Nylon 6
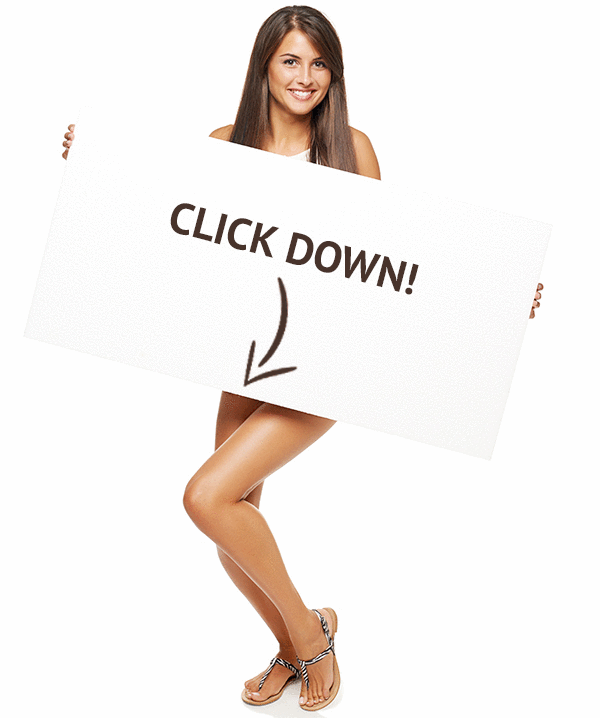
⚡ 👉🏻👉🏻👉🏻 INFORMATION AVAILABLE CLICK HERE 👈🏻👈🏻👈🏻
Nylon 6 or polycaprolactam is a polymer developed by Paul Schlack at IG Farben to reproduce the properties of nylon 6,6 without violating the patent on its production. (Around the same time, Kohei Hoshino at Toray also succeeded in synthesizing nylon 6.) It is a semicrystalline polyamide. Unlike most other nylons, nylon 6 is not a condensation polymer, but instead is formed by ring-opening polymerization; this makes it a special case in the comparison between condensation and addition polymers. Its competition with nylon 6,6 and the example it set have also shaped the economics of the synthetic fiber industry. It is sold under numerous trade names including Perlon (Germany), Dederon (former East Germany),[1] Nylatron, Capron, Ultramid, Akulon, Kapron (former Soviet Union and satellite states), and Durethan.
Poly(azepan-2-one); poly(hexano-6-lactam)
Poly[azanediyl(1-oxohexane-1,6-diyl)]
Polycaprolactam, polyamide 6, PA6, poly-ε-caproamide, Perlon, Dederon, Capron, Ultramid, Akulon, Nylatron, Kapron, Alphalon, Tarnamid, Akromid, Frianyl, Schulamid, Durethan, Technyl, Nyorbits ,Winmark Polymers
Except where otherwise noted, data are given for materials in their standard state (at 25 °C [77 °F], 100 kPa).
Nylon 6 can be modified using comonomers or stabilizers during polymerization to introduce new chain end or functional groups, which changes the reactivity and chemical properties. It is often done to change its dyeability or flame retardance.[2] Nylon 6 is synthesized by ring-opening polymerization of caprolactam. Caprolactam has 6 carbons, hence Nylon 6. When caprolactam is heated at about 533 K in an inert atmosphere of nitrogen for about 4–5 hours, the ring breaks and undergoes polymerization. Then the molten mass is passed through spinnerets to form fibres of nylon 6.
During polymerization, the amide bond within each caprolactam molecule is broken, with the active groups on each side re-forming two new bonds as the monomer becomes part of the polymer backbone. Unlike nylon 6,6, in which the direction of the amide bond reverses at each bond, all nylon 6 amide bonds lie in the same direction (see figure: note the N to C orientation of each amide bond).
Nylon 6 (above) has a structure similar to Nylon 6,6 (below).
Nylon 6 fibres are tough, possessing high tensile strength, as well as elasticity and lustre. They are wrinkleproof and highly resistant to abrasion and chemicals such as acids and alkalis. The fibres can absorb up to 2.4% of water, although this lowers tensile strength. The glass transition temperature of Nylon 6 is 47 °C.
As a synthetic fiber, Nylon 6 is generally white but can be dyed in a solution bath prior to production for different color results. Its tenacity is 6–8.5 gf/D with a density of 1.14 g/cm3. Its melting point is at 215 °C and can protect heat up to 150 °C on average.[3]
Flavobacterium sp. [85] and Pseudomonas sp. (NK87) degrade oligomers of Nylon 6, but not polymers. Certain white rot fungal strains can also degrade Nylon 6 through oxidation. Compared to aliphatic polyesters, Nylon 6 has poor biodegradability. Strong interchain interactions from hydrogen bonds between molecular nylon chains is said to be the cause by some sources.[4]
At present, polyamide 6 is the most significant construction material used in many industries, for instances in automotive industry, aircraft industry, electronic and electrotechnical industry, clothing industry and medicine.[dubious – discuss] Annual demand for polyamides in Europe amounts to a million tonnes. They are produced by all leading chemical companies.
The largest producers of polyamide 6 in Europe:[5]
^ Rubin, E. (2014), Synthetic Socialism: Plastics and Dictatorship in the German Democratic Republic. The University of North Carolina Press. ISBN 978-1469615103
^ "Synthesis of Modified Polyamides (Nylon 6)", NPTEL (National Programme On Technology Enhanced Learning), retrieved May 9, 2016
^ ”Polyamide Fiber Physical and Chemical Properties of Nylon 6”, textilefashionstudy.com, retrieved May 9, 2016.
^ Tokiwa, Y.; Calabia, B. P.; Ugwu, C. U.; Aiba, S. (2009). "Biodegradability of Plastics". International Journal of Molecular Sciences. 10 (9): 3722–42. doi:10.3390/ijms10093722. PMC 2769161. PMID 19865515.
^ "Segment Tworzywa 2015" (PDF) (in Polish). static.grupaazoty.com. Retrieved 2016-04-12.
^ "Alphalon™ (PA6)" (in Polish). att.grupaazoty.com. Retrieved 2016-04-12.
^ "Grupa Azoty: Nowa wytwórnia pozwoli zająć pozycję 2. producenta poliamidu w UE" (in Polish). wyborcza.biz. Retrieved 2016-04-12.
Content is available under CC BY-SA 3.0 unless otherwise noted.
Nylon 6 is the best known application and lends itself well to reactive processing, for example, NYRIM, a variant patented by DSM.
Many Ultramid® resins are suitable for outdoor applications. The unreinforced stabilized Ultramid® resins (i.e., those with the letters K and H in the nomenclature type) are extremely resistant to weathering, even if they are uncolored. The outdoor performance can be further improved by the use of suitable pigments, the best effects being achieved with carbon black. For instance, seats that have been produced from Ultramid® B3K and B35K containing special UV stabilizers and have been exposed for more than ten years in an open-air stadium have remained unbreakable, and their appearance has undergone hardly any change.[73]
Thin articles for outdoor use should be produced from Ultramid® resins with a high carbon black content (e.g., the Black 20590 and 20592 types) to ensure that their strength remains undiminished. Moldings with a high proportion of carbon black can also withstand several years of exposure to tropical conditions.[73]
Housings for automobile rear-view mirrors are examples of articles that must remain attractive for many years. In this type of application, the best results have been obtained with products containing special UV stabilizers and products with a high carbon black content (e.g., Ultramid® B35EG3 Black 20590).[73]
Table 20-1.. Mechanical Properties Retained after Outdoor Weathering Exposure in Florida for BASF Capron® Nylon 6
Table 20-2.. Mechanical Properties Retained after Outdoor Weathering Exposure in California and Pennsylvania for LNP Engineering Plastics® Nylon 6
Graph 20-1.. Elongation at Break after Outdoor Exposure for Ube Ube® Nylon 6.
