Machine Tube
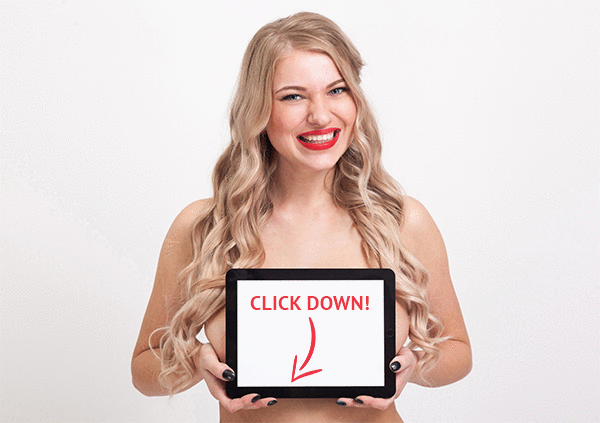
⚡ ALL INFORMATION CLICK HERE 👈🏻👈🏻👈🏻
Machine Tube
增值电信业务经营许可证:浙B2-20080224 | 增值电信业务经营许可证(跨地区): B2-20150210 | 浙网文【2022】0403-017号 | 浙江省网络食品销售第三方平台提供者备案:浙网食A33010001 |
互联网药品信息服务资格证书(浙)-经营性-2018-0010 | 短消息类服务接入代码使用证书:号【2016】00154-A01 | 信息网络传播视听许可证:1109364号 | 出版物网络交易平台服务经营备案号:新出发浙备字第002号 |
Copyright © 2022 SaintyCo ® . All Rights Reserved
Do you want to package liquids, semi-liquid or paste?
Well, you may consider using tubes – it is a perfect packaging material.
Therefore, you need a tube filling machine.
And, in this guide, you will learn various aspects of tube filling machines from tube feeding, filling, folding, sealing, marking, code printing, packaging, etc.
By the end of this guide, I will recommend 12 tube filling machines (I want to help you know and choose suitable equipment).
It refers to the type of equipment that you use to fill up a wide range of products in various tubes.
When manufacturing products such as creams, cosmetics, adhesives, sealants, greases, and some pharmaceuticals, you need to package them.
And the nature of such products makes it difficult for you to merely pack them effectively and faster.
So, this is where the essence of this machine becomes fundamental since you’ll use it to fill the products into respective tubes or containers.
This type of machine has been in the industry for quite a considerable time but has been developing technologically, as time goes by.
It thus implies that the kind of tube filling instrument that was available in the earlier days can no longer sustain the manufacturing needs.
The advancements, of course, are tailored to enhance the performance, efficiency as well as the convenience of the manufacturing process.
Of which is of great significance as you’ll later come to learn about the benefits of this machine.
The tube filling equipment come in different sizes, designs, shapes, as well as capacity.
And before we delve into understanding more about this machine, let’s first look at its benefits which makes it an ideal acquisition.
One important factor that we can’t rule out is that packaging is a significant aspect of the business.
Remember packaging is a vital determinant in the sale of a product.
Certainly, a product sells better if it has an attractive appearance, which unquestionably is an excellent approach to enhance sales.
And therefore, you have every reason to invest in an ideal tube filling machine.
The benefits you obtain by having this equipment are numerous and equally important.
So let’s look at some of the benefits of investing in this type of equipment in your industry;
Suppose you’re using human labor to fill up the tubes for a particular product you’re producing, you can imagine how many people you’ll need.
It doesn’t matter the method that they’ll use to fill up the product.
What matters most is the amount of money you’ll have to spend in compensating them for the work they do.
With a tube filling unit, you need close to zero human labor.
All you need is an operator who ensures that every component of the machine is effective and appropriate.
And therefore in a great way, you’ll realize that having this kind of machine reduces labor needs and charges to a considerable extent.
Evidently, the essence of this is that you’ll increase your profit turnover other than convenience and efficiency in the production process.
You may not want to read this, but here we go.
The truth is that nowadays, the only way of profiting from a production process is by optimizing speed.
The speed at which you produce and fill up your products and taking them to the market plays a huge role in the success of any business.
