 = 0,276 = 27 мкм.
ВАЛА: Т ф = 0,3Т р = 0,3 × 25 = 7,5 мкм
ОТВЕРСТИЯ: Т ф = 0,3Т р = 0,3 × 40 = 12 мкм
6. Шероховатость поверхности:
ВАЛА: R zd = 0,05Т d = 0,05 × 25 = 1,25 мкм
ОТВЕРСТИЯ: R zD = 0,05Т D = 0,05 × 40 = 2 мкм
7. Вычерчиваем схему расположения полей допусков на рисунке 1.А.1.
Таблица 1.1- Основные параметры элементов цилиндрических соединений.
Шероховатость поверхности отверстия
Рис. 1.А.1. Схема расположения полей допусков
Рис. 1.А.2. Чертежи соединения и его детали
Рис. 1.Б.1. Схема расположения полей допусков.
Рис. 1.В.1. Схема расположения полей допусков
Задача № 2. Расчет
и назначение посадок
номинальный диаметр соединения d = 32 мм;
частота вращения вала n =
700 об/мин;
абсолютная вязкость масла = 0,02 H c/м;
удельное давление на опору p =
0,46 МПа;
втулки R ZD = 2,5 мкм; вала R zd = 2,5 мкм;
1. Определяем значение наивыгоднейшего зазора по формуле
2. Определяем величину расчетного наивыгоднейшего зазора с учетом
величины износа поверхности отверстия и вала в период приработки(принимаем 0,7
от R отверстия и вала):
3. Принимаем по таблице ближайшую посадку, удовлетворяющую условию . Такой посадкой будет Ø 32 H7/f7, у которой =62 мкм; =20 мкм и средний зазор будет:
4. Определяем наименьшую толщину масляного слоя при максимальном
зазоре выбранной посадки:
5. Проверить достаточность слоя смазки: 9.96 ˃ 5
Т. К. минимальный слой смазки больше суммы параметров R zd шероховатости поверхности отверстия
и вала - посадка выбрана правильно.
6. Схема расположения полей допусков соединения изображена на рис.
3.1 совместно со схемой расположения полей допусков калибров.
Задача № 3. Расчет
и выбор посадок колец подшипников качения
1. По заданному шифру подшипника определяем его серию и
присоединительные размеры (таблица [2] или приложение Д).
внутренний диаметр внутреннего кольца d = 32 мм;
наружный диаметр наружного кольца D = 150 мм;
радиус закругления ( фаска ) r = 3,5 мм;
2. По таблицам 4.82 и 4.83 или приложению Г, определяем предельные отклонения соответствующих диаметров внутреннего и наружного кольца подшипника качения
Для внутреннего кольца: Для наружного кольца:
3. Определяем значение минимального натяга внутреннего кольца:
где: - минимальный монтажный натяг, R -
наибольшая радиальная нагрузка, к - коэффициент,
зависящий от геометрических параметров кольца подшипника. Принимаем: для тяжелой серии к = 2,0, В - ширина кольца, мм; r - радиус галтели
( фаска ) кольца, мм
По таблицам ГОСТ 24347 - 80 ( СТ ЭВ 144 - 75 ) принимаем для шейки вала
поле допусков m6, при котором минимальный натяг = 20 мкм, а максимальный = 39 мкм (в соединении с кольцом
подшипника).
4. Пользуясь таблицей 4.82 [4] назначаем поля допуска для корпуса подшипника (наружное кольцо имеет местное погружение) Н7.
Определяем предельные отклонения: ES = + 40 мкм; EJ = 0;
По таблицам ГОСТ 24347 - 82 определяем предельные отклонения размеров шейки вала, es = +
24 мкм; ei = 10 мкм
5. Назначаем допуски цилиндричности для поверхностей шейки вала и
корпуса по зависимости Т ф = 0,25Т d и по таблице 2.18 (3)
принимаем ближайшее значение стандартного допуска цилиндричности поверхностей:
6. Назначаем допуски опорных торцов вала и корпуса по таблице 2.28
(3), принимаем степень точности.
7. По таблице 4.95 (4) назначаем параметр поверхности R a
для поверхности шейки вала и гнезда корпуса:
8. Проверяем прочность внутреннего кольца при максимальном натяге выбранной посадки:
где: σ д - допускаемое напряжение при растяжении для подшипниковой стали: σ д = 42 кг * с \см 2
d -
диаметр внутреннего кольца подшипника
Так как максимальный натяг в соединении внутреннего кольца при выбранной
посадке = 39 мкм, то посадка кольца выбрана
правильно.
