Модернизация автоматизированной системы регулирования температуры в горне агломашины. Дипломная (ВКР). Другое.
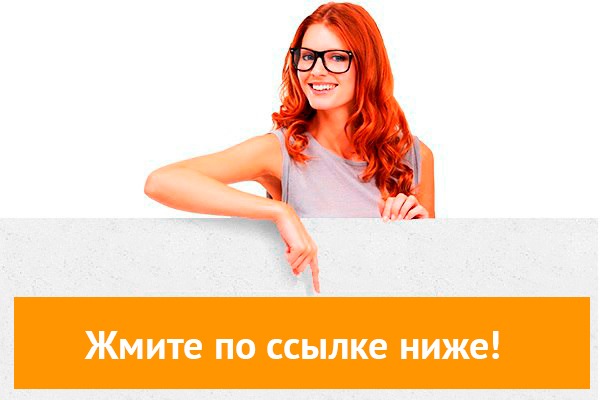
👉🏻👉🏻👉🏻 ВСЯ ИНФОРМАЦИЯ ДОСТУПНА ЗДЕСЬ ЖМИТЕ 👈🏻👈🏻👈🏻
Вы можете узнать стоимость помощи в написании студенческой работы.
Помощь в написании работы, которую точно примут!
Похожие работы на - Модернизация автоматизированной системы регулирования температуры в горне агломашины
Нужна качественная работа без плагиата?
Не нашел материал для своей работы?
Поможем написать качественную работу Без плагиата!
. Аналитический обзор существующей системы автоматизации и
выбор варианта решения
.1 Описание технологического процесса объекта
.3 Технические требования к САУ и выбор варианта решения
. Разработка функциональной схемы и выбор оборудования
.1 Функциональная схема автоматизации
. Математическое описание АСУ и выбор автоматического
управляющего устройства (АУУ)
.1 Структурная схема и алгоритм работы системы
.2 Определение математической модели объекта
.3 Определение передаточных функций
измерительно-преобразовательных и исполнительных устройств
.5 Выбор автоматического управляющего устройства на основе
ПЛК
.6 Определение математической модели САУ, исследование на
динамику системы
. Конструктивное оформление системы
Современное производство развивается в жесткой конкуренции и его развитие
идет в следующих направлениях: значительное повышение качества продукции;
уменьшение времени обработки конкретных агрегатов за счет технических
усовершенствований; увеличение интеллектуальной оснащенности металлургической
отрасли. Каждые 10 лет становления науки и техники обуславливается усложнением
технических объектов в 2-3 раза. Беря во внимание, что период освоения новых
технологических процессов в производстве составляет важный этап (5 и больше
лет) и эффективность процессов обработки развивается тоже медленно, ключевым
резервом увеличения экономических показателей металлургического производства
является увеличение степени непрерывности и безаварийности рабочего процесса.
Данная задача в металлургическом производстве принимается главным образом
методом автоматизации производственного процесса.
Современное развитие производства предполагает значительному увеличению
уровня автоматизации производственного процесса, созданию принципиально новых
технологий и управлению с целью обеспечивания выпуска продукции требуемого
качества в данный срок при наименьших расходах. Для достижения целей развития
производственных систем нужен комплекс мероприятий каждого направления:
совершенствование способов планирования производства и основ организации; ввод
новых и улучшение существующих технологических процессов; повышение уровня
автоматизации.
В металлургическом производстве обширное место занимают
автоматизированные системы управления. Это разъясняется сложностью процессов,
происходящих при производстве металла. Без использования устройств
автоматизации и автоматики невозможно точно поддерживать протекание
технологических процессов. Развитие управляющих систем идет по пути решения
задач автоматизации при посредстве широкого применения всевозможных электронных
систем и вычислительной техники, которая позволяет, при наличии развитого ПО,
решать всевозможные задачи на всех этапах управления, начиная со сбора
информации о состоянии объекта и кончая выработкой управляющего решения.