Remember there are no end users who are merely willing to wait for you to take your precious time and produce when it’s convenient for you.
So using this machine allows you to fill up the particular products in the respective tubes within the shortest time possible.
You’ll find that you quickly fill up thin free-flowing products as well as the high viscous items in multiple containers in just one cycle.
Filling tubes faster – Photo courtesy: Kelly Xu
In fact, you can find some tube filling machines with the capacity of filling more than 120 tubes per minute.
And undoubtedly you can imagine the number of tubes you can fill up per day at that rate.
The bottom line here is that this machine increases efficiency in the production process of different items to fill up in tubes.
When you choose to fill the product in tubes manually, expect to have a lot of variances in the amount each bottle will contain.
Clearly, there are a few measuring devices which you can use to mitigate such variances.
But that notwithstanding, such devices may require you to add more time which can, of course, affect the production process adversely.
So the moment you choose to use this type of machine you’re guaranteed of repeatable, reliable and homogeneous fill with every cycle.
Section of tube filling machine – Photo courtesy: Jack Du
It doesn’t matter if the fill is on the basis of weight, volume, level of any other measurement for that matter.
Let me tell you one fact you probably didn’t know about tube filling machines.
You’ll hardly come across one which is specifically designed for a single product, container or tube.
Most of them allow you to set up different types of containers regardless of the size or shape.
Different sizes of tubes – Photo courtesy: NJS Packaging
Additionally, most of these machines can also handle multiple products.
Some of them can also fill up both thin and viscous products.
If your company packages several products in various containers, then the versatility of this filling equipment can be the ultimate benefits of all.
So fundamentally, you require this machine for its versatility ability which also reduces your cost and enhances production.
The tube fillers seemingly require lengthy set up irrespective of how you look at it for the first time.
And that aspect should never confuse you with the actual operation of the equipment to think that it’s also cumbersome.
In fact, you’ll only need a few hand adjustments from time to time particularly when changing bottles from one bottle to another.
Easy to change tube filling station
Some of the critical settings including, pump speeds, indexing times, and fill times among others will be set on the touchscreen interface.
And once you formulate the ideal settings for particular bottler fill up combination, you’ll only need to relax and monitor the progress.
So in a big way, using this equipment enables you as an operator to experience better working conditions.
Which incidentally is vital by any standards because it enables you to be productive and useful all the time.
Using a tube filling machine is one of the surest ways of preventing the products from unnecessary wastage.
Unlike hand filling, which ends up wasting a considerable amount of the item you’re filling, this machine guarantees precision.
Precise toothpaste filling machine – Photo courtesy: PENGLAI INDUSTRIAL
Such that it measures the exact amount of product that you need to fill in each container hence avoiding incidents of wasting the same.
Furthermore, the machine only needs you to set the necessary level to get into the tube appropriately,and you’re good to go.
Using this type of filler machine gives you the opportunity to grow depending on the manufacturer’s packages.
You can start with a simple tube filling machine which has few fill heads let’s say like four, six or even eight.
But with time, the production demands shall grow. And this would mean that the need for more fill heads become a necessity.
Easy to upgrade tube filling station
So you’ll have to get filler equipment with even more than 16 fill heads which allow more containers to fill up in a single cycle.
Understandably, the model of the machines will differ regarding limits, and the speed will depend on elements like bottle size, shape and product itself.
Well, the point I’m trying to put across, in this case, is that using this type of machine allows you to grow from a basic to a complex machine.
And it’s definitely a good feature because as you grow, you also learn more perspectives surrounding the machine.
Now, these are the key benefits of having this machine.
And as you can see it, investing in the same makes a considerable sense.
It is a unit which if you utilize it well you’ll never regret having it.
In fact, you’ll always need to invest more as demands also grow.
Since you’ve now known that a filler machine is quintessential in various industrial production, let’s look at its multiple types available.
Well, when it comes to importing or purchasing this machine, you have to know the particular type suitable for your needs.
In other words, I’m trying to say that tube filling equipment come in various types.
And so depending on various factors, the choice may vary from one user to another.