Таблица 2. Параметры соединения колец подшипника
качения
Рис. 3.1. Схемы расположения полей допусков подшипника качения
Рис. 3.2. Чертежи подшипникового соединения и его деталей
Задача №
4. Выбор предельных
отклонений и допусков гладких калибров, расчет их исполнительных размеров
. По таблице ГОСТ 25347-82 (СТ СЭВ 144-75) находим предельные
отклонения соединяемых деталей:
Отверстия D max = 32,025мм, D min = 32 мм;
Вала d max = 31,975 мм, d min = 31,950 мм;
. По (8, таблица 1) находим соответствующие отклонения и допуски
калибров для (пробки) и для вала (скобы):
Калибр-пробкаZ = 3мкм, H = 4 мкм, Y = 3;
Калибр-скоба =3 мкм, =4 мкм, =3 мкм.
. Определяем предельные размеры калибров и размеры проходных
калибров после износа:
Размеры не проходной части калибра;
Размеры не проходной части калибра;
. Определяем исполнительные размеры калибров:
Вычерчиваем схему расположений полей допусков калибров и соединения.
Задача 5. Взаимозаменяемость соединений сложной
формы
Задача 5.1. Расчет шпоночного соединения
Дано: шпонка призматическая, диаметр вала d = 85 мм; характер соединения шпонки: нормальная в пазу вала и нормальная в пазу втулки; назначение: для массового производства.
1. По таблице 4.64 [4] ( ГОСТ 23360 - 78 ) определяем размеры
шпонки, шпоночных пазов вала и втулки: размеры шпонки b h l ( ширина высота диаметр ) 25 14 85 мм;
2. Исходя из характера соединения шпонки в пазу вала и в пазу
втулки, по Таблице 4.65 [4] ( ГОСТ 23360 - 73 )
- назначаем поля допусков и предельные отклонения для сопрягаемых размеров
шпонки, паза вала и паза втулки по ГОСТ 25347 - 82, результаты заносим в
таблицу 3
3. Определяем предельные значения сопрягаемых размеров шпонки, паза
вала и паза втулки и предельные значения
зазоров или натягов в соединениях шпонки с пазом вала и с пазом втулки.
Результаты заносим в таблицу 3.
. Определяем поля допусков размеров несопрягаемых элементов
соединения пользуясь таблицей 4.66 [ 4 ] и
находим их предельные отклонения по ГОСТ 25347 - 82. Результаты заносим в
таблицу 3.
5. Назначаем допуски симметричности шпоночного паза относительно
оси вала
и параллельности поверхностей шпоночного паза, пользуясь зависимостями:
Т сим = 2 Т ш.п.,; Т пар = 0,5 ш.п.,
где: Т сим - допуск симметричности;
Т пар - допуск ширины шпоночного паза.
Принимаем по таблицам 2.40 и 2.28 ближайшие стандартные значения допусков расположения [4]. Полученные данные заносим в
таблицу 3.
. Пользуясь таблицей 4.64 [4] - назначаем параметры шероховатости
Поверхностей элементов шпоночного соединения.
.Строим схемы расположения полей допусков для посадок шпонки в пазу вала и в пазу втулки; вычерчиваем соединение и его детали с
простановкой соответствующих размеров, полей
допусков, предельных отклонений, допусков
формы и расположения поверхностей и параметров их шероховатости (рис. 4).
Таблица 3. Основные параметры элементов
шпоночного соединения
Зазор в соединении со шпонкой максимальный
Натяги в соединении со шпонкой максимальный
Несопрягаемые Размеры Высота шпонки
Рис. 4.1. Схема расположения полей допусков шпоночного соединения
Рис. 3.2. Чертежи шпоночного соединения и
его деталей
Задача 5.2. Расчет шлицевого соединения.
Дано: шлицевое соединение с прямоточным профилем зубьев и с указанием посадок по заданным параметрам соединения:
- 10 32 H7/t8 40 H12/a11 × 5 F8/e8
1. По таблицам ГОСТ 25347 - 80 определяем предельные отклонения сопрягаемых элементов соединения, находим их предельные
размеры и результаты заносим в таблицу 4.
2. Пользуясь теми же таблицами 4.71 и 4.75 [4] - определяем
предельные отклонения или допускаемые размеры
нецентрирующих элементов соединения, результаты заносим в таблицу 4.
. Назначаем параметры шероховатости на рабочие и нерабочие
поверхности деталей соединения.
. Строим схемы расположения полей допусков центрирующих элементов соединения, вычерчиваем шлицевое соединение в сборе и его
детали, с простановкой соответствующих размеров, полей допусков, предельных
отклонений и параметров шероховатости ( рис. 5 ).
Таблица 4. Параметры элементов шлицевого
соединения
Номинальный размер, мм;
поле допуска
Центрирующие элементы:
Диаметр втулки
Нецентрирующие элементы:
Диаметр втулки
Рис. 5.1. Схемы расположения полей допусков шлицевого соединения
Рис. 5.2. Чертежи шлицевого соединения и его деталей.
