Mastering the Work with Molds for Injection Molding: Essential Tips and Tricks
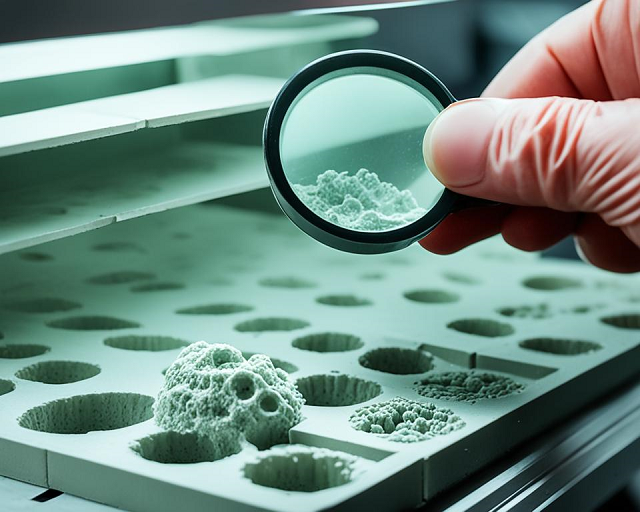
At the heart of manufacturing, the prowess of injection molding techniques stands out as a testament to the wonders of modern engineering. This intricate process is pivotal in creating detailed components that form the backbone of countless products we use daily. By delving deeply into the art of optimizing injection mold performance, professionals in the industry unlock the potential for monumental efficiencies and a leap in product quality. It's a field where precision meets practicality, and where every nuance from design to execution can sway the outcome significantly.
To truly master this domain, a comprehensive understanding of injection mold maintenance is indispensable. Through this article, we bridge the gap between the complexities of the process and the craftsmen who make it sing, offering a treasure trove of insights that cater to both the novices and the veterans in the field.
Aimed at molding maestros seeking to refine their craft, the subsequent sections will unfold a series of indispensable tips and tricks. These will range from the crucial considerations in material selection and design intricacies to the diligent assembly and preparation of molds, all directed towards achieving a state of perfection in the injection molding process.
Key Takeaways
- Understanding the fundamentals of injection molding for better process control.
- Selection of mold materials and design to enhance product quality.
- Implementing effective injection mold maintenance practices.
- Maximizing efficiency with advanced injection molding techniques.
- Strategic insights to optimize injection mold performance.
- Techniques for precise mold assembly and preparation.
Understanding the Basics of Injection Molding
The injection molding process is a cornerstone of modern manufacturing, enabling the rapid and efficient creation of high-quality plastic components. Fundamental to this process is proficiency in mold design basics and the application of precise plastic injection techniques. By examining the steps from start to finish, we can appreciate the intricacies involved in producing complex, high-precision parts.
https://www.youtube.com/watch?v=sBEzE4PCmqM
Every cycle of injection molding begins with the clamping of the molds for injection molding. This is a critical step, as it determines the stability of the mold during the injection of the material. After clamping, manufacturers move to the injection phase, where molten plastic is propelled into the mold cavity. Subsequent cooling is essential as it solidifies the injected material, molding it into the desired shape. Finally, the process culminates with the ejection of the finished product, ready for inspection and assembly.
Highlighted below is a table that outlines key factors affecting the quality of injection molded parts. Understanding these variables is pivotal for manufacturers to control the quality and precision of their output.
Quality FactorWhy It MattersControl MethodTemperatureEnsures proper material flow and part solidityMeticulous temperature regulationPressureImpacts material injection and part densityPrecise pressure applicationMaterial ChoiceInfluences the strength and aesthetic of the partSelection of suitable plastics based on part requirementsTo master the injection molding process, it is essential to delve deep into the mold design basics, as this will set the foundation for creating high-precision parts. Additionally, versatile plastic injection techniques must be adopted to cater to the particular needs of each unique project. As we move further into the expansive world of injection molding, one cannot emphasize enough the importance of these fundamentals for delivering quality and efficiency.
Finding the Right Material for Your Molds

Choosing the ideal materials for injection molds is a pivotal factor that can influence the overall success of the manufacturing process. It's essential to consider the unique characteristics of mold materials and how they correlate with the operational demands of thermoplastics. Selecting the most suitable materials not only impacts the mold's ejection efficiency but also its durability, playing a critical role in both the quality of the final products and the longevity of the mold itself.