Graph 20-2.. Flexural Modulus after Outdoor Exposure for Ube Ube® Nylon 6.
Graph 20-3.. Notched Izod Impact Strength after Outdoor Exposure for Ube Ube® Nylon 6.
Graph 20-4.. Tensile Strength after Outdoor Exposure for Ube Ube® Nylon 6.
Graph 20-5.. Flexural Strength at Break after Outdoor Exposure in Hiratsuka, Japan, for Nylon 6.
Graph 20-6.. Flexural Modulus after Outdoor Exposure in Hiratsuka, Japan, for Nylon 6.
Graph 20-7.. Notched Izod Impact Strength after Outdoor Exposure in Hiratsuka, Japan, for Nylon 6.
Graph 20-8.. Weight Change after Outdoor Exposure in Hiratsuka, Japan, for Nylon 6.
Graph 20-9.. Flexural Strength after Outdoor Exposure in Hiratsuka, Japan, for Nylon 6.
Graph 20-10.. Tensile Strength after Outdoor Exposure in Hiratsuka, Japan, for Nylon 6.
Graph 20-11.. Elongation after Sunshine Weatherometer Exposure of Nylon 6.
Graph 20-12.. Tensile Strength after Sunshine Weatherometer Exposure of Nylon 6.
URL: https://www.sciencedirect.com/science/article/pii/B9780815515258500245
XUE-CHAO HU, H.H. YANG, in Comprehensive Composite Materials, 2000
Nylon 6 fiber is produced in two general product types: the regular type for textile uses and the high-strength type for industrial uses. Most nylon 6 is produced in the form of filament yarns and staple fiber yarns for the manufacture of carpets, tire cords, apparel, hosiery, upholstery, seat belts, parachutes, ropes, and industrial cords. This wide spectrum of application can be attributed to the particular combination of fiber properties (Lim et al., 1989; Moncreff, 1975) as shown in Table 1 (Cook, 1984).
Table 1. Typical properties of nylon 6 fiber.
Nylon 6 typically exhibits a glass transition temperature of 48°C and a melt temperature of 214°C. It has a density of 1.14 g cm−3. Nylon 6 filaments have a smooth surface and are as featureless as glass rods. Nylon 6 has an outstanding resistance to abrasion.
The tensile strength of nylon 6 may be varied by adjustment of the manufacturing conditions. In general, the greater the degree of stretch during drawing, the higher the tenacity and the lower the elongation. Regular nylon 6 fiber has a tenacity of 4.4–5.7cN dtex−1 and initial modulus of 1.96–4.41 GN m−2. These tensile properties are quite adequate for textile applications. High-strength nylon fiber for industrial application has a tenacity of and initial modulus of 2.75-5.00 GN m−2. Relatively high fiber strength and initial modulus are necessary for reinforcing applications such as tires and composites.
At low temperatures nylon 6 retains its strength well. There is, in fact, a slight gain in tensile strength after exposure of nylon 6 to low temperatures. The fiber regains its original strength when returned to room temperature. On the other hand, nylon 6 loses strength with increasing temperature. The tensile strength is regained when the fiber is returned to room temperature. However, prolonged exposure of nylon 6 to air at elevated temperatures can cause permanent loss in breaking strength, elongation, and toughness. The fiber discolors with yellowing to some extent.
Nylon 6 is a highly elastic fiber in that it will recover its original dimensions after being deformed by the application of a stress. A typical filament has an elastic recovery of 100% up to an extension of 6–8%. Recovery from 10% extension is about 85%, only part of it being instantaneous and the remainder taking place over several hours.
Nylon 6 melts when heated above 215°C and the molten polymer tends to drip. Fabrics of nylon 6 do not normally support combustion on their own, but their flammability may be increased by the presence of certain chemical finishes and dyes.
On prolonged exposure to light, nylon 6 suffers some loss of strength, with superficial yellowing and a general deterioration of other fiber properties. The degree of deterioration due to light is affected by many factors, of which the following are important: (i) transparency of fiber; bright nylon 6 is more resistant than dull nylon 6; (ii) yarn count: yarns of higher count are more resistant than those of lower count.
Some materials have a permanent effect on nylon 6 fiber, e.g., 3% solution of oxalic acid in water at 99°C for 3 h causes a loss of almost 30% strength and elongation in nylon 6 yarn. There are some solvents for nylon 6 such as (i) concentrated formic acid, e.g., 50% formic acid solution at 80°C, (ii) concentrated hydrochloric, nitric, and sulfuric acids, (iii) 25% solution of zinc chloride in methanol at 50°C, and (iv) phenol and phenolic compounds. Most of the common bleaches cause some degradation in nylon 6.
Nylon 6 yarns heated in dry air for 5 h at 150°C undergo deterioration, losing brightness and becoming yellow. The relatively low melting point of nylon 6 means that it may not be used at elevated temperatures. At temperatures below its melting point, on the other hand, nylon 6 has a somewhat better resistance to prolonged heating. This can be an important factor in some applications, e.g., tires, where the fibers must withstand elevated temperatures.
The capacity of nylon 6 to undergo static electrification is due to its low moisture regain and high electrical resistivity. The dielectric constant of dry nylon 6 is 3.7 at 105 Hz and 20°C. The surface resistance is 2.0×1012 MΩ and the specific resistance 2.6×108 MΩ.
Nylon 6 is absolutely free of all toxic properties, and is chemically inert. It will not cause irritation to the skin.
The increased affinity of nylon 6 for some types of dyestuff makes for greater versatility in dyeing, with the possibility of producing brighter, deeper prints.
Nylon 6 has a better fatigue resistance than nylon 6,6, and this is important in applications such as tires, where the fiber is subjected to repeated stresses.
Nylon 6 fiber tends to shrink more in boiling water than similar types of nylon 6,6. There is a slight amount of lateral swelling of nylon 6 fiber in water, but the length remains almost unaffected.
URL: https://www.sciencedirect.com/science/article/pii/B0080429939000607
Von Moody, Howard L. Needles Ph.D., in Tufted Carpet, 2004
Nylon 6 is produced by ring-opening chain growth polymerization of caprolactam in the presence of water vapor and an acid catalyst at the melt. After removal of water and acid, the nylon 6 is melt spun at 250°–260°C into fibers. Nylon 6,6 is prepared by step growth polymerization of hexamethylene diamine and adipic acid. After drying, the nylon 6,6 is melt spun at 280°–290°C into fibers. Both nylon 6 and 6,6 are drawn to mechanically orient the fibers following spinning.
