Обработка венца зубчатого. Дипломная (ВКР). Другое.
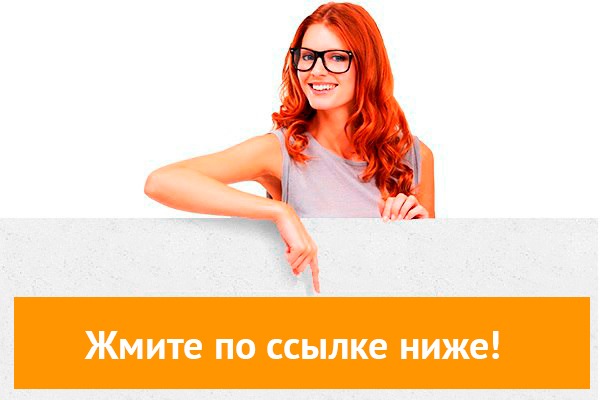
⚡ 👉🏻👉🏻👉🏻 ИНФОРМАЦИЯ ДОСТУПНА ЗДЕСЬ ЖМИТЕ 👈🏻👈🏻👈🏻
Вы можете узнать стоимость помощи в написании студенческой работы.
Помощь в написании работы, которую точно примут!
Похожие работы на - Обработка венца зубчатого
Скачать Скачать документ
Информация о работе Информация о работе
Скачать Скачать документ
Информация о работе Информация о работе
Скачать Скачать документ
Информация о работе Информация о работе
Скачать Скачать документ
Информация о работе Информация о работе
Скачать Скачать документ
Информация о работе Информация о работе
Скачать Скачать документ
Информация о работе Информация о работе
Нужна качественная работа без плагиата?
Не нашел материал для своей работы?
Поможем написать качественную работу Без плагиата!
Успешная реализация конструктивных
решений в большей степени определяется технологией. Проектируемые
технологические процессы должны обеспечивать повышение производительности труда
и качества изделий при одновременном снижении затрат на их изготовление.
Решение этих задач во многом зависит от рационального построения размерных
связей в процессе обработки, обоснованного назначения припусков на обработку
допусков операционных размеров.
Всякое необоснованное установление
допусков на размеры деталей приводит к удорожанию производства. Излишнее
ужесточение допусков вызывает потребность в точном оборудовании и оснастке,
боле точных (а значит, и более дорогих) заготовках. Чрезмерное расширение поля
допуска затрудняет обработку на предварительно настроенных станках и
увеличивает объем пригоночных работ в процессе сборки изделия.
Эффективность технологического
процесса существенно зависит также от рационального выбора припусков.
Чрезмерные припуски влекут за собой перерасход материала и требуют введения
дополнительных технологических переходов, увеличивая расход режущего
инструмента и электроэнергии, трудоемкость обработки и в конечном итоге -
себестоимость продукции. Ввиду высокой стоимости авиационных материалов
уменьшение припусков обычно окупает затраты на изготовление точных заготовок,
однако необоснованно заниженные припуски не обеспечивают удаления дефектной
части поверхностного слоя и достижения заданной точности, увеличивая
вероятность брака.
Даже при сравнительно малых
масштабах производства для получении заготовок деталей применяют такую
обработку давлением, как горячая штамповка, прессование, волочение, чеканка и
т.п. При этом обязательны определенное расположение волокон и надлежащая уковка
материала. Свободная ковка в авиадвигателестроении применяется уже редко.
Высокие требования к качеству материала заставляют применять особые виды
контроля, основанные на применении изотопов и ультразвука.
Для изготовления многих деталей
становится обычным применение различных методов точного литья. Почти все основные
детали двигателей подвергаются термической или термохимической обработке. Это
обстоятельство приводит к усложнению технологического процесса и удлинению
цикла обработки. Выбор места термообработки в плане технологического связан
обычно с целым рядом особых соображений, касающихся как качества детали, так и
возможностей проведения механической обработки.
1.1 Назначение детали,
условия работы
Венец
зубчатый (шестерня внутреннего зацепления) предназначен для
передачи крутящего момента на задний вал дифференциального разомкнутого
редуктора и понижения скорости вращения выходного вала винтовентилятора.
Шестерни относятся к числу наиболее ответственных деталей машин. Существенное
нарушение формы венца из-за высокой радиальной податливости или колебаний, а
тем более разрушение шестерни влечёт за собой выход из строя всей конструкции.
