Методология применения физических и механических способов контроля на примере низкоуглеродистой стали марки 20. Дипломная (ВКР). Другое.
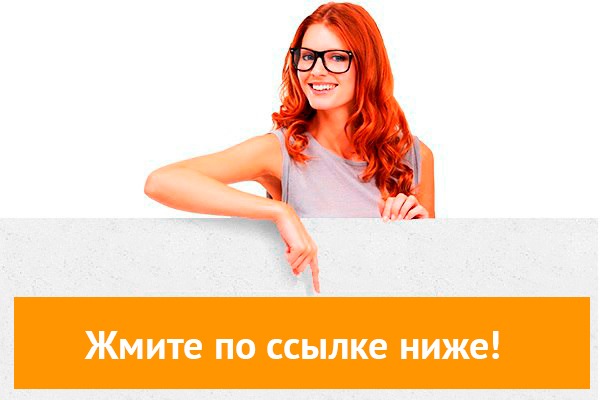
🛑 👉🏻👉🏻👉🏻 ИНФОРМАЦИЯ ДОСТУПНА ЗДЕСЬ ЖМИТЕ 👈🏻👈🏻👈🏻
Вы можете узнать стоимость помощи в написании студенческой работы.
Помощь в написании работы, которую точно примут!
Похожие работы на - Методология применения физических и механических способов контроля на примере низкоуглеродистой стали марки 20
Скачать Скачать документ
Информация о работе Информация о работе
Нужна качественная работа без плагиата?
Не нашел материал для своей работы?
Поможем написать качественную работу Без плагиата!
„Методология применения физических и
механических способов контроля на примере низкоуглеродистой стали марки 20”
1.Изготовление металлографического шрифа
. Испытание материала образцов на ударную вязкость и
сопротивление разрыву
Цель работы: ознакомление с приборами, определение марки стали, выбор
оптимальных режимов термообработки для данной стали, определение механических
свойств, освоение методик микроскопического, дилатометрического,
рентгеноструктурного анализа
Задачи работы: освоить технику приготовления металлографического шрифа и
методику выявления его микроструктуры; ознакомиться с опытом изучения и анализа
характера микроструктуры исследуемой стали; провести испытания, построить
графики, таблицы по результатам исследования.
Краткий обзор стали: Конструкционная сталь, общее название группы сталей,
предназначенных для изготовления строительных конструкций и деталей машин или
механизмов. Конструкционная сталь должна обладать хорошей свариваемостью, в
связи, с чем содержание в ней углерода не должно превышать 0,25%. В обозначении
марки две первые цифры указывают среднее содержание углерода в сотых долях
процента. Примеры марок конструкционных сталей (СНГ): 20, 35, 45, 17Г1С, 40Х,
40ХН, 15ХМ, 30ХМ, 30Х2Н2М, 40ХН2МА, 9ХФ, 5ХНМ, 20Х13, 12Х18Н10Т, 06Х12Н3ДЛ,
10Х12ДЛ.
Химический состав стали марки 20 в %:
С Si Mn
Ni S P Cr Cu As
0.17-0.24 0.17-0.37 0.35-0.65 до 0.25 до 0.04 до 0.04 до
0.25 до 0.25 до 0.08
Сталь 20 считается незаменимым материалом в машиностроении. Критическая
точка нагревания, за которой сталь 20 сохраняет свою прочность 230 - 260
градусов по Цельсию, что свидетельствует об относительно низкой теплостойкости.
Инструменты из стали 20 не применяются для обработки твердых металлов на
больших скоростях. Вследствие низкой твердости сталь 20 обрабатывается резанием
и давлением, а при заточке инструмент из стали 20 трескается. Изготовляют
трубы коллекторов и трубопроводов котлов высокого давления, листы для
штампованных деталей, цементуемые детали для длительной и весьма длительной
службы.
1. Изготовление металлографических шлифов
Место вырезки образцов из изделия определяется задачами
металлографического исследования. Например, ecли необходимо определить природу
дефекта в металле, то образец вырезается таким образом, чтобы плоскость шлифа
пересекла этот дефект. Для установления степени однородности структуры изделия
образцы вырезают из различных мест, располагая их в шахматном порядке по
сечению.