Экономная, безопасная и высокопроизводительная работа технологических агрегатов
металлургической промышленности требует применения современных средств и
методов измерения величин, определяющих ход производственных процессов и
состояния оборудования, использования современной вычислительной техники и
программного обеспечения.
Создание больших металлургических агрегатов позволяет более эффективно
применить сырьё, топливо, финансовложения, раскрыть широкие возможности для
высоких технико-экономических показателей при значимом снижении количества
обслуживающего персонала.
Все перечисленные выше требования в абсолютной мере можно отнести и к
аглопроизводству, которое является 1 стадией в производстве металла. Ключевой
задачей данного производства является осуществление высококачественного агломерационного
процесса, т.е. подготовка качественного сырья для доменного производства из
консистенции железосодержащих материалов. Агломерационный процесс дает лучшие
технико-экономические характеристики и высочайшее качество агломерата тогда,
когда его технологические характеристики оптимальны, строго соблюдается
постоянство физических свойств и хим состава шихты. САУ регулирования
температуры в горне позволяет добиться выше перечисленных характеристик и
выполнить поставленную задачу.
В настоящее время в аглоцехе-3 ОАО “Северсталь” происходит внедрение
новейших средств автоматизации и замена устаревших систем. В связи с этим
необходимо создать АСУ ТП на основе современных программируемых контроллеров.
Темой дипломного проекта является модернизация автоматизированной системы
регулирования температуры в горне агломашины №10 АГЦ-3 ОАО «Северсталь».
Надобность модернизации вызвана тем, что от качества регулирования
процесса спекания шихты и безотказной работы оборудования зависит количество
готового пригодного агломерата, соответствующего всем нормам.
Существующие системы не отвечают всем требованиям, предъявляемым к
современным АСУ и выпускаемой продукции.
обеспечивание оптимального управления технологическим процессом;
увеличение эксплуатационной надежности комплекса АСУ, создание критериев
для устойчивой работы цеха АГЦ-3;
гарантированное обеспечение намеченного уровня производства при
последующем сокращении употребления топлива, снижении затрат на исходные
сырьевые материалы и повышении качества агломерата.
В разрабатываемой системе должны быть учтены меры защиты информации от
помех и резервное питание оборудования АСУ ТП при авариях в системе
электроснабжения при помощи использования источников бесперебойного питания.
В процессе разработки проекта должен быть отработан вопрос минимизации
используемых технических средств и системных решений.
В модернизируемой АСУ ТП должны быть применены стандартные перспективные
типовые технические решения и технические средства при построении составных
частей системы. Также должны быть максимально использованы типы технических и
программных средств, успешно апробированных в работе в АСУ ТП аглопроизводства.
В процессе разработки проекта должен быть проработан вопрос минимизации
используемых технических средств и системных решений.
1. Аналитический обзор существующей системы автоматизации и выбор
варианта решения
Агломерационное производство - это подсобное производство, так как здесь
производится главное сырьё доменного процесса (агломерат).
Процесс агломерации заключается в спекании измельченных руд,
измельченного топлива и концентратов в прочные пористые куски - агломерат.
Агломерат считается одним из основных компонентов доменной шихты.
Технологическая схема агломерационной фабрики показан на рисунке 1.1
Рисунок 1.1 - Технологическая схема аглофабрики
В приемный бункер 1 с рудного двора приходит шихта, оттуда она по
транспортирующим конвейерам 2 и 4 поступает в первичные барабаны-смесители 5,
там ее смешивают, увлажняют и окомковывают. Смешивание, окомкование и
увлажнение - это процесс получения химически однородной консистенции всех
компонентов шихты, владеющих большой способностью газопроницаемостью при
спекании.
Далее возврат поступает из бункера 3 в смеситель. Возвратом (оборотным
продуктом) именуется отсеивание не спёкшейся шихты и агломерата, которые
получаются при грохочении агломерата. Возврат считается интенсификатором
спекательного процесса, тем самым делает лучше газопроницаемость шихты.
