Nylon 12
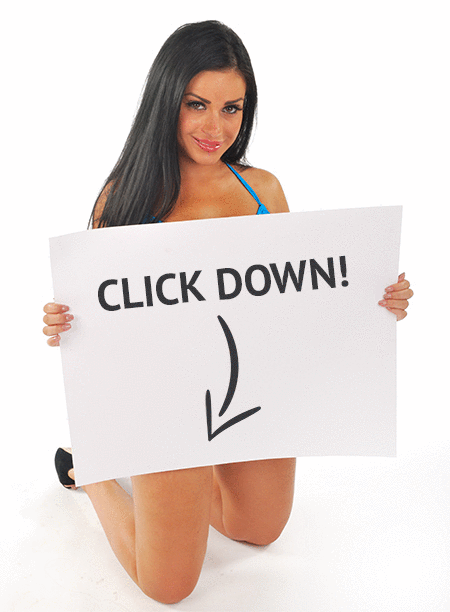
💣 👉🏻👉🏻👉🏻 ALL INFORMATION CLICK HERE 👈🏻👈🏻👈🏻
From Wikipedia, the free encyclopedia
Polyamide 12, PA 12, polylaurolactam, Polylaurinlactam, poly(12-aminododecanoic acid lactam); Daiamid (Daicel Chemical Industries), Grilamid (EMS Chemie); Rilsan A (Elf Atochem); UBE Nylon 12 (UBE Industries); Vestamid (Creanova)
Except where otherwise noted, data are given for materials in their standard state (at 25 °C [77 °F], 100 kPa).
^ Wolfgang. Griehl , Djavid. Ruestem "Nylon 12-Preparation, Properties, and Applications" Ind. Eng. Chem., 1970, vol. 62, pp 16–22. doi : 10.1021/ie50723a005
^
Kubisa, P.; Matyjaszewski, K.; Penczek, S. (1985). Cationic Ring-Opening Polymerization . Advances in Polymer Science. 68/69. Springer Berlin Heidelberg. pp. 201–208. doi : 10.1007/3-540-13781-5_11 . ISBN 978-3-540-13781-8 .
^
Mark, James E. (1999). Polymer Data Handbook . Oxford University Press, Inc. ISBN 978-0195181012 .
^ "Regenerist Micro-Sculpting Cream Moisturizer" . Olay . Procter & Gamble . Retrieved 10 December 2015 .
Nylon 12 is a nylon polymer with the formula [(CH 2 ) 11 C(O)NH] n . It is made from ω-aminolauric acid or laurolactam monomers that each have 12 carbons, hence the name ‘Nylon 12’. It is one of several nylon polymers. [1]
Nylon 12 can be produced through two routes. The first being polycondensation of ω-aminolauric acid, a bifunctional monomer with one amine and one carboxylic acid group.
n H 2 N(CH 2 ) 11 CO 2 H → [(CH 2 ) 11 CONH] n + n H 2 O
The second route is ring-opening polymerization of laurolactam at 260-300˚C. Ring opening can be carried out by cationic or anionic initiators, although cationic initiators have not been used commercially due to the product being less stable and oxidized relatively quickly in comparison to those produced by activated anionic polymerization (monomer casting). [2] Ring-opening polymerization is the preferred route for commercial production.
Nylon 12 exhibits properties between short chain aliphatic nylons (e.g., nylon 6 and nylon 66 ) and polyolefins . [3]
At 178-180 °C, the melting point of nylon 12 is the lowest among the important polyamides . Its mechanical properties, such as hardness, tensile strength, and resistance to abrasion, are similar to those of nylon 6 and nylon 66. Low water absorption and density, 1.01 g/mL, result from its relatively long hydrocarbon chain length, which also confers it dimensional stability and an almost paraffin -like structure. Nylon 12 is also chemical resistant and insensitive to stress cracking.
Nylon 12 has a broad range of applications as polyamide additives. Nylon 12 is mainly used for films for packing material in the food industry and sterilized films and bags for use in the pharmaceutical and medical fields. When added to polyethylene films, it improves water vapor permeability and aroma impermeability.
It is also prepared as sheets and sintered powder for coating metals. In the electronics field, it is used for covering cables and insulating material, while in the automobile industry it is used to prepare oil and gasoline resistant tubes. In the cosmetic and personal care industries, it is used as bulking and opacifying agents in the face and body powders, and skin creams. [4] Nylon 12 has also found uses in the textile industry and for producing sporting and leisure goods among other applications.
Significant suppliers of nylon 12 include EMS-Chemie , the Marl Chemical Park operated by Evonik , Arkema and SH Energy & Chemical
178 to 180 °C (352 to 356 °F; 451 to 453 K)
Nylon 12 first became available on a semicommercial scale in 1963. The monomer , dodecanelactam, is prepared from butadiene by a multistaged reaction. In one process butadiene is treated with a Ziegler-type catalyst system to yield the cyclic trimer, cyclododeca-1, 5, 9-triene. This may then be hydrogenated to give cyclododecane, which is then subjected to direct air oxidation to give a mixture of cyclododecanol and cyclododecanone. Treatment of the mixture with hydroxylamine yields the corresponding oxime, which on treatment with sulphuric acid rearranges to form the lactam ( Figure 18.9 ).
A number of variations in the process are also being investigated, including the direct photo-oximation of cyclododecane.
Nylon 12–coated aluminum composite powder with 50 wt.% of aluminum powder is prepared using the above three kinds of aluminum powder, which is marked as Al-9.36/PA (50/50), Al-18.37/PA (50/50), and Al-27.99/PA (50/50), respectively. Tensile samples and impact samples are formed using an HRPS-III type laser sintering system, carrying out the research on the effect of particle sizes of aluminum powder on tensile properties and impact strength of SLS forming parts. The fracture morphology of the impact sample is observed using a Sirion 200 type field scanning electron microscope manufactured by FEI Company, the Netherlands.
Nylon 12(PA12) [fuse temperature ( T m ) measured by differential scanning calorimetry is 178°C], a product of Degussa Germany, is powdered through solution precipitation. The average size of the powder is about 45 µm.
Two kinds of polymer powder were sintered using the HRPS-III laser sintering system developed by the Rapid Manufacturing Center of Huazhong University of Science and Technology. The scanning rate is 2000 mm/s and scanning distance is 0.1 mm. The laser power ranges from 4 to 20 W. Accordingly the laser energy density ranges from 0.02 to 0.10 J/mm 2 . The slice thickness is 0.1 mm.
The dimensional accuracy is characterized by the dimensional deviation. The size of the test specimen is 50×50×10 mm 3 . See Section 5.4.2.3 for the calculation of dimensional deviation.
The structure of nylon 66 is shown in Fig. 7.39 . The CAS number is 32131-17-2.
Figure 7.39 . Chemical structure of nylon 66.
Some of the characteristics of nylon 66 are:
Outstanding balance of mechanical properties
Outstanding toughness in equilibrium moisture content
Outstanding chemical resistance and oil resistance
Outstanding wear and abrasion resistance
Almost all grades are self-extinguishing. The flame-resistant grades are rated UL 94V0
Outstanding long-term heat resistance (at a long-term continuous maximum temperature ranging between 80 and 150 °C)
Grades reinforced with glass fiber and other materials offer superior elastic modulus and strength
Offers low gasoline permeability and outstanding gas barrier properties
Poor chemical resistance to strong acids and bases
Weathering Properties: Nylon 66 degrades on exposure to natural and artificial weathering. This degradation causes changes in its chemical, physical, and mechanical properties. The degree of changes depends on the wavelength of the UV radiation and the atmospheric conditions. Molded test parts exposed outdoors to UV radiation may ultimately fail for one of the following reasons: (1) loss of strength, (2) loss of toughness or (3) change in appearance.
Weather-resistant compositions of DuPont ZYTEL ® have been in service for more than 20 years. 13 These materials contain a grade of carbon that has been uniformly dispersed to screen out attack by UV light.
Manufacturers and trade names: Exopack Performance Films Inc. Dartek ® , DuPont™ and Zytel ® .
Data for PA66 plastics are found in Tables 7.4–7.9 and Figs 7.40–7.47 .
Table 7.4 . Exposure of DuPont Minlon ® 10B140 Polyamide 66 to Weather-Ometer ® (Xenon Lamp) 13
Table 7.5 . The Effects of Florida Weathering on the Properties of DuPont Polyamide 66 Resins 13
Note: Tensile bars tested as received; moisture contents ranged from 2% to 3% for ZYTEL ® 101, 105 and 101 WT007.
Table 7.6 . The Effects of Arizona Weathering Exposure on the Properties of DuPont Engineering Plastics ZYTEL ® 101, 105 and 101 WT007 Polyamide 66 Resins a 13
Note: (1) After 12 months, ZYTEL ® 101 and 101 WT007 show surface cracking and a broad range in tensile properties.
Table 7.7 . The Effects of Moderate Climate (Delaware, USA) Weathering Exposure on the Properties of DuPont Engineering Plastics ZYTEL ® 101 WT007 a and 105 13
Table 7.8 . The Effects of X-W Weather-Ometer ® Exposure on the Properties of DuPont Engineering Plastics ZYTEL ® 101 NC010, 101 WT007 and 105 13
Note: (1) (Wet–dry cycle), tensile bars 3.2 mm thick.
Table 7.9 . Effects of 6000 Hours of Accelerated Weathering on the Properties of Nylon 66 Resins 14
Note: (1) Sunshine carbon arc model X-W Weather-Ometer ® (wet cycle: 18 min water spray, dry cycle 102 min radiation, temperature 63 °C).
Figure 7.40 . Effect of Florida weathering on the tensile strength of DuPont Engineering Plastics glass-reinforced Zytel ® nylon. 15
Note: Equilibrated to 50% relative humidity before testing.
Figure 7.41 . Effect on Weather-Ometer ® exposure on the tensile strength of DuPont Engineering Plastics Zytel ® 70G33L nylon. 15
Figure 7.42 . Tensile impact strength after accelerated weathering of EMS–Grivory Grilon ® a Polyamide 66 resins. 10
Note: 1-mm-thick testing bar; xenon lamp radiation with water spray cycles and temperatures of 65°C.
Figure 7.43 . Tensile impact strength after accelerated weathering of EMS–Grivory Grilon AG-30 glass-fiber reinforced polyamide 66 resins. 10
Note: 1-mm-thick testing bar; xenon lamp radiation with water spray cycles and temperatures of 65 °C.
Figure 7.44 . Effect of UV on tensile strength of neat polyamide 66 resins. 14
Note: Sunshine carbon arc model X-W Weather-Ometer ® (wet cycle, 18 min water spray; dry cycle, 102 min radiation; temperature 63 °C).
Figure 7.45 . Effect of UV on tensile modulus of polyamide 66 neat resins. 14
Note: Sunshine carbon arc model X-W Weather-Ometer ® (wet cycle: 18 min water spray; dry cycle, 102 min radiation; temperature, 63 °C).
