Курсовая работа: Расчет, выбор и обоснование посадок соединений
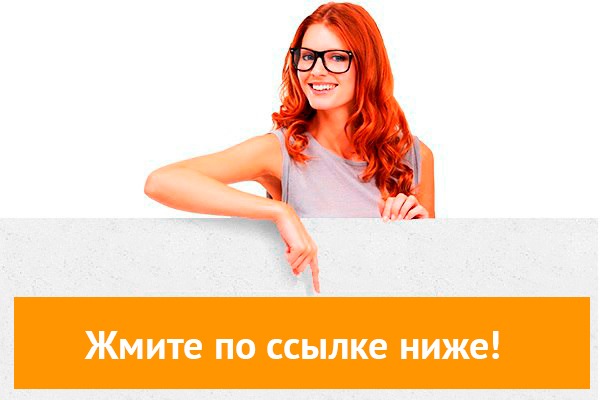
👉🏻👉🏻👉🏻 ВСЯ ИНФОРМАЦИЯ ДОСТУПНА ЗДЕСЬ ЖМИТЕ 👈🏻👈🏻👈🏻
“БЕЛОРУССКИЙ ГОСУДАРСТВЕННЫЙ АГРАРНЫЙ
Кафедра сопротивления материалов и деталей машин
По дисциплине: “Основы стандартизации и взаимозаменяемости ”
“Расчет, выбор и обоснование посадок соединений”
1.1Выбор посадок гладких цилиндрических соединений
1.2 Выбор посадок для шпоночного соединения
1.3 Выбор посадок для шлицевых соединений с прямым профилем зуба
2.1Расчёт и выбор посадок с натягом
3Расчёт и выбор посадок подшипников качения
4.1Расчёт размерной цепи методом полной взаимозаменяемости
4.2Расчёт размерной цепи вероятностным методом
Повышая качество машин, приборов и других изделий, их надежности, долговечности и эффективности возможно только путем тесной интеграции работ по стандартизации, взаимозаменяемости и метрологии, которые оказывают решающее влияние на повышение производительности, снижение себестоимости, формирование качества изделия на всех стадиях производства, начиная с проектирования, изготовления и заканчивая эксплуатацие, ремонтом и ханением изделия.
Приобретение технических знаний, навыков и опыта в области стандартизации и метрологии – обязательная составляющая часть профессиональной подготовки инженера-механика.
Важнейшее свойство совокупности изделий – взаимозаменяемость, в значительной мере определяет технико–экономический эффект, получаемый при эксплуатации современных технических устройств.
Такая роль взаимозаменяемости обусловлена тем, что она связывает в единое целое конструирование, технологию производства и контроль изделий в любой отрасли промышленности. В основе взаимозаменяемости лежит стандаотизация, объектом которой в машиностроении является точность, взаимозаменяемость и технические измерения. Поэтому в курсовой работе подрбно рассматриваются вопросы точности оброботки, основные виды погрешности и причины их возникновения. Взаимозаменяемость деталей, узлов и агрегатов невозможно обеспечить без развития и применения прогрессивных методов контроля. Не должно быть допусков, проверка которых не обеспечена техническими измерениями, поэтому состояние измерительной техники характеризует уровень и культуру призводства.
Основной задачей стандартизации является непрерывное повышение качества изделий, их способности удовлетворять возрастающие требования современного производства. Таким образом, стандартизация и унификация деталей и сборочных единиц способствует ускорению и удешивлению конструирования, изготовления, эксплуатации и ремонта маин.
Вот почему комплекс глубоких знаний и определенных навыков в области стандартизации норм точности является необходимо составной частью прфессиональной подготовки инженера-механика.
1.1 Выбор посадок для гладких цилиндрических соединений
1.1.1 Определение необходимых конструктивных,геометрических и силовых факторов:
Диаметр входного конца вала по пониженным допускаемым напряжениям кручения – согласно формуле 14.7 /1/ с. 294
где : [τ] = 20… 35 Мпа – допускаемые напряжения кручения
Принимаем значение диаметра из стандартного ряда предпочтительных чисел по таблице 1.3 /2/ ч.1, с. 34,с учетом ослабления поперечного сечения выходного конца шпоночнымпазом равным : d = 38 мм.