Задаваемое в шихте количество возврата должно быть строго неизменным и
составлять 20-25% от всей массы шихты.
Маленькие части шихты при смешивании становятся крупнее, образовывая
комки. Шихта делается зернистой и рыхловатой, повышая газопроницаемость. Из
смесителя шихта грузится в бункер 6 и транспортером 7 в конкретном соотношении
с коксиком (коксовая мелочь -используется как горючее), который поступает из
бункера 8, идет во вторичный барабан - окомкователь 9 (с вращательной скоростью
7-8 об/мин). При остановке агломашины, в барабанах-окомкователях
устанавливается устройство по отсечке воды.
Дозирование шихты для обжига выполняется на конвейерах в режиме
автоматического регулирования в соотношении «известняк - топливо». Оно
выполняется установкой нужных расходов компонентов, выдаваемых на транспортер 2
питателями из бункеров.
Выдача материалов из бункеров осуществляется вибрационными и тарельчатыми
питателями.
Смесь антрацитового штыба и коксовой мелочи является агломерационным
топливом. В заданном соотношении, производится дозировка компонентов топливной
смеси. После этого происходит сервировка системой конвейеров в бункера
четырехвалковых дробилок.
Подготавливаемую шихту 15 из бункера 13 передают системой загрузки в
агломашину 17, укладывая на бесконечно передвигающуюся цепочку из колосниковых
тележек (паллетов), сперва переместив постель 16, поступающую из приемного
бункера 10 и промежуточного бункера 12 по транспортеру 11. В процессе спекания
агломерата производится согласование с технологической картой, которая
составляется по состоянию агломашин, на основании расхода шихтовых материалов.
Объектом автоматизации является горн агломашины №10 (рисунок 1.2).
Назначением агломашины является процесс получения агломерата спеканием
концентратов и рудной мелочи путем прососа воздуха сквозь слой шихты,
расположенный на колосниковой решётке.
автоматический электрический алгоритм оборудование
, 2 - бункеры; 3 - барабанный смеситель; 4 - промежуточный бункер; 5 -
ведущий барабан, приводится в движение двигателем постоянного тока; 6 -
зажигательный горн; 7 - вакууум - камеры; 8 - ведомый барабан машины; 9 -
эксгаустер.
В бункер над машиной поступает шихта агломерирующего обжига. Питатель
передает в смеситель шихту, где она перемешивается и увлажняется. Влажная шихта
загружается сверху на передвигающуюся цепочку из паллет, с помощью качающегося
желоба (питателя маятникого), который содействует распределению шихты по ширине
ленты. Загруженные шихтой паллеты, идут под уравнителем, который представляет
из себя железную плиту, передвигающуюся в вертикальном направлении и
необходимую для регулировки толщины слоя шихты на палетах. Далее шихта
поступает под печь (горн), где зажигается и воспламеняется. Паллеты, в этот
момент, расположены над камерами разрежения, в которых отсасываются газы
эксгаустером. Затем паллеты с обжигаемой шихтой медленно двигаются вдоль камер
разрежения. Воздух просасывается сквозь раскаленную шихту и происходит
окисление сульфидов металла, благодаря наличию вакуума в камерах. Сульфиды
металлов быстро сгорают в тонком слое шихты, окруженные излишком воздуха.
Значительное количество тепла выделяют экзотермические реакции обжига, поэтому
спекается обожженная шихта. Скорость перемещения паллет зависит от длины машины
и колеблется в диапазоне 0,6-1,5 м/мин. Паллет, в конце горизонтального пути,
попадает на закругленный участок рамы роликами, опрокидывается, и шихта из него
падает на колосниковый грохот. Далее отсеивается мелочь (меньше 20 мм), а
большие куски агломерата идут в дробилку, и после на грохот с отверстиями 20
мм. Верхний продукт грохота размером 20 -100 мм является готовым агломератом,
идущим в шахтную печь. Нижний продукт грохота представляет собой некондиционный
агломерат, его измельчают и вводят в состав шихты как оборотный агломерат.
