Курсовая работа: Расчет и проектирование привода для пластинчатого конвейера
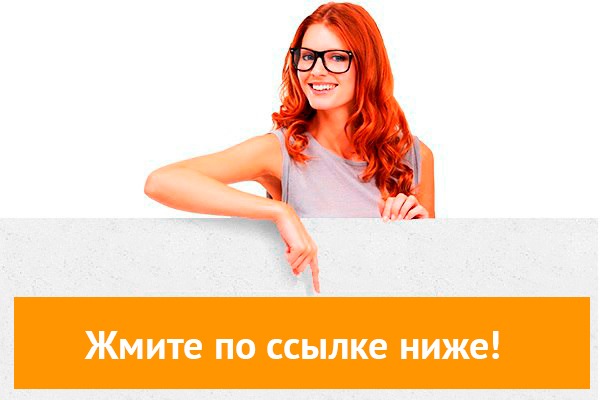
⚡ 👉🏻👉🏻👉🏻 ИНФОРМАЦИЯ ДОСТУПНА ЗДЕСЬ ЖМИТЕ 👈🏻👈🏻👈🏻
Редуктором называют механизм, состоящий из зубчатых или червячных передач, выполненный в виде отдельного агрегата и служащий для передачи мощности от двигателя к рабочей машине. Кинематическая схема привода может включать, помимо редуктора, открытые зубчатые передачи, цепную или ременную передачу.
Назначение редуктора — понижение угловой скорости и повышение вращающего момента ведомого вала по сравнению с валом ведущим, понижение числа оборотов. Механизмы для повышения угловой скорости, выполненные в виде отдельных агрегатов, называют ускорителями или мультипликаторами.
Редуктор состоит из корпуса (литого чугунного или сварного стального), в котором помещают элементы передачи - зубчатые колеса, валы, подшипники и т. д. В отдельных случаях в корпусе редуктора размещают также устройства для смазки зацеплений и подшипников (например, внутри корпуса редуктора может быть помещен шестеренчатый масляный насос) или устройства для охлаждения (например, змеевик с охлаждающей водой в корпусе червячного редуктора).
Редуктор проектируют либо для привода по заданной нагрузке (моменту на выходном валу) и определенной машины, либо передаточному числу без указания конкретного назначения. Второй случай характерен для специализированных заводов, на которых организовано серийное производство редукторов.
В данной курсовой работе необходимо спроектировать привод для пластинчатого конвейера. Данный привод состоит из электродвигателя, муфты и трехступенчатого коническо-целендрического редуктора.
Тип - коническо-цилиндрический трехступенчатый
Обороты быстроходного вала – 2900 об/мин.
Обороты тихоходного вала - 83 об/мин.
Крутящий момент на выходном валу – 697,4 Н·м
Конические зубчатыеколеса применяют в передачах, у которых оси валов пересекаются под некоторым углом. Наиболее распространены передачи с углом =90°.
Конические передачи сложнее цилиндрических в изготовлении и монтаже. Для нарезания конических колес требуются специальные станки и специальный инструмент. Кроме допусков на размеры зубьев здесь необходимо выдерживать допуски на углы, а при монтаже обеспечивать совпадение вершин конусов. Выполнить коническое зацепление с той же степенью точности, что и цилиндрическое, значительно труднее. Пересечение осей валов затрудняет размещение опор. Одно из конических колес, как правило, располагают консольно. При этом увеличивается неравномерность распределения нагрузки по длине зуба. В коническом зацеплении действуют осевые силы, наличие которых усложняет конструкцию опор. Все это приводит к тому, что, по опытным данным, нагрузочная способность конической прямозубой передачи составляет лишь около 0,85 цилиндрической .
Несмотря на отмеченные недостатки, конические передачи имеют широкое применение, поскольку по условиям компоновки механизмов иногда необходимо располагать валы под углом.
В трехступенчатых коническо-цилиндрических редукторах коническая пара может иметь прямые, косые или криволинейные зубья. Цилиндрическая пара также может быть либо прямозубой, либо косозубой.
Наиболее употребительным диапазоном передаточных чисел для коническо-цилиндрических трехступенчатых редукторов можно считать и
== 8÷15. В качестве максимальных передаточных чисел можно принимать: при прямозубых конических колесах U max
== 22; при конических колесах с круговыми зубьями U max
= 34 (в отдельных случаях U max
= 40).