Определяем усилия, действующие в зацеплении
где d1 - делительный диаметр колеса быстроходной ступени ,
Консольное усилие от муфты предварительно рассчитываем согласно таблице 6.2 /3/ с.98:
Строим схему сил, действующих на вал:
Rby= Fr *b /( a+b)=2748.5*150/206=2001.3 H
Rbx= (Ft*b + Fm *c)/( a+b)=(7551.5*150+798*113)/206=5936H
Rax=(7551.5*56-798*(56+150+113))/(56+150)=817 H
Определяем тип подшипников установленных на валу.
Определяем отношение ∑Fa / Rmax; ΣFa =0H; Rmax=Rв=6264.1 H
Cогласно /4/ ч.2, с. 105-106, т.к. это отношение меньше 0.3, следовательно,
Принимаем шариковые радиальные подшипники средней серии 311.
1.1.2 Обоснование выбора посадок, системы, квалитетов
Каждый квалитет может быть достигнут различными способами обработки,
Но из них назначают обычно экономические технологические процессы, при которых себестоимость изготовления наименьшая. В машиностроении для окончательной обработки наиболее распространены квлитеты JT6 и JT7.
Назначаем и обосновываем посадки для соединений, расположенных на данном валу.
Выбираем приборы для измерения вала и отверстия,удовлетворяющие условию δ ≥ δин.
где: δ – допускаемая погрешность измерения, зависящая отдопуска из
меряемого изделия /6/ с.344, δин – предельная погрешность средств измерения.
Таблица 1.2-Объекты измерения и метрологические характеристики выбранных средств измерения
Нутромер индикаторный с ценой деления отсчетного устройства 0,001 мм
1.Используемое перемещение измеряемого
Скоба рычажная с ценой деления 0,002мм
1.2Выбор посадок для шпоночных соединения
Принимаем шпоночное призматическое соединение. Шпоночное соединение предназначено для передачи крутящего момента (T=30,21Hм) и не требует частых разборок, то применяем нормальное шпоночное соединение. Для соединения шестерни с валом в задании 1.1 приняты поля допусков : втулка – Æ60H7, вал Æ60k6.
Форма и размеры элементов шпоночного соединения, зависящие от условий его работы и диаметра вала, стандартизованы.
Определяем по ГОСТ 24071 – 80 /2/ 2ч., стр.239, таблица 4.67 номинальные размеры деталей шпоночного соединения: b = 20мм, h = 12мм, l =70 мм, tl = 7.5 мм,d - tl =66мм, t2 = 4.9мм, d +t2 =74.9мм.
Выбираем по /2/ ч.2, таблица 4.68.1, с.240 посадки для соединений: паз вала – шпонка-20 N9/h9; паз втулки– шпонка 20 Js9/h9.Определяем по ГОСТ 25346-89 предельные отклонения размеров шпоночного соединения и рассчи-
тываемпредельные размеры деталей шпоночного соединения,их допуски предельные зазоры и натяги.
Полученные результаты сводим в таблицы 1.3.1 и 1.3.2.
Таблица 1.3.1 - Размерные характеристики шпоночного соединения
Назначаем шероховатость сопрягаемых поверхностей шпонки, вала и втулкиRa = 3,2 мкм, а несопрягаемых поверхностей – Ra = 6,3мкм. Выбираем по /2/ ч.1, таблица 2.66, с. 517-522 экономические методы окончательной обработки деталей соединения :шпонка-шлифование плоское получистовое; паз вала – фрезерование чистовоефрезой; паз втулки – протягивание чистовое.
Эскизы нормального шпоночного соединения, его деталей, схема расположе-ния полей допусков на размер b приведены дальше.Для обеспечения взаимозаменяемости шпоночного соединения допуск на ширину паза следует рассматривать как комплексный, в пределах которого находятся как отклонения ширины паза,так и отклонения его расположения /2/ ч.1, таблица 2.66, с. 517-522.Ограничение всех этихотклонений в пределах допуска на ширину паза вала достигается контролем комплексными и элементными калибрами.
Таблица 1.3.2 – Характеристики посадок шпоночного соединения
На заводах автотракторного и сельскохозяйственного машиностроения контроль деталей шпоночных соединений производят с помощью предельныхкалибров. Ширину пазов вала и втулки проверяют пластинами, имеющими проходную и непроходную стороны. Размер от образующей цилиндрическойповерхности втулки до дна паза ( d + t2) контролируют пробкой со ступенчатым вы-
ступом.Глубину паза вала t1 проверяют кольцевыми калибрами –глубиномерами; симметричность расположения паза относительно освойплоскости проверяют у втулки пробкой со шпонкой, а у вала – накладной призмойс контрольным стержнем.