- Производительность проектная, т/час ¾ 350 ÷ 450;
- Ширина поверхности рабочей, м ¾ 4;
- Площадь общая газоотсоса, м² ¾ 312;
- Площадь спекающей поверхности, м² ¾ 252;
- Площадь охлаждающей поверхности, м² ¾ 60;
- Количество вакуум-камер газоотсосных, шт ¾ 26;
- Количество тележек спекающих, шт ¾ 130;
- Скорость движения тележек спекающих, м/сек ¾ 0,025 ÷ 0,125;
- Макс толщина слоя спекаемого, м ¾ 0,35;
- Мощность электродвигателя привода ленты, кВт ¾ 85;
- Масса без запчастей с электрооборудованием, кг ¾ 2126100.
Аглофабрика представляет из себя предприятие с непрерывным
механизированным процессом. Оснащена фабрика большим количеством
технологических устройств и сантехнических приборов, установленных в разных корпусах,
находящихся на большой площади. Выключение и включение большого числа
механизмов требует длительного времени, в последствии на этих предприятиях
учитывается дистанционное централизованное управление механизмами из 1-го или
нескольких операторских пунктов (ОП).
Поточность производства, в которой материал последовательно и непрерывно
поступает от 1-го механизма к другому, требует автоматического управления
данными механизмами, исключающей завалы при остановке 1-го из механизмов.
Под комплексом АСУ агломашины №10 понимаются автоматизированные системы
регулирования основных контуров и регистрация технологических параметров
Существующая система (рисунок 1.3) обеспечивает регулирование температуры
горна за счет изменения расхода газа и воздуха на горн.
В ПЛК Ломиконт-110 происходит первичная обработка аналоговых и дискретных
сигналов и регулирование 3-х контуров по программе, записанной в памяти у
контроллера.
Рисунок 1.3 - Функциональная схема существующего варианта САУ
Таблица 1 - Спецификация известного варианта САУ
Система регулирования должна выполнять следующие требования:
- обеспечивать качество регулирования;
- иметь способность к восстановлению впоследствии отказов;
- функционировать в непрерывном режиме с остановками при
техническом обслуживании.
Комплекс технических средств состоит из унифицированных и типовых узлов и
стандартных устройств. Преобразователи информации и датчики должны иметь унифицированные
выходные сигналы.
Система должна быть открытой и допускать вероятность функционального
расширения, с учетом развития к меняющимся технологическим условиям.
Показатели качества объекта управления:
Модернизация системы предполагает замену контроллера Ломиконт-110 на
SIMATIC S7-300, замены термоэлектрического преобразователя КТХА на термопару
типа ТПП10 (платинародий-платиновая) и датчика расхода Сапфир 22ДД на более
новый Метран 100ДД.
Тем самым мы усовершенствуем АСР и обеспечим стабильность технологических
условий, в частности улучшим технико-экономические показатели работы
агломашины, повысим надежность и безопасность работы оборудования, а также
улучшим условия труда персонала.
2. Разработка функциональной схемы и выбор оборудования
.1 Функциональная схема автоматизации
Функциональная схема разработанной САУ изображена на
рисунке 2.1
Рисунок 2.1 - Функциональная схема разработанной САУ
Работа САР состоит в следующем: сигналы с датчиков (1а, 2а, 3а, 4а, 5а)
поступают в контроллер UY (1б). Контроллер обрабатывает контролируемые
параметры, поступающие в систему визуализации и отображающиеся в виде числовых
значений на АРМ оператора UIH
(1в). Зажигание верхнего слоя шихты происходит в горне агломашины при заданной
температуре. Регулирование температуры производится за счет изменения расхода
газа (измерение расхода газа производится датчиком Метран-100ДД, регулирование
расхода газа на горн исполнительным механизмом МЭО 250 (7)). С изменением
расхода газа, в соответствии с заданным соотношением, меняется и расход воздуха
(измерение расхода воздуха производится датчиком Метран-100ДД, а регулирование
расхода воздуха на горн исполнительным механизмом МЭО 250 (6)). Оператор
выбирает нужное значение температуры горна, которое САР должна поддержать и ПЛК
вырабатывает управляющий сигнал для исполнительного механизма, на основе
заложенной программы. Температура в горне меряется термопарой типа ТПП10
(платинородий-платиновая).