Вырезать образцы можно на обычном или специализированном металлорежущем
оборудовании. Особо твердые материалы разрезают с помощью отрезных абразивных
кругов (эльборовых, вулканитовых и т.п.). При вырезке образцов из крупных
деталей допускается огневая резка, но при этом необходим тщательно следить за
тем, чтобы металл в плоскости будущего шлифа не нагревался. Место реза должно
быть достаточно удалено от плоскости будущего шлифа. При механической обработке
также должны быть предусмотрены меры, исключающие нагрев образца. В последнее
время для этих целей успешно применяются анодно-механическая, ультразвуковая и
электроискровая резка.
С точки зрения удобства проведения дальнейших работ приготовлению
микрошлифов оптимальными являются образцы в виде кубика, призмы, цилиндра с
размерами 10-15 мм (сторона, диаметр, высота). Однако в ряде случаев эти формы
и размеры нельзя обеспечить, в связи, с чем образцы приходится монтировать в
специальные держатели, обоймы, струбцины, в пластические массы или легкоплавкие
сплавы.
Для удаления грубого рельефа и наклепа на поверхности образца,
получающегося при вырезке, применяется обработка шлифовкой. Шлифовка
осуществляется путем истирания поверхности образца при последовательном
переходе ко все более мелкозернистому абразивному материалу.
Шлифовка должна начинаться с наиболее крупнозернистого абразивного
материала, способного за несколько минут создать ровную поверхность образца и
снять следы разрезки. При обработке резцом следы деформации распространяются на
глубину от 250 до 2000 мкм. Обычно шлифовка на станках искажает структуру на
глубину до 75-100 мкм. Чаще всего шлифовку абразивными материалами начинают с
частиц, размеры которых составляют 400-500 мкм. Каждая последующая операция
шлифовки должна производиться на все более мелкозернистом абразивном материале
(перескакивать больше чем через один размер зернистости не рекомендуется).
Важно помнить, что шлифовка предпринимается с целью уменьшения глубины слоя
деформированного металла до такой степени, чтобы в последующем его можно было
бы удалить полированием. Размер царапины и глубина наклепанного слоя под
царапиной становятся меньше с уменьшением размера частиц абразива. Необходимо,
чтобы на каждой ступени шлифовки полностью удалялся слой деформированного
металла, созданный на предыдущей ступени. Для удаления шлифовальных царапин,
нанесенных на предыдущей ступени, направление шлифовки изменяется на 90° при
переходе от одного номера абразивного материала к другому. Шлифовка считается
законченной, когда на шлифе полностью уничтожены видимые простым глазом
царапины (риски). Во время шлифовки образца может происходить его значительный
разогрев, приводящий к изменению структуры (например, отпуск мартенсита в
стальных образцах). Такой дефект уже не может быть исправлен последующей
полировкой. Абразивными материалами, используемыми для изготовления
металлографических шлифов, являются электрокорунд карбид кремния, стекло,
кремень. Эти абразивы наносят на основу (бумагу или ткань), имеющую форму
листов или лент различного размера.
Шлифовать образцы можно вручную на неподвижной шкурке и на шлифовальных
станках. Ручная шлифовка - медленный и трудоемкий процесс, однако при этом
меньше разогреваются образцы, соответственно меньше искажается структура
поверхности, а также уменьшается опасность выкрашивания неметаллических и иных
возможных включений. Более производительна механическая шлифовка.