При ремонте машин можно использовать как универсальные средстваизмерния, так и калибры. Из большого числа размеров шпоночного соединения засчет пластических деформаций изменяется только ширина шпоночных пазов иширина самой шпонки. Поэтому при дефектации можноиспользовать унивесальные средства измерения, а при восстановлениижелательно применятьпредельные калибры.
1.3Выбор посадок для шлицевых соединений
1.3.1 Используем в соединении шлицевое соединение с прямобочным профилемзубъев
Так как заданное шлицевое соединение неподвижное, передача нереверсируемая, то такие условия не требуют точного центрирования втулки относительно вала. Перечисленные особенности заданного шлицевого соединения определяют способ его центрирования по наружному диаметру-D. По /2/ с.250 табл. 4.71определяем серию и раз мерb прямобочного шлицевого соединения.
Поля допусков и посадки для размеров b и D выбираем по /2/ с.253 табл.4.73. Поля допусков нецентрирующего диаметра - d выбираем по /2/ с.253 табл.4.75. Окончательный способ механической обработки и шероховатость поверхностей деталей назначаем по /2/ c.517 табл.2.66. Результаты выбора посадок, окончательного механического метода обработки и шероховатости поверхностей деталей сводим в табл. 1.4.
Условное обозначение выбранного прямобочного шлицевого соединения
Проводим проверку зубьев прямобочного шлицевого соединения на условие прочности из расчёта на смятие по формуле 4.2 /1/ с.51:
σсм = Tn/([SF] 1) £[σсм] /1/ стр.51
где: [SF] - суммарный статический момент площади рабочих поверхностей соединения относительно оси вала мм³/мм,
1 - длина шлицевого соединения, 1=45мм,
[σсм] - допускаемые напряжения смятия для материала вала (для стали
[SF] =(Т/[σсм]1) = 30,21*103/(40*45)=16,78 мм³/мм.
Применяем шлицевое прямобочное соединение лёгкой серии табл.4.71 стр.250/1/ (z*d*D =8*28*32) для которого [SF] =126 мм³/мм.
1.3.2 Схема расположения полей допусков, эскизы шлицевого соединения и его деталей приведены в приложении.
1.3.3 Шероховатости центрируемых и нецентрируемых поверхностей деталей
шлицевого соединения назначены в зависимости от вида обработки и эксплуатационного назначения соединения представлены в таблице 1.4.
Контроль шлицевых соединений осуществляется комплексными и поэлементными методами. Пробковыми и кольцевыми комплексными калибрами контролируется взаимное расположение поверхностей соединения, Поэлементный контроль охватывает диаметры валов, отверстий, толщину зубьев и ширину впадины отверстия.
Поля допусков, назначенные на элементы деталей шлицевого соединения и указанные в условном обозначении, контролируют в условном обозначении, контролируют независимо друг от друга специальными гладкими калибрамиустанавливаются в стандартах по ГОСТ 6033-80 на комплексные калибры.
Таблица 1.4 - Поля допусков и шероховатость деталей шлицевого соединения D-8x28х32H7/f7x7F8/f8
2.1 Расчет и выбор посадок с натягом
Передаваемый крутящий момент Т= 249.2 Hм , диаметр вала d= 60 мм.
2.1.1Расчет наибольшего функционального натяга
Определяем величину наибольшего допускаемого давления на сопряженных поверхностях деталей :
pдоп D ≤ 0,58 σTD [ 1 – ( d / D )² ] = 0,58 * 353 * [ 1- ( 60/ 102 )² ] = 133.9 МПа
pдоп d ≤ 0,58 σTd [ 1 – ( d 1/ D )² ] = 0,58 * 353 * [ 1 – ( 0/60)² ] = 204,7 МПа (d1 = 0 т.к. вал сплошной )
где : σT – предел текучести материала деталей при растяжении(σT=353МПа).
Согласно теории наибольших касательных напряжений , наиболее близко соответствующей экспериментальным данным , условие прочности деталей заключается в отсутствии пластической деформации на контактной поверхности втулки . Для снижения пластических деформаций берется наименьшее из двух значений pдоп = 133.9 МПа .