Поэтому к шестерням предъявляют высокие требования по точности изготовления,
прочности, жёсткости, устойчивости и колебаниям.
Конструктивная форма зависит от
нагрузок и способа соединения с валом. При больших вращающих моментах и
повышенных требованиях к центрированию венцы соединяют с валами с помощью
шлицевых соединений.
Технические условия на изготовление
шестерен зависят от требований к конструкции.
Зубья детали работающие в тяжелых
условиях, под действием ударных и знакопеременных нагрузок, поэтому материал
детали должен быть достаточно прочным, иметь пластическую, вязкую сердцевину и
поверхностную твердость. Для достижения поверхностной твердости зубьев
применяется азотирование, которое проходи по поверхности детали.
Деталь образована цилиндрическими
поверхностями и плоскостями. Наивысшая чистота поверхности R a 0,2 мкм - принадлежит поверхностям 18 и 12 низшая R a 1,6 мкм - всем поверхностям, которые не сопрягаются с другими
деталями механизма.
Степень точности зубчатого венца
маховика 5-Bd по ГОСТ 1643-81, а венца колеса 6-Bh по ГОСТ 1643-81.
Материалом детали назначена
конструкционная легированная высококачественная сталь 30Х2Н2ВМФА-Ш. Свойства
материала приведены в таблицах 1.1 и 1.2.
Таблица 1.1 − Химический
состав материала
Таблица 1.2 − Физические
свойства материала при Т=20ºС
Для достижения поверхностной
твердости шестерня подвергается термообработке ТВЧ с достижением твердости HRC 56…58.
2. Определение
показателей технологичности детали
Технологичность детали - это
совокупность свойств детали, обеспечивающих ее высокие эксплуатационные
характеристики при наименьшей трудоемкости и стоимости изготовления.
К анализу технологичности приступают
после назначения типа производства, так как каждому из них свойственны свои
способы получения заготовок и методы их обработки. Качественную оценку
технологичности детали проводят по материалу, геометрической форме, качеству
поверхностей, по простановке размеров и возможным способам получения заготовки.
Количественную оценку проводят по абсолютным и относительным показателям. В
первую очередь устанавливают показатели, такие как: коэффициенты использования
материала, точности обработки, шероховатости поверхности, а также трудоемкость
изготовления, технологическую себестоимость.
Технологичность рассматривается по
двум параметрам: качественная и количественная оценка технологичности.
2.1 Качественная оценка
технологичности
Качественная оценка технологичности
рассматривается в следующих аспектах:
− технологичность по
материалу детали;
− технологичность по
геометрической форме и качеству поверхностей;
− технологичность по
простановке размеров;
− технологичность по способам
и видам механической обработки;
− технологичность
относительно потребности в специальных приспособлениях и технологической
оснастке.
2.1.1 Технологичность по
материалу детали
По материалу [п. 1.2] шестерня имеет
среднюю технологичность ввиду относительно большого содержания углерода и
легирующих элементов, что требует применения соответствующих режущих материалов
при обработке.
2.1.2 Технологичность по
геометрической форме
Данная деталь представляет собой
тело вращения цилиндрической формы переменного диаметра. Вдоль оси вращения
детали выполнено сквозное отверстие так же переменного диаметра. Имеется
наличие ряда нетехнологических поверхностей, обуславливает применение
специального режущего инструмента и оборудования. К таким поверхностям
относятся зубья. Деталь имеет две внутренних зубчатых поверхности. Для их
получения необходимо применять специальные методы обработки, как зубодолбление,
зубошлифование.
Что же касается
технологичности по геометрической формы, то шестерни в этом смысле
нетехнологичны, поскольку операции нарезания зубьев выполняется в основном
малопроизводительными методами. Отношение длины детали к наружному диаметру
невелико, что обеспечивает достаточную жесткость детали при обработке.
Требования точности
формы и расположения поверхностей детали обусловлены необходимостью обеспечить
надежную работу зубчатого зацепления.
2.1.3 Технологичность по
простановке размеров
На чертеже детали конструктором
проставлены собственные размеры детали с учетом отклонений и погрешностей.