Полировка представляет собой конечную ступень в процессе изготовления
микрошлифов. Получение зеркальной поверхности шероховатостью примерно Rz
0,05-0,04 мкм, свободной от царапин, является необходимым условием для
проведения правильного металлографического анализа. Используемая методика
полировки не должна создавать дополнительных искажений строения металла (ямок,
взрывов, «хвостов»), не должна приводить к выкрашиванию неметаллических
включений. Перед механической полировкой качество поверхности должно
соответствовать поверхности, обработанной абразивом с размером частиц не более
25 мкм. Полировку выполняют на станках и приборах, подобных используемым для
шлифовки. Для покрытия полировальных дисков применяют фетр, сукно,
высококачественный драп, бархат, различные шелковые ткани и ткани из
искусственного волокна. Поверхность дисков смачивают водной суспензией
тонкодисперсного (до 1 мкм) абразива. Полировка производится одним или
несколькими сортами абразивов, в качестве которых используются окиси алюминия,
хрома, магния, железа и алмазные смеси.
При проведении механической полировки неизбежно возникает некоторое
искажение поверхностного слоя металла. Это не вызывает осложнений при
дальнейшем исследовании, если при последующем травлении слой удаляется, однако
в ряде случаев этого достигнуть трудно.
Травление в жидких средах, избирательно растворяющих отдельные участки
поверхности микрошлифа, один из наиболее распространенных в практике
металлографического анализа методов.
Поверхность металлографического шлифа, покрытую травителем можно
рассматривать как гальванический элемент из большого числа соединенных между
собой микроскопических электродов. Структурные составляющие металла, имеющие
наиболее электроотрицательный электродный потенциал, играют роль
микроскопических анодов и растворяются в травителе-электролите, образуя впадины
на поверхности шлифа. Структурные составляющие с более положительными
электродными потенциалами выполняют роль катодов, оставаясь в первом
приближении неизменными. В результате травления образуется система выступов и
впадин, характеризующих микроструктуру сплава.
При травлении чистого металла или однофазного сплава границы зерен
растворяются интенсивнее, чем поле зерна, образуя углубления, которые при
визуальном наблюдении кажутся темными, вследствие рассеивания на них света.
Зерна чистых металлов различаются по кристаллографической ориентировке.
Вследствие анизотропии растворение зерен в различных сечениях под действием
реактива идет неодинаково. Зерна, растравленные более сильно, кажутся более
темными, так как отражают меньшую часть падающих на них лучей.
Химическое травление осуществляется путем погружения образца в травящий
реактив или протирания образца реактивом с помощью тампона. Во время травления
поверхность шлифа у большинства материалов теряет свой блеск, что и
свидетельствует о протекании процесса травления. Метод протирания используется
в том случае, когда при травлении образуются пленки, препятствующие проведению
процесса выявления структуры. Продолжительность травления чаще всего
устанавливается опытным путем. После окончания травления производится промывка
и сушка образцов. Хранить металлографические шлифы лучше всего в эксикаторах с
влагопоглощающими веществами (хлористый кальций, силикогель и др.). Для
уменьшения окисления микрошлифов при промывке применяют различные пассивирующие
растворы (например, 10-15 г азотнокислого натрия и 3 г углекислого натрия на
1000 см3 воды).[1]
При отражении света от гладкой и чистой поверхности металла оптический
контраст весьма мал. Поэтому специальной подготовкой на поверхности шлифа
стремятся создать рельеф или тонкие пленки (окислов, продуктов травления).
Рельеф на отражающей поверхности способствует возникновению разности фаз
между лучами, отраженными от выступов и от впадин, и рассеянию света (рассеяние
наблюдается при величине неровностей, соизмеримых с длиной волны). При
полировке и травлении поверхностный рельеф (ступеньки, наклонные поверхности)
может меняться.
Контраст в изображении структуры в первую очередь связан с рельефом у
границ зерен, наблюдается обычно после травления чистых металлов и однофазных
сплавов.
Другим результатом травления может быть образование на структурных
составляющих тонких пленок, что приводят к изменению отражательной способности
и к появлению окраски на шлифе, которая может быть связана как с собственным
цветом вещества пленки, так и с интерференционными явлениям. В отраженном свете
собственные цвета тонких прозрачных пленок на металлическом шлифе часто не
обнаруживаются. При освещении белым светом условие появления интерференционного
максимума может быть выполнено для какого-либо одного из непрерывного ряда
значений длин воли спектра и отраженный свет будет иметь определенную окраску.