Наибольший расчетный натяг , при котором возникает наибольшее допускаемое давление pдоп , находят по формуле :
Nmax доп = pдоп d ( СD /ED + Сd / Ed) = 133.9 * 106 * 0,060*( 0,7 + 2,36) / 2 * 1011 = 126.9 мкм
Значение коэффициентов Ляме ( коэффициент жесткости деталей):
СD = [1+(d/D)²] / [ 1- (d/D)²] + µ = [1+(60/102)²] / [1-(60/102)²] +0,3 = 2,36
Cd= [1+(d1/d)²] / [ 1- (d1/d)²] - µ =[1+(0/60)²] / [1-(0/60)²] - 0,3 = 0,7
где: µ - коэффициент Пуассона, для стали µ = 0,3
E – модуль упругости для материалов деталей, входящих в соединение ( дляcтали Е = 2 * 10¹¹H/м² /2/ таблица 1.06, с.335 )
Определяем величину наибольшего функционального натяга с учетом смятия микронеровностей:
N max F = Nmax доп + u= 126.9 + 8,15 = 135.05 мкм
где u-поправка на смятие микронеровностей поверхностей,
u =5*(RaD+Rad)=5*(1,0+0,63)=8,15мкм
цилиндрический шлицевый посадка цепь
Расчет наименьшего функционального натяга
Определяем величину наименьшего допустимого давления на сопряженных поверхностях деталей
Pmin = 2T / ( π d² l f1 ) = 2 * 249.2/ ( 3,14 * 0,060² * 0,084*0,1 ) = 5.2МПа
Определяем величину наименьшего функционального натяга
Nmin расч = Pmind [(CD / ED) + (Cd / Ed)] =5.2*106*0,060* (0,7+2,36) / 2*1011 = 4.78 мкм
Определяем величину наименьшего функционального натяга с учётом смятия микронеровностей
Nmin F = Nmin расч + u = 4.78+ 8,15 = 12.93 мкм.
NmaxT < NmaxF на величину запаса прочности соединения при сборке
(технологический запас прочности), т.е.
NminT > NminF на величину запаса прочности соединения при эксплу атации, т.е.
По таблице 1.49 /1/ стр.153-257 определяем, что данным условиям удовлетворяет посадка Æ60 H7/u7. Для выбранной посадки определяем:
Nз.с = NmaxF-NmaxТ =135.05-117=18.07 мкм,
Nз.е= NminТ- NminF= 57-12.93=44.07 мкм,
Определим коэффициент запаса точности выбранной посадки
Kf= (NmaxТ- NminF)/ TN = (112-12.93)/60=1,65
Значение коэффициента запаса точности выбранной посанки Kf = 1…2.
3РАСЧЕТ И ВЫБОР ПОСАДОК ПОДШИПНИКОВ КАЧЕНИЯ
Расчет ведем по наиболее нагруженному подшипнику. Это подшипник B (правая опора). Rв =6264 H подшипник № 311 .
Учитывая, что редуктор нельзя отнести к разряду высокоскоростных, принимаем класс точности подшипников 0
По /2/ ч.2, таблица 4.88, с.284 и чертежу узла устанавливаем вид нагружения внутреннего и наружного кольца. Вал вращается, а корпус неподвижен, следовательно, внутреннее кольцо – циркуляционно нагруженное, а наружное – местно.
Выбор поля допуска цапфы вала, сопрягаемого с циркуляционно нагруженным внутренним кольцом подшипника, производим поинтенсивности радиальной нагрузки.
Интенсивность радиальной нагрузки определяется по формуле:
PR = R/ b * К1* К2 * К3 =6264/(29-2*3) *1* 1*1 = 272кH/м,
Где R – радиальная реакция опоры на подшипника, кН; b – рабочая ширина посадочного места, м (b = B – 2r, B – ширина подшипника; r – радиус закругления или ширина фаски кольца подшипника); kп – динамический коэффициент посадки, зависящий от характера нагрузки (при перегрузке до 150%, умеренных толчках и вибрации kп = 1; при перегрузке до 300%, сильных ударов и вибрации kп = 1,8); F – коэффициент, учитывающий степень ослабления посадочного натяга при полом вале или тонкостенном корпусе (при сплошном вале F = 1, табл 4.90); FA – коэффициент неравномерности распределения радиальной нагрузки R между рядами роликов в двухрядных конических роликоподшипников или между сдвоенными шарикоподшипниками при наличии осевой нагрузки А на опору. Значения FA, зависящие от (A/R)ctgβ, приведены втаблице 4.91(β – угол контакта тел качения с дорожкой качения наружного кольца зависят от конструкции подшипника). Для радиальных и радиально-упорных подшипников с одним наружным или внутренним кольцом FA = 1.