Figure 7.46 . Effect of UV on tensile strength of glass-reinforced polyamide 66 resins. 14
Note: Sunshine carbon arc model X-W Weather-Ometer ® (wet cycle, 18 min water spray; dry cycle, 102 min radiation; temperature, 63 °C).
Figure 7.47 . Effect of UV on tensile modulus of glass-reinforced polyamide 66 resins. 14
Note: Sunshine carbon arc model X-W Weather-Ometer ® (wet cycle, 18 min water spray; dry cycle, 102 min radiation; temperature, 63 °C).
To enhance interfacial adhesion between nylon 12 and the nanozirconia matrix, the surfaces of nanozirconia particles are organically modified with the silane coupling agent. The reaction process of APTS with nanozirconia and nylon 12 and stearic acid is shown in Fig. 4.10 .
Figure 4.10 . Reaction formula of silane coupling agent APTS with nanozirconia and nylon 12 resin and stearic acid.
First APTS is hydrolyzed to form hydrolyzates containing alcohol groups (–OH), and the reaction formula is shown in Fig. 4.10A . Second the surface of nanozirconia contains a large amount of –OH, which can carry out condensation polymerization with the hydrolyzates of APTS, so that the amino group (–NH 2 ) is grafted onto the surfaces of nanozirconia particles, and the reaction formula is shown in Fig. 4.10B . Finally the amino group grafted onto the surfaces of nanozirconia reacts with carboxyl groups in nylon 12 and stearic acid to form an amide bond, so that interfacial bonding between nanozirconia and the stearic acid matrix can be improved, and the reaction formula is shown in Fig. 4.10C and D .
The structural changes of nanozirconia before and after surface modification are qualitatively analyzed by Fourier transform infrared spectroscopy (FTIR). The instrument used was a VERTEX 70 Fourier transform microinfrared (micro-IR)/Raman spectrometer from Bruker, Germany. Fig. 4.11 shows the FTIR spectra of nanozirconia before (A) surface modification and (B) after surface modification.
Figure 4.11 . FTIR spectra of nanozirconia (a) before surface modification and (b) after surface modification. FTIR , Fourier transform infrared spectroscopy.
As can be seen from the FTIR ( Fig. 4.11a ) of nanozirconia before surface modification, there is a broad and strong peak at 3450 cm −1 , which is attributed to an O–H stretching vibration peak of the surface of nanozirconia. It can be seen from the FTIR ( Fig. 4.11b ) of nanozirconium dioxide subjected to surface modification that compared with the FTIR prior to surface treatment, as the organic link is grafted onto the surface of nanozirconia during surface treatment, there is a new absorption peak at 2929 cm −1 in the FTIR upon surface modification. The above FTIR indicates that the coupling agent APTS is successfully grafted onto the surface of nanozirconia.
Nylon 11 (PA-11) and nylon 12 (PA-12) have been introduced for use in gas distribution piping. PA-11 is also used in multilayer steel-reinforced offshore risers and flow lines for the production of deepwater oil and gas deposits. Nylon 6 (PA-6) is being used as a permeation barrier layer in multilayer PE/PA piping for crude oil and gas production piping. Nylon 6,12 is just now being introduced for piping applications. A modified nylon 6,6 (PA-6,6) piping material has recently been introduced for oil and gas production piping applications.
Stretched thin films of high molecular weight nylon 12 (η r = 25) were prepared using the same method as for stretched isotactic PS films (Section 34.5.2.1.ii ), and then annealed at 170–175 °C after deposition on EM grids. The ED pattern of the film showed the fiber pattern with crystalline reflections which are indexed on the basis of the crystal structure of the γ-form of nylon 12. 302 Sometimes ED patterns showing special orientations were obtained. This pattern is characterized with a fairly strong 20 2 ¯ reflection, suggesting that the 200 plane, namely the plane on which hydrogen bonds are set, is oriented parallel to the film surface. 303 From such specimens 020 lattice images (1.5 nm in spacing) were obtained. 303 The crystallite size in the direction parallel to the fiber axis ( b -axis) is deduced as 8 to 15 nm because the number of lattice fringes recognized clearly within a coherent region in the micrograph is 5–10.
Morphologies of thin films with a spherulitic texture have been studied extensively by TEM for various polymers such as PPS, PE, isotactic PS and so on. The strain-induced crystallization of isotactic PS from the glassy and rubbery state was examined by Yeh and Lamber 350 using TEM. Recently Geil discussed the presence of ordered domains in amorphous polymers. 304 Such materials were PE, P4M1P, poly(vinylidene fluoride), polypivalolactone, PP, PB and PET. Thin amorphous films of these polymers were prepared by an ultraquenching technique and examined by TEM. Roche and Thomas discussed the defocus microscopy of copolymers. 305 They introduced the phase contrast transfer function , sin χ, to interpret the image contrast.
Kawaguchi et al. reported the preparation of oriented thin films of PPP and structural observations of them by TEM. 292,293 The paracrystalline nature of PPP was discussed by comparing its crystal structure with those of p -phenyls, in particular that of p -hexaphenyl. Here, p -phenyls such as p -hexaphenyl are oligomers of PPP. PPP and p -hexaphenyl are less radiation sensitive, and thus high resolution images were obtained for both materials. Stretched thin films of various polymers, such as PE, 306 isotactic PS, 306–308 PB-1 309 and some blends, were extensively studied using TEM by Petermann and his co-workers. 310,311 Recently, the epitaxial crystallization of PE onto uniaxially oriented PP was studied with TEM and is expected to be used for the adhesion of polymer laminates. 312
A range of nylon combinations can be used for rotomolding . The most common commercial grades are nylon 6, nylon 11, and nylon 12 and special grades have been developed with enhanced flame retardancy properties for use in aerospace duct work applications. They require some care in processing. But, when properly molded, they are strong, abrasion resistant, and self-lubricating, and have good impact, chemical and fatigue resistance as well as high continuous-use service temperatures. They retain their strength properties at high temperatures—values fall off as the material rises in temperature but do not dramatically fall away until the glass transition temperature ( T g ) for the material is passed. Nylon 11 and nylon 12 have better resistance to oxidation that results in longer retention of properties at elevated temperatures than nylon 6.
Nylons need additional antioxidants or processing with an inert atmosphere (typically nitrogen or carbon dioxide) to prevent degradation. Heat stabilizers , such as copper salts can be added to improve heat stability of the final molded product for applications where the service temperature exceeds 165°F (75°C). Nylon 6 can be molded without nitrogen if lower impact and inferior surface appearance is acceptable. Nylon 11 and nylon 12 do not require nitrogen atmospheres, although using a nitrogen bleed during molding can improve color retention and impact strength.
Liquid nylons in a caprolactam-based reaction and reaction injection molding materials, such as Nyrim can also be rotationally molded. Raw materials, usually in two streams, are heated to a liquid state and then mixed just before being added to the mold. Rotation deposits the material on the inside surface of the mold. Control of the reaction rate is critical in ensuring that the material is evenly distributed during the curing stages of molding. The reaction generates heat that accelerates the process—an oven may not be required for some applications.
Nylon is commonly used in applications requiring high temperature resistance while retaining good strength properties; for example, car and truck duct work. It is also used where good abrasion resistance is required and where chemical resistance beyond that of polyethylene is required. High flexural strength and toughness make it a good choice for pressure vessels and excellent permeation resistance makes it ideal for solvent and fuel containment.
In the past, military uniforms in the US were made from the so-called Battledress Uniform (BDU) fabric which was essentially nylon/cotton (50/50) blend twill fabric. Initially the fabric was not flame retarded due to lack of suitable treatments. It was difficult to impart durable flame retardancy to nylon and nylon-containing fabrics due to its low reactivity and poor penetration of a finishing solution into the fibres. Flame retarding nylon fibres during the fibre-forming stage using flame retardant additives such as organophosphorous and halogenated aliphatic/aromatic compounds is not possible owing to the reactivity of the polymer melt towards these additives encountered during the spinning process. Flame retardant finishing of nylon fabric
https://en.wikipedia.org/wiki/Nylon_12
https://www.sciencedirect.com/topics/engineering/nylon-12
Hentai Fuck Dolls
Vintage Hairy Nude Sport
Spokane Escort Body Rubs
Nylon 12 - Wikipedia
Nylon-12 - an overview | ScienceDirect Topics
Nylon-12 | Cosmetics Info
Nylon 12
Nylon 12 FR - info.stratasysdirect.com
Nylon 12 (PA 12) | Cope Plastics | Excellent Chemical ...
Everything You Need to Know About Nylon 12 Material ...
Polyamide 12 (PA 12) - 3D Printing with Nylon Plastic ...
SLS Nylon PA 12 - 3D Printing Materials - Manufacturing ...
Multi Jet Fusion - Nylon PA 12 for Prototype & Production ...
Nylon 12