«Цвет интерференции» должен изменяться с изменением условий наблюдения и с
изменением продолжительности травления. Увеличение продолжительности травления
приводит к утолщению пленки и изменению интерференционной окраски. При очень
большой толщины пленки интерференционные цвета исчезают. Тогда может проявиться
собственный цвет пленки.
Применение микроскопа для исследования структуры металлических материалов
позволяет существенно расширить пределы естественного восприятия глазом.
Видимая величина предмета определяется углом зрения (углом, образованным
крайними лучами, попадающими в глаз от рассматриваемого предмета). Действие
микроскопа сводятся к увеличению угла зрения.
На рисунке 1 дана упрощенная схема металлографического микроскопа.
Структура образца наблюдается благодаря различию в отражающей способности ее
элементов.
Конструкция микроскопа должна обеспечивать жесткость и точность установки
узлов, возможность смены и регулировки отдельных элементов и конструкции в
целом.
Стационарные металлографические микроскопы по конструктивному исполнению
делятся на вертикальные и горизонтальные В горизонтальном микроскопе для
установки оптических узлов и фотокамеры используется оптическая скамья.
Оптические узлы вертикального микроскопа устанавливаются на спектральном
штативе.
Одной из главных характеристик микроскопа является его увеличение, т. е.
обеспечиваемое им изменение размеров изображения, формируемого в глазу
наблюдателя, по отношению размерам изображения, рассматриваемого невооруженным
Для определенности условий принимают, что изображение формируемое микроскопом,
находится в бесконечности, а рассматриваемый глазом предмет на расстоянии
наилучшего зрения(250мм)
Рисунок.1 Упрощенная оптическая схема микроскопа.
В этом случае оптическое увеличение микроскопа, состоящего из объектива и
окуляра, определяется как произведение даваемых ими увеличений:
f’ -
соответствующие фокусные расстояния; -
оптическая длина тубуса.
В
реальных микроскопах между объективом и окуляром размещаются различные
дополнительные линзы и другие элементы оптических схем. Все они в той или иной
мере влияют на увеличение микроскопа, внося соответствующие коррективы.
Дилатометрия
(от лат. dilato - расширяю и ...метрия), раздел физики, изучающий зависимость
изменения размеров тел от воздействия внешних условий: температуры, давления,
электрического и магнитного полей, ионизирующих излучений и т.д. В основном
дилатометрия. изучает тепловое расширение тел и его различные аномалии (при фазовых
переходах и др.). Применяемые для целей дилатометрии приборы называются
дилатометрами. Методы дилатометрии широко применяют при изучении свойств
веществ в физике, а также в материаловедении.
Тепловое
расширение материалов имеет чрезвычайно большое значение в технике. Вследствие
теплового расширения, возможно возникновение термических напряжений в местах
сопряжений деталей из различных материалов, или сплавов.В деталях сложной формы
при неравномерном нагреве. Тепловое расширение является следствием сил
притяжения и отталкивания между атомами кристаллической решетки в процессе
колебательных движений, совершаемых атомами. При повышении температуры, т.е.
при увеличении энергии колебаний атомов, ассиметрия сил притяжения и
отталкивания возрастает, при этом увеличивается смещение атомов относительно
друг друга. Это приводит к изменению линейных размеров деталей и их объемов.
Данное изменение обратимо, если в металле не происходит структурных
превращений. Помимо обратимого изменения размеров, зависящих только от
температуры, металлы при нагреве и охлаждении могут изменять размеры в связи с
фазовыми превращениями, например с полиморфизмом, с распадом пересыщенных
твердых растворов. При этом изменение размеров зависит от времени. Характер его
может меняться в различных температурных областях и при изменении скорости
нагрева. Изучение изменения размеров тел при нагреве и охлаждении занимается
дилатометрия. Основные задачи дилатометрии - определение коэффициентов
характеризующих тепловое расширение материалов при различных температурах,
исследование превращений в материалах в процессе их нагрева и охлаждения, а
также при изотермических выдержках. При этом измеряют лишь температуру начала и
конца превращения, а характеристики теплового расширения материала измеряют только
для температурных интервалов, в которых имеет место собственно тепловое
расширение. В качестве характеристики теплового расширения принят коэффициент
теплового расширения, выражающий относительное изменение линейных размеров
(объема) при изменении температуры на 1 градус Цельсия. Средним коэффициентом
линейного расширения и называется коэффициент, характеризующий тепловое
расширение в интервале от 20 или 0 градусов Цельсия до заданной (рабочей)
температуры.