Асинхронные машины —
это машины переменного тока. Слово «асинхронный» означает не синхронный или не одновременный. При этом имеется в виду, что у асинхронных машин частота вращения магнитного поля отличается от частоты вращения ротора. Асинхронные машины, как и все электрические машины, обладают свойством обратимости, т. е. могут работать как в режиме двигателя, так и в режиме генератора. Асинхронные двигатели имеют значительные преимущества по своим свойствам, характеристикам и эксплуатационным данным перед двигателями других типов. Такие двигатели могут быть однофазными, двухфазными и трехфазными; наибольшее распространение имеют трехфазные двигатели.
Трехфазные двигатели изобретены выдающимся русским электротехником М. О.. Доливо-Добровольским в 1889г. Конструкция двигателя, предложенная М. О. Доливо-Добровольским, была настолько проста, надежна и экономична, что в основных чертах сохранилась до настоящего времени. Подавляющее число электрических двигателей, используемых в промышленности, энергетике и других областях, являются асинхронными. Они широко применяются в станках, вентиляторах, насосах, автоматических системах и т. п. Диапазон мощностей асинхронных двигателей, выпускаемых промышленностью, составляет от долей ватта до тысяч киловатт.
Технические характеристики асинхронного двигателя. Число оборотов двигателя стандартизовано и равно 3000, 1500, 1000, 750 об/мин. Мощность двигателя различна и принимает значения в соответствии с его назначением и зависит от числа оборотов.
Муфты упругие втулочные обладают высокой амортизирующей способностью, допускают кратковременные пиковые нагрузки, в 2,5—3 раза превышающие номинальнные. По ГОСТ 20884—75 они предназначены для соединения валов при величине передаваемого вращающего момента от 20 до 40-10 3
Н-м. Предусматривается изготовление муфт двух типов — с цилиндрическим и с коническим отверстием, и двух исполнений — на длинные и на короткие концы валов с диаметром от 14 до 240 мм.
Подобрать электродвигатель, разбить передаточные отношения по ступеням и определить силовые и скоростные параметры на валах привода
Рисунок 1.1 - Схема для расчета привода пластинчатого конвейера
Таблица 1.1 – Данные для расчета привода пластинчатого конвейера
Двигатель подбираем по требуемой мощности и рекомендуемым оборотам. Передаточное отношение разбиваем согласно рекомендуемых диапазонов.
Требуемую мощность электродвигателя определяют на основании исходных данных. Если указана мощность Р вых..
кВт, отнесенная к ведомому валу, то необходимая мощность электродвигателя
где —
коэффициент полезного действия (КПД) привода, равный произведению частных КПД;
-мощность на выходе (из задания), кВт .
- коэффициент полезного действия (КПД), пары подшипников
-коэффициент полезного действия (КПД), конической зубчатой передачи =0,96 (таблица 1.1 [1]);
-коэффициент полезного действия (КПД), цилиндрической зубчатой передачи =0,97 (таблица 1.1 [1]) .
По найденному значению мощности Р тр.,
кВт выбирают, как правило, асинхронный электродвигатель трехфазного тока. Выбираем электродвигатель (приложение П3 с.328 [1]). Электродвигатель серии 4А. Исполнение закрытое обдуваемое. Электродвигатель типоразмера 90L2. Номинальная мощность 7.5 кВт и число оборотов 2900об/мин.
Передаточные отношения каждой передачи определяются из диапазонов установленных для каждого вида передач.
Для конической передачи i принимаем из диапазона i =2÷4, в данной курсовой работе i кон.з.п.
=2.5.
Для цилиндрических передач i принимаем из диапазона i =2÷6, в данной курсовой работе i пром.з.п.
=4.24; i тих.з.п.
=3.3.
Для того что бы проверить правильность выбора передаточных отношений необходимо их перемножить и сравнить с общим передаточным отношением.
i общ.
= i кон.з.п.·
i пром.з.п ·
i тих.з.п
35=35, значит передаточные отношения каждой передачи подобраны верно.
1.7 Силовые, скоростные параметры на валах
По выходной мощности Р вых.
кВт ,
определяем мощность на каждом валу.
где Р IV
– мощность на 4 валу, кВт;
Р вых.
– выходная мощность редуктора, кВт;
где Р III
– мощность на 3 валу, кВт ;
где Р II
– мощность на 2 валу, кВт ;
Мощность на I валу соответствует требуемой мощности.
2.Число оборотов каждого вала определяется по формуле (с.8 [2]).
где n I
– число оборотов на I валу, об/мин ,
i – передаточное число быстроходной передачи;
где n II
– число оборотов на II валу, об/мин ,
i – передаточное число промежуточной передачи;
где n I
– число оборотов на III валу, об/мин ,
i – передаточное число тихоходной передачи;
2. Угловую скорость каждого вала определяем по формуле
где n –число оборотов на соответственном валу, об/мин.