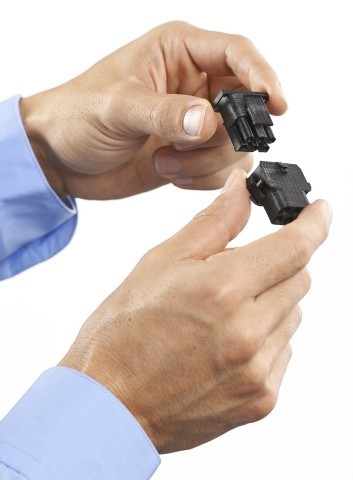


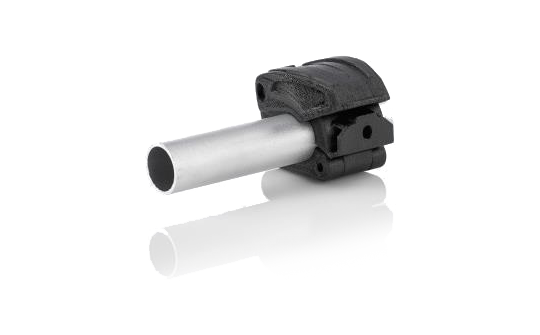

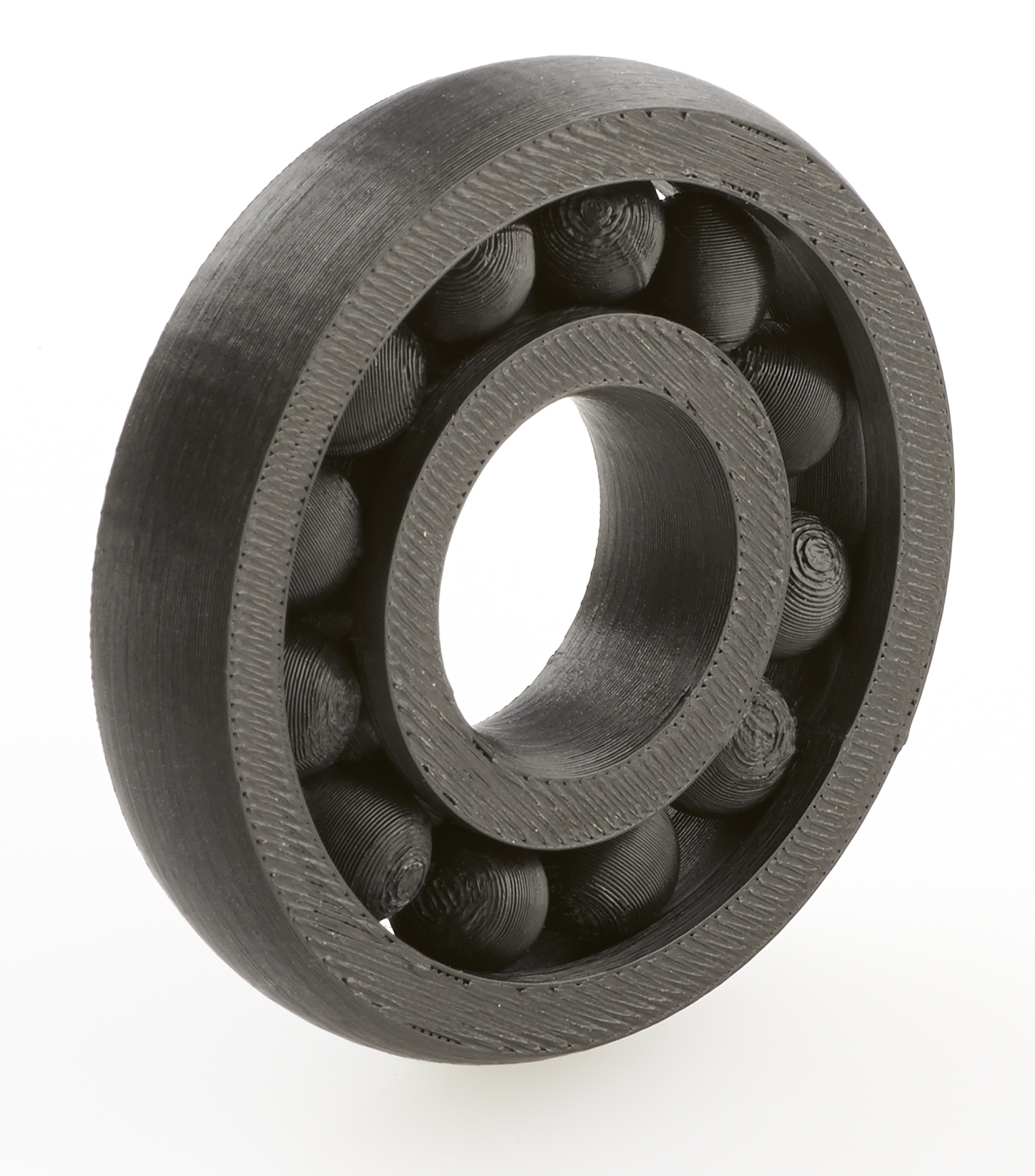









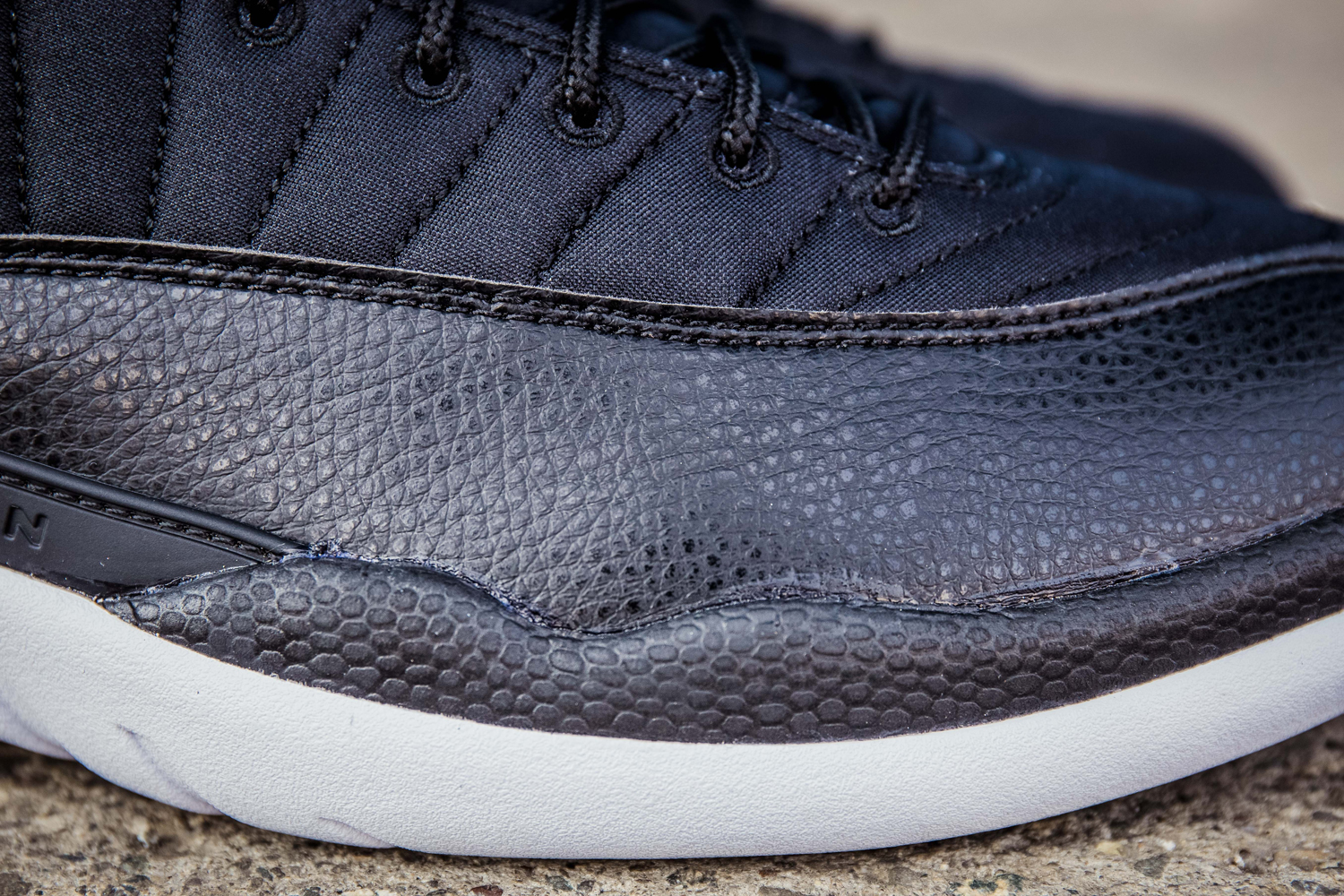