- средний
коэффициент линейного расширения;
- длинна
образца при начальной температуре;
По
принципу действия дилатометры делят на механические оптические и электрические.
По способу записи кривых: простые(l/t),
дифференциальные( ). Дилатометры на которых можно делать простую и
дифференциальную запись называют универсальными. Достоинствами
дилатометрического анализа по сравнению с термическим является независимость
его результатов от скорости нагрева и охлаждения.
Рис.
2 Схема оптико-механического дилатометра: 1 - исследуемый образец; 2 - шток; 3
- зажим; 4 - зеркало, прикрепленное к валику 5; 6 - магнит, притягивающий
зажим; 7 - источник света; 8 - зрительная труба.
3.
Термическая обработка. Выбор режима термической обработки
Термическая обработка- нагрев металла до определенной температуры,
выдержка при этой температуре до завершения фазовых превращений, с последующим
охлаждением с определенной скоростью.
Отжиг
- смягчающая термическая обработка, нагрев до определенной температуры,
выдержка, охлаждение с печью. Получается металл в равновесном состоянии.
Прочность после отжига падает, а плотность и ударная вязкость повышаются. Отжиг
бывает 1 и 2 рода. Отжиг 1 рода делится на диффузионный, рекристализационный и
отжиг для снятия напряжений. Диффузионный отжиг проходит при высоких
температурах, близких к солидусу, так как при высоких температурах наиболее
интенсивно присходят диффузионные процессы, необходимые для выравнивания в
отдельных объемах состава стали. Происходит устранение дендритной ликвации,
которая повышает склонность стали при обработке давлением к трещинообразованию,
анизотропии свойств и возникновению таких дефектов как шиферность, флокены.
Температуру диффузионного отжига определяют по формуле: . Обычно применяют для легированных сталей.
Рекристализационный отжиг заключается в нагреве холоднодеформированной стали
выше температуры начала кристаллизации, выдержке при этой температуре и
последующем охлаждении. Тотж=Трек +150-200ºС. Этот вид отжига применяют как первоначальную стадию перед холодной
обработкой давлением, как промежуточный процесс между операциями холодного
деформирования и как окончательную термическую обработку. Отжиг для снятия
напряжений проводят с целью снятия внутренних напряжений, образовавшихся в
металле при ковке, сварке и способных вызвать коробление и разрушение детали.
Главный процесс-это релаксация остаточных напряжений. Температура примерно 0,4
Тпл. Отжиг 2 рода-термическая обработка, заключающаяся в нагреве стали до
температур выше критических точек Ас1 и Ас3, выдержке и, как правило, в
последующем медленном охлаждении. Отжиг 2 рода связан с фазовыми превращениями.
Делится на полный, неполный и нормализация. Полный отжиг применяется для
доэвтектоидных сталей и состоит в нагреве стали на 30-50ºС выше точки Ас3, выдержке при этой температуре до
полной перекристаллизации металла и медленном охлаждении. При таком отжиге
образуется мелкое аустенитное зерно, из которого при охлаждении формируется
мелкозернистая ферритно-перлитная структура. Скорость охлаждения зависит от
устойчивости аустенита, т. е. от состава стали. Неполный отжиг- сталь нагревают
выше Ас1,но ниже Ас3. Этот вид отжига предназначен, в основном, для
эвтектоидных сталей для улучшения обрабатываемости их резаньем, так как в
результате образуется мягкий перлит. Неполный отжиг широко применяется для
заэвтектоидных углеродистых и легированных сталей. Изотермический отжиг
применяют для улучшения обрабатываемости легированных сталей. Он состоит в
нагреве на 30-50ºС выше Ас3 и сравнительно быстром охлаждении до
температуры Аr1, изотермической выдержке при этой температуре для
получения равновесной перлитной структуры и последующем охлаждении на воздухе.