Таблица 2 - Спецификация разработанной САУ
.2.1 Выбор датчика измерения расхода
Измерение расхода выполняется датчиками Метран - 100ДД (рисунок 2.2). Они
предназначенные для работы в системе автоматического регулирования, контроля,
управления технологическими процессами и обеспечивают преобразование значения
измеряемого параметра - давления абсолютного и избыточного, разрежения,
давления-разрежения, разности давлений агресивных и нейтральных сред в
унифицированный выходной сигнал дистанционной передачи.
Преобразователи Метран - 100ДД применяются в устройствах для
преобразования значения расхода жидкости, уровня жидкости или газа в
унифицированный токовый выходной сигнал.
- Измеряемые среды: жидкости, газ, пар и кислородосодержащие
газовые смеси;
- Диапазоны давлений: минимальный 0-0,04 кПа; максимальный
0-100 Мпа;
- Пределы приведенной основной погрешности измерений ±0,25%;
±0,5%;
Рисунок 2.2 - Внешний вид датчика измерения расхода Метран - 100ДД
- Диапазон перенастроек пределов измерений М100 до 25:1;
- Наличие взрывозащищенности;
- Межповерочный интервал - 3 года;
- контролирует текущее значение измеряемого давления;
- контролирует и настраивает параметры датчика;
- выбирает систему и настраивает единицы измерения;
- настраивает время усреднения выходного сигнала;
- перенастраивает диапазоны измерения, в том числе на
нестандартные;
- настраивает на «смещенный» диапазон измерения;
- выбирает зависимость выходного сигнала от входной величины;
- производится самодиагностика (непрерывная);
- тестирует и управляет параметрами датчика на расстоянии;
- защищает настройки от несанкционированного доступа.
.2.2 Выбор датчика измерения температуры
Для измерения температуры применяются термопары ТПП10
(платинородий-платиновые). Они измеряют температуру газообразных и жидких,
химически неагрессивных сред. По своим свойствам платинародиевые сплавы и
платина представляют из себя уникальные материалы для термопар. Их главное
свойство - высокое сопротивление газовой коррозии.
- Материал термоэлектродов: Положителый - сплав платинародий
(87% Pt - 13% Rh), отрицательный - платина (Pt);
- Коэффициент термо ЭДС, мкв/°С (в диапазоне, °С): 10-14
(600-1600);
- Диапазоны температуры, °С: от 0 до +1300;
- Температура придельная при кратковременном применении, °С:
1600;
- Класс точности (°C): ±1.0 0 °C - 1100 °C; ± [1 + 0.003 ×
(T − 1100)] 1100
°C - 1600 °C.
- отличной устойчивостью к коррозии;
надежной работой в вакууме (в нейтральных средах менее стабильны).
Недостатки: очень чувствительны ко всем загрязнениям, которые могут
появиться при изготовлении, монтаже или эксплуатации термопары.
.2.3 Выбор исполнительного устройства
В настоящий момент для регулирования зазора дросселя в газовых
трубопроводах и водоводах используется исполнительный механизм МЭО
250/63-0,25-99К (рисунок 2.3).
Рисунок 2.3 - Внешний вид исполнительного механизма МЭО 250/63-0,25-99К
Применяются для перемещения регулирующего органа в САР в соответствии с
командными сигналами, которые поступают от управляющих и автоматических
устройств. Принципом действия механизмов МЭО является преобразование
электрического сигнала, поступающего от управляющего или регулирующего устройства
во вращательное перемещение выходного вала.