The degree of polymerization of nylon 6 and 6,6 molecules varies from 100 to 250 units. The polyamide molecular chains lay parallel to one another in a “pleated sheet” structure with strong hydrogen bonding between amide linkages on adjacent molecular chains. The degree of crystallinity of the nylon will depend on the degree of orientation given to the fiber during drawing. Nylon fibers are usually rodlike with a smooth surface or are trilobal in cross section (Figs. 3.2 and 3.3). Multilobal (star) cross sections and other complex cross sections are also found.
Figure 3.2. Nylon 6,6, round × 1900.
Figure 3.3. Nylon 6,6, trilobal × 1200.
URL: https://www.sciencedirect.com/science/article/pii/B978188420799050004X
Both nylon 6 and nylon 66 have been used in a range of applications interchangeably depending on local availability. For industrial grade applications, differences between nylon 6 and nylon 66 become apparent. Comparative relaxation behavior of these two classes of high tenacity nylon filaments is described, based on dynamic mechanical behavior and morphological parameters [34]. Tan Δ peak for nylon 66 is at ~99°C and for nylon 6 it is at 88°C. Due to lower Tg, the heat generation builds up faster from room temperature for nylon 6 than that for nylon 66. Nylon 6 also has higher loss peak height than that of nylon 66, whereas nylon 66 has broader loss peak than nylon 6. Nylon 6 also has slightly lower crystallinity than that of nylon 66. The higher loss peak along with other factors indicates greater heat generation for nylon 6. Nylon 66 has higher thermal stability due to higher melting temperature as compared to nylon 6. These factors combine together to make nylon 66 filaments superior in demanding industrial applications. For these reasons, applications such as airplane tires are made entirely from nylon 66 cords. These observations are supported by morphology data as given in Table 2.3 and these differences relate to crystallinity, integral breadth in amorphous orientation, long period and size of amorphous domains.
Table 2.3. Comparison of morphological factors for highly drawn nylon 6 and nylon 66 filaments
URL: https://www.sciencedirect.com/science/article/pii/B978184569298850002X
M. Kato, A. Usuki, in Polymer Nanocomposites, 2006
Nylon 6-clay hybrid (NCH) is synthesized by the ‘monomer intercalation’ method, in which clay is first ion-exchanged using an organic compound in order for the monomer to intercalate into the layers of the clay. The monomers that form the intercalated layer become a polymerized interlayer. The basic concept of the technique is as follows. Nylon 6 is produced by the ring-opening polymerization of ∊-caprolactam. This can occur in the presence of clay, after ∊-caprolactam intercalates into a clay gallery so that the silicate layers are dispersed uniformly in the nylon 6 matrix. Usuki and his colleagues found that organophilic clay that had been ion-exchanged with 12-aminododecanoic acid could be swollen by molten ∊-caprolactam (the basal spacing expanded from 1.7 nm to 3.5 nm) (Usuki, 1993a). ∊-caprolactam was then polymerized in the clay gallery and the silicate layers were dispersed in nylon 6 to yield a nylon 6-clay hybrid (NCH) (Usuki, 1993b). This is the first example of an industrial clay-based polymer nanocomposite. Figure 1.1 shows a schematic representation of the polymerization.
1.1. Schematic diagram of polymerization to NCH.
The modulus of NCH increased to 1.5 times that of nylon 6, the heat distortion temperature increased to 140°C from 65°C, and the gas barrier effect was doubled at a low loading (2 wt.%) of clay (Kojima, 1993a).
URL: https://www.sciencedirect.com/science/article/pii/B9781855739697500015
Although Nylon 6 and Nylon 6,6 are the most commonly seen polyamides, all of the various Nylons, including 8, 11, 12, 6-9, and 6-10 have been studied extensively.32 Polyamides are made using either a single monomer with an acid group on one end and an amine on the other, or two monomers, one with two acidic ends and the other with two amino ends. For the diacid, adipic acid is used frequently (in polyesters and polyester type polyurethanes also) and this part of the molecule produces cyclopentanone. Other typical products include nitriles and dinitriles form the diamine section. When a single monomer is used, like Nylon 6 (polycaprolactam) the main degradation path is unzipping to monomer. Fig. 16 shows a pyrogram of Nylon 6, with caprolactam eluting at about 12 min. Nylon 6-6 would produce nitriles, including hexane dinitrile, and cyclopentanone, in addition to many other peaks, making the distinction between Nylon 6 and Nylon 6-6 quite easy.
Fig. 16. Nylon 6 pyrolyzed at 750°C.
URL: https://www.sciencedirect.com/science/article/pii/B9780124095472114477
ASHWINI KUMAR AGRAWAL, MANJEET JASSAL, in Polyesters and Polyamides, 2008
Nylon 6 may be modified during the polymerization with comonomers or stabilizers to introduce new functional groups or chain end groups and thus change the reactivity and chemical properties such as dyeability. In addition, the polyamide fibres can also be subjected to a variety of treatments including chemical, grafting, radiation, and plasma which alter the surface characteristics of these polymers.
Various nylon 6 nanocomposite polymers have been synthesized by in situ polymerization ɛ-caprolactam in the presence of nanomaterials.18–21 Nylon 6/nano-TiO2 and nylon 6/nano-Al2O3 composites have excellent photooxidative degradation resistance.18,19 In the presence of pristine and carboxylated multi-walled carbon nanotubes (MWNT and MWNTCOOH) both the storage modulus (E‘) and glass transition temp. (Tg) of the PA6/ CNTs composites increase significantly.20,21
URL: https://www.sciencedirect.com/science/article/pii/B9781845692988500043
Besides nylon 6, there are several kinds of nylon resins like nylon 66, nylon 610, nylon 12, nylon 11, and nylon 46. The synthesis of NCH was realized by polymerizing monomer between
Mommy Store
Hairy Little Teen Porno Video
Porn Cute Hard Orgasm
Tinder Milf Sex
Porno Art Funny
Nylon 6 - Wikipedia
Nylon 6 - an overview | ScienceDirect Topics
nylon-6 - это... Что такое nylon-6?
nylon-6 - это... Что такое nylon-6?
Nylon 6 (PA) — Polyamide 6 - RTP Company
Nylon 6 | Materials Hub
Nylon 6/6 - это... Что такое Nylon 6/6?
Nylon 6