Если
при проведении отжига охлаждение после нагрева и выдержки проводится на
воздухе, то такой процесс называется нормализацией. При нормализации сталь
нагревают до температуры выше линии GSE и охлаждают на воздухе.
Ускоренное охлаждение обуславливает несколько большее переохлаждение аустенита.
Поэтому получается более мелкое зерно и более тонкое строение
эвтектоида(сорбит). Также уменьшается выделение вторичных фаз. В результате
прочность стали становится больше, чем прочность после отжига. Нормализацию
применяют как промежуточную операцию для смягчения стали перед обработкой
резаньем, для устранения пороков и общего улучшения структуры стали перед
закалкой. Нормализацию применяют для сталей с содержанием углерода до 0,3 % для
снятия внутренних напряжений. Для сталей с содержанием углерода больше 0,3 %
нормализацию проводить нельзя из-за угрозы подкалки, т. е. получения структуры
сорбита. Нормализацию для заэвтектоидных сталей проводят с целью растворения
сетки цементита выше Асm на 30-50ºС, но зерно будет крупное и необходим неполный отжиг.
Закалка
стали состоит в нагреве ее выше температур фазовых превращений, выдержке для
завершения всех превращений и охлаждения с высокой скоростью с целью получения
при комнатной температуре неравновесных структур, обеспечивающих более высокую
прочность и твердость стали. В зависимости от температуры нагрева различают
полную и неполную закалку. При полной закалке нагрев осуществляют выше Ас3 или
Асm. Для доэвтектоидных сталей обычно применяют полную
закалку, т. е. нагревают выше Ас3 на 30-50ºС и охлаждают в воде. Для заэвтектоидных сталей применяют неполную
закалку, так как наиболее благоприятная структура этих сталей достигается
тогда, когда включения вторичного цементита имеют форму сфероидов- зернистую
форму и отсутствует сетка цементита по границам зерен, так как она увеличивает
хрупкость. При закалке стараются получать мартенситную структуру (пересыщенный
твердый раствор в άFe.)
В зависимости от скорости охлаждения можно получить различные структуры. Время
закалки будет выражаться из зависимости 1 минута нагрева на 1 мм сечения
образца. Время выдержки 1/5 от времени нагрева.
Для
стали марки 20 была выбрана полная закалка при температуре 850 ºС в течении 12 минут. Такой выбор термической
обработки стали обусловлен тем, что нам необходимо было получить мартенситную
структуру, с максимально высокой твердостью, а при применении неполной закалки
наличие феррита в структуре закаленной доэвтектоидной стали только уменьшит
твердость. Предварительно образцы были заклеймены с торцов.
4.
Испытания материала образцов на ударную вязкость и сопротивление растяжения.
Рисунок 3 На рисунке изображена схема устройства и способ установки
образца для испытаний, где 1 маятник; 2 - образец; 3 - стрелка; 4 - шкала.
На образце перед испытанием предварительно делают треугольный
миллиметровый надрез в средней части для того, чтобы обозначить место начала
разрушения при ударе маятника.
Ударная вязкость - способность материала поглощать механическую энергию в
процессе деформации и разрушения под действием ударной нагрузки. Основным
отличием ударных нагрузок от испытаний на растяжение-сжатие или изгиб является
гораздо более высокая скорость выделения энергии. Таким образом, ударная
вязкость характеризует возможности материала по быстрому поглощению энергии.
Испытания проводятся на приборе, называемого маятниковый копёр. Прибор основан
на превращении потенциальной энергии поднятого тяжёлого маятника в энергию
разрушения металлического образца.