Характеристики МЭО 250/63-0,25-99К:
крутящий момент на выходном валу 250 НхМ;
время полного хода выходного вала 64 сек;
полный номинальный ход выходного вала 0,24 об;
управляющее устройство типа ПБР-3 или ПБР-3А.
Климатическое исполнение «У» категория «2»:
диапазон температур окружающего воздуха от - 30 до + 50 ºС;
влажность (относительная) окружающего воздуха до 90%;
вибрация частот от 10 до 150 Нz с амплитудой 0,075 мм для частот до 57-63 Hz и ускорением 9,7 мм/s2 для частот свыше 63 Hz;
отсутствие воздействия прямой солнечной радиации и осадков.
3. Математическое описание АСУ и выбор автоматического управляющего
устройства (АУУ)
.1 Структурная схема и алгоритм работы системы
В качестве пульта управления (ПУ), в представленной АСУ, применяется
персональный компьютер с установленной на него системой визуализации Step7, позволяющей следить за
технологическим процессом. Исполнительным механизмом (ИМ) является МЭО
250/63-0,25-99К, он позволяет с высокой точностью обрабатывать сигнал,
поступающий с контроллера. Дроссель используется в качестве регулирующего
органа (РО). Объект регулирования (ОР) - это горн. Чувствительным элементом
(ЧЭ) системы является термопара типа ТПП10 (платинородий-платиновая).
Функционирование схемы: на контроллер поступает сигнал с датчика
температуры. Производится сравнение этого значения с заданным. При
рассогласовании контроллер выдает управляющий сигнал на исполнительный
механизм. ИМ воздействует на регулирующий орган, изменяя изменяется расход
воздуха и газа и система приходит к требуемому состоянию.
3.2 Определение математической модели объекта
В структурной схеме САУ объект управления представляется в виде
соединения двух звеньев: звена чистого запаздывания и апериодического (рисунок
3.2).
Рисунок 3.2 - Структурная схема объекта управления
Кривая разгона объекта регулирования - это кривая изменения во времени
выходной величины в переходном процессе вызванным однократным изменением
входной величины. Кривая разгона взята из технической литературы [1] и
представлена на рисунке 3.3.
Динамические параметры ОУ определяются по кривой разгона и равняются:
Подставим параметры в структурную схему ОУ и получим математическую
модель ОУ (рисунок 3.4):
Рисунок 3.4 - Математическая модель объекта управления
.3 Определение передаточных функций измерительно-преобразовательных и
исполнительных устройств
Автоматический регулятор на структурной схеме САУ изображается в виде
трех звеньев (рисунок 3.5).
Рисунок 3.5 - Структурная схема автоматического регулятора
Усилительное звено представляет собой коэффициент усиления К р ,
имеющий следующее значение:
Функция исполнительного механизма имеет следующий вид:
Закон регулирования описывается следующим выражением:
Для того чтобы выбрать регулятор и посчитать его параметры настройки,
нужно знать следующее:
· Динамические параметры объекта регулирования:
- Максимальный коэффициент передачи объекта управления
- Постоянная времени объекта управления
· Величину максимального возмущения по нагрузке:
· Главные показатели качества переходного процесса:
- отклонение регулируемой величины динамическое
- отклонение регулируемой величины статическое
- время регулирования рег ≤ 500 с
· Величину, обратную относительному времени запаздывания
· Динамический коэффициент регулирования
· Остаточное отклонение регулируемой величины
Подставим
значения и получим = 0.009 o C
Большое
количество автоматизированных металлургических процессов протекают успешно,
если система имеет один из трёх процессов регулирования:
- С min интегральной квадратичной ошибкой.
По
выражению выберем тип регулятора.
Данному
значению = 0.309 подходит тип регулятора - релейный. Показатель колебательности
М соответствует промежутку 1.3<М<1.8, возьмем процесс с 20%
перерегулированием.
Используя
график зависимости от (рисунок 3.6) при выбранном процессе, определяем что
0.22 при могут обеспечить П -,ПИ- ПИД - регуляторы.
Вычислим возможность применения П-регулятора.