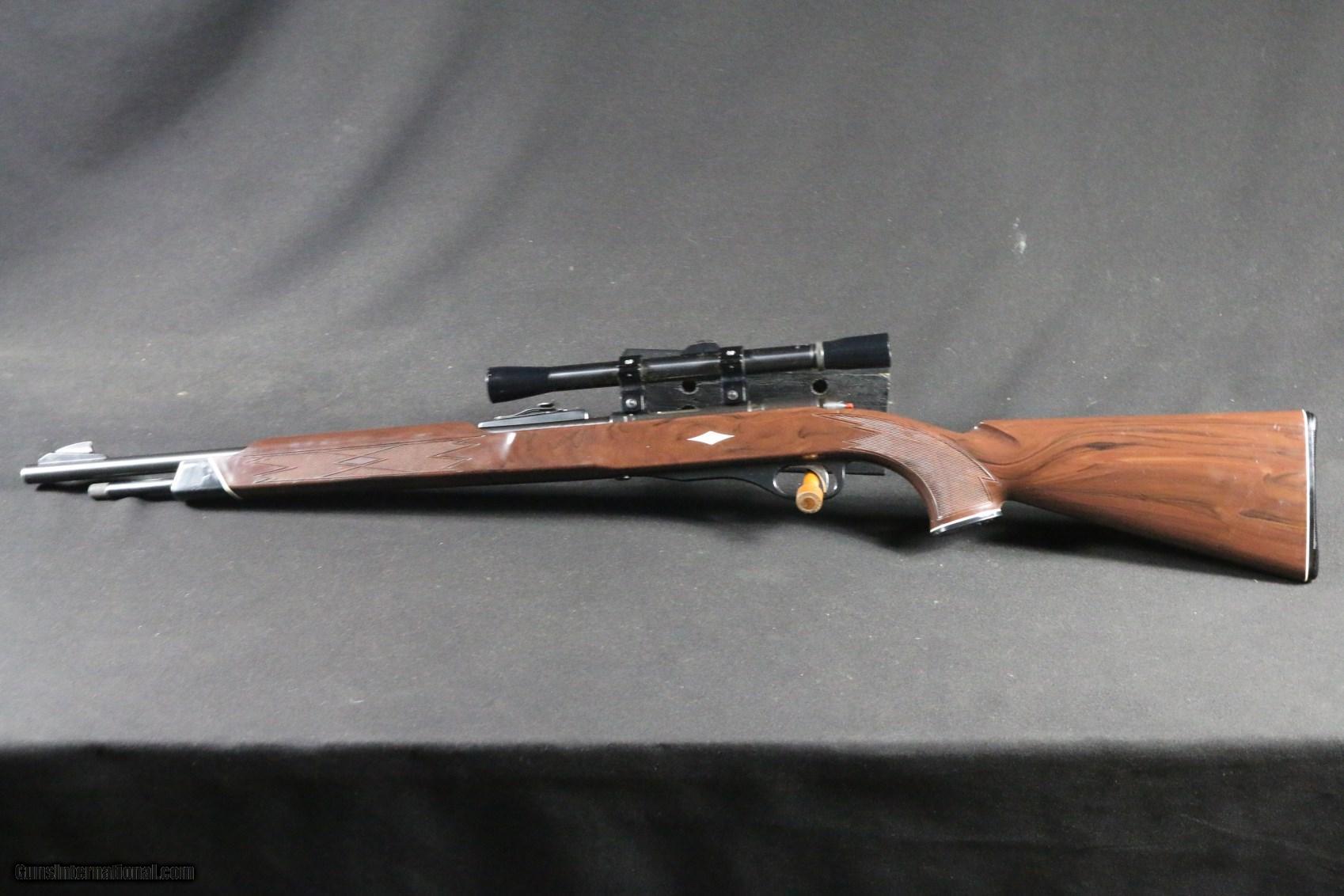

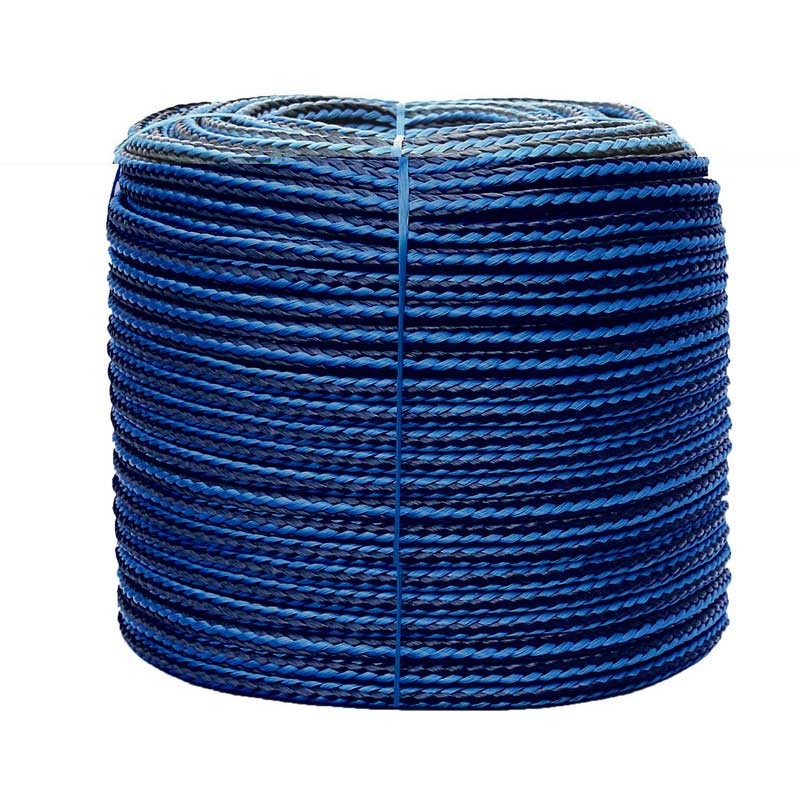

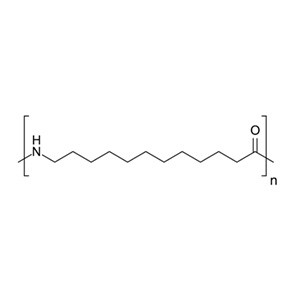