3. Крутящий момент на валах определяем по формуле
где Р – мощность соответствующего вала, кВт
ω- угловая скорость соответствующего вала, с -1
.
Все расчеты для удобства записываем в сводную таблицу
Таблица 1.1. – силовые и скоростные параметры привода
Р в приводе уменьшилось не значительно из-за потерь в подшипниках. Число оборотов и угловая скорость в приводе сильно уменьшились из-за больших передаточных отношений.
Провести проектный расчет, подобрать материал, определить основные геометрические параметры и проверить на контакт.
Рисунок 2.1 – Расчетная схема зацепления колес конической передачи
Данные для расчета передачи берем из кинематического расчета.
Таблица 2.1 - силовые и скоростные параметры для расчета промежуточной передачи
Проектный расчет ведем на контакт, так как основной вид разрушения закрытых зубчатых передач - поверхностное выкрашивание зубьев в зоне контакта. Проверяем на контакт и изгиб.
Материалы для изготовления конических зубчатых колес подбирают по таблице 3.3 [1]).Для повышения механических характеристик материалы колес подвергают термической обработке. В зависимости от условий эксплуатации и требований к габаритным размерам передачи принимаем следующие материалы и варианты термической обработки (Т.О.).
Примем для колеса и шестерни сталь 40ХН и вариант термообработки ( таблица 3.3 [1]);
колесо—улучшение и закалка ТВЧ по контуру, НRC 48…53;
шестерня—улучшение и закалка ТВЧ по контуру, НRC 48…53.
Определяем допускаемые контактные напряжения и напряжения изгиба отдельно для колеса [σ] н2
и [σ] F
2
и шестерни [σ] н1
и [σ] F
1
по формулам (с.10 [2])
где - коэффициент долговечности при расчете по контактным напряжениям, так как редуктор рассчитан на долгий срок службы, то =1 (с.11 [2])
- коэффициент долговечности при расчете по изгибу , так как редуктор рассчитан на долгий срок службы, то =1 (с.11 [2]).
Определяем среднюю твердость зубьев колес НRC ср
=0,5(48+53)=50,5 Мпа
По таблице 2.2 [2] находим формулу для определения допускаемого контактного напряжения
[σ] н1
=[σ] н2
=14· HRC ср
+170 (2.1)
[σ] н1
=[σ] н2
=14· 50,5+170=880 МПа
Допускаемое напряжение на изгиб [σ] F
1
=[σ] F
2
=370 МПа (с.24 [2]).
где - коэффициент вида конических колес, (с. 20 [2]) ;
- передаточное число быстроходной передачи;
Т 2
- вращающий момент на 1 промежуточном валу, Н·м;
- коэффициент неравномерности нагрузки по длине зуба. Для прирабатывающихся зубьев = 1,45 (таблица 2.3 [2]);
- допускаемое контактное напряжение колеса с менее прочным зубом или среднее допускаемое контактное напряжение, н/мм 2
.
Полученное значение внешнего делительного диаметра колеса округляем до ближайшего стандартного значения .
2. Определяем углы делительных конусов, конусное расстояние и ширина колес.
Угол делительных конусов колеса и шестерни определим по следующим формулам (с. 20[2]):
Конусное расстояние найдем по формуле (с. 20[2]):
где - делительный диаметр окружности колеса, мм;
Для конических колес с круговым зубом находим внешний торцовый модуль передачи (с. 20[2]):
где - коэффициент вида конических колес, =1(с. 20[2]);
- коэффициент, учитывающий распределение нагрузки по ширине венца, =1,71(таблица 2.5[2]);
[σ] F
– допускаемое напряжение на изгиб, МПа.
Число зубьев колеса находим по формуле (с. 20 [2]):
Отклонение от заданного передаточного числа не должно быть более 4%, то есть
Отклонение составляет 1,2, что не превышает допускаемого значения - следовательно передаточное число конической передачи определено точно.
7. Окончательные размеры колеса и шестерни.
Угол делительных конусов колеса и шестерни (с. 21[2]):
где , - коэффициенты смещения, =0,26; =-0,26(таблица 2.7 и 2.8 [2]).
Окружная сила на среднем диаметреколеса (с. 23 [2]):
Находим осевую силу на шестерне по формуле (с. 23 [2]):
где
- коэффициент учитывающий направление вращения шестерни и направление наклона зубьев, определяем по формуле (с. 23 [2]):
Находим осевую силу на шестерне по формуле (с. 23 [2]):
где
- коэффициент учитывающий направление вращения шестерни и направление наклона зубьев, определяем по формуле (с. 23 [2]):
Напряжение изгиба в зубьях колеса определим по формуле (с. 23 [2]):
где - коэффициент динамической нагрузки, зависящий от окружной скорости колес и степени точности передачи (с.16 [2]), =1,1;
- коэффициент неравномерности нагрузки по длине зуба (с.16 [2]),
- коэффициенты формы зуба шестерни и колеса (с.16 [2]), =3,92;
- коэффициент вида конических колес, =1(с. 20[2]).