Однако они проставлялись с учетом реальных условий изготовления детали, но эти
же базы могут быть использованы в качестве исходных, установочных и
измерительных баз почти на всем протяжении технологического процесса
изготовления детали. Вышеизложенное справедливо, например, для размерных цепей
линейных размеров координирующих взаимное положение торцов корпуса и упорных
торцов детали - т.е. их обработку можно вести в полном согласии с
проставленными размерами (имеется в виду как способ расстановки, так и сами
номиналы и допуски на них). Это отвечает принципу совмещения баз, что позволяет
говорить о технологичности детали по этому параметру.
2.1.4 Технологичность по
способам и видам механической обработки
При изготовлении данной детали
используется достаточное количество разнообразных технологических операций,
которые и позволяют получить из заготовки готовую деталь.
Большую часть поверхностей детали
можно получить токарной обработкой при использовании стандартных резцов разных
видов. Отверстия в теле детали выполняются стандартным инструментом, размещение
их удобно, к ним обеспечены хорошие подходы, т.е. их получение не связано с
какими-нибудь значительными трудностями. В целом деталь можно отнести к
технологичным благодаря небольшой номенклатуре видов механической обработки и
использовании стандартных инструментов.
2.2
Количественная оценка технологичности
Количественная
оценка технологичности производится по следующим показателям:
где Т ср
- среднее значение точности;
n i - количество поверхностей одного квалитета;
Т i - степень точности
соответствующих поверхностей;
К Т - средний коэффициент
точности.
Значения точности
поверхностей взяты из табл. 2, с. 441 [2] и занесены в таблицу 2.1.
Таблица 2.1 −
Точности поверхностей детали
Таким образом,
деталь технологична по показателю точности.
где Ш ср
- среднее значение шероховатости;
n i - количество поверхностей одной шероховатости;
Ш i - шероховатость
соответствующих поверхностей;
К Ш - средний коэффициент
шероховатости.
Таблица 2.2 −
Шероховатости поверхностей детали
Таким образом, деталь
технологична по показателю шероховатости.
− коэффициент
использования материала (КИМ)
где М дет = 20,57
кг - масса детали;
М пок =54,51 кг − масса заготовки-поковки.
3. Выбор и обоснование
метода получения заготовки
3.1 Обоснование
выбранного метода получения заготовки
Заготовка - предмет труда, из
которого изменением формы, размеров, свойств поверхности и (или) материала
изготавливают деталь.
При выборе заготовки для заданной
детали назначают метод ее получения, определяют конфигурацию, размеры, допуски,
припуски на обработку и формируют технические условия на изготовление.
Главным при выборе заготовки
является обеспечение заданного качества готовой детали при ее минимальной
себестоимости.
Технологические процессы получения
заготовок определяются технологическими свойствами материала, конструктивными
формами и размерами детали и программой выпуска.
Факторы, определяющие выбор способа
получения заготовки:
) требуемая точность и качество
поверхностного слоя заготовки;
) технологические свойства материала
заготовки;
) производственные возможности
предприятия.
Учитывая назначения и условия работы
детали, ее конфигурацию, свойства материала и тип производства целесообразно
избрать в качестве метода получения заготовки горячую штамповку.
Горячая объемная штамповка находит
широкое применение в машиностроении, так как дает изготовить поковку с высокими
механическими свойствами и по конфигурации близкую к исходной детали.
Применение метода групповой технологии может обеспечить рентабельность горячей
штамповки даже в условиях мелкосерийного производства.
В первую очередь выбирают такой
способ изготовления заготовок, который полностью обеспечивает заданное качество
детали с учетом условий работы. При наличии нескольких возможных способов выбор
делают исходя из условий обеспечения максимальной производительности труда и
минимальной стоимости изготовления заготовки.
) принципиальная возможность её
получения выбранным способом с учетом физико-механических, химических и других
свойств материала.
) простота внешних форм - это
требование определяется стоимостью оснастки (штампов, литейных форм).
) максимальная приближенность
размеров и формы заготовки к размерам и форме готовой детали.
) однородность внутренней структуры
заготовки, отсутствие пустот, пузырей, каверн, трещин и т.п.
) в случае заготовок, получаемых с
помощью обработки давлением - оптимальное расположение волокон максимально
благоприятствующее восприятию нагрузок на деталь в процессе работы.
) низкая трудоемкость изготовления и
себестоимость.
) возможность форсирования
производства (возможность в короткие сроки увеличить выпуск заготовок).
Штамповка на кривошипных горячештампованных прессах (КГШП) была выбрана
благодаря присущим ей особенностям, благодаря которым становится возможным
изготавливать максимально технологичные заготовки.