Рисунок
3.7 - Остаточное отклонение на статических объектах: 1 - апериодический процесс;
2 - процесс с 20%-ным перерегулированием; 3 - процесс с min .
Из
графика, изображенного на рисунке 3.7 видно, что при остаточное отклонение
равно
По
определяем величину фактического остаточного отклонения:
Допустимое
значение , поэтому П-регулятор не подходит.
Рисунок 3.8 - Относительное время регулирования на статических объектах.
1 - И - регулятор; 2 - П - регулятор; 3 - ПИ - регулятор; 4 - ПИД - регулятор
Вычислим
возможность использования ПИ-регулятора. По рисунку 3.8 видим, что , тогда не
превышая времени регулирования. Выберем ПИ-регулятор.
Приблизительные
настройки регулятора вычислим по формулам:
- Коэффициент усиления регулятора
3.5 Выбор автоматического управляющего устройства на основе ПЛК
Для любой системы автоматического управления главным устройством является
управляющее устройство. В нашей системе управляющим устройством является
программируемый логический контроллер (ПЛК). Выбирается контроллер на основе
задач, решаемых при помощи разработанной системы.
Для автоматизированной системы регулирования температуры в горне примним
контроллер фирмы Siemens. Контроллер
данной фирмы полностью совместим с другим оборудованием системы. Siemens занимается выпуском контроллеров
разных серий, но основные контроллеры это S7-200, S7-300, S7-400.
Модернизируемую систему относим к среднему классу сложности. Контроллеры
серии S7-300 считаются достаточно мощными и применяются для систем, выполняющих
задачи самой высокой сложности, имеющих не один контур управления и требующих
довольно высокой производительности. Основные технические характеристики
контроллера представлены в таблице 4.
- программируемый контроллер, состоящий из модулей для выполнения
задач АУ;
- контроллер имеет широкий выбор модулей для максимальной
адаптации к условиям выполняемой задачи;
- используются различные структуры ввода-вывода и простота
включения в сетевые конфигурации;
- работа с естественным охлаждением;
- свобода в наращивании функциональных возможностей при
модернизировании системы управления;
Таблица 3 - Основные технические характеристики SIMATIC S7-300овные технически
- большая мощность благодаря большому количеству встроенных
функций.
3.6 Определение математической модели САУ, исследование на динамику
системы
Система автоматического управления представляет собой совокупность
объекта управления и автоматического регулятора определенным образом
взаимодействующих друг с другом.
Структурная схема разработанной САУ изображена на рисунке 3.9
Рисунок 3.9 - Структурная схема разработанной САУ
Структурная
схема будет иметь вид (рисунок 3.10):
Проверим систему на динамику в среде VISSIM.
Программа VisSim является разработкой компании Visual Solutions. Она
предоставляет пользователю графический интерфейс, используя который, мы можем
создать модель из виртуальных элементов с некоторой условностью так же, если бы
мы строили реальную систему из настоящих элементов. Она позволяет создавать, а
потом оптимизировать и исследовать модели систем широкого диапазона различной
сложности.
Рисунок 3.10 - Структурная схема САР
При описании модели в среде VisSim и последующем построении, не
обязательно записывать и решать дифференциальные уравнения. Программа сделает
это сама, по предлагаемой ей исследователем структуре системы. Результат
решения выводится в наглядной графической форме. Программу могут использовать и
те, кто не владеет глубокими познаниями в программировании и математике.
Интерфейс VisSim представляет из себя виртуальный, интерактивный
лабораторный стенд, который обеспечивает построение модели из отдельных блоков,
управления им, контроль результатов и запуск процесса моделирования.
Начальными данными при построении моделей в VisSim является
структурно-алгоритмическая схема объекта или процесса и описывающие их
дифференциально-алгебраические уравнения. В нашем случае это структурная схема
САР, изображенная на рисунке 3.10.
Создадим
(рисунок 3.11) виртуальный аналог нашей системы, в обратной связи которой
включена термопара с передаточной функцией W(s).