Напряжение изгиба в зубьях шестерни определим по формуле (с. 23 [2]):
где - коэффициенты формы зуба шестерни и колеса (с.16 [2]), =3,92;
- коэффициенты формы зуба шестерни и колеса (с.16 [2]), =3,65;
- напряжение изгиба на колесе, МПа.
Так как [σ] F
1
=370 МПа, [σ] F
2
=370 МПа и σ F
1
=277,688 МПа, σ F
2
=298,23 МПа, что удовлетворяет условию [σ] F
1
σ F
1
, [σ] F
2
σ F
2
, то колеса прошли проверку по напряжениям на изгиб.
где -коэффициенты учитывающие распределение нагрузки между зубьями, неравномерность распределения нагрузки по длине контактной линии, дополнительные динамические нагрузки, =1,45(с.26 [2]);
- коэффициент вида конических колес, =1,3 (с. 26[2]).
При определении погрешности передаточного числа, получили Δi= 1,2% , что позволяет сделать вывод- передаточное число выбрано, верно.
Так как [σ] F
1
=370 МПа, [σ] F
2
=370 МПа и σ F
1
=277,688 МПа, σ F
2
=298,23 МПа, что удовлетворяет условию [σ] F
1
σ F
1
, [σ] F
2
σ F
2
, то колеса прошли проверку по напряжениям на изгиб.
В результате расчетов определили, что 1,8% перегрузки. Это величина не превышает допустимого значения (5 % перегрузки и 10 % недогрузки), следовательно, колеса прошли проверку по контактным напряжениям.
Провести проектный расчет, подобрать материал, определить основные геометрические параметры и проверить на контакт.
Данные для расчета передачи берем из кинематического расчета.
Таблица 3.1 - силовые и скоростные параметры для расчета промежуточной передачи
Проектный расчет ведем на контакт, так как основной вид разрушения закрытых зубчатых передач - поверхностное выкрашивание зубьев в зоне контакта. Проверяем на контакт и изгиб.
Материалы для изготовления зубчатых колес подбирают по таблице 3.3 [1].Для повышения механических характеристик материалы колес подвергают термической обработке. В зависимости от условий эксплуатации и требований к габаритным размерам передачи принимаем следующие материалы и варианты термической обработки (Т.О.).
Рекомендуется назначать для шестерни и колеса сталь одной и той же марки, но обеспечивать соответствующей термообработкой твердость поверхности зубьев шестерни на 20—30 единиц Бринеля выше, чем колеса.
Примем для колеса и шестерни сталь 40ХН и вариант термообработки ( таблица 3.3 [1]);
Для непрямозубых колес расчетное допускаемое контактное напряжение определяют по формуле (3.9 [1])
где σ н
lim
b
– предел контактной выносливости при базовом числе циклов (таблица 3.2 [1])
для колеса σ н1
lim
b
=
2·280+70=630н/мм 2
;
для шестерни _
σ н2
lim
b
=
2·250+70=570 н/мм 2
.
- коэффициент долговечности; если число циклов нагружения каждого зуба колеса больше базового, то принимают = 1
[п] Н
—
коэффициент безопасности; для колес из нормализованной и улучшенной стали, а также при объемной закалке принимают [п] Н
= 1,1—1,2, принимаем [п] Н
= 1,15
Принимаем наименьшее значение [σ] н
=495,65 Мпа
Допускаемые напряжения на изгиб определяем по формуле
Важнейшим геометрическим параметром редуктора является межосевое расстояние, которое необходимо для определения геометрических параметров колес.
1. Определяем межосевое расстояние по формуле (с.11 [2]) :
- вспомогательный коэффициент. Для косозубых передач =43, для прямозубых — =49,5;
- передаточное число промежуточной передачи;
Т 2
- вращающий момент на 2 промежуточном валу, Н·м;
- коэффициент неравномерности нагрузки по длине зуба. Для прирабатывающихся зубьев = 1(см. 3.1, п. 1 [1]);
-коэффициент ширины венца колеса, равный 0,28...0,36 — для шестерни, расположенной симметрично относительно опор (с. 13 [2]).
-
допускаемое контактное напряжение колеса с менее прочным зубом или среднее допускаемое контактное напряжение, Н/мм2.
Полученное значение межосевого расстояния округляют в большую сторону до стандартного по СТ СЭВ 310-76 : 40, 50, 63, 71, 80, 90, 100, 112, 125, 140, 160, 180, 200, 220, 250, 280, 315 мм. Принимаем =140 мм.