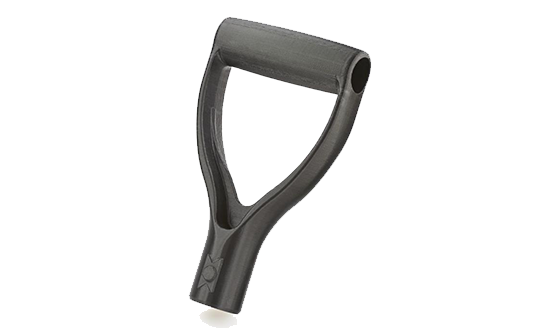



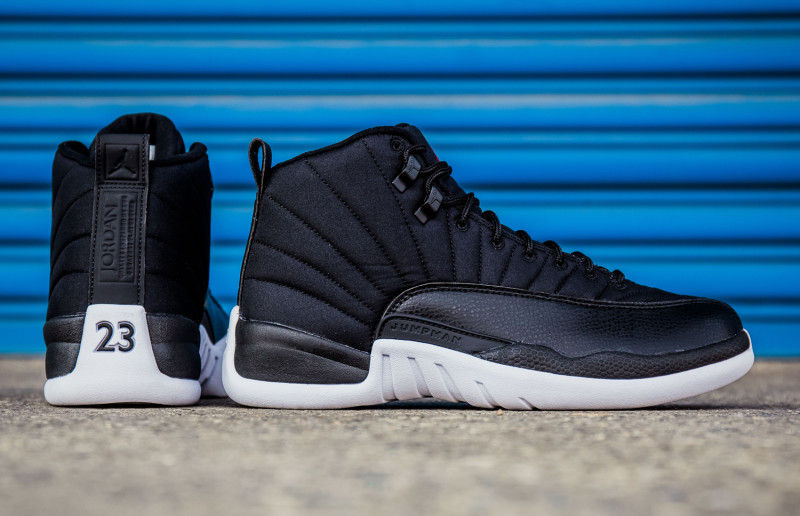






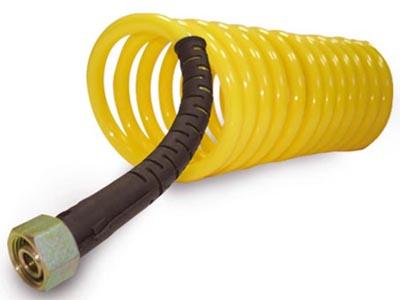
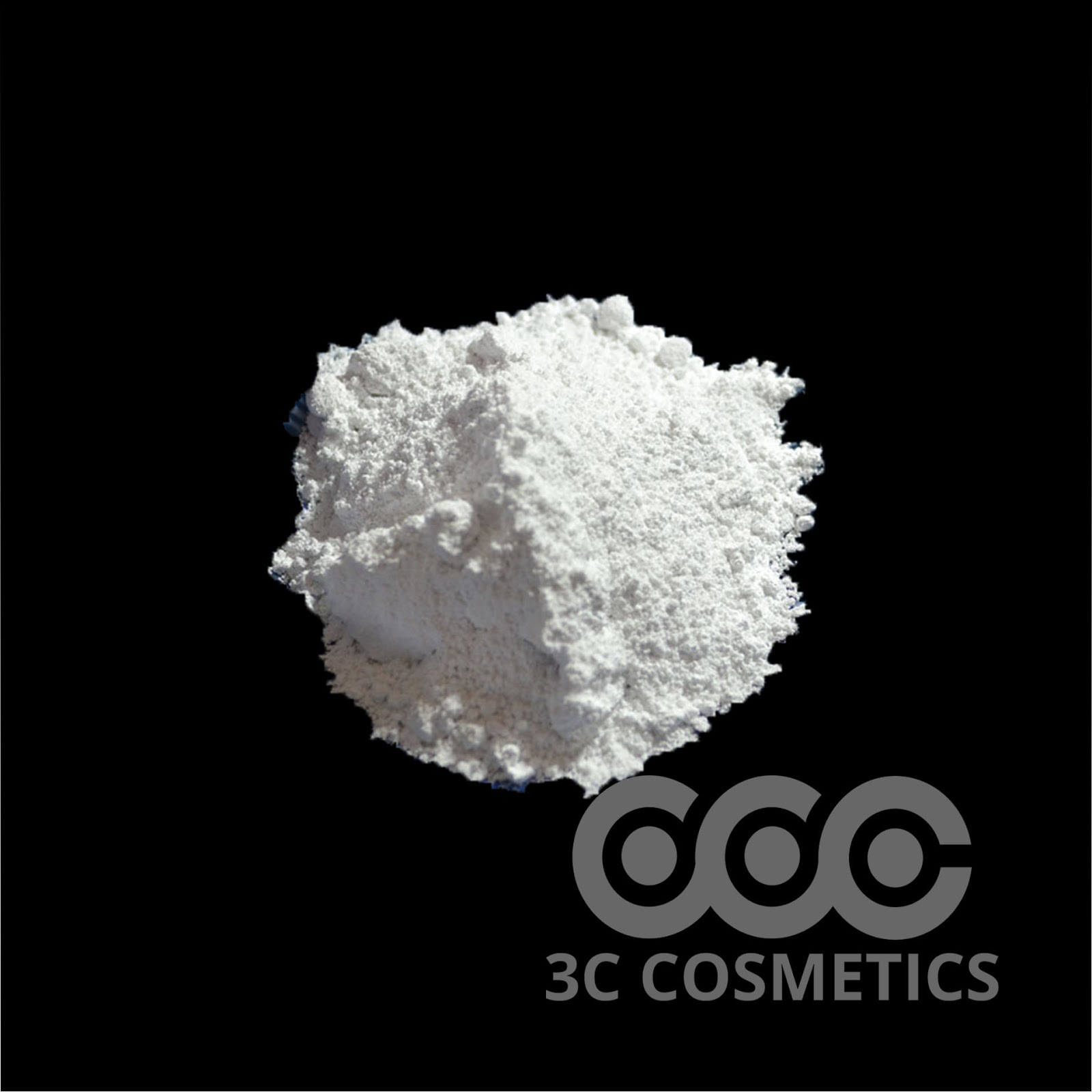