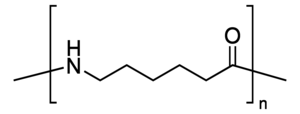





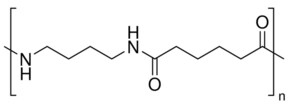
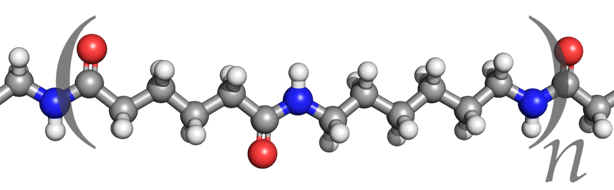




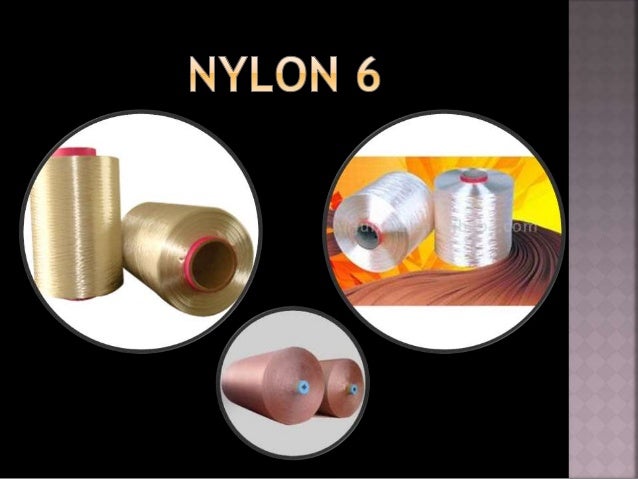
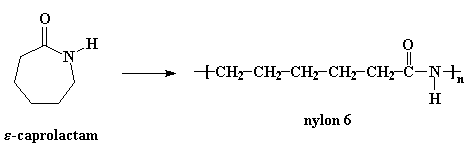

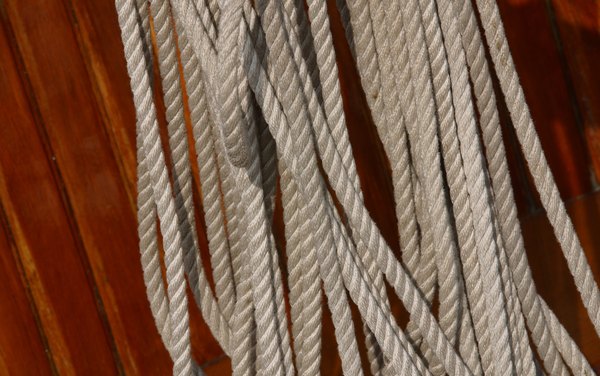
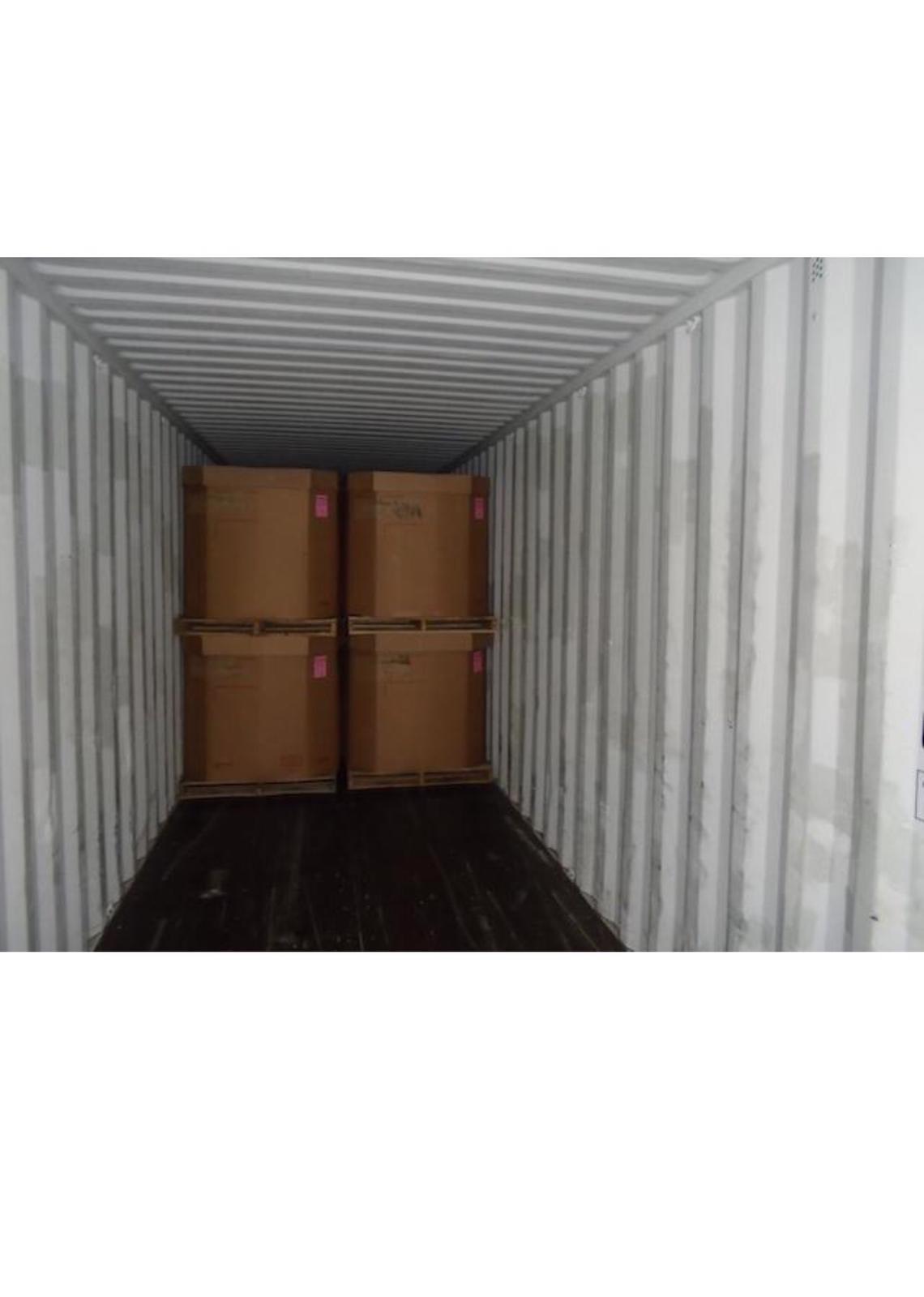