На выходе получили, что перерегулирование Ϭ = 40% и время
регулирования tp = 184 c.
Для хороших систем перерегулирование не превышает 30%, поэтому под
настроим регулятор. Например, уменьшим коэффициент до 0,6.
Рис. 3.11 - VisSim - диаграмма
модели исследуемой системы
Меняем значение коэффициента усиления регулятора с 0,76 на 0.6 и получим VisSim-диаграмму модели скорректированной
системы на рисунке 3.12.
Получили систему с хорошими показателями качества работы, удовлетворяющую
поставленным требованиям:
Рис. 3.12 VisSim - диаграмма
модели скорректированной системы
Рис.3.13 Переходный процесс на выходе
системы
4. Конструктивное оформление системы
Шкафы предназначены для установки на них средств
управления и контроля технологическим процессом (ТП), а точнее контрольно
измерительных приборов (КИП). Производят их на заводах электромонтажных
изделий. Несущей основой является каркас из швелера, на который крепят
болтовыми и винтовыми соединениями стенки, панели, двери т.д.
Для монтажа контроллера выберем шкаф Rittal TS 8 габаритами 1000*600 мм:
· Установка в производственных помещениях;
· Уплотнение термоизоляцией из пенопласта стен с
термодатчиками. Их еще обрудуют амортизаторами в местах установки щитов;
· Многоканальные щиты собирают строго по отвесу и уровню, для
того чтобы лицевая панель их находилась в одной плоскости;
· Зазоры в стыках между щитами могут быть не более 2мм.
Крепления их между собой, а так же к полу (фундаменту) должно быть болтовым;
· Панельные щиты крепят вверху к стене специальными регелями,
для увелечения жёсткости;
· При значительных протяжённостях щитовых сборок их монтируют в
виде многограника, П-образной или Г-образной формы. Щиты с пультами
устанавливаются на бетонные основания в двойном полу, либо над кабель-каналами
в бетонном основании пола;
· Ввод кабеля под раму в щит производится из кабель-канала
шита. Перед монтажем шит по месту крепиться к опорной раме (швелеру)
соединениями с помощью болтов, а в углах рамы, для большей жёсткости,
приваривают косынки;
· Щиты малых габаритов монтируют на стенах, коллонах или на
полу
Похожие работы на - Модернизация автоматизированной системы регулирования температуры в горне агломашины Дипломная (ВКР). Другое.
Курсовая работа по теме Государственное регулирование эмиссионной деятельности акционерных обществ
Брянчанинов Собрание Сочинений Читать
Дипломная работа: Совершенствование организации управления персоналом. Скачать бесплатно и без регистрации
Курсовая работа по теме Сущность инфляции. Предпосылки появления
Реферат На Тему Охрана Здоровья Анестезиологов
Темы Сочинений По Роману Отцы
Реферат по теме Теория монополистической и несовершенной конкуренции
Реферат: Raymond Carver Essay Research Paper A silence
Курсовая Работа На Тему Хобл Лечебное Дело
Отчет По Учебной Практике Младший Воспитатель
Курсовая работа: Разработка программы-компилятора
Реферат: Оборудование для фрезерной обработки
Сочинение: Поэт и поэзия в творчестве Б. Пастернака
Доклад: Герман Холлерит
Курсовая работа по теме Государственная политика обеспечения занятости населения Беларуси: приоритеты, направления и формы реализации, результативность
Реферат: Loyalty In Book Characters 2 Essay Research
Дипломная работа: Оценка эффективности инвестиционного проекта на примере ОАО Саянскхимпласт
Реферат Интернет Как Информационное Пространство Содержание
Развивающее обучение по системе Д.Б. Эльконина - В.В. Давыдова
Всероссийское Сочинение 2022 Результаты
Реферат: Анализ деятельности организации ЗАО Новый звук ,
Реферат: European Union Essay Research Paper INTRODUCTIONThe new
Контрольная работа: Интерполирование функций