Comparing Thermoplastics: Pros and Cons
- ABS: Offers good mechanical properties and is easy to work with but can be prone to warping during cooling.
- Polycarbonate: Known for its excellent strength and impact resistance yet may require higher processing temperatures.
- Polypropylene: Offers great chemical resistance and flexibility; however, it has a lower melting point which can affect mold design.
- PEEK: High-temperature resistance and mechanical strength but can be significantly more costly.
Assessing Material Flow and Ejection Tendencies
Analyzing how mold materials behave during the injection molding process is vital for ensuring ejection efficiency. As thermoplastics have varying flow rates and cooling behaviors, these properties must be closely aligned with the mold design to prevent defects and enhance the ease of part ejection.
Material Durability and Mold Longevity
The durability of mold materials directly affects mold longevity. Choosing high-wear-resistant materials can minimize downtime for repairs and reduce the overall cost of operation. Ensuring mold materials are selected based on their compatibility with thermoplastics can extend the life of the mold and guarantee the production of quality parts repeatedly.
The intricate world of injection molds demands a level of sophistication in design that can only be achieved through rigorous planning and technological aid. In this regard, CAD for molds stands at the forefront of facilitating the meticulous level of detail required for mold design optimization. Below we explore several strategies pivotal to enhancing mold performance and ensuring the production of high-quality parts.
Enhancing Mold Performance with CAD Design
The incorporation of Computer-Aided Design (CAD) software has revolutionized the way industries approach mold design. CAD for molds is not only about drawing precise plans; it is an indispensable tool for simulating mold performance, evaluating potential issues, and enabling complex geometries that were once deemed unattainable. The optimization facilitated by CAD leads to molds that are not only accurate but also ensure cost-effectiveness in the long run by reducing the need for time-consuming revisions.
Strategies for Reducing Cycle Time
Reducing the cycle time of an injection mold is synonymous with enhancing production efficiency. One of the most effective strategies for cycle time reduction lies in the optimal design of cooling systems and runner layouts. By decreasing the time required for cooling, manufacturers can significantly cut down the overall cycle time, allowing for faster turnaround without compromising the integrity of the parts produced.
Maintaining Precision in Part Tolerances
When it comes to high-quality part production, maintaining precision tolerances is non-negotiable. Meticulous mold design optimization ensures that each part meets the stringent standards required for functionality and interoperability. The role of precision engineering in mold making cannot be overstated, and it is here that CAD for molds plays a crucial role, allowing for adjustments to be made with a level of accuracy that manual methods cannot achieve.
Mold Design FeatureImpact on Cycle TimeImpact on TolerancesCooling System DesignDirectly reduces cooling phase duration.Prevents warping, ensuring dimensional stability.Runner System OptimizationMinimizes material flow time.Enhances consistency in filling, reducing defects.Gate LocationImproves filling time and pressure requirements.Offset gate-related blemishes, maintaining aesthetics and function.
Molds for Injection Molding: Assembly and Preparation Techniques
The assembly and preparation of molds are critical steps in the injection molding process that directly impact the efficiency and quality of the final product. Approaching mold assembly requires meticulous attention to detail such as ensuring the precise alignment of mold halves, which is crucial to prevent defects in the molded parts. It is equally important to carefully install pins or inserts, as their correct placement is necessary to maintain the integrity and consistency of each part produced. These initial steps set the foundation for an optimized injection mold setup, contributing to a seamless production flow.
Once the structure of the mold is assembled, mold preparation practices come to the forefront. Here, the focus turns to ensuring all components are thoroughly lubricated to facilitate smooth operation during the molding cycle. Additionally, bringing the mold to the appropriate operating temperature is key to preventing issues such as warping or undesired material properties. Preheating the mold helps in controlling the thermal balance, reducing the occurrence of flash and misalignment when the molten plastic is injected. This preparation not only enhances the performance of the mold but also extends its life by mitigating thermal stress.