Ранее разрушение рассматривалось как заключительная мгновенная стадия
нагружения, которая не может быть остановлена. В настоящее время выявлено, что
стадия разрушения с момента выявления повреждения может составлять до 90 %
долговечности конструкции. Разрушение твердого тела представляет собой разрыв
межатомных связей с образованием новых поверхностей. Если разрыв межатомных
связей происходит перпендикулярно плоскости разрушения, то такое разрушение
происходит сколом или отрывом. Если разрыв связей идет под действием силы,
приложенной параллельно плоскости разрушения, то происходит разрушение сдвигом
или скольжением. При этом характер разрушения зависит также от температуры,
скорости диффузии, напряженного состояния, чистоты металла и т.д. В зависимости
от степени пластической деформации перед разрушением различают два основных вида
разрушения: хрупкое и вязкое. Хрупкое разрушение происходит путем отрыва или
скола, когда плоскость разрушения перпендикулярна нормальным напряжениям. Такое
разрушение начинается от какого-либо дефекта, вблизи которого развивается
концентрация напряжений, превосходящих теоретическую прочность материала. Под
действием нормальных напряжений происходит упругая деформация кристаллической
решетки, а после достижения предельной степени ее искажения происходит
последовательный разрыв межатомных связей с отрывом одной плоскости от другой.
У достаточно пластичных материалов, характеризующихся релаксацией напряжений,
местные концентрации напряжений вблизи дефектов оказываются недостаточными и
развитие скола не происходит. Вязкое разрушение происходит путем сдвига под
действием касательных напряжений. Плоскость скольжения располагается под углом
45° к направлению главных нормальных напряжений. Характерными признаками
вязкого и хрупкого разрушений являются:
вид трещины и поверхности разрушения
При разрушении по хрупкому механизму затрачивается значительно меньшая
работа на процесс самого разрушения, чем при вязком, т.к. начавшееся хрупкое
разрушение является самопроизвольным процессом. Оно происходит за счет высвобождения
накопленной в системе упругой энергии. И поэтому для распространения трещины не
требуется подвод энергии извне. При вязком разрушении для его развития
необходим непрерывный внешний подвод энергии, расходуемой на пластическое
деформирование металла впереди растущей трещины и преодоление возникающего при
этом упрочнения. При этом работа, затрачиваемая на пластическую деформацию
значительно превышает работу собственного разрушения. При хрупком разрушении
магистральная трещина имеет малый угол раскрытия(острая трещина). При вязком
разрушении трещина имеет большой угол раскрытия(тупая трещина). Поверхность
разрушения характеризуется значительной степенью деформации. При низких
температурах межзеренные границы обычно прочнее самих зерен, поэтому у большинства
металлов при низких температурах разрушение имеет транскристаллитный характер и
проходит по зернам, а не по границам. При повышенных температурах межзеренные
границы обычно слабее зерен. Микроизлом при хрупком разрушении имеет блестящую
гладкую поверхность. Плоские грани расколотых кристаллитных зерен придают
металлический блеск хрупкому излому. Под электрическим микроскопом хрупкий
излом имеет ручьистое строение, является следствием взаимодействия движущейся
трещины с дефектами кристалла, а также на нем обнаруживается наличие
предпочтительных кристаллографических ориентировок. Излом при вязком разрушении
имеет матовый волокнистый характер без металлического блеска. Для хрупкого
разрушения характерна высокая скорость распространения трещины. Для сталей она
составляет примерно 2000м/с. Для вязкой трещины она ниже, определяется
скоростью нарастания напряжений. В случае вязкого разрушения мерой борьбы
является повышение прочности материала. В случае хрупкого разрушения
увеличиваем вязкость.
Предназначен для испытания на сжатие образцов сравнительно не больших
размеров. При помощи специальных приспособлений на прессе можно проводить
испытания образцов на растяжения, изгиб и срез. Например, на рисунке 2 показаны
преобразования сжимающего усилия в усилие, растягивающие образец с помощью
реверсора. Особенностью пресса является возможность получения на нем диаграммы
растяжения, то есть зависимости между усилиями Р и продольной деформацией ∆
l образца, в большом масштабе.