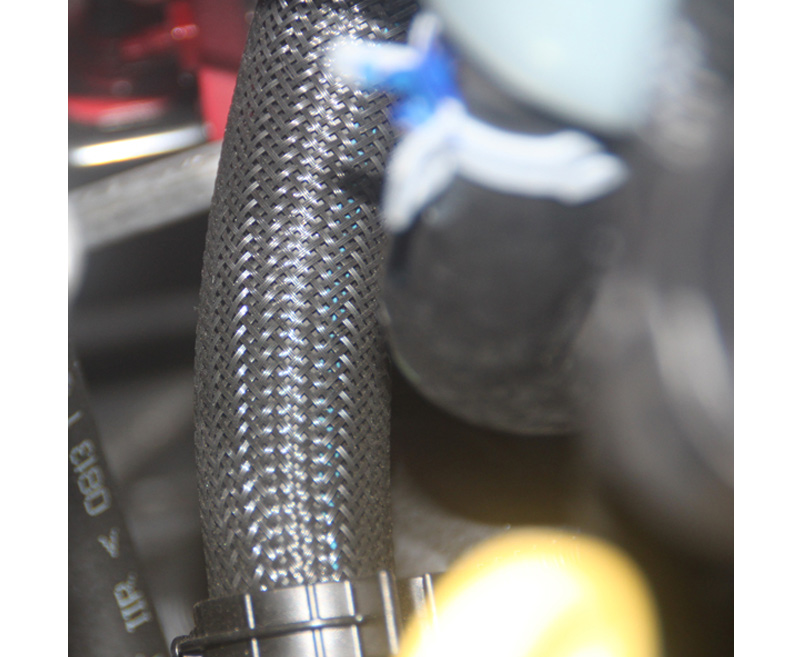
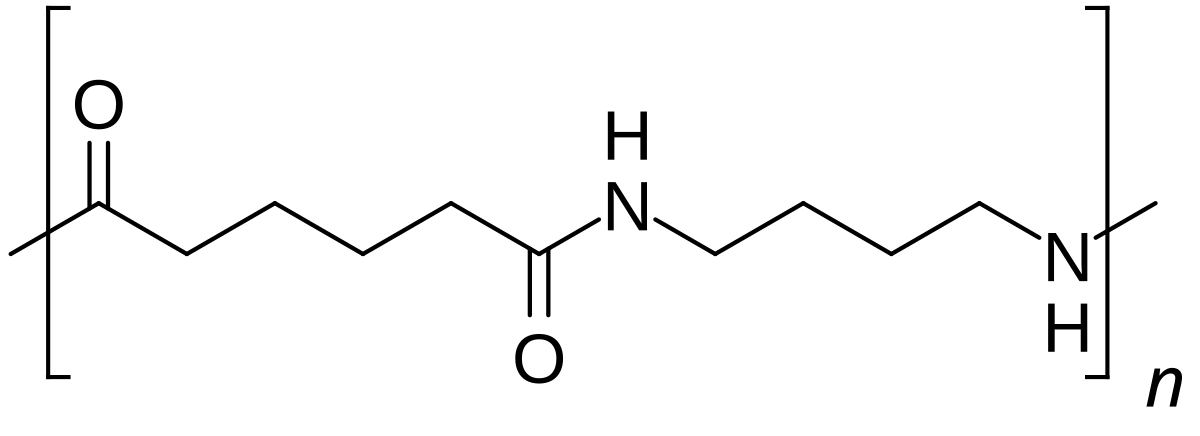