Effective injection mold setup is rounded off by a series of checks and tests aimed at preempting any potential disruptions. These can include inspecting the mold for any signs of wear or damage, and verifying that all settings on the injection molding machine align with the material and design specifications. Taking the time to rigorously prepare the mold ensures that each production run starts off on the right foot, leading to consistent quality and reduced downtime. Armed with these techniques, industry professionals can fine-tune their processes for optimal outcomes in injection molding.
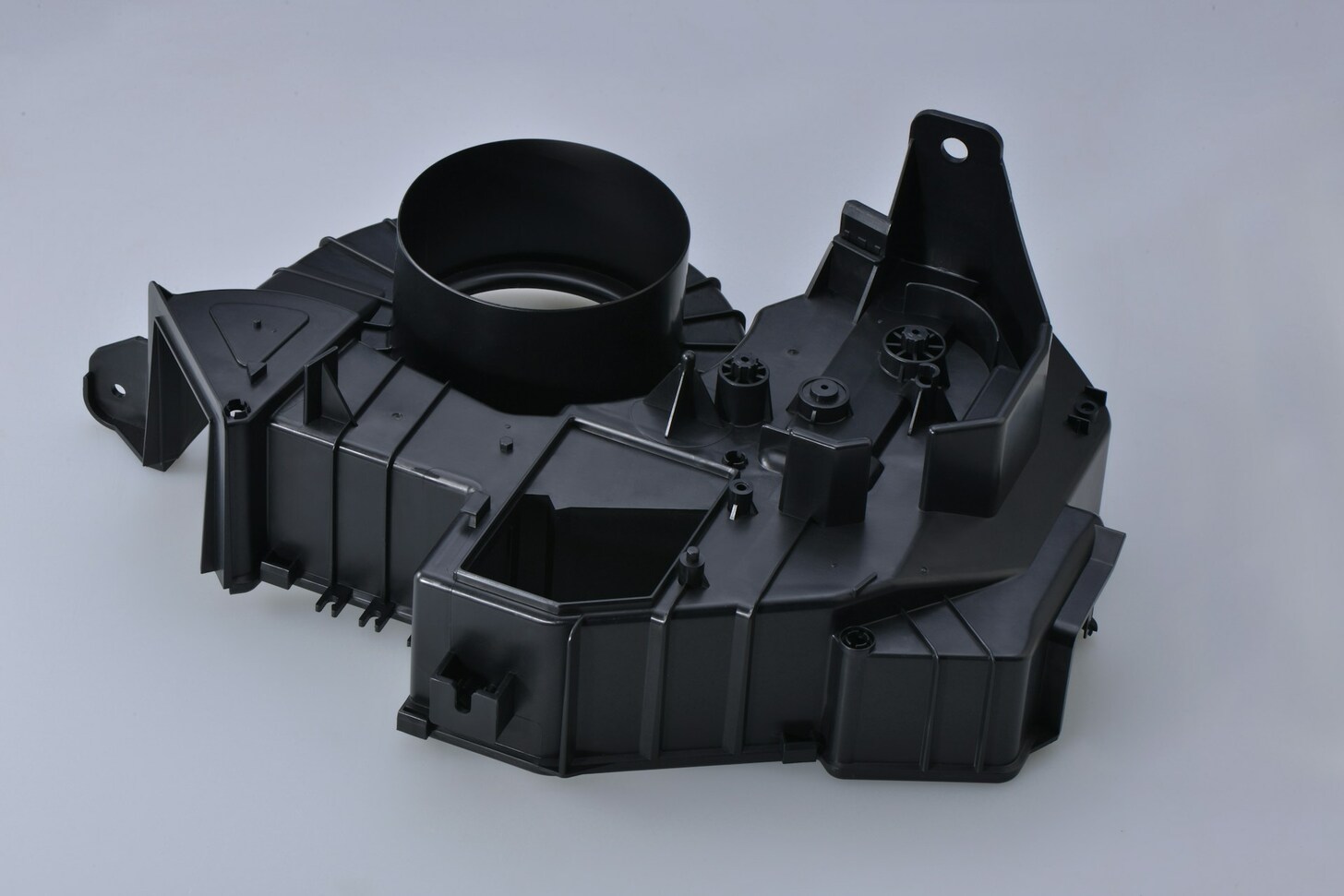