Making everyday objects out of plastic is common, even habitual.
mouldinginjectionTo do this, many companies offer various techniques, including plastic injection molding manufacturer. In Europe, we face competition from manufacturers who do not have the same ethics as we do. We have focused our production on relocating cheap injection moulds to France and Belgium.
But before presenting the manufacturing policy of our production unit, it is important, even essential, to specify what Plastic Injection Molding represents. What is this process that facilitates design? What can be achieved using this state-of-the-art plastic technology? What plastics are used in our designs? Let's take a look at Plastic Injection Molding at your fingertips.
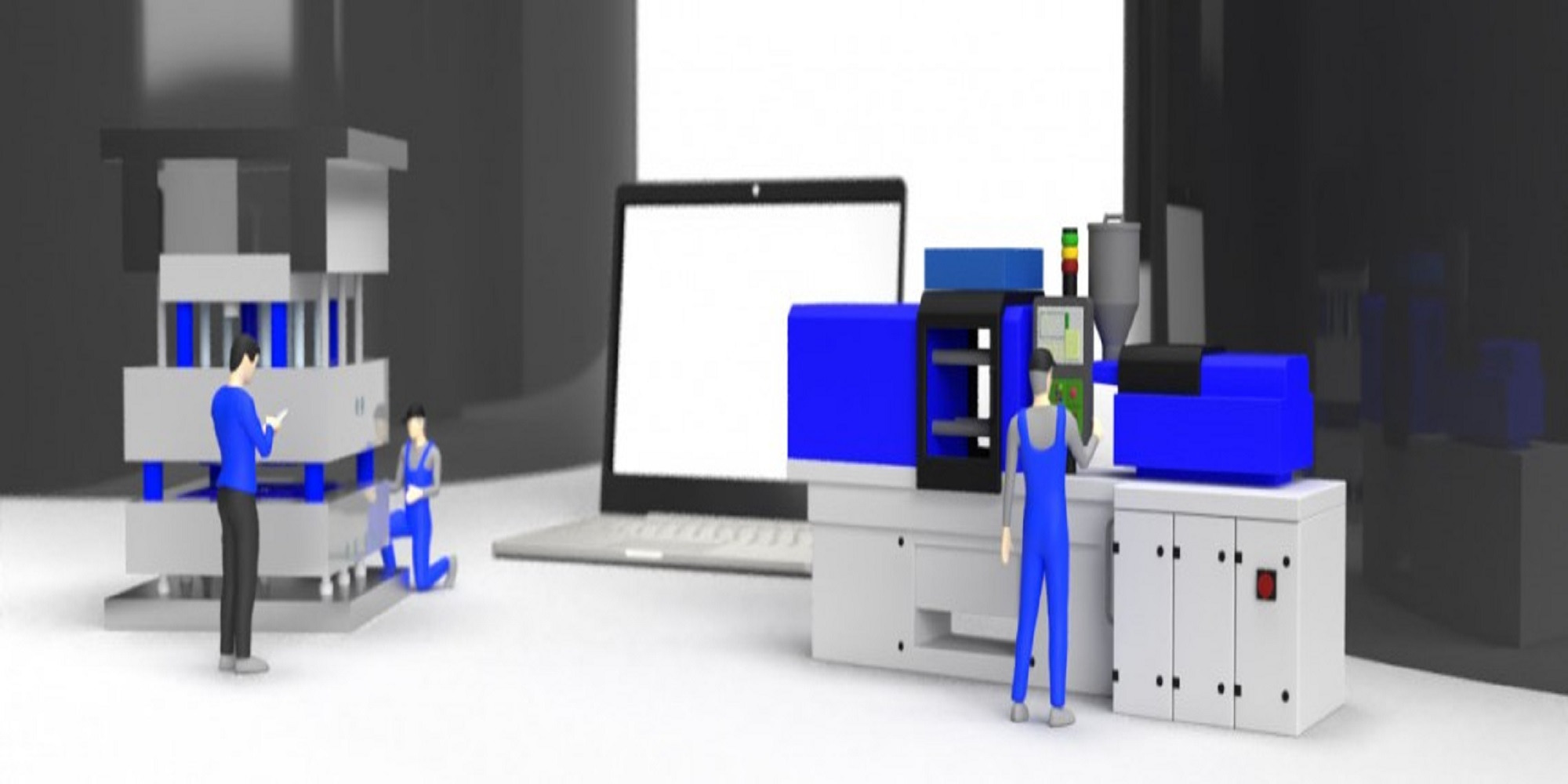
1. What is plastic injection moulding?
In order to reproduce parts on a large scale, the technique of molding dates back to the dawn of humanity. Egyptian artefacts, for example, bear witness to the mastery of this technique with various metal alloys. Many civilisations have used this technology to produce coins bearing the effigy of monarchs, artillery components and many other everyday objects.
The lost-wax technique has also had many followers. Of course, the advent of plastics in the 20th century completely changed the casting industry. Whereas metals were heavy and alloys difficult to stabilise, plastic and consequently plastic molding became the material of choice for the production of various parts. The process is based on the injection of pre-melted plastics into moulds of different shapes and sizes. When the plastic cools, its appearance permanently takes on the shape given to the mould.
Plastic injection molding thus allows the large-scale production of plastic parts of various origins. However, there are tolerance limits for the different qualities of plastic which can prevent the production of particularly complex mouldings. For this reason, it is necessary to call on the services of a specialist in plastic injection moulding in order to obtain quality designs.
The processes of production and product design have developed as we've advanced from revolutionary breakthroughs like the light bulb to the telecommunications age of radio, phones, and TVs. The advancements in current injection frisbee are driven by computers, the internet, renewable electricity, and all that follows after. However, before we can grasp where we're headed, we must first understand how we got here.
2. What plastics are used and what are their characteristics?
As our plastics industry is very rich, there are thousands of different types of plastics, which makes their characteristics and aesthetic specificities very diverse. However, there are two main groups that can be used to make a Plastic Injection Mould:
- Thermoset plastics: to make a plastic thermoset, it must undergo polymerisation, which makes its structure irreversible. It is therefore impossible to recycle them. They are used in liquid or paste form. On the other hand, their increased strength makes them very durable.
3. What are the main plastic injection moulding techniques?
Different plastic injection moulding techniques can be developed. Each has its own specificities depending on the quality of the material, its thickness and the quantity of parts to be produced.
- Low-pressure plastic injection moulding: this is a process that consists of filling the bottom of an open mould. The mould is connected to a pipe underneath so that the molten plastic rises. This type of moulding makes it possible to produce fairly large parts in small series. This is the case for the plastic injection of polycarbonate showers;
- Thermoforming moulding: this is a plastic processing technique adapted to parts with a simple geometry, particularly rounded parts. A plastic sheet is heated in an oven to make it malleable and placed over the mould. The mould, connected to a vacuum system, comes into hermetic contact with the plate, and all that remains is to suck out the air so that the plate adheres perfectly to the mould.
- Thermocompression moulding: its main advantage is that it is done in one go. The heated material is then distributed in single or multi-layers depending on the thickness of material required. It is then processed in a press to obtain the desired shape. This process, which superimposes several layers, improves the mechanical characteristics of the part;
- Overmoulding: this is a technique that allows plastic material to be added to a specific point on an existing product. The target location can be on the surface or inside depending on the need to reinforce the base part. It is a technique that allows the optimisation of an assembly in order to quickly commercialise small and medium series;
- Bi-injection moulding: thanks to this innovative technique, two different materials are injected through two pipes into the same mould. The result is a mixed product with combined specificities.
Our company is constantly looking for performance in order to produce low-cost injection moulds by reducing its production costs. Limiting transport and controlling the production chain allows us to meet this objective. By calling on our professionalism to produce plastic injection moulds quickly, you are assured of a reliable service that meets your expectations. Whether it is for a plastic injection molding France or any other request concerning our plastic production units, we are at your disposal.