Ideally, though, all the types of this machine available in the market are designed to attain a specific purpose.
But in general, you’ll realize that the efficiency and performance among the different types of this machine also contrast.
For that reason, let’s quickly have a look at the three common types of tube fillers you’ll mostly come across.
As the name indicates, this refers to a type of tube filler which is 100% automatic.
It means that almost all of its functionalities are programmed.
And in that case, human interaction with this kind of equipment is as minimal as possible.
The features of a fully automatic tube filler are exceptional, which makes it an ideal option especially for the large-scale production.
Fully automatic tube filling machine
For example, most of them have a dosing system which helps in easy suction.
Some models also feature a bottom-up filling which has a shut-off nozzle for enhancing accuracy and clean fill.
And since it is fully automatic, you’re guaranteed of tool-less adjustments.
In that case, all you need is to change settings via the touchscreen user interface.
It also comes with a product level sensor integrated lubrication system as well as a myriad of safety features.
These are just but a few specifications of a fully automated tube filling machine.
And the truth is that this is arguably the most suitable option that you need to go for.
It might be somewhat an expensive investment for the first time, but once you start using it, the operating costs become less.
What’s more is that fully automatic filler machines come in different shapes, designs, capacities, and sizes.
So the next time you think of buying this form of equipment, ensure you go for one that suits your specific requirements.
This is the other type of tube filler also common in many industries for filling various products including pastes, adhesives, lotions, and creams, etc.
It is one of the best especially when it comes to the comparatively small-scale production of something like 30-35 tubes per minute.
Semi-automatic tube filling machine
Other people may also refer to it as a semi-automatic tube filling sealer.
Most of these types of sealing machines tend to be comparatively small but are nevertheless easy to operate.
They also provide excellent filling and sealing performance hence allowing you to meet your needs effectively.
And also as the name suggests, this equipment is semi-auto.
However, it requires only one operator to start the process, and the machine automatically finishes the filling and sealing aspects.
Again, this tube filling equipment comes in different sizes, shapes, capacities as well as design.
This machine also features a digital temperature control which is also ideal in maintaining power supply.
Furthermore, it also comes with a sensor for measuring the level of liquid in the reservoir for subsequent automatic filling up.
It is easy to operate given that it doesn’t ideally require much of human interaction.
You only to set it accordingly and the machine will perform other processes automatically.
The price also varies depending on different manufacturers.
But the bottom line is that it is a necessary device to have if at all you need to increase your production capacity.
In some instances, you may choose to have it merely for the sake of supplementing the fully automatic tube filler.
Such that it serves as a backup option whenever there’s a breakdown, or there is a need for more production at the same time.
This is also a common type of tube filler that many people use in different industries including pharmaceutical.
An exciting element of this type of machine is that it comes both in fully and semi-automatic.
Such that it becomes easy for you to choose the particular one which you’re sure suits your needs accordingly.
A rotary tube filler has some of the exceptional features you can ever find in this kind of instrument.
For instance, they have a relatively heavy base as well as robust construction with an elegant finish.
This machine is also versatile in the sense that you can use it for filling products, sealing, crimping, batch coding and ejecting all in one cycle.
Now that’s an aspect of this machine which makes it popular in various industrial processes.
Significantly, you’ll find that it helps to enhance production process, cut cost and at the same time provide a suitable working environment.
Another great feature of this component is that it uses a patented hot air sealing system.
You need to know that that this sealing system is arguably the most reliable one, especially for plastics and laminate tube.
Most of the rotary tube fillers are easy to operate and provide accurate adjustments of fill desired amount.
This is of course with the assistance of change parts.
And in most cases, you’ll find it in different applications including pharmaceutical, food processing, cosmetic and nutraceutical.
Well, these are the major type of tube filling machines that you’ll ordinarily come across most of the time.
What happens nevertheless is that they come in different models depending on the manufacturer.
So when it gets to that point that you want to buy one, you’ll have to consider your needs first and import the appropriate one.
At least for now, you have the idea of the various types of this machine in the market.
Therefore, I also think it would be fundamental to even have an idea of some of the significant parts of the same.