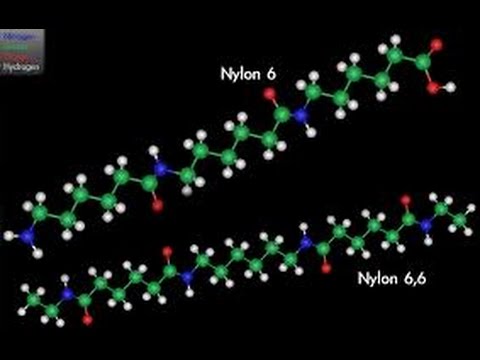





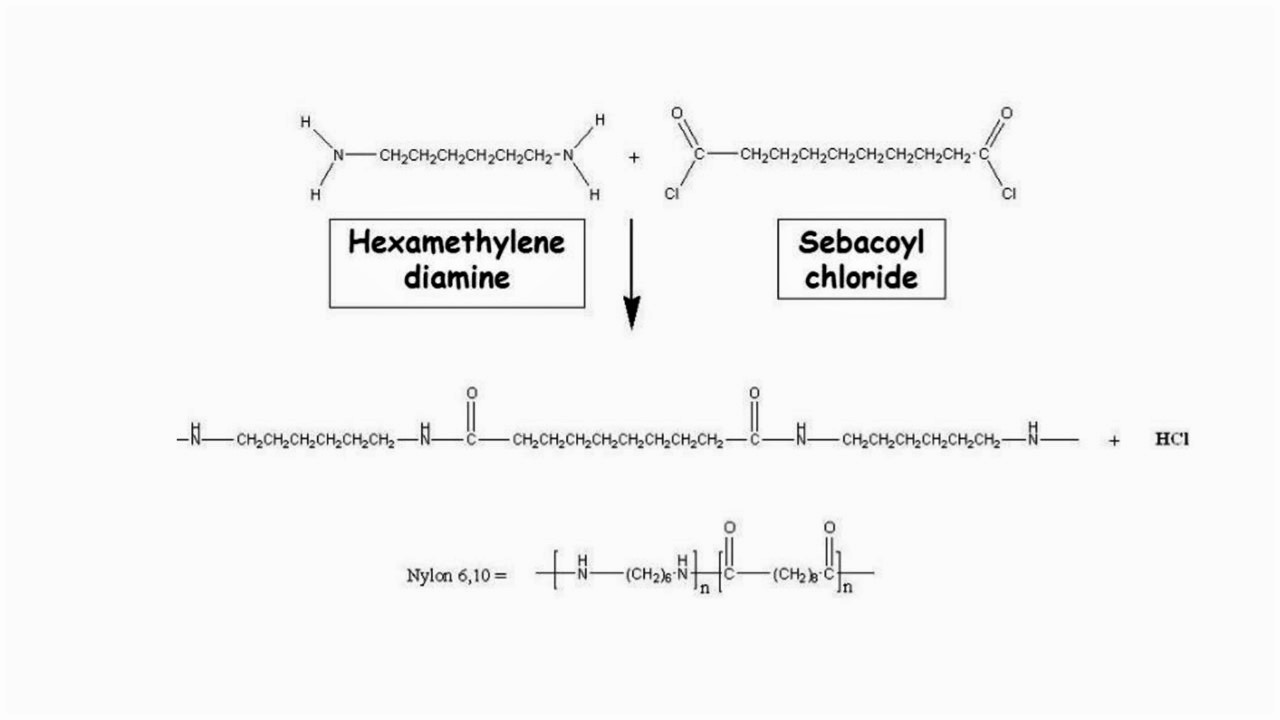


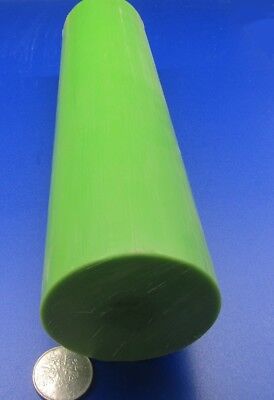


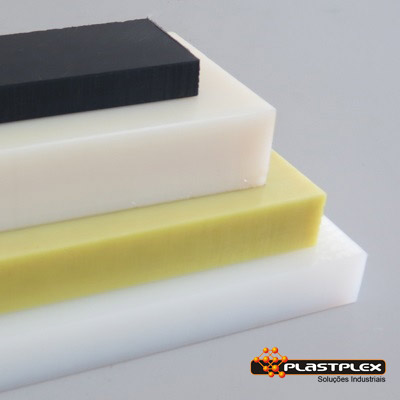

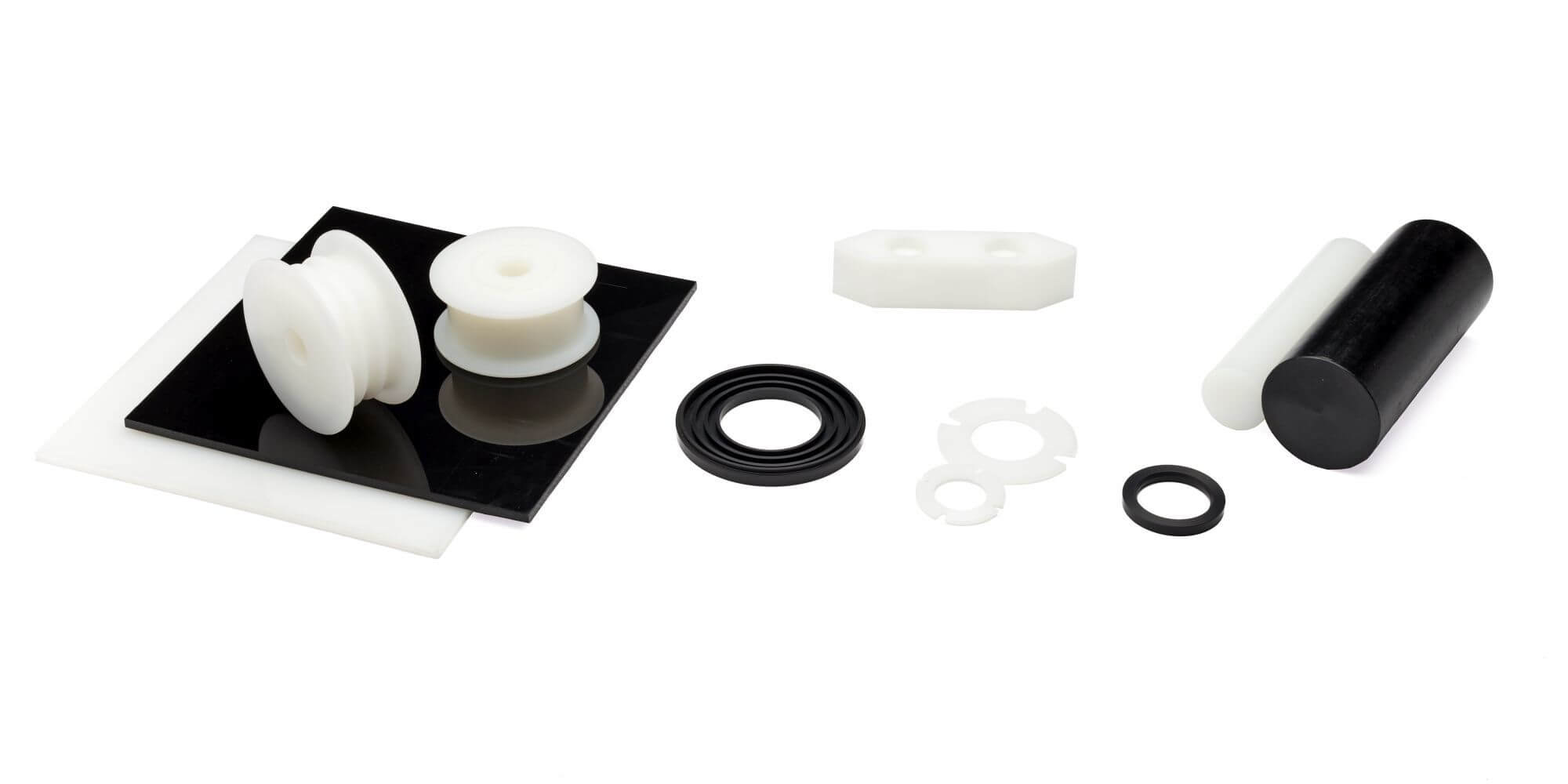
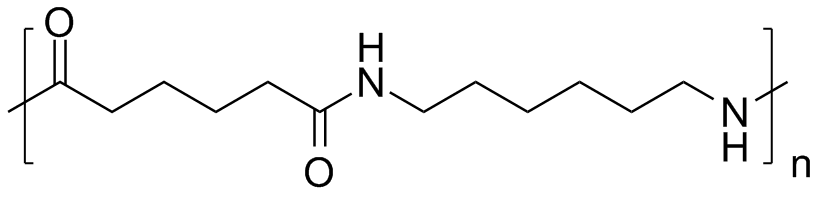