Допускаемые значения PR, подсчитанные по средним значениям посадочных натягов, приведены /2/ ч.2,таблица, с.287.Заданным условиям соответствует поле допуска цапфы Æ55js6.
Принимаем по /2/ ч.2,таблице 4.92, с. 287 поле допуска для внутреннего циркуляционно нагруженного кольца js6 с предельными отклонениями: es=+9,5 мкм; ei=-9,5 мкм.
где, L0 – поле допуска посадочного размера (диаметра) внутреннего кольца подшипника класса точности 0.
Поле допуска на диаметр отверстия в корпусе под местно нагруженное кольцо подшипника выбираем по таблицам 4.89, 4.93, 4,94 /2/, ч.2, с.285-289 Принимаем поле допуска Н7 с предельными отклонениями: ES=35мкм; EI=0
где l0-поле допуска посадочного размера (диаметра) наружного кольца подшипника класса точности 0.
Таблица 3.1 – Выбор посадки подшипника №304 для заданных условий работы
В соединении внутреннего кольца с валом имеем:
Nmax=es-EI=9,5-18=27.5 мкм, Nmin=ei-ES=0мкм
TN=TD+Td=37 мкм, Nm=( Nmax +Nmin)/2=13.75мкм
В соединении наружного кольца подшипника с корпусом имеем:
Smax=ES-ei=30-(-13)=43мкм, Smin=EI-es=0-0=0мкм
TS=TD+Td=43мкм, Sm=( Smax + Smin)/2=21,5мкм
Выполняем проверку наличия радиального зазора в подшипнике после посадки его на вал или в корпус с натягом.
По /1/ таблица 42, с. 247 определяем предельные значения зазоров в подшипнике:Gremin=10мкм; Gremax=30мкм; Grem=0,5*(10+30)=20мкм.
Вычисляем диаметральную деформацию дорожки качения внутреннего кольца. Для этого определяем приведённый наружный диаметр внутреннего кольца:
Действительный натяг: Ne»0,85NmaxNe =0,85×27,5=23.37мкм
Определяем диаметральную деформацию дорожки качения внутреннего кольца:
Посадочный зазор определяем по формуле:
Шероховатость поверхностей вала и отверстия в корпусе выбираем по/2/ ч.2,таблица 4.95, с.296: Rad = 0,8 мкм, RaD =1,25 мкм, торцов заплечиков вала иотверстия Ra = 2,5 мкм.
Определяем допуски соосности посадочных поверхностей вала и корпуса
В приложении 7 ГОСТ 3325-85 приведены числовые значения допусков соосности посадочных поверхностей вала и корпуса при длине посадочного места B1=30мм. При другой длине посадочного места В2 для получения этих допусков следует табличные значения умножить на В2/10. Тогда допуск соосности поверхностейваласоставит:
Т©=(4*В2)/10=(4*29)/10=11.6 мкм (принимаем равным 12),
Т©=(8*В2)/10=(8*29)/10=23.2 мкм (принимаем равным 24).
Допуски цилиндричности посадочных поверхностей подшипников качения 0 и 6 класса точности не должны превышать четверть допуска на размер /2/ ч.2,с.288:
Решить линейную размерную цепь (А∆ = 5 ± 0,8). Выполнить размерный анализи построить схему размерной цепи. Рассчитать размерную цепь методом полной взаимозаменяемости и вероятностным методом. Сделать вывод оприменении выше названных методов.
Составляем размерную цепь и выявляем составляющие (увеличивающие и уменьшающие) звенья по заданному чертеже.