And for that reason, let’s now shift focus and learn a few things regarding the key parts and components of tube filling equipment.
One important thing that you always need to have in mind is that this machine is made from assembling different parts and components.
And by the way, every part or component of this machine is deliberately designed and integrated to perform a specific role.
That is to mean that each component is essential for the functioning, performance, and efficiency of this machine.
Parts of tube filling machine – Photo courtesy: WIMCO ENGINEERING
In this section of the guide, we want to look at some of the main parts which you ideally need to know about.
However, it should be of ideal significance to acknowledge that we can’t discuss all the parts of this machine.
And that doesn’t necessarily imply that is not important.
The basis here is to inform you with the parts that you’ll often come across or handle most of the time.
Let’s, therefore, get straight away to the main point and discuss this major parts;
Frame primarily refers to the entire structural system which supports all the other parts and components of this machine.
It’s what houses the internal parts of the equipment and also holds the external parts of the same.
The frame of a tube filling machine is made of a robust material due to the fact that it has to support the other parts.
In most instances, the materials for manufacturing the frame have to be resistant to several elements.
Some of these elements may include corrosion, weather as well as resistance from physical destruction.
In other words, we can describe the frame as the backbone component of the tube filling machine.
Tanks, in this case, refer to the containers that the machine uses for holding the product that needs to be filled up.
The tanks in most of these machines are elevated to make it easy for the product to flow into the tubes during filling up.
The machine may contain a single or multiple tanks depending on the design and its capacity to fill up the product.
Also, you can get customized tanks that would meet your specifications and requirements.
The tanks obviously have to be resistant to corrosion and must be able to withstand different temperature variations.
In many cases, stainless still is the preferred material for manufacturing these tanks due to its high resistance properties.
This refers to the device for controlling the direction of the fluid flow the moment it exits the filler into the container or tube.
They are connected to the product supply in most cases using a tri-clover connection.
From a plain appearance, these devices may seem mundane or straightforward.
But the reality is that filling nozzles are essential elements in determining the performance of the machine.
And so you shouldn’t just look at the nozzle as a simple tool which only plays the role of directing the liquid to the desired container.
This device is available in numerous designs.
By the way, this vital since it allows you to choose a particular which suits your needs.
Some are suitable for normal liquids, whereas others are appropriate for low surface tension liquids.
In general, larger fill volumes will definitely require nozzles of larger sizes.
And also remember the fill speed is dependent on the size of the nozzle.
But then again, if the size is excessively big, then issues surrounding dripping will likely arise.
These refer to the devices which you use to easily and quickly set the machine to help in producing a quality finish.
In most of the modern tube filling machines, you’ll realize that the coding jaws are adjustable.
So this enables you to fill and seal a wide range of tubes regardless of its material, thickness or hardness.
These devices are also vital in ensuring that they keep all elements of this unit in good condition.
It refers to a relatively compact, positive displacement pump.
The design of this component is to pump an accurate flow rate of the substance into water, steam or gas flow.
This pump produces an exact flow rate of the product you’re filling up using various methods.
However, it primarily draws a measured quantity into a chamber then injecting it into the dosing tank.
It is often powered using an electric motor, and you can as well control it either by an external control system or internal pump controller.
All that matters is its ability to alter the flow rate.
It is unquestionably the most sensitive component of the tube filling machine.
The control unit is basically the component which contains all the elements for regulating the different parameters of this machine.
In modern models, the control unit features a touchscreen interface that allows you to determine the particular operation.
Normally, it is from the control unit that you’ll choose the speed, adjustments and many other aspects of the equipment’s parameters.
A comprehensive control unit lets you take charge of the machine in almost all the processes until in production of the final product.
In some machines, you’ll find that the control unit features quite a lot of buttons.
So it means that you also have to be knowledgeable enough to obtain high-quality product and efficiency in the production process.
This refers to the components which allow the substance from the tanks to get into the tubes or fill up containers for that matter.
This unit helps to determine the amount of substance that is ejected from the machine to fill up the tubes.
The discharge unit is equally impor
Female Pee Desperation 18
Sensual Cinema
Wife Husband Fuck Shemale