2. Выбирают модуль в интервале m=(0,01÷0,02) , по СТ СЭВ 310—76 (в мм)
3. Определяем суммарное число зубьев данной передачи по формуле (с.13 [2]) :
Находим число зубьев на шестерни по формуле (с.14 [2]) :
где - передаточное число промежуточной передачи.
4. определяем фактическое передаточное число по формуле (с.18 [2]) :
Погрешность при выборе передаточного числа определяем по формуле (с.18 [2]) :
Погрешность составляет всего 1,4% , что позволяет сделать вывод, что передаточное число выбрано верно.
5. Определяем диаметры колес (с.41 [1]) .
Диаметры окружностей вершин и впадин шестерни
d f
2
=d 2
-2,5m = 226-2,5·2=221 мм
6. Определяем ширину шестерни и колеса.
Ширину колеса находим по формуле (с.41 [1]) :
где - коэффициент ширины венца колеса, равный 0,28...0,36 — для шестерни, расположенной симметрично относительно опор, принимаем =0,3 (с. 13 [2]).
Ширина шестерни больше на (3÷8) мм чем у колеса
Таким образом, найденные диаметры определены, верно.
Окружная сила направлена по касательной в точки касания колеса и шестерни.
где Т 2
- вращающий момент на 2 промежуточном валу, Н·м;
d 2
– делительный диаметр шестерни, мм.
Радиальная сила направлена к центру окружности и определяется по формуле (с.19 [2]) :
α – между геометрической суммой радиальной и осевой силами,
β- угол наклона зубьев, tg β=0,364.
Проверяем зубья колес по напряжениям изгиба. Должно выполняться неравенство
где - коэффициент, учитывающий распределение нагрузки между зубьями. (с.15 [2]), =0,91;
- коэффициент динамической нагрузки, зависящий от окружной скорости колес и степени точности передачи (с.16 [2]), =1,4;
- коэффициент неравномерности нагрузки по длине зуба (с.16 [2]),
- коэффициент, учитывающий наклон зуба,
- коэффициенты формы зуба шестерни и колеса (с.16 [2]), =3,61;
где - коэффициенты формы зуба шестерни и колеса (с.16 [2]), =3,61;
- коэффициенты формы зуба шестерни и колеса (с.16 [2]), =3,92;
- напряжение изгиба на колесе, Мпа.
Так как [σ] F
1
=547,83 МПа, [σ] F
2
=495,65 МПа и σ F
1
=390,5 МПа, σ F
2
=359,91 МПа, что удовлетворяет условию [σ] F
1
σ F
1
, [σ] F
2
σ F
2
то колеса прошли проверку по напряжениям на изгиб.
Проверяем зубья колес по контактным напряжениям .
где , , -коэффициенты учитывающие распределение нагрузки между зубьями, неравномерность распределения нагрузки по длине контактной линии, дополнительные динамические нагрузки, так как редуктор рассчитан на долгий срок службы то =1, =1, =1.
При определении погрешности передаточного числа, получили Δi= 1,4% , что позволяет сделать вывод- передаточное число выбрано, верно.
Так как [σ] F
1
=547,83 МПа, [σ] F
2
=495,65 МПа и σ F
1
=390,5 МПа, σ F
2
=359,91 МПа то колеса прошли проверку по напряжениям на изгиб.
В результате расчетов определили, что 0,5% перегрузки. Это величина не превышает допустимого значения (5 % перегрузки и 10 % недогрузки), следовательно, колеса прошли проверку по контактным напряжениям.
В результате проверочного расчета убедились, что полусумма делительных диаметров равна межосевому расстоянию.
Провести проектный расчет, подобрать материал, определить основные геометрические параметры и проверить на контакт.
Данные для расчета передачи берем из кинематического расчета.
Таблица 3.1 - силовые и скоростные параметры для расчета промежуточной передачи
Проектный расчет ведем на контакт, так как основной вид разрушения закрытых зубчатых передач - поверхностное выкрашивание зубьев в зоне контакта. Проверяем на контакт и изгиб.
Материалы для изготовления зубчатых колес подбирают по таблице 3.3 [1]).Для повышения механических характеристик материалы колес подвергают термической обработке. В зависимости от условий эксплуатации и требований к габаритным размерам передачи принимаем следующие материалы и варианты термической обработки (Т.О.).
Рекомендуется назначать для шестерни и колеса сталь одной и той же марки, но обеспечивать соответствующей термообработкой твердость поверхности зубьев шестерни на 20—30 единиц Бринеля выше, чем колеса.