При штамповке на КГШП получают
поковки, более близкие по форме к готовой детали, с более точными размерами
(особенно по высоте), чем при штамповке на молотах. Более совершенная
констукция штампов обеспечивает меньшую величину смещения половин штампа,
уменьшение припусков (на 20…30%), напусков, штамповочных уклонов (в 2…3 раза),
допусков и как следствие - увеличение коэффициента использования металла.
Штамповка в открытых штампах на
кривошипных горячештампованных прессах в неразъемных матрицах достигается
применением более точных заготовок, более точной дозировки металла, применением
обычной заготовки и компенсирующего устройства в штампах для размещения излишка
металла (5-10% объема заготовки). Точная дозировка металла для штамповки
связана с дополнительными затратами из-за более сложного инструмента и меньшей
производительности при отрезке. Несмотря на недостатки КГШП (высокая стоимость;
меньшая универсальность; худшее заполнение глубоких полостей из-за малой
скорости деформации; более сложная конструкция; регулировка и эксплуатация
штампов) КГШП очень хорошо подходит к особенностям такой отрасли промышленности
как авиадвигателестроение.
Чертёж поковки составляют по чертежу
готовой детали. При этом надлежит установить разъём штампов и назначить
припуски и допуски, определить штамповочные уклоны, радиусы закруглений, а
также установить форму и размеры наметок отверстий и перемычек под прошивку.
К основным факторам, определяющим
величины допусков и припусков относятся прежде всего технологические свойства
штампуемых сплавов, габаритные размере (или масса) и форма поковки.
Штамповочные уклоны необходимы для
облегчения удаления поковки из ручья. Однако их величина (отклонение по
вертикали) должна быть минимальной, так как её уменьшение способствует снижению
массы поковки, уменьшению напуска, облегчению заполнения окончательного ручья и
увеличению его стойкости.
Острые кромки на поверхности поковки
необходимо закруглить. При закруглении этих кромок радиусами недостаточной
величины концентрация напряжений в соответствующих углах окончательного ручья
при работе штампа ведёт к быстрому образованию в нём трещин. Вместе с тем
затекание металла в углы резко затруднено и требует повышенного давления при
штамповке.
Значения радиусов закругления
внешних углов (так называемых наружных радиусов закруглений) установлены ГОСТ
7505-74 в пределах 0,8-8,0 мм в зависимости от массы поковки в пределах до 200
кг.
3.2 Определения точности
размеров заготовки
Для определения точности размеров
заготовки необходимо определить следующие параметры:
− группа обрабатываемого
материала: по содержанию углерода и легирующих элементов сталь 30Х2Н2ВМФА-Ш
относится к группе М3;
− степень точность поковки по формуле:
где −
масса простой фигуры, в которую вписывается поковка;
ρ =
7900 кг/м 3 − плотность стали 30Х2Н2ВМФА-Ш;
D max = 0,625 м −максимальный диаметр поковки;
Степень сложности
поковки относится к С 3 .
Таблица 3.1 −
Допуски основных размеров поковки
4. Расчет числа
технологических переходов обработки основных поверхностей детали
Число переходов,
необходимое для обработки каждой из поверхностей детали и их состав по
применяемым методам обработки определяются соотношением характеристик точности
размеров, формы и шероховатости одноимённых поверхностей исходной заготовки и
готовой детали.
При определении
необходимого и достаточного количества ступеней обработки отдельных
поверхностей для обеспечения заданных характеристик точности формообразующих
размеров, формы и качества поверхности с достаточной для практических целей
точностью, воспользуемся зависимостями:
1) число ступеней
обработки, необходимое для обеспечения заданной точности:
где Т заг
- допуск размера заготовки, мкм [табл. 3.1];
Т дет - допуск размера детали, мкм [табл. 2, с. 441 [2]].
2) число ступеней
обработки, необходимое для обеспечения заданной шероховатости:
где Ra заг - шероховатость
поверхности заготовки, мкм;
Ra дет - шероховатость поверхности готовой детали, мкм.
Для торцевых и
конических поверхностей расчет потребного числа переходов производится только
по шероховатости ввиду отсутствия допусков на эти поверхности.
Число потребного количества ступеней
обработки принимаем исходя из следующих факторов:
. Увеличение ступеней обработки
приводит к уменьшению доли общего припуска, снимаемого на каждой операции в
отдельности, что в свою очередь приводит к разгрузке оборудования, увеличению
стойкости режущего инструмента, улучшению процесса резания.