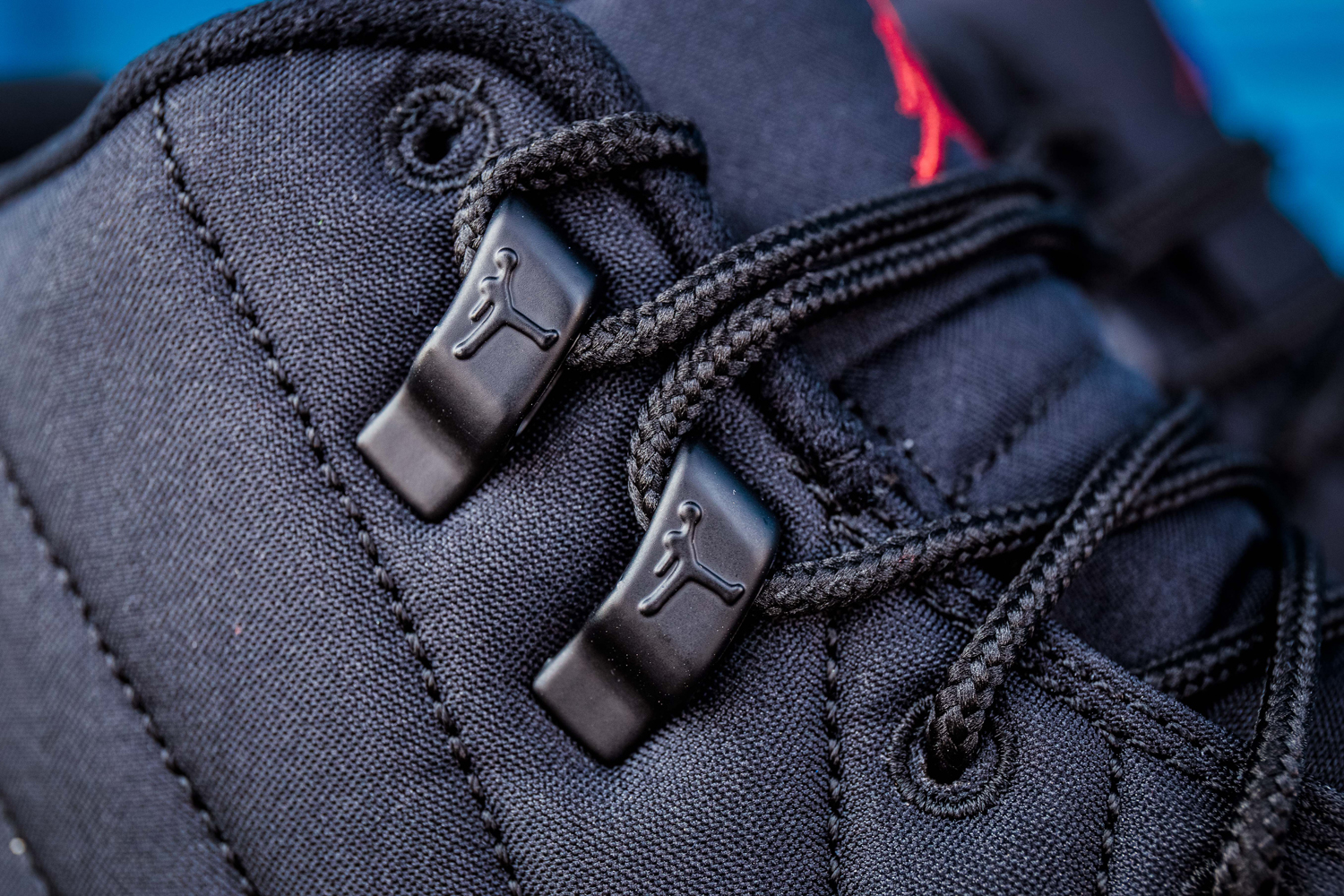


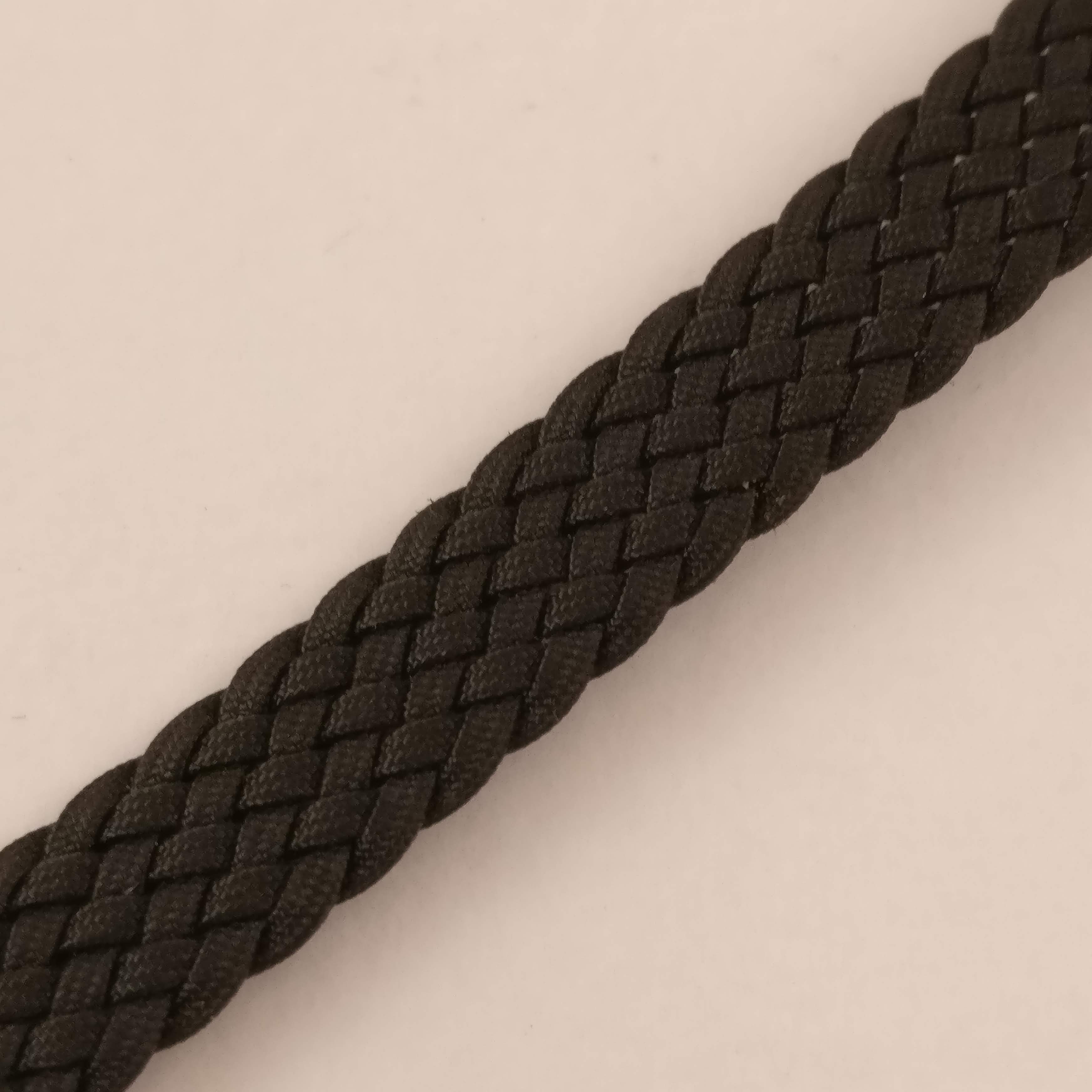
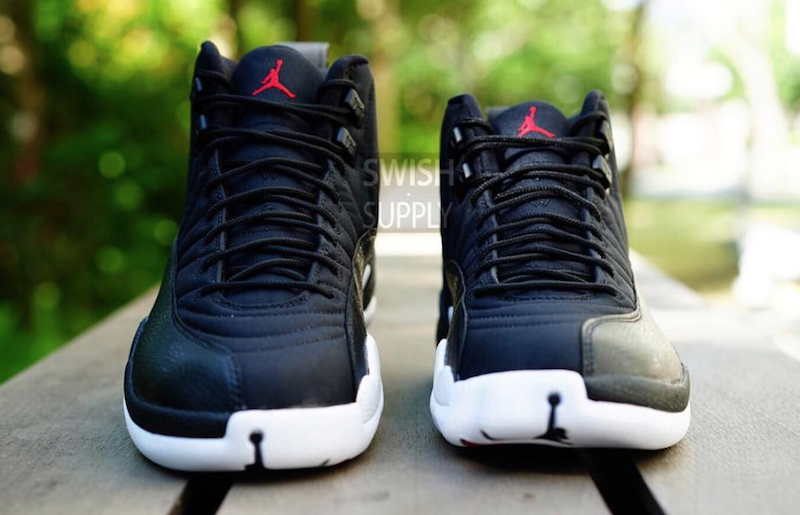