Дано: резьбовое соединение М12 1,5 резьба метрическая по ГОСТ 8724
- 81.
1. Пользуясь данными таблицы 4.24 - рассчитываем значение
номинальных размеров среднего и внутреннего
диаметров соединения:
2 ( D 2 ) = 12 -
2 + 0,376 = 10,376мм
номинальный внутренний
диаметр резьбы
d 1 ( D 1 ) = 12 - 1 + 0,026 = 11,026 мм;
2. Пользуясь таблицей 4.29 [4] - находим предельные отклонения
элементов деталей резьбового соединения и
заносим их в таблицу 5.
3. Рассчитываем предельные значения размеров элементов деталей
резьбового соединения, результаты заносим в
таблицу 5.
. Строим схему расположения полей допусков элементов деталей
резьбового соединения и вычерчиваем соединение в
сборе и подетально, с указанием требуемых размеров, полей допусков и параметров
шероховатости.
Таблица 5. Параметры элементов деталей
резьбового соединения
Рис. 6.1. Схема расположения полей допусков резьбового соединения
Рис. 6.2. Чертежи резьбового соединения и его деталей.
Задача № 6. Выбор универсального мерительного инструмента
Дано: гладкое цилиндрическое соединение Ø
1. По таблице определяем, что для данного отверстия допускаемая погрешность измерений δ = 10 мкм
2. Пользуясь таблицей определяем погрешность методов измерения -
находим что для измерений этого размера
подходит индикаторный нутромер ГОСТ 868 - 72 с ценой деления отсчетного
устройства 0,01 мм с используемым перемещением измерительного отверстия с
установкой на ноль по концевым мерам второго класса точности с боковинами.
Здесь ∆lim = 5 мкм
1. Так же как и для отверстия определяем, что для данного вала
допустимая погрешность измерений составляет δ
= 10 мкм.
2. По таблице придельных погрешностей методов измерения (измерение наружных размеров) находим, что для измерений этого размера
подходит микрометр гладкий ГОСТ 6507 - 78 и головка пружинная 10 ИПГ 6953 - 81,
у которых ∆lim = 5 мкм.
Т. к. гладкий микрометр более эргономичен и с ним легче работать,
принимаем его универсальным мерительным инструментом со специальным покрытием
для защиты рук (ГОСТ 6507 - 78).
Задача №7.
Выбор посадок для
различных соединений заданной сборочной единицы
Требуется подобрать посадки для всех видов соединений, входящих в сборочную единицу, пользуясь методом аналогии или на основе рекомендации литературы.
Можно условно считать, что детали и соединения заданной сборочной единицы в процессе эксплуатации испытывают средние нагрузки и посадки следует принимать при средней точности обработки
сопрягаемых поверхностей.
При выборе посадок так же необходимо правильно выбирать систему посадок и характер соединения.
Посадка крышки на фланец с зазором Ø 70 F7/h6
Посадка подшипника на вал Ø 50 H7/n6
Посадка звездочки на вал Ø 30 K9/h9
Посадка на фланец на шпильках Ø 10 D9/l8
Принятые посадки заносим в таблицу 6.
Таблица 6. Посадки соединений сборочной единицы
Задача №8. Расчет
уровня стандартизации сборочной единицы
Дано: чертеж сборочной единицы и его спецификация.
Определить: уровень стандартизации заданной сборочной единицы.
Уровень стандартизации для данного объекта определяем по формуле:
где: N - общее число деталей в сборочной единице,
Сборочная единица состоит из N = 40 деталей, причем в ней имеется
Подставив данные в формулу, получаем:
Чертеж сборочной единицы с размерами, входящими в размерные цепи
механизма.
1. Выявляем размеры, входящие в размерные цепи, и строим схемы размерных цепей ( рис. 7 ).
Вычерчиваем схемы размерных цепей, одновременно отмечаем увеличивающие и
уменьшающие звенья и размеры.
2. Определяем номинальные размеры замыкающих звеньев цепей:
А ∆ = А 1 - А 2 - А 3 - А 4 =
60-2-6-12 = 40 мм;
ВШ = L + П + Ш= 55 + 25 + 10 = 90 мм
3. Определяем номинальные размеры замыкающих звеньев цепей:
T AΔ = E SAΔ - E iA = 500 - (-500) = 1000 мкм;
4. Определяем точность размерной цепи (методом среднего допуска)
где: Т ср - средний допуск составляющих звеньев
Наиболее точной является размерная цепь №5, с которой и начинаем решение
задачи, затем решаем цепь №3.
5. Решаем прямую задачу методом среднего допуска и квалитета при
условии полной взаимозаменяемости. Решаем
цепь №5.