Примем для колеса и шестерни сталь 40ХН и вариант термообработки ( таблица 3.3 [1]);
Для непрямозубых колес расчетное допускаемое контактное напряжение определяют по формуле (3.9 [1])
где σ н
lim
b
– предел контактной выносливости при базовом числе циклов (таблица 3.2 [1])
для колеса σ н1
lim
b
=
2·280+70=630н/мм 2
;
для шестерни _
σ н2
lim
b
=
2·250+70=570 н/мм 2
.
- коэффициент долговечности; если число циклов нагружения каждого зуба колеса больше базового, то принимают = 1
[п] Н
—
коэффициент безопасности; для колес из нормализованной и улучшенной стали, а также при объемной закалке принимают [п] Н
= 1,1—1,2, принимаем [п] Н
= 1,15
Принимаем наименьшее значение [σ] н
=495,65 Мпа
Допускаемые напряжения на изгиб определяем по формуле
Важнейшим геометрическим параметром редуктора является межосевое расстояние, которое необходимо для определения геометрических параметров колес.
1. Определяем межосевое расстояние по формуле (с.11 [2]) :
- вспомогательный коэффициент. Для косозубых передач =43, для прямозубых — =49,5;
- передаточное число тихоходной передачи;
Т 2
- вращающий момент на 2 промежуточном валу, Н·м;
- коэффициент неравномерности нагрузки по длине зуба. Для прирабатывающихся зубьев = 1(см. 3.1, п. 1 [1]);
- коэффициент ширины венца колеса, равный 0,28...0,36 — для шестерни, расположенной симметрично относительно опор =0,3 (с. 13 [2]).
- допускаемое контактное напряжение колеса с менее прочным зубом или среднее допускаемое контактное напряжение, н/мм2.
Полученное значение межосевого расстояния округляют в большую сторону до стандартного по СТ СЭВ 310-76 : 40, 50, 63, 71, 80, 90, 100, 112, 125, 140, 160, 180, 200, 220, 250, 280, 315 мм. Принимаем =200 мм.
2. Выбирают модуль в интервале m=(0,01÷0,02) , по СТ СЭВ 310—76 (в мм)
3. Определяем суммарное число зубьев данной передачи по формуле (с.13 [2]) :
Z Σ
– суммарное число зубьев передачи.
Находим число зубьев на шестерни по формуле (с.14 [2]) :
где - передаточное число промежуточной передачи.
4. определяем фактическое передаточное число по формуле (с.18 [2]) :
Погрешность при выборе передаточного числа определяем по формуле (с.18 [2]) :
Погрешность составляет всего 1,5% , что позволяет сделать вывод, что передаточное число выбрано верно.
7. Определяем диаметры колес (с.41 [1]) .
Диаметры окружностей вершин и впадин шестерни
8. Определяем ширину шестерни и колеса.
Ширину колеса находим по формуле (с.41 [1]) :
- коэффициент ширины венца колеса, равный 0,28...0,36 — для шестерни, расположенной симметрично относительно опор, принимаем =0,3 (с. 13 [2]).
Ширина шестерни больше на (3÷8) мм чем у колеса
Таким образом, найденные диаметры определены, верно.
Окружная сила направлена по касательной в точки касания колеса и шестерни.
где Т 2
- вращающий момент на 2 промежуточном валу, Н·м;
d 2
– делительный диаметр шестерни, мм.
Радиальная сила направлена к центру окружности и определяется по формуле (с.19 [2]) :
где α – между геометрической суммой радиальной и осевой силами,
β- угол наклона зубьев, tg β=0,364.
Проверяем зубья колес по напряжениям изгиба. Должно выполняться неравенство
где - коэффициент, учитывающий распределение нагрузки между зубьями. (с.15 [2]), =1;
- коэффициент динамической нагрузки, зависящий от окружной скорости колес и степени точности передачи (с.16 [2]), =1,4;
- коэффициент неравномерности нагрузки по длине зуба (с.16 [2]),
- коэффициент, учитывающий наклон зуба,
- коэффициенты формы зуба шестерни и колеса (с.16 [2]), =3,61.
где - коэффициенты формы зуба шестерни и колеса (с.16 [2]), =3,61;
- коэффициенты формы зуба шестерни и колеса (с.16 [2]), =3,88;
- напряжение изгиба на колесе, Мпа.
Так как [σ] F
1
=547,83 МПа, [σ] F
2
=495,65 МПа и σ F
1
=233,67 МПа, σ F
2
=217,41 МПа , то колеса прошли проверку по напряжениям на изгиб.
Проверяем зубья колес по контактным напряжениям .