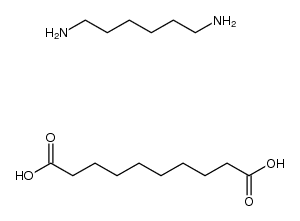

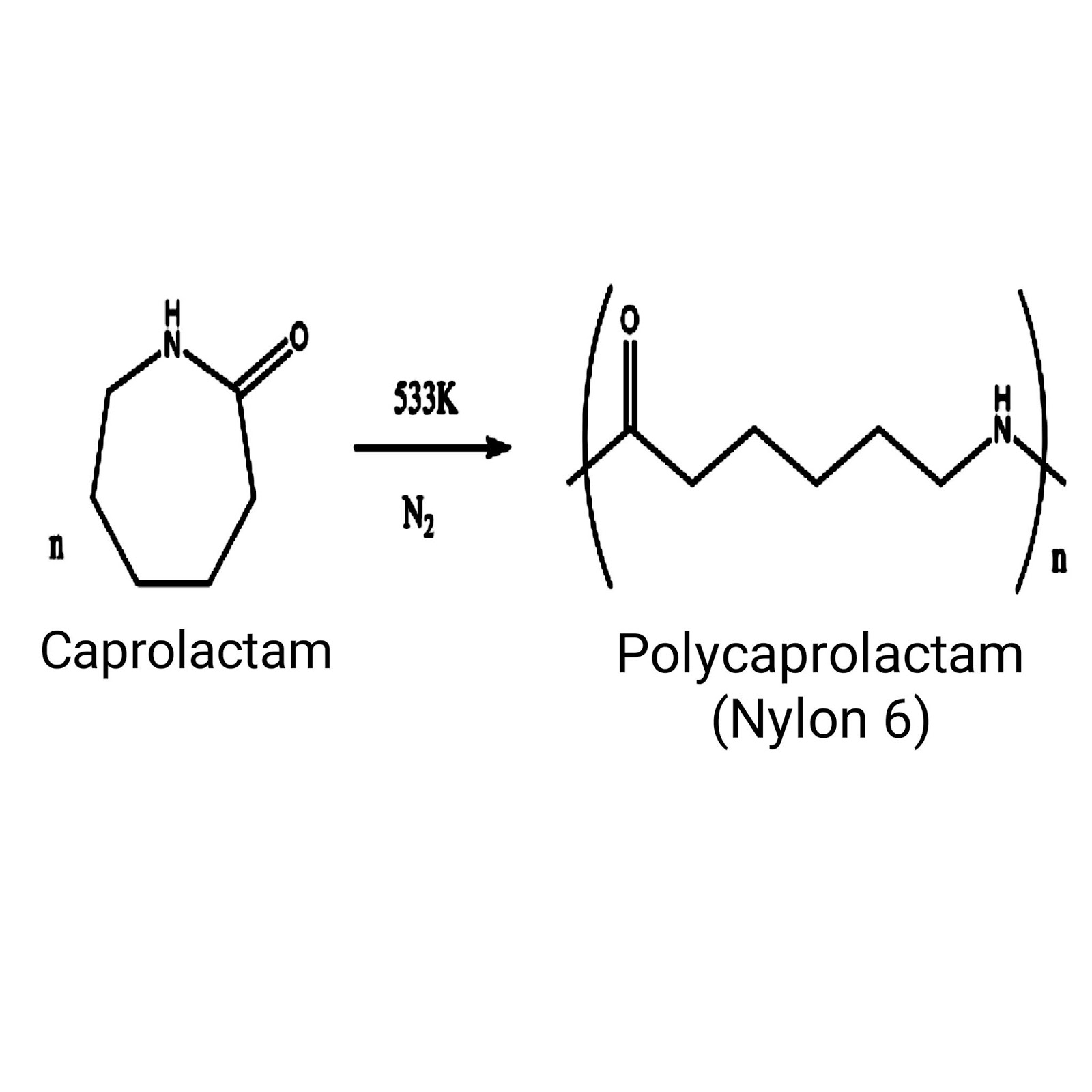






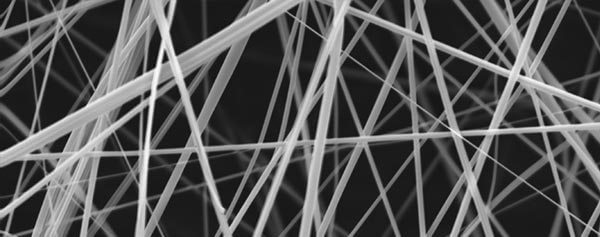

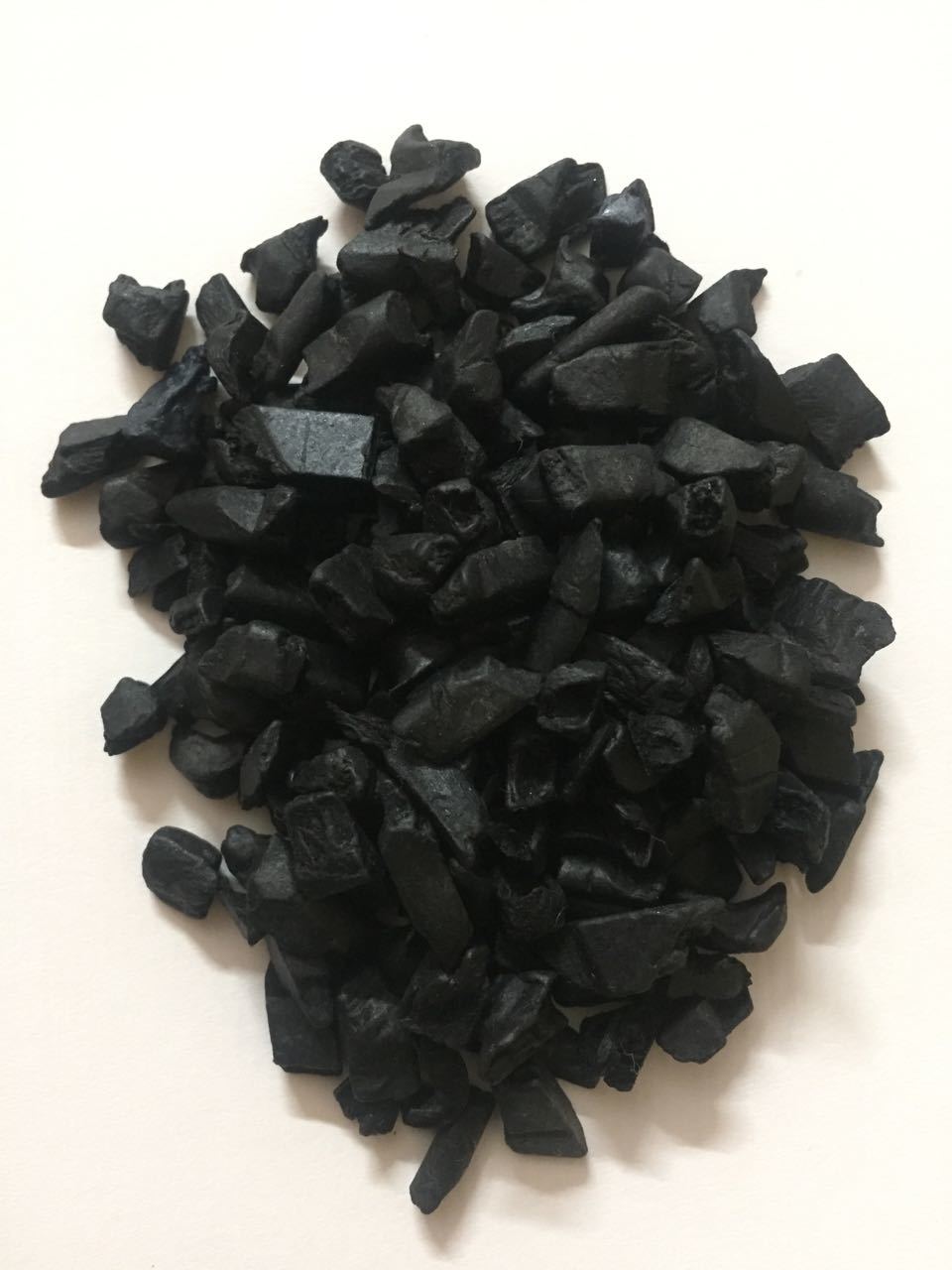

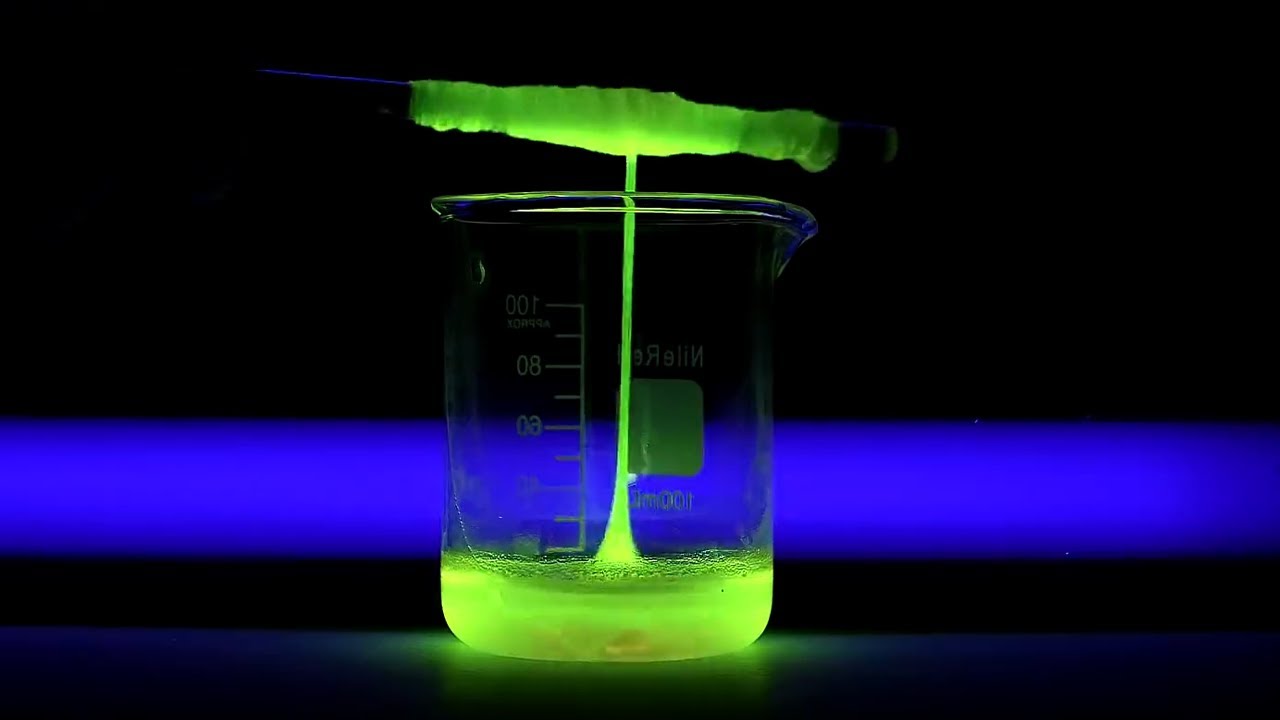