Принцип работы Реверсор
с образцом при испытании на растяжение устанавливается на подставке. От
электромотора через систему ременных и червячных передач вращение передается на
зубчатый обод массивной гайки. При вращении гайки вокруг вертикальной оси из
нее выдвигается винт, соединенный с нажимной плитой пресса. Вдоль винта имеется
продольный паз, в который входит шпонка станины пресса вызывающей деформацию
образца.
Диаграммы растяжения или сжатия вычерчиваются на миллиметровой бумаге,
обернутой вокруг барабана. Барабан вращается и при помощи пера, вычерчивается
диаграмма. После разрыва обе части образца плотно складывают и измеряют длину
между головками l к , диаметр шейки d к , рассчитывают площади F в и F к . Прочность - это способность металла
сопротивляться деформации и разрушению. Деформацией называется изменение
размеров и формы тела под действием внешних сил.
Деформации подразделяются на упругие и пластические. Упругие деформации
исчезают, а пластические остаются после окончания действия сил. В основе
пластических деформаций - необратимые перемещения атомов от исходных положений
на расстояния, большие межатомных, изменение формы отдельных зерен металла, их
расположения в пространстве.
Способность металлов пластически деформироваться называется
пластичностью.
Для испытаний на статическое растяжение используют образцы как с круглым,
так и с прямоугольным сечением. Предъявляются повышенные требования к
изготовлению образцов, как с точки зрения геометрии, так и с точки зрения
обработки резанием. При изготовлении образцов следует избегать перегрева
материала и изменений его микроструктуры.
Образцы круглого сечения, как правило, имеют рабочую длину, равную
четырём или пяти диаметрам - т. н. короткие образцы или десяти диаметрам - т.
н. нормальные образцы. Перед началом испытания замеряется диаметр образца
(обычно 6, 10 или 20 мм) для вычисления напряжения σ и для расчёта относительного
остаточного сужения после разрушения образца. При отсутствии экстензометра (не
рекомендуется стандартом), отмечается рабочая длина образца, деформация ε рассчитывается по перемещениям конца
образца (захвата), а относительное удлинение при разрушении рассчитывается
путём замера разрушенного образца.
Основным и наиболее распространенным является испытание на растяжение,
при котором удается получить наиболее важные характеристики материала,
находящие прямое применение в расчетной практике.
При растяжении образца изучают зависимость между действующей нагрузкой и
соответствующим удлинением. Графическое изображение этой зависимости называют
д
Похожие работы на - Методология применения физических и механических способов контроля на примере низкоуглеродистой стали марки 20 Дипломная (ВКР). Другое.
Реферат: Immigration Paper Essay Research Paper American Immigration
Сочинение Мой Любимый Поэт Серебряного Века Бунин
Реферат по теме Дилерская и брокерская деятельность
Курсовая работа по теме Оценка сельскохозяйственных животных
Ловушки Нефти И Газа Реферат
Великобритания В Новейшее Время Реферат
Реферат: Церковь и интеллигенция. Скачать бесплатно и без регистрации
Вторичный и третичный гиперпаратиреоз
Банковская Система России Эссе
Порядок Назначения И Выплаты Пенсий Курсовая
Отчет По Практике Финансового Учета
Курсовая работа: Экономико-географическая характеристика Гренландии
Этапы Созревания Мозга У Детей Реферат
Геометрическая характеристика злп. n-мерное пространство. Выпуклое множество. Граничные и крайние точки, выпуклый n–мерный многогранник.
Контрольная работа по теме Особенности развития представления о времени у дошкольников
Научная Работа На Тему Модель Работы Зао Кб "Кедр"
Реферат: Совершенствование процесса принятия управленческих решений 2
Краткие Рассказы Для Декабрьского Сочинения
Профориентация Управления В Организации Реферат
Принцип Работы Контрольно Измерительной Аппаратуры
Реферат: Вопросы к экзамену по макроэкономике
Реферат: Научно-методические основы
Реферат: Поздние стадии эмбрионального развития