где , , -коэффициенты учитывающие распределение нагрузки между зубьями, неравномерность распределения нагрузки по длине контактной линии, дополнительные динамические нагрузки, так как редуктор рассчитан на долгий срок службы, то =1, =1, =1 .
При определении погрешности передаточного числа, получили Δi= 1,5% , что позволяет сделать вывод- передаточное число выбрано, верно.
Так как[σ] F
1
=547,83 МПа, [σ] F
2
=495,65 МПа и σ F
1
=233,67 МПа, σ F
2
=217,41 МПа то колеса прошли проверку по напряжениям на изгиб.
В результате расчетов определили, что 0,88% недогрузки. Это величина не превышает допустимого значения (5 % перегрузки и 10 % недогрузки), следовательно, колеса прошли проверку по контактным напряжениям.
В результате проверочного расчета убедились, что полусумма делительных диаметров равна межосевому расстоянию.
Определить основные размеры валов редуктора предварительно.
Рисунок 5.1 – Схемы для расчета a) быстроходного вала; b) 1 промежуточного вала; c)2 промежуточного вала; d) тихоходного вала.
Крутящий момент быстроходного вала – 22,8 Н·м
Крутящий момент 1 промежуточного вала –54,2 Н·м
Крутящий момент 2 промежуточного вала – 220,1 Н·м
Крутящий момент тихоходного вала – 697,4 Н·м
Расчет валов ведем по заниженным допускаемым напряжениям на чистое кручение.
Расчет быстроходного вала ведется по следующим формулам
где Т- крутящий момент на валу, Н·м;
Для того чтобы вести дальнейший расчет необходимо выбрать стандартный диаметр входного конца вала под муфту. Выбираем упругую муфту с торообразной оболочкой. Муфта выбирается по диаметру выходного вала двигателя ( мм). Тогда
=25 мм.
Так как при расчете значение
оказалось меньше, чем значения валов применяемых в практике, то принимаем
= 30 мм.
При расчёте быстроходного вала необходимо подобрать диаметр выходного конца вала под муфту. При подборе нужно руководствоваться стандартными значениями диаметров муфт. Для входного конца быстроходного вала подбираем упругую муфту с торообразной оболочкой, так как она больше всего подходит для соединения двигателя и выходного конца вала редуктора.
При расчёте первого промежуточного вала диаметры валов получились маленькими по сравнению с применяемыми в производстве, поэтому мы увеличиваем значение диаметров валов к большему из ближайших стандартных значений.
Определить расстояние между точками приложения сил на валах.
Быстроходная передача (берём из пункта 2.6) :
Промежуточная передача (берём из пункта 3.6):
Тихоходная передача (берём из пункта 4.6):
Диаметры валов (берём из пунктов 5.5 5.6 5.7 5.8):
Выполняется графически, расстояния определяются непосредственным замером с компановки.
Провести проверочный расчёт валов в виде уточнённого расчёта.
Проверочный расчёт производим в виде определения коэффициента запаса прочности в опасных сечениях
Определение реакций, построение эпюр изгибающих моментов первого промежуточного вала.
Примем вал за балку, закрепленную с двух концов на подвижно шарнирных опорах. Силы в подшипниках заменим на реакции опор. И рассчитаем изгибающий момент в каждой точке приложения сил.
Определяем реакции опор в плоскости (XoY) действия сил
Сумма моментов относительно точки А равен нулю.
Сумма моментов относительно точки В равен нулю
Определяем реакции опор в плоскости (XoZ) действия сил
Сумма моментов относительно точки А равен нулю
Сумма моментов относительно точки В равен нулю
Определяем общий изгибающий момент в каждом опасном сечении по формуле
Производим расчет изгибающих моментов для построения эпюр.
Примем, что нормальные напряжения от изгиба изменяются по симметричному циклу, а касательные от кручения .
Коэффициент запаса прочности рассчитываем для опасных сечений ( опасным сечением является, то сечение вала, где наибольший изгибающий момент; есть концентратор напряжений; наименьший диаметр вала).