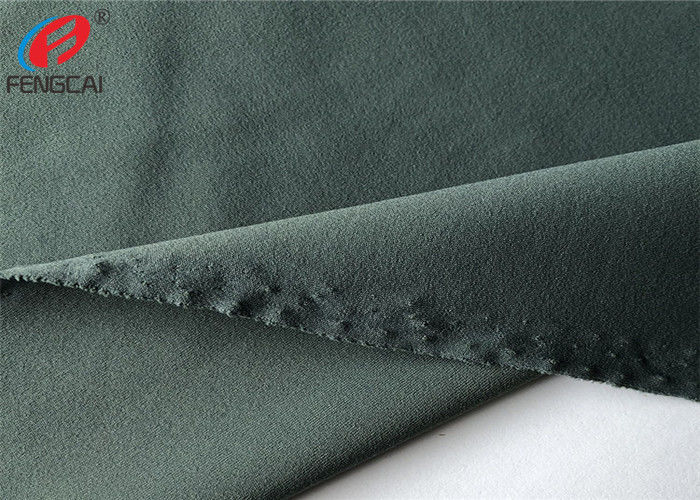

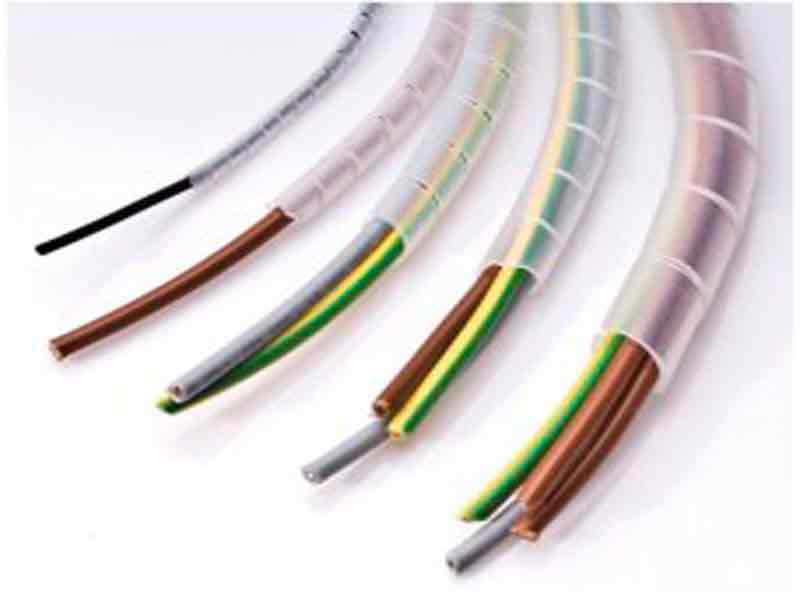
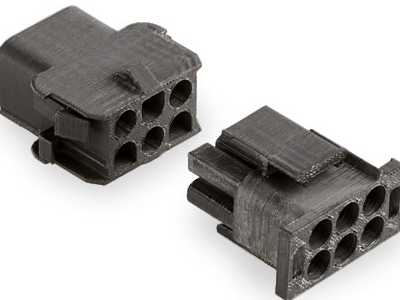