Размерные связи деталей через сборочные базы:
А1 =62 мм (увеличивающее звено); i = 1,86 (ось)
А2 = 10 мм (уменьшающее звено); (подшипник)
А3 = 10 мм (уменьшающее звено); (подшипник)
А4 =20 мм (уменьшающее звено); i = 1,31 (втулка)
А5 = 2 мм (уменьшающее звено); i = 0,55 (шайба)
А6 =15 мм (уменьшающее звено); i = 1,08 (гайка)
Проверяем правильность составления размерной цепи :
4.2 Расчет размерной цепи методом полной взаимозаменяемости
По заданным отклонениям замыкающего звена находим его допуск :
TАΔ = ESАΔ – EIАΔ =0,8-( -0,8) = 1,6мм
Предполагаем, что все размеры выполнены по одному классу точности (квалитету).Определяем среднее число едениц допуска( коэффициент точности)размерной цепи с учетом известных допусков (стандартных деталей) и по нему определяем квалитет :
ас=(TАΔ - ΣTАi изв) /ΣiАi опр=(1600-240)/(1,86+1,31+0,55+1,08)=283
где: ΣTАi изв – cумма известных допусков составляющих звеньев(стандарт-ных деталей ), мкм;
ΣiАiопр – сумма единиц допусков определяемых составляющих звеньев,мкм
По /2/ ч 2,таблица 48, с.45 находим, что полученный коэффициент точностиcоответствует 13-ому квалітету. По выбранному квалитету назначаем допуски и отклонения на звенья исходя из общего правила: для охватывающих размеров, какна основные отверстия (H13),а для охватываемых – как на основные валы (h13).
В тех случаях, когда это трудно установить, на звено назначают симметричные отклонения ± IT13/2.
Допуски составляющих звеньев определяем:
Так как коэффициент точности ас не полностью соответствует расчетному, тоодно из звеньев выбираем в качестве корректирующего. При выборе корректирующего звена руководствуются следующими соображениями.
Если выбранный коэффициент точности а меньше вычисленного ас, то естьа < ас, то в качестве корректирующего звена выбирается технологически более сложное звено. Если же а > ас, то в качестве корретирующего звена выбирается технологически более простое звено.
Принимаем в качестве корректирующего звена увеличивающее звено А5.
Отклонения корректирующего звена находим по формулам:
EsА5=Es(А∆)+∑EiА(ум)-∑EsА(i-1)(ув)=0,8-0,12-0,12-0,33-0,27=-0,04мм
EiА4=Ei(А∆)+∑EsА(j)(ум)-∑EiА(i-1)(ув)=-0,8+0,46=-0,34мм
Предельные отклонения корректирующего звена:
ТА4= ESА4кор – EIА4кор = -40 + 340 = 300 мкм
Проверяем правильность назначения допусков и предельных отклонений составляющих звеньев:
TАΔ = ΣTАi = 460+120+120+300+140+270=1600 мкм
Результаты расчётов сводим в таблицу 4.1
Таблица 4.1-Результаты расчета размерной цепи методом полной взаимозаменяемости
Заключение. Назначенные допуски и отклонения составляющих звеньевобеспечивают заданную точность замыкающего звена.
4.3 Расчет размерной цепи вероятностным методом
Допуски замыкающего звена определено в пункте 4.1.
Принимаем, что рассеяние действительных размеров звеньев близко к нормальному закону распределения и допуск размера Т равен полю рассеянияразмеров ω для каждого из звеньев цепи, т.е. Тai = ωi и TАΔ = ωΔ,oтсюда коэффициент относительного рассеяния λi = λ Δ= 1/3 , а коэффициент относительной асимметрии αi = αΔ = 0 /2/ ч.2, с.37.
По /2/ ч.2, таблица 3.8 находим значение коэффициента риска t, зависящего от процента риска Р. Принимаем ti = tΔ, H = 0,27%, в этом случае ti = tΔ = 3.
4.2.2 Находим среднее число единиц допуска:
По /2/ ч.2, таблица 1.8, с.45 определяем, что ас приблизительно соответствует 15 квалитету.
4.2.3По /2/ ч.2, таблица 1.8, с.45находим допуски на составляющие звенья:
Так как ас ≠ а, то А7 принимаем за корректирующее звено, для которого допуск определим по формуле:
4.2.4Определяем координаты середины поля допуска звеньев цепи:
4.2.5Определяем середину поля допуска корректирующего звена:
EcА1= ΣEcАi ув + EcАΔ- Σ EcАi ум = 0-60-60-420-200-350=-1090 мкм
4.2.6Определяем предельные отклонения корректирующего звена:
EsА1= EcА1+ TА1/ 2 =-1090+1084/2 = -548 мкм
EiА1 = EcА1 – TА1/ 2 =-1090-1084/2 = -1632мкм
4.2.7Проверяем правильность назначения предельных отклонений состаляющих звеньев:
Проверка показывает соответствие назначенных предельных отклоненийсоставляющих звеньев заданным предельным отклонениям замыкающего звена.