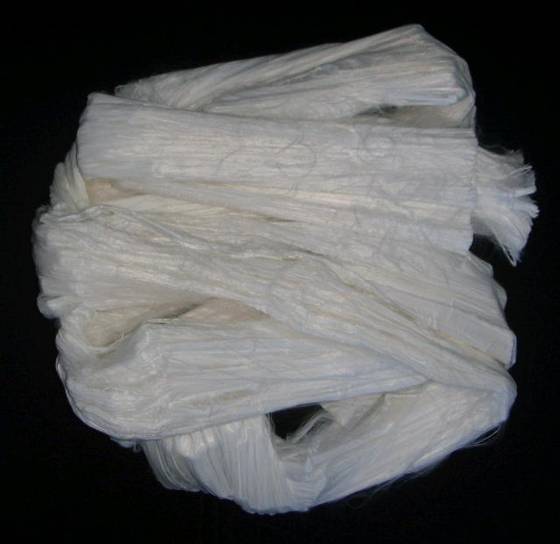



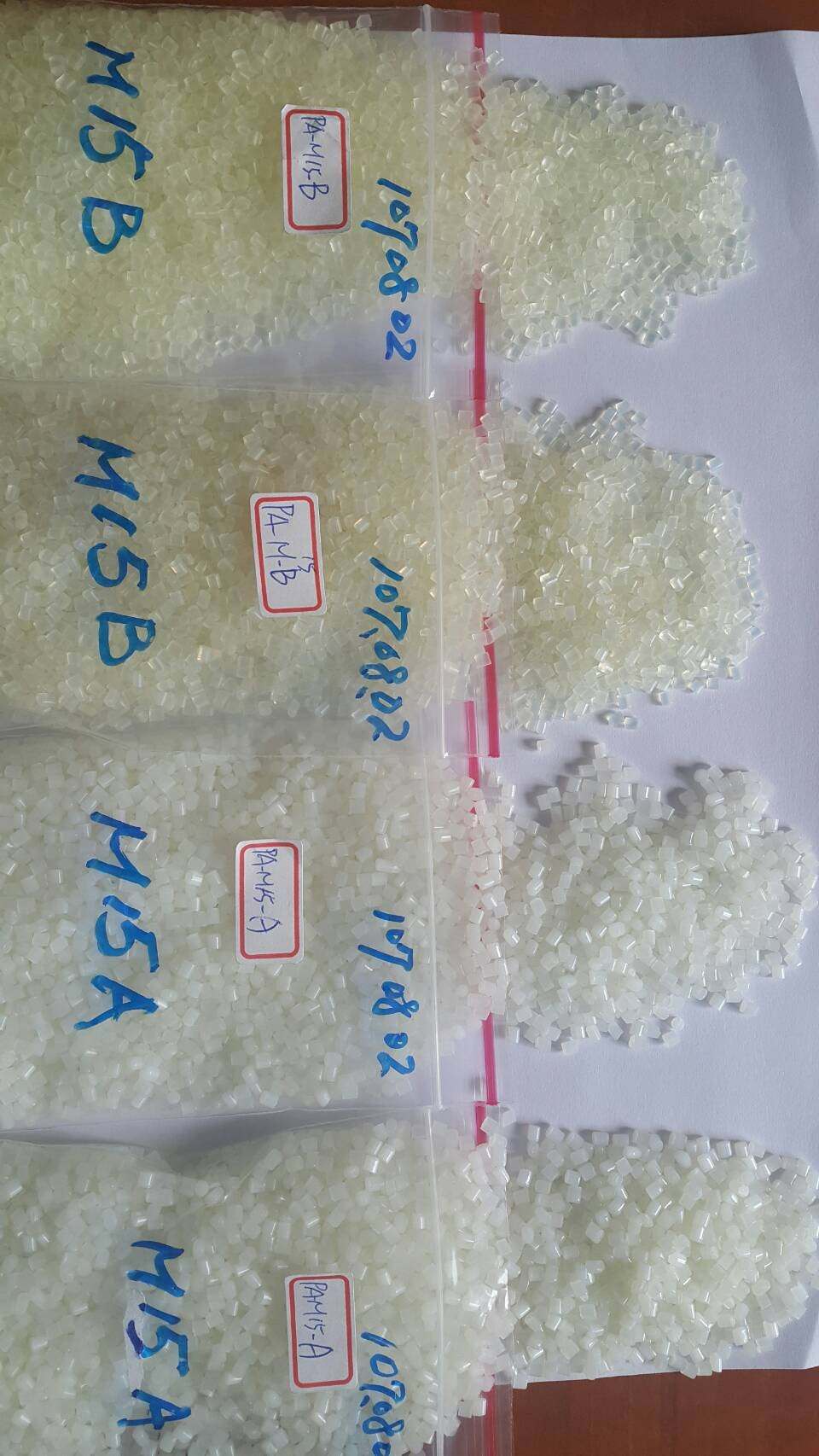
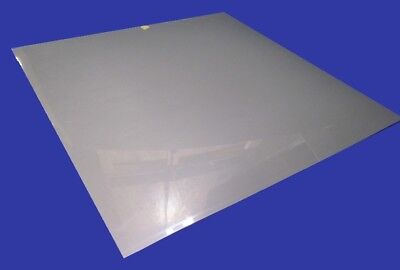
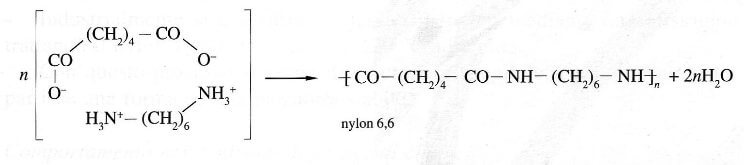
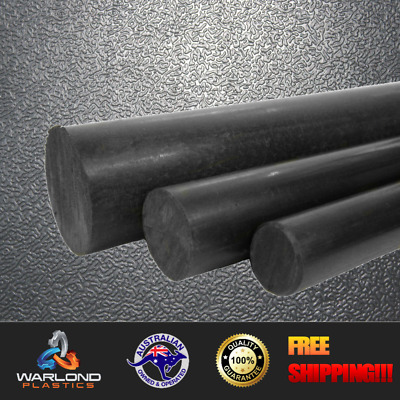