. В свою очередь меньшее количество
ступеней обработки требует меньшего количества оборудования, меньшее количество
людей, значительно упрощается техпроцесс и уменьшается время на обработку.
Исходя из этих
соображений будем намерено завышать количество операций для наиболее
ответственных поверхностей. Для наименее ответственных поверхностей, будем
намеренно занижать количество операций. Разбивку точности проводим исходя из
метода обработки.
Для поверхности №3
[рис. 2.1] имеем:
Принимаем ближайшее
целое число для большего, т.е. n = 5.
5.
Разработка предварительного плана технологического процесса
венец зубчатый
редуктор технологический
Исходными данными
для разработки маршрутного технологического процесса изготовления детали
являются заданный чертеж детали и тип производства.
При проектировании
маршрутного технологического процесса необходимо разработать графический план
обработки заготовки, установить состав и последовательность операций, указав
для каждой операции обрабатываемые поверхности, методы их обработки и
характеристики точности, схемы установок и позиции, тип оборудования.
Для проектирования
плана обработки рациональна определенная последовательность решений:
− составление
укрупненного плана обработки заготовки, устанавливающего рациональную
последовательность формообразующих операций, а также наличие и место в плане
обработки термических, контрольных и других вспомогательных операций;
− выявление
конструкторских баз расположения поверхностей и отсчета координатных размеров
связей с ними исходных поверхностей заготовки и необрабатываемых поверхностей
детали.
5.1
Описание структурной схемы технологического процесса
Весь план обработки
состоит из четырех этапов: черновой, получистовой, чистовой и отделочный.
Кратко рассмотрим каждый из них.
. Черновой этап
состоит из черновых операций, на которых снимается до 60-70% припуска на
обработку. На этом этапе достигается равномерное распределение припусков на
дальнейшую обработку, и удаляются дефекты на поверхности заготовки.
. Получистовой этап
обработки выполняется, как правило, в той же последовательности, что и черновая
обработка, но более точно, с меньшими режимами резания, при этом устраняют
коробление, возникшее после первого этапа.
. На чистовом этапе
снимается до 30% припуска, и детали придается окончательная форма.
. Отделочный этап
включает операции, обеспечивающие заданную точность и чистоту рабочей
поверхности. Выполняется, как правило, после термообработки, если она имеет
место в технологическом процессе.
5.2
Выбор и обоснование технологических баз
База − это
поверхность или выполняющее ту же функцию сочетание поверхностей, ось или
точка, принадлежащая заготовке (детали) и используемая для базирования.
На чертеже детали
конструктором проставлена одна конструкторская база. Также имеется точно
обработанная цилиндрическая поверхность, которая имеет жесткие допуски и одна
торцевая поверхность с жестким допуском по радиальному биению относительно
базы. Таким образом, имеем три поверхности, которые могут быть использованы в
качестве технологических баз. Исходя из соображений удобства закрепления
заготовки на станке, выбираем за базы поверхности вершин зубьев 2 и 13.
Также необходимо
выбрать торцевые поверхности, которые будут служить упорами при обработке.
Принимаем сопряженные с базами поверхности торцов 1 и 10.
Таким образом,
имеем 2 комплекта технологических баз:
− левый
комплект баз: наружная цилиндрическая поверхность 2 и торец 1;
− правый
комплект баз: внутренняя цилиндрическая поверхность 13 и торец 10.
Для большинства
операций соблюдается принцип совмещения и постоянства баз, и такие базы
называются чистыми. Исключение составляют первые операции, на которых базы
уступают по точности и качеству обрабатываемым поверхностям. Это черновые базы,
которые могут быть использованы только один раз и для координации только одной
из обрабатываемых поверхностей. То есть обработку детали начинаем с той
поверхности, которая будет служить установочной базой для дальнейших операций.
Обработку
поверхностей точным взаимным расположением включаем в одну операцию, и
выполняем за одно закрепление заготовки. А черновую и чистовую обработки
заготовок со значительными припусками выделяем в отдельные операции, так как
совмещение черновых и чистовых переходов в одной операции приводит к снижению
точности обработки вследствие повышенного износа инструмента на черновых
операциях.
План обработки
строим так, чтобы последними обрабатывались поверхности, к которым
предъявляются повышенные требования по точности, а в начале те поверхности, к
точности которых предъявлены меньшие требования. При определении
последовательности переходов операции, предусматриваем опережающее выполнение
тех переходов, которые подготавливают возможность осуществления следующих за
ними переходов.