Коэффициент запаса прочности определяем по формуле (6.17 [1]):
где - коэффициент запаса прочности нормальных напряжений, определяется по формуле (6.18 [1]):
где - предел выносливости стали при симметричном цикле изгиба; для углеродистой стали ; ( - предел прочности (таблица 3.3 [1]) =780 Н·мм, тогда Н·мм. - эффективный коэффициент концентрации нормальных напряжений =1,36 (таблица 6.2 [1] );
- масштабный фактор для нормальных напряжений; =0,88 (таблица 6.8 [1] );
- амплитуда цикла нормальных напряжений, равная наибольшему напряжению изгиба в рассматриваемом сечении, определяем по формуле ( с. 285 [1] ):
где М - изгибающий момент в данном сечении (из эпюр);
W- момент сопротивления сечения нетто, определяется по формуле:
для концентратора напряжений – шпонка:
для концентратора напряжений – совпадение с краем шестерни:
где - коэффициент запаса прочности нормальных напряжений, определяется по формуле (6.18 [1]):
где - предел выносливости стали при симметричном цикле изгиба; для углеродистой стали ; тогда Н·мм. - эффективный коэффициент концентрации касательных напряжений =1,14 (таблица 6.2 [1] );
- масштабный фактор для нормальных напряжений; =0,77 (таблица 6.8 [1] );
- амплитуда цикла касательных напряжений, равная наибольшему напряжению изгиба в рассматриваемом сечении, определяем по формуле ( с. 285 [1] ):
где М к
– крутящий момент в данном сечении (кинематического расчета);
W-момент сопротивления сечения нетто, определяется по формуле:
для концентратора напряжений – шпонка:
для концентратора напряжений – совпадение с краем шестерни:
- коэффициент чувствительности материала к асимметрии цикла, =0,1 ( с. 100 [1] ).
Предварительный расчет размеров шпонок :
Рассчитываем коэффициент запаса прочности для шестерни:
Рассчитываем коэффициент запаса прочности для колеса ( шпоночный паз:
При уточнённом расчёте мы рассчитывали коэффициент запаса прочности, который позволяет одновременно учитывать как касательные, так и нормальные напряжения на вал. Для того чтобы выполнялось условие прочности, необходимо чтобы [n]= >10 (с.95[3]). Сравнивая расчётный результат с допускаемым значением можно сделать вывод, то жёсткость вала обеспечивается.
8 Подбор и проверка подшипника качения и скольжения
Подобрать и проверить подшипники на долговечность.
Подшипник номер 305, шариковый радиальный, внутренний диаметр 25мм, серия диаметра средняя.
C=29,6 kH – динамическая грузоподъёмность
V – коэффициент вращения; при вращающемся внутреннем кольце подшипника V=1
Подшипник подбираем по диаметру вала и направлению воспринимаемой нагрузки, а проверяем на долговечность с учётом динамической нагрузки.
На первом этапе подшипник выбираем по диаметру вала, характеру нагрузки (действующими силами), частоте вращения вала, по условиям работы, наиболее дешевые шариковый радиальный средней серии 305(ГОСТ 8388-75).
Наружный диаметр подшипника D=62 мм;
Внутренний диаметр подшипника d=25 мм;
Динамическая грузоподъёмность C=17,3 kH;
m – показатель степени: m=3,33 – для роликовых подшипников;
- коэффициент учитывающий влияние качества подшипника и качества его эксплуатаций; при обычных условиях работы подшипника =0,7…0,8 – для шариковых подшипников;
n – частота вращения внутреннего кольца подшипника соответствующего вала, об/мин.
Полученный результат долговечности подшипника удовлетворяет условию 10000Курсовая работа: Расчет и проектирование привода для пластинчатого конвейера
Реферат: Исследование маркетинговой деятельности предприятия и разработка рекомендаций по ее совершенство
Конструкция Итогового Сочинения 11 Класс
Курсовая работа по теме Анализ оборотных средств и повышение эффективности их использования на примере ООО 'Элин' г. Ижевск
Реферат: Стратегія діяльності підприємства
Диссертация Библиотека Ленина
Реферат: Лечение и профилактика чумы плотоядных в Архаринском районе Амурской области
Почему Важно Учитывать Мнение Другого Человека Сочинение
Доклад по теме Как приблизиться к Богу
Реферат: Королева Марго и Генрих IV, Ришелье и Мазарини. Скачать бесплатно и без регистрации
Сочинение На Тему Характеристика Образа Простакова
Курсовая работа: Методы стимулирования сбыта. Скачать бесплатно и без регистрации
Острая Лучевая Болезнь Реферат
Монополистическая Конкуренция Курсовая Работа
Экскаватор Демолятор Скачать Реферат
Сочинение: Нравственные проблемы в романе М.Ю.Лермонтова "Герой нашего времени"
Дипломная работа: Технологический процесс послеуборочной обработки зерна в ОАО Агрофирма им ВМ Зайцева
Реферат по теме Управление предприятием оптовой торговли
Развитие Физкультуры И Спорта Реферат
Пособие по теме Дистанционные технологии в образовании
Кандидатская Диссертация Скачать Бесплатно
Дипломная работа: Эколого-экономическая оценка деятельности предприятия (на примере МУП "Теплотехнология")
Реферат: Способы акционирования и приватизации
Реферат: Коммуникации в менеджменте