где: а ср - средняя единица допуска
Пользуясь таблицей 1.8 (3), находим, что полученное значение а = 109
соответствует примерно 11-му квалитету, для которого а = 100.
По той же таблице назначаем стандартные допуски на каждое составляющее
звено, принимая линейные размеры цепи как диаметры:
Сумма допусков составляющих звеньев оказалась меньше заданного допуска
замыкающего звена на 75 мкм, т. е. условие полной взаимозаменяемости не
выполнено.
Для обеспечения полной взаимозаменяемости следует принять для какого-либо
звена нестандартный допуск. Для этой цели наиболее подходящим является звено Б 5 ,
т. е. длина средней части вала, обработка и измерение которой не представляет
затруднений. Т. о. Для звена Б 5 имеем:
Теперь условие полной взаимозаменяемости обеспечено, т. к.
Окончательное значение заносим в таблицу.
6. Назначаем предельные отклонения.
Находим координаты середины поля допуска звена Б 5 , решив
уравнение:
Тогда предельные отклонения звена Б 5 будут:
Полученные значения предельных отклонений звеньев заносим в таблицу 7.
7. Расчитав размерную цепь определяем средний допуск размерной цепи
и назначаем полученное значение допуска на каждое звено цепи, корректируя его
величину с учетом номинальных размеров звеньев, сложности их обработки и
измерений, условий работы и других факторов. Правильн решений проверяем по
формуле:
8. Т. о. Сумма допусков всех составляющих звеньев должна быть равна
допуску замыкающего звена 562. Для этой цели наиболее подходящим является звено
А 5 .
Теперь условие полной взаимозаменяемости обеспечено.
9. Находим координаты середины поля допуска звена А 5 , решив
уравнение:
10. Полученные значения предельных отклонений звеньев заносим в
таблицу 7.
Таблица 7. Параметры звеньев размерных цепей
Задача №10.
Оценка качества
сборочной единицы экспертным методом
подшипник вал калибр стандартизация
Получены следующие оценки качества конструкции, данные 10 экспертами, разбитыми на 3 группы по весомости:
1. Определяем среднюю оценку конструкции:
где: О ср - среднее значение оценки качества конструкции;
О i - единичная оценка качества
экспертом i - ой группы;
К гр - групповой эффект весомости оценки качества ( для 1 - ой
группы - 1; для 2 - ой - 0,9; для 3 - ей - 0,7
);
2. Определяем среднеквадратичное отклонение оценки качества:
где: σ 0
- средне квадратичное отклонение оценки;
- среднее значение оценки качества i - ой группы экспертов;
О ср - среднее значение оценки качества;
3. Определяем стандарт среднеквадратического отклонения:
4. Определяем границы рассеивания среднего значения оценки
качества:
где: t а - коэффициент пограничности, t а = 1,38 при вероятности α = 0,8
5. Определяем относительную ошибку расчета оценки качества
конструкции:
где: ∆а - относительная ошибка точности расчета оценки качества,
которая не должна превышать 20 %, как
установлено ГОСТ;
- верхняя оценка качества конструкции;
ВЫВОД: средняя ошибка оценки сборочной единицы -3,73, определенная по
результатам опроса 10-ти экспертов. При увеличении числа экспертов оценка может
быть повышена до -3,86 или снизится до 3,59.
Похожие работы на - Основы машиностроения Контрольная работа. Другое.
Основные Этапы Развития Социологии Реферат
Реферат по теме Синергетика и Демократия
Налоговая Политика Курсовая Работа
Контрольная работа: Коснтитуция и ее значение в РФ
Сочинение На Английском Моя Любимая Профессия
Проблема Смысла Жизни В Философии Эссе
Реферат: Регулирование региональных рынков. Скачать бесплатно и без регистрации
Контрольная работа по теме Мнемические процессы
1с Предприятия Реферат
Доклад по теме Створення комп’ютерного клубу "ВІРУС" на період 2022-2022 рр.
Реферат: Принцип театрализации в романе Теккерея Ярмарка тщеславия
Летописи – первые письменные источники
Реферат: Педагогический процесс. Скачать бесплатно и без регистрации
Практическое задание по теме Денежное довольствие военнослужащих, проходящих службу по контракту на должностях прапорщиков, рядов...
Реферат: Организация и порядок учета кассовых операций
Курсовая работа по теме История родного села
Сочинение Эссе Бедная Лиза
Реферат по теме Развитие кооперативного движения в Европе
Курсовая работа по теме Инфляция в рыночном хозяйстве
Реферат: Философия истории Р. Дж. Коллингвуда. Скачать бесплатно и без регистрации
Реферат: Маркетинг 24
Реферат: Социальная стратификация
Похожие работы на - Информационные системы бухгалтерского учета