6. Расчет припусков и
операционных размеров на диаметральные поверхности
Выполним расчет
припусков расчетно-аналитическим методом, суть которого описана в пособии [3, с. 10-24, с. 68-72].
Величину
минимального припуска на диаметральные поверхности определяют по формуле:
где Rz i -1 и h i -1 - соответственно
шероховатость и глубина дефектного слоя на предыдущей ступени обработки, мкм;
Δ i -1 - величина суммарных пространственных отклонений на предыдущей
ступени обработки, мкм;
ε i - погрешность установки
детали в данной ступени обработки, мкм.
Величина суммарных
пространственных отклонений определяется по формуле:
где Δ кор - величина коробления
поковки, мкм;
Δ см - величина смещения
поковки, мкм.
Величина
пространственных отклонений в процессе обработки полностью не исчезает, а
значительно уменьшается по величине. Величина остаточных отклонений
определяется по величине коэффициента уточнения формы:
где К у
- коэффициент уточнения формы.
Номинальный припуск
определяется по формуле:
где T i -1 - допуск размера на предыдущей обработке, мкм.
Максимальный
припуск определяется для отверстия и вала отдельно:
Расчетный диаметр
определяется для отверстия и вала отдельно:
Технологический операционный размер
на каждой ступени обработки записывается как номинальный размер с допуском. При
этом, в случае обработки охватывающих поверхностей в качестве номинального
выступает минимальный размер, а в случае охватываемых - максимальный.
Технологический размер заготовки
записывается как номинальный размер заготовки с соответствующим допуском.
Для остальных
поверхностей расчет проводим нормативным методом, в котором минимальный
расчетный припуск 2 Z min . p принимается из таблицы П. 5.1 [3]. Остальные расчеты аналогичны
описанным выше.
7.
Расчет припусков и операционных размеров на обработку торцевых поверхностей
7.1
Определение минимальных припусков расчетно-аналитическим методом
Расчет проводится
аналогично разделу 6. Величину минимального припуска на обработку торцевой
поверхности определяют по формуле:
где Rz i -1 и h i -1 - соответственно
шероховатость и глубина дефектного слоя на предыдущей ступени обработки;
Δ i -1 - величина пространственных отклонений на предыдущей ступени
обработки;
ε i - погрешность установки
детали в данной ступени обработки.
Результаты расчета минимальных
припусков на обработку торцевых поверхностей расчетно-аналитическим методом
сведены в таблицу 7.1.
Таблица 7.1 − Расчет
минимальных припусков на торцевые поверхности
Расчетный припуск 2 Z min . p , мкм
7.2 Разработка и анализ
размерной схемы обработки торцевых поверхностей детали
Расчёт линейных операционных
размеров начинают с построения размерной схемы технологического процесса.
Основой для построения схемы служит план технологического процесса.
Размерную схему необходимо строить,
располагая эскизами плана обработки детали, следующим образом. Вычерчивают
контур готовой детали, утолщёнными линиями указывают координаты торцов
поверхностей в соответствии с координацией размеров на рабочем чертеже.
С учётом количества обрабатываемых
торцевых поверхностей на эскизе детали условно показывают операционные припуски
вплоть до соответствующего размера заготовки. Затем все исходные, промежуточные
и окончательные торцевые поверхности нумеруются слева направо.
Через пронумерованные поверхности
проводятся вертикальные линии. Между вертикальными линиями, начиная с
последующей операции, с учётом эскизов обработки, указывают технологические
размеры (обозначаем S n ). Размер представлен в виде стрелок с точкой, причём точка
совмещена с установочной базой, а стрелка своим остриём упирается в ту
поверхность, которую мы получили на данной операции, после снятия
соответствующего межоперационного припуска.
После построения размерной схемы мы
можем составить размерные цепи. В качестве замыкающих звеньев выступают
конструкторские размеры или размеры припусков, в качестве составляющих, искомых
звеньев, выступают операционные размеры, которые функционально связывают
торцевые поверхности на всех операциях от заготовительной до окончательной.
7.3 Расчет
технологических размерных цепей торцевых поверхностей детали
Выявление и расчет технологических
размерных цепей начинают с двухзвенных цепей. А затем в такой
последовательности, чтобы в каждой цепи имелось только одно неизвестное звено.