Результаты расчета сводим в таблице 4.2
Таблица 4.2 – Результаты расчета размерной цепи вероятностным методом
Сравнивая допуски звеньев, рассчитанных разными способами можно убедитьсяв том, что расчет размерных цепей вероятностным методом позволяет назначитьболее широкие допуски на обработку деталей, при том же допуске замыкающегозвена.
1 Кузьмин, А.В.Расчеты деталей машин[Текст]: справочное пособие/ А.В.
Кузьмин,И.М. Чернин, Б.С. Козинцов.- Минск: Вышэйшая школа, 1986.- 400с.: ил.
2 Мягков, В.Д. Допуски и посадки [Текст]: справочник в 2-х ч./ Мягков В.Д. [и др.]. – изд. 6-е, перераб. и доп. – Ленинград: Машиностроение, 1982. – 2ч.
3 Шейнблит, А.Е. Курсовое проектирование деталей машин [Текст]: учебное пособие/ А.Е. Шейнблит. – Москва: Высшая школа, 1991. – 432 с.: ил.
4.Палей, М.А. Допуски и посадки [Текст]: справочник в 2-х ч./ М.А.Палей, А.Б. Романов, В.А. Брагинский. – изд. 8-е, перераб. и доп.. – Санкт-Петербург: Политехника, 2001.-2ч.
5 Козловский, Н.С. Сборник примеров и задач по курсу «Основы стандартизации, допуски, посадки и технические измерения»: учеб. пособие/ Н.С. Козловский, В.М. Ключников. – Москва: Машиностроение, 1983. – 304 с.: ил.
6 Серый И.С. Взаимозаменяемость, стандартизация и технические измерения. : учебное пособие/ И.С. Серый. – Москва: Агропромиздат, 1987. – 367 с.: ил.
Название: Расчет, выбор и обоснование посадок соединений
Раздел: Промышленность, производство
Тип: курсовая работа
Добавлен 03:38:34 04 апреля 2011 Похожие работы
Просмотров: 634
Комментариев: 14
Оценило: 2 человек
Средний балл: 5
Оценка: неизвестно Скачать
Привет студентам) если возникают трудности с любой работой (от реферата и контрольных до диплома), можете обратиться на FAST-REFERAT.RU , я там обычно заказываю, все качественно и в срок) в любом случае попробуйте, за спрос денег не берут)
Да, но только в случае крайней необходимости.
Курсовая работа: Расчет, выбор и обоснование посадок соединений
Эссе По Английскому Экологические Проблемы
Курсовая работа по теме Историческая наука России на современном этапе
Дипломная Работа На Тему Управление Развитием Сетевой Торговли На Примере Мебельных Салонов Ооо "Дубль-Дон"
Сочинение по теме Тредиаковский В.К.
Реферат На Тему Классификация Костей
Лабораторная Работа 6 Изучение Треков
Курсовые работы: Экономико-математическое моделирование, эконометрика
Сочинение Про Маму Смешное Папа Плакал
Дипломная работа: Возникновение Османской империи
Реферат по теме Физическое совершенствование ребенка до 3 лет
Курсовая работа по теме Расчет привода главного движения радиально-сверлильного станка
Проведение Лабораторной Работы По Химии
Реферат На Тему Эволюция Звезд
Реферат по теме Крымский экономический район (Судак, Феодосия)
Дипломная работа: Бухгалтерский и налоговый учет на предприятиях малого бизнеса
Реферат: Виховання бережливого ставлення до природи
Сочинение по теме Падпольны і партызанскі рух на тэрыторыі Карэліцкага раёна ў гады Вялікай Айчыннай вайны
Курсовая Работа Введение Щитовых Денег Объединяет
Понятие и состав финансовой системы РФ
Курсовая работа по теме Анализ Финляндии
Реферат: Визначення термостійкості пластичних мас
Реферат: Личность и психика
Реферат: Кожа