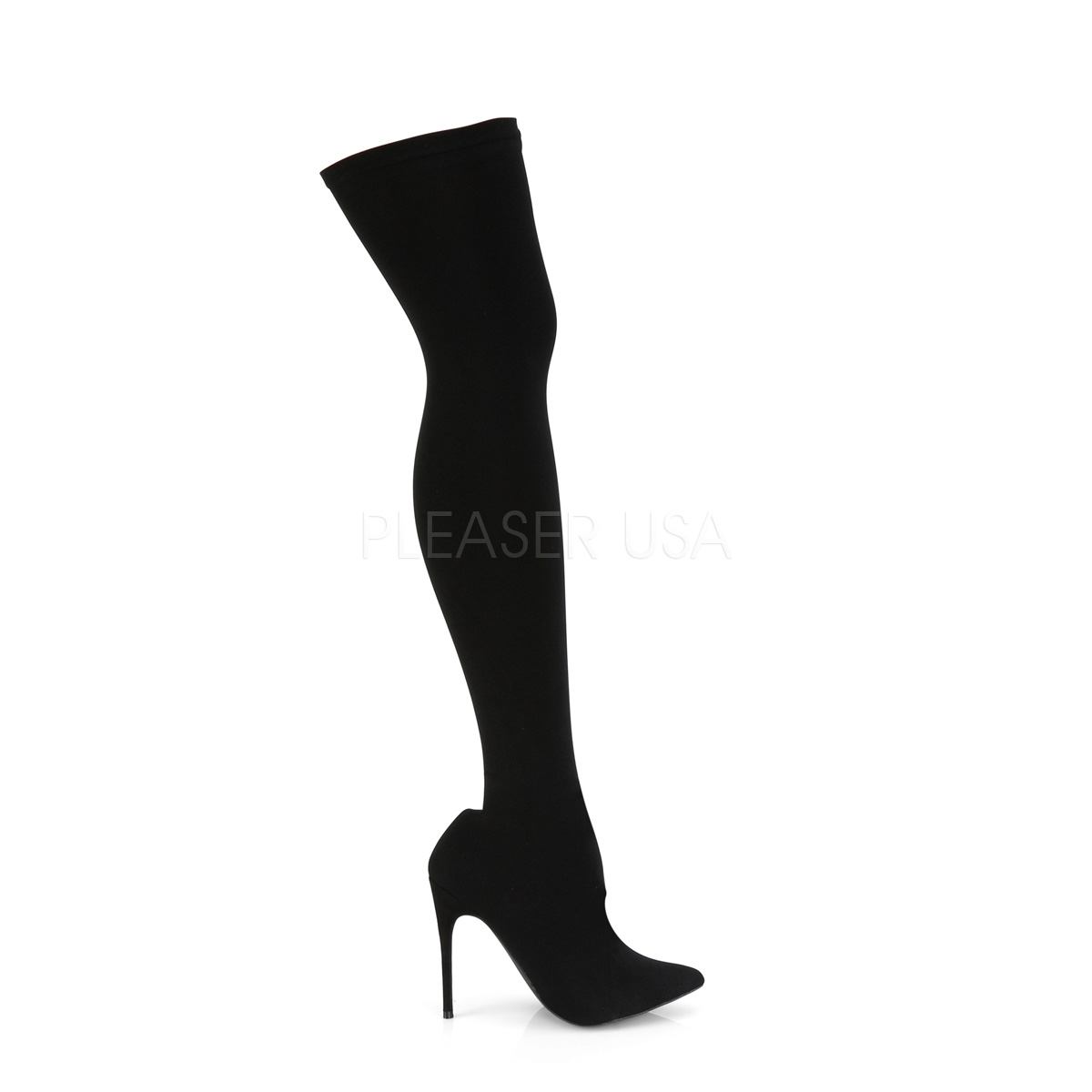




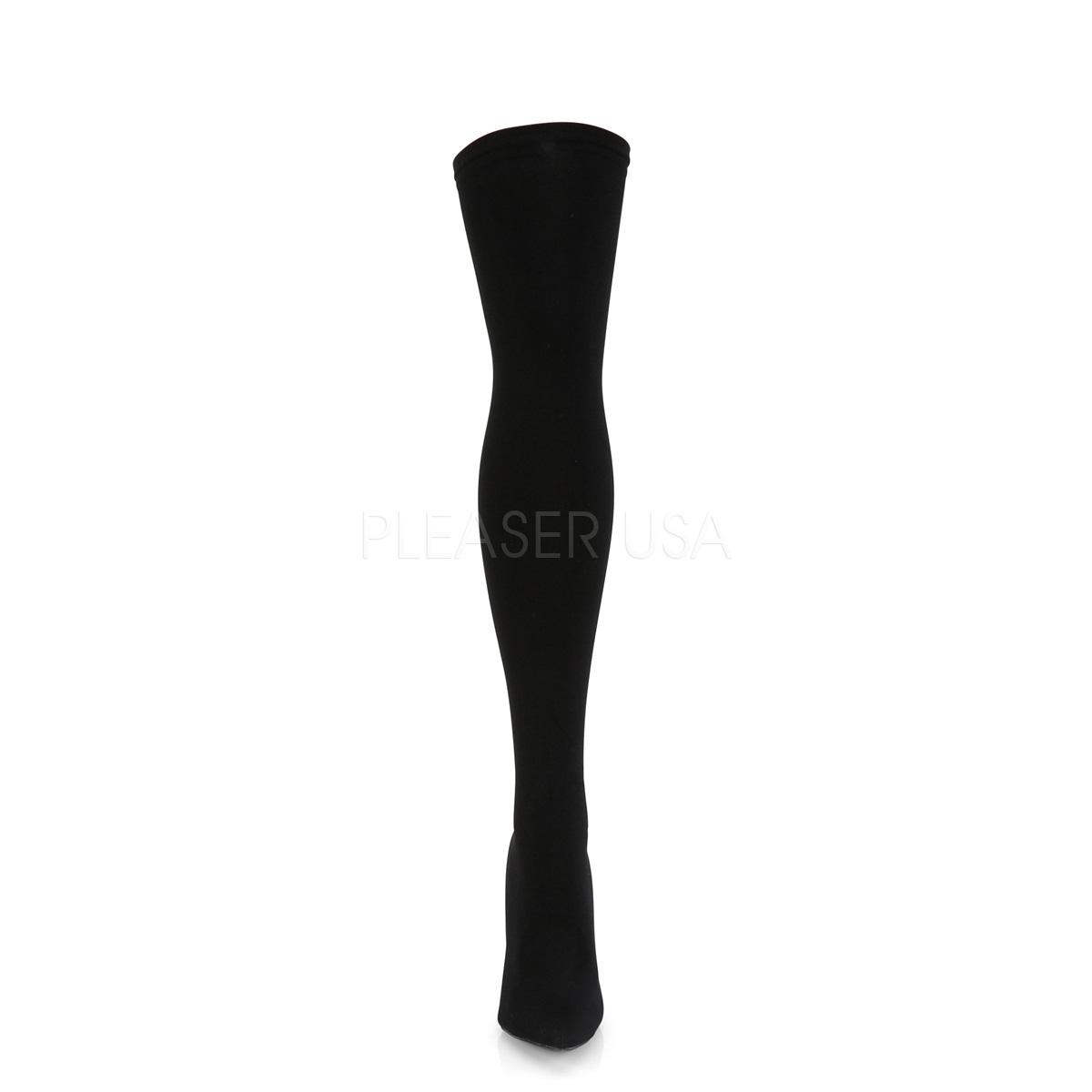
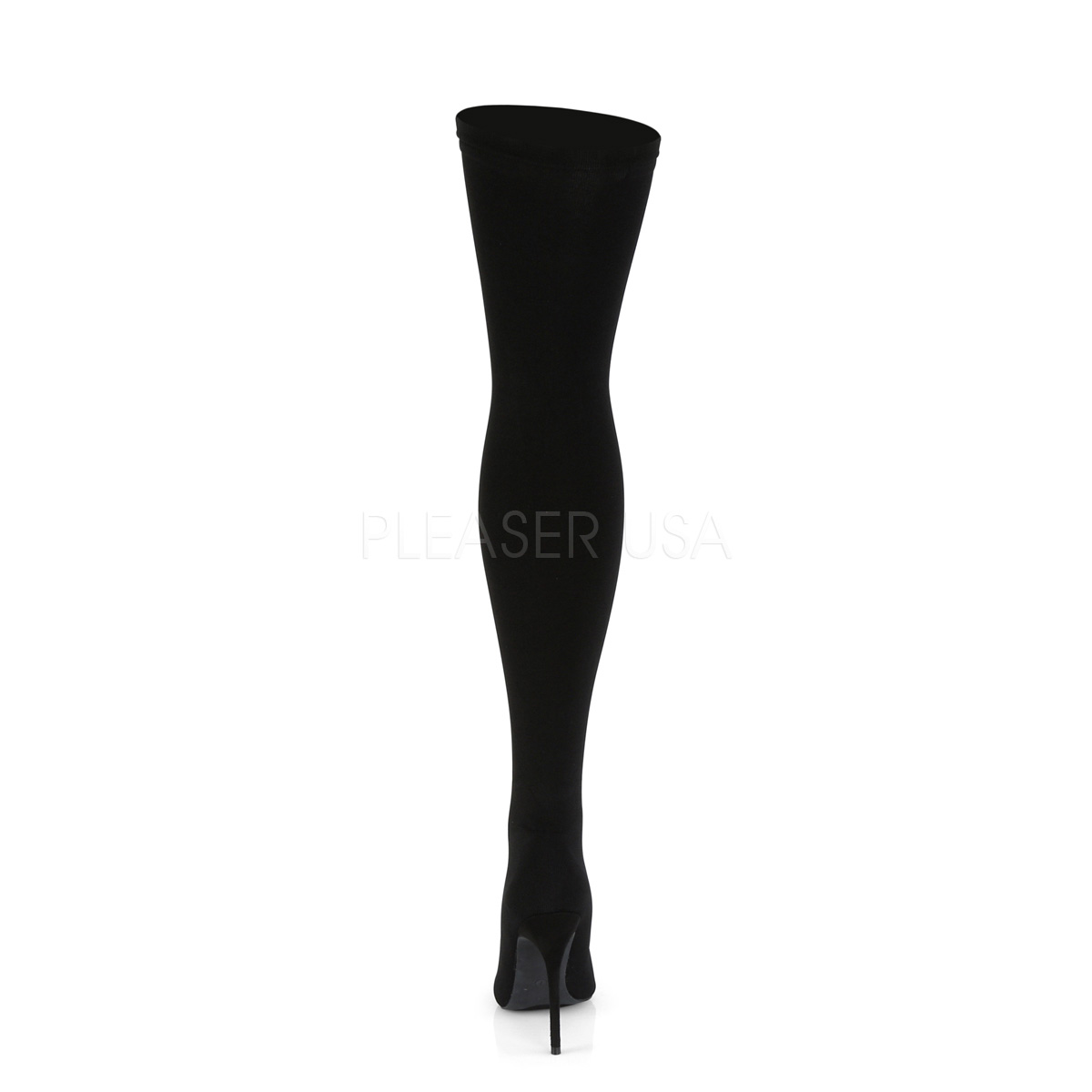