Остальные звенья уже определены расчетом предыдущих размерных цепей. Для
выполнения этого условия необходимо начинать выявление и расчет цепей в
последовательности, обратной выполнению операций в технологическом процессе
изготовления шестерни.
Любой замкнутый контур на размерной
схеме, включающий в себя только один конструкторский размер или один припуск,
образует технологическую размерную цепь.
Определив Z i - jmin составляем
исходные уравнения размерных цепей относительно Z i - jmin :
где Х r min - наименьший
предельный размер увеличивающего звена размерной цепи;
Х q max - наибольший
предельный размер уменьшающего звена размерной цепи;
Обозначим определяемый операционный
размер Х Х , тогда если искомый размер является уменьшающим
звеном, получаем:
а если искомый размер
является увеличивающим звеном, то:
Определив величины X X max , X X min на размеры Х Х , устанавливаем допуск на
операционный размер δ Х .
7.4 Проектирование
чертежа заготовки
Метод выполнения заготовки для
деталей машин определяется назначением и конструктивными особенностями детали,
материалом, технологическими требованиями. Выбор заготовки определяет метод ее
получения и припуски на ее изготовление. Припуск представляет собой слой
металла, подлежащий в процессе обработки удалению, чем обеспечиваются необходимые
размеры, класс точности и величины шероховатости поверхности. Установление
оптимальных припусков является важнейшим технологическим показателем.
Для разработки чертежа поковки и
операции штамповки используются следующие исходные данные:
1. Материал детали: сталь
30Х2Н2ВМФА-Ш 4543-71.
2. Точность изготовления
поковки: для уменьшения величины снимаемого припуска при обработке принимаем І класс точности
заготовки.
. Группа стали - М3,
поскольку поковка изготавливается из среднелегированной стали с содержанием
углерода выше 0,4% и легирующих элементов более 2% [с. 145 [1]].
. Конфигурация поверхности
разъема штампа - плоская (П).
. Степень сложности - С3 [п. 3.2].
Заготовку получаем штамповкой на
горизонтально-ковочной машине. Максимально допустимые штамповочные уклоны по
ГОСТ 7505-55 составляют 5˚ для наружных и 7˚ для внутренних стенок
поковки. Однако, если возможно, эти уклоны необходимо уменьшать в целях
снижения веса детали и расхода материала, уменьшения механической обработки,
облегчения заполнения окончательного ручья и увеличения его стойкости.
Для упрощения изготовления ручьев и
унификации режущего и измерительного инструмента рекомендуется применять
следующий ряд штамповочных уклонов: 3; 5; 7 и 10˚, хотя допустимо
использование уклонов 1,5 0 , 2,5 0 .
Значения радиусов закруглений
внешних углов (наружных радиусов закруглений) рекомендованы ГОСТом 7505-55 в
пределах 0,8-10 мм в зависимости от массы поковок. Для поковок массой до 63 кг
Похожие работы на - Обработка венца зубчатого Дипломная (ВКР). Другое.
Что Для Меня Значит Родина Мини Сочинение
Сочинение На Тему Русские Басни
Реферат На Тему Оренбург
Реферат: Понятия о интродукции и аклиматизации
Отчет По Производственной Практике По Профессии Автомеханик
Реферат: Безопасность жизнидеятельности. Скачать бесплатно и без регистрации
Курсовая работа по теме Сущность и особенности конного туризма на примере европейского региона
Сочинение На Тему Проблема Двуличия Людей
Реферат: Політичне управління та його соціотехніка
Реферат На Тему Transnational Corporations
Курсовая Работа На Тему Безработица И Ее Последствия
Реферат: Украинская линия
Мой Родной Край Сочинение 2 Класс
Контрольная работа по теме Адвокатура України
Курсовая работа по теме Литературные источники цикла очерков И. А. Бунина 'Тень Птицы'
Сенина Огэ 2022 Ответы На Сочинения
В Чем Трагичность Жизни Обломова Сочинение
Реферат: Финансовое состояние предприятия и проблемы управления им
Эссе Про Горы Казахстана На Казахском Языке
Реферат по теме Высшее образование в России во второй четверги XIX века
Реферат: Romeo Essay Research Paper Romeo
Доклад: Республиканский политический идеал Ж Ж Руссо
Курсовая работа: Планирование кредитных ресурсов банка и анализ их использования на предприятии